铁路桥梁板式橡胶支座最新Word格式.docx
《铁路桥梁板式橡胶支座最新Word格式.docx》由会员分享,可在线阅读,更多相关《铁路桥梁板式橡胶支座最新Word格式.docx(23页珍藏版)》请在冰豆网上搜索。
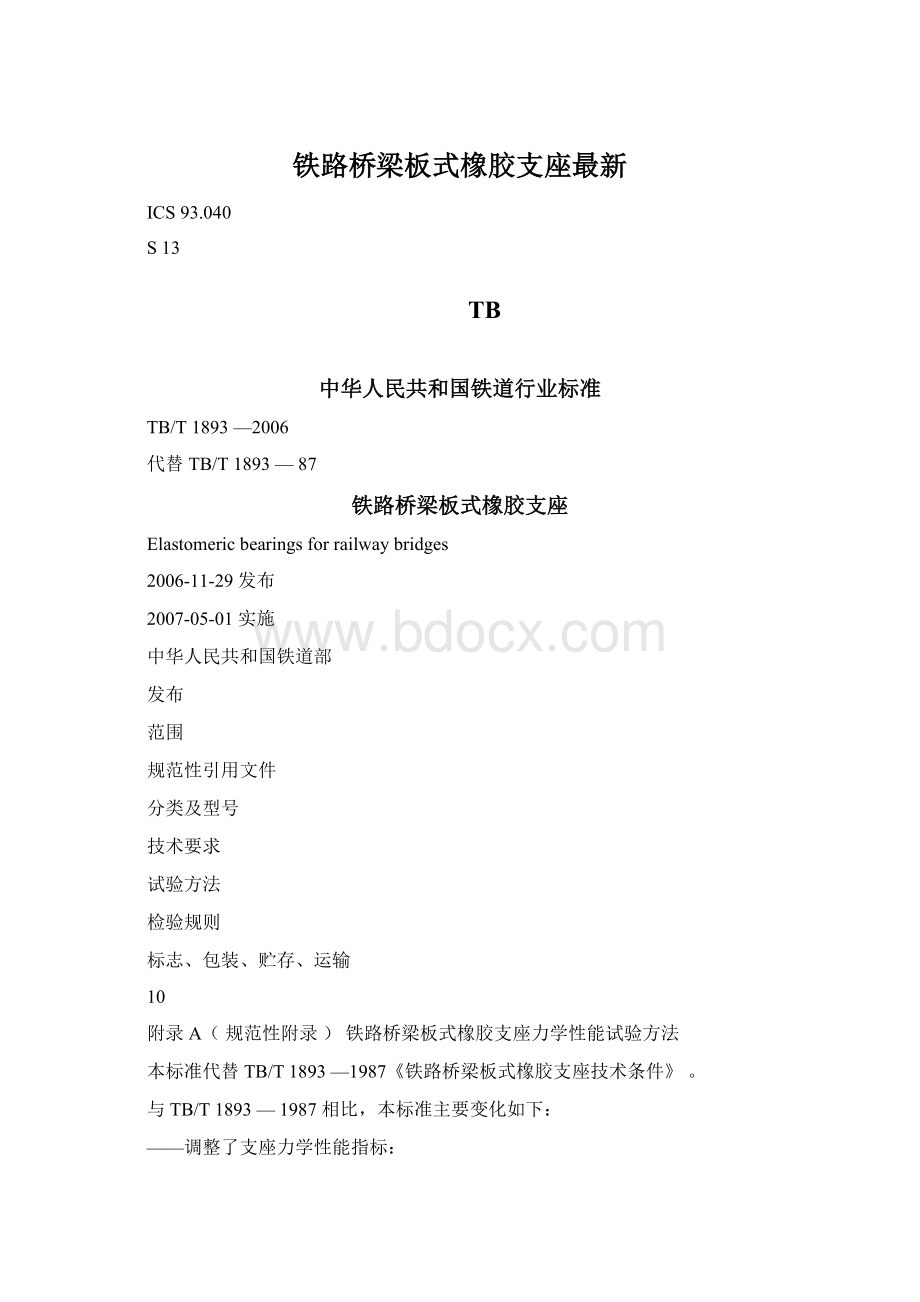
+60C,宜采用氯丁橡胶(CR);
耐寒型支座的适用温度范围为一40C〜+60C,应采用天然橡胶(NR)。
3.2型号
支座型号表示如下:
支座竖向设计承载力(kN)
支座名称
示例1:
TBZ1000GD—(CR)表示竖向设计承载力为1000kN的常温型固定板式橡胶支座。
示例2:
TBZ2000ZX—e40(NR)表示竖向设计承载力为2000kN,设计主位移为±
40mm的耐寒型纵向活动板式橡胶支座。
3.3结构形式
3.3.1铁路桥梁板式橡胶支座由上支座板、承压橡胶板、下支座板和支座锚栓等组成。
结构示意图见
4。
图1、图2、图3及图
pq
1——上支座板;
2――下支座板;
图1固定支座结构示意图
3.3.2
结构示意图见图5。
承压橡胶板结构应由多层橡胶及加劲钢板构成,钢板全部包在橡胶材料内,
承压橡胶板中单层橡胶片的厚度ti为5cm、8cm、11cm三种,支座中加劲钢板的厚度to为2cm、3cm、
2.5mm,加劲钢板侧面橡胶保护层的厚度不宜
4cm三种。
顶、底加劲钢板橡胶保护层的厚度不宜小于小于5mm。
1——上支座板;
2――下支座板;
3――承压橡胶板;
4――锚栓。
图2纵向活动支座结构示意图
1——上支座板;
图3横向活动支座结构示意图
A—AHl面图
B—B剖面图
图4多向活动支座结构示意图
1——橡胶;
2――加劲钢板。
图5承压橡胶板结构示意图
3.4规格系列
3.4.1支座竖向承载力系列分15级(单位为千牛,kN):
300、400、500、600、750、875、1000、1250、1500、1750、2000、2250、2500、2750和3000。
3.4.2活动支座主位移方向的位移分3级:
±
20mm、±
30mm和±
40mm。
固定支座和单向活动(纵
1mm。
向活动和横向活动)支座在限位方向的最大允许位移不大于±
3.4.3固定支座顺、横桥向和纵向活动支座横桥向、横向活动支座顺桥向所承受的水平力宜为支座竖向设计承载力的15%或30%,在特殊情况下,支座的水平力可根据需要确定。
4技术要求
4.1支座力学性能要求
支座的力学性能要求见表
支座形状系数S应按下列公式计算:
a旳
2(a+b)hi
表2板式橡胶支座抗压弹性模量E
表1
项目
指标
极限抗压强度Ru
>
60
MPa
抗压弹性模量E1
E±
EX20%
抗剪弹性模量Gi
G±
GX15%
疲劳试验后的抗压弹性模量E2
<
(E1+E1X5%)
老化后抗剪弹性模量G2
(G1±
0.15MPa)
抗剪粘结性能(T=2MPa时)
无橡胶开裂和脱胶现象
支座抗压弹性模量标准值E按表2取值。
S
5
6
7
8
9
11
12
13
E
270
340
420
