5轴数控龙门铣床机械结构设计毕业论文Word文档格式.docx
《5轴数控龙门铣床机械结构设计毕业论文Word文档格式.docx》由会员分享,可在线阅读,更多相关《5轴数控龙门铣床机械结构设计毕业论文Word文档格式.docx(28页珍藏版)》请在冰豆网上搜索。
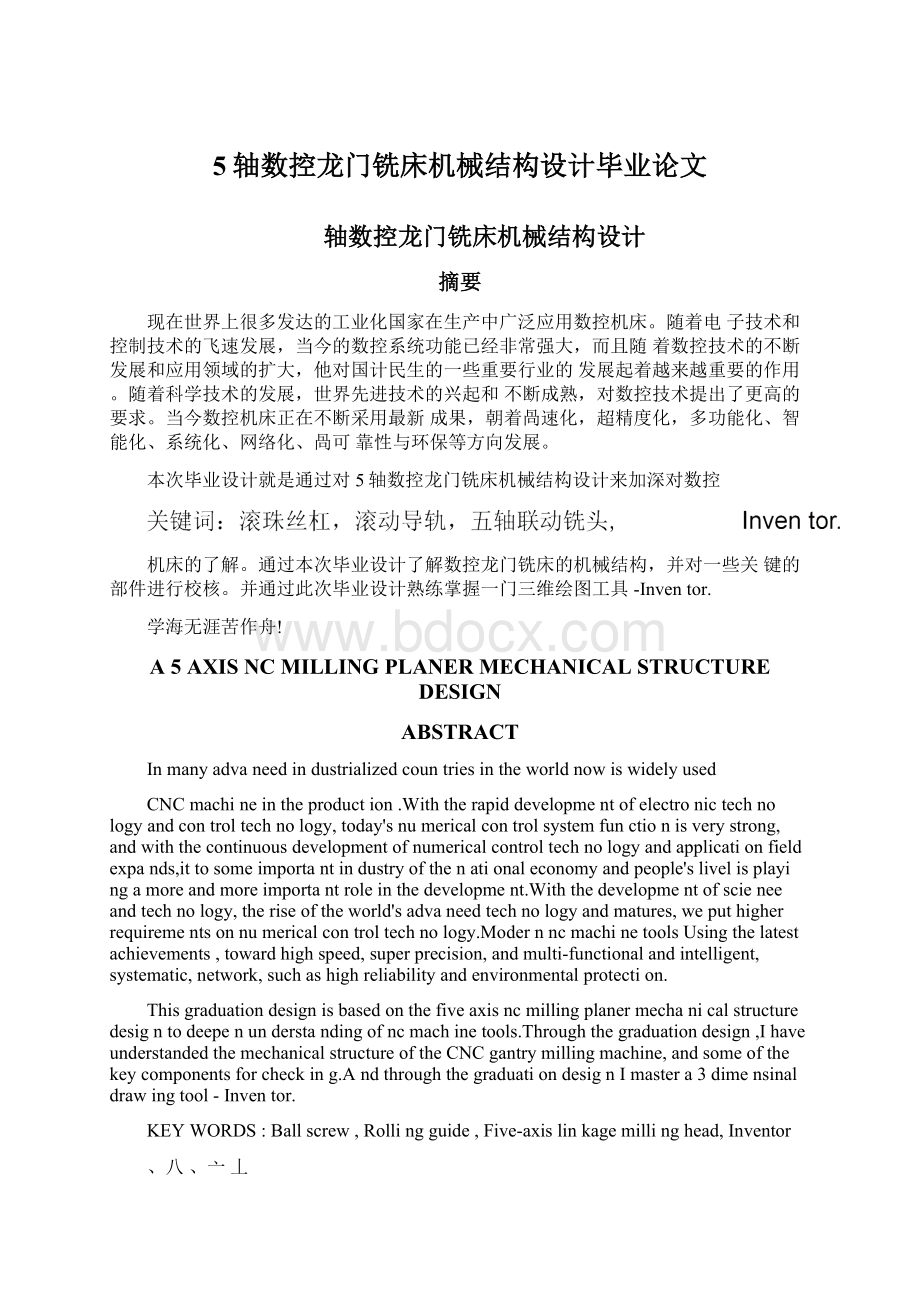
4.2伺服电机的选择与计算21
结论26
参考文献27
致谢28
毕业设计是实现培养目标的重要教学环节,是培养大学生的创新能力、实践能力和创业精神的重要过程。
毕业设计在培养大学生探求真理、强化社会意识、进行科学研究基本训练、提高综合实践能力与素质等方面,具有不可替代的作用,也是教育与生产劳动和社会实践相结合的重要体现。
毕业设计的目的是:
(1)使学生进一步巩固和加深对所学的基础理论、基本技能和专业知识的掌握,使之系统化、综合化。
培养学生的独立工作、独立思考和综合运用已学知识解决实际问题的能力,尤其注重培养学生开发创造能力和独立获取新知识的能力。
(2)使学生初步掌握科学研究的基本方法,获得从事系统科学研究的初步训练,注重科学能力和素质的培养。
在实际工程设计中,学生可以得到所学过的理论基础,技术基础等全面的训练,为将来做好机械设计工程师的工作提供全面的锻炼机会。
我们一组此次毕业设计是结合老师的具体研制项目设立的,以在实习工厂所参观的设备为参考,结合自己所学知识,在老师和同学的指导和帮助下,
查阅许多相关手册,最终设计出了此次5轴数控龙门铣床。
此外,本次毕业设计主要由Inventor实体造型完成。
它被广泛应用于机械制造行业,通过Inventor设计的5轴数控龙门铣床,和一般应用工程图的表达方式相比,具有更加直观的效果。
在张波老师的指导下,我一边查资料、计算、绘图,一边观察实习。
其间曾经遇到很多问题,如三维图的装配,滚珠丝杠的选型等等,但在张波老师和同学们的帮助下,经过自己的努力,问题一个一个得到了解决。
本次设计得到了学校、图书馆、老师、同学们的大力支持,在此表示衷心的感谢。
限于本人水平和经验有限,再加上时间仓促,难免有疏漏和不妥的地方,敬请广大老师和同学批评指正。
谢谢!
第一章数控机床概述
从20世纪中叶数控技术出现以来,数控机床给机械制造业带来了革命性的变化。
数控加工具有如下特点:
加工柔性好,加工精度高,生产率高,减轻操作者劳动强度、改善劳动条件,有利于生产管理的现代化以及经济效益的提高。
数控机床是一种高度机电一体化的产品,适用于加工多品种小批量零件、结构较复杂、精度要求较高的零件、需要频繁改型的零件、价格昂贵不允许报废的关键零件、要求精密复制的零件、需要缩短生产周期的急需零件以及要求100%佥验的零件。
数控机床的特点及其应用范围使其成为国民经济和国防建设发展的重要装备。
进入21世纪,我国经济与国际全面接轨,进入了一个蓬勃发展的新时期。
机床制业既面临着机械制造业需求水平提升而引发的制造装备发展的良机,也遭遇到加入世界贸易组织后激烈的国际市场竞争的压力,加速推进数控机床的发展是解决机床制造业持续发展的一个关键。
随着制造业对数控机床的大量需求以及计算机技术和现代设计技术的飞速进步,数控机床的应用范围还在不断扩大,并且不断发展以更适应生产加工的需要。
