直齿圆柱齿轮的设计及加工工艺Word文档格式.docx
《直齿圆柱齿轮的设计及加工工艺Word文档格式.docx》由会员分享,可在线阅读,更多相关《直齿圆柱齿轮的设计及加工工艺Word文档格式.docx(29页珍藏版)》请在冰豆网上搜索。
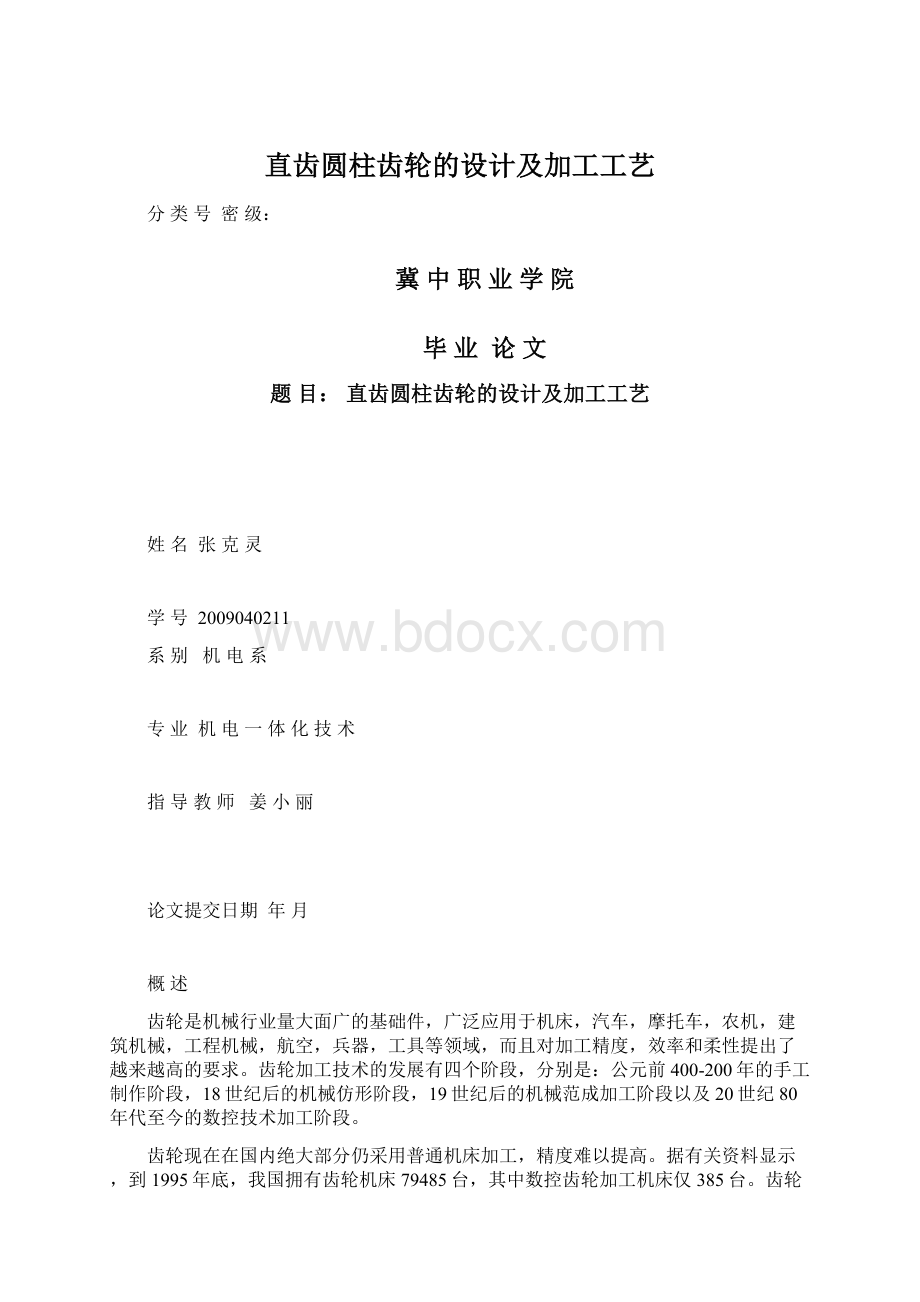
近年来,结构紧凑的直驱电机在砂轮主轴和齿轮工件主轴上的使用日渐增加。
直驱主轴可避免传动链误差。
因此,在“修砂轮—磨齿轮”循环中运用直驱电机,并配以较好的砂轮和多轴联动控制,可消除切削纹、偏畸几何形状、齿轮使用噪音的高频误差及有害振动。
(3)自动化
“自动化”一词越来越多地应用于磨齿加工特别是流程化生产中,包括工件安装、换刀以及与工件流程同步的库存分类等。
自动化消除了机器空转时间并有利于减少工序间等待时间。
(4)磨齿机软件
基于Windows的软件也像应用于个人计算机一样,广泛应用于今天的磨齿机中(如基于Windows的设计系统和数控系统)。
以前只能以纸绘图,现在,图形界面和算法软件相结合的设计加修正软件包可使齿轮几何尺寸设计程序化和局部制造仿真化。
驱动、滚珠丝杠和位置传感器三者间的高精度闭环控制因软件的应用而得以实现。
许多新一代磨齿机的部件配有与驱动单元分离的位置传感器,因而具有更高的精度和热稳定性。
绝对式位移传感器和绝对编码技术保证了在高定位精度前提下,反馈数据的高速传输和机床传动的稳定性。
(5)新材料砂轮
先进的陶瓷结合剂砂轮和电镀立方氮化硼(CBN)砂轮有着同样高的生产效率。
由于“混合颗粒”型合成物中使用了新材料以及粘接工艺的进步,提高了陶瓷结合剂砂轮的强韧性、形状精度保持力、材料切除力和耐用性。
这些优异性能来源于高性能颗粒结构和增大的孔隙度。
同时,良好的颗粒结构减少了磨削压力,降低了磨削温度。
(6)磨削费用的降低
如今,磨齿成本大幅下降,其原因很多,如基于模块化设计的高性价比机型、数控系统、流程化生产等,即使是综合了前述所有先进技术的磨齿机也比以前的机型便宜得多,大批量生产使单件生产周期比以前缩短了50%~70%,损耗品(砂轮和金刚石修正器等)成本也大幅下降。
第一章直齿圆柱齿轮的设计……………………………………..2
1.1齿轮的基础知识............................................................................2
1.2齿轮材料的合理选择.....................................................................4
1.3影响齿轮工作平稳性的加工误差分析.........................................8
第二章直齿圆柱齿轮的工艺分析……………………………...…10
2.1轴类零件加工的工艺路线.............................................................10
2.2齿轮加工方法.................................................................................10
