摇臂座加工工艺编制Word文档下载推荐.docx
《摇臂座加工工艺编制Word文档下载推荐.docx》由会员分享,可在线阅读,更多相关《摇臂座加工工艺编制Word文档下载推荐.docx(17页珍藏版)》请在冰豆网上搜索。
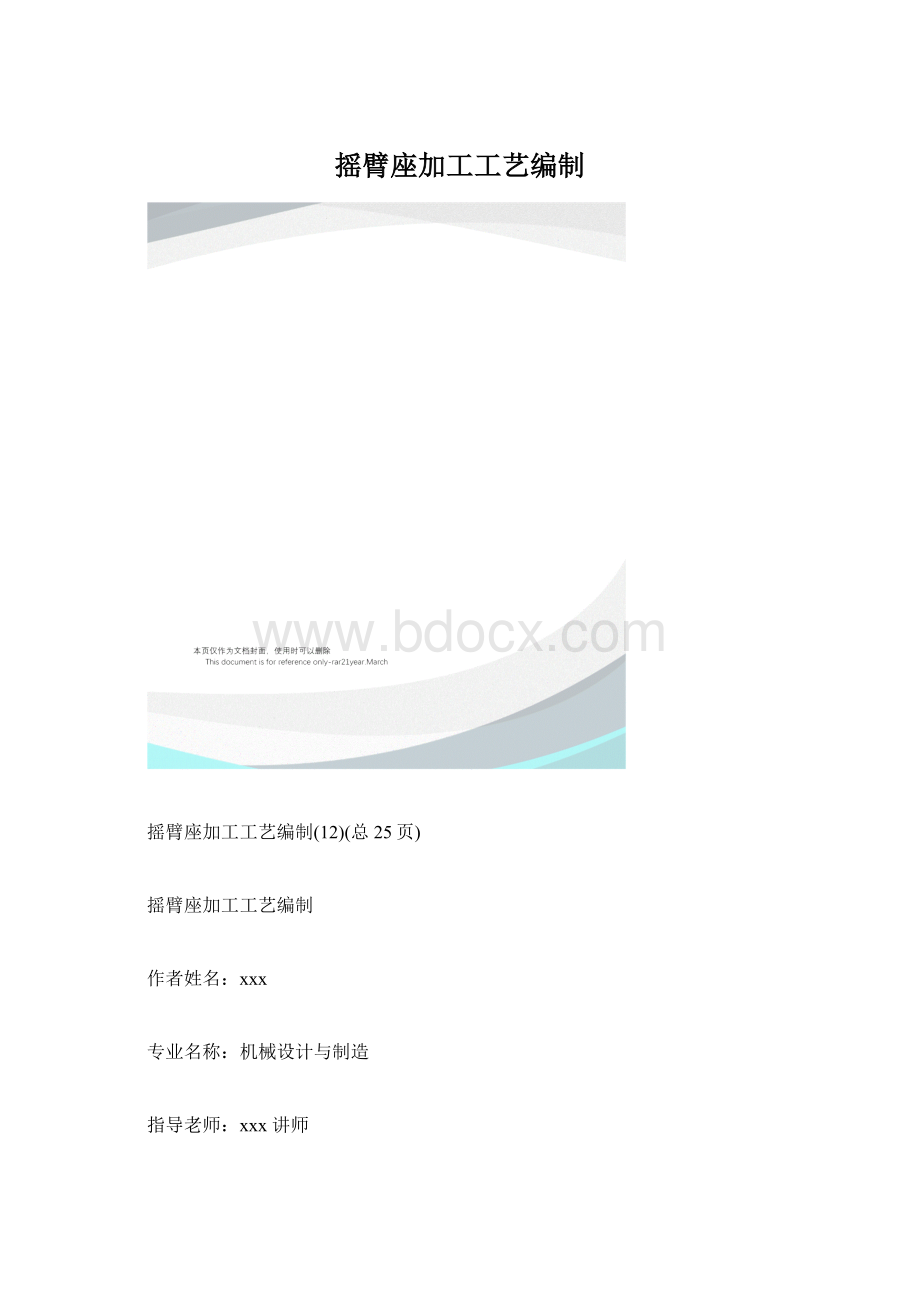
巩固已学过的各类专业知识。
论文正文主要包括4个部分,安排如下:
第1部分简要介绍摇臂座的主要功能和工作特点。
第2部分阐述摇臂座的工艺分析。
第3部分选择毛坯和确定毛坯。
第4部分选择摇臂座的加工方法和工艺路线。
最后论文对课题内容及成果进行了总结。
1摇臂座的主要功能概述
1.1摇臂座的作用
1.摇臂座主要作用:
摇臂座是固定摇臂的底座,起固定作用。
在顶置式气门发动机中,摇臂座是进排气机构的一个部件。
进排气机构是由凸轮轴、挺杆、摇臂、摇臂轴、摇臂座、气门、气门弹簧等零件组成。
气门的开启和关闭是由挺杆和摇臂动作完成的,摇臂就是通过摇臂轴安装在摇臂座上,一端是从凸轮轴经挺杆驱动,另一端顶在气门杆上和弹簧一起作用控制气门的开合。
柴油机中的摇臂座,是支撑摇臂轴的,其作用相当于滑动轴承座,摇臂是安装在摇臂轴上的。
1.2.摇臂座的零件图:
(1-1图为摇臂座的主视图)
(1-2图为摇臂座的俯视图)
(1-3图为摇臂座的C—C截面图)
(1-4图为摇臂座的三维模型)
2零件的工艺分析
2.1.分析零件的结构
该零件有三个通孔,一个孔为Φ20﹢0.035,第二个孔为Φ16﹢0.035,第三个孔为Φ12.5。
零件底座为40×
32厚度为8的长方形,R10×
4的圆角。
在孔Φ20﹢0.035上方有一个与该孔中心轴线呈20度的圆形台。
主结构上伸出一条R12、R30、R6的悬臂.主结构上有一个Φ12.5深度为55﹢0.1的通孔。
孔Φ12.5为中心的加工表面,加工面包括Φ24平面,底端面40×
32,Φ18的斜面,主要加工表面为底端面。
2.2.零件的加工基准
基准是用来确定工件上其他几何要素之间的几何关系所依据的那些点、线、面。
基准根据其用途不同,可分为设计基准和工艺基准两大类。
设计基准是指在零件图上标注设计尺寸时所采用的基准。
工艺基准是指零件在加工过程中中采用的基准。
按照用途不同,工艺基准又分为工序基准、定位基准、测量基准和装配基准。
2.2.1.零件的设计基准
摇臂座底座是主结构的设计基准。
Φ20﹢0.035结构孔为尺寸24±
0.05的设计基准。
摇臂座底座是Φ20﹢0.035孔的设计基准。
Φ20﹢0.035结构孔为孔Φ16﹢0.035的设计基准。
2.2.2.零件的工艺基准
零件的上表面是以摇臂底座为工序基准。
Φ12.5的孔是以摇臂座底面为基准,孔中心线与底面垂直。
Φ16﹢0.035的以孔摇臂座底面做工序基准,其孔轴线与底面平行。
悬臂的工序基准是孔Φ12.5的中心轴线。
