国内外线材生产的兴起与发展.docx
《国内外线材生产的兴起与发展.docx》由会员分享,可在线阅读,更多相关《国内外线材生产的兴起与发展.docx(12页珍藏版)》请在冰豆网上搜索。
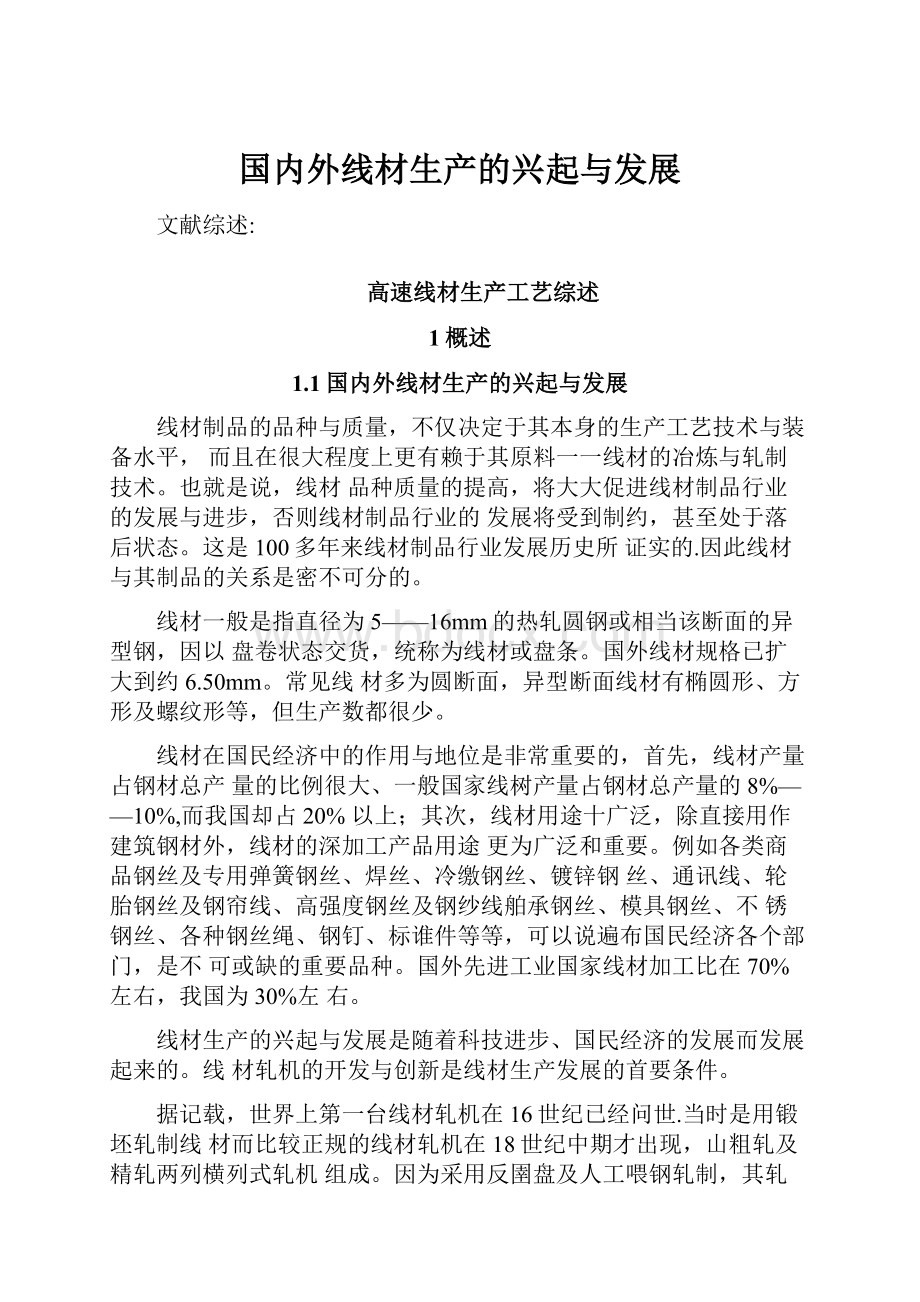
国内外线材生产的兴起与发展
文献综述:
高速线材生产工艺综述
1概述
1.1国内外线材生产的兴起与发展
线材制品的品种与质量,不仅决定于其本身的生产工艺技术与装备水平,而且在很大程度上更有赖于其原料一一线材的冶炼与轧制技术。
也就是说,线材品种质量的提高,将大大促进线材制品行业的发展与进步,否则线材制品行业的发展将受到制约,甚至处于落后状态。
这是100多年来线材制品行业发展历史所证实的.因此线材与其制品的关系是密不可分的。
线材一般是指直径为5——16mm的热轧圆钢或相当该断面的异型钢,因以盘卷状态交货,统称为线材或盘条。
国外线材规格已扩大到约6.50mm。
常见线材多为圆断面,异型断面线材有椭圆形、方形及螺纹形等,但生产数都很少。
线材在国民经济中的作用与地位是非常重要的,首先,线材产量占钢材总产量的比例很大、一般国家线树产量占钢材总产量的8%——10%,而我国却占20%以上;其次,线材用途十广泛,除直接用作建筑钢材外,线材的深加工产品用途更为广泛和重要。
例如各类商品钢丝及专用弹簧钢丝、焊丝、冷缴钢丝、镀锌钢丝、通讯线、轮胎钢丝及钢帘线、高强度钢丝及钢纱线舶承钢丝、模具钢丝、不锈钢丝、各种钢丝绳、钢钉、标谁件等等,可以说遍布国民经济各个部门,是不可或缺的重要品种。
国外先进工业国家线材加工比在70%左右,我国为30%左右。
线材生产的兴起与发展是随着科技进步、国民经济的发展而发展起来的。
线材轧机的开发与创新是线材生产发展的首要条件。
据记载,世界上第一台线材轧机在16世纪已经问世.当时是用锻坯轧制线材而比较正规的线材轧机在18世纪中期才出现,山粗轧及精轧两列横列式轧机组成。
因为采用反圉盘及人工喂钢轧制,其轧速度超过8m/s,同时受头尾温差大的影响,线材存在着尺寸精度差、盘重小、性能不稳定等致命缺点,限制了横列式轧机的发展。
为了保证产品质量并提高产量,同时也为了降低生产成本,必须提高轧制速度,所以20世纪初开发了半连续式轧机。
该轧机山粗、中、精轧机组组成,粗轧及中轧采用连轧,精轧机组仍采用横列式轧机,即活套轧制:
复二重轧机是半连续式轧机的一个特例,中轧及桔轧机列在两个正圉盘之间采用连轧,实现了机械化操作,轧制速度提高到16in/s,生产能力有很大提高,盘重增加到200kg左右,尺寸精度较横列式为好,但品种及质量未有根本好转。
20世纪60年代是线材生产技术发展的兴盛与创新时期,在轧制速度不断提高的同时也解决丁大盘重线材的控制冷却问题,因此从根本上解决了盘重增大后,内层的线村长时间在高温下停留生成粗大的晶粒,使内外线材的力学性能差别很大,表面氧化铁皮厚等问题。
