金属材料热处理试题答案文档格式.docx
《金属材料热处理试题答案文档格式.docx》由会员分享,可在线阅读,更多相关《金属材料热处理试题答案文档格式.docx(15页珍藏版)》请在冰豆网上搜索。
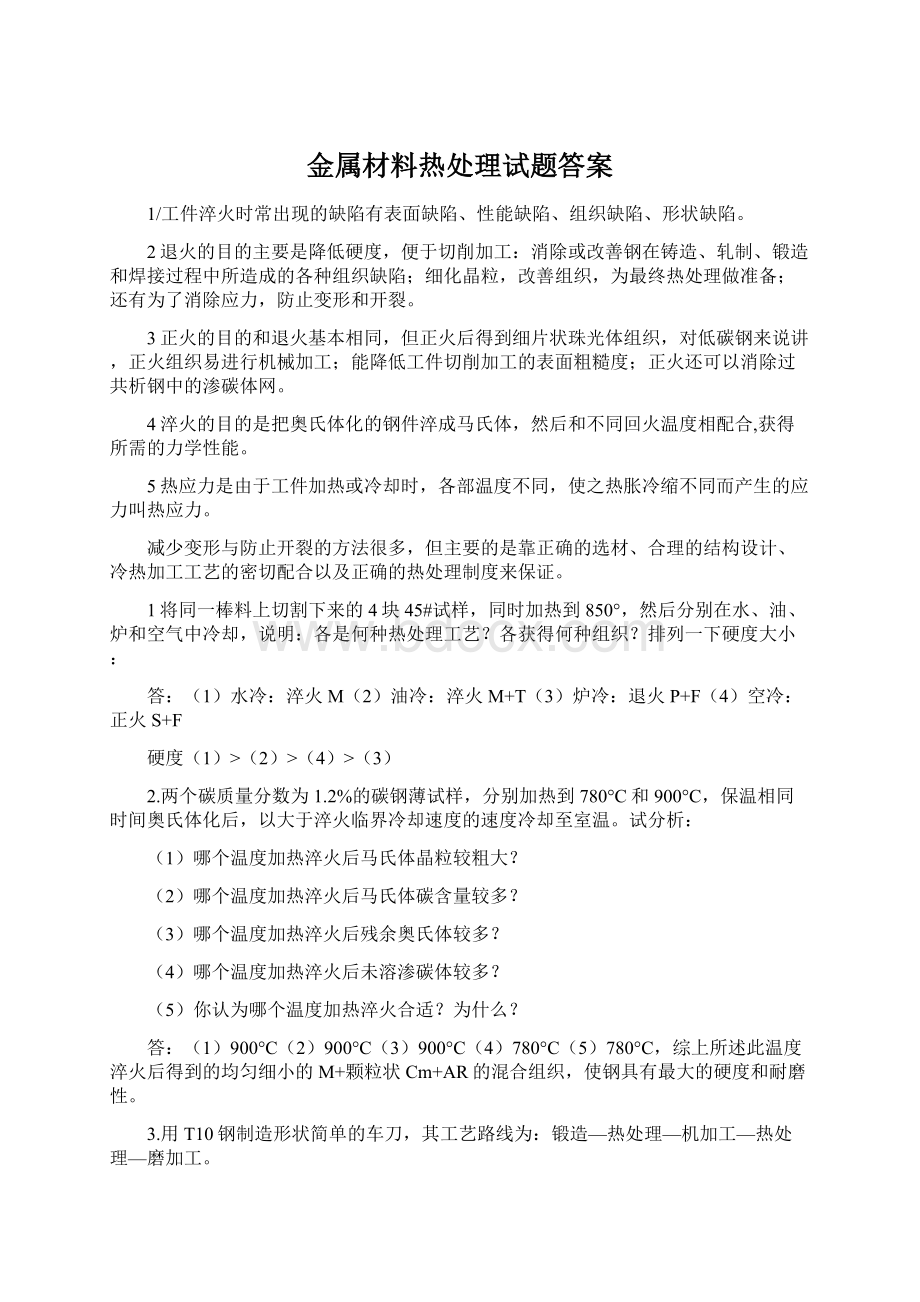
(5)你认为哪个温度加热淬火合适?
为什么?
