法兰盘加工的回转工作台设计Word文件下载.docx
《法兰盘加工的回转工作台设计Word文件下载.docx》由会员分享,可在线阅读,更多相关《法兰盘加工的回转工作台设计Word文件下载.docx(19页珍藏版)》请在冰豆网上搜索。
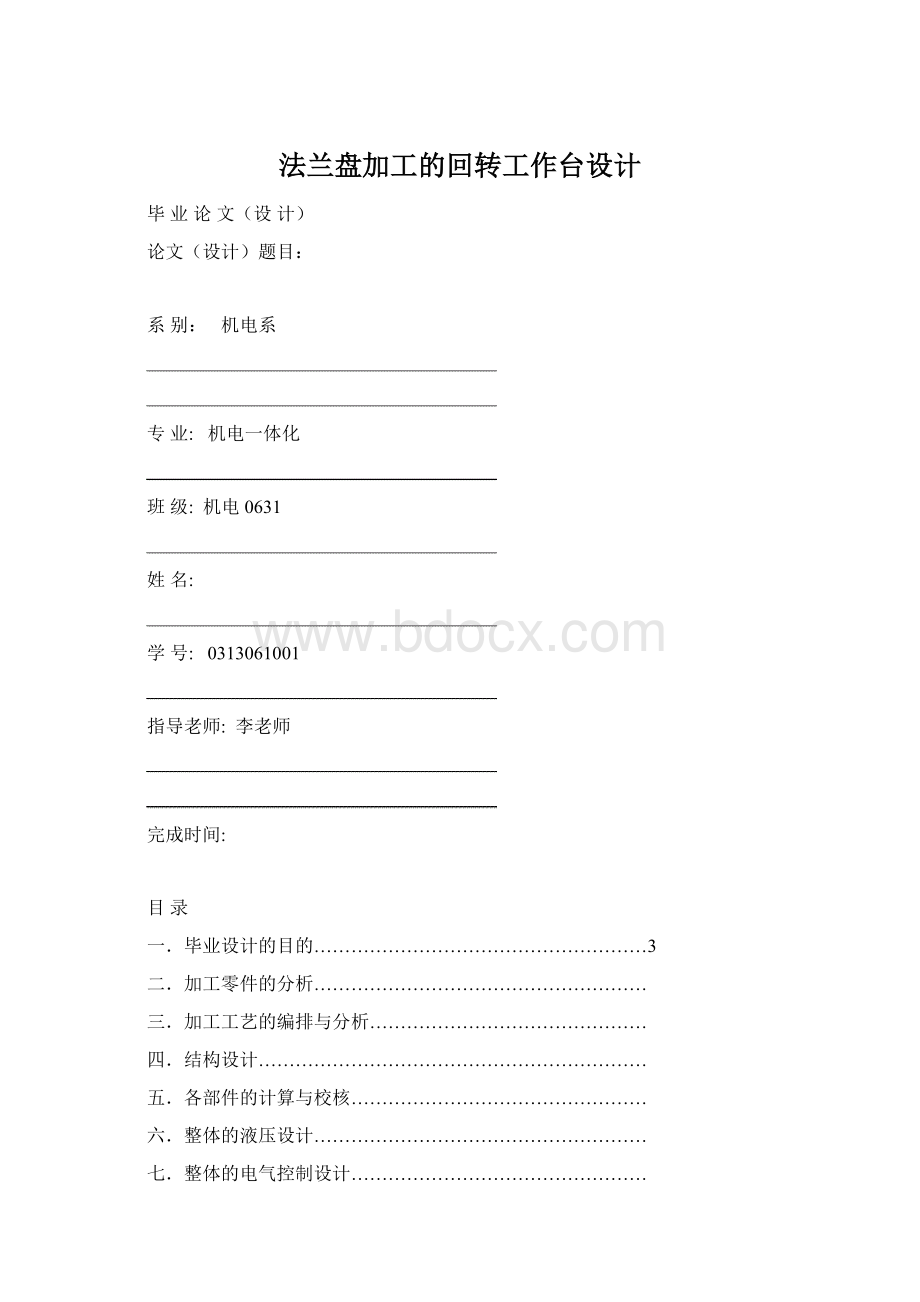
自己写的东西自己要懂
目录与正文的内容不一样
自己多读几遍,再叫别人读读,然后发给我
一.毕业设计的目的
毕业设计是学生综合运用所学过的基本理论,基本知识与基本技能去解决专业范围内的工程技术问题而进行的一次基本训练,其主目的:
(1)培养学生综合分析的解决本专业的一般工程技术问题的独立工作能力,拓宽和深化学过的知识
(2)培养学生树立正确的设计思想,设计构思和创新思维,掌握工程设计的一般程序规范和方法。
(3)培养学生正确使用技术资料,国家标准,有关手册图册等工具书,进行设计计算,数据处理,编写技术文件等方面的工作能力。
(4)培养学生进行调查研究,面向实际,面向生产,面向工作和工程技术人员学习的基本工作态度,工作作风和工作方法。
二.法兰盘加工的回转工作台设计
(一)加工零件的分析
如此法兰盘为一个式厂常用件,加工精度要求不太高,但年需求量较大。
因此,加工此法兰盘时,首先,需要考虑的问题就是加工的生产效率。
1、采用通用机床夹加工此法兰盘时,加工的范围可以进行扩大,可以加工出一系列的法兰盘,但通用机床的调整时间较长,装央与拆卸工件的时间较工,使得法兰盘的加工效率无法进行提高。
2、专门化机床的工艺范围较窄,只能加工一尺寸范围内的某一类零件,完成某一种特定工序,但生产效率较通用的机床高。
3、专用机床的工艺范围最窄,通常只能完成某一特定零件的特定工序,但专用机床的加工效率是这三类机床中最高的。
因此专用机床较为适用了加工此类法兰盘。
4、组合机床作为专用机床中的一种与通用机床的专门化机床相比较。
(1)组合机床由70-90%的通用零部件组成,可以缩短设计和制造周期,而且在需要的时候,还可以部分或全部改装。
以组成适应新加工要求的设备就是说组合机床有重新改装的优越性,其通用零部件可以多次重复利用。
(2)组合机床是按具体加工对象专门设计的,中以按最佳工艺方案进行加工。
(3)在加工零件时,组合机床可以同时从几个方向采用多把刀具对几个工件进行加工,是实现集中工序,提高生产效率的最好途径,这也正是加工法兰盘所需要的。
(4)组合机床是在工件一次装夹下用的轴实现多孔同时加工,有利保证各孔相互之间的精度要求,提高产品质量,减少了工件工序间的搬运,改善了劳动条件上,减少了占地面积。
(5)组合机床在多数的零部件是同类的通用部件简化了机床的维护和修理。
(6)组合机床的通用部件可以组织专门厂家集中生产。
有利于提高产品质量和技术水平,降低制造成本。
综合上面的分析,可得采用组合机床加工法兰盘,有利于提高法寺盘的加工精度和生产效率降低生产成本。
5、在采用组合机床的基础上,如果采用自动线或回转工作台来进行加工,将可以进一步提高法兰盘的加工效率,采用自动线或回转工作台,可以减少工件的搬运与装夹次数,减少了工人的劳动强度。