为了进一步解决产品品种及质量问题,英国在1862年建成了第一台连续式轧机。
该轧机机座采用串列式布置形式,轧件同时在儿个机架中轧制,各道次的金属秒流量相等。
可单机驱动,有较高的调整精度,实现微张力或无张力轧制:
山于没有穿唆轧制,没有大活套,所以头尾温差小,产品性能得到改善。
到20世纪50年代,随着机械制造、电气传动及控制水平的提高,线材轧制速度达36m/s,尺寸公差(0.3—0.4)mm,盘重为500kg左右,一套轧机年广量在30—50万吨。
当时典型的连续式线材轧机是两线8架集体传动的美国摩根型轧。
U前世界上应用最广泛的摩根型高速无扭轧机是美国摩根公司1962年开始研制的,1966年首先应用于加拿大钢铁公司哈密尔顿厂。
第一套摩根型高速线材轧机于1966年9月正式投产,轧制速度43一50m/s,同时摩根公司和加拿大斯太尔摩公司联合,开发了线材轧后控制冷却系统,称之为斯太尔摩线。
高速线材轧机一出现就显示出极大的优越性,继美国之后,其他一些国家和公司也纷纷创新高速线材轧机,出现了各种机型。
目前基本上有四种1)测交45的美国摩根型;2)15/75的德国德马克型;3)顶交45的英国阿希洛型;4)0/9平一立布置的意大利达涅利肋型。
其中摩根机型应用最广泛。
各种机型各有优点,但基本工艺特点差异不大。
1.2高速线材生产特点
高速线材轧机一出现就显示出极大的优越性,高速、无扭、控冷是现代高速线材轧机主要的工艺特点:
(1)高速,普通线材轧机轧制速度很少超过35m/s,我国广泛应用的复二重轧机。
其轧制速度为16m/s左右,而LI前使用的高速线材轧机的实际轧制速度一般为75m/s,最高轧制速度可达120m/s。
(2)无扭,摩根无扭轧机机组一般由10个机架组成,使用碳化餌辗环,轧轮为悬臂式,相邻机架的轧轨互成90度,这样就避免了轧件进入下一道时的扭转翻钢,实现了无扭轧制。
(3)控冷,由于轧制速度高,盘重大(一般为1.2t),已不可能采取普通轧机的集卷冷却方式。
线材从精轧机轧出后,首先进行芽水冷却,快冷至要求的温度范围,然后通过成圈器使线团散布在运输轮道上,进行散卷冷却。
一股采用风冷,水冷及散卷冷却,具体工艺根据不同钢种的要求确定,从而得到全长冷却均匀和性能良好的线材。
这种斯太尔摩冷却工艺生产线,后来乂发展成为标准型、缓冷型、延迟型三种,根据不同钢种性能的要求,采用不同类型的冷却方式。
控制冷却丄艺主要是控制终轧温度、吐丝温度、相变区冷却速度(通过调节运输机速度、风量大小及保温时间来控制)和集卷温度等。
三种斯太尔摩冷却法的主要匸艺参数见表2—1o
2.1国内外线材生产的兴起与发展!
3
*2-1斯太尔冷却法主要工艺参数
冷却类堂
玲却速度/(X/3)
0.25-40
4-10
延迟型
0.05-1.40
1~!
0
缓冷瑕
0.05-1.40
0.25-10
随着科学技术的进步,对炼钢的生产率、成本、产品内在质量等都提出了愈来愈高的要求。
