热电厂锅炉炉膛温度控制课程设计说明书111111Word文件下载.docx
《热电厂锅炉炉膛温度控制课程设计说明书111111Word文件下载.docx》由会员分享,可在线阅读,更多相关《热电厂锅炉炉膛温度控制课程设计说明书111111Word文件下载.docx(15页珍藏版)》请在冰豆网上搜索。
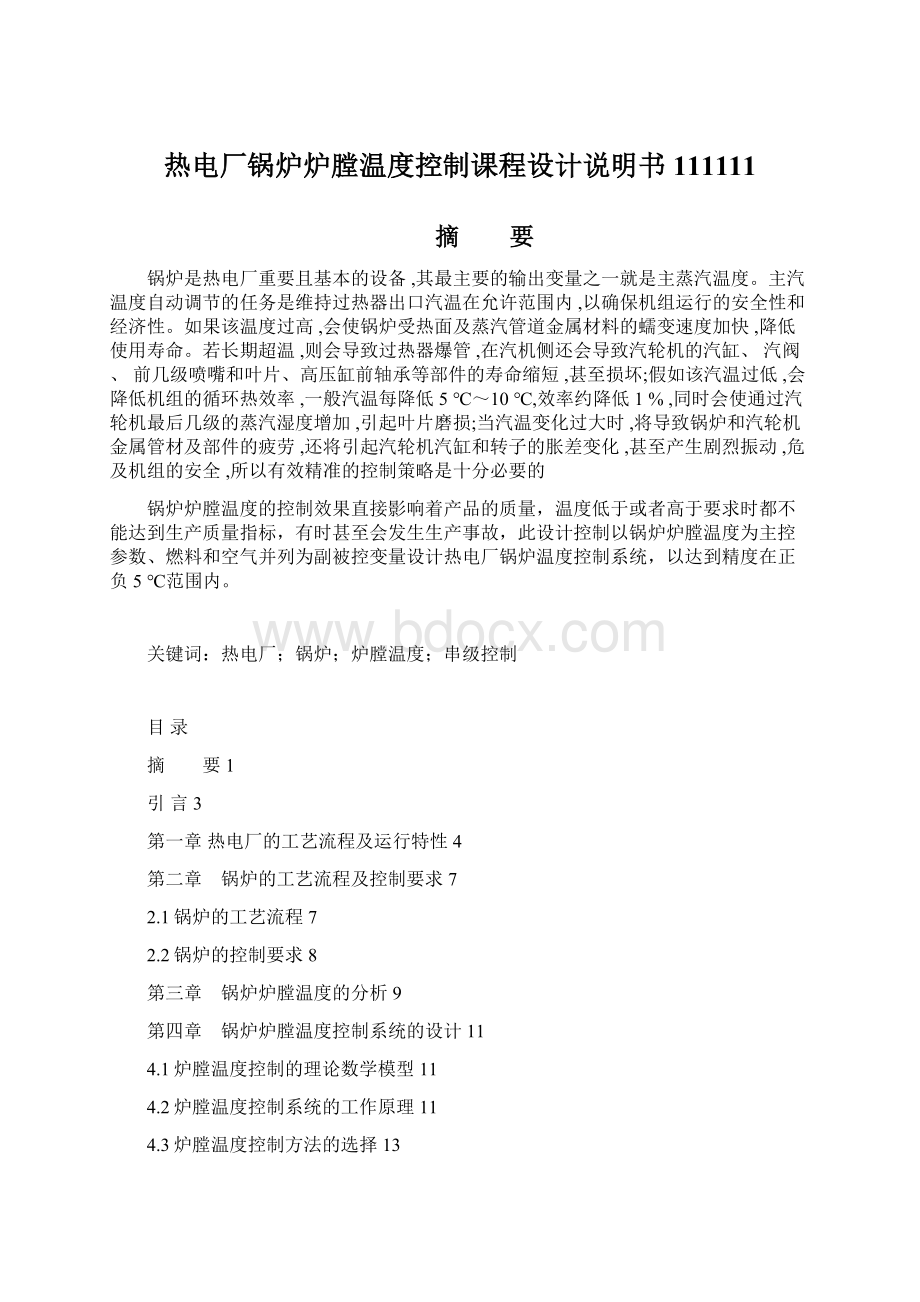
而单回路控制系统往往不能满足生产工艺的要求,在这样的情况下,串级控制系统应运而生。
锅炉温度串级控制系统的生产工艺要求:
(1)可以实现对整个锅炉系统工艺流程的控制。
(2)能够自动控制锅炉温度,并达到所需精度。
(3)有良好的人机界面,能方便地在线修改参数,并以动画实现数据和流程的“可视化。
工程控制是工业自动化的重要分支。
几十年来,工业过程控制获得了惊人的发展,无论是在大规模的结构复杂的工业生产过程中,还是在传统工业过程改造中,过程控制技术对于提高产品质量以及能源的节约都起着重要的作用。
生产过程是指物料经过若干加工步骤而成为产品的过程。
该过程中通常会发生物理化学反应、生化反应、物质能量的转换与传递等等,或者说生产过程表现为物流过变化的过程,伴随物流变化的信息包括物流性质的信息和操作条件的信息。
生产过程的总目标,应该是在可能获得的原料和能源条件下,以最经济的途径,将原物料加工成预期的合格产品。
为了打到目标,必须对生产过程进行监视和控制。
因此,过程控制的任务是在了解生产过程的工艺流程和动静态特性的基础上,应用理论对系统进行分析与综合,以生产过程中物流变化信息量作为被控量,选用适宜的技术手段。
实现生产过程的控制目标。
第一章热电厂的工艺流程及运行特性
1.1热电厂生产工艺
原煤经过制粉系统将大块的煤转化成可供锅炉燃烧的煤粉,生水经过水处理系统再经过除盐处理而除去水质里的钙、镁、钠等盐分子,然后通入锅炉,锅炉里的煤粉和通入的热空气经过一定比例的混合后燃烧使得锅炉产生蒸汽,这些高温的蒸汽通过汽轮机,使得汽轮机高速运转产生的旋转机械能,发电机连接着汽轮机,发电机将汽轮机产生的旋转机械能转化成电能,这些电压不定的电力在主变压器的作用下变成一定电压的电量,经过高压远程输电送入各个电网输送到全国各地
热电厂是联合生产电能和热能的发电厂。