法兰盘以往工厂下料时,都采用气割或液压机但气割 时毛坯的精度比较低,加工时毛坯的切削余量比较大,使得加工成本与加工时间都有所提高。
且采用气割下料时,毛坯易形成氧化层从而给下一工序的加工带来困难。
采用液压机进行下料时,加工精度与加工效率都有较气割有较提高。
但毛坯的厚度提高,液压机的吨位也在提高,从而使得液压机的制造成本也随之提高。
因此,就法兰盘的下料有必要也设计一台专机,从而提高加工效率与降低加工成本。
下料专机的设计得法兰盘的外圆尺寸在下料时就可以得到保证,下料后的法兰盘外圆加工精度也达到了要求,从而法兰盘的外圆与A都无须再进行加工。
三.法兰盘加工工艺的编挑与分析
1.加工方法的选择
平放 工件不转
工件回转
竖放 工件不转
工件回转不利于采用随行夹具在自动线上加
平放时工件的装夹比较方便且所需的夹紧力也较低,但不利于底面的加工。
采用竖放工件不转,可以从两个方向对工件进行加工提高了生产效率,加工B面时,因为工件不转,可以以铣来代车。
由零件图上的精度要求与待加工表面,工件材料生产批量各加工面的加工方法待选。
①平面B 因为工件的加工是采用组合机床和回转工作台进行加工,无论回转工作台上采用固定夹具还是采用随行夹具,工件都无需进行旋转运动。
因而工件需要进行旋转运动的车削加工就无法使用了,可选择刀具运动工件不动的加工方法,刨削加工或铰削加工,蚀削加工主要用于挟长表面的加工,这样才能体现出刨削加工的加工效率,而加工的法兰盘为一个圆柱表面,所以采用铁削比较好B面的加工尺寸不是太大的,可以采用端铁进行加工来提高加工效率。
B面的加工精度要求不是太高铁削就能达到,因而无需再考虑精加工的磨削加工,以免提高工件的加工成本。
②内孔的加工方法可选、钻扩、铰、磨
因为法兰盘的内孔比较大,为了节约材料,采用套料的方法来进行下料,以便内孔的冲压件用于小尺寸法兰盘加工。
由于待加工内孔的孔径较大,钻削是用于小钻径加工的,孔径较大时铰刀的制造带来了困难,制造成本大幅度的提高。
通常钻、扩、铰用于φ80以内的内孔加工的精度较高,工件内孔的精度较低,采用磨削加工将会提高成本,且磨削加工时多数需要工件进行旋转。
镗削通常用于尺寸较大且精度要求较高的孔,特别是分布在不同表面上,孔距和位置精度要求很严的内孔采用镗加工。
③小孔
钻床一般用于加工直径不大,精度要求较低的孔,小孔最理想的加工方法是采用多轴钻一次性将其加工出来,这样既提高了加工效率了,又保证了小孔之间的相互位置精度小孔采用钻削加工
2、加为法兰盘中的A面与外圆无须加工,因而首先考虑以这两个面进行定位夹紧
加工工艺方案一
①下料,外圆φ200,厚度为15mm的毛坯
②以φ200与A面为基准进行装夹,加工的基准为φ200的仆圆中心线。
③镗削φX的内孔
④倒角φX的B面0.5×
45°
与B面外圆的0.5×
。
⑤铣削B面
⑥钻削X-φX的孔
⑦倒X-φX的孔的1×
的角。
⑧倒φX的A面的0.5×
加工工艺方案二
①下料:
外圆为φ200,内孔为φX,厚度为15mm的毛坯
②以φ200与A面为基准进行装夹
③铣削B面
④鎲削φX的内孔
⑤倒角φX的B面上0.5×
⑥钻削X-φX的孔倒角
⑦倒角φX的A面45×
的角
3、工艺方案的分析