500
590
670
760
860
950
14
15
1060
1180
单位为兆帕
4.2材料要求
4.2.1橡胶
橡胶的物理机械性能应满足表3的要求。
表3
技术指标
氯丁橡胶
(适用于—25C〜60C)
天然橡胶
(适用于一40C〜60C)
硬度
IRHD
60±
5
拉伸强度
17
18
扯断伸长率
%
400
450
脆性温度
—40
—50
恒定压缩永久变形(70CX24h)
15
30
耐臭氧老化(试验条件,20%伸长,40CX96h)
1X104%
0.25X04%
无龟裂
热空气老化试验(与未老化前
试验条件
°
CXh
100X70
70X168
数值相比发生的最大变化)
—15
扯断伸长
-40
-20
硬度变化
+10
-5
橡胶与钢板粘结剥离强度kN/m
10
不应使用任何冉生胶或粉碎的硫化橡胶,其最小含胶量不得低于重量的
55%。
4.2.2加劲钢板
4.2.2.1加劲钢板的强度不应低于允许使用拼接钢板。
4.2.2.2钢板加工时,应除锈、去油污,钢板应平整,无翘曲,
4.2.3上、下支座板
上、下支座板宜采用ZG270—500铸钢件,材质应符合波探伤检验,达到I级铸件要求;
上、下支座板采用钢板焊接时,
Q235钢板强度,其质量应满足GB/T912的有关要求。
加劲钢板不
周边应去除毛刺。
GB/T11352的要求,铸件加工后须经超声
钢板强度不宜低于Q235,材质应满
足GB/T700的有关要求,焊接质量应符合JB/T5943的要求,上、下支座板上的限位挡块与钢板的焊
接可靠,并经超声波探伤无缺陷。
4.2.4粘结剂
3的要求。
粘结剂质量应稳定,橡胶与钢板粘结后的剥离强度应满足表
4.3承压橡胶板定位
承压橡胶板与上、下支座板之间可采用定位钢板定位或粘结定位。
橡胶板与钢板采用粘结定位时,粘结剥离强度不小于4kN/m。
4.4尺寸偏差
4.4.1
GB/T1804
上、下支座板机加工尺寸应符合设计要求,设计图中未标注公差的部件,其公差按的m级取值。
4.4.2承压橡胶板平面尺寸偏差应符合表4的规定。
单位为毫米
承压橡胶板
长边范围(lb)
偏差
lb<
300
+2
300<
lbW500
+4
lb>
500
+5
4.4.3承压橡胶板厚度尺寸偏差应符合表5的规定。
表5单位为毫米
厚度范围(t)
tw49
+1
49<
tw100
100Vt<
150
4.5外观质量
每块承压橡胶板外观质量应符合表6的规定。
4.6内在质量
7的要求。
表6
承压橡胶板解剖后应满足表
名称
成品质量标准
气泡、杂质
气泡、杂质总面积不应超过支座平面面积的0.1%,且每一处气泡,杂质面积不
能大于50mm2,最大深度不超过2mm
凹凸不平
当支座平面面积小于0.15m2时,不多于2处;
大于0.15m2时,不多于4处,且每处凹凸高度不超过0.5mm,面积不超过6mm2
四侧面裂纹、钢板外露
不允许
掉块、崩裂、机械损伤
钢板与橡胶粘结处开裂或剥离
表面平整度
承压橡胶板表面不平整度不大于平面最大长度的0.4%
表7
解剖检验标准
