第二章 风烟系统Word文件下载.docx
《第二章 风烟系统Word文件下载.docx》由会员分享,可在线阅读,更多相关《第二章 风烟系统Word文件下载.docx(22页珍藏版)》请在冰豆网上搜索。
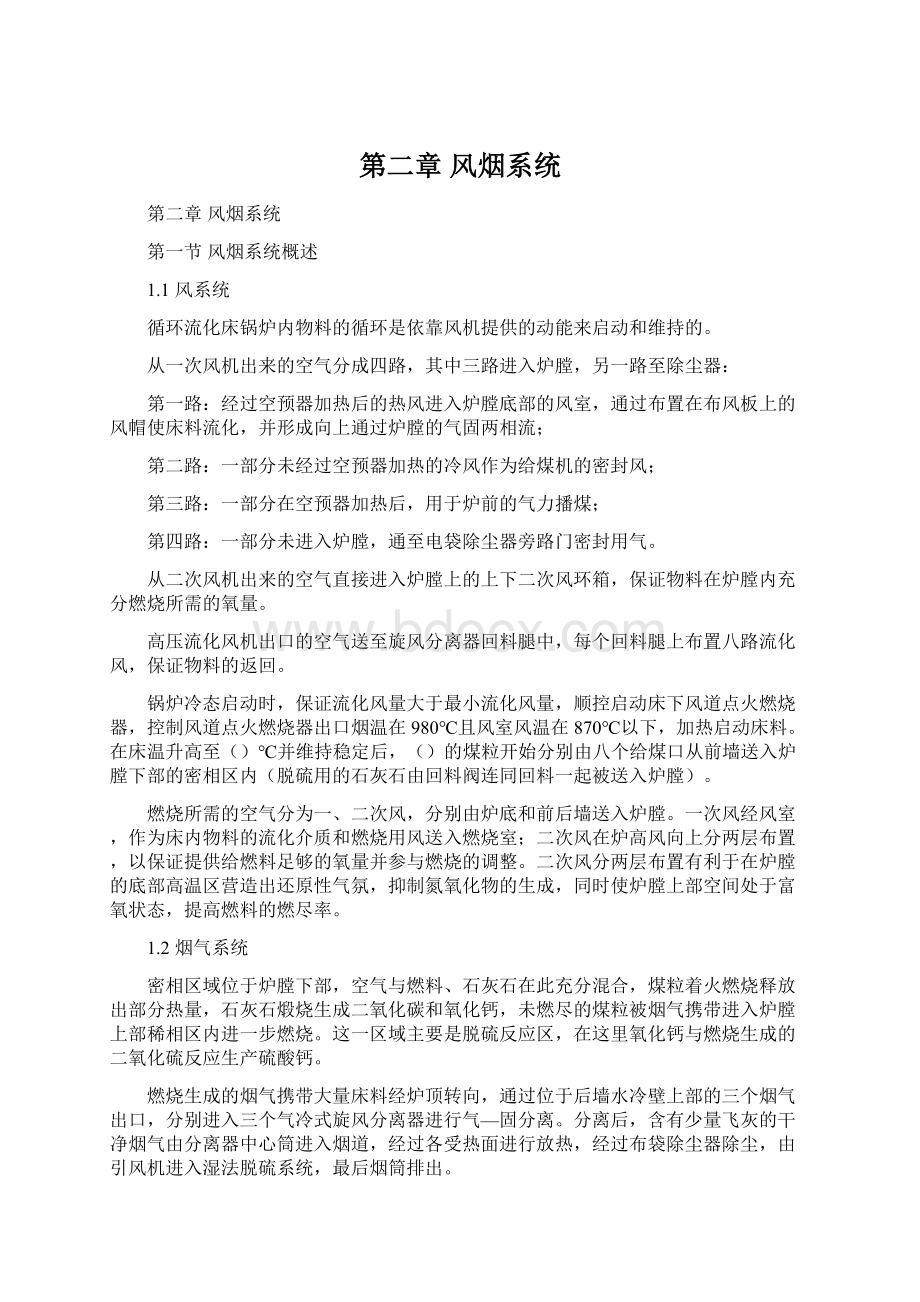
升力原理(如图2-1):
图2-1气体升力产生原理
理想流体绕孤立叶型流动时,在叶型上会产生一个与流动速度相垂直的力即升力。
对升力的产生可做如下解释:
流体绕叶型流动时,由于叶型本身是不对称的形体,在叶型上面流动的断面减小,流型受到挤压,流线变密,流速增加。
而叶型的下面流动端面增大,流线不但不被挤压,反而扩张。
因而流线变疏,流速降低。
由能量方程可知,叶型上面由于流速增加,压力必然降低,而叶型下面因为流速降低,引起了压力升高。
这样一来,作用在叶型上、下两个表面上的压力不相等,因而产生一个自下而上的作用力——升力。
轴流风机就是利用这种升力进行工作的。
轴流风机的每一个叶片截面的形状就是一个孤立的叶型。
当轴流风机的叶轮在原动机的驱动下旋转时,叶片在流体中运动,就给流体一个作用力,这个力与叶型的升力大小相等,方向相反。
在这个升力的作用下,流体沿着泵轴的方向,从进口流向出口。
2.3离心风机和轴流风机的特性比较
2.3.1风机运行效率
两种类型风机在设计负荷时的效率相差不大,轴流风机效率最高达90%,机翼型叶片离心风机效率可达92.8%。
但是,当机组带低负荷时,动叶可调轴流风机的效率要比具有入口导向装置的离心风机高许多。
2.3.2风机对烟风道系统风量压头变化的适应性
目前烟风道系统的阻力计算还不能做的很精确,尤其是锅炉烟道侧运行后的实际阻力与计算值误差较大。
在实际运行中,由于燃料品种的变化也会引起所需要风机风量和压头的变化,这时对于离心风机来说,在设计时要选择合适的风机来适应上述各种变化是困难的。
如果考虑了上述几种流量和压头变化的可能性,使离心式风机的余量选得过大,会造成在正常运行时达不到额定出力。
而轴流风机对风量、风压的适应性很大,尤其是采用动叶可调的轴流风机时,可以用关小或开大动叶的角度来适应变化的工况,而对风机的效率影响很小。
2.3.3机械特性
轴流风机的总重量约为离心风机重量的60-70%。
轴流风机有低的飞轮效应值,这是由于轴流风机允许采用较高的转速和较高的流量系数,所以在相同的风量、风压参数下,轴流风机的转子重量较轻,即飞轮效应值较小,使得轴流风机的启动力矩远低于离心风机的启动力矩。
一般,轴流风机的启动力矩只有离心风机启动力矩的14.2-27.8%,显著地减少了电动机功率余量和对电动机启动特性的要求,降低了电动机的造价。
轴流风机转子重量较轻,但是结构上比离心风机转子复杂的多,因此,大容量的两种类型风机价格(包括电动机)相差不多。
2.3.4运行可靠性
动叶可调轴流风机由于转子结构复杂,转速高,转动部件多,对材料和制造精度要求高,其运行可靠性比离心风机稍差一些,但经多年来的改进,可靠性大为提高。
2.3.5体型尺寸
轴流风机比离心风机的结构紧凑,外型尺寸小,占据空间也少(占地面积较离心风机少30%),而且轴流风机重量轻,飞轮效应小,因此布置起来比较灵活,它可以布置在地面基础上,也可以布置在钢架结构顶上,可以卧式布置,也可以立式布置。