我国数控机床行业总体的技术开发能力和技术基础薄弱,信息化技术应
用程度不高。
行业现有的信息化技术来源主要依靠引进国外技术,且外方在许多高新产品的核心技术上具有掌控地位,我们对国外技术的依存度较高,对引进技术的消化仍停留在掌握已有技术和提高国产化率上,没有上升到形成产品自主开发能力和技术创新能力的高度。
具有高精度、高速、高效、复合功能、多轴联动等特点的高性能实用数控机床基本上还得依赖进口。
与国外产品相比,我国的差距主要是机床的高速高效化和精密化上。
对高速加工技术,国外已进行了多年的研究,对高速加工的机理、机床结构、机床刚度和精度的影响等都有了系统的研究,并开发生产了各种高速铣削中心、高速加工中心,广泛应用于航空器铝合金零件和模具加工上
第二章整体结构方案
方案一:
采用数控龙门移动结构,龙门移动,工作台固定在龙门底座上,且配置为二轴联动的旋转工作台。
X轴采用双丝杠驱动加线性滚珠导轨,Y
轴采用双线性滚珠导轨安装呈垂直分布状态,Z轴采用大规格线性滚珠导
轨。
方案二:
与方案一1样,采用龙门移动结构,工作台与龙门底座采用一体结构,Z轴滑枕上配置五轴联动铣头。
导轨配置方面,与方案1一样。
方案三:
机床采用定梁式龙门铣床结构。
配置二轴联动的旋转工作台,且工作
台,且工作台在线性滚珠导轨上作X向运动,滚珠丝杠螺母副与导轨配置方
面,与方案1一样。
方案四:
与方案3一样,采用定梁式龙门铣床结构,工作台在线性滚珠导
轨上作X向运动,Z轴滑枕上配置五轴联动铣头。
导轨配置方面,与方案1
一致。
对比分析以上4种方案设计,方案1与方案2都采用动梁式龙门结构。
此结构的最大缺陷:
①由于是靠滚珠丝杠与线性滚珠导轨驱动形式,则难以保证机床的刚性;
②采用双丝杠驱动技术,对机床控制部分要求提高了,同时提高了零件加工工艺难度。
优点在于机加工效率较高。
方案1采用了二轴
联动的旋转工作台结构;
方案2采用了五轴联动铣头结构。
相比之下,二轴联动的旋转工作台因受结构及空间的约束。
不宜加工大型工件;
而五轴联动铣头相对结构紧凑,在空问上自由度较大。
方案3与方案4都采用定粱式龙门结构,此结构的最大优点:
在结构上具有较高的刚度。
且不用担心质量不当而影响机床的加速度方面的性能;
结构的缺陷在于工作台移动,从而在x轴方向上占用的空间较大,也不利机床
x轴向上的加速度性能。
其旋转工作台结构与五轴联动铣头方面的特点前面已作说明,此处不再重述旧[5]。
综合上述资料,本课题采用方案4的总体结构设计
图2-1五轴数控龙门铳床
第三章伺服进给系统机械传动机构的设计
伺服进给系统机械传动机构是指将电动机的旋转运动,变为工作台或刀架的运动的整个机械传动链,包括引导和支撑执行部件的导轨、丝杠螺母副、
齿轮齿条副、蜗杆副、齿轮或齿链副及其支撑部件等。
由于进给传动系统的精度、灵敏度、稳定性直接影响了数控机床的定位精度和轮廓加工精度,因此,在机械传动机构的设计中应满足下列要求:
⑴提高传动部件的刚度
一般来说,数控机床的直线运动的定位精度和分辨率都要达到微米级,回转的定位精度和分辨率都要达到角秒级,如果传动部件的刚度不足,必然会导致传动部件产生弹性变形,工作台产生爬行、振动和反向死区,影响系统的定位精度、动态稳定性和响应的快速性。
关于机械传动机构的传动刚度,
