纯低温余热发电技术Word文档下载推荐.docx
《纯低温余热发电技术Word文档下载推荐.docx》由会员分享,可在线阅读,更多相关《纯低温余热发电技术Word文档下载推荐.docx(42页珍藏版)》请在冰豆网上搜索。
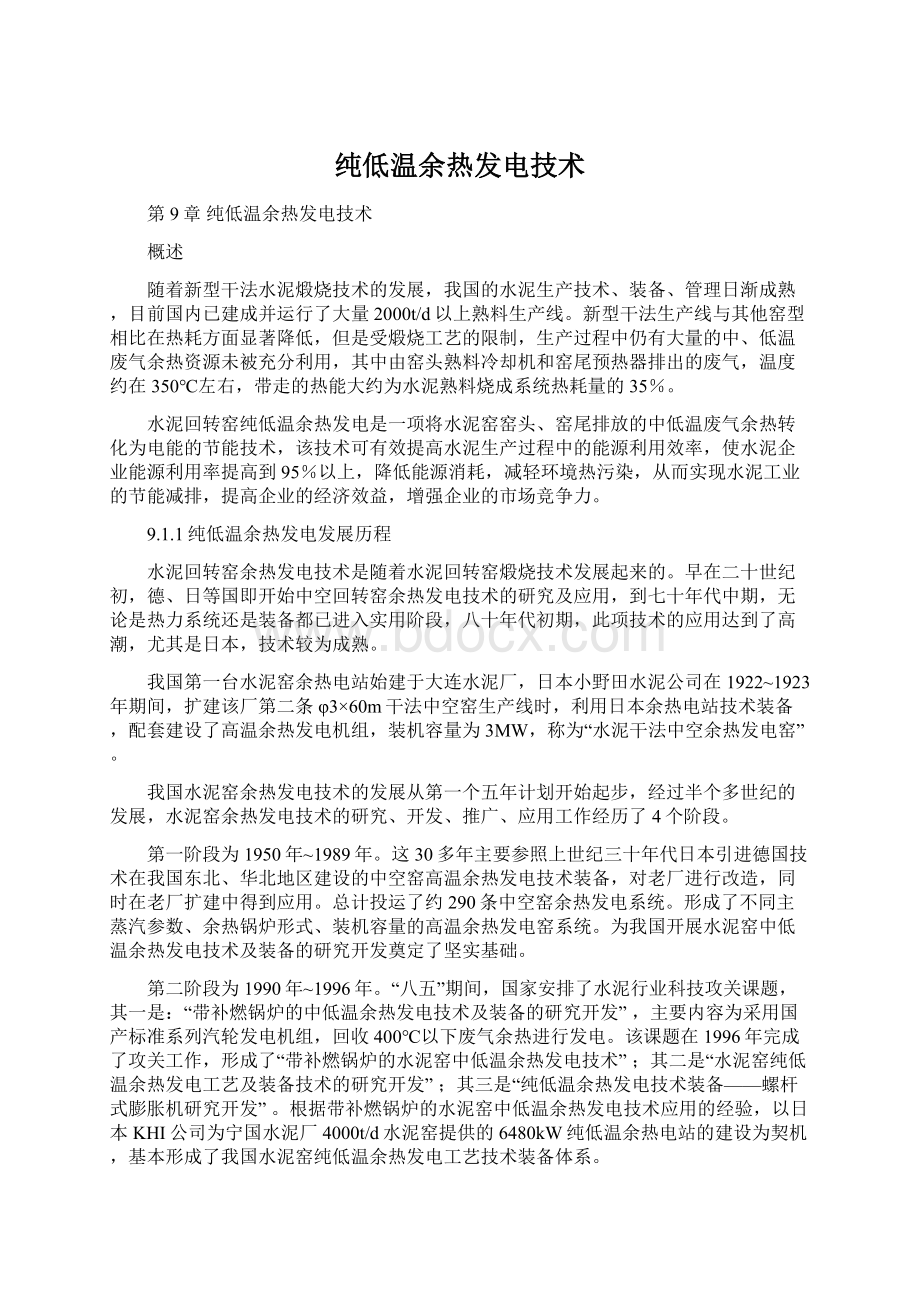
其二是“水泥窑纯低温余热发电工艺及装备技术的研究开发”;
其三是“纯低温余热发电技术装备——螺杆式膨胀机研究开发”。
根据带补燃锅炉的水泥窑中低温余热发电技术应用的经验,以日本KHI公司为宁国水泥厂4000t/d水泥窑提供的6480kW纯低温余热电站的建设为契机,基本形成了我国水泥窑纯低温余热发电工艺技术装备体系。
第三阶段为1997年~2005年。
推广、改进“带补燃锅炉的水泥窑中低温余热发电技术”和“水泥窑纯低温余热发电技术”。
截止2005年底,利用“带补燃锅炉的水泥窑中低温余热发电技术”的水泥厂,国内有23个36条1000~4000t/d预分解窑生产线上安装了28台带补燃锅炉的中温余热发电机组,总装机为。
与此同时,我国水泥窑纯低温余热发电技术的研发也取得了突破性的进展,利用国产设备和技术先后在13条新型干法窑上,配套建设了装机容量分别为、、、的纯低温余热电站。
第四阶段为2005年以后。
由于水泥窑纯低温余热发电技术和装备已日臻成熟,国家产业政策明确规定不允许上带补燃炉的余热发电系统,而纯低温余热发电的概念是相对于带补燃炉余热发电技术而命名的,随着带补燃炉余热发电技术被取缔,纯低温余热发电技术被更名为水泥窑低温余热发电技术。
自此,水泥余热发电进入了蓬勃发展阶段。
9.1.2纯低温余热发电技术
1.单压式纯低温余热发电系统
(1)单压系统工艺流程
新型干法水泥生产线上,一般中低温纯余热发电系统的余热回收分为两部分:
一是窑尾预热器一级筒出口排出的300~350℃的废气余热;
二是窑头熟料篦式冷却机尾部排出400℃以下的废气余热。
由于生产需要,生产线的废气余热还将作为生料粉磨系统、煤粉制备系统的烘干热源。
为了同时满足发电与原、燃料烘干的需要,窑尾SP锅炉一般均采用立式锅炉,布置在窑尾预热器后的高温风机之上。
窑尾在最上一级(C1级)预热器至窑尾高温风机的下行管道上引出废气管道与SP锅炉相连,锅炉出口烟气温度控制在220℃左右,送到窑尾高温风机进风口的管道上,以满足下道工序烘干原料和燃料的需要。
烘干原料和燃料后的废气由原废气处理系统的收尘器净化后排入大气。
控制锅炉的烟气阻力≤1000Pa,使系统的阻力在窑尾高温风机的能力允许范围之内。
在原预热器出口至高温风机的烟道引出管道、原下行管道以及锅炉出口管道上均增设电动百叶阀门,对气流进行控制和切换,原下行管道可做为锅炉的旁通烟道。
当需要提高烘干原料和燃料的烟气温度时,可适当调节下行烟道调节阀,让锅炉出口的低温烟气和C1级出口直接下行的高温烟气混合,提高进窑尾风机(原料磨)的烟温,其调节范围从220℃或更低直至C1级出口温度(即烟气一点不通过SP锅炉),而且SP炉的进口烟道阀和旁路烟道阀,正常设计在窑控制室操作,窑操作可随时根据具体情况调整,既满足了水泥生产的稳定运行,又保证了SP炉的安全。