2.3齿轮加工方案选择及使用要求.....................................................14
2.4齿轮加工工艺过程.........................................................................15
第三章齿轮的加工............................................................................19
3.1圆柱齿轮齿形加工方法和加工方案………………………….....19
3.2典型齿轮零件加工工艺分析……………………………..……...20
结束语.......................................................................................................23
参考文献....................................................................................................24
第一章直齿圆柱齿轮轴的设计
1.1齿轮的基础知识
1.1.1齿轮的基础知识
(1)齿轮机构的优点有:
1)齿轮机构传别可达100000kw、300m/s。
2)齿轮机构的传动比恒定,寿命长,工作可递的功率和圆周速度分靠性高。
3)齿轮机构能够实现平行轴和不平行轴之间的传动。
(2)齿轮机构的缺点有:
1)齿轮机构得制造成本过高。
2)齿轮机构不适用于远距离的传动。
3)低精度齿轮会产生有害的冲击,噪音和振动。
1.1.2齿轮的分类
从《机电一体化实用手册》(见参考文献,以下皆是)一书中我们了解到:
齿轮的传动是通过轮齿之间的相互啮合来实现直接接触的传动方法。
这种传动方法的传动比精确、传递功率较大。
齿轮传动要满足瞬时传动比保持不变,则两轮的齿廓不论在何处接触,过接触点的公法线必须与两轮的连心线交于固定的一点。
外啮合齿轮
直齿轮内啮合齿轮
齿轮齿条啮合
平行轴
斜齿轮
直齿圆锥齿轮
相交轴—圆锥齿轮
螺旋齿圆锥齿轮
齿轮传动蜗轮与蜗杆
交错轴
准双曲面齿轮
同心轴—行星齿轮
图1-1齿轮的分类
1.1.3共轭齿廓的重要一种----渐开线齿廓齿轮
通过这段时间的考查与探讨,我们得出以下一些结论:
(1)发生线沿基圆滚过的长度,等于基圆上被滚动过的圆弧长。
(2)渐开线上任意一点的法线必与基圆相切;
渐开线上各点的曲率半径不相等;
渐开线的形状决定基圆的大小。
(3)基圆内无渐开线。
图1-2渐开线的形成及压力角图1-3渐开线形状与基圆大小的关系
(4)渐开线齿廓啮合的特点:
1)渐开线齿轮中心距的可分性。
2)啮合角为恒定值。
(5)压力角(ak)及展角(invak)的计算
cos(ak)=(rb)/(rk)inv(ak)=tg(ak)-(ak)
1.1.4标准直齿圆柱齿轮外啮合几何尺寸计算
(1)分度圆、模数和压力角
我们把齿轮上作为齿轮尺寸基准的圆称为分度圆,分度圆以d表示。
相邻两齿同侧齿廓间的分度圆弧长称为齿距,以p表示,p=πd/z,z为齿数。
齿距p与π的比值p/π称为模数,以m表示(模数是齿轮的基本参数)。
