发动机五大件加工工艺Word格式文档下载.docx
《发动机五大件加工工艺Word格式文档下载.docx》由会员分享,可在线阅读,更多相关《发动机五大件加工工艺Word格式文档下载.docx(13页珍藏版)》请在冰豆网上搜索。
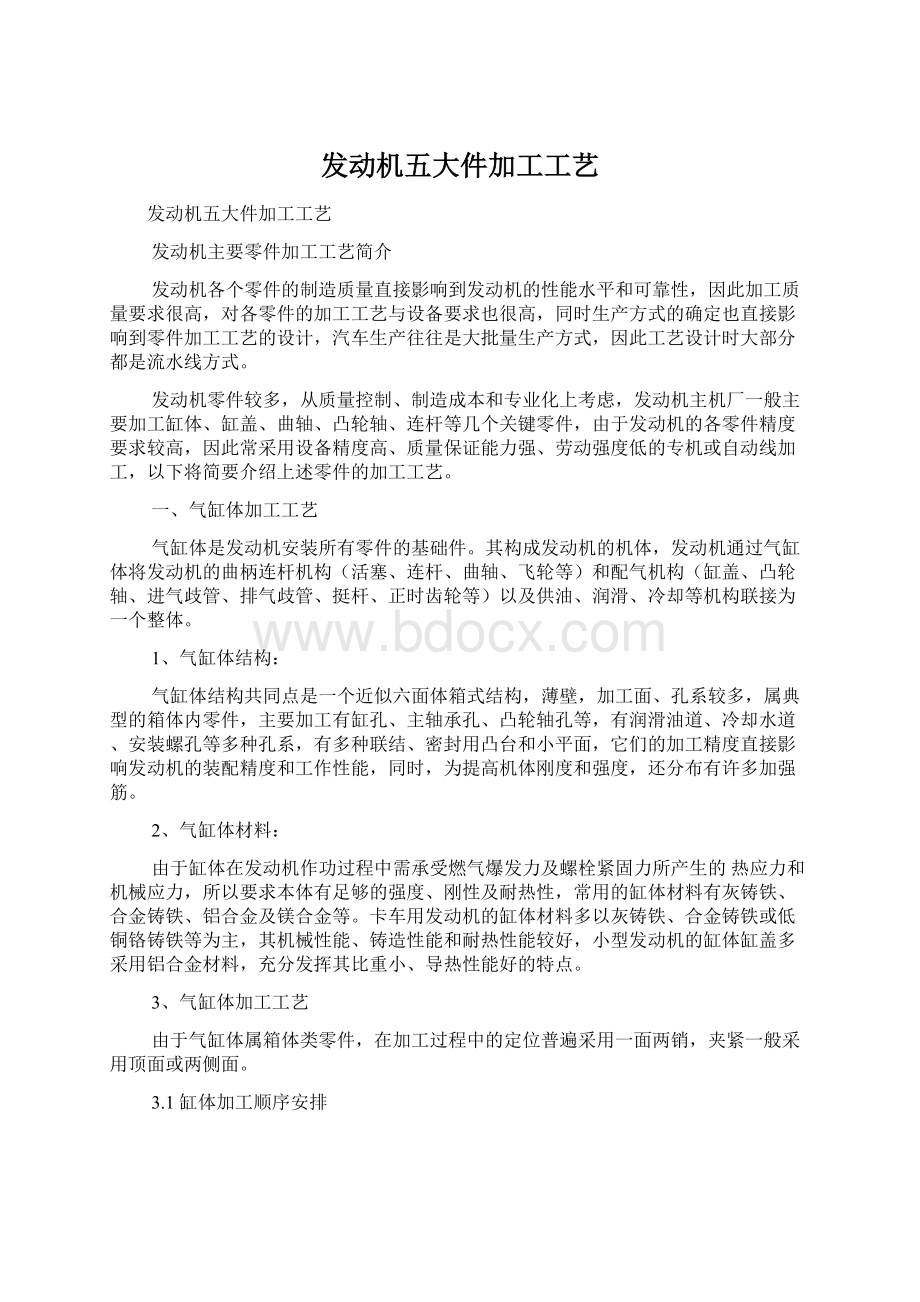
3.2主要工艺介绍
3.2.1缸孔加工:
采用粗镗、半精镗及精镗、珩磨方式加工。
主要工艺流程:
粗镗缸孔底孔→半精镗缸孔底孔→精镗缸孔底孔→压装缸套→精镗缸孔→粗珩缸孔→精珩缸孔
3.2.2主轴承孔的加工:
一般采用粗加工半圆孔,再与凸轮轴孔等组合精加工。
粗镗半圆孔→装配瓦盖→半精镗主轴承孔→精镗主轴承孔。
3.2.3凸轮轴孔的加工:
一般采用粗镗,再与主轴承孔等组合精加工。
粗镗/半精镗凸轮轴孔→精镗凸轮轴孔→压衬套。
3.2.4挺杆孔的加工:
一般采用钻、扩(镗)及铰孔的加工方式。
钻挺杆孔→扩挺杆孔→铰挺杆孔。
3.2.5主油道孔的加工:
传统的加工方法是采用麻花钻进行分级进给方式加工,其加工质量差、生产效率低,目前工艺常采用枪钻进行加工。
4、缸体主要加工工艺过程
工艺设计时主要根据设计纲领的大小、产品加工精度要求、工艺水平、生产成本等因素,考虑工艺设计和设备选型方案,各个缸体的结构略有不同,工艺设计也有不同,但工艺流程大致相同,主要工艺流程有以下内容:
序号
1
2
3
4
5
6
7
8
9
10
11
12
13
14
15
16
17
18
20
21
22
23
24
25毛坯上线、检查粗铣缸体前后端面粗铣缸体顶平面工序内容常用设备专机或加工中心专机或加工中心专机或加工中心专机或加工中心专机或加工中心专机或加工中心专机专机或加工中心专机或加工中心专机或加工中心专机或加工中心专机或加工中心粗铣缸体底平面、瓦盖结合面及止口面粗镗缸体曲轴半圆孔半精铣底平面、钻铰底面定位销及底面孔加工钻凸轮轴孔、主油道孔粗镗缸孔粗、精铣缸体两侧面前后端面孔系加工顶面水孔、缸盖定位销孔及深油孔加工缸体挺杆孔、缸盖紧固螺栓孔加工精铣底平面、瓦盖结合面,缸盖紧固螺栓孔及瓦盖螺栓孔加工零件中间清洗瓦盖装配凸轮轴孔,挺杆体定位销孔及前后端面销孔加工前后两端面精铣精镗主轴孔、第四主轴承止推面、凸轮轴孔精铣顶平面,精镗缸孔缸孔珩磨零件最终请洗缸体油道、水道密封试验压凸轮轴衬套总成检查及下线专机或加工中心专机或加工中心专机专机专机专机
在加工过程中,会根据零件姿态的变换需要增加翻转设备。
二、气缸盖加工工艺
1、气缸盖的结构及材料
气缸盖形状一般为六面体,系多孔薄壁件,其上有气门座孔、气门导管孔、各种光孔及螺纹孔、凸轮轴孔等。
汽油机缸盖有火花塞孔,柴油机缸盖有喷油器孔。
根据缸盖在一台发动机上的数量可分为整体式缸盖和分体式缸盖等。
