材料成型原理 复习题Word格式.docx
《材料成型原理 复习题Word格式.docx》由会员分享,可在线阅读,更多相关《材料成型原理 复习题Word格式.docx(32页珍藏版)》请在冰豆网上搜索。
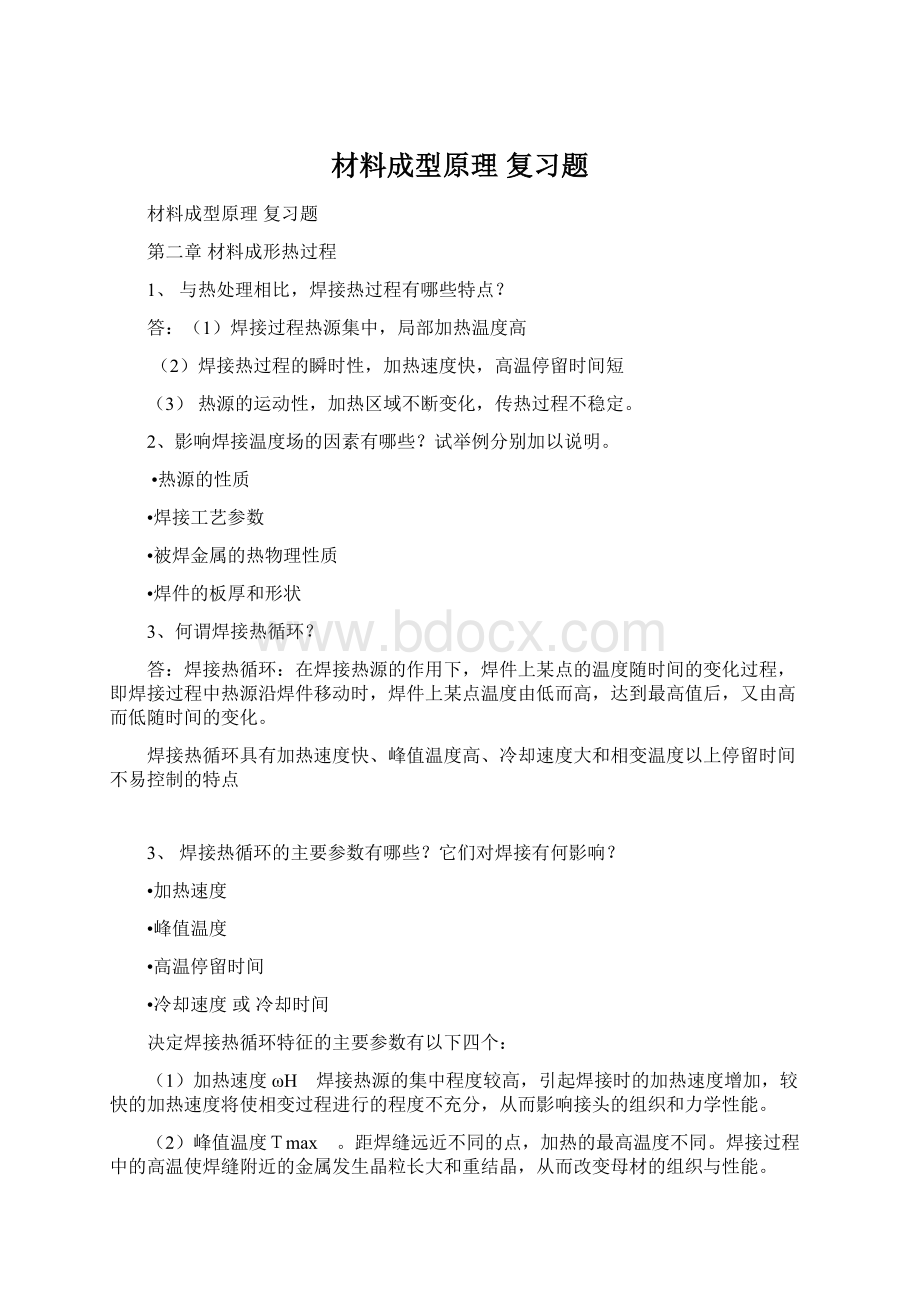
的含义是什么?
