电子元件目检设备设计文档格式.docx
《电子元件目检设备设计文档格式.docx》由会员分享,可在线阅读,更多相关《电子元件目检设备设计文档格式.docx(32页珍藏版)》请在冰豆网上搜索。
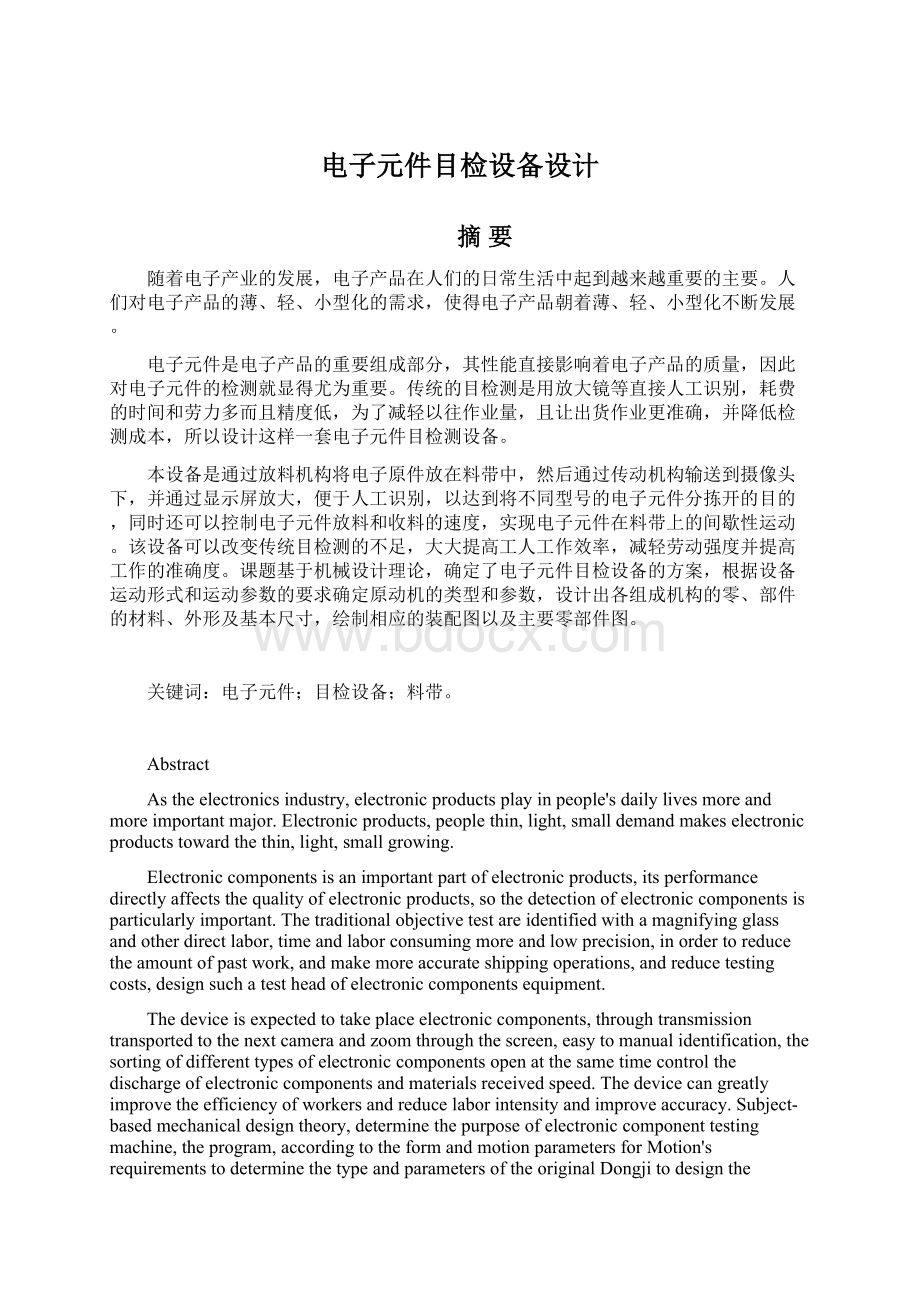
同时,新型电子元件技术的发展体现了当代和今后电子元件向高频化、片式化、微型化、薄型化、低功耗、响应速率快、高分辨率、高精度、高功率、多功能、组件化、复合化、模块化和智能化等发展的趋势,产品的安全性和绿色环保也是其发展方向。
世界电子元件技术片式化、小型化、高精度化、高频率化的发展趋势,在电子元件的各个门类中都得到了充分体现。
1.2本课题的研究意义
电子产品在日常生活与生产当中起着举足轻重的角色,对于电子元件的检测也就固然成了一项很重要的步骤。
由于电子元件体积微小,而且制造精密,通过肉眼直接观察比较难辩别,以往的目检都是用放大镜等直接人工识别,要引进设备又要花费大量的资金,为了减轻以往作业上所需耗费的时间与劳力,且让出货作业更准确,并降低检测成本,所以设计这套方案其目的就是想改进这些不足。
1.3国内外发展现状
电子目检设备的目检测部分所用的机器视觉系统自起步发展到现在,已有15年的发展历史。
应该说机器视觉作为一种应用系统,其功能特点是随着工业自动化的发展而逐渐完善和发展的。
目前,国际上视觉系统的应用方兴未艾,1998年的市场规模为46亿美元。
在国外,机器视觉的应用普及主要体现在半导体及电子行业,其中大概40%-50%都集中在半导体行业。
具体如PCB印刷电路。
主要的机器视觉公司诸如德国克朗斯公司,美国的工业动力机械有限公司等等。
而在国内,工业视觉系统尚处于概念导入期,导致以上各行业的应用很少,即便是有,也只是低端方面的应用,大多数国内公司多代理国外公司产品,自主研发的相对较少,这样产品在国内售价相对很高,导致很多工厂在权衡利弊之后,放弃了使用机器视觉的想法。
但随着我国配套基础建设的完善,技术、资金的积累,各行各业对采用图像和机器视觉技术的工业自动化、智能化需求开始广泛出现,同时也由于视频采集系统硬件产品的价格下降,国内有关大专院校和研究所近两年在图像和机器视觉技术领域进行了积极思索和大胆的尝试,逐步开始了工业现场的应用。
另外,各行业的领先企业在解决了生产自动化的问题以后,已开始将目光转向视觉测量自动化方面。
这些应用大多集中在如电子元件目检测、药品检测分装、印刷色彩检测等。
真正高端的应用还很少,因此,以上相关行业的应用空间还比较大。
[1]
2总体方案的确定
本方案拟定电子元件在皮带轮上传动,通过目检测设备自动检测电子元件,从而达到区分各类元件的目的,该设备的组成部分主要有:
电动机、减速器、传动设备、料带收放料机构、目检测设备等。
整套设备通过一个料带放料机构将装有电子元件的料带输送到料带轨道中,通过皮带传动,将料带传输到检测设备下进行检测,最后再由收料机构卷收到料带盘中。
其传动部分简图如下:
图1-1传动结构简图
3原动机的选定
3.1原动机的分类
电动机俗称马达,是一种将电能转化成机械能,并可再使用机械能产生动能,用来驱动其他装置的电气设备。
电动机驱动电气设备,是系统运行的基础部分,因此电动机的选择就显得尤为重要。
电动机的种类有很多:
①按工作电源分类根据电动机工作电源的不同,可分为直流电动机和交流电动机。
其中交流电动机还分为单相电动机和三相电动机。
