150kta亚硫酸钠续建项目之可行性研究报告书文档格式.docx
《150kta亚硫酸钠续建项目之可行性研究报告书文档格式.docx》由会员分享,可在线阅读,更多相关《150kta亚硫酸钠续建项目之可行性研究报告书文档格式.docx(28页珍藏版)》请在冰豆网上搜索。
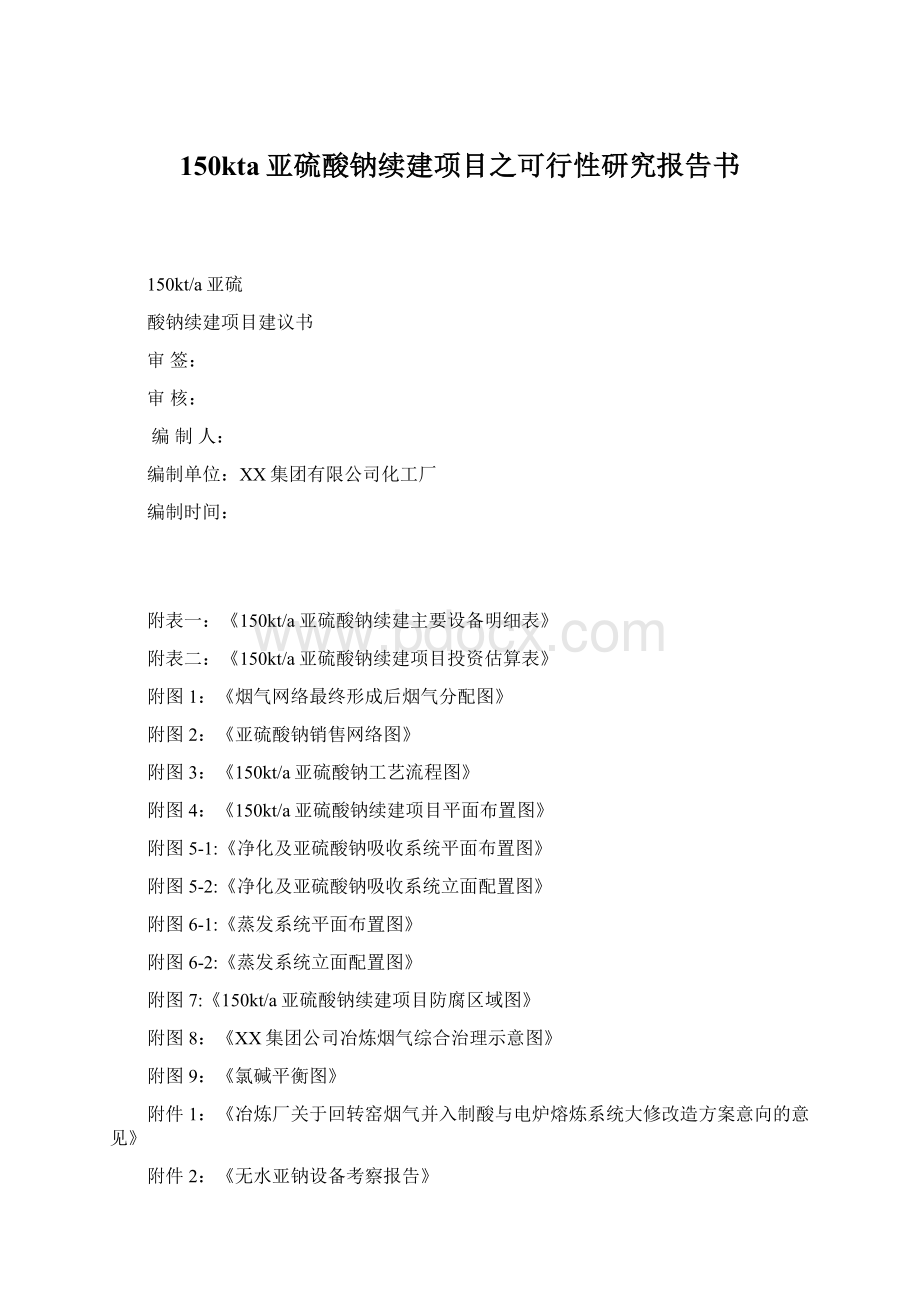
附图8:
《XX集团公司冶炼烟气综合治理示意图》
附图9:
《氯碱平衡图》
附件1:
《冶炼厂关于回转窑烟气并入制酸与电炉熔炼系统大修改造方案意向的意见》
附件2:
《无水亚钠设备考察报告》
150kt/a亚硫酸钠续建项目建议书
1、前言
亚硫酸钠项目是集团公司冶炼烟气治理的环保项目。
2000年硫酸产量仅有220kt/a,硫酸外销价格在200元/吨以下,销售一度受阻,根据公司“铜的文章做大”发展战略,需延伸二氧化硫的产品链,为此,化工厂利用自产烧碱和自有技术,2000年立项建设了20kt/a无水亚硫酸钠项目,烟气设计浓度为5%~5.5%,2002年20kt/a无水亚硫酸钠建成投产,2004年立项建设150kt/a亚硫酸钠项目,期间因原料烧碱供应紧张,当年仅建成了100kt/a七水亚硫酸钠,30kt/a无水亚硫酸钠暂缓建设。
按照公司的安排40万吨离子膜烧碱项目一期工程计划于2009年3月建成投产,将为亚硫酸钠的生产和续建项目提供充足的原料。
2008年5月20日由规划发展部组织对《150kt/a亚硫酸钠续建项目建议书》进行专业技术评审,评审组从市场、技术方案、投资、项目建设的必要性等方面进行了论证。
6月23日公司经理办公会要求化工厂就亚硫酸钠的国际市场、质量标准、产品方案等内容进行完善,并对亚硫酸钠和硫酸生产的经济性进行比较。
7月15日公司经理专题会、7月20日公司经理办公会及8月23日公司主要领导现场调研的精神,化工厂从技术方案、质量、成本、各种烟气浓度下生产的运行方式等进行风险分析。
进一步完善了《150kt/a亚硫酸钠续建项目建议书》。
2、项目建设的必要性
2.1低浓度二氧化硫烟气综合治理的需要
2.1.1公司冶炼烟气治理的现状
随着回转窑烟气并入制酸网络体系及公司新镍系统的建成,届时公司将形成2000kt/a硫酸生产能力。
公司现有六大制酸系统,按烟气来源可分为铜冶炼烟气制酸系统和镍冶炼烟气制酸系统。
各制酸系统与冶炼各炉窑烟气走向关联图见图1(图中数值均为设计值)。
图1各制酸系统与冶炼各炉窑烟气走向关联图
从关联图可以看出:
烟气网络体系能将一期贫化电炉、矿热电炉、回转窑等低浓度二氧化硫烟气与其它炉窑产生的高、中浓度的二氧化硫烟气进行平衡调配,送入制酸体系和亚硫酸钠生产系统,形成以双转双吸制酸工艺为主力,单转单吸制酸工艺为补充,以亚硫酸钠系统作为最终保障的烟气治理格局。
但从网络系统运行来看,所有冶炼炉窑烟气总量偏大,烟气网络体系中低浓度二氧化硫烟气量偏多,回转窑烟气成分复杂,整个网络体系运行十分被动,主要表现在:
(1)烟气总量的平衡问题有待解决
从图1分析可以看出,随着新镍系统的建成,进入制酸体系中的烟气总量将达到106万Nm3/h,其中,一期冶炼各炉窑烟气总量为60.78万Nm3/h,主要送往一硫酸一二系列、53万吨、30万吨等制酸系统。