热电厂供热系统是利用汽轮机同时生产电能和热能的热电系统作为热源。
以热电厂作为热源不仅热能利用效率高,同时有利于环保。
以热电厂作为热源的供热系统称为热电厂集中供热系统。
集中热水供应系统主要由热媒系统,热水供应系统和附件三个部分组成。
热媒系统由热源,换热器和热媒管网组成。
由锅炉生产的蒸汽通过热媒管网送到换热器加热冷水,变成高温水通过热媒管网供暖。
经过热交换蒸汽变成冷凝水,大部分和新补充的软化水经冷凝循环泵再送回锅炉加热成蒸汽,如此循环完成热传递过程。
热水供水系统由热水配水管网和回水管网组成。
被加热到一定温度的冷水,从换热器出来,经配水管网送至各个热水配水点,而换热器冷水由高位水箱或给水管网补给。
供热后的热水经回水管使一定量的热水经过循环水泵再流回换热器。
热电厂包含有火力发电厂车间、水处理车间和热力车间三个部分。
其中火力发电厂流程为燃料的化学能→蒸汽的热势能→机械能→电能。
在锅炉中,燃料的化学能转变为蒸汽的热能;
在汽轮机中,蒸汽的热能转变为轮子旋转的机械能;
在发电机中机械能转变为电能。
水处理系统就是为了产出电导率<
0.6us/cm的锅炉用水。
热电厂主要是有两个阴床,两个阳床和两个混床,在其工作的时候,分别就一个工作,另一个主要是备用。
另外,热力车间燃气蒸汽联合循环发电装置一般由燃气轮机、原料气压缩机、蒸汽轮机、余热锅炉、热交换器、发电机等组成。
燃气轮机的燃料主要有油、高炉煤气、水煤气、炼油长气等,如下图1.1
图1.1热电厂生产工艺流程图
1.2热电厂的特点及运行特性
热电厂由于即发电又供热,锅炉容量大于同规模火电厂。
热电厂必须比一般火电厂多增设锅炉容量以备用,水处理量也大。
热电厂必须靠近热负荷中心,往往又是人口密集区的城镇中心,其用水、征地、拆迁、环保要求等均大大高于同容量火电厂,同时还建热力管网。
在发电的同时,还利用汽轮机的抽汽或排汽为用户供热的火电厂。
一般发电厂都采用凝汽式机组,只生产电能向用户供电。
工业生产和人们生活用热则由特设的工业锅炉及采暖锅炉房单独供应。
这种能量生产方式称为热、电分产。
在热电厂中则采用供热式机组,除了供应电能以外,同时还利用作过功(即发了电)的汽轮机抽汽或排汽来满足生产和生活上所需热量。
这种能量生产方式称为热电联产。