②按结构及工作原理分类电动机按结构及工作原理可分为直流电动机,异步电动机和同步电动机。
③按起动与运行方式分类电动机按起动与运行方式可分为电容起动式单相异步电动机、电容运转式单相异步电动机、电容起动运转式单相异步电动机和分相式单相异步电动机。
④按用途分类电动机按用途可分为驱动用电动机和控制用电动机。
⑤按转子的结构分类电动机按转子的结构可分为笼型感应电动机和绕线转子感应电动机。
⑥按运转速度分类电动机按运转速度可分为高速电动机、低速电动机、恒速电动机、调速电动机。
电动机种类多种多样,不同的电动机有不同的用途,它们使用的场合也不同。
根据原始资料料带送料为间歇运动,每传输五个电子原件,停止2秒,因此电动机的选择应该能够实现料带间歇运动,步进电动机的步距角0.72度刚好能被旋转一周的角度360度整除,能满足送料时的运动方式。
因此,本系统的原动机选择步进电动机。
[2]
3.2步进电动机的优点
随着数控技术及电子设备的发展,特别是电子计算机的普及,就有了步进电动机,其新型驱动方式也不断出现,为步进电动机的应用带来了广阔的前景。
步进电动机是一种以电脉冲信号进行控制,并将电脉冲信号转换成相应的角位移或线位移的控制电动机。
与其他电动机相比它有很多优点:
每步的精度在3%-5%,而且不会将一步的误差积累到下一步因而有较好的位置精度和运动的重复性;
有着优秀的起停和反转响应;
没有电刷,可靠性较高电机的响应仅由数字输入脉冲确定,因而可以采用开环控制,这使得电机的结构可以比较简单而且控制成本;
速度正比于脉冲频率,因而有比较宽的转速范围。
步进电动机是一种将电脉冲转化为角位移的执行机构。
当步进驱动器接收到一个脉冲信号,它就驱动步进电机按设定的方向转动一个固定的角度(称为“步距角”),它的旋转是以固定的角度一步一步运行的。
可以通过控制脉冲个数来控制角位移量,从而达到准确定位的目的;
同时可以通过控制脉冲频率来控制电机转动的速度和加速度,从而达到调速的目的。
步进电机可以作为一种控制用的特种电机,利用其没有积累误差(精度为100%)的特点,广泛应用于各种开环控制。
3.3步进电动机的选型
根据原始资料料带送料为间歇运动,每传输五个电子原件,停止2秒,步进电动机的步距角0.72度刚好能被旋转一周的角度360度整除,所以能满足送料时的运动方式。
有效地解决料带间歇运动的问题。
根据已知条件,选择的步进电动机型号90BF006(BF系列步进电动机)其的具体参数如下:
表3.1步进电动机参数
品名
最大
静力矩
(
)
相数
额定电流(A/相)
基本步距角(度)
输入电源
脉冲数(step/s)
90BF006
2.156
五相十拍
3A
0.36
24V
2400
电动机外形尺寸:
φ90×
65mm[3]
4减速器的确定
4.1减速器的分类
减速器是原动机和工作机之间的独立的闭式传动装置,用来降低转速和增大转矩,以满足工作需要,在某些场合也用来增速,称为增速器。
减速器的类别、品种、型式很多,目前已制定为行(国)标的减速器有40余种。
减速器的类别是根据所采用的齿轮齿形、齿廓曲线划分;
减速器的品种是根据使用的需要而设计的不同结构的减速器;
减速器的型式是在基本结构的基础上根据齿面硬度、传动级数、出轴型式、装配型式、安装型式、联接型式等因素而设计的不同特性的减速器。
[4]
4.2减速器齿轮的计算
4.2.1原动机参数
P=24*3=72w
