单梁箱形桥式起重机主梁设计Word格式文档下载.docx
《单梁箱形桥式起重机主梁设计Word格式文档下载.docx》由会员分享,可在线阅读,更多相关《单梁箱形桥式起重机主梁设计Word格式文档下载.docx(16页珍藏版)》请在冰豆网上搜索。
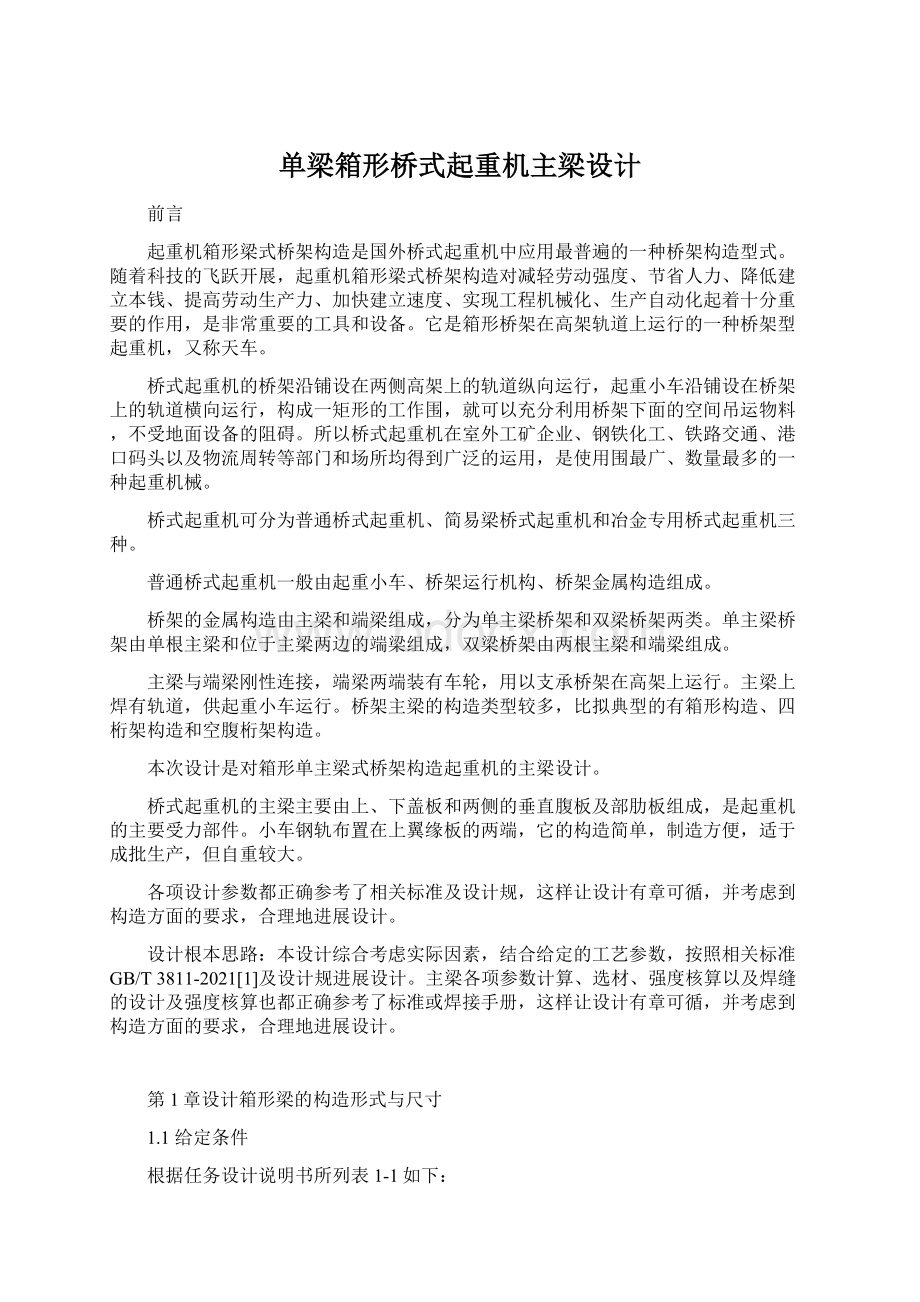
跨距
桥架主梁形式
大车不大于21.8t
起升速度
大车运行速度
〔中级〕
22.5m
箱形梁
8m/min
90m/min
表1-1箱形梁设计给定条件
1.2箱形梁的构造和主要尺寸确实定
1.2.1箱形梁的构造
箱形梁的构造尺寸示意图如图1-1所示。
1.2.2箱形梁的主要尺寸确定
1、筋板及腹板的相关设计
〔1〕主梁端部长度C确实定
〔2〕主梁盖板厚度与腹板厚度确实定〔给出推荐值如表1-2〕
起重量Q〔tf〕
5,8
10〔12.5〕
15〔16〕
20
30〔32〕
50
腹板厚
6
6,8
盖板厚
8,10
10,12
12,14
1622
表1-2箱形主梁腹板和盖板厚度的推荐值〔mm〕
注:
表中所列板厚较大者用于跨度较大者
据表1-2选出跨度为22.5m的盖板厚,腹板厚。
〔3〕主梁中部高度H和盖板间距h确实定
当17<
L<
23时
〔4〕主梁端部高度确实定
起升重量为10t,属于起升重量较重,
〔5〕腹板间距b确实定
根据起重机设计原那么,b应该选择较小值,即。
〔6〕上下盖板的宽度B确实定
本次设计采用的是手工MAG焊,
2、主梁筋板的设置
〔1〕横向大筋板间距a的设置
当时,横向筋板之间的距离不应大于2h或3m
跨中处的
主梁端头处的
〔2〕横向小筋板高度及间距的设置
1〕横向小筋板高度的设置
2〕横向小筋板间距的设置
〔3〕纵向筋条设置
当
时,需要设置纵向筋条。
当横向小筋板与纵向筋条都存在时,可适当减小筋板高度,
那么
所以为了平安,选择整数。
〔4〕筋板间距的设置
根据以上C,主梁处的a、,端梁处的a、以及考虑到筋板在主梁及主梁端部的均布情况综合得出:
,
主梁、
主梁端部、
〔5〕横向筋板厚度确实定〔据非标准机械设计手册[2]中式5-44和5-45得如下公式〕
据起重机计设计手册[3]中表1-8-34选取。
〔6〕纵向角钢确实定〔据非标准机械设计手册[2]中式5-42的如下公式〕
据起重机计设计手册[3]中表1-8-41选取
同时据厚度可以选出相应的6号等边角钢,其标准为
1.3主梁预制上拱度计算
规定梁跨度中央的最大上拱度
。
第2章梁的校核
2.1梁的静载强度校核
2.1.1许用应力
材料的许用应力是材料的极限应力除以平安系数n,即
对于Ⅱ类载荷情况下的强度计算平安系数见表2-1。
Q235和16Mn的机械性能分别见表2-2和表2-3。
Ⅱ类载荷组合情况时钢材的许用应力见表2-4。