20世纪60年代、在世界范圉内,传统的炼钢方法发生了根本性的创新,即山原来单一设备初炼及精炼的一步炼钢法,变成山传统炼钢设备初炼然后再进行炉外精炼的二步炼钢法.从而出现了各种各样的炉外精炼法。
炉外精炼是近年来发展起来的一项炼钢新技术,无论转炉、电炉都可采用各种各样的炉外精炼方法。
国外经炉外精炼的普通钢已占其总量的70%以上,特殊钢儿乎100%经过炉外精炼。
炉外精练这种新技术得到迅猛发展的原因是:
(1)提高韧烁炉生产率。
电弧炉生产率提高25%左右,可提高超高功率电炉生产率50%—10%o
(2)降低产品成本。
对于精炼超低碳不锈钢,可降低成本500-10007L/吨:
(3)提高产品内在质量、扩大产品品种。
当钢中氢含量低于某含量时可以避免白点的形成:
钢的纯治度大大提高、同时钢的化学成分均匀稳定,偏析减轻;钢的综合力学性能得到显著提高,品种也得到扩大,从而满足了用户的要求。
1.3国内外线材生产的现状与展望
1,3.1国外线材生产现状
20世纪70年代以来,国外主要产钢国家普遍采用高速线材轧机和控制冷却技术作为线材生产的主要工艺技术;在冶炼方面.主要是用转炉或电炉初炼,然后采用炉外精炼技术进行二次精炼,同时基本上是以连传代替模铸,而且釆用全保护浇铸;所以.生产出的线材生产率高、成本低、品种多、质量乂好。
据不完全统计,目前世界上有近3万条高速线材轧机。
年产线材约7000万吨、其中高线产量约80%以上,线材产量占钢材总产量9%-10%;各国的输出量与输入量平均在20%左右。
美国是世界上最大的线材输入国,每年线材消费员约800万吨,而本国每年只牛产400—450万吨,输入量占30%—50%,日本是世界上线材输出量最大的国家.每年线材产量约750万吨,输出量约20万吨;世界上线材产量最大的国家是中国,19四年线材实际产量为260B万吨。
H前我国拥有线材轧机近110套,其中复二重轧约占一半,横列式线材轧机有近30套(将逐步被淘汰);其余40多套多为高速线材轧机,其中从国外引进的高水平线材轧机有20多台.国产高速线材轧机有近20套。
1999年,全国生产线材2608万吨,其中高线产量1218万吨,高线比已经达到46.7%:
优质硕线比约10%,但精练比不到30%o
从品种与质量来看,我国对国际标准ISO、欧洲标D2TN、日本标准J15中所列线材钢种、规格等基本可以全部生产,而且能达到相应的标准要求。
国产线材除个别品种外(如钢帘线、气门弹簧、超低碳不锈钢用线材等),基本都能满足用户要求,供需基本平衡,自给率达93%
1.3.3对我国线材发展的几点看法
纵观我国线材发展的历史,可以说有了突飞猛进的发展.特别是近儿十年来,我国线材行业持续高速发展,以每年净增产200多万吨高速度增长,其产量从1987年的693万吨,增加列]999年的2608万吨。
增长2.8倍;同期高速线材产量从32万吨增加到1218万吨,增长37倍;线材自给率达到99%以上;在品种质量方面也有很大提高,LI前完全可以按国际先进技术指标进行生产。