n=360/0.36=1000
各级传动比分配初定
传动装置总效率:
(弹性联轴器)
(滚动轴承)
(圆柱齿轮传动)
各轴转速
n0=nm=1000r/min
n1=nm=1000r/min
n2=n1/i1=250r/min
n3=n2/i2=82.236r/min
各轴输入功率
p0=ped=72w
p1=p0*η1=71.27w
p2=p1*η2*η3=68.45w
p3=p2*η2*η3=65.73w
各轴转矩
T0=9550P0/n0=0.6876N.m
T1=9550P1/n1=0.681N.m
T2=9550P2/n2=2.615N.m
T3=9550P3/n3=6.633N.m
4.2.2高速级减速齿轮设计(直齿圆柱齿轮)
1.齿轮的材料,精度和齿数选择,因传递功率不大,转速不高,,小齿轮采用40Cr,大齿轮采用45号钢,锻造毛坯,大、小齿轮均调质处理,均用软齿面。
齿轮精度用7级,轮齿表面精糙度为Ra1.6,软齿面闭式传动,失效形式为点蚀。
[5]
2.设计
(1)设计准则,按齿面接触疲劳强度计算,再按齿根弯曲疲劳强度校核。
考虑传动平稳性,齿数宜取多些,初步取Z1=23Z2=72
(2)按齿面接触疲劳强度设计,
T1=9550P/n=681N·
mm
确定公式的各计算数值
1)试选载荷系数kt=1.3
2)小齿轮转矩T2=2615N·
3)选取齿宽系数φd=1
4)查得材料的弹性影响系数zE=189Mpa
5)选取材料的接触疲劳,极限应力为
бHILim=600MPaбHILin=550MPa
6)应力循环次数N
N1=60n1jLh=0.504×
109
N2=N1/i2=0.166×
7)查得接触疲劳寿命系数;
KHN1=0.93;
KHN2=0.95
8)取接触疲劳安全系数:
SFmin=1
3.计算
1)试计算小齿轮分度圆直径将有关值代入得
D1t=19.58
2)计算圆周速度
V1=πd1tn1/(60×
1000)=0.51m/s
3)计算齿宽b
b=φd*d1t=19.58mm
4)计算齿宽与齿高之比
模数mt=d1t/z1=2.00
齿高h=2.25mt=4.50mm
b/h=10.67
5)计算载荷系数
根据V1=0.51m/s,7级精度,查得KV=1.04;
直齿轮,KHα=KFβ=1;
使用系数kA=1.00
用插值法查得7级精度小齿轮相对支承非对称布置时kHβ=1.419
由b/h=10.67,kHβ=1.419查得KFβ=1.34
所以K=KAKVKHαKHβ=1.476
6)按实际的载荷系数校正所得的分度圆直径:
d1=d1t
=20.4
7)计算模数m=d1/z1=2.09mm
按齿轮根弯曲强度设计得弯曲强度的设计公式
确定公式内的各计算数值
小齿轮的弯曲疲劳强度极限σFE1=500MPa
大齿轮的弯曲疲劳强度极限σFE1=380MPa
KFN1=0.90KFN1=0.93
取弯曲疲劳安全系数S=1.4
计算载荷系数k=KAKVKFαKFβ=1.394
齿形系数YFa1=2.65Ysa1=1.58
YFa2=2.246Ysa2=1.756
代入数据得
取标准模数:
m=3mm
按接触强度算得分度圆直径d1=16.86mm
Z1=d1/m=17
Z2=z1×
i1=52
计算几何尺寸
d1=mZ1=16mm
d2=mZ1=52mm
a=m(d1+d2)/2=34.84mm
b=φddt=17mm