在热电联产中燃料化学能则转变为高位热能先用来发电(高品位热能),然后使用做过功的低品位热能向用户供热,这符合按质用能和综合用能的原则。
所以热电厂的特点是,一次能源利用得比较合理,做到按质供能,梯级用能,能尽其用,使地区的整个能量供应系统节约了能源。
以热电联产为基础的热电厂,其运行特点与许多因素有关,如热负荷特性、供热机组形式、连接电网的特性等。
在装有背压式供热机组的热电厂中,其运行特点是:
①生产的热量与电量之间相互制约,不能独立调节。
一般是按热负荷要求来调节电负荷。
②热负荷变化时,电功率随之变化,难以同时满足热负荷和电负荷要求。
当满足不了电负荷时,就要依靠电力系统的补偿容量来承担热电厂发电不足的电量。
在装有抽汽、凝汽式供热机组的热电厂中,由于机组相当于背压式和凝汽式机组的组合,所以它的运行特点是:
①热、电生产有一定的自由度,在规定范围内热、电负荷可以各自独立调节。
所以它对热、电负荷变化适应性较大。
②双抽汽式供热机组对工业用热、采暖及电负荷之间的独立调节范围更大,所以它对热、电负荷变化的适应性更强。
第二章 锅炉的工艺流程及控制要求
2.1锅炉的工艺流程
由于锅炉设备使用的燃料、燃烧设备、炉体形式、锅炉功用和运行要求的不同,锅炉有各种各样的流程。
常见流程如图2.1所示。
由图可知,蒸汽发生系统由给水泵、给水调节阀、省煤器、汽包及循环管组成。
燃料和热空气按照一定的比例进入燃烧室燃烧,产生的热量传递给蒸汽发生系统,产生饱和蒸汽
然后经过热器,形成一定汽温的过热蒸汽
,汇集至蒸汽母管。
压力为
的过热蒸汽,经负荷设备调节阀供给生产负荷使用。
与此同时,燃烧过程中产生的烟气,将饱和蒸汽变成过热蒸汽后,经省煤器预热锅炉给水和空气预热器预热空气,最后经引风机送往烟囱排入大气。
图2.1锅炉系统工艺流程图
2.2锅炉的控制要求
根据生产负荷的不同需要,锅炉需要提供不同规格(压力和温度)的蒸汽,同时,根据安全性和经济性的要求,是锅炉安全运行和完全燃烧,锅炉设备的主要控制要求如下。
1、供给蒸汽量适应负荷变化需要或者保持给定负荷;
2、锅炉供给用汽设备的蒸汽压力应当保持在一定的范围内;
3、过热蒸汽温度保持在一定范围;
4、汽包水位保持在一定范围;
5、保持锅炉燃烧的经济性和安全性;
6、炉膛负压保持在一定的范围内。
根据上述要求,锅炉设备的主要控制系统见表2.1.