由此可知:
齿距p=mπ度圆直径d=mz
我们把渐开线齿廓上与分度圆交点处的压力角α称为分度圆压力角,简称压力角,国家规定标准压力角α=20°
。
(2)齿距、齿厚和槽宽
齿距p分为齿厚s和槽宽e两部分,即
s+e=p=πm
标准齿轮的齿厚和槽宽相等,即
s=e=πm/2
齿距、齿厚和槽宽都是分度圆上的尺寸。
(3)齿顶高、顶隙和齿根高
由分度圆到齿顶的径向高度称为齿顶高,用ha表示
ha=ha*m
两齿轮装配后,两啮合齿沿径向留下的空隙距离称为顶隙,以c表示
c=c*m
由分度圆到齿根圆的径向高度称为齿根高,用hf表示
hf=ha+c=(ha*+c*)m
式中ha*、c*分别称为齿顶高系数和顶隙系数,标准齿制规定:
正常齿制ha*=1、c*=0.25,短齿制ha*=0.8、c*=0.3。
由齿顶圆到齿根圆的径向高度称为全齿高,用h表示
h=ha+hf=(2ha*+c*)m
齿顶高、齿根高、全齿高及顶隙都是齿轮的径向尺寸。
表1-1渐开线标准直齿圆柱齿轮几何尺寸计算公式
名称
符号
计算公式
齿距
p
p=mπ
齿厚
s
s=πm/2
槽宽
e
e=πm/2
齿顶高
ha
ha=ha*m
齿根高
hf
hf=ha+c=(ha*+c*)m
全齿高
h
h=ha+hf=(2ha*+c*)m
分度圆直径
d
d=mz
齿顶圆直径
da
da=d+2ha=m(z+2ha*)
齿根圆直径
df
df=d2hf=m(z2ha*2c*)
基圆直径
db
db=dcosα=mzcosα
中心距
a
a=m(z1+z2)/2
1.2齿轮材料的合理选择
在加工之前,为了保证齿轮工作的可靠性,提高其使用寿命,齿轮的材料及其热处理应根据实际的工作条件和材料的特点来选取。
在本文的一些条件下,对齿轮材料的基本要求是:
应使齿面具有足够的硬度和耐磨性,齿心具有足够的韧性,以防止齿面的各种失效,同时应具有良好的冷、热加工的工艺性,以达到齿轮的各种技术要求。
可以知道的是,常用的齿轮材料为各种牌号的优质碳素结构钢、合金结构钢、铸钢、铸铁和非金属材料等。
一般多采用锻件或轧制钢材。
当齿轮结构尺寸较大,轮坯不易锻造时,可采用铸钢。
开式低速传动时,可采用灰铸铁或球墨铸铁。
低速重载的齿轮易产生齿面塑性变形,轮齿也易折断,宜选用综合性能较好的钢材。
高速齿轮易产生齿面点蚀,宜选用齿面硬度高的材料。
受冲击载荷的齿轮,宜选用韧性好的材料。
对高速、轻载而又要求低噪声的齿轮传动,也可采用非金属材料、如夹布胶木、尼龙等。
1.2.1满足材料的机械性能
在加工过程中,如果齿根部受到大弯曲应力,可能产生齿面或齿体强度失效;
如果齿面各点都有相对滑动,会产生磨损。
齿轮主要的失效形式有齿面电蚀、齿面胶合、齿面塑性变形和轮齿折断等。
因此我们要求齿轮材料有高的弯曲疲劳强度和接触疲劳强度,齿面要有足够的硬度和耐磨性,芯部要有一定的强度和韧性。
1.2.2满足材料的工艺性能
材料的工艺性能是指材料本身能够适应各种加工工艺要求的能力。
齿轮的制造要经过锻造、切削加工和热处理等几种加工,因此选择材料时要特别注意材料的工艺性能。
一般来说,碳钢的锻造、切削加工等工艺性能较好,其机械性能可以满足一般工作条件的要求,但强度不高,淬透性较差。
而合金钢淬透性好、强度高,但锻造、切削加工性能较差。