(1)900°
C
(2)900°
C(3)900°
C(4)780°
C(5)780°
C,综上所述此温度淬火后得到的均匀细小的M+颗粒状Cm+AR的混合组织,使钢具有最大的硬度和耐磨性。
3.用T10钢制造形状简单的车刀,其工艺路线为:
锻造—热处理—机加工—热处理—磨加工。
(1)写出其中热处理工序的名称及作用。
(2)制定最终热处理(磨加工前的热处理)的工艺规范,并指出车刀在使用状态下的显微组织和大致硬度。
答:
(1)球化退火,作用:
利于切削加工。
得到球状珠光体,均匀组织,细化晶粒,为后面淬火处理作组织准备。
淬火+低温回火,作用:
使零件获得较高的硬度、耐磨性和韧性,消除淬火内应力,稳定组织和尺寸。
(2)工艺规范:
760°
C水淬+200°
C回火;
显微组织:
M回+Cm,大致硬度:
60HRC.
4.如下图所示,T12钢加热到Ac1以上,用图示
的各种方法冷却,分析各自得到的组织。
A:
水中淬火M+Fe3C
B:
分级淬火M+Fe3C
C:
油中淬火M+T+Fe3C
D:
等温淬火B下+Fe3C
E:
正火S+Fe3C
F:
完全退火P+Fe3C
G:
等温退火P+Fe3C
5为改善可加工性,确定下列钢件的预备热处理方法,并指出所得到组织:
(1)20钢钢板
(2)T8钢锯条
(3)具有片状渗碳体的T12钢钢坯
(1)20钢钢板:
正火S+F
(2)T8钢锯条:
球化退火球状P;
(3)具有片状渗碳体的T12钢钢坯:
球化退火球状P+Cm
6指出下列工件的淬火及回火温度,并说明其回火后获得的组织和大致的硬度:
(1)45钢小轴(要求综合机械性能);
(2)60钢弹簧;
(3)T12钢锉刀。
(1)45钢小轴(要求综合机械性能),工件的淬火温度为850℃左右,回火温度为500℃~650℃左右,其回火后获得的组织为回火索氏体,大致的硬度25~35HRC。
(2)60钢弹簧,工件的淬火温度为850℃左右,回火温度为350℃~500℃左右,其回火后获得的组织为回火屈氏体,大致的硬度40~48HRC。
(3)T12钢锉刀,工件的淬火温度为780℃左右,回火温度为150℃~250℃,其回火后获得的组织为回火马氏体,大致的硬度60HRC。
7指出下列零件的锻造毛坯进行正火的主要目的及正火后的显微组织:
(1)20钢齿轮
(2)45钢小轴(3)T12钢锉刀
(1)目的:
细化晶粒,均匀组织,消除内应力,提高硬度,改善切削加工性。
组织:
晶粒均匀细小的大量铁素体和少量索氏体。
(2)目的:
细化晶粒,均匀组织,消除内应力。
晶粒均匀细小的铁
素体和索氏体。
(3)目的:
细化晶粒,均匀组织,消除网状Fe3CⅡ,为球化退火做组织准备,消除内应力。
索氏体和球状渗碳体。
8确定下列钢件的退火方法,并指出退火目的及退火后的组织:
1)经冷轧后的15钢钢板,要求降低硬度;
再结晶退火。
目的:
使变形晶粒重新转变为等轴晶粒,以消除加工硬化现象,降低了硬度,消除内应力。
细化晶粒,均匀组织,消除内应力,降低硬度以消除加工硬化现象。
等轴晶的大量铁素体和少量珠光体。
2)ZG35的铸造齿轮
完全退火。
经铸造后的齿轮存在晶粒粗大并不均匀现象,且存在残余内应力。
因此退火目的:
细化晶粒,均匀组织,消除内应力,降低硬度,改善切削加工性。
晶粒均匀细小的铁素体和珠光体。
3)锻造过热后的60钢锻坯;
由于锻造过热后组织晶粒剧烈粗化并分布不均匀,且存在残余内应力。
晶粒均匀细小的少量铁素体和大量珠光体。
4)具有片状渗碳体的T12钢坯;
球化退火。
由于T12钢坯里的渗碳体呈片状,因此不仅硬度高,难以切削加工,而且增大钢的脆性,容易产生淬火变形及开裂。
通过球化退火,使层状渗碳体和网状渗碳体变为球状渗碳体,以降低硬度,均匀组织、改善切削加工性。
粒状珠光体和球状渗碳体。
9何谓钢的热处理?
