大跨度网壳安装Word文件下载.docx
《大跨度网壳安装Word文件下载.docx》由会员分享,可在线阅读,更多相关《大跨度网壳安装Word文件下载.docx(20页珍藏版)》请在冰豆网上搜索。
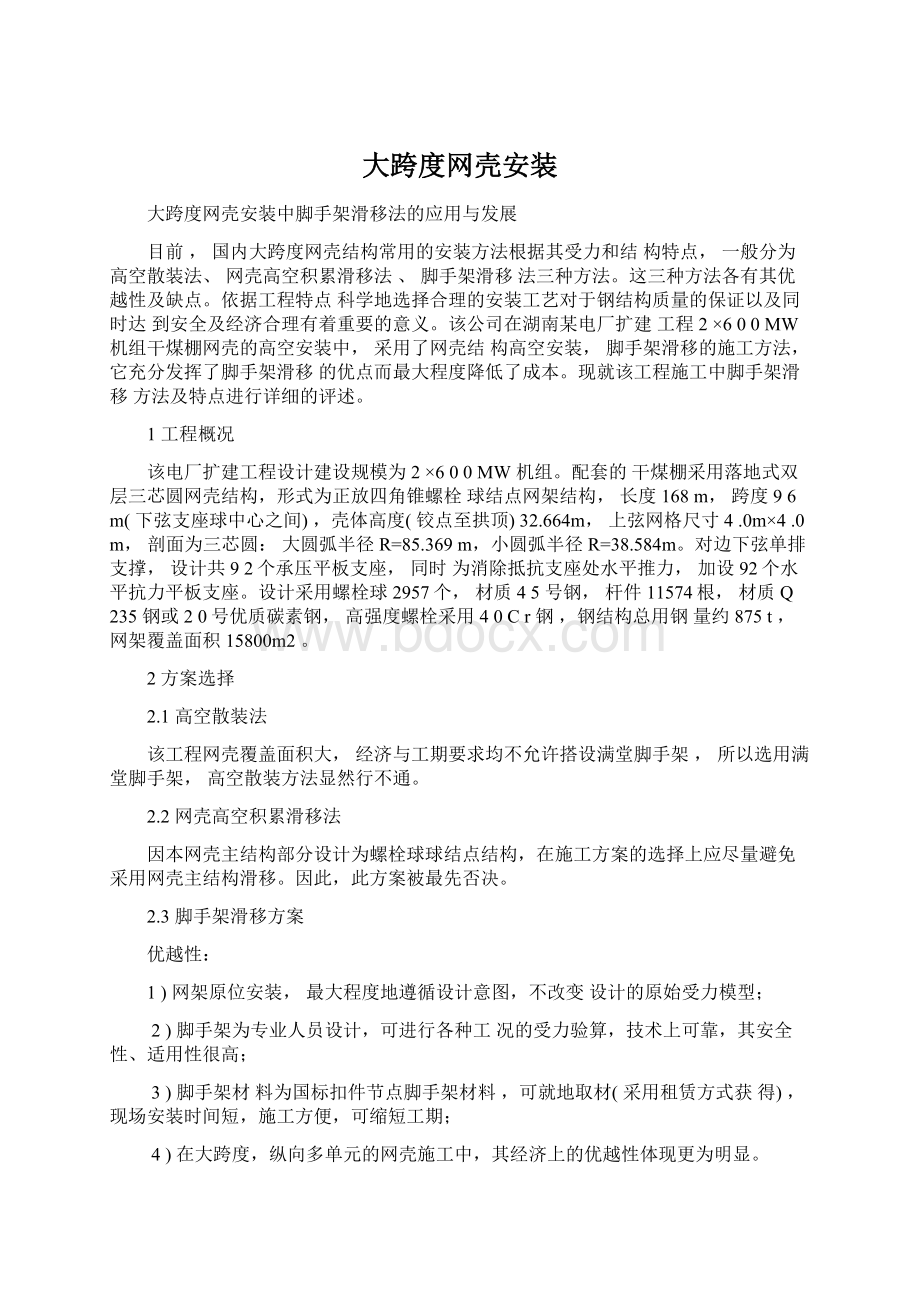
优越性:
1)网架原位安装,最大程度地遵循设计意图,不改变设计的原始受力模型;
2)脚手架为专业人员设计,可进行各种工况的受力验算,技术上可靠,其安全性、适用性很高;
3)脚手架材料为国标扣件节点脚手架材料,可就地取材(采用租赁方式获得),现场安装时间短,施工方便,可缩短工期;
4)在大跨度,纵向多单元的网壳施工中,其经济上的优越性体现更为明显。
3施工方案
该工程施工方法采用脚手架高空,网架高空安装的施工方法。
工程主体网壳分15个安装单元,每个安装单元的完成均在脚手架操作平台上完成,一个拼装单元完成后,脚手架滑移至预定位置进行下一个安装单元,脚手架滑移14次,最后一个单元补空完成,不再滑移。
网壳构件材料垂直运输使用一台25t汽车吊(主要考虑移动方便)来完成,其吊臂接长37m。
4脚手架滑移方案的应用特点
4.1脚手架设计特点
该脚手架经专业设计人员设计及分析计算,采用普通扣件管件材料。
脚手架跨度为86m,宽度12m(沿网架纵方向),最高处29.50m,顶部根据网架结构特点呈圆弧形;
下底部根据脚手架滑移要求共设置12条滑移轨道,整体脚手架自重约220t,脚手架设计承载力270kg/㎡。
该脚手架设计主要特点:
整个脚手架重量落在6个支架承台(平均间距17m)上,每个支架承台承重面积为3.0m×
12m,用[300型槽钢焊接为格构式,具有良好的强度与刚度;
每个支架承台下部焊接连接8个滚轮,每侧4个;
滑移轨道选用16号非对称工字钢(轨道专用工字钢),每根长度12m,滚轮两侧设置挡板,同滑移轨道之间为滚动摩擦。
脚手架在搭设过程中,按照设计要求,滑移轨道之间部分脚手架留置适当高度及宽度的三角形门洞,极大地减轻脚手架自重;
在脚手架同承台连接部位采用焊接连接,为保证脚手架整体稳定性,在纵横向加设斜支撑,纵向斜支撑间距1.2m,横向斜支撑间距1.5m。
为保证脚手架滑移同步性及减小摩擦力,脚手架在中间部位分隔为左右两部分,中间设置50cm宽间距,在网架结构安装过程中,左右两部分临时连接;
在脚手架滑移时,保证两部分完全独立。
脚手架立面图见图1。
图1脚手架立面图
4.2脚手架应用的先进性。
1)本工程中网壳跨度96m(下弦支座球心距离),脚手架跨度达到85.5m,为降低脚手架造价,采用支架承台支撑,中间留置门洞,实际节约架管材料70t~80t,节省费用约8万元。
2)脚手架在中间部位分隔为左右两部分,可最大限度保证脚手架滑移过程中各支架承台同步性,避免脚手架在纵向产生扭曲。
同时,脚手架左右两侧部分可以先后独立滑移,可分别计算其滑移摩阻力。