主要取决于丝杠螺母副、蜗杆副及其支撑结构的刚度。
缩短传动链、合理选择丝杠以及丝杠螺母副的支撑部件等,施加预紧力是提高传动刚度的有效途径。
⑵咼谐振
为了提高系统的抗振性,应使机械传动部件具有高的固有频率和合适的阻尼,一般要求机械传动系统的固有频率应高于伺服驱动系统固有频率的2〜3倍。
(3)摩擦阻力小
为了提高伺服进给系统的快速响应特性,保证其运动平稳、定位准确,除对伺服元件提出要求外,还必须减小运动件的摩擦阻力和动、静摩擦系数之差。
机械传动机构的摩擦阻力主要来自丝杠螺母副和导轨。
为了减小摩擦阻力,普遍采用滚珠丝杠螺母副、静压丝杠螺母副、滚动导轨和塑料导轨
(4)减小传动部件的惯量
传动部件的惯量对伺服机构的起动和制动特性都有影响,尤其是处于高
速运转的零件,由于对进给系统的加速度要求较高。
在驱动电机一定时,传动部件的惯量直接决定了进给系统的加速度,它是影响进给系统快速性的主要因素。
因此,在满足系统强度和刚度的前提下,应尽可能减小零部件的重量、直径,以降低惯量,提高快速特性。
(5)无间隙
机械传动部件之间的间隙是造成伺服进给系统反向死区的一个主要原因,因此,对传动链的各个环节,如联轴器、齿轮副、蜗杆副、丝杠螺母副及其支撑部件等,均采用消除间隙的结构措施或施加预紧力。
3.2滚珠丝杠螺母副的原理及支撑方式
滚珠丝杠螺母传动属于滚动螺旋传动。
滚动螺旋传动的滚动体有滚珠和滚子两大类,其应用最广泛的是以滚珠为滚动体的滚珠丝杠螺母传动。
滚珠丝杠螺母副作为精密、高效的传动元件在数控机床得到广泛应用,在机械工业、交通运输、航天航空、军工产品等领域应用也很普遍,可作精密定位自动控制、动力传递和运动转换⑴。
3.2.1滚珠丝杠螺母副的原理及特点
滚珠丝杠螺母副是由丝杠、螺母、滚珠等零件组成的机械元件,基结构原理如图3.1所示
图3-1滚珠丝杠螺母副
在丝杠和螺母上都有半圆形的螺旋槽,当他们套装在一起时便成了滚珠的螺旋滚道。
螺母上有滚珠回珠滚道,将数圈螺旋滚道的两端连接成封闭的循环滚道,滚道装满滚珠,当丝杠旋转时,滚珠在滚道内自转,同时又在封闭滚道内循环,使丝杠和螺母相对产生轴向运动。
当丝杠(或螺母)固定时,
螺母(或丝杠)即可产生相对直线运动,从而带动工作台或其他移动件作直线运动。
滚珠丝杠副具有如下特点:
(1)传动效率高
滚动摩擦的摩擦损失小,传动效率n=0.92~0.94,是普通滑动丝杠的3~4
倍。
(2)摩擦力小
因其动、静摩擦系数小,故传动灵敏、运动平稳、低速不易爬行,随动精度和定位精度高。
(3)可预紧
滚珠丝杠副经预紧后可消除轴向间隙,有助于定位精度和刚度的提高,即使反向也没有空行程,反向定位精度高,且传动平稳
(4)定位精度和重复定位精度高。
(5)有可逆性
因滚珠丝杠副摩擦系数小,所以不仅将旋转运动转换为直线运动,也可
以将直线运动转换为旋转运动,丝杠和螺母既可作主动件,也可作从动件。
(6)使用寿命长
滚珠丝杠副采用优质合金钢制成,其滚道表面淬火硬度达60〜62HRC,
表面粗糙度小,而且是滚动摩擦。
故磨损很小,使用寿命长。
(7)同步性好
用几套相同的滚珠丝杠副同时传动几个相同的部件或装置时,可获得较
好的同步性⑴。
322滚珠丝杠螺母副的支撑方式
数控机床的进给系统要获得高的传动精度,除了滚珠丝杠副本身的刚度