取B2=17mmB1=19mm
4.2.3低速级减速齿轮设计(直齿圆柱齿轮)
1.齿轮的材料,精度和齿数选择,因传递功率不大,转速不高,材料按表7-1选取,小齿轮采用40Cr,大齿轮采用45号钢,锻选项毛坯,大、小齿轮均调质处理,均用软齿面。
考虑传动平稳性,齿数宜取多些,取Z1=24[7]
则Z2=Z1*i2=73
T2=9550P2/n2=38910N·
选取材料的接触疲劳,极限应力为
бHILim=600MPaбHILin=550MPa
应力循环次数N
N1=60n,at=60×
366.5×
(10×
3300×
10)=0.504×
N2=N1/i2=0.166×
接触疲劳寿命系数;
KHN1=0.93;
取接触疲劳安全系数:
将有关值代入
则V2=πd2tn2/(60×
1000)=0.88m/s
根据V1=0.95m/s,7级精度,KV=1.04;
直齿轮,KHα=KHβ=1;
由b/h=8.89得KFβ=1.34
所以K=KAKVKHαHβ=1.476
d1=16.86
m=d1/Z1=2.09mm
2)按齿轮根弯曲强度设计;
小齿轮σFE1=500MPa
大齿轮σFE1=380MPa
KFN1=0.90KFN2=0.93
计算载荷系数k=kAkVkFαkFβ=1.394
由表10-5查得YFa1=2.65Ysa1=1.58
(3)计算几何尺寸
d1=mZ1=3×
17=17mm
d2=mZ1=3×
52=52.5mm
b=φddt=17.2mm
2.设计计算。
总结:
高速级z1=26z2=104m=1.25
低速级z1=17z2=52m=3
4.3轴的设计
4.3.1输出轴参数的设计
由于减速器传递的功率不大,对其重量和尺寸也无特殊要求故选择常用材料45钢,调质处理。
[8]
1、输出轴上的动力参数
T3=9550P3/n3=113.77N.m
p3=p2*η2*η3=1.370kw
n3=n2/i2=115r/min
2、求作用在齿轮上的力
已知大齿轮的分度圆直径d2=mZ1=52.5mm
圆周力Ft=2T3/d2=1458.59N
径向力Fr=Fttant20=530.88N
3、初步估计轴的最小直径
按扭矩初估轴的直径,c=106至117,考虑到安装联轴器的轴段仅受扭矩作用.取c=112则:
输出轴的最小直径显然是安装联轴器处轴的直径,为了使所选的轴的直径与联轴器的孔径相适应,需同时选取联轴器型号。
联轴器的计算转矩Tca=KAT3,查表,考虑到转矩变化很小故选取KA=1.3,则Tca=14970N.mm
按照计算转矩应小于联轴器公称转矩的条件,选用HL2型弹性柱销式联轴器,其公称转矩为315000N.mm,半联轴器的孔径d=28mm,故轴最小直径dmin=28mm,半联轴器长度L=62mm,半联轴器与轴配合的毂孔长度L1=44mm。
4.3.2轴的结构设计
1、拟定轴上零件的装配方案
2、根据轴向定位的要求确定轴的各段直径和长度
1)为了满足半联轴器的轴向定位要求,1-2轴段右端面需制出一轴肩,故2-3段的直径d2-3=28+(0.07-0.1)*28=32mm;
左端用轴端挡圈定位,按轴端直径取挡圈直径D=35mm,半联轴器与轴配合的毂孔长度L1=44mm,为了保证轴端挡圈只压在半联轴器上而不压在轴的端面上,故1-2段的长度应比L1略短一些,现取L1-2=42mm。
2)初步选择滚动轴承