只覆盖一个气缸的称为单体气缸盖,覆盖两个以上气缸的称为块状气缸盖(通常为两缸一盖,三缸一盖),覆盖全部气缸的称为整体气缸盖(通常为四缸一盖,六缸一盖)。
根据气缸盖上凸轮轴的个数可分为单顶置凸轮轴式(SOHC)、双顶置凸轮轴式(DOHC)气缸盖。
根据缸盖每缸的气门数量可分为如2气门、4气门等。
由于气缸盖在发动机作功过程中需承受燃气爆发力及螺栓紧固力所产生的热应力和机械应力,所以要求缸盖本体有足够的强度、刚性及耐热性,以保证在气缸体的压力和热应力的作用下能可靠地工作。
它与气缸垫的结合面应具有良好的密封性,其内部的进排气通道应使气体通过时流动阻力最小,还应冷却可靠,并保证安装在其上的零件能可靠地工作。
常用的缸盖材料有灰铸铁、合金铸铁、铝合金及镁合金等。
卡车用发动机的缸盖材料多以灰铸铁、合金铸铁或低铜铬铸铁等为主,其机械性能、铸造性能和耐热性能较好;
小型发动机的缸盖多采用铝合金材料,充分发挥其比重小、导热性能好的特点。
随着市场对高马力、高转矩、低废气排放以及降低燃料使用量等需求的持续增长,这迫使大功率柴油发动机需要不断提高点火峰压,使发动机的热负荷和机械负荷大幅度增加。
热负荷及机械负荷的同时升高,使目前使用的常规铸铁和合金铸铁发动机已达到或超过了其使用上限。
目前蠕铁已逐渐在发动机缸盖的铸造生产领域得到应用。
2、气缸盖的工艺安排
缸盖安排加工顺序时总的原则是:
先面后孔、先粗后精、先主后次、先基准后其他,大致过程是顶底平面、过渡定位基准加工→主定位基准加工→前后端面及两侧面加工→各面一般孔系加工→精铣底面→导管阀座底孔及精加工。
为避免底平面划伤,影响缸盖的密封性,保证导管阀座的加工精度,在
阀座导管底孔精加工工序之前将底平面精铣一次,若基准定位销反复定位使用后,有明显磨损,可考虑安排两套定位销或对原定位销再精铰一次。
导管阀座加工是整个缸盖工艺的重点,为保证产品质量,导管阀座的精加工一般采用专机,锥面加工采用车削工艺,小批量生产线主要采用加工中心完成导管阀座的粗精加工。
在所有机加工序完成后,设总成试漏工序,以保证缸盖无”漏水、漏气、漏油”等三漏问题。
导管阀座压装工序采用压力位移监控,保证压装质量。
为保证缸盖清洁度,应合理安排除毛刺,振动除屑、清洗等边缘工序。
3、缸盖加工的定位方式
3.1缸盖为典型的箱体类零件,其加工工艺复杂,加工精度高,定位方式一般为一面两销。
由于缸盖顶面与缸体无直接配合关系,缸盖顶面及该面上的两个定位销孔常用来作为过渡基准,缸盖底面(与缸体的接合面)及该面上的两个定位销孔作为主要定位基准。
3.2导管阀座的加工定位方式
精加工气门阀座工作锥面和导管孔时,多数是以与缸体的接合面和该平面
上的两个定位销孔进行定位。
这种曾被普遍应用的一面二销的定位方式,由于夹具定位销与阀座、导管孔之间的位置误差以及相邻阀座(和相邻导管孔)之间的位置误差均会造成加工余量的偏移,在最终精加工时,导致刚性差的铰刀也随之产生加工偏移,所以采用这种定位方式并非总能达到规定的精度。
