织造工艺与质量控制期末复习总结文档格式.docx
《织造工艺与质量控制期末复习总结文档格式.docx》由会员分享,可在线阅读,更多相关《织造工艺与质量控制期末复习总结文档格式.docx(13页珍藏版)》请在冰豆网上搜索。
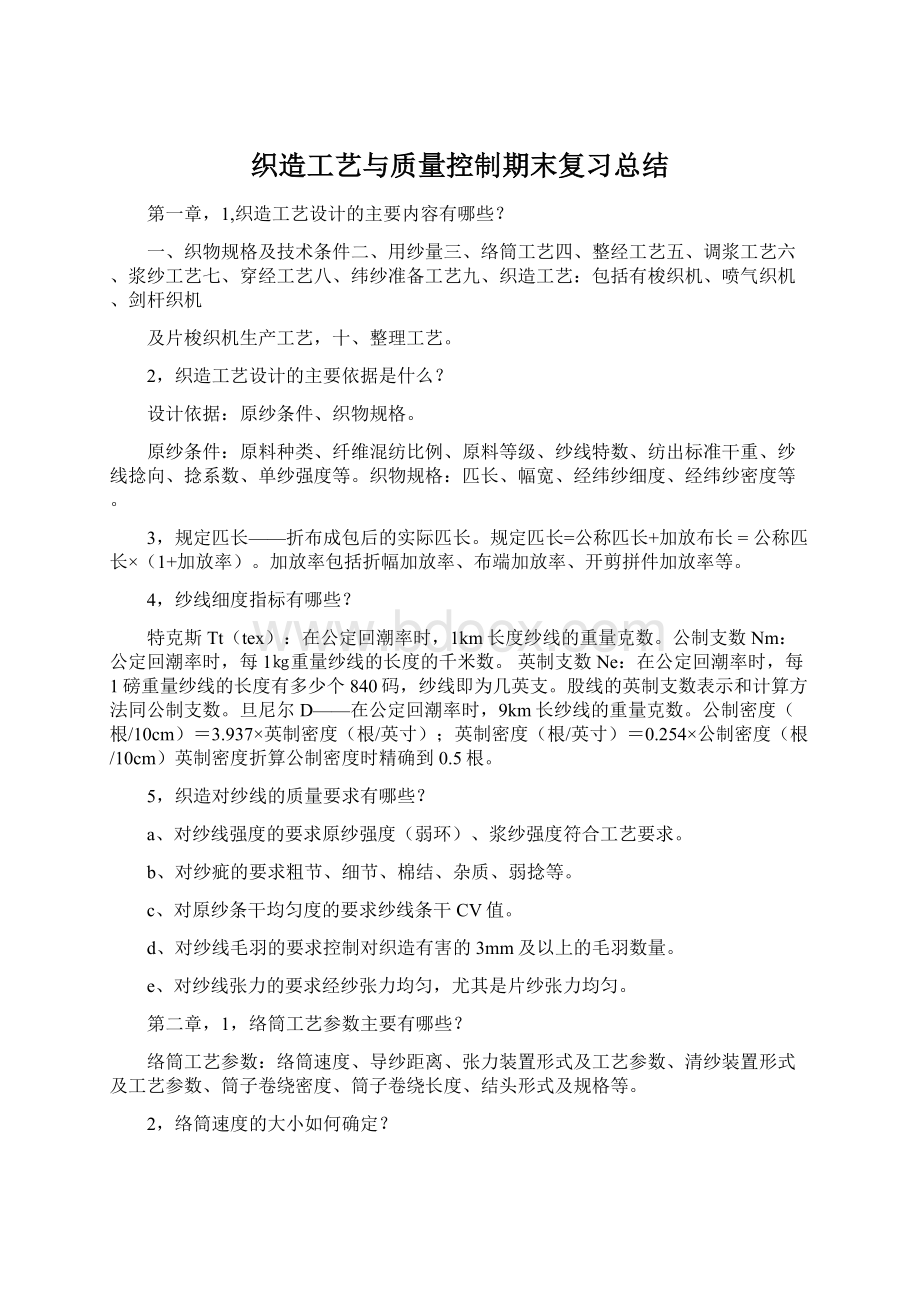
纱线较粗或络股线时,络筒速度可适当高些。
3,络筒张力装置的形式有哪些?
