某工作面设备回撤作业规程Word格式.docx
《某工作面设备回撤作业规程Word格式.docx》由会员分享,可在线阅读,更多相关《某工作面设备回撤作业规程Word格式.docx(31页珍藏版)》请在冰豆网上搜索。
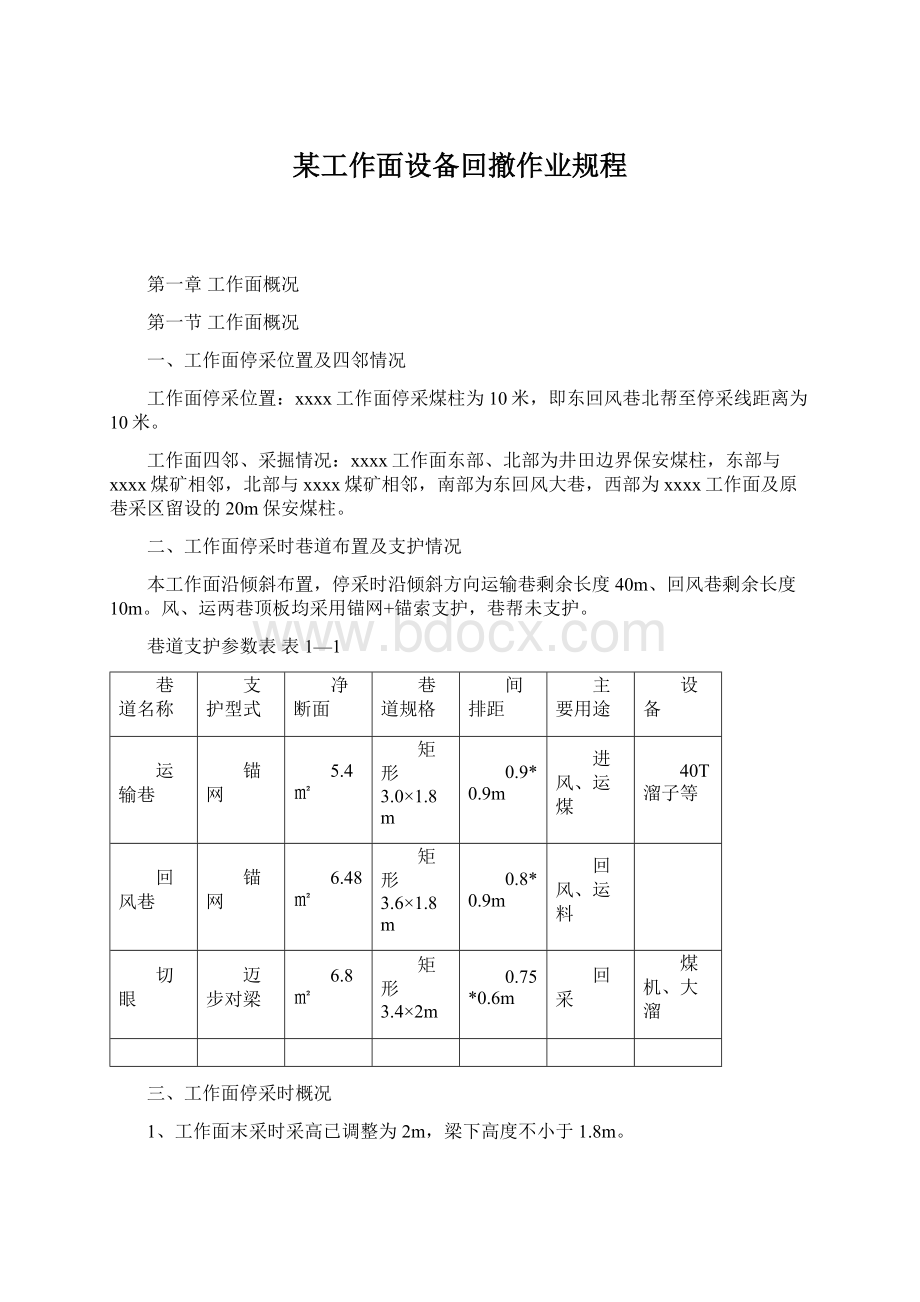
3、工作面上下端头仍采用DW22-300/100液压单体支柱与3.6m长π梁组成四对八梁支护,对梁与对梁中心距为0.75m,对梁两梁中心距为0.25m,一梁四柱。
4、工作面两巷超前支护:
仍采用DW22-300/100液压单体支柱配合2.8mπ型梁,双排支护,一梁二柱,柱距1.0m,排距2m。
运巷支护长度不小于20m,回风巷支护至巷口,且在回风巷口交岔点根据现场情况而增加一梁二柱抬棚或木垛加强支护,并加强该区域顶板管理,发现问题立即处理。
距煤壁20m范围内巷道高度不得低于1.8m,浮煤要清理干净,不允许乱放杂物,要保证有0.8m宽的人行道。
四、工作面地质与水文地质情况
工作面地表为中山区地貌,沟谷发育,有利于自然排水,较大沟谷雨季才有洪水排泄,且为季节性流水冲沟。
工作面上覆为富水性的砂岩裂隙水,根据地质报告,单位涌水量为0.0017L/s.m,属富水性弱的裂隙含水层。
工作面回采过程中未出现涌水、透水等水害影响。
第二节工作面主要回撤设备明细及位置情况
一、工作面主要回撤设备明细及位置情况如下表:
回撤设备明细表表1—2
序号
名称
型号及规格
数量
地点
1
刮板输送机
SGZ-630/220
1部
工作面
SGB620/40T
2
胶带输送机
DSJ80/40/2×
30
3
采煤机
MG160/380
工作面机尾
4
乳化液泵
BRW125/31.5
2套
东轨道大巷
二、主要回撤设备参数情况:
1、采煤机
采煤机技术参数表表1—3
型号
单位
截割高度
m
1.4-3.2
煤层倾角
°
≤35°
总功率
Kw
377.5
截割功率
2×
160
牵引功率
25
泵站功率
7.5
电压等级
V
1140
最多截割高度
mm
2880
过煤高度
455
滚筒直径
1400
截深
630
机面高度
摇臂摆动中心距
6200
调速方式
交流变频调速
牵引方式
销轨牵引
牵引力
KN
360
牵引速度
m/min
0-7.5/10
整机重量
t
2、工作面刮板输送机
刮板输送机技术参数表表1—4
运输能力
(t/h)
铺设长度
(m)
刮板链速
(m/s)
总装机功率(KW)
(v)
450
78
110
3、运巷刮板输送机
刮板输送机技术参数表表1—5
150
10
0.86
40
660
4、运巷胶带输送机
胶带输送机技术参数表表1—6
DSJ80/40/2*30
输送量
t/h
400
带速
m/s
输送长度
传动滚筒直径
500
转向滚筒直径
托辊直径
108
铰接托辊槽形角
输送带
类型
PVG800S
宽度
800
贮藏输送带长度
50
液力耦合器
YOXD-400
主电动机
DSB-40
KW
2*30
电压
转速
r/min
1470
减速器
JS40
速比
18.4
张紧绞车
JZB-0.9
功率
绳速
4.74~7.68
机尾搭接长度
总重
Kg
51000
5、乳化液泵
乳化液泵技术特征表表1—7