2.3.6噪声
轴流风机产生的噪声强度比离心风机要高,因为轴流风机的叶片数往往比离心风机多两倍以上,转速也比离心风机高,因此轴流风机的噪声发生在较高的频率。
然而,把噪声消减到允许的噪声标准,在消声器上所花费的投资几乎相等。
第三节液力耦合器
考虑风机调速节能的需要,我厂在一、二次风机上加装液力偶合器。
液力偶合器采用大连创思福产品。
该设备包括液偶本体、液力偶合器油系统两部分,油系统需同时给电机轴承供油。
联轴器采用无锡创明蛇形弹簧联轴器JS系列,转速测量系统采用上海金积电子的产品,执行器采用SIPOS品牌,压力开关、差压开关、温度开关、流量开关、过程分析仪表等设备采用SOR产品。
液力偶合器采用滑动轴承。
3.1液力耦合器的工作原理
3.1.1液力传动原理:
液力偶合器相当于离心泵与涡轮机的组合。
当动力机通过液力偶合器输入轴驱动泵轮旋转时,充填在工作腔中的工作液体在离心力的作用下,沿泵轮叶片流道由泵轮入口向外缘流动,同时,液体的动量矩产生增量,即偶合器的泵轮将机械能转化为了液体动能。
当工作液体由泵轮冲向对面的涡轮时,工作液体便沿涡轮叶片流道做向心流动,同时释放液体动能,转化为涡轮的机械能,使涡轮旋转并带动工作机械做功。
就这样工作液体在偶合器腔内周而复始地做螺旋环流运动,输出与输入在没有任何直接机械连接的情况下,仅靠液体动能,便柔性地联接在一起了。
3.1.2液力调速原理
液力偶合器传递动力的能力与其工作腔内的充液度(有效充液量与总充液量之比)成递增函数关系。
因此,改变液力偶合器腔内的充液度,便可以调节输出力矩和输出转速。
这种充液度的调节是依靠调节勺管的位置来实现的。
原理如下:
当液力偶合器工作时,套装在输入轴上驱动齿轮在输入轴带动下旋转,驱动从动齿轮带动油泵旋转,油泵将工作油从箱体吸出经冷却器冷却后进入导管壳中的进油室,并继而经泵轮入口进入工作腔。
与此同时,工作腔中的工作液体在做螺旋环流运动的同时,还通过泵轮的泄油孔进入外壳围成的导管腔并形成一个旋转油环。
旋转油环在静止的勺管处形成压头,工作液体便由勺管导出。
因此通过电动执行器操作导管的伸缩程度,便可以改变导管腔内的油环厚度。
由于导管腔与工作腔连通,所以也就改变了工作腔内的充液度,实现无级调速。
导管排出的油通过回油三通重新回到油箱。
由于勺头排油和油泵的进、出油口均与偶合器的转向有关,所以油泵转子与勺头安装方向要与偶合器转向相适应。
也就是说,第一,勺头开口方向必须迎着导管腔油环的旋转方向;
第二,油泵泵盖上箭头方向必须与电机转向相同。
3.1.3液力耦合器油系统
液力偶合器油系统主要包括润滑油循环和工作油循环。
工作油泵为离心泵,润滑油泵为齿轮泵。
润滑油由齿轮润滑油泵抽出后,经过冷却器和过滤器,进入润滑油母管,然后流向各轴承和齿轮组,还有一部分作为勺管控制阀的控制油。
在液力偶合器起动前、停机后和润滑油泵损坏时,由辅助润滑油泵提供润滑油。
工作油循环可分为一个开式循环和闭式循环。
在液偶内部泵轮、涡轮及旋转内套中的工作油经勺管和排油管进入工作油冷油器,冷却后的工作油进入控制阀,控制阀控制着联轴器进油量的多少,油由此进入泵轮、涡轮及旋转内套。
这部分连续工作的系统称为工作油闭式循环系统。