外,滚珠丝杠的正确安装及支撑结构也不容忽视。
滚珠丝杠副作为数控机床关键功能部件之一,它的安装形式的优劣很大程度上决定了机床的运动精度和加工精度。
在现有机床中,滚珠丝杠的安装方式一般有五种:
a、一端固定,
一端自由;
b、一端固定,一端游动;
c、两端游动;
d、两端固定;
e、丝杠
固定,螺母旋转;
常见的四种主要支承形式见图3—2。
其各安装方式所适用
的加工状况如下:
方式a适用于低速回转、丝杠较短的情况;
方式b适用于
中速回转、高精度的情况;
方式c适用于中速回转的情况。
方式d适用于高
速回转、高精度的情况;
方式e适用于丝杠长且速度较高的情况。
本课题三
轴均采用了两端固定(d)的支撑方式
图3-2滚珠丝杠螺母副的支承形式
3.2.3支承轴承的选择
滚珠丝杠对轴承的要求是要保证足够的精度和疲劳寿命。
但滚珠丝杠主要承受轴向载荷,除丝杠自重外,一般无径向载荷。
因此,滚珠丝杠的轴承的轴向精度和刚度要求高。
进给系统要求运转灵活,对微小位移响应要灵敏。
滚珠丝杠支承中用得最多的滚动轴承是60接触角推力角接触球轴承,其
次是滚针和推力滚子轴承的组合轴承。
后者多用于牵引力大,要求刚度高的大型与重型机床。
结合本机床的特点及支承方式,因此选择60接触角推力角
接触球轴承。
3.3滚珠丝杠副的疲劳寿命计算
滚珠丝杠副的额定寿命计算原理与滚动轴承相同,这里只引用一些有关的理论和计算公式。
(1)额定寿命
Lh:
为滚珠丝杠副在可靠性为90%的额定寿命(h)
Ca:
为额定轴向动载荷(N)fm:
为丝杠的轴向当量负荷(N)
Nm:
为丝杠的当量转速(r/min)
ft为温度系数fh为硬度系数
fa为精度系数fw为负载性质系数
fk为可靠性系数
⑵当量负荷
在转速变负荷情况下,必须折算成当量转速和当量负荷进行寿命计算。
①当转速变动,负荷不变动时,当量转速按各转速所占的时间百分比折合,按下式计算:
nm=-q^n^i+~^门2+...+-^n*
100100100
式中,nm为当量转速(r/min),qi,q2,...qn为转速ni,n2,...nn所占的时间百分比
②当负荷与转速都变动时,当量负荷按下式计算
Fm=3Fi3肛出+F23也生+...+F「匹出
Vnm100nm100nm100
式中,q1,q2,...qn为负荷F1,F2,...Fn所占的时间百分比
(3)滚珠丝杠副的选用
当滚珠丝杠副在较高转速(一般转速n>
1000r/min)下工作时,应按使用寿
命选择基本尺寸,并验算其承载能力是否超过额定动载荷;
当滚珠丝杠副在低速(n<
30r/min)下工作时,应按使用寿命和额定静负荷两种方法确定基本尺寸,并选择其中较大尺寸,当滚珠丝杠副在静负荷下工作时,只需按额定
静负载选择。
式中:
Fa为滚珠丝杠副的轴向负载(N)
Caj为滚珠丝杠副的计算动载荷Kh为寿命系数
Kn为转速系数仁.为综合系数
3.4预加负荷
为了消除滚珠丝杠副的间隙,提高传动定位精度和轴向刚度,用双螺母预紧的方法消除丝杠副间的间隙。
预紧原理和计算与滚动轴承预紧相同,一对角接触球轴承背靠背或面对面安装,当轴向外载荷达到预紧力的3倍时,另一侧轴承将卸载。
这个结论
对于双螺母预紧的滚珠丝杠副也是适用的。