焊接热循环中的冷却时间
表示从800C冷却到500C的冷却时间。
焊接热循环中的冷却时间
表示从800C冷却到300C的冷却时间。
表示从峰值冷却到100C的冷却时间。
6、影响焊接热循环的因素有哪些?
试分别予以说明。
•焊接热输入的影响
•预热温度的影响
•焊件形状尺寸的影响
•接头形式的影响
•焊道长度的影响
•冷却条件的影响
8、已知某半无限大板状铸钢件的热物性参数为:
导热系数λ=46.5W/(m·
K),比热容C=460.5J/(kg·
K),密度ρ=7850kg/m3,取浇铸温度为1570℃,铸型的初始温度为20℃。
试求该铸件在砂型和金属型铸模(铸型壁均足够厚)中浇铸后0.2h时刻,铸型表面和距铸型表面0.1m处的温度并作分析比较。
(铸型的有关热物性参数见表2-2。
)
解:
(1)砂型:
=12965
=639
界面温度:
=1497℃
铸件的热扩散率:
=1.310-5m2/s
根据公式
分别计算出两种时刻铸件中的温度分布状况见表1。
表1铸件在砂型中凝固时的温度分布
与铸型表面距离(m)
0.02
0.04
0.06
0.08
0.10
温度
(℃)
t=0.02h时
1497
1523
1545
1559
1566
1569
t=0.20h时
1505
1513
1521
1528
1535
根据表1结果做出相应温度分布曲线见图1。
(2)金属型:
=15434
=727.6℃
同理可分别计算出两种时刻铸件中的温度分布状况见表2与图2。
表2铸件在金属型中凝固时的温度分布
727.6
1030
1277
1438
1520
1555
823
915
1005
1080
1159
图2铸件在金属型中凝固时的温度分布曲线
图1铸件在砂型中凝固时的温度分布曲线
(3)分析:
采用砂型时,铸件金属的冷却速度慢,温度梯度分布平坦,与铸型界面处的温度高,而采用金属铸型时相反。
原因在于砂型的蓄热系数b比金属铸型小得多。
9、凝固速度对铸件凝固组织、性能与凝固缺陷的产生有重要影响。
试分析可以通过哪些工艺措施来改变或控制凝固速度?
①改变铸件的浇注温度、浇铸方式与浇铸速度;
②选用适当的铸型材料和起始(预热)温度;
③在铸型中适当布置冷铁、冒口与浇口;
④在铸型型腔内表面涂敷适当厚度与性能的涂料。
10、比较同样体积大小的球状、块状、板状及杆状铸件凝固时间的长短。
一般在体积相同的情况下上述物体的表面积大小依次为:
A球<
A块<
A板<
A杆
根据
与
所以凝固时间依次为:
t球>
t块>
t板>
t杆。
11、右图为一灰铸铁底座铸件的断面形状,其厚度为30mm,利用“模数法”分析砂型铸造时底座的最后凝固部位,并估计凝固终了时间.
将底座分割成A、B、C、D四类规则几何体(见右下图)
查表2-3得:
K=0.72(
)
对A有:
RA=VA/AA=1.23cm
A=RA²
/KA²
=2.9min
对B有:
RB=VB/AB=1.33cm
B=RB²
/KB²
=3.4min
对C有:
RC=VC/AC=1.2cm
C=RC²
/KC²
=2.57min
对D有:
RD=VD/AD=1.26cm
D=RD²
/KD²
=3.06min
因此最后凝固部位为底座中肋B处,凝固终了时间为3.4分钟。
12、对于低碳钢薄板,采用钨极氩弧焊较容易实现单面焊双面成形(背面均匀焊透)。
采用同样焊接规范去焊同样厚度的不锈钢板或铝板会出现什么后果?
为什么?