表2.1锅炉设备的主要控制系统
控制系统
被控变量
操纵变量
控制目的
锅炉给水控制系统
锅炉汽包水位
给水流量
锅炉内产生的蒸汽和给水的无聊平衡
过路燃烧控制系统
蒸汽压力
烟气成分
炉膛负压
燃料流量
送风流量
引风流量
蒸汽负荷的平衡
燃烧的完全和经济性
锅炉运行的安全性
过热蒸汽控制系统
过热蒸汽温度
喷水流量
过热蒸汽的温度和安全性
第三章 锅炉炉膛温度的分析
火电厂的锅炉炉膛由于采用的燃料为煤粉,在燃烧过程中,炉膛和汽包之间的传热过程是一个相当复杂的过程,炉膛的温度的动态特性具有一般的大滞后、时变、非线性和不对称性等特点。
在过程控制中,为了方便设计,同时又在一定的要求范围内,我们通常把锅炉炉膛的温度的动态特性看作是一个线性的系统。
可以用以下传递函数描述。
具有时滞的一阶环节
(式3-1)
具有时滞的二阶环节
(式3-2)
在现场环境中,炉膛内的温度变化是时时刻刻的,很难用一个固定的数学公式将炉温的变化规律总结出来。
但是我们要对炉膛内的温度进行控制就必须要对炉膛内的温度变化进行一个规律的总结,所以在规定的要求范围内,对一些情况进行近似处理是很合理和必要的。
在通常情况下,我们给定炉膛一个温度值,作为系统的给定,使锅炉炉膛在这个给定的温度状态下工作。
这个温度的变化又是和炉内的燃料燃烧量和炉体的总散热量相关的。
对于火电厂锅炉来说,炉体的容量、结构、检测元件及其安放位置等都影响着滞后的大小。
它不是一个单一的问题,是一个系统问题(容积滞后时间就是级联的各个惯性环节的时间常数之和)。
纯滞后产生的根源也要从整个测量系统来考虑,并且与温度的高低有关。
热量从热源传到温度传感器要经过多个热阻与热容相串联的热惯性环节,而串联的多容对象会产生等效纯时滞后。
随着温度的升高,辐射传热的比例增大,辐射具有穿透性,使传热路径缩短,传热速度加快。
所以纯滞后的时间会随温度升高而减小。
由于火电厂锅炉使用的燃料是煤粉,即锅炉能量的来源方式是通过化学燃料的燃烧获得能量的,同时,炉膛内能量的散发形式又是以炉膛的炉体热量散失,对汽包进行热量传导进行散失等多种途径进行的,所以炉膛内的温度的变化是一个相当复杂的过程,是一个非线性变化的过程。
从模型参数上看,在锅炉炉膛的整个温度调节范围内,对象的增益、容积滞后时间和纯滞后时间通常是与工作温度与负载变化有关的变参数,而且参数变化量与温度变化量之间是非线性关系。
由于锅炉炉膛内的温度是高温段的,在高温段,温度变化的纯滞后时间和过程增益将比低温段有显著减少,而时间常数则显著增大。
锅炉作为一种高负荷运转的设备,特别是火电厂内的锅炉,长期处于高负荷运转下,随着运行时间的变化,其各项性能都会逐渐发生变化,特别是随着使用时间的增长,炉子的保温隔热材料会逐渐老化,炉膛内部由于长期处于高温环境中,炉体的保温、密封性能变差,通过炉体向外散失的热量增大。
此外,锅炉初次使用和久停后再用时,由于绝热保温材料中的水分大,炉膛温度的特性差别也是很大的。
另外,随着季节的变换,锅炉运行的外部环境温度也是经常变化的,冬天外部环境相对较冷,炉体的散热较快;
夏天气温炎热,炉体的散热相对会较慢。
如此种种因素都会引起炉膛温度特性的变化,但变化的速度十分缓慢而不明显。
火电厂锅炉炉膛温度具有大惯性、大滞后特性。
在炉膛的整个温度范围内,对象的增益、容积滞后时间、纯滞后时间都是与工作温度有关的变参数。
从传热原理可知,这些参数也与负荷变化有关。