孔Φ20﹢0.035的工序基准是摇臂座底面,该孔中心轴线与摇臂座底面平行。
Φ18圆形凸台的工序基准是以孔20﹢0.035的中心轴线所定,呈20度。
孔Φ20﹢0.035、孔Φ16﹢0.035、孔Φ12.5的定位基准为其中心轴线。
零件其他部分的定位基准为摇臂座底座。
以孔Φ20﹢0.035为中心的加工表面为孔和倒角,孔Φ34的两端面。
以孔Φ16﹢0.035为中心的加工表面有,孔孔Φ16﹢0.035和倒角,铣Φ28两端面。
孔Φ20﹢0.035与孔孔Φ12.5孔底面的平行度公差为0.25。
Φ34两端面与孔Φ20﹢0.035的垂直度公差为0.08。
孔Φ16﹢0.035与孔Φ20﹢0.035的平行度公差为100:
0.10
3零件毛坯的选用
3.1.毛坯的选择
毛坯的好坏,对零件的加工质量、加工方法、材料利用率、加工劳动量和制造成本等都有很大的影响。
机械加工中常用的毛坯有铸件、锻件、型材、焊接件等。
外形尺寸较大的零件,一般用自由锻件或砂型铸造件;
零件尺寸较大但结构较简单时,可选用焊接件;
中小型零件可选用模锻件或特种铸造毛坯件;
阶梯轴零件,各台阶直径相差不大时可选用棒料,相差较大时可选用锻件;
形状复杂、薄壁的零件,往往不能采用金属型铸造毛坯。
摇臂座是顶置式气门发动机中,进排气机构的一个部件。
该毛坯为中小型零件,材料选择HT20—40灰铸铁,年产量为中批量生产,采用铸造生产方法。
3.2.毛坯尺寸的确定
摇臂座零件材料选择HT20—40灰铸铁,毛坯采用铸造生产方法。
铸造采用金属模机械工业砂型。
精度等级达到(CT)8—9,毛坯公差1—3,加工余量等级为G。
差《机械制造工艺设计简明手册》以下简称《工艺手册》表13-1。
根据上述原始资料及加工工艺,分别确定各加工表面的机械加工余量,工序尺寸及毛坯尺寸。
⑴铣24底面、铣24顶面、铣18斜侧面。
毛坯精度等级为9级,查《工艺手册》表2.2—4,加工余量为3。
⑵内孔Φ20﹢0.035,毛坯为实心,不冲出孔。
内孔精度为8—10,参考《工艺手册》表2.3—9。
钻孔:
18.0
扩孔:
Φ19.8
Z=1.8
铰孔:
Φ20+0.035
Z=0.2
(表3-1)
⑶内孔Φ16﹢0.035
15.0
Φ15.85
Z=0.85
Φ16+0.035
Z=0.15
(表3-2)
⑷34两端面的加工余量
按照《工艺手册》表1.4—8加工余量等级介入8—10级,表2.2—4。
毛坯尺寸
铸造尺寸
零件尺寸
单加工余量
74
67-0.2
上3下4
29
24+0.10
2.5
21
16±
0.20
2.5
(表3-3)
尺寸允许偏差
偏差
67—0.2
±
0.8
0.5
(表3-4)
3.3基准面的选择
基面选择是工艺规程中的重要工作之一。
基面选择正确合理,可以使加工质量得到保证,生产率得以提高。