锯开胶层厚度
胶层厚度应均匀,t1为5mm或8mm时,其偏差为±
0.4mm;
t1为11mm时,其偏差不应大于±
0.7mm
钢板与橡胶粘结
钢板与橡胶粘结应牢固,且无离层现象,其平面尺寸偏差为±
1mm;
上下保护
层偏差为+0.5mm
剥离胶层(应按HG/T2198规定制成试样)
剥离胶层后,测定的橡胶性能与表2的规定相比,拉伸强度的下降不应大于15%,扯断伸长率的下降不应大于20%
4.7支座钢件外露部分应按TB/T1527—2004第六套涂装体系的规定进行表面油漆防护。
采用的涂料
应符合TB/T1527—2004、TB/T2772—1997、TB/T2773—1997的要求。
5试验方法
支座外形尺寸应用钢直尺量测,厚度应用游标卡尺或量规量测。
长短尺寸应在四边上测量,厚度应
在四边中点测量。
外形尺寸和厚度取其实测值的平均值。
5.3承压橡胶板外观质量
承压橡胶板外观质量,用目测方法或量具逐块进行检查。
5.4力学性能
支座成品力学性能试验应按照附录A的规定进行。
5.5内在质量
3层的支座,将承压橡胶板沿垂直方向锯开,
支座解剖检验,应抽取一块承压橡胶板橡胶层数大于进行规定项目检验。
6检验规则
6.1检验分类
支座检验分为进厂原材料检验、出厂检验和型式检验。
6.1.1进厂原材料检验
支座加工用原材料及外协加工件进厂时,应按本标准要求进行验收检验。
6.1.2出厂检验
出厂检验为每批产品交货前应进行的检验。
出厂检验应由工厂质检部门进行,确认合格后方可出厂。
6.1.3型式检验
有下列情况之一时,应进行型式检验;
新产品试制或老产品转厂生产的定型鉴定;
正常生产后,胶料配方、工艺、材料有较大改变,可能影响产品性能时;
产品停产一年以上,恢复生产时。
6.2检验项目及要求
6.2.1
8进行检验。
支座用原材料应附有材质合格证明书,胶料、钢材和粘接剂应按表
表8
项目
检验内容
检验频次
要求
胶料
物理机械性能
脆性温度、热空气老化、恒定压缩永久变形每季度一次;
耐臭氧老化每年一次;
其余每批胶料
4.2.1
钢材
机械性能、外观
每批钢材
4.2.2
4.2.3
粘结剂
与钢板、橡胶粘结剥离强度
每批
4.2.4
6.2.2支座出厂检验应满足表9的要求。
表9
外形尺寸
平面尺寸、厚度偏差
每块
4.4
外观质量
外观缺陷
4.5
内在质量
内容缺陷、偏差
每200块取一块
4.6
力学性能
抗压、抗剪弹性模量,极限抗压强度,抗剪粘结性能检验
每500块至少取一种
4.1
10的要求。
6.2.3支座型式检验、原材料检验、出厂检验应满足表
6.3判定规则
6.3.1进厂原材料材质按本标准规定检验时,有一项不合格者,则该批原材料为不合格。
6.3.2外形尺寸、外观质量中有一项不合格者,则该批支座为不合格。
内在质量不合格者,可从该批产品中随机双倍取样,对不合格项进行复检。
若该项仍不合格,则该批产品不合格。
6.3.3支座力学性能试验时,对于任一项力学性能,随机抽取三块(或三对)支座进行试验。
若三块(或