公称流量
(L/min)
公称压力
(MPa)
电机功率
(KW)
(V)
125
31.5
75
6、工作面柱梁
工作面柱梁参数表表1—8
液压单体柱
DW22-300/100
780根
π梁
2.8m
280根
3.6m
16根
第二章设备回撤准备工作
第一节工作面辅助运输系统
一、辅助运输设施
本工作面设备回撤辅助运输:
采用轨道配合小绞车接力运输。
1、绞车安装周边情况:
绞车位置应选在宽敞平整,便于操作,顶帮完好、无淋水的地方。
2、绞车位置确定和轨道线路长度
在xxxx两巷口及工作面两端头,选择安全合理的位置,分别各安装1台JD-1调度绞车,绞车最大运输距离180m。
3、绞车型号、性能及主要参数
JD-1绞车主要参数:
绞车型号
JD-1
外层钢丝绳静张力
10KN
外层钢丝绳速度≥
1.0m/s
容绳量≤
180m
钢丝绳直径
15.5mm
滚筒尺寸(直径×
宽度)
235mm×
303mm
电动机
YBJ-11.4
11.4KW
1460r/min
660V
外形尺寸
长*宽*高
1070*766*727mm
绞车质量
550Kg
4、绞车固定方式以及相关材料
JD-1调度绞车打设地锚配合将军柱固定,采用四根1.5m地锚固定。
将军柱必须打在顶板上并掏柱窝深度不小于100mm,严禁打在金属网上。
柱子选用直径不小于200mm的优质圆木,将军柱打设时落山角度为60-70°
。
柱子与护绳板之间应留有不少于0.7m操作空间,用链条将绞车与柱子连接拴紧且柱子有防倒护绳(用8#铅丝双股与固定支护绑牢)。
5、钢丝绳的选型
(1)选用直径为15.5mm钢丝绳作为绞车牵引绳,绳头加设与钢丝绳配套的绳卡、绳皮,绳头卡绳长度不得小于600mm,且绳皮有足够强度,绳卡同向打设至少3道,间距200mm。
第一道绳卡距绳皮距离不得大于50mm。
(2)运输设备重量:
平板车1.0t,煤机最大件10t,其他最大物件6t,即按照最大单车重量11t验算绞车拉力和钢丝绳强度。
(3)绞车最大牵引力验算和最小安全系数验算
按照煤安规程规定,专用提升物料钢丝绳安全系数不小于6.5。
①JD-1绞车最大牵引力校验
绞车牵引力:
F=Wgsinα=11000×
9.8×
0.087=9.38KN
式中:
F—绞车承受最大拉力,N
α—运行段最大坡度,5°
W—绳端荷重量,11t
g—重力加速度取9.8
查JD-1绞车牵引力为:
10KN>9.38KN,故可选型于JD-1绞车。
②JD-1绞车钢丝绳安全系数校验:
Pmax=Wg(sinα+f1cosα)+QLg(sinβ+f2cosβ)
=11000×
(0.087+0.013×
0.996)×
9.8+0.85×
180×
(0.087+0.13×
9.8
=11156.3N
Pmax—绞车承受最大拉力,N
αβ—运行段最大坡度,5°
f1—车轮在轨道上运行阻力系数为0.013
f2—钢丝绳在运行中阻力系数0.13
Q—钢丝绳单位长度重量,Φ15.5mm,0.85kg/m。
L—使用地点钢丝绳长度,绞车运输最大距离为180m。
查15.5mm钢丝绳破断拉力为:
Nmax=143000N;
钢丝绳的安全系数:
n=Nmax/Pmax=143000/11156.3=12.8>