53万吨硫酸和30万吨硫酸系统烟气处理能力通过挖潜,可超设计能力消化约5万Nm3/h的烟气,处理气量可分别提高到20.5万Nm3/h和18万Nm3/h,一硫酸一二系列制酸系统处理气量为14万Nm3/h,亚硫酸钠系统处理烟气量为3万Nm3/h。
一硫酸各制酸系统和亚硫酸钠系统总处理气量为55.5万Nm3/h,剩余5.28万Nm3/h进入网络体系;
二期冶炼各炉窑烟气总量为17万Nm3/h,主要供三硫酸制酸系统,其处理气量为13.5万Nm3/h,剩余3.5万Nm3/h的烟气需进入网络体系;
新镍系统烟气总量28万Nm3/h,主要供70万吨硫酸系统;
氯浸渣项目产生二氧化硫烟气约为1万Nm3/h。
从以上分析可以看出,整个网络体系中将有约10万Nm3/h烟气需做开路处理。
(2)烟气浓度仍然无法保障
2005年以来,公司共投入1.8亿元从源头上做好烟气的除尘和稳定二氧化硫的浓度,采用冶炼烟气除尘新技术、新工艺、新设备对原有除尘系统进行了彻底的技术改造,使所有的冶炼炉窑均配套安装了高效电除尘设施,电收尘出口烟气含尘监测值除铜合成炉烟气在0.5~0.8g/Nm3外,其它炉窑烟气含尘均在0.5g/Nm3以内,不仅降低了硫酸系统净化费用,在提高镍、铜等有价金属回收率、治理污染的同时,稳定各炉窑中二氧化硫的浓度,为公司长期外排的一期电炉及回转窑烟气的回收治理创造了条件(冶炼各炉窑的烟气状况见表一)。
表一:
各冶金炉窑烟气条件汇总表(设计值)
炉窑名称
数量
单台烟气量
烟气总量
温度
SO2
含尘
备注
Nm3/h
℃
(%)
g/Nm3
回转窑
2
37000
74000
110~180
2.5
0.2
矿热电炉
3
45000
135000
250
0.9~1.5
进53万吨、30万吨系统
86吨镍转炉
3+1
62000
186000
250~320
4.2
0.35
进一硫酸一、二系统
铜合成炉
1
60000
270~320
18~23
0.4
110吨铜转炉
2+1
65000
130000
200~300
4.7~6.0
0.3
铜贫化电炉
7800
250~300
0.57
同上
自热炉、卡尔多炉
15000
30000
6
进30万吨系统
镍闪速炉
80000
14.4
进三硫酸系统
二期转炉
90000
进三硫、53万吨
富氧顶吹炉
151569
280
12.07
0.5
进70万吨系统
富氧顶吹转炉
54286
108572
6.21
富氧顶吹贫化炉
21200
0.61
2006年公司利用铜合成炉产生的高浓度二氧化硫烟气将冶炼炉窑产生的高中低三种不同浓度的二氧化硫烟气引入制酸体系,形成了烟气网络体系。
2006年、2007年分别将矿热电炉及回转窑烟气并网,烟气网络体系中增加了21万Nm3/h,SO2浓度在2%左右不宜制酸的低浓度烟气。
从公司冶炼系统的生产格局来看,随着富氧顶吹熔炼的建成投产,一期电炉及回转窑系统将转产炼铜,二氧化硫浓度有所提高,但条件变化不大(根据《冶炼厂关于回转窑烟气并入制酸与电炉熔炼系统大修改造方案意向的意见》,回转窑炼镍时烟气中二氧化硫浓度为1.8~3.2%,回转窑炼铜时烟气中二氧化硫浓度为2.1~3.1%,冶炼炉窑的烟气状况与设计值相比不会有明显的改变)。