钢的热处理操作有哪些基本类型?
试说明热处理同其它工艺过程的关系及其在机械制造中的地位和作用。
(1)为了改变钢材内部的组织结构,以满足对零件的加工性能和使用性能的要求所施加的一种综合的热加工工艺过程。
(2)热处理包括普通热处理和表面热处理;
普通热处理里面包括退火、正火、淬火和回火,表面热处理包括表面淬火和化学热处理,表面淬火包括火焰加热表面淬火和感应加热表面淬火,化学热处理包括渗碳、渗氮和碳氮共渗等。
(3)热处理是机器零件加工工艺过程中的重要工序。
一个毛坯件经过预备热处理,然后进行切削加工,再经过最终热处理,经过精加工,最后装配成为零件。
热处理在机械制造中具有重要的地位和作用,适当的热处理可以显着提高钢的机械性能,延长机器零件的使用寿命。
热处理工艺不但可以强化金属材料、充分挖掘材料潜力、降低结构重量、节省材料和能源,而且能够提高机械产品质量、大幅度延长机器零件的使用寿命,做到一个顶几个、顶十几个。
此外,通过热处理还可使工件表面具有抗磨损、耐腐蚀等特殊物理化学性能。
10.为什么要对钢件进行热处理?
通过热处理可以改变钢的组织结构,从而改善钢的性能。
热处理可以显着提高钢的机械性能,延长机器零件的使用寿命。
恰当的热处理工艺可以消除铸、锻、焊等热加工工艺造成的各种缺陷,细化晶粒、消除偏析、降低内应力,使钢的组织和性能更加均匀。
11.退火的主要目的是什么?
生产上常用的退火操作有哪几种?
指出退火操作的应用范围。
(1)均匀钢的化学成分及组织,细化晶粒,调整硬度,并消除内应力和加工硬化,改善钢的切削加工性能并为随后的淬火作好组织准备。
(2)生产上常用的退火操作有完全退火、等温退火、球化退火、去应力退火等。
(3)完全退火和等温退火用于亚共析钢成分的碳钢和合金钢的铸件、锻件及热轧型材。
有时也用于焊接结构。
球化退火主要用于共析或过共析成分的碳钢及合金钢。
去应力退火主要用于消除铸件、锻件、焊接件、冷冲压件(或冷拔件)及机加工的残余内应力。
12何谓球化退火?
为什么过共析钢必须采用球化退火而不采用完全退火?
(1)将钢件加热到Ac1以上30~50℃,保温一定时间后随炉缓慢冷却至600℃后出炉空冷。
(2)过共析钢组织若为层状渗碳体和网状二次渗碳体时,不仅硬度高,难以切削加工,而且增大钢的脆性,容易产生淬火变形及开裂。
13正火与退火的主要区别是什么?
生产中应如何选择正火及退火?
与退火的区别是①加热温度不同,对于过共析钢退火加热温度在Ac1以上30~50℃而正火加热温度在Accm以上30~50℃。
②冷速快,组织细,强度和硬度有所提高。
当钢件尺寸较小时,正火后组织:
S,而退火后组织:
P。
选择:
(1)从切削加工性上考虑
切削加工性又包括硬度,切削脆性,表面粗糙度及对刀具的磨损等。
一般金属的硬度在HB170~230范围内,切削性能较好。
高于它过硬,难以加工,且刀具磨损快;
过低则切屑不易断,造成刀具发热和磨损,加工后的零件表面粗糙度很大。
对于低、中碳结构钢以正火作为预先热处理比较合适,高碳结构钢和工具钢则以退火为宜。
至于合金钢,由于合金元素的加入,使钢的硬度有所提高,故中碳以上的合金钢一般都采用退火以改善切削性。
(2)从使用性能上考虑
如工件性能要求不太高,随后不再进行淬火和回火,那么往往用正火来提高其机械性能,但若零件的形状比较复杂,正火的冷却速度有形成裂纹的危险,应采用退火。
(3)从经济上考虑
正火比退火的生产周期短,耗能少,且操作简便,故在可能的条件下,应优先考虑以正火代替退火。
14一批45钢试样(尺寸Φ15*10mm),因其组织、晶粒大小不均匀,需采用退火处理。
拟采用以下几种退火工艺;
(1)缓慢加热至700℃,保温足够时间,随炉冷却至室温;
(2)缓慢加热至840℃,保温足够时间,随炉冷却至室温;
(3)缓慢加热至1100℃,保温足够时间,随炉冷却至室温;
问上述三种工艺各得到何种组织?