通过旁通烟道的调节作用还可使水泥生产及余热锅炉的运行均达到理想的运行工况。
在熟料冷却机与窑头收尘器之间设一台AQC锅炉,由废气管道连接。
为保证锅炉正常产汽量,需对冷却机进行改造,从冷却机中部(原煤磨抽风处)引出管道,抽出350℃左右的废气送至沉降室,滤去大颗粒粉尘后再由管道引向AQC锅炉。
从冷却机中部抽风的目的是提高进入AQC余热锅炉的废气温度,提高整个系统的循环效率。
出AQC锅炉的废气进入原有的窑头收尘器收尘后,由原有窑头排风机排放,冷却机剩余的低温余风仍由原路进窑头收尘器。
原余风管路系统可做为锅炉的旁通烟道,当锅炉故障或水泥生产不正常时可关闭去AQC锅炉的阀门,气流可不经锅炉而由此旁路系统直接排至窑头收尘器。
在冷却机原余风管路上、新设的去锅炉管路上和出锅炉管路上均增设电动百叶阀门,以实现对气流的控制和切换。
锅炉和沉降室的烟气总阻力控制小于1000Pa,使改造后的气体流量和压力在窑头排风机的能力允许范围之内。
(2)热力系统方案
目前普遍采用的单压系统热力流程如图9-1所示。
图9-1单压系统热力流程图
本热力系统中,由于窑尾SP锅炉排气需要提供给水泥原料生产系统作为烘干用热源,因此排气温度不能太低,故SP锅炉只设蒸发器和过热器,蒸发器给水由窑头AQC锅炉的省煤器加热后供给。
窑头AQC锅炉排气温度要保证在系统中不结露和节点温差合理的前提下尽可能低,故窑头锅炉由省煤器、蒸发器、过热器组成,省煤器加热后的热水同时作为窑尾和窑头蒸发器的给水。
窑头、窑尾锅炉同时生产一种压力的过热蒸汽,混合后进入汽轮机,汽轮机排气经凝汽器凝结成水由凝结水泵输送到除氧器,除氧后再由给水泵加压送回窑头锅炉的省煤器,从而形成完整的汽水热力循环系统。
单压热力系统的特点是汽轮机只设置一个进汽口,窑头余热锅炉和窑尾余热锅炉只生产参数相同或相近的主蒸汽。
那么考虑水泥窑废气余热的调配及利用、余热锅炉的设计、电站热力系统的配置等因素的唯一目的,就是提高主蒸汽品质及产量。
主蒸汽品质及产量在外部条件确定的情况下,完全决定了系统的发电功率。
(3)主要设备及系统配置
①SP余热锅炉
在窑尾设置SP余热锅炉,利用预热器一级筒出口废气作热源。
锅炉仅设置蒸汽段,生产~,310~340℃的过热蒸汽,与窑头AQC余热锅炉生产的过热蒸汽混台后送入汽轮发电机,出SP余热锅炉的废气温度降到190~220℃,供生料粉磨或煤粉制备烘干使用。
②AQC余热锅炉
在窑头设置AQC余热锅炉,利用篦式冷却机中部抽取的废气(约350~400℃)作为热源。
余热锅炉分为蒸汽段和热水段运行,蒸汽段生产的~,310~340℃过热蒸汽,与窑尾SP余热锅炉生产的过热蒸汽混合后送入汽轮发电机组,热水段生产的85~200℃热水作为AQC余热锅炉蒸汽段及SP余热锅炉的给水,出AQC锅炉废气温度降至100℃左右。
③汽轮发电机组
配置凝汽式汽轮机组一套。
④除氧系统方案