以φ200的外圆与A面为基准,进行加工,可以一次性将法兰盘的设计基准为φ200外圆的中心孔线,这样既保证了加工基准与设计基准的统一又保证加工基准的重合。
从而使得法兰盘的加工精度有了提高。
保证了各个加工表面的位置精度,而且大大简化了夹具的设计和制造工作,缩短了生产准备时间。
由于工件的两端面A、B都 有位置要进行加工,因为工件只进行一次性夹紧,为了保证基准的统一与基问候语的重合,因而必须对工件进行两面加工,则回转了工作台,要采用内外圈都必须安排组合机床,如果在组合机床的加转工作台上安排一个回转结构,这样就可以减小回转工作台的结构。
为了减少加转的次数,加工完一个面的全部加工工序后再进行转位再加工另一个面的全部工序,同时采用工序集中的原则。
工序集中的优点
①减少了设备的数量,减少了操作工人和生产面积
②减少了工序数目,减少了运输工作量,简化了生产计划工作缩短了生产周期
③减少了工件的装夹次数,不仅有利于提高生产率,而且由于在一次装夹下加工了许多表面也易于保证这些表面间的位置精度。
因为多一个工序就要多出一个组合机床,而且回转工作台的回转结构也要增大。
B面需加工的
B面的铣削,内也0.5×
的倒角,B面外圆的0.5×
的倒角。
A面需加工
X-φX的1×
的倒
X×
φX与φX的内孔,两个面都可以加工。
由于采用工序集中的原则,将φX的内孔镗削安排在B面进行加工,同时将内孔的B面0.5×
的倒角与B面φ200的外圆的0.5×
的倒角与镗孔的工序安排在一起。
φX的钻孔安排在B面进行加工,采用复合钻将X×
X的内孔的1×
的倒角安排在一个工序中,这样B面的加工工序为铣与镗
A面的加工工序为,钻与倒角
将铣削加工安排在镗加工之前,这样既可以提高镗削加工开始时的受力平稳进,又可以减少镗削加工的工和行程。
钻削加工时产生的内应力要较倒角时产生的内应力大,从而将钻削加工安排在倒角的前面。
为了安排工件与拆卸工件的方便,在倒角的后面需要再安排一个回转机构,使得夹具在回到装卸工位时,依然是安排位置。
工艺方案
1铣削B面到t=14mm
2、镗内孔到φX,同时倒φX的0.5×
B面角倒φ200的B面角0.5×
3、转位将A面转至回转工作台的外面
4、钻X-φX的孔倒是1×
的倒角
5、倒φX的0.5×
的A面角
6、拆卸工件
四、结构设计
由上面的工序分析可知,回转工作台北须有5个工位,装卸工位、铣削工位、镗削工位、钻削工位、倒角工位
1、组合机床对分度回转工作台;
①提高分度定位精度和定位刚度,以提高分度回转工作台组合机床的加工精度
②缩短分度回转时间,以提高机床加工效率,但是要求分度运动平稳以保证必要的回转精度。
③要求定位机构磨损小,以便长期地保持分度回转工作台的精度
④结构简单可靠、调整维修方便,经济合理。
2、分度回转工作台的动作
定位销的拔出——工作台台面松开——工作台台面抬起——工作台台面回转,分度并到位——定位销插八并定位——工作台台面落下——工作台台面被夹紧;
回转工作台必须有两个动作
(1)上下升降运动
(2)回转运动
能够实现上下直线运动的机构
(1)曲柄滑块机构
(2)液压缸机构(3)凸轮机构等
曲柄滑块机构、结构简单运动平稳,成本低,但曲柄滑块机构的功率较小,而工作台台面的升降运动所需功率较大。