否则,加工工艺过程中会问题百出,更有甚者,还会造成零件的大批报废,试生产无法正常进行。
3.3.1.粗基准的选择
确定基准时除了考虑满足有关的基准选择原则外,还要考虑怎样实现所选择的基准,确定各工序基准与定位及夹紧方式,还有夹紧位置和夹紧作用方向。
要考虑定位精度的要求,分析定位误差,故选Φ24的上端面为粗基准面,摇臂座底端面为精基准。
3.3.2.摇臂座定位基准的分析
底面精度应以下端面为基准,铣上端面。
其次以上顶面为基准,粗铣下底面。
再以上顶面为基准,精铣下底面。
以下底面为基准,粗铣Φ18的圆台。
以下底面为基准,钻孔Φ12.5
由于圆柱面与底座平行,则应以底座为粗基准铣圆柱Φ34端面,粗铣圆柱梯形端面分三个工序。
圆柱孔的中心线垂直端面,则应以端面为基准对孔进行钻、扩、铰,其中应换钻头,已达到相应的精度。
再以孔中心线为基准,精铣圆柱端面。
3.4.毛坯图设计
(图3-1)
4选择加工方法制定工艺路线
4.1.加工方法的选择
制定工艺路线的出发点,应当是零件的几何形状,尺寸精度及位置精度等技术要求能得到合理的保证。
在生产纲领已确定为重批量生产的条件下,可以考虑采用使用专用夹具,并尽量使工序集中来提高生产率,除此以外,还应当考虑经济效果,以便使生产成本尽量下降。
由于摇臂座是多面体零件,所以粗加工加工时选择铣床,精加工时选择铣床和磨床。
4.2工艺路线方案的制定
工序一
铣Φ24上端面
工序二
铣Φ24底端面
工序三
钻Φ12.5的孔
工序四
铣Φ34两端面
工序五
铣Φ28两端面
工序六
钻、扩、铰Φ20﹢0.035的孔
工序七
钻、扩、铰Φ16﹢0.035的孔
倒角0.5×
45°
工序八
铣Φ18斜端面
工序九
去毛刺,锐边
工序十
终检,入库
(表4-1)
4.3.工艺方案的比较与分析
工艺方案二
铸造
退火
粗铣Φ22圆柱端面、22×
36底面
精铣22×
精铣Φ28圆柱端面、Φ26圆柱端面
精铣Φ28圆柱两端面
钻孔Φ11
钻、扩、铰Φ18、Φ16两孔至图样尺寸并锪倒角1×
45
钻孔Φ3
去锐边、毛刺
工序十一
终检、入库
(表4-2)
上述两个方案的特点在于:
方案一是先加工Φ28、Φ26两圆柱端面,然后以此为基面加工22×
36底面,再以该底面为定位基准加工孔;
方案二则与此相反,先是加工22×
36底面,然后以此为基准加工各端面和孔。
两者相比较可以看出,方案二的精基准符合“基准重合”原则,而方案一前后精基准选择不符合。
用方案一加工的两Φ18+0.027、Φ16+0.11孔达不到图样的要求,因此方案二好,但是仔细考虑后还是有问题。
根据先面后孔、先主要表面后次要表面和先粗加工后精加工的原则,最后的加工路线确定如下:
序号
工序内容
定位基准
1
2
改善材料性能
3
粗铣底平面
以上圆柱端面定位
4
粗铣圆柱上端面
以底面定位
5
粗铣Φ26、Φ28圆柱两端面