在锅炉设计的工作温区,在工作点附近的小范围内其动特性接近于线性,较容易控制,用常规的PID调节器也能控制得很好,但不能经受太大的扰动,也不能够大范围地跟踪变化较快的给定信号。
对于常规仪表,大范围地改变温度要靠手动,仅当温度接近给定值时方可投入自动。
根据以上分析,可以认为火电厂锅炉炉膛温度是一种具有大容积滞后和大纯滞后的对象。
在整个炉膛的温区内,其动态参数随锅炉的工作温度变化,在工作点附近的小温度范围内,炉膛的动态特性近似线性的。
第四章 锅炉炉膛温度控制系统的设计
4.1炉膛温度控制的理论数学模型
根据以上分析可知,炉膛温度问题是比较复杂的。
对炉膛温度动态特性进行分段线性化,则在每个较小的温度区间,锅炉炉膛的燃料流量—炉膛温度系统的动态特性可近似地用一个惯性环节和一个纯滞后环节串联的简化模型来表征,即:
(式4-1)
其中K。
为过程的增益,
为过程的纯滞后时间,To为过程的等效容积滞后时间。
在锅炉炉膛的整个温度范围内,对象的增益、容积滞后时间和纯滞后时间都是炉膛温度和负载的非线性函数。
K。
随锅炉炉膛内温度升高而减小,To随锅炉炉膛内的温度升高而增大。
机理建模和计算机仿真分析以及实验辨识等也证明了这一模型的可行性。
4.2炉膛温度控制系统的工作原理
锅炉炉膛温度的控制,我选用普通的PID控制,由PID作为基本的控制算法。
在此次设计中我采用串级回路控制方法。
本系统具有2个调节器和2个闭合回路,2个调节器分别设置在主、副回路中,设在主回路的调节器称主调节器,设在副回路的调节器称为副调节器。
两个调节器串联连接,主调节器的输出作为副回路的给定量,副调节器的输出去控制执行元件
串级调节系统多用于燃料源受频繁扰动的锅炉炉膛,该系统由主回路和副回路组成,主回路根据实际值与给定值的偏差由PID调节规律对燃料流量进行调节,副回路根据燃料流量实际值与主回路温度调节器输出的燃料流量的偏差对流量进行调节,以避免扰动对燃料流量的影响。
在系统稳定状态时,温度PID的输出以A1送到煤粉流量调节回路PID作为设定值,以B1送到空气流量调节回路PID作为设定值。
在负荷剧增(温测<
温给)时,温度PID的输出剧增.对于空气流量调节回路,随着B1开始增加时,B1<
B2,低选器选中B1,空气流量增加,当B1正跳变到B1>
B2时,低选器选中B2,B1被中断,同时B3<
B2,高选器选B2,B2作为该回路PID的设定值,使空气流量随着煤粉流量的增加而增加,交叉限制作用开始,当B2增加到B2>
B1时,低选器又选中B1,B1又作为该回路PID设定值,交叉限制作用结束,系统稳定。
对于煤粉流量调节回路,随着煤粉流量的增加,高选器选A1,而低选器中,开始时选A1作为该回路PID的设定值,煤粉流量增加,A1>
A2时,低选气选A2,A1被中断,煤粉流量随着空气流量增加而增加,交叉限制作用开始,当A2增加到A2>
A1时,低选器又选A1,此时A1>
A3,使交叉限制作用结束,系统恢复稳定。
负荷剧减时相反。
可见负荷增加过程中,先开空气后开煤粉,煤粉和空气交替逐渐增加,从而保证充分燃烧,不产生黑烟。
负荷减少时,先关煤粉后关空气,空气和煤粉交替逐渐减少,保证合理燃烧,不会空气过剩,带走热量。
图4.1锅炉炉膛温度控制系统框图
4.3炉膛温度控制方法的选择
以锅炉炉膛温度为主被控量、燃料和空气并列为副被控变量的串级控制系统。
其中,两个并列的副环具有逻辑比值功能。
使该控制系统在稳定工作的情况下保证空气和燃料的最佳比值,也能在动态过程中尽量维持空气、燃料在最佳比值附近。