a.真空除氧
真空除氧器是一种使水在真空下低温沸腾,脱除水中的氧气、氮气、二氧化碳等气体的设备。
一般在30~60℃温度下进行,可实现水面低温状态下除氧(60℃或常温),对热力锅炉和负荷波动大而热力除氧效果不佳的蒸汽锅炉,均可用真空除氧而获得满意除氧效果。
真空除氧能利用低品位余热,可用射气抽汽器加热软化水,又能分级及低位安装,除氧可靠,运行稳定,操作简单,适应性强。
当负荷在40%~120%范围内变化时,除氧效果都能达标。
对于低压蒸汽锅炉,其给水含氧量≤L即可符合要求。
b.热力除氧
热力除氧的工作原理即利用蒸汽对水进行加热,使水达到一定压力下的饱和温度,即沸点。
这时除氧器的空间充满着水蒸气,而氧气的分压力逐渐降低为零,溶解于水中的氧气将全部逸出,以保证给水含氧量合格,同时还能去除其他的气体。
低参数的小型电站采用的是大气式除氧器,工作压力,工作温度104℃,给水含氧量L。
通过对热力系统的合理设计,在余热电站中使用热力除氧器的同时,可以使AQC锅炉出口的废气温度≤100℃,余热利用效率还有所提高。
c.化学除氧
化学除氧是利用容易和氧发生化学反应的一些药剂,使之与水中溶解氧化合而达到除氧目的。
化学除氧能够彻底除去水中溶解氧,但不能除去其他气体。
现在常用的化学药剂是联氨(N2H4),它不仅能除氧、提高给水的pH值,同时还可在管道内表面形成一层保护膜。
2.闪蒸式纯低温余热发电系统
(1)闪蒸系统工艺流程
闪蒸纯低温余热发电系统窑尾余热锅炉(PH炉)一般均采用框架结构,其型式为卧式强制循环。
从预热器出口风管引高温废气至窑尾PH余热锅炉,经过锅炉热交换后,从锅炉出口返回到预热器出口的热风管道,锅炉内运行时沉降下来的生料粉尘通过除灰系统送回熟料生产线。
高温废气是否经过余热锅炉可以由预热器出口分别到窑尾高温风机热风管道和锅炉取风管道上的两台电动百叶阀来控制。
当锅炉取风管道上的电动百叶阀打开,旁路电动百叶阀关闭时,高温废气通过PH锅炉;
当锅炉取风管道上的电动百叶阀关闭,旁路电动百叶阀打开时,高温废气从原通道通过。
当原料的水分偏高时,还可以部分打开旁路电动百叶阀,以提高进入原料磨的热风温度,满足原料烘干的要求。
窑头AQC(熟料冷却机)锅炉:
由于水泥熟料生产线中熟料冷却机出口的废气温度一般较低,很难进行动力回收,需要对冷却机进行必要的改造,使进入AQC炉的废气温度提高。
改造方法是在冷却机中部新开抽气口,并增设出口废气管道,利用这部分温度为360℃左右的废气,通过沉降室引入AQC余热锅炉进行回收。
沉降室中收集的粉尘通过除灰系统送回熟料生产线。
AQC锅炉系统一般共设五台阀门。
在新安装的锅炉取风管道上安装一台电动百叶阀,用来控制锅炉入口风量;
在冷却机至原收尘器入口管道上安装一台电动百叶阀,用来控制或切断直接进入收尘器的废气;
在锅炉出口废气管道上安装一台电动闸板阀,以满足窑系统运行而锅炉系统故障需要临时检修时完全切断进入锅炉的废气;
在冷却机尾部余风风管至锅炉取风管之间连接一根风管并安装一台电动百叶阀,用于调节入锅炉风温;