因轴承只承受径向力,故选用深沟球轴承,参照工作要求并根据d2-3=32mm。
初步选取0基本游隙,标准精度等级的深沟球轴承6007,其基本尺寸d*D*B=35mm*62mm*14mm,故d3-4=d7-8=35mm,而L7-8=14mm。
右端轴承采用轴肩定位,由设计手册查得6007型轴承定位轴肩的高度h=3,因此取d6-7=41mm。
3)取安装齿轮的轴段d4-5=40mm;
齿轮的左端与左端轴承之间采用套筒定位。
已知齿轮轮毂宽度为51mm,为了使套筒端面可靠的压紧齿轮,此轴段应略短于轮毂的宽度,取为L4-5=48mm。
齿轮右端面采用轴肩定位,轴肩的高度h>
0.07d,取h=3mm,则轴环处的直径d5-6=46mm,轴环的宽度b≥1.4h,取L5-6=6mm。
4)轴承端盖的总长度为20mm,根据轴承端盖的装拆及便于对轴承润滑的要求,取端盖与半联轴器右端面的距离l=20mm,故L2-3=40mm。
5)取齿轮距箱体内壁的距离a=10,考虑箱体的铸造误差,在确定轴承的位置时,应距箱体的内壁一段距离S-5mm,已知滚动轴承宽度B=14mm,中间轴大齿轮宽度B2=32.5mm,则L3-4=B+S+a+(56-53)=32mm,L6-7=76.5mm。
4.3.3轴上零件的周向定位。
齿轮、半联轴器与轴的周向定位均采用平键联接,按d4-5由表6-1查得平键截面b*h=12mm*8m,键槽长度36mm,同时为了保证齿轮与轴配合有良好的对中性,选择齿轮轮毂与轴的配合为H7/h6;
同样半联轴器与轴的连接选用平键8mm*7mm*36mm,半联轴器与轴的配合为H7/k6,滚动轴承与轴的周向配合是由过渡配合来保证的,此处选用轴的直径尺寸公差为m6。
[10]
4.4润滑与密封及箱体尺寸
4.4.1润滑与密封
1、齿轮的润滑
采用浸油润滑,由于低速级周向速度为,所以浸油高度约为六分之一大齿轮半径,取为35mm。
2、滚动轴承的润滑
由于轴承周向速度为,所以宜开设油沟、飞溅润滑。
3、润滑油的选择
齿轮与轴承用同种润滑油较为便利,考虑到该装置用于小型设备,选用L-AN15润滑油。
4、密封方法的选取
选用凸缘式端盖易于调整,采用闷盖安装骨架式旋转轴唇型密封圈实现密封。
密封圈型号按所装配轴的直径确定为(F)B25-42-7-ACM,(F)B70-90-10-ACM。
轴承盖结构尺寸按用其定位的轴承的外径决定。
4.4.2箱体尺寸:
箱体壁厚
箱盖壁厚
箱座凸缘厚度b=12mm
箱盖凸缘厚度b1=12mm
箱座底凸缘厚度b2=20mm
5带传动的设计
5.1带传动
同步带传动综合了带传动和链传动的优点。
同步带通常是以钢丝绳或玻璃纤维等为抗拉层、氯丁橡胶或聚氨酯橡胶为基体、工作面上带齿的环状带。
工作时,带的凸齿与带轮外缘上的齿槽进行啮合传动。
由于抗拉层承载后变形小,能保持同步带的周节不变,故带与带轮之间没有相对滑动,从而保证了同步传动。
同步带传动时,传动比准确,对轴作用力小,结构紧凑,耐油,耐磨性好,抗老化性能好,一般使用温度-20℃―80℃,v<
50m/s,P<
300kw,i<
10,对于要求同步的传动也可用于低速传动。
根据本课题要求设计传动精度较高的传动装置,同步带传动符合设计要求,它具有以下的优点:
a)无滑动,能保证固定的传动比,本课题设计的传动比为1:
1具要求传动精准;
b)预紧力较小,轴和轴承上所受的载荷小,本课题设计的轴尺寸本身比较小,所以