凸轮机构的优点只要适当地设计凸轮之廓曲线,使可使从动件获得任意预期的运动规律,且机构比较简单紧凑,易于综合,但凸轮的制造比较复杂,制造成本较高,随着计算机的出现,凸轮制造变得比较简单,但凸轮之廓面与动件之间为点中缕接触,故易于磨损,因此凸轮机构通常用于传力不大的场合。
采用液压缸的机构,便于实现电气控制与自动化控制,工作平稳,换向冲击小,便于实现频繁换向液压元件易于实现系列化,标准化和通用化,便于设计和制造。
能够实现间歇回转的机构
(1)棘轮棘机构
(2)槽轮机构
(3)不完全齿轮机构
不完全齿轮机构的加工工艺较复杂,且从动轮在运动开始和修正时有较大的冲击。
采用槽轮机构若要使槽轮转一周,拔盘要转1-5周,拔盘的转动,需要一个原动机,若采用电动机,电动机的最低转速为750r/min,要想将这样的转速降到需要的低时需要一个庞大的减速机构,从而增加了回转工作台的结构尺寸。
棘轮机构结构简单,工作可靠,棘轮转角的大小可以进行有级调节,常用于低速轻载下实现间歇运动工作台面,只需要克服少量的磨擦力就中以进行回转了。
棘轮棘爪回转运动,采用齿轮机构来带动,为了减小回转工作台的结构,不采用电动来作为原动机,否则需要增加一个减速机构。
在相同功率的情况下,液压传动能量转换元件的体积较小,重量较轻,因而采用液压缸的直线运动来带动齿条运动,从而来带动齿轮的运动。
3、工作台的分度与定位
(1)小型机械分度回转工作台
1机械分度回转机构的结构
②小型机械分度回转工作台的传动
分度回转工作台的动作,是装有蜗轮的同一根轴上的三个凸轮强制控制的
凸轮1——控制是位销动作,并有曲柄销拔动工作台台面转动
凸轮2——控制工作台面抬起和落下
凸轮3——控制夹紧和松开工作台台面的凸轮
凸轮的大小与形状,有转位的多少,时间的长短等因素来决定。
这种工作台可根据生产节拍的要求,通过要换电动机轴上的皮带轮来改变转位时间。
这种工作台只用一个电动机实再分度、定位抬起落下和夹紧松开等动作,动作可靠 ,结构紧凑,但是定位销容易磨损,磨损后影响分度精度。
(2)反靠定位分度回转工作台的结构
①反靠定位机构采用面定位,消除了间隙,定位精度有所提高较圆柱销定相比,并增加了工作中面的夹紧机构,工作台刚性较好,这种系列回转工作台具有液压和机械两种驱动方式,回转工作台具有液压机械两种驱动方式,回转工作台部分是通用的,只是把传动装置部分设计成独立设计部件,分为液压传动装置和机械传动装置。
这系列分度回转工作台的动作循环
动力部件原位——工作台花盘1抬起,自锁销脱开——花盘回转——花盘反靠——工作台夹紧,自锁销插上——动力部件工作循环
②反靠定位分度回转工作台的结构
这个系列回转工作台部分和回转装置部分组成。
回转工作台部分,包括花盘,工作台体、定位机构抬起头夹紧装置和自锁装置等部分,工作台的定位块是浮动的,当花盘回转时,花盘上的定位销端部的斜面压下定位块,定位销转过定位块后,由弹簧将定位块抬起,花盘反靠。
定位销反靠在定位块上,在浮动定位块2的后面两边有固定挡块。
为了保证分度回转,工作台的分度定位精度,反靠定位完成讯号必须在反靠讯号开关和时间继电器延时终了,同时有讯号发出,并且必须在工作台夹紧完成后发出讯号。