在锅炉取风管道上安装一台用于掺入冷风的电动蝶阀,在回转窑工况波动时调节锅炉风温。
(2)热力系统介绍
整个热力系统工艺流程是一个完整的水汽循环利用过程。
在生产线窑尾、窑头各设置一台余热锅炉,用于与废气的热量交换,热交换后锅炉产生的过热蒸汽导入汽轮机做功,汽轮机带动发电机发电。
做过功后的蒸汽经凝汽器冷凝成凝结水,经凝结水泵与闪蒸器出水汇合,通过锅炉给水泵增压进入AQC锅炉省煤器进行加热,经省煤器加热后的高温水分三路分别送到AQC炉汽包、PH炉汽包和闪蒸器内。
进入两台锅炉汽包内的高温水在锅炉内循环受热,最终产生过热蒸汽,两路过热蒸汽汇集后进入汽轮机。
进入闪蒸器的高温水根据闪蒸汽化原理(高温高压水进入低压空间后会部分瞬间汽化)产生一定压力的饱和蒸汽进入汽轮机后级辅助做功,做功后的蒸汽经过凝汽器冷凝后形成凝结水重新参与系统循环,循环过程中消耗掉的水由纯水装置制取出的纯水补充到系统中。
闪蒸发电技术是一种能最大限度地利用中、低温余热的纯余热利用发电技术。
该技术主要以200℃~500℃的低温废气作为热源,通过余热锅炉生产出过热蒸汽和一定量的饱和水,将常规发电系统无法利用的部分低品位低温热能,通过闪蒸系统生产出饱和蒸汽,与过热蒸汽一起进入多参数汽轮机做功发电,从而增加功率。
同时,因为增加了闪蒸回路,使得该系统具有平衡和吸收不稳定热源发生的参数变化,保证发电系统安全、稳定、高效的运行,也对原工艺系统起到了平衡稳定的作用。
图9-2闪蒸系统热力流程图
①余热锅炉子系统
窑尾PH锅炉形式为卧式,锅炉由过热器、蒸发器、汽包及热力管道构成,废气流动方向为水平流动,换热管采用蛇形光管,以防止积灰。
因生料粉尘具有黏附性,故锅炉下部设置振打装置进行除灰,工质循环采用循环泵进行强制循环。
窑头AQC锅炉形式为立式,锅炉由省煤器、蒸发器、过热器、汽包及热力管道等构成。
AQC锅炉前设置一台预收尘器(沉降室),以降低入炉废气粉尘浓度。
锅炉内的废气流动方向为自上而下,换热管采用螺旋翅片管,以增大换热面积、减少粉尘磨损。
工质循环方式为自然循环。
②汽轮发电机组子系统
针对水泥窑余热资源品位低、流量大的特点,为充分利用余热热能,汽轮机采用多级补汽凝汽式汽轮机,利用压力参数较低的主蒸汽和来自闪蒸器的饱和蒸汽导入汽轮机做功。
针对汽轮机后级蒸汽中水分较多、叶片易发生水蚀现象的特点,在低压部分特别设计了集水槽和疏水孔,充分利用转子转动的离心力分离水珠,避免水蚀。
另外,在末两级叶片前部覆盖一层特殊合金,以减轻水击产生的损伤。
发电机为三相交流同步发电机,采用同轴交流无刷励磁或静止可控硅励磁方式。
③锅炉给水子系统
汽轮机排汽通过凝汽器冷凝后,其凝结水经凝结水泵增压通过管道进入汽封凝汽器,在汽封凝汽器中利用来自主蒸汽联合调节阀以及汽轮机高压端轴封泄漏的部分蒸汽将凝结水加热,这样可以充分回收热能。
加热后的凝结水再通过管道与闪蒸器下降管束水汇合,作为锅炉给水泵进口给水,经锅炉给水泵增压后通过锅炉给水管道送往AQC锅炉省煤器,提高锅炉给水温度后作为余热锅炉的给水。