滚动净摩擦系数取0.10,滚轮与钢轨之间可取0.5mm,滚轮的外圆半径rl=150mm,滚轴的半径r2=40mm,则单侧最大摩阻力为:
Ft=(k/rl+'
μ2.r/r1)·
Gok
=(0.5/150+0.10×
40/150)×
110=3.30t。
在单侧脚手架滑移过程中实际选用3副5t手动倒链,可轻松牵引滑移。
3)选用的5t手动倒链为同一规格型号,滑移控制速度50mm/min,滑移作业过程协调一致,统一指挥,滑移的不同步严格控制在20mm以内,平稳滑移,滑移的安全性大大提高。
4)该脚手架滑移方案最大限度的利用了原有的施工场地的优越条件,根据建设单位场地堆煤的要求,施工场地按照设计要求全部推平碾压后,浇筑150mm素混凝土地面,更利于脚手架的滑移。
5)脚手架门洞的留置,在施工期间建设单位可以继续安装斗轮机及其辅助设施。
这一点对建设单位的同步施工,有着积极的意义。
5工程效果
采用该脚手架滑移方案,仅用78d就完成了800多吨钢结构安装工作,取得了圆满成功。
同时,最大限度节约了成本及满足了建设单位的总施工进度协调要求,为以后的类似工程提供了宝贵经验。
国内首次采用大跨柱面网壳“机构→结构”整体提升
施工方法取得圆满成功
河南省鸭河口电厂干煤棚跨度108米,采用三心圆柱面双层网壳的结构形式,是目前亚洲跨度最大的柱面网壳。
该工程在施工中采用“机构→结构”整体提升方法,提升工作于2001年5月31日一天内完成。
全国空间结构学术委员会和全国升板建筑和提升技术学术委员会的14位国内著名专家现场指导考察。
现场召开了柱面网壳“机构→结构”整体提升施工方法的研讨会,与会专家对该种施工方法的技术先进性和经济性给予了充分的肯定。
柱面网壳“机构→结构”整体提升施工方法的基本思想是将网壳去掉部分杆件,使一个静定结构变成一个可以运动的机构,这样就可以将柱面网壳在地面折叠起来,最大限度的降低安装高度;
然后将折叠的网壳提升到设计高度;
最后补缺未安装的构件,机构又变成静定的结构。
所以,整个施工过程是机构→结构的变化过程。
由图1可以看出,提升过程是一个机构运动的过程,这是此方法与一般网架提升法的本质区别。
柱面网壳“机构→结构”整体提升施工方法的优点是大部分构件的安装工作都在贴近地面处完成,可以保证安装质量,加快安装速度,保障施工人员安全,并且节省大量脚手架。
鸭河口电厂干煤棚网壳整体提升的施工技术在国内尚属首次采用,并取得了圆满成功,为该项技术应用于大跨度结构的施工积累了宝贵的经验。
本工程由浙江大学空间结构研究中心设计并提出施工方法,浙江东南网架集团公司承接施工。
图1
柱面网壳“机构→结构”整体提升施工过程示意图
大跨度柱面网架折叠展开提升技术
1、工程概况和技术原理
河南南阳鸭河口电厂原有露天的煤炭堆场,场内有斗轮机和输煤栈道。
近年来因雨水增多,为防雨水冲淋煤炭需要在煤场上建造一个干煤棚。
干煤棚的结构形式为钢结构的柱面网架,纵向90m、跨向108m、高38.8m、重505t,是国内最大跨度的干煤棚。