4.4控制系统单元元件的选择
4.4.1温度检测变送器的选择
热电偶温度变送器与各种测温热电偶配合使用,可将温度信号线性地转换成为4~20mADC电流信号或1~5VDC电压信号输出,它是由量程单元和放大单元两部分组成的。
热电偶温度变送器的主要特点是采用非线性负反馈回路来实现线性变化。
表4.1不同类型的温度变送器对比
类别
材
质
分度号
测量范围
热
电
偶
镍铬-康铜
E
0-1000℃范围内任选
镍铬-镍硅
K
0-1300℃范围内任选
铂铑10-铂
S
0-1600℃范围内任选
铂铑30-铂铑6
B
0-1800℃范围内任选
铜-康铜
T
0-400℃范围内任选
铁-康铜
J
0-1200℃范围内任选
阻
铜热电阻
Cu50
-50-+150℃范围内任选
Cu100
-50-+15℃范围内任选
铂热电阻
Pt100
-200-+600℃范围内任选
由表4.1可以看出,由于锅炉炉膛内的温度较高,而热电阻温度变送器的测量范围较小,所以在这里我选用热电偶温度变送器,热电偶温度变送器与各种测温热电偶配合使用,可将温度信号线性地转换成为4~20mADC电流信号或1~5VDC电压信号输出,它是由量程单元和放大单元两部分组成的。
在同样的都满足测量要求的条件下,考虑到经济性的原则,我选用的是DBW-1150型热电偶温度变送器。
DBW-1150型热电偶温度变送器是DDZ-III系列仪表的主要品种。
本温度变送器用热电偶作为测温元件,将被测温度线性地转换成标准信号1-5VDC或4-20mADC输出,供给指示、记录、凋节器、计算机等自动化监控系统。
技术参数:
◆输
入:
标准热电偶
出:
输出电流:
4~20mADC
输出电压:
1~5VDC
输出电阻:
250Ω
允许负载变化范围:
100Ω
◆量程:
0~1600℃
◆冷端补偿误差:
≤1℃
◆温度漂移:
≤0.1×
基本误差/1℃
◆绝缘电阻:
电源、输入与输出端子间≤100MΩ
◆绝缘强度:
电源/输入/输山端子间1500VAC/分钟
◆工作条件:
环境温度:
0~50℃
相对湿度:
≤90%(RH)
◆电源电压:
24VDC±
5%
◆功
耗:
<2W
◆防爆等级:
(ib)IICT6
◆重
量:
<2Kg
4.4.2流量检测变送器的选择
本次流量变送的对象是煤粉和空气,所以在选择流量变送装置的时候,必须能够既测量煤粉固体颗粒,又能测量气体的流量。
由于炉膛内的是热空气,所以还要求变送装置能够在一定的高温下工作,所以根据具体情况,我们可以选用LUGB型涡街流量计。
LUGB型涡街流量计根据卡门涡街原理测量气体、蒸汽或液体的体积流量、标况的体积流量或质量流量的体积流量计。
广泛用于各种行业气体、液体、蒸汽流量的计量,也可测量含有微小颗料、杂质的混浊液体,并可作为流量变送器用于自动化控制系统中。
LUGB型涡街流量传感器防爆型,符合GB3836-2000《爆炸性环境用防爆电气设备》规定,防爆标志为“ExiaIICT6”,在本次设计中,选用LUGB型涡街流量传感器其精度等级完全可以满足火电厂锅炉温度控制系统的精度要求。
产品特点:
•结构简单而牢固,无可动部件,可靠性高,长期运行十分可靠。
•安装简单,维护十分方便。
•检测传感器不直接接触被测介质,性能稳定,寿命长。
•输出是与流量成正比的脉冲信号,无零点漂移,精度高。
•测量范围宽,量程比可达1:
10。
•压力损失较小,运行费用低,更具节能意义。