④循环冷却水子系统
循环冷却水子系统的作用主要是为凝汽器及其他冷却设备提供冷却循环用水,包括冷却水泵和一套机械强制通风立式冷却塔及相应的冷却水管道等。
蒸汽冷凝时放出大量热,必须要有大流量的冷却水带走,为解决冷却水本身的温度升高问题,设置机械强制通风立式冷却塔对其进行冷却,水系统为循环运行,为保证循环水质,系统内应投加相应的除垢剂和防腐剂。
根据实际需要,可以采用自然通风逆流双曲线型冷却塔。
在水资源缺乏的地区,也可以采用风冷凝汽技术。
⑤化学水处理子系统
化学水处理装置一般采用离子交换方式来置换出原水中的阴阳离子形成软化除盐水,作为发电系统的补充水,以达到减少热力系统结垢与腐蚀的目的。
化学水处理装置运行中失效的阳离子树脂和阴离子树脂分别通过化学药品进行再生,以恢复树脂变换能力。
根据水质情况,也可以采用反渗透法纯水制取装置。
原水
原水箱
原水泵
多级砂过滤器
过滤水箱
原床
子核
阴床
纯水箱
凝汽器热水井
图9-3化学水处理流程
⑥DCS子系统
整套余热发电机组采用先进、成熟的集散控制系统(DCS)进行控制、监视。
DCS系统由现场控制层和控制管理层组成。
现场控制层的作用是对现场的I/O信号进行采集、运算和逻辑顺控处理,通过现场控制层网络将相关数据送入控制处理机,实现过程控制和顺序、逻辑控制。
根据发电系统工艺流程和实际操作的需要,配置不同数量的AQC锅炉控制站、PH锅炉控制站、汽轮机及辅机控制站和汽轮机本体控制站。
控制管理层的作用是实现集中操作和统一管理。
通过监控系统和生产过程,实现控制方案,生成系统数据库、用户画面和报表等,从而在用户与系统功能之间提供了一个接口,使操作员能够观察过程回路参数状态、实时趋势、历史趋势、报警和日报月报情况,实现设备起停、过程回路操作和参数调整等。
过程工程师可以通过工程师站调出过程组态画面进行操作方案组态、过程流程圈组态、趋势画面及各种报表组态等。
根据实际需要,系统控制管理层由数量不同的工程师站(ES)、操作站(OSl/OS2)、现场操作站(OS3)、后备操作按钮、激光打印机、彩色喷墨打印机组成。
为了系统的安全和可靠运行,整套系统在配置时充分考虑到必要的网络设备和控制处理机冗余,并由UPS电源和市电冗余供电。
DCS系统的软件主要功能:
流程图显示,控制回路显示和操作,报警及报警显示,趋势图显示,表格显示,数据记录,在线诊断,在线数据存储,主要变量表格显示以及与MIS网进行信息通讯等。
⑦汽轮机DEH控制系统
a.基本工作原理
DEH控制系统的主要目的是控制汽轮发电机组的转速和功率,从而满足供电的要求。
对于供热机组,DEH控制系统还将控制供热压力或流量。
DEH系统具有转速控制回路,电功率控制回路,主汽压控制回路,超速保护回路等基本控制回路以及同期、调频限制、解耦运算、信号选择、判断等逻辑回路。
DEH主要通过DDV伺服阀控制高压阀门,从而达到控制机组转速,功率的目的。
b.ETS保护系统