6
精铣底平面
7
钻Φ11孔
划线
8
精铣Φ28圆柱端面
9
钻→扩→铰Φ18+0.027、Φ16+0.11孔
10
Φ18+0.027、Φ16+0.11两孔两端倒角1×
各圆柱端面
11
Φ18+0.027、Φ16+0.11两孔
12
去毛刺、锐边
13
(表4-3)
4.4.选择加工方法:
选择加工方法应该考虑各种加工方法的特点、加工精度、表面粗糙度及各种加工方法的经济性。
分析该零件,该零件要加工的内容有端面和孔,零件为非回转体零件,端面加工选择铣削加工。
对于上端面Φ22圆柱端面,粗糙度12.5,无其他要求,粗铣即可。
底面22×
36采用粗铣→精铣。
Φ26圆柱端面粗糙度要求12.5,无其他要求,采用粗铣即可。
Φ28圆柱2端面粗糙度要求3.2,圆跳动0.1,采用粗铣→精铣。
孔的加工:
Φ11、
3孔粗糙度12.5,直接钻孔即可。
Φ18+0.027、Φ16+0.11孔粗糙度要求1.6,精度等级较高,有平行度要求,采用钻→扩→铰孔即可满足要求。
4.4.1.选择加工设备及工艺装备
1.平面加工:
采用铣削,工序3、4、5、6、8由于是批量生产,要求加工效率较高,选择立式铣床采用端铣效率较高。
选择机床型号X52
2.孔加工:
工序7、9、11,选择立式钻床Z525,工序9采用摇臂钻床Z3025。
3.夹具选择:
该零件的加工内容是孔和端面,其中孔Φ18+0.027、Φ16+0.11精度要求高,孔Φ3是斜小孔,铣底平面,都需要专用夹具。
精铣Φ28圆柱两端面精度要求较高,且有圆跳动要求,需采用专用夹具其余加工采用通用夹具。
4.刀具选择:
铣削加工:
选择错齿三面刃铣刀。
钻削加工:
钻孔Φ11采用锥柄麻花钻(GB1438-85)直径d=11mm,Φ3采用d=3mm锥柄麻花钻。
钻孔Φ18+0.027采用d=16mm锥柄麻花钻,钻孔Φ16+0.11采用d=14mm锥柄麻花钻。
(由文献[1]表3.1-6)。
扩孔Φ18+0.027、Φ16+0.11分别采用d=17.8mm,d=15.8mm锥柄扩孔钻(GB1141-84)(由文献[1]表3.1-8)
铰孔Φ18+0.027、Φ16+0.11分别选择d=18mm,d=16mm锥柄机用铰刀(GB1133-84)(由文献[1]表3.1-17)。
4.4.1.确定切削用量及基本工时:
1.工序3(粗铣底平面)切削用量及时间定额:
工序实际切削用量
=0.105mm/z,
=950mm/min,n=750r/min=12.5r/s
v=2.18m/s
时间定额:
min
2.工序4粗铣上端面:
=900mm/min,n=750r/min=12.5r/s
0.022min
3.工序5(粗铣Φ28、Φ26两圆柱两端面)切削用量及时间定额:
工序时间定额:
本工序加工面为两个圆柱的4个端面,时间为加工4个端面的和.
