油底壳模具设计Word文档下载推荐.docx
《油底壳模具设计Word文档下载推荐.docx》由会员分享,可在线阅读,更多相关《油底壳模具设计Word文档下载推荐.docx(18页珍藏版)》请在冰豆网上搜索。
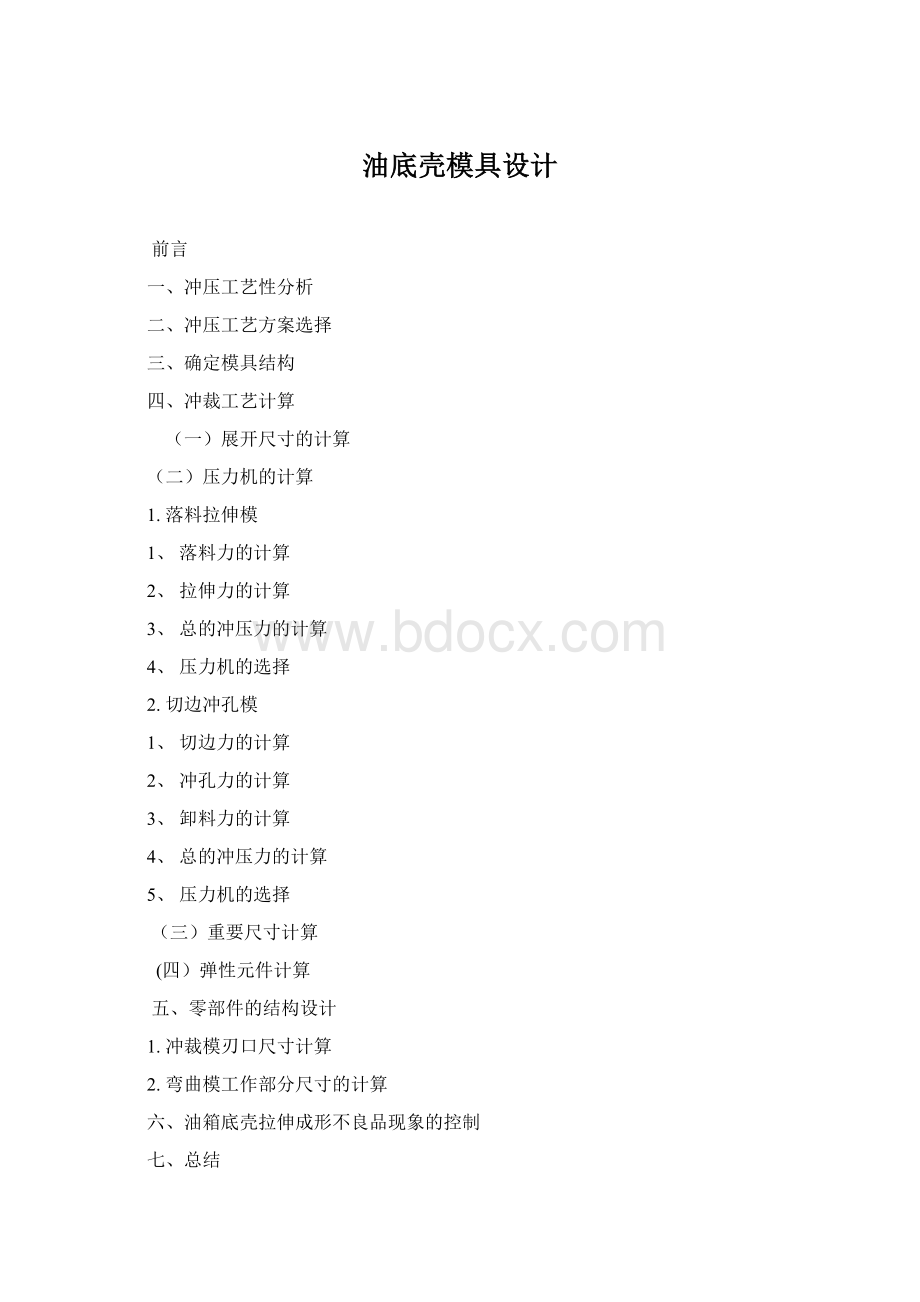
采用模具CAD/CAM技术,还可提高模具质量,大大减少设计和制造人员的重复劳动,使设计者有可能把精力用在创新和开发上。
尤其是pro/E和UG等软件的应用更进一步推动了模具产业的发展。
。
数控技术的发展使模具工作零件的加工趋进于自动化。
电火花和线切割技术的广泛应用也对模具行业起到了飞越发展。
模具的标准化程度在国内外现在也比较明显。
特别是对一些通用件的使用应用的越来越多。
其大大的提高了它们的互换性。
加强了各个地区的合作。
对整个模具的行业水平的提高也起到了重要的作用。
随着冲压技术的广泛应用和发展,各个工业部门几乎都离不开冲模,尤其是汽车、电器、电机、仪表和日用品工业,其产品质量、生产效率、生产成本及产品更新换代的快慢等,都在很到程度上取决于模具。
因此,模具工业是带动各项工业产品发展的先行工业。
如何提供更好、更快、更多的模具,是模具工作者共同的重要课题。
冲模结构是冲模的灵魂。
它不仅决定了模具的功能,同时也决定了模具的成本和制造周期。
一副好的冲模结构,往往凝聚着许多人的智慧和汗水。
因此可以说,冲模结构是冲模设计师智慧的结晶。
模具是成型不同形状制品的一种装置。
按照制品所采用的原料不同,成形的方法也不同;
一般将其分为金属冲压模具,金属压铸模具,塑料模具,橡胶模具,玻璃模具等。
模具在汽车行业,飞机行业,家用电器行业,工程机械、冶金、机床等制造行业中有着极其重要的作用;
采用模具生产的毛坯或产品零件,是材料成型的重要形式,模具生产和切削相比具有材料利用率高,能耗低,产品性能好,生产效率高和成本低等显著特点。
从20世纪80年代开始,工业发达国家的模具行业,已从机床工业中分离出来,并发展成为一种独立的工业部门,其产值已超过了机床工业的产值。
改革开放以来,我国的模具工业发展十分迅速,近年来,一直每年以15%左右的速度快速发展,在高校中也专门设置了专门的模具专业,培养出了大批的高级技术人才。