ETS即汽轮机紧急跳闸保护系统,用来监视对机组安全有重大影响的某些参数,以便在这些参数超过安全限制值时,通过该系统去关闭汽轮机的全部进汽阀门,实现紧急停机。
该系统具有各种保护投切、自动跳闸保护、首出原因记忆等功能。
c.TSI系统
TSI汽轮机监视仪表系统,用来在线监测对机组安全有重大影响的参数,主要是汽轮机的转速、振动、轴向位移等参数,以便在这些参数超过安全限值时,通过DEH和ETS控制汽轮机,实现安全停机。
⑧接入系统主接线
余热发电站发出的电能一般是并网但不上网,自发自用,即发电机发出的电能,通过电缆接入水泥工厂的总降压变电站中压母线,电能供水泥生产的设备使用。
在余热电站未运行之前,先通过总降中压开关柜将总降的电能输送至余热电站,以启动电站设备。
当电站发电机开始发电后,通过电站内的开关柜、电缆及总降联络开关柜与外部电网同期并网运行,向水泥生产设备供电,同时发电机还通过电站内开关柜向站用变压器供电。
3.双压补汽式纯低温余热发电系统
(1)双压余热发电技术的原理
双压余热发电技术指采用两种压力等级的蒸汽参数均衡换热端差分级吸收烟气余热,使工质吸热量最大程度趋近于烟气放热量,两种压力等级的蒸汽进入双压补汽汽轮机,拖动发电机发电的技术集成系统。
根据朗肯循环原理,提高工质的初参数、降低工质的终参数可以提高火力发电厂热力系统热经济性。
在余热锅炉蒸汽动力循环中,提高蒸汽压力和温度可以提高循环效率,但随着给水压力升高,其饱和温度升高,为了保持一定的传热温差,必须将加热水和蒸发所需的受热面放在较高的烟温区段,势必相应提高排烟温度,使余热利用受到限制,在余热烟气温度较低时,只能采取较低的蒸汽压力,才能使余热锅炉的效率不会过低。
而水泥窑纯低温余热系统由于受水泥生产线废气参数的限制,考虑到热端温差,蒸汽参数压力不能太高。
(2)工艺流程
窑尾余热锅炉(SP炉)采用立式锅炉,布置在窑尾预热器后的高温风机之上,在预热器一级筒出口引出废气管道与SP锅炉入口相连,SP锅炉的出口与高温风机的入口管道连接,引出管道与原烟气管道以及锅炉出口管道上均增设电动百叶阀,对气流进行控制和切换,原窑尾烟气管道可做为锅炉的旁通烟道。
当SP锅炉出现故障或水泥生产不正常时,气流可不通过锅炉而流向旁通烟道,使锅炉解列,既满足了水泥生产的稳定运行,又保证了SP炉的安全。
水泥生产线窑尾预热器产生的300~350℃废气经烟气管路引入窑尾余热锅炉,换热后的废气为满足烘干原料的需要,锅炉出口烟气温度控制在240±
10℃。
烘干原料后的废气由原废气处理系统的收尘器净化后排入大气。
窑头余热锅炉(AQC炉)设在篦冷机与窑头收尘器之间,露天布置在窑头篦冷机框架旁,为减少熟料粉尘对AQC锅炉的磨蚀,窑头废气进入AQC锅炉前应设一级沉降室。
由于篦冷机原废气出口位于篦冷机尾部,废气温度较低,为提高主蒸汽品质,去AQC锅炉的废气应由篦冷机中部引出。
保留原有的废气管道,作为篦冷机剩余低温废气的通道。
去AQC锅炉的废气管路、锅炉出口管路及原有废气管路均增设电动百叶阀,以实现对气流的控制和切换,当锅炉出现故障或水泥生产不正常时可关闭去AQC锅炉的阀门,废气可不经锅炉而由原废气管路直接排至窑头收尘器。