比较优缺点。
a,累加法特点:
不扩大纱线张力的波动程度;
接头或粗节通过压板时,会发生动态张力波动。
(导纱速度越快,波动越大);
b,倍积法张力装置纱线通过导纱部件产生的张力属倍积张力。
垫圈式张力装置中纱线与柱芯之间摩擦产生倍积张力。
特点:
动态张力波动较小。
张力波动成倍数增加,纱线张力的不匀程度得不到改善。
C,间接法张力装置特点:
高速条件下纱线磨损少;
纱线张力均值增加的同时,张力不匀率↓;
结构复杂。
4,络筒张力的大小如何确定?
张力范围:
棉纱:
张力不超过其断裂强度的15%~20%(一般取8%~12%)。
毛纱:
张力不超过其断裂强度的20%。
麻纱:
张力不超过其断裂强度的10%~15%。
确定原则:
在满足筒子成形良好或后加工特殊要求的前提下,尽量采用较小的张力。
粗特纱线的络筒张力应大于细特纱线,混纺纱的络筒张力略小于同支纯棉纱。
5,什么是最佳清纱范围?
如何确定?
种类:
机械式、电子式。
机械式分为隙缝式、梳针式和板式三种。
电子式分为光电式和电容式两种。
最佳清纱范围:
允许保留在纱线中的无害纱疵级别及个数与必须清除的有害纱疵级别及个数之间最佳的折衷。
乌斯特纱疵分级样照分23级。
短粗节有碍纱疵可定在纱疵样照的A4、B4、C4、C3、D4、D3和D2七级。
涤棉纱:
短粗节有碍纱疵定在A4、A3、B4、B3、C4、C3、D4、D3和D2九级。
6,设计筒子卷绕长度的目的是什么?
筒子定长方法有哪些?
满足整经或其它后工序的要求确定;
机械定长和电子定长。
7,络筒工艺参数对纱线性能有何影响?
络筒后纱线线密度下降、长度增加、捻度增加。
络筒使纱线毛羽增加,且速度越高,毛羽增加越多,小纱时毛羽增加最多。
络筒速度对纱线条干无明显影响。
纯棉纱:
速度适当时,细节、粗节和棉结略有降低,但高速时条干CV恶化。
涤/棉纱:
细节、粗节和棉结都随络筒速度增大有增加。
8,,络筒工序主要质量指标有哪些?
如何检验?
1,百管断头次数;
检验方法:
分品种在任意机台上测试100只管纱,发现断头时记录并分析断头原因,有突出问题应留出样纱以便详细分析分别记录实验前后实验区的温度和性对湿度。
2,筒子卷绕密度;
取样时任取筒子,数量不少于5只,测试筒子卷绕尺寸,v(g/cm^3)=G/V(cm^3)3,毛羽增加值:
检验方法每个品种随即取10只管纱和筒子,满管纱去掉100m左右,满筒纱去掉1000m左右,连续测10次,最后求平均值。
毛羽增加率=(筒纱毛羽数-管纱毛羽数)/管纱毛羽数4,好筒率5,电子清纱器正切率6,无结头纱捻接质量。
9,络筒疵点主要有哪几种?
其形成原因是什么?
对后道工序有何影响?
a,小辫子、双纱形成原因:
头后送纱太快,,强捻纱对后工序影响:
造成布机无故关车或经缩疵布。
b,襻头或脱边,形成原因:
挡车工操作不良,大端未装拦纱板或装得不正,筒管、筒锭.C,重叠筒子形成原因:
筒管位置不对,间歇开关参数调整不当,锭子转动不灵活,防叠槽筒本身不良对后工序影响:
造成单纱及片纱张力不匀,增加断头,严重重叠的筒子不能使用。
D,重叠筒子形成原因:
E,葫芦筒子形成原因:
(1)导纱器上飞花阻塞
(2)张力架位置不对(3)槽筒沟槽在相交处有毛刺(4)导纱杆套筒磨出槽纹对后工序影响:
增加整经断头和张力不匀。
F,凸环筒子形成原因:
纱线未断而筒子略有抬起,形成小凸环,当筒子落下后纱线在凸环处受阻而绕成大凸环。
对后工序影响:
G,铃形筒子形成原因:
(1)锭子位置不正
(2)纱线引出时受阻使张力太大对后工序影响:
H,菊花芯筒子,形成原因:
(1)筒子托架固定螺丝未扳紧,顶端抬起
(2)锭子定位弹簧断裂或松动(3)纱线张力松弛(4)筒锭或筒管松动(5)槽筒与筒子表面接触不良对后工序影响:
J,纱线磨损形成原因:
(1)机械或工艺配置不当
(2)筒子太大,被槽筒磨损(3)断头自停装置失灵,断头不关车(4)槽筒表面有毛刺对后工序影响:
纱身毛羽增加,单纱强力降低。
10,自动络筒机有哪些优势?