三对)的该项力学性能均满足要求,则该组支座的该项力学性能满足要求;
若有两块(或两对)不满足
要求,则该组试样不合格;
若有一块(或一对)支座不能满足要求时,应从同批产品中随机再抽取双倍支座进行复检,若仍有一块(或一对)不合格,则判定该批产品不合格。
表10
序号
型式检验分类
力学性能检验项目
抗压弹性模量
抗剪弹性模量
抗剪粘结性
抗剪老化
疲劳后抗压弹性模量
极限抗压强度
抽检支座规格
1
新产品试制定型鉴定
△
三种规格
2
胶料配方、工艺改变
—
3
停产一年恢复生产
每种规格支座抽检数量(各项检验通过)
三块
三对
任选三种规格中的一种,一块
满足4.1
注:
表中“△”表示应作项目,“空白”表示可不作项目。
试验方法见附录A。
6.3.4型式检验时,全部检验项目均满足要求时试件为合格。
7标志、包装、贮存、运输
7.1标志
每个支座应有永久性标志,其内容应包括:
产品名称、规格型号、主要技术指标(竖向承载力、位移量、转角)、生产厂名、出厂标号和生产日期。
7.2包装
支座应根据分类、规格分别包装。
包装应牢固可靠,包装外面应注明产品名称、规格、出厂日期。
包装内应附有产品合格证、材质、单层橡胶和钢板厚度、钢板平面尺寸、钢板层数、橡胶总厚度。
7.3
触,
7.4
贮存支座的库房应干燥通风,支座应堆放整齐,保持清洁,严禁与酸、碱、油类、有机溶剂等相接并应距热源1m以上,且不应与地面直接接触。
运输
支座在运输中,应避免阳光直接曝晒、雨淋、雪浸,并应保持清洁,不应与影响橡胶质量的物质相接触。
附录A
(规范性附录)
铁路桥梁板式橡胶支座力学性能试验方法
本附录规定了铁路桥梁板式橡胶支座抗压弹性模量、抗剪弹性模量、疲劳后抗压弹性模量、抗剪老抗剪粘结性能、极限抗压强度的试验方法和判定规则。
、-~P'
fV*夹A*曰试样数量
每次检验用的试样的规格和数量应符合表10的规定,各种试验试样通用。
A.2.4试样抽取
试验用的试样应在仓库内随机抽取。
A.2.5试样停放
试验前应将试样直接暴露在标准温度23C〜±
5C下,停放24h。
A.3检测仪器及对检测单位和人员的要求
A.3.1试验机应具备下列功能:
能平稳连续加载、卸载,且无冲击和颤动现象,试验用承载板应具有足够的刚度,平面尺寸应大于被测试样的平面尺寸,在最大荷载下不应发生挠曲。
A.3.2进行剪切试验时,其剪切试验装置的水平油缸、负荷传感器的轴线应和中间钢拉板的对称轴相重合,确保被测试样水平轴向受力。
A.3.3试验机的级别为I级,示值相对误差最大允许值为±
1.0%,试验机正压力宜在最大力值的
0.4%〜90%范围内。
水平力宜在最大力值的1%〜90%范围内。
A.3.4测量支座试样变形量的仪表量程应满足试样变形量的需要,测量竖向压缩变形量和水平位移变
形量的分度值为0.01mm,其示值误差和相关技术要求应按相关的检验规程进行检定。
A.1。
检测人员应经过技术培训和考核,
A.3.5检测单位应通过省级及其以上计量行政主管部门的计量认证。
并持有上岗证书。
A.4试验方法
A.4.1抗压弹性模量试验
A.4.1.1试验步骤及试验装置