〔运送一般货物/运送液态金属〕
〔括号为大高度起重机〕
Q235
16Mn
1.5/1.7
1.55/1.75
1.2(1.3)
1.25(1.35)
表2-1金属构造构件材料的平安系数n
表2-2Q235的机械性能
材料名称
组别
棒钢直径或厚度
型钢和异型钢厚度
钢板厚度
1组
2组
3组
≤40mm
41~100mm
101~250mm
≤15mm
16~20mm
>
20mm
4~20mm
21~40mm
41~60mm
240
230
220
380~400
410~430
440~470
表2-316Mn的机械性能
钢号
钢材厚度或直径〔mm〕
抗拉强度(≥MPa)
延伸率〔≥%〕
<
16〔1组〕
17~25〔2组〕
26~36〔3组〕
37~50
55~100的方圆钢
520
500
480
350
330
310
290
280
210
190
表2-4Ⅱ类载荷组合情况时钢材的许用应力
应力种类
符号
许用应力〔MPa〕
第1组
第2,3组
第2组
第3组
拉,压,弯
剪切
160
95
140
85
130
205
120
本次设计的是Ⅱ类载荷组合的设计,所以可以根据表2-1选出Q235的,16Mn的。
根据表2-2和表2-3选出Q235的,。
16Mn的,。
所以,Q235和16Mn的许用应力可以从表2-4中选用,即
2.1.2强度校核
主梁自重确实定给定如图2-1的曲线图。
据图2-1可知,起重量为10t,跨距为22.5米的梁的重量,小车重量。
1、主梁自重引起的均布载荷q
2、梁的自重在处引起的最大弯矩为:
3、额定载荷P在处引起的最大弯矩为:
4、危险截面最大弯矩为:
5、主梁跨中截面对水平重心轴x-x的抗弯截面模量〔〕
主梁跨中截面对水平重心轴x-x的惯性矩〔〕
主梁跨中截面的一半
6、危险截面处的最大正应力σ的计算:
所以Q235和16Mn钢都可以用来制造箱形梁。
2.2主梁跨端截面的最大剪切应力的计算
1、各参数及其含义
梁自重引起的剪力〔N〕,最大载荷移至跨端时引起的剪〔N〕,主梁跨端最大剪力〔N〕,主梁端部支承截面对水平重心轴x-x的惯性矩〔〕,S主梁端部支承截面半面积对水平重心轴x-x的静矩〔〕。
2、各参数的计算
所以应该选择16Mn钢进展箱形梁的制造。
2.3主梁的静刚度计算
1、挠度许用值确实定
选取严格的挠度许用值。
2、挠度计算
主梁中部截面对水平重心轴x-x的惯性矩〔〕
E为弹性模量,对于钢可取
自重引起的最大挠度
额定载荷引起的最大挠度
第3章焊脚尺寸的设计及校核
3.1主梁的角焊缝
据焊接工艺简明手册[4]表7-6知,当7mm<
δ=10mm<
18mm时,焊脚尺寸选K=4mm。
据焊接构造学[5]中表4-12和表4-13知,16Mn钢的焊缝剪切应力许用值。