另外一种定位方式为采用缸盖结合面平面和导管孔外圆进行定位。
采用这种定位方式,夹具的定位导套与机床主轴应保持很严的同轴度,以确保加工余量的均布。
这样,阀座和导管孔只需进行一次性加工就能达到规定的公差。
但是,缺点是在一个工位上只能加工一个阀座及导管孔。
与采用一面两销定位方式相比,生产率要低一些,也就是,在保持同样生产率的情况下,需要增加一定数量的加工工位,从而增加了生产线的长度。
4、缸盖的加工工艺简介
4.1主要加工工艺
缸盖的平面加工一般采用机夹密齿铣刀进行铣削加工,孔系一般采用摇臂钻床、组合机、加工中心等设别进行钻、扩、铰方式加工;
导管及阀座采用冷冻或常温压装方式进行压装,常温压装过程中一般采用位移—压力控制法对装配过程进行控制。
4.1.1缸盖底平面的加工
缸盖与缸体结合面的贴合质量将直接影响发动机质量,同时,此面通常作为缸盖加工的统一工艺基准。
因此,缸盖结合面的加工也是缸盖加工的关键工序。
根据加工精度的不同要求,缸盖底面的加工主要采用铣削,也有采用砂轮或砂带磨削的加工方法,磨削的速度高、精度高、毛刺少。
4.1.2气门座圈底孔和导管底孔的加工
气门座圈和导管与缸盖底孔为过盈配合,要求精度高,因此底孔加工质量很重要,压装压气门座圈和导管之前的底孔加工典型工艺方法是:
钻导管底孔→扩锪气门座圈底孔→镗或铰导管底孔→半精镗气门座圈底孔→镗气门座圈底孔、铰或枪铰导管底孔。
4.1.3气门座圈锥面和导管孔的加工
发动机工作时,由于可燃气体是在缸盖燃烧室压缩后进行点燃,致使气门阀座承受很高的热负荷和机械负荷。
这既要求阀座有很高的耐磨性,还要有很好的密封性。
如果阀杆工作时中心发生偏移除了会导致有害的热传导和阀杆及导管孔的很快磨损外,还会造成耗油量的增加。
因此,对气门阀座和导管孔的加工精度提出了很高的要求,特别是对气门阀座工作锥面与导管孔的相互间的同轴度规定了很严的公差。
压装气门座圈和导管之后的气门座圈锥面和导管孔加工,一般均采用精镗(车)或锪气门座锥面、枪铰导管孔。
导管阀座的加工刀具常采用一把专用刀具同时加工气门阀座和导管孔,有利于提高同轴度。
气门座圈的加工难点在于内孔的几何形状复杂,为了获得一个宽度恒定的工作锥面,特别是交线处的尺寸公差与位置公差更难控制,加工阀座的工作锥面,一般是采用锪削和车削两种成型工艺。
采用锪削加工时,由于阀座是淬硬材料(HRC50-58),刀刃的磨损较快,而这种刀刃磨损的轮廓会复制在密封锥面上,从而影响到阀座工作时的密封性。
但其优点是刀具的结构和刀具切削运动的控制较为简单。
用车削工艺加工阀座工作锥面可避免锪削时出现的缺陷。
4.1.4气缸盖总成试漏
气缸盖加工完成后,需对气道、水道、油道进行试漏,根据毛坯状况,也