0.04min
0.037min
=0.077min。
由于每个圆柱要铣2个端面,时间是计算时间的2倍,总时间
=0.15min。
4.工序6(精铣底平面)切削用量及时间定额:
实际切削速度:
V=47.1m/min。
实际
=375mm/min,
0.067mm/z
工序时间定额:
0.116min
5.工序7(钻孔Φ11)切削用量及时间定额:
切削工时:
=17.8s=0.3min
6.工序8(精铣Φ28圆柱两端面)切削用量及时间定额:
0.097min
7.工序9(钻、扩、铰孔Φ18+0.027、Φ16+0.11)切削用量及时间定额:
A.钻孔Φ16+0.11至Φ14,
由文献[11]表9-32,f=0.26~0.32mm/r,取f=0.26mm/r
由文献[11]表9-36,取v=0.35m/s
代入公式
=8r/s=480r/min
由文献[1]表4.2-12,机床为Z3025,选择转速
=500r/min
则实际切削速度:
v=0.37mm/r
扩孔至
15.8钻孔
f=0.5mm/r(由文献[11]表9-42)
v=0.48m/s(由文献[11]表9-44)
=9.7r/s=582r/min
由文献[1]表4.2-12,机床为Z3025,选择转速:
=630r/min=10.5r/s
v=0.52m/s
铰孔Φ16+0.11:
由文献[11]表9-50,f=1.0mm/r,v=0.155m/s带入:
=3.09r/s=185.4r/min。
=200r/min。
实际速度:
v=0.167m/s。
=18.8
19s
B.钻Φ18+0.027至Φ16
由文献[11]表9-32,取f=0.26mm/r
由文献[11]表9-36,取v=0.30m/s
代入公式:
=5.95r/s=357r/min
取机床实际转速:
=400m/min,则实际切削速度:
v=0.32m/s
扩孔至Φ17.8
v=0.48m/s(由文献[11]表9-44)代入公式:
n=8.6r/s=516r/min
n=630r/min=10.5r/s
v=0.599m/s
铰孔Φ18+0.027
由文献[11]表9-50,f=1.8mm/r,v=0.13m/s代入
得=2.3r/s=138r/min。
n=125r/min=2.08r/s
v=0.11m/s
工序总时间定额:
55s≈1min
8.工序11(钻孔Φ3)切削用量及时间定额:
=17.1s
总结
论文首先简要分析了摇臂座的主要功能、作用。
作出了摇臂座的平面和三维的零件图。
然后简单分析了零件的工艺,其中包括对零件结构的分析。
还分析了零件的加工基准,其中又对零件的设计基准和工艺基准做了初步的分析。
在前面两个部分的基础上,论文对零件的毛坯件的选用做了详细的分析。
首先从毛坯材料的选择开始,我们根据零件的实际用途和工作性质选择合适的材料;
其次对毛坯件的各个部分的尺寸进行计算确定,选择加工基准面和做定位基准的分析;
最后进行毛坯图的绘制。
论文的最后对零件的加工方法及工艺路线进行了详细的制定。
根据零件的使用要求选择零件的加工方法,列出了多种工艺方案,并将其比较分析,选出最合适最经济的工艺路线。
确定加工方法和工艺路线方案后,对加工中所需要的加工设备和工艺设备进行选择。
总的来说,此次毕业实习及毕业设计完成了任务书规定的各项要求,对已学过的知识进行了巩固和复习以及与实际操作相结合的学习体验,让我更深刻的掌握了专业知识。
既学习了不少新的知识和技术,又温习了以前的知识,个人觉得收获颇丰。
当然,这次设计的摇臂座加工工艺编制还不完善,还可以从对零件的主要功能和工艺分析上做进一步的完善
最后敬请各位专家、老师和同学对论文和今后的研究工作提出宝贵的指导意见和建议。
致谢
大学三年学习时光已经接近尾声,在此我想对我的母校,我的父母、亲人们,我的老师和同学们表达我由衷的谢意。
大学生活一晃而过,回首走过的岁月,心中倍感充实,当我写完这篇毕业论文的时候,有一种如释重负的感觉,感慨良多。
首先诚挚的感谢我的论文指导老师郑才国老师。
他在忙碌的教学工作中挤出时间来审查、修改我的论文。
还有教过我的所有老师们,你们严谨细致、一丝不苟的作风一直是我工作、学习中的榜样;
他们循循善诱的教导和不拘一格的思路给予我无尽的启迪。
本论文是在导师郑才国讲师的悉心指导下完成的。
导师渊博的专业知识,严谨的治学态度,精益求精的工作作风,诲人不倦的高尚师德,严以律己、宽以待人的崇高风范,朴实无华、平易近人的人格魅力对我影响深远。
不仅使我树立了远大的学术目标、掌握了基本的研究方法,还使我明白了许多待人接物与为人处世的道理。
本论文从选题到完成,每一步都是在导师的指导下完成的,倾注了导师大量的心血。
在此,谨向导师表示崇高的敬意和衷心的感谢!
本论文的顺利完成,离不开各位老师、同学和朋友的关心和帮助。
参考文献
[1]李益民.机械制造工艺设计简明手册[M].北京.机械工业出版社.1993.4
[2]倪森寿.机械制造工艺与装备[M].北京.化学工业出版社,2003.
[3]周光万.机械制造工艺学[M].成都.西南交大出版社.2010.
[4]李旦.机械制造工艺学[M].哈尔滨.哈尔滨工业大学出版社.2003.
[5]骆志斌.金属工艺学[M].北京.高等教育出版社.20