我所设计的是油底壳模具,属于金属冲压模具,产品是经过冷冲压得到的。
冷冲压是利用安装在压力机上的冲模对材料施加压力,使其产生分离或塑性变形,从而获得所需要零件的一种压力加工方法。
因为它通常是在室温下进行加工,所以称为冷冲压。
冷冲压不但可以加工金属材料,还可以加工非金属材料和复合材料。
冷冲压与其它加工方法相比,具有独到的特点,如冲压设备操作简便,所得产品尺寸稳定、互换性好等,所以在工业生产中应用十分广泛。
通过冲压加工,大大提高了生产效率,降低了成本。
可以说,如果在生产中不广泛采用冲压加工工艺,许多工业部门的产品要提高生产率、提高质量、降低成本,进行产品的更新换代是难以实现的。
冲模是实现冲压生产的基本条件。
它是将材料加工成所需冲件的一种工艺设备。
冲模在冷冲压中至关重要,一般来说,不具备符合要求的冲模,冷冲压就无
法进行;
先进的冲压工艺也必须依靠相应的冲模来实现。
性能良好的冲压设备是提高冲压生产技术水平的基本条件。
模具的标准化和专业化生产,已得到模具行业的广泛重视。
这是由于模具标准化是组织模具行业专业化生产的前提,而模具的专业化生产是提高模具质量、缩短模具制造周期、降低成本的关键。
我国已经颁布了冷冲压术语、冷冲模零部件的国家标准。
冲模的模架等基础零部件已专业化、商品化。
但总的来说,我国冲模的标准化和专业化水平还是比较低的,先进国家标准化已达70%--80%。
在模具材料及热处理、模具表面处理等方面,国内外都进行了不少研制工作,并取得了良好的实际效果,冲模材料的发展方向是研制高强韧性冷作模具钢,如65Nb、LD1、CG2等就是我国研制的性能优良的冲模材料。
冷冲压加工的零件,由于其形状、尺寸、精度要求、生产批量等各不相同,因此生产中所采用的冷冲压工艺方法也是多种多样的,概括起来可分为两大类,即分离工序和成形工序。
在实际生产中,一般采用组合工序,即把两个以上的单独工序组成一道工序,构成所谓复合、级进、复合—级进的组合工序。
本设计就是多工位级进模的设计。
在设计中,深刻的体会到了自己知识的有限,得到了身边同学的热情帮助,尤其是知道老师的大力帮助下才能完成此次毕业设计,在此表示衷心感谢!