A,纱线通道设计合理b,配置完善的在线监控系统c,捻接质量优良d,、良好的卷绕成形:
采取金属槽筒,卷绕沟槽设计合理,适应高速。
采取筒子架横动、摆动,程序控制的槽筒速度微调等防叠措施,使筒子成形良好。
E,完善的清洁系统:
定点和巡回相结合的气动清洁系统,减少飞花
11,在普通络筒机上可采用哪些措施提高络筒质量?
1、改用电子清纱器2、加装空气捻接器3、采用筒子定长装置4、采用金属槽筒5、电子防叠6、使用巡回清洁装置。
第三章:
1,分批整经工艺参数主要有哪些?
整经机类型、张力器型式、整经张力、整经速度、整经轴数和根数、整经长度、整经卷绕密度及整经结头规格等。
2,分批整经速度大小如何确定?
高速整经机设计速度为1000m/min左右,生产中选600m/min以上。
滚筒摩擦传动的1452A整经机为200~300m/min。
整经轴幅宽大,纱线质量差,纱线强力低,筒子成形差时,速度应低一些;
涤棉纱的整经速度应比同特棉纱低一些。
3,造成整经片纱张力不匀的因素有哪些?
简述均匀片纱张力的措施。
因素:
纱线退绕张力、张力装置产生的纱线张力、空气阻力和导纱部件引起的纱线张力
均匀片纱张力的措施:
①、间歇整经,集体换筒②、合理设置张力装置的工艺参数③、纱线合理穿入伸缩筘④、适当增大筒子架到整经机机头的距离⑤、加强管理,保持良好的机器状态
4,什么是整经张力的分段分层配置?
什么是弧形配置,比较这两种配置方法的优缺点?
分段分层配置张力圈重量遵循:
前排大于后排,中层重于上层和下层,分段分层越多,片纱张力越趋于均匀一致,但是生产管理也越不方便。
5,什么是纱线的分层穿法和分排穿法?
比较其特点。
分排穿筘法从缩扣中第一排开始,由上而下将纱线从伸点往外侧逐根逐筘穿入,此方法操作不便,但是能均匀纱线张力的作用,纱线断头不易缠绕临纱;
分层法纱线从上层开始把纱线穿入伸缩扣中部,然后逐渐向伸缩扣外侧穿入,此方法层次清楚,找头引纱方便,但是纱线张力差异大,影响整经质量。
5,整经工艺参数对纱线性能有何影响?
1、纱线经过整经加工后,在张力的作用下会发生伸长,其细度、强力和断裂伸长均有减小。
2、纱线在高速条件下经导纱部件摩擦,对纱线有磨损,增加毛羽。
3、纱线从固定的筒子上退绕下来,其捻度会有些改变。
筒子退绕一圈,纱线上就会增加(Z捻纱)或减少(S捻纱)一个捻回。
随着筒子退绕直径减少,纱线的捻度变化速度加快。
研究表明整经对纱线的物理性能没有明显的改变。
6,整经工序主要质量指标有哪些?
如何检验?
整经断头率检验方法分品种分机台任意测定5000m发现断头及时记录并分析原因,记录实验前后靠近实验区的温度和相对湿度2,经轴卷绕密度检验任取5只空经轴到指定的整经机上做满5只经轴,分别测定各只经轴的卷绕密度,最后求平均值3,经纱排列的均匀性在抽查的左中右三处不同位置,用尺子各测出10cm内的经纱根数,并以此与标准的平均排列密度比较,误差在正负5%以内合格。
4,刹车制动性能5,好轴率。
7,整经疵点主要有哪几种?