这种出油由勺管控制,进油由控制阀控制的系统就称为进出油控制系统。
开式循环由工作油泵、止回阀、节流孔板以及安全阀组成。
它的主要作用是向联轴器里补充油,或将多余的油通过安全阀排回油箱。
节流孔板连接工作油与润滑油管,起动时可以快速向联轴器充油。
现代大机组液力偶合器工作油量的调节都是靠联轴器的进油和出油两者综合作用,以达到快速升降转速的目的。
联轴器的进油由闭式循环控制阀开度决定,联轴器的出油由勺管位置决定。
勺管位置由控制油(来自润滑油)通过活塞带动,控制阀控制活塞腔室的进油和回油。
勺管上还设置有一反馈杠杆,当勺管移动到位后,反馈杠杆使控制阀关闭,于是勺管活塞腔室不再进油,系统平衡在一个新的转速点上
图2-2液力耦合器的基本结构
A、体式润滑系统B、变矩器C、D齿轮
1、泵轮2、涡轮3、导流叶片4、电液执行器5、工作油6、润滑油
7、工作油泵8、工作冷油器9、润滑油泵10、润滑油冷却器11、过滤器
12、外置润滑油13、辅助润滑油泵14、辅助润滑油泵电动门
图2-3液力耦合器工作原理图
3.2液力耦合器检测和控制项目(至少)
偶合器勺管控制(进口)
偶合器轴承温度检测、报警、联锁
偶合器勺管排油温度检测、报警、联锁
偶合器油泵排油压力检测、报警、联锁
油箱油位检测
工作油压力检测、报警、联锁
润滑油压力检测、报警、联锁
工作油/润滑油滤网差压检测及报警
工作油/润滑油冷却器出口油温检测、报警、联锁
第四节一次风机
1.型式:
双吸双支撑离心式、液力耦合器调速
2.数量:
每台炉两台
3.运行方式:
并联运行
4.风机旋转风向:
从电机一端正视,叶轮顺时针旋转,为右旋转风机,相反旋转,则为左旋转风机。
每台锅炉配置左右旋风机各一台。
5.风机进/出口角度:
45度/135度(暂定)
6.布置方式:
左右对称
7.安装地点:
室内布置
8.参数
表2-1一次风机设计参数
序号
工况/煤种
项目名称
设计煤种
TB工况
BMCR工况
50%BMCR
THA
1
风机入口流量(Nm3/h)
253689
230626
174627
220925
2
风机入口流量(m3/h)
302644
275131
208326
263558
3
风机入口静压升(Pa)
-660
-550
-400
-500
4
风机出口静压升(Pa)
21598
17999
12882
16948
5
风机全静压升(Pa)
22259
18549
13282
17448
图2-4双吸双支撑离心风机外观图
第五节二次风机
双吸双支撑离心式,液力偶合器调速
每台炉配置两台,本期工程共4台
两台风机并联运行
4.风机旋转方向:
从电动机一端正视,叶轮顺时针旋转,为右旋转风机。
相反旋转,则为左旋转风机。
每台锅炉配置左、右旋转风机各1台。
45/135(暂定,待设计院书面确认进出口角度后风机才可投料加工)
8.二次风机参数﹑容量/能力(暂定)
表2-2二次风机设计参数
312722
284293
224404
376390.4
341588.3
-795
-636
16659
13327
17454
13963
13370
第六节引风机
6.1动叶可调双级轴流式风机结构
(a)整体结构示意图;
(b)扩压器沿导轨移动