可在中间增加试漏工序。
试漏时采用堵头将气道、水道、油道进行密封,然后充气,检测气压降低或泄漏量,判断是否有漏点。
试漏有干式和湿式试漏两种。
4.2气缸盖加工工艺过程
根据缸盖的结构、材料、产量、加工精度等要求,工艺过程设计也会有所不同,主要工艺过程有以下内容:
123456789101112
毛坯上线、检查
顶面定位基准及弹簧座面加工粗铣、半精铣进排气面粗铣、半精铣前后端面粗铣、半精铣顶底平面缸盖螺栓孔加工
进排气阀座底孔、导管底孔粗加工前后端面燃油道、回油孔加工前后端面和进气面及其孔系加工导管底孔和阀座底孔加工进、排气导管压装压装进、排气阀座
工序内容
常用设备
专机或加工中心专机或加工中心专机或加工中心专机或加工中心专机或加工中心专机或加工中心专机或加工中心专机或加工中心专机或加工中心专机或加工中心专机或加工中心
堵头
1314151617
顶平面及其孔系精加工底平面及其孔系精加工清洗总成试漏终检下线
专机或加工中心专机或加工中心
专机专机
三、曲轴加工工艺1、曲轴结构及材料:
曲轴属细长杆件,主要由主轴颈、连杆颈、油封轴颈、齿轮轴颈组成,在主轴颈、连杆颈上有油孔,两端有螺纹孔
油封轴颈
连杆轴颈
主轴颈
齿轮轴颈
油孔
根据发动机的结构,曲轴主要有直列和V型曲轴,上图为直列曲轴,主轴颈用于支撑整个曲轴,连杆颈与连杆相连,带动连杆活塞做上下往复运动
根据发动机的工作状况,曲轴常用材料有:
球墨铸铁、合金钢。
对于汽油机曲轴和小型柴油机曲轴,由于功率较小,曲轴毛坯一般采用球墨铸铁和优质碳素钢,常用材料有:
QT700-2、45钢等;
中、重型柴油机曲轴毛坯一般采用合金钢,常用材料有:
48MnV、35CrMo等。
曲轴是发动机中的重要零件,由于曲轴具有结构复杂、刚性差、技术要求高的特性,因此加工工艺难度大,而其加工质量又直接影响到发动机的技术性能和寿命,且曲轴属细长杆件零件,在加工中极易产生变形,这就需要在进行加工工艺设计时,根据曲轴的材料、技术要求、生产能力等要求,综合、全面考虑加工方案,
2、主要工艺介绍2.1中心孔的加工
曲轴的中心孔是曲轴加工过程的重要定位基准,曲轴常见的中心孔加工方式为几何中心孔和质量中心孔。
以曲轴毛坯轴颈的外圆定心来加工出的中心孔称为几何中心孔,以曲轴毛坯的旋转质量中心加工的中心孔称为质量中心孔。
由于几何中心孔的加工工艺简单、设备价格低,因此国内目前大多采用几何中心孔,但对毛坯质量差的曲轴的动平衡影响较大。
质量中心孔的加工是寻找出曲轴的质量中心线后,在曲轴两端加工出中心孔,使其两端加工出中心孔的轴线与曲轴的质量中心线重合。
采用质量中心孔定位加工曲轴的主要优点为:
减少曲轴动平衡时的去重量,提高动平衡的合格率,降低去重工序的加工节拍,改善曲轴内部质量补偿,但质量中心孔的设备价格昂贵,且设备大都需要进口。