浪纱产生原因:
(1)经轴边部卷绕不平整;
(2)伸缩筘经纱排列宽度与经轴幅宽不一致(3)经轴两端加压不一致、轴承磨灭过大等造成经轴两端卷绕直径不一致;
(4)经轴轴管弯曲、盘片歪斜或转动不稳,经轴卷绕不平整;
(5)滚筒两边磨损。
对后工序影响:
浆纱断头、粘并,织造时开口不清、断头、产生“三跳”织疵和豁边疵布,布面不匀整、有条影等。
绞头产生原因:
(1)断头后刹车过长,造成找头不清;
(2)落轴时穿绞线不清。
经轴退绕阻力增大,浆纱片纱张力不匀,易断头。
错特产生原因
(1)换筒工筒子用错
(2)筒子内有错特、错纤维对后工序影响:
布面错特,印染后造成染色不一致
倒断头产生原因:
(1)断头自停装置失灵。
(2)经轴刹车不及时,使断头卷入。
(3)操作工断头处理不善。
造成浆纱断头,影响浆纱质量。
长短码产生原因:
(1)测长装置失灵。
2)操作不良,测长表未拨准等。
造成浆纱回丝或小浆轴。
杂物卷入产生原因:
(1)接头回丝或换筒回丝带入纱层。
2)做清洁时飞花落入纱层未及时清(3)筒子堆放时间长,上面附有飞花。
引起布机断头,或造成疵布.油污渍。
8,分批整经工艺参数:
整经机类型、张力器型式、整经张力为主、张力装置型式,整经速度、整经轴数和根数、整经长度、整经卷绕密度及整经结头规格等
9,三种整经方式:
分条、分批、分段
1、分批:
总经纱发别卷绕在几个轴上再合并生产效率高,适于大批量容易产生短码,回丝多花形变化不方便,多用于本色布生产2、分条:
先卷绕在滚筒上再倒轴生产效率低,张力不均匀花型变化方便回丝少,适于毛棉色织,不上浆织物3、分段用于经编机,先卷成多个小轴。
10,提高整经产量及质量的技术措施:
A,分批整经的技术措施1,高速、大卷装2,完善的纱线品质保护3,均匀纱线整经张力4,均匀的纱线排列5,减少整经疵点6,良好的劳动保护7,集中方便的调节和显示8,改善纱线品质,提高纱线的可织性。
第四章:
1,什么是浆纱含固率?
含固率对上浆质量有何影响?
浆液中各种粘着剂和助剂的干燥质量相对浆液质量的百分比;
浆液含固率直接决定了浆液的捻度,并影响经纱的上浆率。
含固率高,对纱线的浸透性差,被覆好,上浆率高。
2,高压上浆工艺包括哪几个方面?
A,高浓,高压,低粘主压浆辊的压力为20-40kn,浆液含固率大于等于上浆率,浆液捻度较低b,降低覆盖系数c,压力配置先轻后重,重浸透,低被覆d,高硬度压浆辊,低压出回潮率e,出浆槽配湿分绞,进烘房分层预烘f,高温预烘,低压合并。
3,浆纱质量指标有哪些?
其含义是什么?
浆纱质量指标有:
上浆率,伸长率,回潮率,减伸率,增强率,浸透率,被覆率,浆膜完整率,浆纱耐磨次数,浆纱毛羽降低率。
上浆率:
纱线上浆料干重对原纱干重的百分率;
回潮率:
浆纱含水量对浆纱的百分率;
伸长率是指纱线在浆纱机上的伸长量对原纱长度的百分率;
减伸率:
指纱线断裂伸长率的减少量对原纱断裂伸长率的百分数
4,上浆率大小对织造织物质量有何影响?
确定上浆率的依据有哪些?
上浆率大小如何调节?
上浆率大,经纱的强度及耐磨性增加,但是经纱的弹性伸长减小,织造时易产生脆断头,上浆率过多的上浆量会导致织物手感粗糙浆料成本增加。
上浆率小,经纱的强度及耐磨性不足,织造时纱线表面容易起毛气球,造成梭口不清,产生断头,但经纱的弹性伸长降低。
分类依据:
纤维种类,经纱的密度,经纱的捻度,经纬纱的密度,织物组织,浆料的性能及织机种类等;
经纱的线密度小,捻度小,经纬纱线密度大时,上浆率应大一些,无梭织机上浆率比有梭织机的大;
当织物改变时,一般通过改变浆液的含固率和粘度来调节上浆率。
5,回潮率大小对织造及织物质量有何影响?