1、进气箱;
2、集流器;
3、前导叶;
4、动叶片;
5、机壳;
6、后导叶;
7、扩压器;
8、扩压器支撑叶片;
9、内芯筒;
10、轴承箱;
11、主轴;
12、导轨
图2-5轴流风机
动叶可调双级轴流风机如图2-5,由进气室、集流器、两级叶轮、导叶、扩压器、动叶调节机构等构成。
两级叶轮布置在轴承室两端,风机转子与电机转子之间由一根空心轴连接,在电机转子和风机转子侧分别有一个挠性联轴器,风机轴承箱下部通过几根筋板与外壳的下半部相连,风机及电机由四个支承轴承和一个推力轴承支承(见图2-6)。
该类型风机与一般轴流风机和离心风机的最大差别是其具有两级叶轮,在长期运行中,两级叶轮均会因磨损引起质量不平衡,造成风机振动超标。
图2-6引风机轴系支撑简图
6.2设备规范
动叶可调双级轴流式
两台风机并联运行或单台运行
4.风机调节方式:
动叶调节。
5.布置方式:
水平对称布置,垂直进风,水平出风。
6.安装地点:
室外
7.引风机参数﹑容量/能力(暂定)
表2-3引风机设计参数
项目
THA工况
煤质
1144684
1002665
897521
风机入口流量(mN3/h)
747890
646073
557900
引风机与增压风机合并后全压(Pa)
9731
8109
7697
入口烟气温度(℃)
138.5
123.5
烟气含湿量(g/kg)
49.26
6
收到基全硫St.ar(%)
1.37
7
露点(℃)
102.38
8
入口烟气密度经负压修正后(kg/m3)
0.736
0.764
9
入口粉尘含量mg/Nm3)
≤200
10
引风机入口压力(Pa)
-7331
-6109
-5697
11
引风机出口压力(Pa)
2400
2000
第七节动叶可调轴流风机动叶调节原理(TLT结构)
轴流送风机利用动叶安装角的变化,使风机的性能曲线移位。
不同的动叶安装角对应的性能曲线与风道性能曲线,可以得出一系列的工作点。
若需要流量及压头增大,只需增大动叶安装角;
反之只需减少动叶安装角。
轴流风机采用动叶调节,调节效率高,同时能使调节后的风机处于高效率区内工作。
动叶调节还可以避免轴流风机在小流量工况下落在不稳定工况区内。
但轴流风机动叶调节使风机结构复杂,调节装置要求较高,制造精度要求亦高。
动叶安装角的改变是通过动叶调节机构来执行的,它包括液压调节装置和传动机构(见图2-7)。
液压缸内的活塞由轴套及活塞轴的凸肩被轴向定位的,液压缸可以在活塞上左右移动,但活塞不能产生轴向移动。
为了防止液压缸在左、右移动时通过活塞与液压缸间隙的泄漏,活塞上还装置有两列带槽密封圈。
当叶轮旋转时,液压缸与叶轮同步旋转,而活塞由于护罩与活塞轴的旋转亦作旋转运动。
所以风机稳定在某工况下工作时,活塞与液压缸无相对运动。
图2-7轴流风机动叶调节机构示意图
活塞轴的另一端装有控制轴,叶轮旋转时控制轴静止不动,但当液压缸左右移动时会带动控制轴一起移动。
叶片装在叶柄的外端,每个叶片用6个螺栓固定在叶柄上,叶柄由叶柄轴承支撑,平衡块与叶片成一规定的角度装设,二者位移量不同,平衡块用于平衡离心力,使叶片在运转中成为可调。
动叶调节机构被叶轮及护罩所包围,这样工作安全,避免脏物落入调节机构,使之动作灵活或不卡涩。