多数线品种与质量能够满足线材制品企业使用要求。
所有这些都说明:
我国已经成为世界最大的线材生产国,为世界同行所嘱LI。
但是也应看到,我国虽然是世界线材生产大国,但还不能说是线材主产强国;LI前我国还有部分线材品种仍然依靠进口维持生产。
如钢帘线、高应力弹簧钢、不锈钢、冷墩钢等线材。
在重要用途线材实物质量方面,与世界先进工业国家仍有较大差距,为此,对我国线材发展提出以下儿点看法。
(1)今后线材生产的重点任务是提高品种质量而不是追求产量、特别是要提高重要用途线材品种实物质量。
(2)应该进一步发展高速线材轧机,国外先进工业国家高线比已超过80%应该淘汰落后的横列式线材轧机,改造并限制复二重线材轧机的发展,重点发展国产高速线材轧机。
(3)扩大线材出口是今后发展方向之一,我国是世界线材产量最大的国家,但是出口却很少,每年只有儿十万吨,同时还有儿十万吨需要进口。
这种现象应该得到改变・。
2高速线材生产工艺
线材生产由5个基本工序织成即:
坯料、加热、轧制、冷却、精整。
2.1坯料
坯料的清理、检查一般在供坯车间进行,提供给线材车间的原料应该是合格钢坯。
但仍要对坯料进行检查,剔除不合格坯料。
为了生产特殊钢线材,有些厂在钢坯进入炉前设置“抛九一超声波探伤一磁场探伤一修磨”工艺生产线。
一般情况下不应设置修磨线。
对钢还进行称重测长。
称重是轧机生产技术经济统讣的需要;测长是为了防止在装步进式加热炉时跑偏对中系统提供控制信号;称重测长乂是物流跟踪系统所必须输人的数据。
2.2加热
这是热轧工艺的必需工序,除非是连铸坯直接轧制。
目前,由于轧制设备能力的加强,轧件在粗轧机组及中轧机组时降温小,在精轧机组还升温,一般采用低温轧制。
因此,加热温度可适当降低,既节省了加热能耗,乂减少钢坯表面的氧化铁皮生成和脱碳层深度。
除特殊钢外一般台金钢和普通碳家钢根据钢种不同,一般开轧温度在900-1050度。
除加热温度外,保证加热均匀也是加热工序的重要任务。
目前主要采用步进式加热炉。
2.3轧制
在钢坯进入轧机前,为了得到好的线材表面质量,需去除加热时生成的氧化铁皮,在轧机前设置大流量、快速高压水除鳞装置,进行高压水除鳞。
生产普通碳家结构钢时可以不要高压水除鳞。
采用无头轧制工艺时,在除鳞之后进入轧机前,将钢坯的尾部与下一根钢坯的头部焊接在一起,在轧制时就保轧制一根无限长的钢坯,可以提高生产率,降低成本,使整个轧制过程平稳、顺利,并便于实现整个轧线的自动控制。
2.3.1粗轧
粗轧的主要作用是使坯料得到初步的圧缩和延伸,得到温度合适、断面形状正确、尺寸合格、表面良好、端头规矩、长度适合工艺要求的轧件。
粗轧一般釆用微张力或低张力轧制,因为此时轧件断面尺寸较大,对张力不敬感,设置活套实现无张力轧制十分困难也极不经济。
为保证成品尺寸的高精度,为保证生产工艺的稳定和避免粗轧后工序的轧制事故,通常要求粗轧轧出的轧件尺寸偏差不大于土1mm。
2.3.2中轧