确定回潮率的依据有哪些?
回潮率大小如何调节?
回潮率过大,浆膜发粘,浆纱的耐磨性降低,织造时造成开口不清,断头与织疵增加,易产生窄幅长码布,回潮率小,浆膜发硬发脆,造成浆纱断头,易产生宽幅断码布;
主要依据纤维的种类,浆料性能及上浆率大小等;
当织物品种改变时,通过改变蒸汽压力,调节烘房温度来控制与调节浆纱回潮率。
6,伸长率大小对织物质量及织造有何影响?
确定伸长率的依据有哪些?
伸长率大小如何调节?
浆纱伸长率过大,纱线弹性损失,断裂伸长和强力下降,增加织造断头,织物强力也会下降,织物匹长增加,浆纱伸长率过小,说明经纱张力小,易造成片纱张力不匀,织物匹长减少;
主要依据纤维种类;
通过整经时加放千米纸条,控制经轴制动动力,引纱辊和经轴之间、织轴卷绕时设置张力检测与自动调节装置等方法,由此控制经纱的伸长。
7,浆纱的目的及要求目的:
赋予经纱抵御外部复杂机械力作用的能力,提高经纱的可织性,保证织造过程顺利进行。
要求:
1)浆纱具有良好的可织性;
(良好的耐磨性、毛羽贴伏、增强保伸、弹性)2)粘着剂、助剂来源充足,成本低,易退浆,不污染环境;
3)织轴卷绕质量良好,表面圆整,排纱整齐;
4)保证优质生产的前提下,提高浆纱生产效率、浆纱速度、浆纱质量、提高浆纱质量控制自动化程度、提高浆纱生产的经济效益
8,浆纱主要疵点及成因。
4,上浆不匀:
由于浆液粘度、温度、压浆力、浆纱速度的波动以及浆液气泡等原因。
1,回潮不匀:
主要是烘房温度和浆纱速度不稳定引起。
2,张力不匀:
经轴退绕张力不匀,各导纱轴不平行,不水平等引起。
3,浆斑:
浆皮、浆块粘在纱线上或长期停车所致。
9,醇解度(DH):
指制造PVA时聚醋酸乙烯中的醋酸根被羟基所取代的程度。
当DH=98±
1%,该PVA称为完全醇解PVA(FH-PVA);
当DH=88±
1%,该PVA称为部分醇解PVA(PH-PVA)
10,确定浆料配方时主要考虑哪些因素?
一浆料组分的选择依据1、纱线的纤维种类——根据“相似相容”原理选择黏着剂即经纱的纤维材料与粘着剂具有相同基团或相似极性基团2、纱线特数和品种:
细特纱:
以浸透增强为主,兼顾被覆,用性能好的粘着剂并加浸透剂,采用较高的上浆率。
粗特纱:
以被覆为主,贴伏毛羽,用天然淀粉加助剂即可。
捻度大的纱线:
结构紧密,加浸透剂或增大压浆力股线和加捻长丝:
可不上浆或上轻浆。
化纤混纺纱:
增加纤维抱合力,加浸透剂、吸湿剂、抗静电剂。
3、织物组织、密度、用途交织次数多,密度大:
单位长度上受到机械作用次数多,则相应上浆率要高且选用好的黏着剂,添加柔软剂、减摩剂、浸透剂等。
4、织造工艺条件:
织机速度、环境温湿度等。
考虑添加吸湿剂、抗静电剂、减摩剂等。
工艺:
使各种原材料、半成品加工成为产品的方法和过程。
11,浆纱疵点1、上浆不匀:
由于浆液黏度、温度、压浆力、浆纱速度的波动以及浆液起泡等原因,使上浆率忽大忽小,严重者形成重浆和轻浆疵点。
2、回潮不匀:
烘燥温度和浆纱速度不稳定是回潮不匀的主要原因。
浆纱回潮率过大,浆纱耐磨性差,浆膜发粘,纱线易粘在一起,使织机开口不清,易产生跳花,蛛网等疵布,同时断头增加,纱线易发霉。
回潮率过小,浆纱容易发生脆断头,并且浆膜易被刮落,纱线起毛而断头。
3、张力不匀:
浆纱过程中引起张力不匀的因素很多。
反映在织物上,张力过小形成经缩疵点,过大产生吊经疵点。
5、倒、并、绞头:
浆纱断头后缠绕导纱部件会产生浆轴倒断头疵点,干分绞断头造成并头,断头处理不当,夹纱等造成绞头6、松边或叠边:
浆轴盘片歪斜或伸缩筘位置调节不当。
7、墨印长度不正确、流印、漏印:
长短码8、油污:
机器润滑油、浆液内油乳等。
9、浆斑:
浆液中的浆皮、浆块沾在纱线上经压轧之后形成分散性块状浆斑。
第五章:
1,如何选用经停片,其穿法有哪些?