电动机的慢速饭靠回转才能停止。
回转工作台的自锁装置,可保证在加工过程中定位位置不变,提高了回转方向的刚性。
③反靠定位分度回转工作台的缺点。
分度精度只能达到±
7”精度再提高有困难,传动机构等都在底座里。
敞开性较差。
使工作台的调整维修较为困难,如工作台反靠完毕的讯号,由微动开关和压力继电器联合发出。
微动开关易出故障,调整不便,另在反靠时产生撞击。
尤其是机械反靠时撞击更明显。
(3)盘定位分度回转工作台
1齿盘的形状与结构如图所示。
共有两个齿盘,将上齿盘固定在回转工作台上,将下齿盘固定在工作台的底座上,当回转工作台上升时,上下齿盘分开。
工作台开始回转,回转结束后工作台下降,上下齿盘开始噬合。
定位齿盘上齿数的多少和齿形的大小由转位次数与工作台的大小和工作台的受力来决定。
2齿盘定位与分度回转工作台的特点
分度精度高,分度精度达到±
3”,能用于加工高精度的工件
刚性较好,由于工作台采用了齿盘定位且具有夹紧机构工作台的承载能力和抗震性都较好。
分度节拍时间较短
结构简单,维修方便,新系列回转工作台的零件少。
而且所需的电气元件和液压元件数量也少。
对管路的安装,行程开关的性能都予以考虑,调整维修比较方便。
但齿盘要求精度高,制造比较困难,随科技的发展,计算机的广泛应用,数控机床等先进和高科技技术的应用与出现这种制造困难已不再是困难了。
4、转位机构的设计
1采用不完全齿轮机构。
将随行夹具的轴上装一个小齿轮,在大立柱上装一个大的不完全齿轮。
因为回转工作台上共有5个工位,则随行夹具在绕立柱72。
后要转动180。
且分度要求精确。
在大立柱上装的不完全齿轮的轮齿安排在72。
以内且不完全齿轮的轮齿刚好是小齿轮数的一半。
这样就可以保证夹具在镗完φX的内孔以后,工作台上升旋转72。
后转动180。
保证钻孔的确定位置。
采用不完全齿轮进行转位,精度较高,转动平稳,但在刚噬合时和分开时容易产生冲击和撞击且在其他的几个工序中没有自锁机构。
如果受到外力时就有可能产生转动,而使随行夹具与组合机床的相对位置不衡定,从而影响零件的加工。
甚至使零件的加工无法进行下去。
2采用槽轮机构转位
为了是得随行夹具在其他的工序中有一个准确的加工位置,在转位机构此处删减NNNNNNNNNNNNNNNN字
需要整套设计请联系q:
99872184。
液压缸的流量为:
⑦水平液压缸的选取
立柆上的套与立柱是采用的间隙配合。
在转动时它们之间的摩擦力很小,从而齿车条的传动也就很小,液压缸所承受的水平推务也就很小。
一个轮齿的一齿高为
h=ha+hf=9mm
参考垂直液压缸的进取可得:
D2取80mm
2、根据各部件的计算,可得出各部件的尺寸,结合现先前的结构设计,作出总类图(见装配图)
3、回转分度工作台的动作顺序
①垂直液压缸上升,使得齿盘分开,工作台面上升,随行夹具下的上下齿盘也全都分开,随行夹具随工作台面一起上升。
②水平液压缸动作,使得齿条运动,从而带动齿轮运动,在为棘爪是用螺钉固定在齿轮上的所以棘爪随齿轮一起旋转,从而带动棘轮旋转而棘轮又是用螺钉固定在立柱上的套上的,套也随着旋转套与工作台面固定在一起的工作台面也就齿条的前进而产生旋转,随行夹具下面的槽轮与止锁弧相啮合时就使得随行夹具不产生旋转当随行夹具运动到镗与这间和倒角与拆卸工件工花之间时,因为凹槽与曲柄上的拔销作和使得槽轮产生旋转,槽轮与随行夹具之间采用了键联接使得随行具产生了旋转从而转动180°