若要得到大小均匀的细小晶粒,选何种工艺最合适?
(1)因其未达到退火温度,加热时没有经过完全奥氏体化,故冷却后依然得到组织、晶粒大小不均匀的铁素体和珠光体。
(2)因其在退火温度范围内,加热时全部转化为晶粒细小的奥氏体,故冷却后得到组织、晶粒均匀细小的铁素体和珠光体。
(3)因其加热温度过高,加热时奥氏体晶粒剧烈长大,故冷却后得到晶粒粗大的铁素体和珠光体。
要得到大小均匀的细小晶粒,选第二种工艺最合适。
15淬火的目的是什么?
亚共析碳钢及过共析碳钢淬火加热温度应如何选择?
试从获得的组织及性能等方面加以说明。
淬火的目的是使奥氏体化后的工件获得尽量多的马氏体并配以不同温度回火获得各种需要的性能。
亚共析碳钢淬火加热温度Ac3+(30~50℃),淬火后的组织为均匀而细小的马氏体。
因为如果亚共析碳钢加热温度在Ac1~Ac3之间,淬火组织中除马氏体外,还保留一部分铁素体,使钢的强度、硬度降低。
但温度不能超过Ac3点过高,以防奥氏体晶粒粗化,淬火后获得粗大马氏体。
过共析碳钢淬火加热温度Ac1+(30~50℃),淬火后的组织为均匀而细小的马氏体和颗粒状渗碳体及残余奥氏体的混合组织。
如果加热温度超过Accm,渗碳体溶解过多,奥氏体晶粒粗大,会使淬火组织中马氏体针变粗,渗碳体量减少,残余奥氏体量增多,从而降低钢的硬度和耐磨性。
淬火温度过高,淬火后易得到含有显微裂纹的粗片状马氏体,使钢的脆性增加。
16常用的淬火方法有哪几种?
说明它们的主要特点及其应用范围。
常用的淬火方法有单液淬火法、双液淬火法、等温淬火法和分级淬火法。
单液淬火法:
这种方法操作简单,容易实现机械化,自动化,如碳钢在水中淬火,合金钢在油中淬火。
但其缺点是不符合理想淬火冷却速度的要求,水淬容易产生变形和裂纹,油淬容易产生硬度不足或硬度不均匀等现象。
适合于小尺寸且形状简单的工件。
双液淬火法:
采用先水冷再油冷的操作。
充分利用了水在高温区冷速快和油在低温区冷速慢的优点,既可以保证工件得到马氏体组织,又可以降低工件在马氏体区的冷速,减少组织应力,从而防止工件变形或开裂。
适合于尺寸较大、形状复杂的工件。
等温淬火法:
它是将加热的工件放入温度稍高于Ms的硝盐浴或碱浴中,保温足够长的时间使其完成B转变。
等温淬火后获得B下组织。
下贝氏体与回火马氏体相比,在碳量相近,硬度相当的情况下,前者比后者具有较高的塑性与韧性,适用于尺寸较小,形状复杂,要求变形小,具有高硬度和强韧性的工具,模具等。
分级淬火法:
它是将加热的工件先放入温度稍高于Ms的硝盐浴或碱浴中,保温2~5min,使零件内外的温度均匀后,立即取出在空气中冷却。
这种方法可以减少工件内外的温差和减慢马氏体转变时的冷却速度,从而有效地减少内应力,防止产生变形和开裂。
但由于硝盐浴或碱浴的冷却能力低,只能适用于零件尺寸较小,要求变形小,尺寸精度高的工件,如模具、刀具等。
17说明45钢试样(Φ10mm)经下列温度加热、保温并在水中冷却得到的室温组织:
700℃,760℃,840℃,1100℃。
温度
加热后组织
水冷后组织
700°
C
P+F
A+F
M+F
840°
A
M
1100°
700℃:
因为它没有达到相变温度,因此没有发生相变,组织为铁素体和珠光体。
760℃:
它的加热温度在Ac1~Ac3之间,因此组织为铁素体、马氏体和少量残余奥氏体。
840℃:
它的加热温度在Ac3以上,加热时全部转变为奥氏体,冷却后的组织为马氏体和少量残余奥氏体。
1100℃:
因它的加热温度过高,加热时奥氏体晶粒粗化,淬火后得到粗片状马氏体和少量残余奥氏体。
18有两个含碳量为1.2%的碳钢薄试样,分别加热到780℃和860℃并保温相同时间,使之达到平衡状态,然后以大于VK的冷却速度至室温。
试问:
答;
因为860℃加热温度高,加热时形成的奥氏体晶粒粗大,冷却后得到的马氏体晶粒较粗大。
(2)哪个温度加热淬火后马氏体含碳量较多?