当轴流送风机在某工况下稳定工作时,动叶片也在相应某一安装角下运转,那么伺服阀将油道①与②的油孔堵住(如图2-8),活塞左右两侧的工作油压不变,动叶安装角自然固定不变。
图2-8调节机构的伺服阀
当锅炉工况变化需要减小调节风量时,电信号传至伺服马达使控制轴发生旋转,控制轴的旋转带动拉杆向右移动。
此时由于液压缸只随叶轮作旋转运动,而调节杆(定位轴)及与之相连的齿条是静止不动的。
于是齿套是以B点为支点,带动与伺服阀相连的齿条往右移动,使压力油口与油道②接通,回油口与油道①接通。
压力油从油道②不断进入活塞右侧的液压缸容积内,使液压缸不断向右移动。
与此同时活塞左侧的液压缸容积内的工作油从油道①通过回油孔返回油箱。
由于液压缸与叶轮上每个动叶片的调节杆相连,当液压缸向右移动时,动叶的安装角减小,轴流送风机输送风量和压头也随之降低。
当液压缸向右移动时,调节杆(定位轴)亦一起往右移动,但由于控制轴拉杆不动,所以齿套以A为支点,使伺服阀上齿条往左移动,从而使伺服阀将油道①与②的油孔堵住,则液压缸处在新工作位置下(即调节后动叶角度)不再移动,动叶片处在关小的新状态下工作。
这就是反馈过程。
在反馈过程中,定位轴带动指示轴旋转,使它将动叶关小的角度显示出来。
若锅炉的负荷增大,需要增大动叶角度,伺服马达使控制轴发生旋转,于是控制轴上拉杆以定位轴上齿条为支点,将齿套向左移动,与之啮合齿条(伺服阀上齿条)也向左移动,使压力油口与油道①接通,回油口与油道②接通。
压力油从油道①进入活塞的左侧的液压缸容积内,使液压缸不断向左移动,而与此同时活塞右侧的液压缸容积内的工作油从油道②通过回油孔返回油箱。
此时动叶片安装角增大、锅炉通风量和压头也随之增大。
当液压缸向左移动时,定位轴也一起往左移动。
以齿套中A为支点,使伺服阀的齿条往右移动,直至伺服阀将油道①与②的油孔堵住为止,动叶在新的安装角下稳定工作
第八节轴流风机的失速与喘振
8.1喘振
轴流式风机采用调整动叶片安装角度来改变送、引风机的流量,特点是在较大的流量范围内可以保持较高的效率。
当安装角一定时,风机的流量越小,功耗越大,从原理上不允许空载启动风机。
大容量轴流风机在运行中还应避免风机的喘振。
喘振是流体机械及其管道中介质的周期吸入排出产生的机械振动。
风机发生喘振时,气压、流量急剧波动,并产生气流撞击使风机发生强烈的振动,噪声增大。
风机的容量与压头越大,则喘振时危害也越大。
图2-9为具有“驼峰”形Q-H性能曲线的轴流风机,当工作点在曲线K点左侧,即风机处于不稳定工作区,而且该风机又与大容量的风道系统相连接。
如风机原来的工作点为A,输出流量QA、风压HA。
若风机负荷增加,则工作点从A点移至B点,此时风机的工作仍然是稳定的。
当外界需要的流量减少为QE时,工作点向E点移动;
流量进一步减少至QK,对应的风机工作点为K点。
假如外界需要流量瞬时降低到Q<
QK时,这时风机所产生的最大压头也随之下降(见图2-5),因为风道系统容量较大,在这一瞬间流量的减少并没有使风道的压力下降,而仍为HK,因此风道中的压力瞬时大于风机所产生的压头,气流反方向倒流,工作点由K点迅速移至C点。
但是气流的倒流使风道系统的风量减少,风道中的压力迅速下降,工作点沿着CD线迅速下降至Q=0的D点,此时风机的供风量为零。