所以,即选用4mm焊脚高度适宜。
据起重机计设计手册[3]表2-2-2选出筋板的焊脚尺寸。
3.2主梁与端梁的角焊缝
据起重机计设计手册[3],主梁与端梁以角焊缝焊接,有公式。
式中为角焊缝切应力、为主梁最大支反力、为焊缝长度之和、为焊缝剪切强度许用应力。
据起重机计设计手册[3]中表2-2-2选,据表2-2-3可以得出
所以所选焊缝形式及焊脚尺寸强度校核合格。
第4章装焊工艺
4.1根本要求
4.1.1对焊工的要求
受力构件应由持证焊工施焊。
从事制造、安装、修理起重机的受力构件的焊工必须进展考试,对考试合格者发给焊工合格证(已取得锅炉、压力容器焊工合格证的可不再另行考试),凡考试不合格者不得从事起重机受力构件的焊接〔起重机的主要受力构件指:
主梁、端梁、支腿、塔架、臂架等〕。
4.1.2对设备的要求
要根据焊接方确选择焊接设备。
据MAG焊选择NBC-630〔直流〕型焊机。
4.1.3对材料的要求
1、根据使用条件确定母材种类、厚度。
根据市售钢板尺寸确定拼板时共有多少条拼接焊缝。
2、确定焊接材料的种类和规格
焊接材料应选用性能高于或等于相应母材标准规定值的下限或满足图样规定的技术要求。
还保证力学性能,且需控制抗拉强度上限。
选用熔化极气保护焊,那么应确定保护气体种类和气体流量,焊丝牌号和直径。
4.1.4坡口和焊缝形式的选择
拼板采用对接焊缝,根据板厚、焊接方法和加工能力,坡口形式选择I型坡口。
箱形梁的角接头通常采用角焊缝。
根据焊缝的受力情况、部位、焊接方法及装焊顺序,角焊缝选择单面连续角焊缝以及双面连续角焊缝。
4.1.5对环境的要求
桥式箱形梁一般制造时都在室,所以对环境要求较小。
只有湿度和温度要求。
一般要求湿度小于90%,温度大于-10。
4.2焊前准备
4.2.1焊接方法
主梁的上下盖板及腹板的对接采用MAG焊,腹板的下料采用微机控制,筋板用剪板机进展下料。
为了保证主梁的几何尺寸,在盖板、筋板、腹板定位焊完成后,按照工艺确定的电流、电压、焊接顺序、焊接方向、焊缝的分布进展二人、四人对称焊接,确保构造受热均匀,变形在控制围,然后在平台上进展桥架起吊翻转焊接。
在构造件的生产过程中,根据生产过程的检测结果,采取变换支撑点,变换焊接顺序,采用定位工装,配合火焰矫正等方法来控制和修复构造的变形,保证起重机的上拱度,同一截面上下差,垂直度等几何参数到达标准要求。
1、主梁下料采用自动火焰切割方法。
a、盖板下料将上、下盖板校正后在对接长度方向上放400mm的工艺余量。
b、腹板下料腹板矫平后首先在长度方向上拼接,然后左右两侧腹板对称气割,以防主梁两侧腹板尺寸不同,引起主梁的扭曲变形。
为使主梁有规定的上拱度,腹板下料时,需放22.5mm的拱度,并且在离中心处不得有接头,为防止焊缝集中,上下盖板与腹板的接头应错开,距离不小于200mm,腹板下料后长度误差为10mm。