答;
因为加热温度860℃已经超过了Accm,此时碳化物全部溶于奥氏体中,奥氏体中含碳量增加,而奥氏体向马氏体转变是非扩散型转变,所以冷却后马氏体含碳量较多。
因为加热温度860℃已经超过了Accm,此时碳化物全部溶于奥氏体中,使奥氏体中含碳量增加,降低钢的Ms和Mf点,淬火后残余奥氏体增多。
(4)哪个温度加热淬火后未溶碳化物较少?
因为加热温度860℃已经超过了Accm,此时碳化物全部溶于奥氏体中,因此加热淬火后未溶碳化物较少
(5)你认为哪个温度加热淬火后合适?
780℃加热淬火后合适。
因为含碳量为1.2%的碳钢属于过共析钢,过共析碳钢淬火加热温度Ac1+(30~50℃),而780℃在这个温度范围内,这时淬火后的组织为均匀而细小的马氏体和颗粒状渗碳体及残余奥氏体的混合组织,使钢具有高的强度、硬度和耐磨性,而且也具有较好的韧性。
19为什么工件经淬火后往往会产生变形,有的甚至开裂?
减小变形及防止开裂有哪些途径?
淬火中变形与开裂的主要原因是由于淬火时形成内应为。
淬火内应力形成的原因不同可分热应力与组织应力两种。
工件在加热和(或)冷却时由于不同部位存在着温度差别而导致热胀和(或)冷缩不一致所引起的应力称为热应力。
热应力引起工件变形特点时:
使平面边为凸面,直角边钝角,长的方向变短,短的方向增长,一句话,使工件趋于球形。
钢中奥氏体比体积最小,奥氏体转变为其它各种组织时比体积都会增大,使钢的体积膨胀;
工件淬火时各部位马氏体转变-先后不一致,因而体积膨胀不均匀。
这种由于热处理过程中各部位冷速的差异使工件各部位相转变的不同时性所引起的应力,称为相变应力(组织应力)。
组织应力引起工件变形的特点却与此相反:
使平面变为凹面,直角变为钝角,长的方向变长;
短的方向缩短,一句话,使尖角趋向于突出。
工件的变形与开裂是热应力与组织应力综合的结果,但热应力与组织应力方向恰好相反,如果热处理适当,它们可部分相互抵消,可使残余应力减小,但是当残余应力超过钢的屈服强度时,工件就发生变形,残余应力超过钢的抗拉强度时,工件就产生开裂。
为减小变形或开裂,出了正确选择钢材和合理设计工件的结构外,在工艺上可采取下列措施:
1.采用合理的锻造与预先热处理
锻造可使网状、带状及不均匀的碳化物呈弥散均匀分布。
淬火前应进行预备热处理(如球化退火与正火),不但可为淬火作好组织准备,而且还可消除工件在前面加工过程中产生的内应力。
2.采用合理的淬火工艺;
正确确定加热温度与加热时间,可避免奥氏体晶粒粗化。
对形状复杂或导热性差的高合金钢,应缓慢加热或多次预热,以减少加热中产生的热应力。
工件在加热炉中安放时,要尽量保证受热均匀,防止加热时变形;
选择合适的淬火冷却介质和洋火方法(如马氏体分级淬火、贝氏体等温淬火),以减少冷却中热应力和相变应力等。
3.淬火后及时回火
淬火内应力如不及时通过回火来消除,对某些形状复杂的或碳的质量分数较高的工件,在等待回火期间就会发生变形与开裂。
4.对于淬火易开裂的部分,如键槽,孔眼等用石棉堵塞。
20淬透性与淬硬层深度两者有何联系和区别?