抗压弹性模量应按下列步骤进行试验,试验装置示意图见图
1——上承载板;
2——下承载板;
3――位移传感器;
4――支座试样。
fl
图A.1抗压弹性模量试验装置示意图
d)
安装试样。
误差小于试件短边尺寸的四只位移传感器,确认无误后开始预压。
预压。
将压应力以0.03MPa/s〜0.04MPa/s的速率连续增至平均压应力d=10.0MPa(以承压橡胶板的面积计算得出),持荷2min后以连续均匀的速度将压应力卸至2.0MPa,持荷5min,记录初始值。
预压三次。
正式加载。
每一加载循环自2.0MPa开始,将压应力以0.03MPa/s〜0.04MPa/s的速率均匀加载
至4MPa,持荷2min后采集支座变形值,然后以同样的速率每2MPa为一级逐级加载,采集支
座变形数据直至平均压应力d=10MPa为止,然后以连续均匀的速度卸载至压力为1.0MPa。
加
载过程应连续进行三次。
以承载板四角测得的变形值的算术平均值作为各级荷载下试样的累计竖向压缩变形加载次数),按试样支座总厚度h求出各级试验荷载作用下试样的累计压缩应变
将试样置于试验机的承载板上,上、下承载板与支座接触面不得有油渍;
对准中心,
1%。
缓慢加载至压力为2.0MPa,稳压后核对承载板四角对称安置的
△ci(i表示
£
i=△ci/ho
A.4.1.2
试样实测抗压弹性模量由平均压应力d=4MPa、6MPa、8MPa和10MPa四级荷载下的累计压缩应
变值按线性回归求得。
A.4.1.3结果
每一块试样的抗压弹性模量E1为三次加载过程所得的三个实测结果的算术平均值,但每一次的结果
和算术平均值之间的偏差不应大于±
5%,否则应对该试样重新复核试验一次。
如果仍超过±
5%,则认
为该试样不合格。
A.4.2抗剪弹性模量试验
A.4.2.1
试样实测抗压弹性模量
抗剪弹性模量应按下列步骤进行试验,试验装置示意图见图
支座应顺其短边方向受剪,将试样及中间钢拉板按双剪组合配置好,使试样和中间钢拉板的对称轴及试验机承载板中心轴处在同一垂直面上,安装误差应小于试件短边尺寸的1%。
为防
止出现打滑现象,可在上、下承载板和中间钢拉板上粘贴防滑摩擦板,以确保试验的准确性。
A.2。
以0.03MPa/s〜0.04MPa/s的速率连续对支座施加压应力至平均压应力胶板的面积计算得出),并在整个抗剪试验过程中保持不变。
d=5.0MPa(以承压橡
1——上承载板;
2――支座试样;
3——中间钢拉板;
4——下承载板;
5――防滑摩擦板。
C)
e)
f)
图A.2抗剪弹性模量试验装置示意图
调整试验机的剪切试验装置,使水平油缸、荷载传感器的轴线和中间钢拉板的对称轴重合。
预剪水平力。
以0.002MPa/s〜0.003MPa/s的速率连续施加水平剪应力至剪应力t=1.0MPa(以承压橡胶板的面积计算得出),持荷2min,然后以连续均匀的速度卸载至剪应力为0.1MPa,持荷5min,记录初始值。
预剪三次。
每一加载循环自T=0.1MPa开始,每级剪应力增加0.1MPa,采集支座变形数据,