6.5
通过计算,所选绞车和钢丝绳的安全系数均能满足运输要求。
6、在用小绞车施闸后,闸把在水平线以上30-45°
即应闸死,闸把严禁打至水平线位置,另外调节螺栓拧入螺母内深度不得小于螺栓直径的1.5倍。
7、绞车护绳板应用框架固定,护绳板高过滚筒上方中线,小绞车防护装置保证牢固。
8、小绞车控制按钮和信号按钮应在操作牌板集中安设,其中操作牌板应固定在便于绞车司机操作的合适位置,声光信号设在便于绞车司机看到的位置,且与绞车司机操作位置间距不大于5m。
9、牵引钢丝绳必须采用专门卡绳装置压牢,不得系在滚筒上,绞车松绳到使用地点,滚筒上至少要有三圈不得放出,收绳后滚筒边缘应高出最外层钢丝绳至少2.5倍的绳直径。
10、工作面各绞车之间设置警示系统:
对辅助运输系统内的各部绞车,在服务长度内均设置单独的声光对打信号系统。
11、挡车装置的设置和防跑车设置:
在车辆的装卸点、车场坡头、坡底均应打设阻车器,且保持常闭状态。
12、轨道线路设置及质量要求:
本次回撤铺设临时轨道。
(1)、轨道型号为22kg/m,无杂物拌道,无缺眼道。
(2)、轨枕间距1m,且质量合格无失效轨枕。
(3)、轨距为600mm,允许偏差不大于10mm。
(4)、轨面水平误差不大于5mm。
(5)、水平允许偏差不大于10mm,轨缝不大于10mm。
(6)、轨道前后高低,方向符合标准,目视直顺,明显变坡点处不得有急弯。
(7)、扣件齐全,密贴紧固,道钉齐全有效不浮离。
(8)、掩道充填不超过枕面,不低于枕面的1/3,轨枕长度范围内全部充填,钢轨下面两侧200mm范围内加强充填。
(9)、道岔、弯道符合要求,轨道牢固不晃动,疏密合理,接头间隙不大于5mm,道钉齐全,巷道无积水,在设备运输过程中,轨道发生变形等不合格现象时,必须及时进行维修,轨道不合格时,不得进行运输工作。
二、辅助运输线路:
xxxx回风巷提前铺设轨道,xxxx运巷轨道紧跟运巷设备随撤随铺,工作面轨道紧跟大溜随撤随铺,运输路线如下。
工作面设备→xxxx回风巷→东轨道大巷→12轨道巷→1203车场→1203回风巷→1203切眼设备存放点
工作面设备→xxxx运输巷→东轨道大巷→12轨道巷→1203运输巷设备存放点
第二节回撤前其他准备工作
一、临时起吊方式
本工作面设备回撤临时起吊采取在临时起吊地点打设起吊锚索配合手拉葫芦起吊,预计本次工作面设备回撤需要临时起吊地点为工作面机头、机尾及设备卸载地点,因此需在以上几个临时起吊地点提前打设专用起吊锚索。
起吊锚索采用Φ17.8×
6500mm的钢绞线,锚固力不得低于150KN。
起吊地点加强支护方法:
根据现场情况而定,如需加强支护则采取架设一梁二柱抬棚的方式加强支护该处顶板。
二、回撤前加强顶板支护措施
1、回撤前全面检查工作面柱梁支护情况,确保工作面支护齐全可靠。
2、工作面及端头支护所有柱梁必须齐全完好,支柱初撑力不小于90KN,支柱初撑力应用支柱测力计进行检查。
3、工作面两巷超前支护安全可靠。
4、工作面支柱停采时要打成一条线,排距误差不超过±
50mm、柱距误差不超过±
100mm。
5、所有支护不准缺梁少柱,长π梁严禁出现单梁单柱现象。
6、支柱要迎山有劲,迎山角符合要求。
三、临时泵站安安设及其他系统