采用同样焊接规范去焊同样厚度的不锈钢板可能会出现烧穿,这是因为不锈钢材料的导热性能比低碳钢差,电弧热无法及时散开的缘故;
相反,采用同样焊接规范去焊同样厚度的铝板可能会出现焊不透,这是因为铝材的导热能力优于低碳钢的缘故。
13、何谓焊接热循环?
焊接热循环的主要特征参数有那些?
14、焊接热循环对母材金属近缝区的组织、性能有何影响?
怎样利用热循环和其他工艺措施改善HAZ的组织性能?
(1)对组织的影响:
A不易淬火钢的热影响区组织:
在一般的熔焊条件下,不易淬火钢按照热影响区中不同部位加热的最高温度及组织特征,可分为以下四个区
1)熔合区:
焊缝与母材之间的过渡区域。
范围很窄,常常只有几个晶粒,具有明显的化学成分不均匀性。
2)过热区(粗晶区):
加热温度在固相线以下到晶粒开始急剧长大温度(约为1100℃左右)范围内的区域叫过热区。
由于金属处于过热的状态,奥氏体晶粒发生严重的粗化,冷却后得到粗大的组织,并极易出现脆性的魏氏组织。
3)相变重结晶区(正火区或细晶区):
该区的母材金属被加热到AC3至1100℃左右温度范围,其中铁素体和珠光体将发生重结晶,全部转变为奥氏体。
形成的奥氏体晶粒尺寸小于原铁素体和珠光体,然后在空气中冷却就会得到均匀而细小的珠光体和铁素体,相当于热处理时的正火组织,故亦称正火区。
4)不完全重结晶区:
焊接时处于AC1~AC3之间范围内的热影响区属于不完全重结晶区。
因为处于AC1~AC3范围内只有一部分组织发生了相变重结晶过程,成为晶粒细小的铁素体和珠光体,而另一部分是始终未能溶入奥氏体的剩余铁素体,由于未经重结晶仍保留粗大晶粒。
B易淬火钢的热影响区组织:
母材焊前是正火状态或退火状态,则焊后热影响区可分为:
1)完全淬火区:
焊接时热影响区处于AC3以上的区域。
在紧靠焊缝相当于低碳钢过热区的部位,由于晶粒严重粗化,得到粗大的马氏体;
相当于正火区的部位得到细小的马氏体。
2)不完全淬火区:
母材被加热到AC1~AC3温度之间的热影响区。
快速加热和冷却过程得到马氏体和铁素体的混合组织;
含碳量和合金元素含量不高或冷却速度较小时,其组织可能为索氏体或珠光体。
母材焊前是调质状态,则焊接热影响区的组织分布除上述两个外,还有一个回火软化区。
在回火区内组织和性能发生变化的程度决定于焊前调质的回火温度:
若焊前调质时回火温度为Tt,低于此温度的部位,组织性能不发生变化,高于此温度的部位,组织性能将发生变化,出现软化。
若焊前为淬火态,紧靠Ac1的部位得到回火索氏体,离焊缝较远的区域得到回火马氏体。
(2)对性能的影响
使HAZ发生硬化、脆化(粗晶脆化、析出脆化、组织转变脆化、热应变时效脆化、氢脆以及石墨脆化等)、韧化、软化等。
(3)改善HAZ组织性能的措施
1)母材焊后选择合理的热处理方法(调质、淬火等)。
2)选择合适的板厚、接头形式及焊接方法等。
3)控制焊接线能量、冷却速度和加热速度。
15、焊接条件下组织转变与热处理条件下组织转变有何不同?