影响钢淬透性的因素有哪些?
影响钢制零件淬硬层深度的因素有哪些?
淬透性是指钢在淬火时获得淬硬层的能力。
不同的钢在同样的条件下淬硬层深不同,说明不同的钢淬透性不同,淬硬层较深的钢淬透性较好。
淬硬性:
是指钢以大于临界冷却速度冷却时,获得的马氏体组织所能达到的最高硬度。
钢的淬硬性主要决定于马氏体的含碳量,即取决于淬火前奥氏体的含碳量。
影响淬透性的因素:
①化学成分
C曲线距纵坐标愈远,淬火的临界冷却速度愈小,则钢的淬透性愈好。
对于碳钢,钢中含碳量愈接近共析成分,其C曲线愈靠右,临界冷却速度愈小,则淬透性愈好,即亚共析钢的淬透性随含碳量增加而增大,过共析钢的淬透性随含碳量增加而减小。
除Co和Al(>2.5%)以外的大多数合金元素都使C曲线右移,使钢的淬透性增加,因此合金钢的淬透性比碳钢好。
②奥氏体化温度
温度愈高,晶粒愈粗,未溶第二相愈少,淬透性愈好。
21回火的目的是什么?
常用的回火操作有哪几种?
指出各种回火操作得到的组织、性能及其应用范围。
回火的目的是降低淬火钢的脆性,减少或消除内应力,使组织趋于稳定并获得所需要的性能。
常用的回火操作有低温回火、中温回火、高温回火。
低温回火得到的组织是回火马氏体。
内应力和脆性降低,保持了高硬度和高耐磨性。
这种回火主要应用于高碳钢或高碳合金钢制造的工、模具、滚动轴承及渗碳和表面淬火的零件,回火后的硬度一般为HRC58-64。
中温回火后的组织为回火屈氏体,硬度HRC35-45,具有一定的韧性和高的弹性极限及屈服极限。
这种回火主要应用于含碳0.5-0.7%的碳钢和合金钢制造的各类弹簧。
高温回火后的组织为回火索氏体,其硬度HRC25-35,具有适当的强度和足够的塑性和韧性。
这种回火主要应用于含碳0.3-0.5%的碳钢和合金钢制造的各类连接和传动的结构零件,如轴、连杆、螺栓等
22表面淬火的目的是什么?
常用的表面淬火方法有哪几种?
比较它们的优缺点及应用范围。
并说明表面淬火前应采用何种预先热处理。
表面淬火的目的是使工件表层得到强化,使它具有较高的强度,硬度,耐磨性及疲劳极限,而心部为了能承受冲击载荷的作用,仍应保持足够的塑性与韧性。
常用的表面淬火方法有:
1.感应加热表面淬火;
2.火焰加热表面淬火。
感应加热表面淬火是把工件放入有空心铜管绕成的感应器(线圈)内,当线圈通入交变电流后,立即产生交变磁场,在工件内形成“涡流”,表层迅速被加热到淬火温度时而心部仍接近室温,在立即喷水冷却后,就达到表面淬火的目的。
火焰加热表面淬火是以高温火焰为热源的一种表面淬火法。
将工件快速加热到淬火温度,在随后喷水冷却后,获得所需的表层硬度和淬硬层硬度。
感应加热表面淬火与火焰加热淬火相比较有如下特点:
1)感应加热速度极快,只要几秒到几十秒的时间就可以把工件加热至淬火温度,:
而且淬火加热温度高(AC3以上80~150℃)。
2)因加热时间短,奥氏体晶粒细小而均匀,淬火后可在表面层获得极细马氏体,使工件表面层较一般淬火硬度高2~3HRC,且脆性较低。
3)感应加热表面淬火后,淬硬层中存在很大残余压应力,有效地提高了工件的疲劳强,且变形小,不易氧化与脱碳。
4)生产率高,便于机械化、自动化,适宜于大批量生产。
但感应加热设备比火焰加热淬火费用较贵,维修调整比较困难,形状复杂的线圈不易制造
表面淬火前应采用退火或正火预先热处理。
23化学热处理包括哪几个基本过程?