•在一定的雷诺数范围内,输出信号频率不受流体物理性质和组分变化的影响,仪表系数仅与旋涡发生体的形状和尺寸有关,测量流体体积流量时无需补偿,调换配件后一般无需重新标定仪表系数。
•应用范围广,蒸汽、气体、液体的流量均可测量
公称通经(mm):
15,20,25,40,50,65,80,100,125,150,200,250,300
仪表材质:
1Cr18Ni9Ti
公称压力(Mpa):
PN1.6Mpa;
PN2.5Mpa;
PN4.0Mpa
被测介质温度(℃):
-40~+250℃;
-40~+350℃
环境条件:
温度-10~+55℃,相对湿度5%~90%,大气压力86~106Kpa
精度等级:
测量液体:
示值的±
0.5
测量气体或蒸汽:
1.0、±
1.5
量程比:
1:
10;
15
阻力损失系数:
Cd<2.6
输出信号:
传感器:
脉冲频率信号0.1~3000Hz低电平≤1V高电平≥6V
变送器:
两线制4~20mADC电流信号
供电电源:
+12VDC、+24VDC(可选)
+24VDC
现场显示型:
仪表自带3.2V锂电池
信号传输线:
STVPV3×
0.3(三线制),2×
0.3(二线制)
传输距离:
≤500m
信号线接口:
内螺纹M20×
防爆等级:
ExdIIBT6
防护等级:
IP65
允许振动加速度:
1.0g
4.4.3主、副调节器正反作用的选择
1.副调节器的正、反作用确定:
根据生产工艺安全的原则,调节阀采用气开式,故Kv为正;
当调节阀开度增大,空燃比增大,故Ko2为正,流量变送器的Km2通常为正,为了使整个系统中各环节静态放大系数的乘积为正,故副控制器的Kc为正,选用反作用控制器。
2.主调节器的正、反作用确定:
副回路的放大倍数可视为正,因温度变送器一般为正,当调节阀开度增大,温度升高,故,Ko1为正,故主控制器的Kc为正,选用反作用控制器。
4.4.4主、副回路调节器调节规律的选择
主调:
定制控制;
副调:
随动控制
主被控参数温度是工艺操作的主要指标,允许波动的范围很小,一般要求无静差,因此主调节器应选择PID调节规律。
副被控参数燃料和空气流量,为了保持稳定,P较大,可引入积分,一般不引入微分,因为微分会使调节阀动作过大,对控制不利,所以需要采用PI调节,以增强控制作用。
4.4.5控制器仪表的选择
采用模拟控制器:
DDZ-III型调节器,DDZ―Ⅲ基型控制器框图如图4.3。
由控制单元和指示单元两部分组成。
控制单元包括输入电路、比例积分微分电路、手动电路、保持电路。
指示单元有两种,因此基型控制器也分两种,即全刻度指示控制器和偏差指示控制器。
控制器的输入信号为1~5V的测量信号。
设定信号有内设定和外设定两种。
内设定信号为1~5V,外设定信号为4~20mA。
测量信号和设定信号通过输入电路进行减法运算,输出偏差到比例积分微分电路进行比例积分微分运算后,由输出电路转换为4~20mA信号输出。
手动电路和保持电路附于比例积分微分电路之中,手动电路可实现软手动和硬手动两种操作,当处于软手动状态时,用手指按下软手动操作键,使控制器输出积分式上升或下降,当手指离开操作键时,控制器的输出值保持在手指离开前瞬间的数值上,当控制器处于硬手动状态时,移动硬手动操作杆,能使控制器的输出快速改变到需要的数值,只要操作杆不动,就保持这一数值不变。
由于有保持电路,使自动与软手动相互切换,硬手动只能切换到软手动,都是无平衡无扰动切换,只有软手动和自动切换到硬手动需要事先平衡才能实现无扰动切换。
如果是