1、本次回撤因机电硐室位于轨道巷内不影响工作面设备回撤工作,因此不需要安装临时泵站。
2、排水、供水、压风系统不变,回撤期间做好各系统维护工作,确保工作正常。
3、供电系统:
因回撤时工作面机电硐室最后回撤,故工作面供电系统不变;
所安局扇供电为主电源来自于中央变电所5#馈电开关,另一路电源来自东轨道配电点630馈电开关。
4、通风系统:
回撤过程中工作面顶板未冒落前工作面通风方式及风量不变,当出现顶板冒落阻断风流情况时,工作面采用局扇为其供风,启动局扇前通风部门提前做好调风准备工作。
回撤前在东轨道大巷里程570m处安设两台局扇(一用一备),风筒接至xxxx回风巷内并试转,为工作面风巷供风;
在东轨道大巷里程590m安设两台局扇(一用一备),风筒接至xxxx运输巷内并试转为工作面运巷供风,风流路线如下:
工作面风巷侧:
新鲜风流:
东轨道大巷局扇→xxxx回风巷→xxxx工作面
乏风风流:
xxxx回风巷→回风大巷→回风立井→地面
工作面运巷侧:
东轨道大巷局扇→xxxx运巷→xxxx工作面
xxxx运输巷→东轨道大巷→回风大巷→回风立井→地面
风量计算:
1)按瓦斯和二氧化碳涌出量计算:
Q=100×
q×
K=100×
1.3×
2.0=260m3/min
Q----回撤工作面实际需要的风量,m3/min;
100----单位瓦斯涌出配风量,以回风流瓦斯浓度不超过1%的换算值;
q-----回撤工作面的瓦斯绝对涌出量为1.3m3/min;
K-----回撤工作面的瓦斯涌出不均匀和备用风量系数,此处取2.0;
2)按人数计算:
Q=4×
n=4×
25=100m3/min
式中:
4------每人每分钟不低于4m3的配风量;
n-----回撤工作面同时工作最多人数,此处n=25人;
3)风速验算:
通过以上计算,回撤工作面实际需要的风量取Q=260m3/min。
按风速验算:
V=Q/S=4.3/6=0.72m/s,V高于最低风速0.25m/s,低于最高风速4m/s符合要求。
4)风机选型:
根据工作面实际需要的风量,选用FBD№5.6/2×
11型对旋式局部通风机,风量190~330m3/min,风筒采用直径600mm的抗静电、阻燃帆布风筒,满足回撤通风要求;
xxxx运巷需配备120米风筒,xxxx回风巷需配备150米风筒。
5、通讯、监测监控系统
通讯:
在两巷距工作面10—20m范围内各安设一部防爆电话,同时在两巷距工作面10—20m处各设置一部直通调度室的直通电话。
人员定位系统:
运输巷、回风巷距工作面不大于50m处分别设置读卡器;
所有入井人员必须携带识别卡。
瓦斯监测监控:
xxxx回风巷距风巷口10~15m安设一台瓦斯传感器、温度传感器、一氧化碳传感器。
xxxx工作面端尾上隅角,安设一台瓦斯传感器、一氧化碳传感器。
xxxx回风巷距工作面不大于10m范围内,安设一台瓦斯传感器、一氧化碳传感器。
瓦斯传感器分别由东轨道大巷分站监控,实现工作面电气设备瓦斯电闭锁。
第三章工作面设备回撤工作
第一节设备回撤顺序
一、设备回撤项目:
采煤机、工作面刮板输送、运巷刮板输送机、运输巷胶带输送机、工作面柱梁、乳化液泵。
二、设备回撤顺序:
运巷胶带输送机、刮板输送机→采煤机→工作面刮板输送机→工作面柱梁→乳化液泵