由于风机在继续运转,所以当风道中的压力降低到相应的D点时,风机又开始送出气流。
为了与风道中的压力平衡,风机的工作点又从D点跳至相应的压头的F点。
只要外界流量小于QK,上述过程又会重复出现,这种现象称为喘振。
如果这种循环的频率与系统的自振频率接近时,就会引起系统共振,导致风机无法正常工作。
Q---风量H---风压
图2-9轴流风机的Q-H性能曲线
风机产生喘振,从理论上讲应具备下列三个条件:
1.风机的工作点落在具有驼峰形Q-H性能曲线的不稳定区域内;
2.风道系统具有足够大的容积;
3.整个系统的喘振频率与系统自振频率重叠时发生共振。
为防止轴流风机发生喘振,应避免风机在不稳定工况内工作。
采用动叶调节的轴流风机,当外界需要的流量减少时,应减小动叶安装角,从而使Q-H性能曲线下移,临界点K线向下方移动,输出的流量与压头相应变小,保持工作点处于稳定区域。
在风机启动时也要考虑喘振问题。
风机并联工作时,Q-H曲线发生变化,工作时应确保避开喘振区。
轴流风机启动前关闭动叶与进风门的目的,就是减少动叶安装角与切断风道。
一台风机在运行中,而另一台风机要启动,应先将运行风机负荷降低,即将动叶关小到一定位置再启动另一台风机。
锅炉两侧风烟分别自成系统,一般引、送风机不采用交叉运行方式。
当一台风机要停止,另一台风机仍在运行时,先将运行中风机动叶关小,再停另一台风机运行。
8.2失速
由流体力学知,当速度为v的直线平行流以某一冲角(翼弦与来流方向的夹角)绕流二元孤立翼型(机翼)时,由于沿气流流动方向的两侧不对称,使得翼型上部区域的流线变密,流速增加,翼型下部区域的流线变稀,流速减小。
因此,流体作用在翼型下部表面上的压力将大于流体作用在翼型上部表面的压力,结果在翼型上形成一个向上的作用力。
如果绕流体是理想流体,则这个力和来流方向垂直,称为升力。
(见图2-10a)
图2-10失速原理
轴流风机性能曲线的左半部具有一个马鞍形的区域,在此区段运行有时会出现风机的流量、压头、和功率的大幅度脉动等不正常工况,一般称为“喘振”,这一不稳定工况区称为喘振区。
实际上,喘振仅仅是不稳定工况区内可能遇到的现象,而在该区域内必然要出现不正常的空气动力工况则是旋转脱流或称旋转失速。
这两种不正常工况是不同的,但是它们又有一定的关系。
轴流风机叶片前后的压差,在其它都不变的情况下,其压差的大小决定于动叶冲角的大小,在临界冲角值以内,上述压差大致与叶片的冲角成比例,不同的叶片叶型有不同的临界冲角值。
翼型的冲角超过临界值时,气流会离开叶片凸面发生边界层分离现象,产生大面积的涡流,气流在叶片背部的流动遭到破坏,升力减小,阻力却急剧增加,这种现象称为“旋转脱流”或“失速”(如图2-10-b)。
如果脱流现象发生在风机的叶道内,则脱流将对叶道造成堵塞,使叶道内的阻力增大,同时风压也随之而迅速降低。
风机的叶片由于加工及安装等原因不可能有完全相同的形状和安装角,同时流体的来流流向也不完全均匀。
因此当运行工况变化而使流动方向发生偏离时,在各个叶片进口的冲角就不可能完全相同,如果某一叶片进口处的冲角达到临界值时,就首先在该叶片上发生脱流,而不会所有叶片都同时发生脱流。
如图2-11所示:
假设在