顺穿、逆穿、飞穿、照图穿、分区穿、间断穿等。
2,结经和穿经如何使用?
结经只能在不改变织物品种的生产中,而且经停片、综丝和钢筘质量优良或经停片。
综丝和钢筘不需要维修时使用。
穿经在一般情况下都可以使用。
3,经停片排列密度如何计算?
P=总经根数/经停杆排数(1+综框上综丝的上机宽度)
4,综丝排列密度如何计算?
计算综丝排列密度有何意义?
P=总经根数/(综丝列数*综框上综丝的上机宽度);
与经纱的排列密度有直接的关系,对经纱之间的摩擦有关。
5,织物每筘齿穿入数如何确定?
穿入数过大或过小对织造有何影响?
织物每筘齿穿入数影响织物的外观和经纱断头率,应根据织物的经纱密度、织物组织、对胚布的要求和织造条件来定。
同一种织物,采用小的穿入数会使筘号增大,筘齿稠密,虽然有利于经纱均匀分布,但是会增加筘片和经纱之间的摩擦而增加断头,采用大的穿入数,则筘号减小,筘齿稀疏,对经纱摩擦小,但是经纱分布不匀,筘路明显,影响织物外观质量。
6,结经和穿经如何选用?
结经:
把新织轴上的经纱与带有停经片、综丝和钢筘的了机经纱逐根进行打结,然后把新经纱按原来的穿经顺序拉过停经片、综丝和钢筘,完成穿经任务。
应用:
只能在织物品种不变,而且停经片、综丝和钢筘质量优良或停经片、综丝和钢筘不需要维修时使用。
7,穿综方法有哪些?
如何选用?
穿综方法:
根据织物的组织、原料、密度及操作确定。
有顺穿法,飞穿法,照图穿,间断穿,分区穿;
穿综的原则:
交织规律相同的经纱可穿入同一页综框中,也可穿入不同的综页(列),而交织规律不同的经纱必须穿入不同的综页内。
8,布边的作用与要求是什么?
作用:
防止织物在织造过程中幅宽方向的过分收缩使布面平整,减少边部经纱与筘齿的摩擦,减少边经断头;
增加织物强度,防止在染整过程中出现布边撕扯或卷边;
牢固,外观平整,布边组织要简单,缩率一致,边经根数少,尽量不用布边。
9,穿经工序主要质量指标有哪些?
好轴率=(抽检已穿轴数-疵轴数)/抽检已穿轴数检测方法:
按好轴率测试标准在生产现场实查,统计织轴总数和疵轴数,并及时记录疵轴成因,
10,穿经疵点有哪几种?
综穿错产生原因:
穿综顺序不符合工艺要求或漏穿综丝。
织物组织错误,形成经向疵点。
2)筘穿错产生原因:
插筘时插筘刀没有移动而重复插筘;
插筘后跳过一个筘齿。
织物经向稀密路。
3)多头、少头产生原因:
浆轴上有倒断头;
浆轴封头附近有断头,未接好而直接穿经;
浆纱上经轴时有漏头。
绞头、甩头,松紧经疵布。
4)绞头产生原因:
没按浆轴封头夹子上的浆纱排列顺序分纱;
浆纱落轴时封头夹子没有夹紧纱头以至纱头紊乱;
穿经前纱头梳理不良。
松紧经疵布。
5)综丝、钢筘、停经片不良产生原因:
穿经前没有认真检查综丝、钢筘、停经片质量。
经纱断头、织机停台。
6)双经产生原因:
浆纱并头;
穿经时分头不清,一个综眼穿入两根经纱。
布机甩头和布面双经疵点。
7)用错筘号产生原因:
工艺设计错误;
配错钢筘。
织物经密和幅宽不符合工艺要求。
8)绞综产生原因:
综丝没理清,综丝相绞。
布机停台。
9)油污渍产生原因:
织轴污染油污渍;
综丝、钢筘、停经片有锈渍、污渍。
布面油污疵点。
第六章:
1,纬纱准备包括:
络筒、纬纱定捻和卷纬等工序。
纬纱加工形式直接纬和间接纬。
2,有梭织机纬纱准备工艺流程?