2.2轴颈的粗加工
传统的加工工艺设计时,曲轴主轴颈及连杆轴颈的粗加工都采用多刀车削工艺,即同时使用多把刀具一次完成轴颈的粗加工。
曲轴车削机床采用多刀径向切削轴颈的方式,效率较高,但存在变形大、加工精度低、柔性差等缺点。
由于多刀车削受到加工精度低和柔性差的影响,已逐步被后来开发出的CNC车削、CNC外铣和CNC内铣、车-拉工艺所淘汰。
CNC曲轴内铣机床是70年代开发的曲轴加工新机床,内铣的加工方式是:
当装有硬质合金刀片的内铣刀盘高速旋转径向切入至轴颈尺寸后,刀盘环绕轴一周完成曲轴扇形面、轴颈、圆角、轴颈的铣削。
机床带有中心架,可在一次安装下,依次铣削出所有主轴颈、连杆颈,由于各轴移动均为数控,因此机床具有极大的柔性,适用于多品种生产,铣削过程中多个刀片参与切削,铣削力小,因而曲轴弯曲变形小,加工精度高。
内铣加工
2.3轴颈的精加工
曲轴是以两端孔定位的轴类零件,工件两端中心孔的几何形状、粗糙度的好坏在加工过程中都会影响到轴颈精加工的质量,而且在粗加工过程中,中心孔也会受到破坏,因此,曲轴在精磨之前往往都会增加一道工序,对粗加工后的中心孔进行修正,以提高磨削加工质量。
曲轴是发动机中的重要零件之一,技术要求也较高,其轴颈直径公差一般
为IT6级公差,轴颈表面粗糙度为Ra0.4~Ra0.2,因此为保证产品质量要求,曲轴在经过粗加工后,必须对所有轴颈进行磨削的精加工,以提高轴颈精度和降低表面粗糙度。
曲轴轴颈传统的磨削方法分半精磨和精磨两个阶段,但随着毛坯制造技术的发展和粗加工设备加工精度的提高,目前大多数曲轴加工厂已取消了半精磨工艺,这样可以缩短曲轴的加工流程,同时也降低了曲轴的生产成本。
曲轴磨削加工
普通外圆磨削方式适用于曲轴主轴颈的磨削加工,而无法实现连杆颈的加工,传统的连杆颈的加工常采用偏心夹具定位夹紧加工连杆颈,但这样设备的柔性较差,加工精度较差,目前随着机床制造技术的发展,连杆颈的磨削则采用跟踪磨削法。
跟踪磨削法是以主轴颈中心线为回转中心,一次装夹依次完成曲轴连杆颈的磨削加工(也可用于主轴颈磨削),磨削连杆轴颈的实现方式是通过CNC控制砂轮的进给和工件回转运动两轴联动,来完成曲轴加工进给。
跟
踪磨削法采用一次装夹、在一台数控磨床上依次完成曲轴主轴颈和连杆颈的磨削加工,能有效地减少设备费用,降低加工成本,提高加工精度和生产效率。
磨削完成后需对轴颈和圆角进行抛光,以降低轴颈的表面粗糙度,提高表面质量,曲轴抛光根据磨削表面质量以及产品要求,采用不同粒度的砂带进行抛光。
曲轴砂带抛光
2.4曲轴油孔加工
曲轴油孔一般孔径较小、深度较深,属深孔加工,因此加工难度较大,曲轴油孔加工最早采用摇臂钻加工,内壁质量较差,刀具寿命较低,工人劳动强度大,无法满足大批量加工需求,后逐渐被组合机代替,虽说可以满足大批量生产需求,但是设备柔性较差,刀具寿命也相对较低,目前已逐渐采用枪钻加工,枪钻用来加工深孔的深度一般可以做到枪钻直径的100倍以上,另外枪钻加工可以达到的精度很高,视不同的被加工材料和选用不同的切削用量可以一次加工出精度很高的孔。