我们可以通过改变工艺规程、热处理方法等途径来改善材料的工艺性能。
1.2.3材料的经济性要求
在满足使用性能的前提下,选用齿轮材料还应该注意尽量降低零件的总成本。
从材料本身价格来考虑,碳钢和铸铁的价格比较低廉,因此在满足零件机械性能的前提下选用碳钢和铸铁,不仅具有较好的加工工艺性能,而且可以降低成本。
从齿轮生产过程的耗费来考虑。
首先,采用不同的热处理方法相对加工费用也不一样。
其次,通过改进热处理工艺也可以降低成本。
1.2.4齿轮的材料及热处理
《材料成形原理与工艺》中对齿轮材料的基本要求如下:
-齿面要硬,齿芯要韧
-易于加工及热处理
-软齿面齿轮齿面配对硬度差为30-50HBS
常用的齿轮材料及其热处理方法有:
(1)中碳钢(如45钢)进行调质或表面淬火,综合力学性能较好,用于低速、轻载或中载的一些不重要的齿轮。
(2)合金调质钢(如40Cr)进行调质或表面淬火,综合力学性能更好,且热处理变形小,适用于中速、中载及精度要求较高的齿轮。
(3)合金渗碳钢(如20Cr,20CrMnTi)进行渗碳淬火或液体碳氮共渗,齿面硬度可达58HRC,且心部有较高韧性,适用于高速、中载和或有冲击载荷的齿轮
(4)铸铁及其他非金属材料(如尼龙、夹布胶木等)。
这些材料强度低、易加工,适用于一些轻载的齿轮。
由于本文用到的齿轮材料为钢制齿轮,因此主要介绍一下它的的热处理方法(本篇文章的加工工艺过程的选用中需要用到的热处理方法是正火和调质):
a.表面淬火
表面淬火常用于中碳钢和中碳合金钢,如45、40Cr钢等。
表面淬火后,齿面硬度一般为40~55HRC。
特点是抗疲劳点蚀、抗胶合能力高。
耐磨性好;
由于齿心部分未淬硬,齿轮仍有足够的韧性,能承受不大的冲击载荷。
b.渗碳淬火
渗碳淬火常用于低碳钢和低碳含金钢,如20、20Cr钢等。
渗碳淬火后齿面硬度可达56~62HRC,而齿轮心部仍保持较高的韧性,轮齿的抗弯强度和齿面接触强度高,耐磨性较好,常用于受冲击载荷的重要齿轮传动。
齿轮经渗碳淬火后,轮齿变形较大,应进行磨削加工。
c.渗氮
渗氮是一种表面化学热处理。
渗氮后不需要进行其他热处理,齿面硬度可达700~900HV。
由于渗氮处理后的齿轮硬度高,工艺温度低,变形小,故适用于内齿轮和难以磨削的齿轮,常用于含铅、钼、铝等合金元素的渗氮钢,如38CrMoAl等。
d.调质
调质一般用于中碳钢和中碳合金钥,如45、40Cr、35SiMn钢等。
调质处理后齿面硬度一般为220~280HBS。
因硬度不高,轮齿精加工可在热处理后进行。
e.正火
正火能消除内应力,细化晶粒,改善力学性能和切削性能。
机械强度要求不高的齿轮可采用中碳钢正火处理,大直径的齿轮可采用铸钢正火处理。
表1-2常用齿轮材料及其力学性能
类别
材料牌号
热处理方法
抗拉强度
σb/MPa
屈服点
σs/MPa
硬度
HBS或HRC
优质碳素钢
35
正火
500
270
150~180HBS
调质
550
294
190~230HBS
45
588
169~217HBS
647
373
229~286HBS
表面淬火
40~50HRC
50
628
180~220HBS
合金结构钢
40Cr
700
240~258HBS
48~55HRC
35SiMn
750
450