由篦冷机中部抽取的360℃左右的废气通过废气管道送至沉降室,滤去大颗粒粉尘后,再由管道引向窑头双压余热锅炉,经过AQC锅炉充分换热后,废气温度降至80~100℃左右,然后通过排气管路送入窑头收尘器,净化后的废气通过窑头排风机经烟囱排入大气。
(3)热力循环系统
窑尾余热锅炉带单汽包,设加热器、蒸发器和过热器,给水由窑头AQC锅炉的公共加热器加热后供给。
窑头双压余热锅炉带双汽包,设公共加热器、低压蒸发器、低压过热器、高压蒸发器、高压过热器,公共加热器加热后的热水同时作为窑尾蒸发器、窑头低压蒸发器、窑头高压蒸发器的给水。
图9-4双压系统热力流程图
窑尾余热锅炉和窑头双压余热锅炉产生的中温中压过热蒸汽通过进汽速关阀进入汽轮机,窑头双压余热锅炉产生的低压蒸汽则通过汽轮机的补汽口送入汽轮机,蒸汽在汽轮机内进行能量转换,汽轮机拖动发电机进行发电。
做功后的蒸汽进入凝汽器,凝结水则通过轴封加热器进入真空除氧器,然后通过给水泵送入窑头双压余热锅炉。
窑头双压余热锅炉产生的主蒸汽和窑尾余热锅炉产生的主蒸汽与低压蒸汽分别从不同部位进入汽轮机。
窑头双压余热锅炉和窑尾余热锅炉排污水通过排污管道分别进入定排扩容器及连排扩容器,定排扩容器及连排扩容器内污水进入降温池。
汽轮机尾部做过功的蒸汽经冷凝器冷却后变为冷凝水,经轴封加热器加热成约55℃的给水经给水泵进入窑头双压余热锅炉,给水先后经过公共加热器、低压蒸发器、低压过热器、高压蒸发器、高压过热器,与烟气进行逆向对流换热;
给水在公共加热器被加热成饱和热水后,分成三路经管路分别进入窑头双压余热锅炉低压汽包,窑头双压余热锅炉高压汽包和窑尾锅炉加热器;
进入窑头双压余热锅炉低压汽包的饱和水经过低压蒸发器、低压过热器后被加热成低压过热蒸汽;
进入窑头双压余热锅炉高压汽包的饱和水经过高压蒸发器、高压过热器后变成高压过热蒸汽;
进入窑尾余热锅炉加热器的饱和水经过窑尾余热锅炉内部的加热器、蒸发器、过热器时与烟气进行逆向对流换热后被加热成高压过热蒸汽;
两台锅炉的高压过热蒸汽经管路混合后进入汽轮机主汽门;
窑头双压余热锅炉产生的低压过热蒸汽进入汽轮机补汽。
双压余热发电技术按照能量梯级利用的原理,在同一台余热锅炉中设置两个不同压力等级的汽水系统,使温度相对较高的介质产生较高参数的蒸汽,温度相对较低的介质产生较低参数的蒸汽,分别进行汽水循环,产生高压和低压两种过热蒸汽。
高压过热蒸汽作为主蒸汽、低压过热蒸汽作为补汽分别进入补汽凝汽式汽轮机,推动汽轮机做功发电,使能量得到合理利用,提高了余热回收效率。
(4)主要设备及系统配置
窑尾余热采用立式SP锅炉,带单汽包,设加热器、蒸发器和过热器,烟气在管外流动,受热面为蛇形光管,并用特定的技术保证锅炉管束免受烟气颗粒的冲刷、磨损及腐蚀,以防止高速高温含尘气体对对流管束的韧性、强度、耐磨性造成影响;
锅炉受热面布置合理,设置机械振打装置来解决废气的粉尘附着问题。
窑头采用立式双压AQC锅炉,采用立式自然循环,带有两个汽包;
烟气