棉白织生产:
中、低档产品用直接纬,高档产品用间接纬。
直接纬工艺流程:
管纱→给湿或自然定捻→织造
棉色织、丝织、毛织和麻织生产:
采用间接纬。
废棉纺纱、黄麻纱和低支毛毯纱,卷成空心纡间接纬工艺流程:
纯棉织物:
管纱→络筒→卷纬→给湿或自然定捻→织造
涤/棉织物:
管纱→络筒→定捻→卷纬→织造或管纱→定捻→络筒→卷纬→织造
3,无梭织机纬纱准备工艺流程?
自然或给湿定捻:
管纱→自然或给湿定捻→络筒→织造或管纱→络筒→自然或给湿定捻→织造;
热湿定捻:
管纱→络筒→热湿定捻→织造或管纱→热湿定捻→络筒→织造
4,纬纱定捻方法有哪几种?
各有何优缺点?
一,自然定捻适用于纱线捻度低,捻度容易稳定,原料周转比较充裕的情况,如低捻真丝,棉纬纱和一些涤棉股线二,给湿定捻喷雾法用于棉织生产,给湿间給湿用于丝织生产三,水浸法适合亲水性纤维四,机械給湿法适用于棉织生产五,纱线加热定捻适用于中低捻度人造丝的定捻六热湿定捻,应用范围广,对细特纱,强捻纱混纺纱较为合适。
5,棉纱定捻工艺棉纱特点:
棉纤维细而柔软,抗捻力不大,只需对纬纱进行自然或给湿定捻,但强捻经纬纱需热湿定捻。
定捻工艺:
筒子定捻,压力1.02×
104Pa,蒸纱时间40~60min。
涤棉纱定捻工艺涤棉纱特点:
涤棉纱的弹性好,反捻力强,应采用热湿定捻。
定捻温度不易过高,最好在65~70℃,最高不超过100℃,否则会影响印染成品的质量。
定捻温度80~85℃,保温时间40~50min,真空度66.65kPa,压力不超过0.5×
105Pa。
6,如何评价定捻效果?
1.目测法:
两手伸开执长度为100cm的纱,然后缓慢移近至两手距离为20cm时,看下垂纱线的扭结程度,一般以不超过3~5转为准。
2.手执法:
两手执长度为50cm或100cm的纱线两端,一端固定,一端缓慢平行移近至打扭为止,测量其长度,计算定捻效率(捻度稳定度)。
定捻效率在40%~60%即能满足织造的工艺要求。
P=1-b/a
7,卷纬工艺参数设计主要包括哪些内容?
卷纬工艺参数包括卷纬速度、卷纬张力和纡子卷绕密度;
卷纬速度主要根据卷纬机机型,纱线种类及纱特确定;
卷纬张力应根据原料性质织物品种纱线粗细和纱线的捻度等因素而确定;
纡子卷绕密度主要有卷绕张力确定,也与卷装形式,卷绕速度,纱线特数,纱线原料等因素有关。
第七章:
1,平纹织物为什么采用早开口、高后梁?
因为平纹织物纱线交织次数多,打纬阻力大,且容易产生筘路织疵,因此采用早开口织造,以利于织物紧密厚实,布面平整、丰满,清除筘痕。
又因为平纹织物交织次数多,纱线特数较高经纬密度不是很大。
织造时打纬阻力较大,且容易产生筘痕织疵,所以应采用较高的后梁,使上下层经纱张力的差异增大,以利于经纱排列匀整、减少筘痕、打紧纬纱,达到布面平整、丰满,条影少的外观要求。
3,在有梭织机上生产府绸织物时,如何确定织造工艺参数,简述理由。
A,开口时间应比平布类早,因为府绸经密大,梭口不易开清,所以一般采用早开口,以利于开清梭口,布面匀整丰满,减少条影、纬缩、边跳花等疵点。
B,在梭口清晰和不增加断头的条件下,适当抬高后梁,以求颗粒突出,布面匀整。
C,投梭时间应较平布