217~269HBS
45~55HRC
40MnB
735
490
241~286HBS
20Cr
渗碳淬火后回火
637
392
56~62HRC
20CrMnTi
1079
834
56~62HRC
38CrMnAlA
渗氮
980
850HV
铸钢
ZG45
580
320
156~217HBS
ZG55
650
350
169~229HBS
灰铸铁
HT300
─
300
185~278HBS
HT350
202~304HBS
球墨铸铁
QT600-3
600
370
190~270HBS
QT700-2
420
225~305HBS
非金属
夹布胶木
100
25~35HBSv
1.2.5齿轮的技术要求
齿轮本身的制造精度,对整个机器的工作性能、承载能力及使用寿命都有很大的影响。
根据其使用条件,齿轮传动应满足以下几个方面的要求。
(1)传递运动准确性
我们要求齿轮能较准确地传递运动并使传动比恒定。
即要求齿轮在一转中的转角误差不超过一定范围。
(2)传递运动平稳性
我们要求齿轮传递运动平稳,以减小冲击、振动和噪声。
即要求限制齿轮转动时瞬时速比的变化。
(3)载荷分布均匀性
我们要求齿轮工作时,齿面接触要均匀,以使齿轮在传递动力时不致因载荷分布不匀而使接触应力过大,引起齿面过早磨损。
接触精度除了包括齿面接触均匀性以外,还包括接触面积和接触位置。
(4)传动侧隙的合理性
我们要求齿轮工作时,非工作齿面间留有一定的间隙,以贮存润滑油,补偿因温度、弹性变形所引起的尺寸变化和加工、装配时的一些误差。
由于齿轮的制造精度和齿侧间隙主要根据齿轮的用途和工作条件而定。
在实际运用中:
对于分度传动用的齿轮,主要要求齿轮的运动精度较高;
对于高速动力传动用齿轮,为了减少冲击和噪声,对工作平稳性精度有较高要求;
对于重载低速传动用的齿轮,则要求齿面有较高的接触精度,以保证齿轮不致过早磨损;
对于换向传动和读数机构用的齿轮,则应严格控制齿侧间隙,必要时,须消除间隙。
1.2.6齿轮毛坯
由于齿轮毛坯的选择取决于齿轮的材料、结构形式与尺寸、使用条件及生产批量等因素。
常用的齿轮毛坯有:
(1)下料件用于一些不重要,受力不大且尺寸较小,结构简单的齿轮。
(由于实际需求,本文使用的就是下料件)
(2)锻件用于重要而受力较大的齿轮。
(3)铸钢件用于直径大或结构形状复杂,不宜锻造的齿轮。
(4)铸铁件用于受力小,无冲击的开式传动的齿轮。
1.3影响齿轮工作平稳性的加工误差分析
1.3.1机械加工的阶段
由于齿轮的传动精度主要决定于齿形精度和齿距分布均匀性,而这与切齿时采用的定位基准(孔和端面)的精度有着直接的关系,所以,这个阶段主要是为下一阶段加工齿形准备精基准,使齿的内孔和端面的精度基本达到规定的技术要求。
在这个阶段中除了加工出基准外,对于齿形以外的次要表面的加工,也应尽量在这一阶段的后期加以完成。
1.3.2齿形的加工
对于不需要淬火的齿轮,一般来说这个阶段也就是齿轮的最后加工阶段,经过这个阶段就应当加工出完全符合图样要求的齿轮来。
对于需要淬硬的齿轮,必须在这个阶段中加工出能满足齿形的最后精加工所要求的齿形精度,所以这个阶段的加工是保证齿轮加工精度的关键阶段。
应予以特别注意。
1.3.3热处理阶段
在这个阶段中主要对齿面的淬火处理,使齿面达到规定的硬度要求。