焊接条件下热影响区的组织转变与热处理条件下的组织转变相比,其基本原理是相同的。
但由于焊接过程的特殊性,使焊接条件下的组织转变又具有与热处理不同的特点。
焊接热过程概括起来有以下六个特点:
(1)一般热处理时加热温度最高在AC3以上l00~200℃,而焊接时加热温度远超过AC3,在熔合线附近可达l350~l400℃。
(2)焊接时由于采用的热源强烈集中,故加热速度比热处理时要快得多,往往超过几十倍甚至几百倍。
(3)焊接时由于热循环的特点,在AC3以上保温的时间很短(一般手工电弧焊约为4~20s,埋弧焊时30~l00s),而在热处理时可以根据需要任意控制保温时间。
(4)在热处理时可以根据需要来控制冷却速度或在冷却过程中不同阶段进行保温。
然而在焊接时,一般都是在自然条件下连续冷却,个别情况下才进行焊后保温或焊后热处理。
(5)焊接加热的局部性和移动性将产生不均匀相变及应变;
而热处理过程一般不会出现。
(6)焊接过程中,在应力状态下进行组织转变;
而热处理过程不是很明显。
所以焊接条件下热影响区的组织转变必然有它本身的特殊性。
此外,焊接过程的快速加热,首先将使各种金属的相变温度比起等温转变时大有提高。
加热速度越快,不仅被焊金属的相变点AC1和AC3提高幅度增大,而且AC1和AC3之间的间隔也越大。
加热速度还影响奥氏体的形成过程,特别是对奥氏体的均质化过程有着重要的影响。
由于奥氏体的均质化过程属于扩散过程,因此加热速度快,相变点以上停留时间短,不利于扩散过程的进行,从而均质化的程度很差。
这一过程必然影响冷却过程的组织转变。
焊接过程属于非平衡热力学过程,在这种情况下,随着冷却速度增大,平衡状态图上各相变点和温度线均发生偏移。
在焊接连续冷却条件下,过冷奥氏体转变并不按平衡条件进行,如珠光体的成分,由w(C)0.8%而变成一个成分范围,形成伪共析组织。
此外,贝氏体、马氏体也都是处在非平衡条件下的组织,种类繁多。
这与焊接时快速加热、高温、连续冷却等因素有关。
16、在相同的条件下焊接45钢和40Cr钢,哪一种钢的近缝区淬硬倾向大?
在相同条件下,40Cr的淬硬大。
根据金属学原理可知,碳化物合金元素(如Cr、Mo、Ti、Nb等)只有他们充分溶解在奥氏体的内部才会增加奥氏体的稳定性(既增加淬硬倾向)。
在焊接条件下,由于速度快,高温停留时间短,导致这些合金元素不能充分溶解造成淬硬倾向。
不含碳化物合金元素的钢如45钢,不存在碳化物的溶解过程。
另一方面近缝区组织易粗化,相比较之下淬硬向要小于40Cr钢。
例如:
40Cr钢在36℃可得到100%的马氏体,而45*钢在60℃下也只得到98%的马氏体。
17、焊接热影响区的脆化类型有几种?
如何防止?
焊接热影响区的脆化类型及防止措施:
(1)粗晶脆化:
对于某些低合金高强钢,由于希望出现下贝氏体或低碳马氏体,可以适当降低焊接线能量和提高冷却速度,从而起到改善粗晶区韧性的作用,提高抗脆能力。
高碳低合金高强钢与此相反,提高冷却速度会促使生成孪晶马氏体,使脆性增大。
所以,应采用适当提高焊接线能量和降低冷却速度的工艺措施。
(2)析出脆化:
控制加热速度和冷却速度,加入一些合金元素阻止碳化物,氮化物等的析出。
(3)组织脆化:
控制冷却速度,中等的冷速才能形成M-A组元,冷速太快和太慢都不能产生M-A组元氏体(孪晶马氏体);
控制合金元素的含量,合金化程度较高时,奥氏体的稳定性较大,因而不易分解而形成M-A组元;
控制母材的含碳量,选用合适含碳量的材料。
(4)HAZ的热应变时效脆化(HSE):
焊接接头的HSE往往是静态应变时效和动态应变时效的综合作用的结果。
尽量使焊接接头无缺口,从而减轻动态应变时效脆化程度;
采用合适的冷作工序,静态应变时效脆化的程度取决于钢材在焊前所受到的预应变量以及轧制、弯曲、冲孔、剪切、校直、滚圆等冷作工序。