至T=1.0MPa为止,然后以连续均匀的速度卸载至剪应力为0.1MPa,10min后进行下一循环试
验。
加载过程连续进行三次。
按试样橡胶层的总厚度te求出在各级试验荷载作用下试样的累计剪切应变为各级水平荷载下位移传感器所测得的试样累计水平剪切变形。
试样的实测抗剪弹性模量由剪应力
丫=△s/te,其中△s
A42.2
性回归求得。
A.4.2.3结果
每对检验支座所组成试样的抗剪弹性模量但各单项结果与算术平均值之间的偏差应不大于±
过±
5%,则认为该对支座不合格。
A.4.3抗剪粘结性能试验
整体支座抗剪粘结性能试验方法与抗剪弹性模量试验方法相同,对支座以0.03MPa/s〜0.04MPa/s
的速率连续施加压应力至平均压应力(T=5.0MPa(以承压橡胶板的面积计算得出)。
然后以0.002MPa/s〜
0.003MPa/s的速率连续施加水平力,当剪应力达到2MPa(以橡胶层面积计算得出)持荷5min后,水平
力以连续均匀的速度卸载,试验中随时观察试件受力状态及变化情况,试样不得出现橡胶开裂和脱胶现
象。
A.4.4抗剪老化试验
将已经过抗剪弹性模量试验的试样置于热空气老化箱内,在70C±
2C温度下经72h后取出,将试
样在标准温度23C±
5C下停放48h,再在标准试验室温度下进行剪切试验,试验与A.4.2抗剪弹性模量
T=0.3MPa/s〜1.0MPa/s,8级荷载下的累计剪切应变按线
G1,为该对试件三次加载所得的三个结果的算术平均值。
5%,否则应对该试样重新复核试验一次。
如果仍超
A45抗压疲劳试验
将已经过抗压弹性模量试验的试件安放在疲劳试验机上,对试样施加最大平均压应力bmax=15
MPa(以承压橡胶板的面积计算得出),开启疲劳试验机,使支座最小平均压应力bmin=4.5MPa,以加载
频率3Hz〜5Hz反复加载200万次。
试验过程中监测支座表面温度,其值不应超过42C。
试验后观察支
座表面状况,停放24h后按A.4.1抗压弹性模量试验方法再次测定支座在疲劳荷载作用后的抗压弹性模量
E2°
A.4.6极限抗压强度试验
极限抗压强度试验应按下列步骤进行:
将试样放置在试验机的承载板上,上、下承载板与支座接触面不应有油污;
对准中心位置,安
装误差应小于试件短边尺寸的1%。
以0.1MPa/s的速率分10级加载至试样极限抗压强度Ru=60MPa(以承压橡胶板内的面积计算得出),绘制荷载一变形图,并随时观察试样受力状态及变化情况。
受试验设备能力所限,大型支座无法压至60MPa时,经有关各方协商,可采用双倍荷载检验方
A.5
A.5.1
求。
A.5.2求。
A.5.3
式,即加压至b=20MPa,观察试样受力状态及变化情况,或采用相同生产工艺的小型支座进行替代试验。
试验结果判定
试样的抗压弹性模量E1与标准值E的偏差在±
20%范围之内时,则试样的抗压弹性模量满足要
试样的抗剪弹性模量Gi与标准值G的偏差在±
15%范围之内时,则试样的抗剪弹性模量满足要
在两倍剪应力作用下,橡胶层未开裂、脱胶,中间层钢板未断裂错位,卸载后支