干煤棚网架的安装采用地面折叠拼装、整体提升展开的新工艺。
其技术原理:
拼装时抽掉一些杆件后将网架结构分成5块,块与块之间以及网架根部基础采取铰连接,使结构成为一个折叠式可在地面拼装的可变机构。
网架的大部分杆件、设备安装以及部分装修工作在地面完成,然后采用钢铰线承重、计算机控制、液压千斤顶集群整体提升等先进工艺,将该机构展开提升到预定高度后装上补缺杆件,使之形成一个稳定、完整的网架结构。
2、施工难题和控制要求
1)网架是可变机构
网架在地面拼装后是一个折叠的可变机构,展开提升过程中水平方向很容易失稳,因此必须采取技术措施使之转化为一个稳定结构,才能进行展开提升。
2)提升负载呈动态变化
以往网架是完全悬空提升的,其质量全部由提升千斤顶承受,只要提升时控制好同步,提升力相对来说是一个常数。
而这次提升时网架根部始终与基础铰接,其质量由提升千斤顶与基础共同承受,在提升过程中千斤顶的提升负载随着提升高度的变化而变化,负载动态均衡的控制难度很大。
3)内应力控制是一个关键难题
网架提升时共有6个铰轴,各铰轴之间必须相互平行,每一铰轴上的铰必须多铰同轴(同轴度误差应<3mm),否则会产生过大的内应力,严重时将发生网架变形,甚至损坏。
因此网架的拼装精度必须严格符合要求,提升中网架内应力控制是一个关键的难题。
4)研究抗结构瞬变技术
提升过程中提升力随着提升高度的增加而变小,如果不采取技术措施,网架提升将到位时提升力会突然消失,在反拱力和水平力的作用下结构将发生瞬变,因此必须研究抗瞬变技术。
5)保证临时提升架的稳定问题
该网架是无柱落地网架,跨内没有结构梁柱可作支架,需在跨内设置临时提升架,提升架除了能承受竖向荷载外还需承受一定的水平力。
由于构件制作误差、地面拼装误差以及液压系统离散性等问题,同一提升架上两侧提升千斤顶的动态负载会有差异,如果此差异值过大将使提升架弯曲,甚至失稳而发生重大事故,因此要采取措施保证提升架的稳定和安全。
6)同步控制要求高
提升时如果各个吊点不同步,除了网架会发生变形外还会由于两边不同高差引起的水平力而偏移,甚至失稳。
在提升过程中网架两端是固定铰支座,中间是不固定的铰支座,这种结构提升时如果同步控制不好将增加结构的不稳定性,因此在展开提升中对各吊点的动作同步、高度偏差、负载均衡的控制要求都很高。
3、施工技术研究
3.1提升系统设计
通过对提升力的计算分析得出网架提升过程中提升力随着提升高度的变化而变化的规律,据此确定提升吊点的分布,完成提升系统的设计和布置。
3.2临时提升架设计
临时提升架的设计既要考虑提升架的承载能力(包括压力与变矩),更要考虑本身的稳定问题,为此选择TQ80/60塔机的塔身作为提升架,每个提升架由2个塔身组成,塔身底下做砼基础。
在提升过程中严格控制同一提升架上两个吊点的负载差异,专人观测提升架垂直度变化和两吊点液压千斤顶压力差。
一旦压力差达到警戒值必须立即停机调整,确保压力差在安全范围内。