因此,滚珠丝杠副的预紧力不应小于最大轴向载荷的1/3,即应满足以下条件:
FaO>
1/3Fmax
Fa0为轴向预紧力Fmax为轴向最大载荷
用户订购滚珠丝杠副时,将滚珠丝杠副所需预紧力,即在技术要求中规定的并由生产厂家出厂产品调整好的预紧力大小通知生产厂家。
3.5机床滚珠丝杠副总体校核
设此机床的参数如下:
工作台质量mi=500kg工件最大质量m2=200kg
J=0.006
0.02/300mm
工作台最大行程l=800mm工作台滑动导轨摩擦系数丝杠两端为固定支承,切削方式为铣削,定位精度
丝杠寿命:
10a工作可靠性:
96%
表3-1
切削力,速度和时间比
切削方式
纵向切削力
Fa/N
速度v/(m/min)
时间比例q/%
强力切削
2000
0.6
15
一般切削
1000
0.8
30
精密切削
500
1
50
快速移动及定位
8
5
表3-2设计计算结果见下表⑴
序号
计算项目
符号
单位
计算依据
计算结果
丝杠载荷导轨摩擦
%
42
力
Famax
'
卩(mi+m2)g=0.006(500+200)
2042
强力切削时载荷
Fa
>
9.8
1042
一般铳削时载何
Famax=2000+42
542
精铳时载荷
N
Fa=1000+42
快移时载荷
Fa=500+42
Fa=42
2
电机转速(最大)
nmax
1500
丝杠最大转速(快
移)
n
强力铳削
一般铳削
ni
r/min
60
精密铳削
n2
80
n3
100
3
丝杠导程
Ph
mm
工作台最大速度
Vmax=8x1000=8000mm/min
Ph=Vmax/n=8
4
当量转速
nm
nm=n1q〃100+n2q2/100+...=601>
/1
133
00+80^30/100+100汇50/100+1000
汉5/100
当里负何
Fm
Fm=
1215
JR3虹皿+F23匕•业+...+F;
丫nm100nm100
nnqnnm100
3204
23$°
肿土04玉叭
303
+5423x.
X
5(
\133100133
10
=1215
6
初选滚珠丝杠
Caj=K
hFm/Knf寸=3.9X215n.64
18147
(1)计算动载荷
Caj
408
)(日)X6(h)X0.6(开机
(2)要求寿命
Lh
h
Lh=30
28800h
fz
率)Xl(
)(a)=28800h
(3)综合系数
(查表得
*Kh=3.9,Kn=0.64)
(4)滚珠丝杠副
L
hfafk/fw=1X1X1XJ.53~1・3=0・4
0.408
的型号
08
有标准
选用FFZD型内循环浮动
反向器
宇双螺母垫片预紧滚珠丝杠
畐U,型
号FFZD3208,额定动载荷
Ca=32
KN>
Caj.
预
紧力
F0=0.2
5Ca=8000N>
1/3Fmax=X20
符合要求
42=68(
)N
7
丝杠螺纹部分长度
lu
Lu=工
作台最大行程(800mm)+
螺母长
W度(123mm)+两端余程
1264
(2X1
70.5mm)=1264mm
支承距离1
支承距
离1应大于lu
1286
9
临界转速校核
nc
nc=99(
222
0f2d2/Lc=9900X4.73X0.02
4700
(1)丝杠底径
d2
M
34/1.05
_2
(2)支撑