第二节设备回撤工艺
设备回撤工艺及技术要求
一、运输巷胶带输送机回撤
1、准备工作
①将胶带输送机机内及两侧的浮煤、杂物清理干净。
②提前打设好起吊锚索,检查起吊点范围内顶板情况,确保支护安全可靠;
稳固好各部绞车。
③备齐专用工具。
2、回撤工作及技术要求
①松张紧绞车,抽出皮带接头通条,掐开皮带,点动电机将皮带拉出装车运走。
②为保证足够长的皮带,严禁随意截割、折坏、磨损皮带。
装皮带时,层与层之间要垫好道木,防止折坏皮带。
皮带装车严禁超长超宽。
③胶带输送机断电,拆除其电控部分。
④依次拆除胶带输送机贮带仓和张紧绞车以及H架、中间架、上下托辊、机尾,并装车运走,为确保小件不丢失,分类集中装运小件(包括各种螺丝、销子)。
安排专人提前拆机头紧固件螺丝,每处留有两条螺丝,将托辊拿掉装车运走。
⑤将胶带机机头电机减速箱拆开,装车运走,使用10t手拉葫芦起吊装车,注意起吊位置的顶板变化情况。
拆机头电机时,一组至少有4人工作,一人监护,负责监护煤帮、起吊点、生根及物件的稳定情况,发现问题停止工作,立即进行处理,待处理好安全后再工作。
其它拆除工作必须至少两人一组同时工作,相互监护。
操作人员身体的任何部位不得在起吊设备下部,其他人员要远离现场,有队干现场跟班作业。
二、运巷刮板输送机回撤
①将刮板输送机机内、运输机两边的浮煤、杂物清理干净。
①运巷刮板输送机依次从运巷风桥处开始向里逐部拆除。
②拆链条,先从机头处将溜子链条掐开,然后将溜子上链拆散并运走后,再用溜子打反转将底链抽出并逐段拆运走,最后甩掉溜子电源,把电缆、开关装车外运。
③拆机头时先拆电机减速箱,再人工拆掉与机头叉的连接螺栓,用手拉葫芦配合绳头使轴头离开,然后把电机减速箱放在底板上并运走。
对拆解下的易损件、紧固件、零碎小件,要分类装箱保管;
对解体后外露孔、腔必须严密封闭后方能进行装运;
起吊使用的钩环链必须闭合,指派有经验的老工人看护顶板,发现问题及时处理。
④将运输机溜槽进行解体,用绞车托运到装车位置处进行装车,每3节装一车,并封车牢固可靠。
三、工作面采煤机回撤
①配备熟悉采煤机设备技术结构及性能的人员进行施工作业,并备齐专用工具。
②提前将运输线路拐弯处抹角支护,打设好专用起吊锚索,检查起吊点范围内顶板情况,确保支护安全可靠。
③停煤机高压电,将煤机开关负荷电缆拆除,用挡板挡好开关接线嘴,把电缆外运装车。
④稳固好各部绞车,检查运输路线确保畅通。
2、拆解回撤工作及技术要求
①机组整机拆解为以下5部分:
左滚筒、左摇臂、右滚筒、右摇臂、机体中间部;
拆解顺序依次为左滚筒拆解—→左摇臂拆解—→右滚筒拆解—→右摇臂拆解—→机体中间部。
②严格按说明书、质量标准要求对拆解的部件按次序依次编号、登记后方可对设备进行拆解、转运。
③拆解各部件时,尽量保留小型零件,避免丢失,但拆解程度要尽量保证拆解后的各部件在运输装车后方便运输;
对解体后外露孔、腔必须严密封闭,对活动部分必须加以固定,油管、水管两端必须封堵包扎后方能进行装运。
④在施工过程中,作业人员必须细致,操作准确无误,以防在拆、装、运、卸过程中造成设备损坏。
⑤拆装重大型部件时,必须使用专用起吊锚索配合10t手拉葫芦起吊,起吊注意事项要求见第五章第三节重物起吊安全技术措施,起吊点指派有经验的老工人看护顶板情况,发现问题及时处理。