3.3网架稳定措施
1)在网架的关键位置拉上若干浪索,采取合理的浪索形式,精确计算浪索拉力,并且设计提升过程中浪索同步调整的步骤和要求。
提升中使网架两边浪索的张紧程度基本相同,必要时通过浪索的张驰纠正网架的水平偏移。
2)在每个提升架上各安装一条垂直滑道,滑道与网架之间设置导轮,导轮固定在网架杆件上,与提升架间有20mm间隙,使网架既能上下移动又有水平方向约束,从而由可变机构转化为稳定结构。
在提升时滑道又可以兼作观测提升过程中网架晃动幅度的参照物。
3)为确保提升时网架的稳定,提升日的风力应小于4级。
3.4内应力控制技术
1)严格控制网架制作和拼装误差,网架在地面拼装后各铰轴必须相互平行,同一铰轴上各个铰的同轴度误差≤3mm。
2)提升中严格控制各吊点负载的变化差异,使网架保持动态平衡。
3)解决网架提升到位后提升千斤顶的同步卸载问题以及随着补缺杆件的安装和紧固网架内力的重新分布问题,以确保网架结构安全。
3.5抗结构瞬变措施
1)进行机构分析,明确提升中可能发生瞬变的阶段和高度,以利及时采取针对性的防范措施。
2)在铰支座处设置限位装置,克服或限制提升中将要发生的瞬变反拱。
3)在提升进入瞬变阶段时采取短行程提升,每次行程为20mm,每升一次就观测校正一次,使网架两边浪索的调节容易和精确,确保提升安全。
3.6测量和监测
提升前,严格复测网架拼装情况,如发现铰座同轴度误差超标必须进行调整。
提升中,虽然各提升点的偏差受计算机控制,但为保险起见必须人工辅助监测。
监测的方法简单可靠,内容包括网架提升高度、水平偏移,提升架垂直度以及液压千斤顶压力等,如发现超标立即通知提升控制室及时调整。
提升结束后,在提升系统卸载前对提升吊点作最后一次标高测量作为提升施工的验收依据。
4、提升系统构成
提升系统由液压子系统、计算机子系统和电气子系统构成。
1)液压子系统
液压子系统是网架提升的动力和承载系统,根据计算机系统的控制指令进行提升作业。
液压子系统主要由4个临时提升架、8套液压提升器、4台液压泵站以及提升承重的钢铰线组成。
每个提升架上布置2个提升吊点,配置2套液压提升器和1台液压泵站,液压提升器由1台液压千斤顶和相应的液压阀组组成。
2)计算机子系统
其主要任务是通过顺序控制技术驱动液压子系统按规定作业流程进行网架提升,通过偏差控制技术控制提升过程中的高差和负载,在必要时进行网架姿态和提升负载的调节修正和点动短距提升。
计算机子系统还负责提升系统的操作台控制,供操作人员对提升作业实施总控。
该子系统由顺序控制计算机、偏差控制计算机、操作台控制计算机以及相应的输入输出设备构成。
3)电气子系统
电气子系统根据计算机指令驱动液压子系统,并且采集提升工作状态和吊点数据反馈给计算机子系统。
电气子系统还负责提升系统的供配电管理,并提供多种安全连锁控制以确保施工安全。
该子系统由总控操作台、总电气柜、电液控制台、各类传感器、吊点控制箱、泵站控制箱、各类控制和信息传输电缆以及供配电线路和各类电源装置等组成。