2、坡口制备所有对接焊缝均采用Ⅰ坡口,间隙为2mm。
角焊缝也不开破口。
上盖板与腹板的角接采用双面焊,下盖板月腹板的焊接采用单面焊。
4.2.2备料及下料
1、气割零件的边缘和气割焊接坡口面应去除挂渣飞溅,对重要的焊接接头〔如上盖板对接焊缝〕,其坡口面必须用砂轮打磨光亮。
2、应对焊件坡口两侧10mm围进展油、锈、漆、垢、毛刺等去除干净,且不得有裂纹、夹层等缺陷。
3、盖板〔δ=10mm〕
〔1〕对已选定的16Mn材料进展校平、喷丸等预处理。
〔2〕上盖板重846.62Kg,下盖板重850.56Kg。
〔3〕切割:
选用宝钢钢板规格可自定,定制长宽为8500×
490mm,使用数控氧乙炔火焰切割加工成两块7010×
490mm和一块8020×
490mm的三块板,对边缘进展精打磨,每边打磨量不超过2mm。
〔4〕选用MAG焊对板材进展拼接〔对接前采用夹具固定,且采用压具以防止波浪变形,两端使用引弧,收弧板〕,并对焊缝外表进展清理,使形成平角焊缝。
〔5〕预置拱度:
腹板拱度要求焊切割伤、下拱度曲线,应同时同向切割。
上盖板下料的长度方向的加工余量为:
下盖板下料的长度方向的加工余量为:
4、腹板〔δ=6mm〕
〔1〕对已选定的16Mn进展校平到喷丸预处理。
〔2〕腹板单重1224.8Kg,总重2449.6Kg。
1230mm,使用数控氧乙炔切割腹板,上下弦为预置上拱,①号板切成长×
宽为8300×
1230mm的板和两块②号板切成长×
宽为6900×
1230mm的板。
②号板的一端切成直角梯形,〔上底+下底〕×
高为〔750+1230〕×
2225mm的板。
然后对材料进展精整打磨。
〔4〕开坡口:
δ=6mm,据简明焊工手册[6]知板厚小于10mm无需开坡口。
即“I〞型接头。
〔5〕与盖板一样采用MAG焊进展拼接。
〔6〕下料拱度:
在腹板两侧到中心的位置需要有渐升式的拱度,拱度最大处为22.5mm。
5、大小筋板〔δ=5.5mm〕
〔1〕主梁大筋板单重23.7Kg,总重237Kg;
纵向筋条单重9.2Kg,总重165.6Kg。
主梁端部大筋板单重19.14Kg,总重38.28Kg;
纵向筋条单重5.24Kg,总重41.92Kg。
小筋板单重5.83Kg,总重460.57Kg。
〔2〕大筋板切割成1220×
450mm的板12块,小筋板切割成300×
450mm的板79块。
注意下料时将宽度方向两角切出8×
8mm的等腰三角形,为使盖板能与腹板焊接成型。
6、纵向筋条
采用标准件
利用带锯进展大批量切割方法下料。
7、桥式起重机各部件所用钢材需要做防锈处理。
8、主梁上、下盖板和腹板下料时,要保证使焊缝在组成箱形梁后不再同一截面,而且相互错开;