53万吨硫酸、30万吨硫酸,适合于治理高浓度二氧化硫(6~8%)烟气;
一硫酸一二系列为单转单吸制酸工艺,适合于治理较低浓度二氧化硫(3~6%)烟气。
冶炼炉窑产生的高、中、低不同浓度的烟气配气后送入各制酸系统。
即将投产的富氧顶吹熔炼炉系统,熔炼炉、转炉、贫化电炉混合烟气的浓度为8.5%,与70万吨制酸系统相配套,不能接受网络体系中低浓度二氧化硫烟气。
综上分析可以看出:
为了达到制酸体系中最基本的SO2浓度,必须从网络体系中至少分离出10万Nm3/h,SO2浓度为2%左右的烟气。
烟气网络体系最终形成后烟气分配详见附图1。
(3)回转窑烟气成分复杂,影响硫酸产品质量
回转窑烟气不仅二氧化硫浓度低,而且烟气中含有大量的烃类气体,这些有机物在制酸过程中被浓硫酸碳化,使硫酸呈黑色,影响成品酸质量,因此必须将回转窑烟气从网络体系中分离出来。
综上所述,为了使冶炼与化工在较为轻松的环境下运行,需要从体系中分离出10万Nm3/h低浓度烟气。
2.1.2国内低浓度冶炼烟气制酸的现状
国内低浓度烟气治理主要有制酸法、吸收解析法和亚硫酸钠三种工艺。
制酸工艺有WAS湿法催化制酸和非稳态法制酸。
WAS湿法催化制酸工艺虽具有转化率较高(98%),不产生废水、废渣等优点,但WAS工艺装置投资昂贵,操作要求相对较苛刻(要求烟气中含尘不超过1mg/m3,净化收率在99%以上),操作弹性小。
我国株冶于2003年首次引进该技术,运行效果并不理想,主要表现为系统设备腐蚀泄露严重、系统热量极度不稳定、尾气二氧化硫和酸雾含量高等,系统故障率高,不能正常运行。
目前国内对低浓度烟气治理普遍采用非稳态法制酸工艺,现已有9套装置投入运行(沈阳冶炼厂、安阳豫北金属冶炼厂、焦作东方金铝有限公司等),最大处理气量为5万Nm3/h。
非稳态法制酸虽对负荷波动的适应性强,但该工艺存在转化率低(一般在82%左右),尾气难达标,需另建尾气吸收系统,运行成本高(触媒用量是常规制酸工艺的2倍,触媒粉化严重,使用寿命不到1年,且需进口触媒),设备腐蚀严重,产品质量差,成品酸只能用于生产磷肥。
吸收解析法主要有柠檬酸钠法和活性焦法,这两种工艺投资较高,运行成本高(超过1000元/吨SO2),一般适用于更低浓度二氧化硫(低于1%)烟气的治理。
2.1.3二氧化硫烟气治理方案的确定
从上述分析可以看出,为确保网络体系正常运行,需从体系中分离出约10万Nm3/h,二氧化硫浓度为1.5~2%的低浓度烟气,不宜采用吸收解析工艺,我们对非稳态法制酸工艺与亚硫酸钠生产工艺进行比较。
非稳态法制酸工艺投资大约为1.8亿,其硫酸产量不到50kt/a,运行成本为600元/吨硫酸(目前我厂制酸成本在135元/吨硫酸),且技术需要引进,需昂贵的技术引进费用,显然是不经济的。
我公司有技术成熟的亚硫酸钠生产线,拥有多年亚硫酸钠生产控制经验,而亚硫酸钠生产工艺恰能处理这部分低浓度二氧化硫烟气,从而提高制酸系统中的烟气浓度。
现就亚硫酸钠法与非稳态制酸工艺的经济性进行比较(见表1)。
表1经济效益比较
项目
亚硫酸钠法
非稳态制酸法
产量