5、控制技术创新
本项目与一般的网架整体提升方法有很大不同,需要针对其特点和难点在现有的整体提升控制技术的基础上进行创新,主要创新点如下。
1)高精度的偏差控制技术
采用多因素模糊控制逻辑,集成和调度PID控制、步进控制、数字滤波等多种算法,实现高精度的偏差控制,基本消除控制过程中常见的超调、欠调现象,使各提升点高度差始终控制在设计所要求的3mm以下,满足了安全施工需要。
由于高精度控制对提升效率有所影响,因此设计了控制精度可调功能,操作人员可根据实际需求设定合理的控制精度。
2)高稳度的负载调节技术
综合应用泵源调压、过载溢流、增益补偿以及提升姿态调整等控制技术,以计算机控制和人工控制相结合,实现平稳、精确的提升负载调节,并且做到实时的在线调节(边提升边调节),满足了提升全过程的负载控制要求。
3)多点同步调整技术
多点同步调整是在控制系统原有单点调整功能上的改进,在需要进行吊点高度或网架姿态调整时,计算机子系统可根据要求对所有吊点参数进行计算、生成各点调整量(也可由操作人员输入),提升系统就可一次同步地完成所有吊点的调整工作。
这一功能缩短了因调整而停机的时间,提高了效率,并且提高了调整工作本身的可靠性和安全性。
4)点动短距提升技术
网架提升进入抗瞬变阶段时要求进行短行程提升,以便于观察、测量以及浪索调节等工作。
为此研究开发了点动短距提升技术,启动提升开关一下网架就平稳缓慢地提升一次,提升高度可在10~270mm范围内自行设定。
网架提升到位后进行杆件安装时也可应用此功能进行精确定位。
6、结语
本项目突破了传统的大跨度网架安装方法,在国内是首创,在国际上100m以上跨度的大型柱面网架采用折叠展开提升法安装也是第一次。
由于坚持技术领先、安全第一,施工方案切实可行,在实施阶段又及时调整和优化,在设计、总包、业主、监理的密切配合下,比原计划提前15天安全优质地完成了网架的展开提升工程。
在展开提升过程中,当3个铰轴移到一直线上时出现了瞬变,由于技术措施正确有效顺利地克服了瞬变现象。
在展开提升过程中,前28m用了约7h,而最后不到1m的距离却用了将近4h,可见最后阶段为了抗瞬变提升速度很慢、难度也最大。
在展开提升过程中各吊点的高差始终控制在3mm以下,提升架两侧提升力的差异控制在2~3t,网架到位的安装精度完全符合设计要求。
本项目的成功不仅发展了企业的核心技术,增强了企业在空间结构和钢结构施工技术领域的竞争力,而且是对我国钢结构施工技术的创新和发展。
本项目共节省项目建设费用80多万元(主要是脚手架费用、斗轮机和输煤栈道搬迁费、煤场地基加固费等),更重要的是减少了高空作业,降低了劳动强度,提高了施工安全性,施工质量更容易控制和保证。
我国已建网壳结构工程的施工安装方法归纳起来有以下几种
(1)高空散装法。
一般需采用满堂脚手架作为安装和操作平台来组装网壳结构,该法散件多、且在高空作业,要特别注意节点和杆件的空间定位及焊接节点的焊缝质量。