操作人员身体的任何部位不得在起吊设备下部,其他人员要远离现场,现场必须有跟班队干跟班作业。
四、工作面刮板输送机回撤
①将刮板输送机机内、运输机两边的浮煤、杂物清理干净,运输机移平、推直。
②对工作面支护进行全面检查,确保支护安全可靠;
提前打设好专用起吊锚索;
稳固好各部绞车,并检查运输路线确保畅通。
③背实煤帮,备齐专用工具。
①刮板输送机回撤分为两组同时作业,分别从机头、机尾进行回撤作业,工作面轨道随大溜回撤随撤随铺;
回撤顺序为拆大链、大溜机头尾回撤,然后依次回撤中部溜槽。
③拆大链,先从机头处将溜子大链掐开,然后将溜子上链拆散并运走后,再用溜子打反转将底链抽出并逐段拆运走,最后甩掉溜子电源,把电缆外运装车。
④拆机头、机尾:
拆件时先拆电机减速箱,再人工拆掉与机头叉的连接螺栓,用手拉葫芦配合绳头使轴头离开,然后把电机减速箱放在底板上并运走。
对解体后外露孔、腔必须严密封闭,对活动部分必须加以固定,油管两端必须封堵包扎后方能进行装运;
⑤将运输机中部槽进行解体,用绞车托运到装车位置处进行装车,每两节装一车,并封车牢固可靠。
拆除运输机各部连接螺栓、销子、哑铃销、各部位小件,并分类集中装车运输。
拆机头、机尾、电机减速箱工作,一组至少有4人工作,一人监护,负责监护煤帮、起吊点、生根及物件的稳定情况,发现问题停止工作,立即进行处理,待处理好安全后再工作。
五、工作面柱梁回撤
1、回收方法及工期要求:
采用单体液压柱配合回柱器人工直接回收,回撤柱梁前在工作面距机尾20米处提前打设2个木垛加强顶板支护;
工作面柱梁回撤分为两组同时作业,从工作面距机尾20m处开始分别向机头、机尾回撤作业,由里向外逐架进行;
工作面轨道随柱梁回撤一起回收;
柱梁回收工期要求为2天内必须回撤结束。
2、回收顺序:
由老塘区到煤壁的顺序逐架依次回收,将拆下的柱梁及时装车搬运到指定位置。
3、工作面上下出口以外30米处,各备用不少于100根串杆及不少于2个木垛用的支护材料,以防回撤时顶板来压、破碎、冒顶或老塘窜矸时打设木垛、背顶、挡矸使用。
4、回收工作面柱梁前,先将回撤地点以外10m范围内增设支柱,加强顶板支护,并随工作面回撤,逐架向外补打支柱,顶板破碎处增设木垛;
班长及安全员必须检查采面的支护、顶板、煤壁等情况确认无其他安全隐患后方可回收。
5、回收时,回收迎头必须安排有经验的老工人观察顶帮变化情况,严禁太多人员拥挤在回收迎头;
作业人员只能站有支柱掩护的安全地点进行操作。
6、回收时应由3人配合作业,一人操作回柱、梁,一人观察顶帮变化情况,一人将回撤的物料及时运出工作面,确保后路畅通;
操作人员回撤前要首先检查工作地点的支护是否完好,如有问题立即处理,检查时应由外向里逐架进行;
回柱前解开防倒链,回柱时应视顶板情况而进行近距离或远距离操作,远距离操作时必须使用回柱器进行回柱;
支柱卸载时,必须由小到大逐步卸载,待顶板稳定支柱脱落后方可快速卸载。
7、回收时若所回收的支架上有戗柱时先回戗柱,但严禁超前于所回收的支架回收戗柱。
8、回收过程中若采面顶板压力突然增大时,班队长及安全员必须及时将所有人撤至安全地点,待顶板压力稳定,对工作面支护进行加强支护后,经班队长及安全员对回收迎头的支护情况进行