③垂直液压缸下降,工作台台面因为自重也随着液压缸的下降一起下降。
上下齿盘啮合、夹紧,如果工作台台面旋转时存在着一定的分度误盖上下齿盘相啮合时会自动进行调整,随行夹具如随着工作台面一起下降小齿盘也相互啮合,如果槽轮机构转位时存在着一定的转位误差时,齿盘啮合时也会自动进行调整。
齿条退回,从而劳动齿轮回转,棘爪也随着齿轮一起回转,由于棘棘轮上的凸轮曲线弧与棘不后面的弹簧作用棘爪在曲线弧上滑动棘轮不动。
液压缸退回原位。
六、总体液压设计
选用了哪些液压元件,型号规格,怎样选,为什么?
为了使工作平稳,操纵简单,便于实现自动化,除拆卸工位外的其他四个工位都采用液压滑台作为组合机床实现进给运动的部件为了防止因为钻孔时产生的轴向力太大而夹具的夹紧力不足从而产生工件的偏科,使得加工无法进行,增加一个辅助支承来,增加轴而刚性。
为了使辅助支承运动平稳,冲击小,同时也为了便于实现自动化,决定辅助支承也采用液压控制。
1、各个液压缸的动作顺序:
①垂直液压缸上升——②水平液压缸前进
③垂直液压缸下降——④水平液压缸退回
⑤辅助支承液压缸上前顶工件
⑥各个组合机床的滑压台快进。
⑦各个组合机床的滑压台工进。
⑧各个组合机床的滑压台快退,钻孔专机快退时辅助支承液压缸快退。
2、各个典型回路的参考
1为了防止立式液压缸及材工作部件在悬空停止期间因自而自行不滑,或在下行运动中由于自重而造成失控超座的不稳定运动,设置平稳回路平衡回路中若无节流阀,运动部件下行时会因自重而超座运动,缸上腔出现其真空致使液控单向阀关闭,待压力重建后才能再扩开,这会造成下行运动时断时续和强烈振动的现象。
②垂直液压缸与水平液压缸之间的动作是顺序动作为了保证这两个液压之间准确的顺充动作有必要设计一顺充动作回路。
顺序动作回路有行程控制与压力控制
压力控制回路,动作灵敏、安装直接方便,但可靠性不高。
当运动部件卡住或压力较大脉动时误动作不可避免,位置精度低,且只宜用于液压缸数目不多负载变化不大的系统中。
行程控制的顺序回路,换接位置准确,动作可靠,特别是行程阀控制回路换节平稳,常用于对位置精度要求较高处。
但行程阀需布置在缸附近,改变动作顺序较困难,而行程开关控制的回路只需要改变变电气线路的可改变顺序。
故应用较广泛。
1YA得电,缸A向右运动能动行程开关2使3YA得电,使缸A向左运动。
触动行程开关1使得4YA得电,使缸B向左运动。
2由于切削时切削为变化教小,而且是正负载。
为了保证切削过程速度稳定,决定采用调速阀进行节流调速,回路加背压阀。
动力滑台在工作进行时是高压小流量供油,而快速行程时则是低压大流量供油。
因此可选用双联叶泵供油回路或变量泵供油贿赂。
但由于四个滑台在工作时候要采用互不干涉的贿赂,所以只能选用双联叶泵供油贿赂。
为了使四个液压控制系统工作时互不干涉。
小流量高压油泵的高压油分别经一流阀进入各自系统,大流量泵低压油分别经一单向阀进入各自系统。