(2)高空分块安装法。
一般采用少量立承架,把在地面上已组装好的小块网壳吊装到设计标高就位,然后与相邻的小块网壳连接成整体。
石家庄新华集贸中心营业厅双曲扁网壳的施工安装便采用这一方法。
(3)高空滑移法。
可在地面上组装成条状的网壳,吊装后在高空滑移就位并连成整体。
也可在网壳一端高空组装一段网壳,滑移后让出该段网壳的组装平台,便可组装第二段网壳并与第一段网壳连成整体,再高空滑移一段距离,再组装一段网壳,如此重复,直至组装最后一段网壳,即完成整个网壳的安装工作。
这种网壳的施工安装方法称为高空积累滑移法。
北京奥林匹克体育中心综合体育馆的斜拉网壳便采用这种四支点三滑道高空积累滑移法。
(4)整体吊装法。
网壳在地面上组装,然后采用把杆或其它起重设备整体吊装就位。
如汾阳网架公司铸造车间双曲扁网壳是采用这种安装方法施工的。
(5)整体提升法。
网壳在地面上组装,然后采用升板机或其它提升设备把整个网壳提升到设计标高就位。
杭州钱江海岸实验室钢筋混凝土联方型圆柱面网壳采用了这种安装方法,提升总重量600t。
我国大跨度网壳结构液压整体提升施工技术应用展望
【大中小发布时间:
2005-09-1211:
32:
11浏览次数:
219】
一、网壳结构液压整体提升法概述
对于超大型空间结构,在施工方案的选择上一般基于以下原则:
①确保安装精度;
②尽量减少高空作业量;
③尽量减少支撑架的量;
④尽量缩短工期;
⑤尽量降低施工成本。
液压提升法是一种用于超大、超重型结构施工的现代化施工方法,该工法的基本过程是先在地面组装完成一个完整的结构,再把提升支点和液压千斤顶设在建筑物的上部,施工时用液压千斤顶连接的钢索把结构整体平稳地提拉上去,然后把网壳结构固定在支座上。
液压提升法的特点是提升设备起重能力很大而设备本身的重量却相对较轻,而且提升高度几乎不受限制。
把该工法应用于大跨度网壳结构施工的主要优点是:
①由于组装工作几乎全部在地面或靠近地面的位置进行,所以高空作业量大大减少,这对方便施工操作、提高施工质量和保障施工安全有利,同时也方便了施工检查与管理工作。
②除网壳结构外,地面组装还包括屋面、设备等其它材料,使安装总工作量明显减少。
③脚手架用量最少,节省了支架材料租用与装拆费用,也节省了装拆脚手架的时间。
④由于钢结构网壳与土建可同步施工,所以对大跨度空间结构以及高度较大的空间结构来说,该施工方法总工期最短,成本最低。
在准备工作充分、操作过程规范的前提下,液压提升法是工效最高、最省力和最安全的施工方法。
因此,它具有很好的推广应用价值。
二、国外网壳结构工程施工应用实例
鉴于液压整体提升法的巨大优越性,国外一些巨型空间结构施工应用了该方法,以日本为例,90年代建成的几个大跨度的巨型穹顶都采用了液压整体提升施工法。
例如:
矢高36.2m、直径187.2m的名古屋穹顶是当今世界上最大跨度的单层网壳,该网壳结构及其屋面全部组装完成后的总重量达10300吨,于1995年12月15日从上午开始到下午结束总共花费近8个小时的时间,垂直提升距离30.7m就顺利完成了提升工作。
于1997年2月建成位于日本大阪市的大阪穹顶,直径210m,顶部标高83.7m,建筑面积34450㎡,是一座可用于体育比赛和大型展览会、音乐会的综合型场馆,见图1。
建筑屋盖部分为一直径为166.5m的联方网格型圆形穹顶,支座36点。
穹顶底部一圈为Y字型钢筋砼材料构件,中间部分为一直径134m部分为钢网壳结构,杆件采用型钢材料,节点为特制铸钢材料,杆件与节点采用焊接方式连接。
大阪穹顶的施工方案是:
土建部分(包括钢筋砼材料的Y字型构件)采用现场浇筑方法;
钢网壳部分(包括屋面材料与照明设备)采用先地面组装,然后液压提升的施工方案。
由于土建钢筋混凝土现浇工作与钢结构拼装工作分别处在不同的工作面上进行,两个工种可平行施工,所以工程的施工总工期大大缩短。
液压提升施工过程见图(abcd)。
图1大阪穹顶
(a)土建施工与网壳结构地面组装
(b)网壳安装完毕并开始提升
(c)网壳提升完毕并与支座连接
(d)工程全部竣工
需进行提升的钢网壳以及屋面材料和照明设备等的总重量达5500吨,向上垂直提升的距离达48.97m。
通过施工设计,最后确定采用18个提升点,即间隔一个支座设一个提升点。
提升施工于1996年1月25日上午开始,提升速度为6m/h,历时近9个小时,于当日下午提升到位并固定结束。
在提升施工前,进行了结构施工分过程的力学分析。
由于设计时的力学模型与施工时的力学模型不同,所以两种状态,即安装完成时构件的内力计算值与施工过程中构件的内力计算值完全不同。
以吊点所在位置的第七榀水平构件为例,设计时的内力计算值为受压力-852吨,而在施工时的内力计算值为受拉力613吨。
除内力值应分别计算外,施工过程中的变形也进行了计算,尤其是连接部位的变形值,因为这与施工的顺利实施有直接关系。
经计算在提升到位放下网壳时,连接部位的水平变位δH=32mm,垂直变位δV=65mm,如图4所示。
为保证施工的安全,对施工过程中的风速、结构内力、变位等进行实时自动监测,平均每2秒读数一次,以监测提升过程中结构实际受力情况。
施工非常顺利,最后的结果是令人满意的。
图3
结构施工时的变位图
三、我国空间结构液压整体提升施工技术现状及与国外的差距
液压整体提升法在我国的一些重型钢结构工程施工中已经得以成功应用,比如:
450吨重的上海东方明珠电视塔上部钢结构桅杆的整体提升施工、1200吨重的北京西客站钢门楼、上海歌剧院5800吨重钢结构屋盖以及其它一些平板网架均采用了液压整体提升施工法。
这些成功的工程实践说明我国的液压整体提升施工技术已经有了较好的基础,国内的液压起重设备的起重能力完全可以胜任大吨位的吊装工作,但是,我们也应该看到,我国的这些工程都是结构刚度很大的钢结构工程,不是网壳结构工程。
网