焊接工艺上控制加热速度和最高加热温度以及焊接线能量。
18、分述低碳钢焊接热影响区各区域的温度区间、组织及性能特点。
低碳钢属不易淬火钢,其焊接热影响区可分为熔合区,过热区,相变重结晶区和不完全重结晶区。
1)熔合区:
温度在固液相线之间,具有明显的化学成分不均匀性,导致组织、性能不均匀,影响焊接接头的强度、韧性,是焊热影响区性能最差的区域。
2)过热区:
温度为从固相线到晶粒急剧生长温度(约1100℃)之间。
因为存在很大的过热,该区奥氏体严重粗化,冷却后得到粗大组织,并且出现脆性的魏氏组织。
因此,塑、韧性很差。
3)相变重结晶区:
温度:
从晶粒急剧生长温度(1100℃)到AC3。
加热过程中,铁素体和珠光体全部发生重结晶转变为细小奥氏体。
冷却后得到均匀细小的铁素体和珠光体。
组织,成分均匀,塑、韧性极好。
类似于正火组织,亦称“正火区”。
是热影响区中组织性能最佳的区域。
4)不完全重结晶区:
AC1~AC3,在此温度范围内,只有一部分铁素体和珠光体发生了相变重结晶,冷却形成了细小的铁素体和珠光体;
而另一部分为未转变的原始铁素体,因此,晶粒大小不一,形成的组织不均匀,导致力学性能不均匀。
判断题:
1、与金属型比较,采用砂型铸件金属的冷却速度慢,温度梯度分布平坦,与铸型界面处的温度高。
()
2、低碳钢焊接熔合区,具有明显的化学成分不均匀性,导致组织、性能不均匀,影响焊接接头的强度、韧性,是焊热影响区性能最差的区域。
3、焊接热循环中的冷却时间
4、稳定温度场通常是指温度场内各点的温度不随时间而变的温度场。
5、同样体积大小相同的情况下,球状铸件的凝固时间大于块状铸件的凝固时间。
()
第3章金属的凝固
1、试述液态金属充型能力与流动性间的联系和区别,并分析合金成分及结晶潜热对充型能力的影响规律。
(1)液态金属充满铸型型腔,获得形状完整、轮廓清晰的铸件的能力,即液态金属充填铸型的能力,简称为液态金属充型能力。
液态金属本身的流动能力称为“流动性”,是液态金属的工艺性能之一。
液态金属的充型能力首先取决于金属本身的流动能力,同时又受外界条件,如铸型性质、浇注条件、铸件结构等因素的影响,是各种因素的综合反映。
在工程应用及研究中,通常,在相同的条件下(如相同的铸型性质、浇注系统,以及浇注时控制合金液相同过热度,等等)浇注各种合金的流动性试样,以试样的长度表示该合金的流动性,并以所测得的合金流动性表示合金的充型能力。
因此可以认为:
合金的流动性是在确定条件下的充型能力。
对于同一种合金,也可以用流动性试样研究各铸造工艺因素对其充型能力的影响。
(2)合金的化学成分决定了结晶温度范围,与流动性之间存在一定的规律。
一般而言,在流动性曲线上,对应着纯金属、共晶成分和金属间化合物之处流动性最好,流动性随着结晶温度范围的增大而下降,在结晶温度范围最大处流动性最差,也就是说充型能力随着结晶温度范围的增大而越来越差。
因为对于纯金属、共晶和金属间化合物成分的合金,在固定的凝固温度下,已凝固的固相层由表面逐步向内部推进,固相层内表面比较光滑,对液体的流动阻力小,合金液流动时间长,所以流动性好,充型能力强。
而具有宽结晶温度范围的合金在型腔中流动时,断面上存在着发达的树枝晶与未凝固的液体相混杂的两相区,金属液流动性不好,充型能力差。
(3)对于纯金属、共晶和金属间化合物成分的合金,在一般的浇注条件下,放出的潜热越多,凝固过程进行的越慢,流动性越好,充型能力越强;
而对于宽结晶温度范围的合金,由于潜热放出15~20%以后,晶粒就连成网络而停止流动,潜热对充型能力影响不大。
但也有例外的情况,由于Si晶体结晶潜热为α-Al的4倍以上,Al-Si合金由于潜热的影响,最好流动性并不在共晶成分处。
2、某飞机制造厂的一牌号Al-Mg合金(成分确定)机翼因铸造常出现“浇不足”缺陷而报废,如果你是该厂工程师,请问可采取哪些工艺措施来提高成品率?