150kt/a
50kt/a
亚硫酸钠产量为:
无水亚硫酸钠100kt/a、七水亚钠50kt/a
投资(万元)
12772
18000
成本(元/吨)
1637.5/500
600
无水亚钠成本1637.5元/吨;
七水亚钠成本500元/吨
销售价(元/吨)
2600/600
850
2600元/吨为无水亚钠市场最低价;
600元/吨为目前我公司七水亚钠销售价;
因硫酸质量差,价格为850元/吨
销售收入(万元)
29000
4250
年净利润(万元)
5911
632
通过对低浓度烟气治理的两种工艺经济性比较,我们选择亚硫酸钠生产工艺。
在去年回转窑烟气引入制酸体系时,已提出将亚硫酸钠系统同步建成,但由于当时烧碱供应紧张,亚硫酸钠暂缓建设,当时这种抉择无疑是正确的,避免了项目投资的闲置,也为时隔一年后市场、烟气条件、技术工艺水平提升、调整项目建设思路留下空间。
2.240万吨离子膜烧碱建成为亚硫酸钠续建项目提供原料保证
从目前烧碱用量来看:
公司内部用碱量为87kt/a(不含化工厂亚硫酸钠项目烧碱用量),其中精炼厂用碱40kt/a,实业公司用碱47kt/a。
150kt/a亚硫酸钠项目建成之后烧碱用量为94kt/a,公司内部用碱总量为181kt/a。
公司目前在建的离子膜烧碱项目(一期)将于明年3月建成投产,公司烧碱产能将达到260kt/a,届时,亚硫酸钠生产的主要原料—烧碱供应稳定、充足,这样困扰亚硫酸钠生产多年的原料问题将迎刃而解。
150kt/a亚硫酸钠项目建成之后公司内部用碱总量为181kt/a,项目设计50kt/a固体烧碱,可远距离运输,再加之周边地区烧碱用量,离子膜烧碱一期工程建设后,氯碱基本平衡。
从这个角度上讲,150kt/a亚硫酸钠项目的实施是氯碱平衡的重要途径,否则新建成的烧碱生产线必将会因液碱涨库而难以组织满负荷生产,从而影响整个氯碱产业链的经济运行。
3、亚硫酸钠产品用途及市场情况
3.1产品用途
亚硫酸钠是一种重要的基础化工原料,主要用于造纸工业木质素脱除剂、人造纤维稳定剂、织物漂白剂、照相显影剂、染漂工业脱氧剂、香料和染料还原剂、鞣革工业阻氧剂和医药工业用于生产安乃定和氨基比林以及对氨基水杨酸等产品的还原剂、食品工业生产脱水蔬菜用的还原剂等,还在水处理行业、电子行业、电镀行业、浮选行业等有着广泛的应用。
3.2国际市场情况
美国是亚硫酸钠生产和消费的大国。
据统计,2007年美国的产能已达到310kt/a(折百),需求量为424kt/a。
其亚硫酸钠消费结构为:
造纸制浆:
55%;
水处理:
20%;
照相业:
10%;
纺织印染的漂白、食品的保鲜、化工中间体以及浮油选矿:
油制品的回收:
5%。
作为一种重要的造纸用化学品,亚硫酸钠在制浆造纸工业有着极大的发展潜力,是未来亚硫酸钠市场的主要增长点之一。
在过去20年里,世界造纸工业发展迅速,1998年使用化学品的造纸产量首次突破3亿t,2007年总产量达到了3.7亿t,增长率为2.6%。
出于环境保护的需要,世界制浆造纸工业(尤其是北美、西欧、日本等发达国家或地区)的制浆工艺正越来越多地使用亚硫酸钠。
据预测,今后几年美国、西欧及日本造纸用化学品业务的年均增长率将分别达到3.4%、4.5%和2%。