枪钻2.4曲轴强化工艺
为提高曲轴的强度、增加表面耐磨性,曲轴一般需要对轴颈表面、圆角等处进行强化处理,常用的强化工艺有淬火、滚压、氮化等,由于淬火适应范围广、效率高、强化效果好,因此淬火成为目前主要的强化工艺。
感应淬火3、曲轴加工工艺过程
虽然曲轴的品种较多,结构上一些细节有所不同,
但加工工艺过程大致相
同。
序号1234567
铣端面打中心孔(毛坯厂加工)毛坯上线、检查车止推轴颈外圆粗磨止推轴颈外圆主轴颈粗加工两端轴颈粗加工连杆颈粗加工
常用设备专机专机或数控车外圆磨床专机或数控车专机或数控车万能设备配偏心夹具、专机、外铣或内铣机床
891011121314151617181920
油孔加工中间清洗热处理校直止推面磨削轴颈磨削
两端螺纹孔、定位销孔加工铣键槽动平衡探伤抛光清洗下线检查
万能设备或专机
清洗机专机或专用工装
专机专机专机专机或加工中心万能设备或专机
专机专机专机清洗机
在关键工序常配备专用量具对加工质量进行检测。
四、凸轮轴加工工艺1、凸轮轴结构及材料:
凸轮轴是发动机中配气机构中的重要部件,在发动机工作循环中,它合理地控制进排气门的开启、关闭时间和开合量,使经过压缩的燃油混合气充分燃烧,推动活塞运动做功,然后将废气排出燃烧室,因此它影响着发动机的动力性、经济性和排放。
凸轮轴属于细长轴类零件,刚性差、易变形,要准确控制发动机的进排气门定时开启和关闭,凸轮应具有很高的轮廓精度、相位角度要求和良好的耐磨性能及整体刚性。
因此,其轴颈和凸轮的加工成为整个凸轮轴加工工艺的重点,其加工多以车削、铣削和磨削工艺及表面强化(淬火、喷丸、氮化)等辅助工艺相结合。
凸轮轴常用材料有球墨铸铁、合金铸铁、冷激铸铁、中碳钢、合金钢等,球墨铸铁一般用于单缸凸轮轴,合金铸铁一般用于高速凸轮轴。
冷激铸铁取消热处理,节约能源,加工余量较小,常用于轿车发动机或汽油机凸轮轴。
对于少量生产或试制时,也可利用相应的棒料切削加工成型,但这样材料的利用率很低。
2、主要工艺介绍2.1主轴颈的加工
凸轮轴主轴颈的加工常采用车削、热处理、磨削、抛光的加工工艺,传统
粗加工多采用多刀车削工艺,但由于加工变形大、设备柔性差等问题,目前已逐步被CNC车削、外铣等加工方式所替代,磨削加工根据产量的大小,常采用多砂轮或单砂轮磨削。
CNC车削
2.2凸轮轴颈的加工
凸轮轴颈的形状似桃子,其形状设计目的是为了保证进、排气充分,而且气门在开、闭过程中不要产生过大的冲击,凸轮轴颈的形状直接影响发动机整机动力性能、燃油经济性和排放指标,因此凸轮轴中凸轮轴颈的加工至关重要。