我们在齿轮加工中根据不同的目的,安排两类热处理工序:
(1)毛坯热处理在齿坯加工前后安排预备热处理—正火或调质。
其主要目的是消除锻造及粗加工所引起的残余应力,改善材料的切削性能和提高综合力学性能。
(2)齿面热处理齿形加工完毕后,为提高齿面的硬度和耐磨性,常进行渗碳淬火,高频淬火,碳氮共渗和氮化处理等热处理工序。
1.3.4齿形的精加工阶段
这个阶段的目的,在于修正齿轮经过淬火后所引起的齿形变形,进一步提高齿形精度和降低表面粗糙度,使之达到最终的精度要求。
在这个阶段中首先应对定位基准面(孔和端面)进行修整,因淬火以后齿轮的内孔和端面均会产生变形,如果在淬火后直接采用这样的孔和端面作为基准进行齿形精加工,是很难达到齿轮精度的要求的。
以修整过的基准面定位进行齿形精加工,可以使定位准确可靠,余量分布也比较均匀,以便达到精加工的目的。
影响齿轮传动工作平稳性的主要因素是齿轮的齿形误差△ff和基节偏差△fpb。
齿形误差会引起每对齿轮啮合过程中传动比的瞬时变化;
基节偏差会引起一对齿过渡到另一对齿啮合时传动比的突变。
齿轮传动由于传动比瞬时变化和突变而产生噪声和振动,从而影响工作平稳性精度。
1.3.5加工误差分析
(1)齿形误差
从实际操作中,我们不难发现:
齿形误差主要是由于齿轮滚刀的制造刃磨误差及滚刀的安装误差等原因造成的,因此在滚刀的每一转中都会反映到齿面上。
常见的齿形误差有如图1-4所示的各种形式。
图a为齿面出棱、图b为齿形不对称、图c为齿形角误差、图d为齿面上的周期性误差、图e为齿轮根切。
由于齿轮的齿面偏离了正确的渐开线,使齿轮传动中瞬时传动比不稳定,影响齿轮的工作平稳性。
图1-4常见的齿轮误差
01.gif(25.32KB)
2008-1-2203:
22
(2)基节极限偏差滚齿时,齿轮的基节极限偏差主要受滚刀基节偏差的影响。
滚刀基节的计算式为:
pb0=pn0cosα0=pt0cosλ0cosα0≈pt0cosα0
式中:
pb0――滚刀基节;
pn0――滚刀法向齿距;
pt0――滚刀轴向齿距;
α0――滚刀法向齿形角;
λ0――滚刀分度圆螺旋升角,一般很小,因此cosλ0≈1。
由上式可见,为减少基节偏差,滚刀制造时应严格控制轴向齿距及齿形角误差,同时对影响齿形角误差和轴向齿距误差的刀齿前刀面的非径向性误差也要加以控制。
第二章直齿圆柱齿轮轴的工艺分析
2.1.1轴类零件加工的工艺路线
由于我们加工的是齿轮轴工件,因此,要对外圆进行加工。
外圆加工的基本加工路线可归纳为四条:
(1)粗车—半精车—精车
对于一般常用材料,这是外圆表面加工采用的最主要的工艺路线。
(2)粗车—半精车—粗磨—精磨
对于黑色金属材料,精度要求高和表面粗糙度值要求较小、零件需要淬硬时,其后续工序只能用磨削而采用的加工路线。
(3)粗车—半精车—精车—金刚石车
对于有色金属,用磨削加工通常不易得到所要求的表面粗糙度,因为有色金属一般比较软,容易堵塞沙粒间的空隙,因此其最终工序多用精车和金刚石车。
(4)粗车—半精—粗磨—精磨—光整加工
对于黑色金属材料的淬硬零件,精度要求高和表面粗糙度值要求很小,常用此加工路线。
2.2齿轮加工方法
为了便于我们了解齿轮加工,下面我们对齿轮加工的方法进行一个简单的探讨。
齿轮加工的关键是齿面加