因此,亚硫酸钠作为一种重要的造纸用化学品将越来越受青睐,市场前景非常广阔。
3.3国内市场情况
3.3.1国内生产情况
2007年国内亚硫酸钠总生产能力为20.5万吨。
全国亚硫酸钠的生产厂家有15家,主要分布在山东、江苏、广东等沿海一带,其规模均在2万吨以下;
西部地区除XX公司外,还有陕西榆林、张掖、内蒙等中小生产企业,主要采用土碱法生产,其产品等级低,主品位一般在85%以下。
3.3.2国内消费情况
从国内消费状况看,亚硫酸钠消费市场比较成熟,其消费结构为:
造纸制浆62%,水处理11%,照相业7%,染漂业5%,食品的保鲜、化工中间体以及浮油选矿等15%。
亚硫酸钠在造纸行业具有用水量少,纸浆及其制品外观好、韧性强,废水可用于植物绿化等优势,受到政策支持,被造纸行业广泛应用。
造纸行业是亚硫酸钠最大的消费市场。
尽管西部地区关停了部分小造纸厂,其目的是控制污染使其生产规模化,但国内用纸的需求量仍在不断增加,造纸总量仍呈上升趋势,据预测,到2010年国内对纸或纸板的需求量将超过8000万吨,亚硫酸钠的需求仍会增加(1吨纸张消耗0.125吨亚硫酸钠)。
近年来,由于国内产业结构的调整和企业重组,东中部江河流域的造纸企业将纸浆生产线转向西部,陕西、宁夏、甘肃、新疆等地成为纸浆制造首选基地,发展异常迅猛。
据不完全调查统计,以上几省的纸浆生产能力已超过200万吨,同时各省重点扶持地市级大造纸、有治污设施的纸浆企业发展,这种整合必将规范本地行业发展格局。
在西部地区纸浆生产主要原料为木材和麦秆,因亚硫酸钠对其纤维素损害较小,部分造纸厂将烧碱法改为亚钠法,使亚硫酸钠的需求量进一步扩大,如张掖造纸厂全部采用亚硫酸钠法生产工艺。
随着我国城镇化水平的不断提高,工业规模的不断扩大,城市及工业废水的排放量不断增加,环保压力逐渐加大。
目前我国的废水处理采用亚硫酸钠的比例远低于国际水平,因此,亚硫酸钠在水处理方面的应用有很大的潜力。
亚硫酸钠在食品添加剂中作漂白剂是亚硫酸钠的传统消费市场,同时它在诸多经处理后的食品以及酒类产品方面,依然是一个效果非常突出的抗氧剂。
我国人口众多,食品添加剂需求增长很快,对亚硫酸钠具有稳定的市场需求增长。
随着我国基础工业的不断发展,尤其是纺织印染与食品保鲜等行业的快速发展,亚硫酸钠市场需求量不断扩大。
据统计我国近五年内亚硫酸钠需求增长率在11%左右,国内对无水亚硫酸钠的消费量在20万吨以上,甘肃及周边地区对七水亚硫酸钠的消费量在9万吨以上。
3.3.3进出口情况
我国亚硫酸钠主要向印度尼西亚、南朝鲜、塞内加尔、南非、阿根廷、日本等国出口;
主要从日本、德国、意大利等国进口高品质亚硫酸钠。
以下是我国2004年至2007年亚硫酸钠的进出口海关数据统计情况:
年份
2004年
2005年
2006年
2007年
进口数量(t)
608
1323
1211
848
出口数量(t)
18320
29509
38821
53672
从上述数据可看出,亚硫酸钠的出口量呈逐年递增趋势远大于进口量,国际市场氛围良好。
我公司生产的优级品亚硫酸钠产品质量已达到美国标准,可以用于出口,同时满足国内食品级和医药行业的要求,可以取代进口亚硫酸钠产品。