机床快进时,采用液压缸差动连接方式,使其快进快迅速基本相同,同时滑台停止转为快进,工进转快退等换向中,速度变化大,为了保证换向平稳,采和有三位五通电液换阀的换几向回烙,为了保证机床调整时可停在任意位置上,采用中位机能为“O”型的电夜换向阀,快时时,液压缸的油路差动接,进油咱与回油路串通。
且又不允许背压阀流回油路与回油路串通。
且又不允许源北压阀流回油箱,转为工进后,进油路与回油路则要隔开,回油源北压阀流回油箱,所以要在换向阀处把进,回路连通的油路上增加一单向阀。
在背压阀后增加一液控顺序阀,其控制油与进入换向阀的压力油接通。
于是快进时液压缸的回油被液控顺序阀切断,快进时为低压,引阀打不开,只有经单向阀与进油汇合。
转工进后,由于调其阀的作用,系统压力升高液控顺序阀打开,液压缸的回油可经背压阀回油箱,同时单向阀将四油路切断,确保系统形成或高压,以使液压缸正常工作。
3、结合各个液压缸的动作顺序与典型回路,整体设计液压原理图,并作出整体液压原理图(见图纸)
七.电所控制总体设计
组合机床 电气控制是按照预定的工作循环高设计,由若个电气控制住不节构成的顺充控制系统。
该组合是法兰盘零件加工的高效专用机床,所以机床的工作循环是固定的。
循环时间在数分钟采用继电一接触控制一般就能够满足机床对电气控制的寿命和可靠性的要求。
1、组合机床基本环节的控制电路
一个电气控制系统是由若干个基本控制环节构成,组合机床电气控制系统也是如此
(1)多电机同时起动的控制线路
组合机床通常是多个动力部件同时工作,而且对这些部件需要单独调整,这样就歌如潮多台电机同时起动并能单独调整如上图。
上图的工作原理:
合上自动开关QF1-QF3,触点QF1-QF3,闭合接起动按钮SB2,接触器KM1-KM2同时接电并互锁,三台电机同时起动旋转。
按停止按钮SB1 KM1-KM3断电,三台电机同时停转。
钮子开关SA1-S3是分别对KM1-KM3所控制的动力部件作单独调整用的,如对KM,所控制的动力部件要作单独调整而不需KM2、KM3所控制的动力部件动作时,可扳动SA1、SA3,使其动断触点打开,动合触点闭合,按SB2则只有KM1接电自锁,使KM1所控制的动力部件动作,从而达到单独调整的目的按上进方法可相应调整KM1和KM3所控制的动力部件。
(2)两滑台退回原位同时切断主轴电机的线路。
有此组合机床在加工中,当辅助时间较长时,为了节省电力和装卸工件的安全,在两主轴加工时不多的情况下,需要同时停止。
上图的工作原理,按起动按钮SB,接触器KM1和KM2通过中间继电器KA的动断触点按点并互锁左右主轴电机起动旋转。
当两滑台分别向前离开原位,SQ1-SQ4均放开,放SQ3、SQ4的动断触点复位闭合,从而接通KA的动断触点打开,为加工完滑台退回原位切断KM1KM2作准备,同时SQ、SQ2的动断触点闭合,继续为KM1、KM2线圈供电,当机床加工完成后两滑台各自快速退倒原闰,分别下SQ1-SQ2使KM1、KM2断电并随即切断KA,左右主轴电机立即停转。
2、整体电所控制线路的设计
参考各个典型电路,进行综合设计,再根据液压原理图,和液压原理图的动作表,进行整体电所控制线路的设计,设计线路见第六张图
3、整体电气控制线路的顺序动作分析