凸轮轴颈的粗加工常用凸轮仿形车床车削加工或CNC铣削加工,精加工采用凸轮磨床进行磨削,传统磨削采用靠模方式磨削,目前随着数控技术的发展,以采用无靠模的CNC轨迹跟踪磨削,机床砂轮进给轴和工件旋转轴进行插补磨削方式,完全取消了机械靠模,从而具有良好的柔性、加工精度较高。
凸轮轴颈传统加工流程:
仿形多刀车→粗磨→淬火→半精磨、精磨→靠模砂带抛光,目前的加工流程:
CNC无靠模外铣机床铣削凸轮→淬火→CNC无靠模磨床CBN砂轮磨削凸轮→柔性抛光凸轮
3凸轮轴制造工艺的发展3.1快速点磨工艺
快速点磨工作原理:
采用宽度仅几毫米的CBN砂轮磨削,砂轮轴线和水平工件轴线之间倾斜而产生一个后角,这样砂轮与工件之间的接触区由线接触减小为点接触(实际上是一个很小的半椭圆面),由于磨削点四周的冷却性良好和采用了切削能力强的CBN砂轮得以实现高速高效磨削。
3.2组合式凸轮轴
目前,大部分发动机凸轮轴的加工都采用的是整体式凸轮轴,加工工艺流程较长,设备投资较大,因此,凸轮轴的制造工艺已向组合式凸轮轴发展。
组合式凸轮轴只需半精加工和精加工,凸轮、齿轮等可采用不同的材料,而且重量可减轻30%以上。
4、凸轮轴主要加工工艺过程
序号1234567891011
铣端面打中心孔粗车主轴颈凸轮轴颈粗加工热处理校直
粗磨轴颈、凸轮等精磨轴颈、凸轮等探伤抛光清洗下线检查
常用设备专机
万能设备或数控设备
专机、外铣专机专机外圆磨床或专机外圆磨床或专机
专机专机专机
五、连杆加工工艺1、连杆功用及结构
连杆是连接活塞与曲轴的动力功能件。
连杆小头通过活塞销与活塞相连,连杆大头与曲轴的连杆轴颈相连。
并把活塞承受的气体压力传给曲轴,使活塞的往复运动转变成曲轴的旋转运动。
连杆工作时,承受活塞顶部气体压力和惯性力的作用,而这些力的大小
和方向都是周期性变化的。
因此,连杆受到的是压缩、拉伸和弯曲等交变载荷。
这就要求连杆强度高,刚度大,重量轻,连杆常用材料有QT700-2、40MnV、38MnSiV35。
连杆结构分为三部分:
连杆小头、连杆杆身、连杆大头。
连杆组件的构成:
连杆体、连杆盖、螺栓与螺母、衬套。
连杆的结构类型通常按结合面结构形式分为两类:
平切口:
结合面与连杆杆身轴线垂直(见下图),通常用于汽油发动机。
斜切口:
结合面与连杆杆身轴线成一定夹角(见下图),通常用于柴油
发动机。
2、连杆工艺设计
连杆外形不规则而且较复杂,不易实现定位,大小头是细长的杆身连接,容易变形;
尺寸公差、形位公差,表面粗糙度等要求较高。
连杆的加工工序遵循先面后孔,先基准后其它的原则。
连杆是一个刚性比较差的零件,因此定位夹紧应减少变形对加工精度的影响。
连杆加工过程之中,大多数工序都是以大小头端面、大头孔或小头孔,以及零件图纸之中规定的工艺凸台为精基准的。
为保证大头孔与端面垂直,加工大小头孔时,