3.4公司亚硫酸钠的市场情况
我公司亚硫酸钠销售的目标市场主要是中西部及西南地区,目前除陕、甘、宁、青、新等地区外,还销往广东、深圳、四川、上海等地。
我公司生产的无水亚硫酸钠产品质量较好,得到用户的青睐,产品一直供不应求。
2007年国贸公司通过对已有的客户调查显示(见附图2),目前与我公司联系需求亚硫酸钠的企业有50余家,无水亚硫酸钠的需求量9万余吨/年,七水亚硫酸钠的需求量超过4.6万吨/年,总需求量达到13.6万吨/年,其中四川、陕西两省对无水亚硫酸钠的需求量超过6万吨/年,河西、兰州、宁夏、陕西等地对七水亚硫酸钠的需求量超过4.6万吨/年。
随着公司产量的增加,亚硫酸钠货源供应稳定,加之产品的质量、价格优势,公司亚硫酸钠市场可继续拓展。
我公司曾向日本出口过5吨无水亚硫酸钠。
3.5亚硫酸钠价格分析
根据市场最新报价,亚硫酸钠在沿海一带价格较高,96%的亚硫酸钠价格在3500元/t上下浮动,内地湖南地区报价为2600元/t。
由于造纸企业纸浆生产线转向西部,导致陕西地区96%的亚硫酸钠报价在3600元/t以上,85%的亚硫酸钠价格在1300~1700元/t。
由于公司亚硫酸钠生产所需原料均为公司内部提供,且价格低,有保障,因此公司生产的亚硫酸钠价格优势相当明显。
4、亚硫酸钠扩建的优势比较
4.1原料优势
亚硫酸钠生产所需的主要原料为SO2和烧碱。
本项目的二氧化硫来源于冶炼系统中低浓度烟气,几乎无原料成本,而目前世界硫磺价格的暴涨,导致国内一些以硫磺为原料的亚硫酸钠生产企业成本上涨;
烧碱来源于集团公司在建的40万吨离子膜烧碱项目。
以上两种原料均为公司自产,供应稳定充足,且运输距离近。
4.2技术优势
集团公司化工厂具有多年亚硫酸钠的生产经验,已具备了多项自主开发、自主创新的工艺配置与操作控制技术,并结合硫酸、氯碱的单元操作经验,使亚硫酸钠的单元操作水平有了很大的提升,目前的生产工艺已在国内同领域内保持着领先地位。
4.3产品优势
化工厂拥有多年亚硫酸钠生产控制的经验,可生产出七水亚硫酸钠和无水亚硫酸钠。
七水亚硫酸钠主要满足周边地区的需要,无水亚硫酸钠主要销往省外。
无水亚硫酸钠产品满足食品级和医药行业要求,可以作为精细化工产品的原料,同时达到美国标准,可出口创汇。
4.4规模优势
目前,国内亚硫酸钠总生产能力在20万吨以上,各企业生产规模均不足2万吨。
该项目建成后,公司将形成15万吨亚硫酸钠(10万吨无水亚硫酸钠,5万吨七水亚硫酸钠折百为2.5万吨,共计12.5万吨折百的亚硫酸钠)的生产能力,成为国内最大的亚硫酸钠生产企业。
4.5成本优势
亚硫酸钠生产的方法主要有纯碱法和烧碱法。
纯碱法生产亚硫酸钠二氧化硫的单耗约为0.3t/t,纯碱的单耗为:
0.90t/t,其原料成本为0.3×
4500+0.90×
2000=3150元/t(目前纯碱的市场价为2000元/t,二氧化硫为4500元/t)。
我公司采用烧碱法生产亚硫酸钠,其烧碱的单耗为0.7t/t,二氧化硫来源于冶炼炉窑中低浓度二氧化硫烟气,该法的原料成本为0.7×
1400=980元/t,仅原料成本较纯碱法低2170元/t,成本优势相当明显,且烧碱为公司自产,运输费用较低,同时可减少液体烧碱向固体烧碱转化的投资和加工成本。