中轧及预精轧的作用是继续缩减轧件的断面尺寸、为精轧机组提供轧制成品线材所需要的断面形状正确、尺寸精确并匕沿全长断面尺寸均匀、无内在和表面缺陷的小断面料。
中轧机组前面道次(一般指前4道),山于断面尺寸较大,一船采用微张力轧制.对尺寸影响不大。
中轧机组的后儿道(一般为两道)及预精轧一般不能采用微张力轧制。
如采用微张力轧制则精度达不到要求。
因此,在预精轧机前及预精轧机组轧机间设置圉盘,实现无张力轧制。
同样,为了保证成品尺寸的高精度,为保证生产工艺的稳定和避免精轧工序的轧制事故,一般要求预精轧机来料的轧件断面尺寸偏差不大于土0.33mm,而中轧机轧组的相应轧件断面尺寸偏差不大于0.5mmo
2.3.3精轧
精轧机组采用高速无扭机组。
任何形式的拓速线材轧机精轧机组的生产工艺都是采用固定的道次和轧钢转速比,以单线微张力无扭转高速连续轧制的方式进行轧制。
高速线材轧机相轧机组中,保持成品及来料的金属秒流星差不大于1%是工艺设计的一个基本出发点,以保证成品尺寸偏差不大于O.lmmo
2.4冷却
冷却在线材生产中尤其是在高速线材生产中很重要,因为在高速轧制条件下轧件不但不降温还升温。
在高速线材轧机中(粗轧机组),如出口速度为140m/s,则人口速度约为14m/s。
14一16m/s仍属于低速范圉,但轧制速度达到10ni/s时温度不再下降,超过10m/s后温度上升。
高速线材轧机多道次逐次升温给个产工艺带来极大影响,因此必须降低精轧机的轧制温度。
同时为了控制各段的轧制温度,尤其是轧制合金钢时,其至在预精轧机前设置水冷。
因此水冷装置分布在预精轧前、精轧、精轧机架间、精轧机组与减径机之间及定径机后,预精轧前较少安装。
有了这些冷却装置可以进行低温轧制、控制轧制和拧制冷却。
2.5精整
精整主要内线材的集卷、修整、检查、取样、运输、把捆、称重、卸卷及入库等工序组成。
集卷包括集卷与挂卷。
除少数儿种冷却]艺采用集卷过程中或集卷后冷却外,大部分线材控制冷却丁艺是先散卷冷却,然后将散卷收集成竖立的盘卷,并通过翻转机构挂到c形钩上,山运输轨道进行输送。
盘卷的修整主要是对它的头、尾进行修整。
其要求是:
盘卷两端缺陷部分(包括末水冷部分)要切净,一般大规格线材头尾各剪去1——2mm,小规格线村头尾备剪去3——5mm;盘卷的内外直径,特别是内圈应规整,否则影响打捆:
盘卷端部的线圈不得零乱或脱挂;一盘线卷应是一根完整的线材,不得剪成多头。
线材的成品检查包括线材外观质量检查和组织性能检验。
取样需在线材修整完毕后进行,一般按批随机抽取。
盘卷运输是线材精整工序中的重要环节,在运轴线上盘卷将完成修整、检查、取样、打捆、称重、挂牌及卸卷等一系列操作工序。
3孔型设计
孔型是由上下两个或两个以上轧轨的轧槽,在轧制面上所组成的儿何图形。
孔型通常由幅缝、圆角、侧壁斜度、锁口(闭口TL)、轨环等组成。
孔型的尺寸为正在过钢时的尺寸。
孔型设计是指将坯料在轧規孔型中经过若干道次的轧制变形,获得所需要的断面形状、尺寸和性能的产品,所进行的对变形过程的设汁和计算工作。