主梁跨度中心左右2000mm不允许有拼接焊缝。
9、上、下盖板用刨边机下料。
4.3焊接工序
采用随装随焊的焊接工艺。
本次焊接过程中全程采用MAG焊,据起重机计设计手册〔第二版上卷〕[3]中表1-8-24选用气体80%Ar+20%CO2,据焊接手册[6]表7-12焊丝采用型焊丝。
4.3.1定位焊缝
焊接定位焊缝时必须注意以下几点:
1、定位焊焊缝应与最终焊缝有一样的质量要求,焊接材料不能随意选择,必须与以后正式焊接时一样;
2、定位焊缝余高不宜过高,必须保证熔合良好,与母材平缓过渡,防止正式焊接时出现未焊透缺陷;
3、为防止未焊透等缺陷,定位焊时焊接电流应比正式焊接时大10%一15%,定位焊缝不能焊在焊缝穿插处或焊接方向发生急剧变化的地方,通常至少离开这些位置50mm以上,定位焊缝应填满弧坑;
4、假设定位焊缝出现缺陷,必须铲除缺陷,重新进展定位焊;
定位焊缝要有足够的强度且不能开裂,为防止焊接过程中开裂,应尽量防止强制装配,必要时可增加定位焊缝的长度,并减小定位焊缝的间距。
4.3.2装焊顺序
装配——焊接顺序如图4-1所示。
图4-1装配焊接顺序
1、上盖板置于支撑平台上,并加压板固定。
在地上铺好已拼接好的上盖板,在两端加凸台,使其中间向下弯曲,弯曲程度等于预置的上拱度,即中点处向下挠22.5mm。
盖板对接MAG焊焊接工艺如表4-1或附录1。
表4-1盖板对接焊工艺
电流〔A〕
电压〔V〕
焊速〔m/min〕
焊丝直径〔mm〕
气体流量〔L/min〕
电流种类和极性
450
32
42
1.6
25
负极性
2、在上盖板加装大筋板和小筋板并对其进展定位及焊接。
3、加装腹板,定位焊其与盖板、筋板。
焊接时需两侧同时对称焊接其与盖板的焊缝。
盖板、腹板与筋板的角接MAG焊工艺如表4-2或附录2。
表4-2盖板、腹板与筋板角接工艺
4、加装筋条并对腹板和筋条进展定位焊,然后进展大小筋板、筋条与腹板的焊接。
5、加装下盖板,并两侧同时进展对称焊接。
盖板与腹板的角接MAG焊工艺如表4-3或附录3。
表4-3盖板、腹板与筋板角接工艺
420
6、测量挠度:
在上盖板平面上的两端固定一根细钢丝绳,使其滑移到不同的位置,在这个过程中钢丝绳保持水平,检验大梁的上拱度。
4.4检验
1、对焊缝进展探伤检测
首先去除焊缝外表污垢、油脂、氧化皮、焊接药皮、焊渣和飞溅等。
对于上盖板的对接焊缝,用干粉法磁粉检测,探伤标准符合GB/T2695-2021,对于单面或双面角焊缝进展超声波检测,探伤标准符合1152规定的Ⅰ级。
上盖板下料后,毛刺和凹凸不平应铲除,毛刺高度不应大于0.5mm,划痕不得大于1mm。
采用气割下料,气割后气割面与轨制面直偏差不应超过2mm,气割外表不平度不应超过1~1.4mm。
对接后要对余高进展机械加工,从而减小应力集中。