机翼铸造常出现“浇不足”缺陷可能是由金属液的充型能力不足造成的,可采取以下工艺提高成品率:
(1)使用小蓄热系数的铸型来提高金属液的充型能力;
采用预热铸型,减小金属与铸型的温差,提高金属液充型能力。
(2)提高浇注温度,加大充型压头,可以提高金属液的充型能力。
(3)改善浇注系统,提高金属液的充型能力。
3、论述成分过冷与热过冷的涵义以及它们之间的区别和联系。
成分过冷的涵义:
合金在不平衡凝固时,使液固界面前沿的液相中形成溶质富集层,因富集层中各处的合金成分不同,具有不同的熔点,造成液固前沿的液相处于不同的过冷状态,这种由于液固界面前沿合金成分不同造成的过冷。
热过冷的涵义:
界面液相侧形成的负温度剃度,使得界面前方获得大于
的过冷度。
成分过冷与热过冷的区别:
热过冷是由于液体具有较大的过冷度时,在界面向前推移的情况下,结晶潜热的释放而产生的负温度梯度所形成的。
可出现在纯金属或合金的凝固过程中,一般都生成树枝晶。
成分过冷是由溶质富集所产生,只能出现在合金的凝固过程中,其产生的晶体形貌随成分过冷程度的不同而不同,当过冷程度增大时,固溶体生长方式由无成分过冷时的“平面晶”依次发展为:
胞状晶→柱状树枝晶→内部等轴晶(自由树枝晶)。
成分过冷与热过冷的联系:
对于合金凝固,当出现“热过冷”的影响时,必然受“成分过冷”的影响,而且后者往往更为重要。
即使液相一侧不出现负的温度梯度,由于溶质再分配引起界面前沿的溶质富集,从而导致平衡结晶温度的变化。
在负温梯下,合金的情况与纯金属相似,合金固溶体结晶易于出现树枝晶形貌。
4、何为成分过冷判据?
成分过冷的大小受哪些因素的影响?
答:
“成分过冷”判据为:
<
当“液相只有有限扩散”时,δN=∞,
,代入上式后得
(其中:
GL—液相中温度梯度
R—晶体生长速度
mL—液相线斜率
C0—原始成分浓度
DL—液相中溶质扩散系数
K0—平衡分配系数K)
成分过冷的大小主要受下列因素的影响:
1)液相中温度梯度GL,GL越小,越有利于成分过冷
2)晶体生长速度R,R越大,越有利于成分过冷
3)液相线斜率mL,mL越大,越有利于成分过冷
4)原始成分浓度C0,C0越高,越有利于成分过冷
5)液相中溶质扩散系数DL,DL越底,越有利于成分过冷
6)平衡分配系数K0,K0<1时,K0越小,越有利于成分过冷;
K0>1时,K0越大,越有利于成分过冷。
(注:
其中的GL和R为工艺因素,相对较易加以控制;
mL,C0,DL,K0,为材料因素,较难控制)
5、分别讨论“成分过冷”对单相固溶体及共晶凝固组织形貌的影响?