为此我公司利用烧碱生产亚硫酸钠的经济优势明显。
5、亚硫酸钠系统建设的现状
化工厂亚硫酸钠是XX集团公司治理低浓度二氧化硫烟气的环保项目,2002年2万吨无水亚硫酸钠建成投产,2004年建设的10万吨七水亚硫酸钠项目,是以减少硫酸外运为主要目的,烟气浓度是以可制酸的SO2浓度5%~5.5%来考虑的。
无水亚硫酸钠因处理气量小,净化、动力系统均借助于原有硫酸生产系统。
随着烟气网络体系的形成和公司污染物治理总的要求,亚硫酸钠生产系统必须处理低浓度二氧化硫(1%~3%)烟气,处理的烟气量将大幅攀升,这样现有系统烟气净化、吸收等装备的能力明显不足,需对其进行完善,使其设备能力达到100kt/a;
中和工序为间歇操作,设备腐蚀严重,劳动强度大,需对其工艺进行优化;
20kt/a无水亚硫酸钠建设时,蒸发、离心分离、干燥、包装等仅预留了30kt/a的设备空间,需进行工艺优化,设备整合,最终形成一个完整的100kt/a无水亚硫酸钠生产线。
5.1二氧化硫的净化与吸收
原无水亚硫酸钠和七水亚硫酸钠的建设烟气浓度是以可制酸的SO2浓度(5%~5.5%)来考虑的,设计烟气流量为6000Nm3/h和3万Nm3/h。
无水亚硫酸钠的净化、动力系统由原有硫酸系统提供,吸收塔直径也仅为2m;
七水亚硫酸钠的净化、吸收系统按3万Nm3/h的处理能力进行建设的。
从目前烟气网络运行看,进入网络体系中的低浓度烟气较多,网络运行较困难,需将一部分烟气做开路处理,而烧碱可以吸收低于3%的低浓度二氧化硫烟气生成亚硫酸钠,因此可将这一部分需要开路的低浓度二氧化硫烟气引入亚硫酸钠生产系统,这样既处理了烟气,又可以提高网络体系中SO2烟气的浓度,为制酸系统的稳定运行提供了条件。
从烟气网络体系中引出烟气,亚硫酸钠生产系统将处理浓度为1%~3%的冶炼烟气,处理气量为10万Nm3/h。
因此,现有净化与吸收系统能力明显不足,需进行扩建。
5.2中和过滤工序
2002年无水亚硫酸钠建设时,中和过滤工序利用原二硫酸车间的干吸循环槽,设计能力仅为20kt/a。
干吸循环槽进行了简单的内衬处理,当时运行良好,但经过多年的运行,现衬里已基本脱落,钢壳体也腐蚀严重,已无法保持正常稳定生产。
因当时的技术限制,中和、过滤设备操作为间断操作,工艺路线复杂,设备过滤效率低,劳动强度大,能耗高,已不能满足大规模的生产需要。
5.3蒸发工序
(1)2002年蒸发工序是按20kt/a无水亚硫酸钠进行设计的,并在厂房配置上预留了30kt/a无水亚硫酸钠的扩建空间,充分利用该空间,并优化系统工艺,采用高效的预蒸发设备,使蒸发能力最终达到100kt/a。
(2)原20kt/a无水亚硫酸钠蒸发器材质为1Cr18Ni9Ti,蒸发室完好,单个加热室面积为158m2,但列管已腐蚀严重(经测量管壁厚度不足2.5mm),局部裂管因渗漏,两端已被堵死,有效加热面积减小。
(3)离心分离机原有两台,按20kt/a无水亚硫酸钠进行设计。
分离机与干燥设备为平面布置,空间狭小,已无扩建空间。
当无水亚钠生产能力达到100kt/a时,需增加四台离心分离机,要重新考虑设备布置。
(4)母液与蒸发液循