对于下盖板,采用机械压弯方法进展折弯。
2、上拱度的检验
在上盖板平面的两端固定一根细钢丝绳,使其水平,将其滑移到不同位置在此过程中保持水平,检验大梁的上拱度。
3、挠度的检验
在垂直腹板的两端一米高的地方,固定一根悬线,检查大梁在水平面的挠度,在安装大隔板的地方测量大梁挠度,其值不应超过2.25mm。
4、变形量的检验
检验各板的变形量:
腹板波浪变形受压区<
0.7δ=0.7×
6=4.2mm,其余区域<
1.2δ=1.2×
6=7.2mm,上盖板水平度≤0.328mm,腹板垂直度≤6mm。
5、焊缝质量检验
对主要的工作焊缝进展超声检验或磁粉检验。
箱形主梁的质量检验主要是制造过程中的工序检验及制造完成后的专检。
箱形主梁焊接完毕,经质检部门联检,其几何尺寸、上拱度及焊缝质量均符合质量要求才可涂装、标记,交付出厂。
对于大型桥式起重机的箱形主梁的制造,在不具备大型吊装设备的情况下,作者采用合理的装焊顺序及工艺措施,成功地弥补了设备方面的缺乏,防止了对箱形梁的反复翻转,保证了箱形梁的焊接质量并满足了尺寸要求。
总结
经过了为期三周的课程设计,终于完成了?
桥式起重机主梁?
的设计及说明。
从开场接到设计题目到系统的实现,再到说明书的完成,每走一步对我来说都是新的尝试与挑战,这也是我在大学期间独立完成的又一工程。
在这段时间里,我学到了很多知识也有很多感受。
从对专业知识的重新学习,以及用于实践;
从对起重机一无所知,到对工艺卡的制作、对焊接车间的设计等相关技术的了解;
从一个只会书本知识,到现在成为学会独立学习和实践;
从一开场不会使用工具书,到现在可以迅速查找相关的资料和书籍。
这些学习让我头脑中模糊的概念逐渐清晰,使自己的作品从稚嫩,一步一步走向完善。
每一次改良都是我学习的收获,每一次试验的成功都会让我兴奋。
从中我也充分认识到了做工程设计的艰辛。
由于本人理论知识有限,查找的资料较为旧,说明书的一些容不是很成熟,还有很多缺乏之处,在今后的设计中应对此加以改良。
这次做设计的经历也会使我终身受益,我感受到做工艺是要真真正正用心去做的一件事情,马虎不得。
他是真正使自己学习和研究的过程,没有学习就不可能有实践的能力;
没有自己的研究,就不会有所突破。
希望这次的经历能让我在以后学习中鼓励我继续进步。
参考文献
1中华人民国标准GB/T3811-2021.起重机设计规
2宗武,徐履冰,石来德.非标准机械设计手册.:
机械工业,2002,9
3质文,王金诺,程文明,等.起重机计设计手册〔第二版上卷〕.:
中国铁道,2021,6
4徐峰,焊接工艺简明手册.:
科学技术,2021,1
5方洪渊,焊接构造学.:
机械工业,2021,4
6武将,周国萍,焊接手册.:
机械工业,2001,8
7简明焊工手册编写组,简明焊工手册.:
机械工业,2000