常用的化学热处理方法有哪几种?
化学热处理是把钢制工件放置于某种介质中,通过加热和保温,使化学介质中某些元素渗入到工件表层,从而改变表层的化学成分,使心部与表层具有不同的组织与机械性能。
化学热处理的过程:
1分解:
化学介质要首先分解出具有活性的原子;
2吸收:
工件表面吸收活性原子而形成固溶体或化合物;
3扩散:
被工件吸收的活性原子,从表面想内扩散形成一定厚度的扩散层。
常用的化学热处理方法有:
渗碳、氮化、碳氮共渗、氮碳共渗。
24试述一般渗碳件的工艺路线,并说明其技术条件的标注方法。
一般渗碳件的工艺路线为:
下料→锻造→正火→切削加工→渡铜(不渗碳部位)→渗碳→淬火→低温回火→喷丸→精磨→成品
25氮化的主要目的是什么?
说明氮化的主要特点及应用范围。
在一定温度(一般在AC1以下)使活性氮原子渗入工件表面的化学热处理工艺称为渗氮。
其目的是提高工件表面硬度、耐磨性、耐蚀性及疲劳强度。
氮化的主要特点为:
1)工件经渗氮后表面形成一层极硬的合金氮化物(如CrN、MoN、AIN等),渗氮层的硬度一般可达950~1200HV(相当于68-72HRC),且渗氮层具有高的红硬性(即在600~650℃仍有较高硬度)。
2)工件经渗氮后渗氮层体积增大,造成表面压应力,使疲劳强度显着提高。
3)渗氮层的致密性和化学稳定性均很高,因此渗氮工件具有高的耐蚀性。
4)渗温度低,渗氮后又不再进行热处理,所以工件变形小,一般只需精磨或研磨、抛光即可。
渗氮主要用于要求耐磨性和精密度很高的各种高速传动的精密齿轮、高精度机床主轴(如锺轴、磨床主轴)、分配式液压泵转子,交变载荷作用下要求疲劳强度高的零件(高速柴油机曲轴),以及要求变形小和具有一定耐热、抗蚀能力的耐磨零件(阀门)等。
26试说明表面淬火、渗碳、氮化热处理工艺在用钢、性能、应用范围等方面的差别。
表面淬火一般适用于中碳钢(0.4~0.5%C)和中碳低合金钢(40Cr、40MnB等),也可用于高碳工具钢,低合金工具钢(如T8、9Mn2V、GCr15等)。
以及球墨铸铁等。
它是利用快速加热使钢件表面奥氏体化,而中心尚处于较低温度即迅速予以冷却,表层被淬硬为马氏体,而中心仍保持原来的退火、正火或调质状态的组织。
应用范围:
(1)高频感应加热表面淬火应用于中小模数齿轮、小型轴的表面淬火。
(2)中频感应加热表面淬火主要用于承受较大载荷和磨损的零件,例如大模数齿轮、尺寸较大的曲轴和凸轮轴等。
(3)工频感应加热表面淬火工频感应加热主要用于大直径钢材穿透加热和要求淬硬深度深的大直径零件,例如火车车轮、轧辘等的表面淬火。
渗碳钢都是含0.15~0.25%的低碳钢和低碳合金钢,如20、20Cr、20CrMnTi、20SiMnVB等。
渗碳层深度一般都在0.5~2.5mm。
钢渗碳后表面层的碳量可达到0.8~1.1%C范围。
渗碳件渗碳后缓冷到室温的组织接近于铁碳相图所反映的平衡组织,从表层到心部依次是过共析组织,共析组织,亚共析过渡层,心部原始组织。
渗碳主要用于表面受严重磨损,并在较大的冲载荷下工作的零件(受较大接触应力)如齿轮、轴类、套角等。
氮化用钢通常是含Al、Cr、Mo等合金元素的钢,如38CrMoAlA是一种比较典型的氮化钢,此外还有35CrMo、18CrNiW等也经常作为氮化钢。
与渗碳相比、氮