答:
“成分过冷”对单相固溶体组织形貌的影响:
随着“成分过冷”程度的增大,固溶体生长方式由无“成分过冷”时的“平面晶”依次发展为:
“成分过冷”对共晶凝固组织形貌的影响:
1)共晶成分的合金,在冷速较快时,不一定能得到100%的共晶组织,而是得到亚共晶或过共晶组织,甚至完全得不到共晶组织;
2)有些非共晶成分的合金在冷速较快时反而得到100%的共晶组织;
3)有些非共晶成分的合金,在一定的冷速下,既不出现100%的共晶组织,也不出现初晶+共晶的情况,而是出现“离异共晶”。
6、铸件典型宏观凝固组织是由哪几部分构成的,它们的形成机理如何?
铸件的宏观组织通常由激冷晶区、柱状晶区和内部等轴晶区所组成。
表面激冷区的形成:
当液态金属浇入温度较低的铸型中时,型壁附近熔体由于受到强烈的激冷作用,产生很大的过冷度而大量非均质生核。
这些晶核在过冷熔体中也以枝晶方式生长,由于其结晶潜热既可从型壁导出,也可向过冷熔体中散失,从而形成了无方向性的表面细等轴晶组织。
柱状晶区的形成:
在结晶过程中由于模壁温度的升高,在结晶前沿形成适当的过冷度,使表面细晶粒区继续长大(也可能直接从型壁处长出),又由于固-液界面处单向的散热条件(垂直于界面方向),处在凝固界面前沿的晶粒在垂直于型壁的单向热流的作用下,以表面细等轴晶凝固层某些晶粒为基底,呈枝晶状单向延伸生长,那些主干取向与热流方向相平行的枝晶优先向内伸展并抑制相邻枝晶的生长,在淘汰取向不利的晶体过程中,发展成柱状晶组织。
内部等轴晶的形成:
内部等轴晶区的形成是由于熔体内部晶核自由生长的结果。
随着柱状晶的发展,熔体温度降到足够低,再加之金属中杂质等因素的作用,满足了形核时的过冷度要求,于是在整个液体中开始形核。
同时由于散热失去了方向性,晶体在各个方向上的长大速度是相等的,因此长成了等轴晶。
7、试分析溶质再分配对游离晶粒的形成及晶粒细化的影响。
答:
对于纯金属在冷却结晶时候没有溶质再分配,所以在其沿型壁方向晶体迅速长大,晶体与晶体之间很快能够连接起来形成凝固壳。
当形成一个整体的凝固壳时,结晶体再从型壁处游离出来就很困难了。
但是如果向金属中添加溶质,则在晶体与型壁的交汇处将会形成溶质偏析,溶质的偏析容易使晶体在与型壁的交会处产生“脖颈”,具有“脖颈”的晶体不易于沿型壁方向与其相邻晶体连接形成凝固壳,另一方面,在浇注过程和凝固初期存在的对流容易冲断“脖颈”,使晶体脱落并游离出去,形成游离晶。
一些游离晶被保留下来并发生晶体增殖,成为等轴晶的核心,形成等轴晶,从而起到细化晶粒的作用。
8、液态金属中的流动是如何产生的,流动对内部等轴晶的形成及细化有何影响?
浇注完毕后,凝固开始阶段,在型壁处形成的晶体,由于其密度或大于母液或小于母液会产生对流,此外型壁处和铸件心部的熔体温度差也可造成对流,从而使熔体流动。
依靠熔体的流动可将型壁处产生的晶体脱落且游离到铸件的内部,并发生增殖,从而为形成等轴晶提供核心,有利于等轴晶的形成,并细化组织。
9、试分析影响铸件宏观凝固组织的因素,列举获得细等轴晶的常用方法。
铸件的三个晶区的形成是相互联系相互制约的,稳定凝固壳层的形成决定着表面细晶区向柱状晶区的过度,而阻止柱状晶区的进一步发展的关键则是中心等轴晶区的形成,因此凡能强化熔体独立生核,促进晶粒游离,以及有助于游离晶的残存与增殖的各种因素都将抑制柱状晶区的形成和发展,从而扩大等轴晶区的范围,并细化等轴晶组织。
细化等轴晶的常用方法:
(1)合理的浇注工艺:
合理降低浇注温度是减少