3.1孔型设计的基本内容
孔型设计包括以下三国方面的内容:
(1)断面孔型设汁。
根据原料和对成品断面形状、尺寸及性能的要求,确定变形方式,计算轧制道次。
各道次的变形量及孔型形状和尺寸。
(2)轧车昆孔型设计,确定孔型在各机架上的分布及其在轧探上的配置方式,以保证轧制顺畅、操作方便、产品质量奸、轧机产量高为标准,此步骤亦称孔型配置或配翟。
(3)轧辗辅件设计,即导卫或诱导装置的设计。
要保证轧件能按照所要求的状态稳定地进、出孔型,或使轧件在孔型之外发生一定的变形,或对轧件产半矫正翻转作用。
3.2孔型系统的选择
合理地选择粗、中轧机组的孔型系统,对轧机的生产率、产品质量、各项消耗指标以及生产工艺操作都有决定性的影响,必须照具体生产条件选择合适的孔型系统,
3.2.1选择孔型系统的依据
(1)来料的条件:
是连铸坯还是轧制坯,断面的形状、尺才及波动范围,内在及表面质量,钢种等;
(2)设备条件:
轧机布置方式,机架结构形式,机组组成、数量及参数,传动方式,电机能力及调速范围,辅助设备的配置和能力等;
(3)产品条件:
产品品种、规格范围、尺寸精度及线材的性能要求等,
(4)生产正艺操作条件:
是多线轧制还是单线轧制,孔型共用要求,操作人员的操作习惯和技术水平等。
3.2.2粗中轧孔型系统的选择
高速线材轧机粗、中轧机织的轧制工艺采用单线轧制或多线轧制,除中轧机组末一两架外,其他各架的孔型对所有产品都是共用的。
高速线材轧机粗、中轧机组所采用孔型系统,从发展上看.20世纪80年代以前主要选用箱一一椭圆一一方孔型系统,90年代后期开始始采用箱一一椭圆——圆孔型系统。
由于轧机的组成、结构不同,粗、中轧机组的孔型系统也不同。
由奇数道次组成的粗、中轧机组的延伸孔型系统,以选择箱(变态箱)一一椭圆(双弧椭圆)一圆椭圆圆的组合孔型系统最理想,也可选用箱一椭圆一—方一一椭圆一一圆的组合孔型系统。
山偶数道次组成的粗、中轧机组的延伸孔型系统,以选择椭圆一一圆一一椭圆一一圆的组合孔型系统较为理想,也可选用箱一一箱椭圆一一方一一椭圆一一圆的组合孔型系统。
在组合孔型系统上,粗轧机组第一、二、三孔也有所不同,基本有三种情况:
(1)粗轧机组山奇数机架组成,第一、二孔不翻钢连续平压轧制,以下按圆(方)——椭圆——厕(方)轧制。
(2)粗轧机组由平一一立轧偶数机架组成,采用箱一一方一一椭圆一圆(方)系统,没有不翻钢的连续两道次平压轧制;
(3)粗轧机组采用单线紧凑式大压下轧机,其孔型釆用浅槽箱一一箱或箱一—平孔型系统,租、中轧延伸孔型系统应选择箱(平)一一箱(平)一一六角一一方——椭圆一一圆的组合孔型系统
3.3精轧机组孔型系统选择
现代高速线材轧机的预精轧、精轧机组多釆用椭圆一一圆孔型系统。
这一孔型系统的主要优点有:
⑴适合于相邻机架轧轨轴线与地平线呈45度/45度、75度/15度90度/90度相互垂直布置.
(2)变形平稳\内应力小\可得到尺寸精确、表面光滑的轧件.
(3)椭圆一一圆孔型系统可借助调整探缝值得到不同断面尺寸的轧件,增加了孔型样板、孔型加工的刀具和磨具、轧辗辗片和导卫装置的共用性,减少了备件,简化了管理;
(4)这一孔型系统的每一个圆孔型都可以设计•成既是延伸孔型乂是成品孔型,适合于用一组孔型系统轧辗,借助甩去机架轧制多种规格产品。
3.3延伸系数的分配
3.3.1粗、中轧延伸量的分配
在粗轧阶段.除应注意前两三道次钢坯表面氧化铁皮厚、摩擦系数小和咬入困难外,还应充分利用金属在高温阶段塑性好、变形抗力小的特点和这一阶段对轧件尺寸精度要求不甚严格的条件,通常采用较大的延伸系数;在中轧阶段,既要继续利用金属在此较高温度下变形抗力小和塑性较好的特点,乂要保持轧件尺寸稳定,以便保证中、精轧工艺稳定,通常采用中等的延伸系数。
粗轧机组一般为1.3——1.45、紧凑式轧机为1.4——1.7;中轧机组为1.25——1.381、中轧机组或预精轧机组为1.2——1.31。
当初步确定了各机组的平均延伸系数后,即可确定各机组的轧制道次。
具体确定各轧制道次的延伸系数是个复杂问题。
因为影响确定各轧制道次延伸系数的因素较多,这些因素主要是:
孔型的形状、尺寸;咬入条件;轧轨强度;传动能力与传动方式;孔型共用与轧辗磨损均衡要求:
连续轧制过程各道次的连轧常数关系。
在不同情况下,这些因素对每道次延仲系数的影响作用是类似的。
因此需按照具体情况,根据主要影响因素初步确定每道次延伸系数,在大致确定了孔型尺寸之后,再用其他因素进行校核,调整、修正。
在实践中往往是参照类似的生产条件,按现实生产中的数据确定每道次的延伸系数。
各延伸孔型系统平均延伸系数的经验数据是:
箱形孔型系统的平均延伸系数为:
1・2——1.33,变态箱形的可达1.45。
菱一方ZL型系统的平均延伸系数为:
1.2——1.4。
椭圆一方孔型系统的平均延伸系数为:
1.35——1.55o
六角一方7L型系统的平均延伸系数为:
1.40——1.60o
椭圆一圆孔型系统的1平均延伸系数为:
1.25——1.40。
3.3.2精轧孔型延伸系数分配
精轧机组一般由8——10个机架组成,多数为10个机架。
精轧机组的平均延伸系数为1.215——1.255o从中轧机组或顶精轧机组来的轧件一般为4.6——21.5mm当轧制合金钢或采用8机架的粗轧机组时,来料直径相应减小2——4mmo
精轧机组各架延伸系数的分配,除第一架外,大体上是均匀的。
轧件由中轧机组或预精轧机组进精轧机组,固设有活套装置是在无张力状态下轧制,轧制速度较低咬入条件好,延伸系数的大小不受传动条件的限制,为满足多种规格产品的供料要求在精轧机组第一道次椭圆孔型内的延伸系数波动范圉比较大、一般为1.15——1.31o
其他道次的延伸系数,在椭圆孔型和圆孔型中也有所不同。
在椭圆孔型中的
延伸系数为1・23——1.29,—般都赂高于粗轧机组的平均延伸系数。
在同一机组不同道次的椭圆孔型中延伸系数的波动值为0.015——0.03。
在同一架次轧制不同产品时延伸系数的波动值为0.012——0.019o
参考文献
[1]康永林,《轧制工程学》,冶金工业岀版社
[2]王廷溥、齐克敏等,《金属塑性加工力学》,冶金工业岀版社
[3]邹家祥等,《轧钢机械(3)》,冶金工业岀版社
[4]曾光廷等,《材料成型加工工艺及设备》,化学工业出版社
[5]胡城立、朱敏,《材料成型基础》,武汉理工大学岀版社
[6]严绍华等,《材料成形工艺基础(金属工艺学热加工部分)》,淸华大学出版社
[7]黄天佑等,《材料加工工艺》,清华大学岀版社
[8]李登超等,《参数检测与自动控制》,冶金工业岀版社
[9]李登超等,《板带钢生产》,兵器工业岀版社
[10]李登超,《不锈钢板带材生产理论与实践》
[11]髙锦张等,《塑性成形工艺与模具设计》,机械工业出版社