本次设计中存在多处不足之处,恳请各位老师指正。
产品图如下图工件
名称:
无阶梯油底壳
材料:
08
板厚:
t=1mm
生产批量:
大批量;
一、
冲裁工艺分析:
在工艺性分析的基础上,列出各种可能的冲压工艺方案,包括工序性质,工序数目,工序顺序及组合方式等,并对各种可能工艺方案从产品质量,生产效率,模具制造成本,安全性,经济性等方面进行综合分析论证,选出最佳冲压工艺方案。
此次设计的产品为冲压件,材料为08钢板,优质碳素结构钢,具有良好的可冲裁性能,冲裁件结构简单,内、外行无尖锐清角,零件表面粗糙度无特殊要求,零件图上所有尺寸均未标注公差,属于自由尺寸,可以按IT14级确定工件的公差。
另外,在设计中还应该考虑到不锈钢材料的冲裁工艺性,以及其纤维方向的特性。
由相关资料知:
在不锈钢中加入Ni可明显降低刚的冷加工硬化倾向,其原因是可使奥氏体的稳定性增加,减少和消除了冷加工过程中的马氏体转变,降低了冷加工硬化速率,强度降低和塑性提高。
当刚中有足够的铬时,在刚的表面易形成非常薄的致密的氧化膜,它可以防止刚进一步的氧化或腐蚀。
氧化性的环境可以强化这种膜,而还原性环境会破坏这种膜。
故该中材料制作的零件要特别注意它的使用环境,以增加其使用寿命。
另:
用作压力工的钢材,表面不得有肉眼可见的裂缝、折迭、结疤及夹杂,如有必须清除,清除深度从钢材实际尺寸算起应符合有关规定。
结论:
适合于大批量生产。
二、冲裁工艺的选择:
1.毛坯尺寸的计算:
此工件为形状简单的旋转体拉伸件,在计算毛坯直径时,可先将拉伸件划分成若干个简单的集合形状,分别求个部分的面积相加,按照拉伸前后毛坯与工件表面积相等的原则计算,也可以根据经验公式计算。
根据此方案,计算出工件的毛坯尺寸为99.02,取整数100。
此尺寸在实际生产中,根据材料的实际变形情况还需要进行调节。
2.拉伸系数的计算:
拉伸系数的计算分无凸缘圆桶件和有凸缘圆桶件两中。
本次设计的零件是有凸缘的旋转体拉伸件。
有凸缘拉伸件拉伸次数的计算,可根据拉伸的最大相对高度来比较,查表
结合此工件,查表格,确定此工件采用一次拉伸即能成型,保证尺寸。
根据制件工艺性分析,其基本工序有落料、冲孔、拉伸三种。
冲裁结构的工艺性:
(1)冲裁件的形状应能符合材料的合理排样,减少废料。
(2)冲裁件各直线或曲线的连接处,宜有适当的圆角。
本设计采用的是少废料的排样方式、且模具采用镶拼结构,所以各连接处可以无圆角。
(3)冲裁件凸出或凹入部分宽度不宜太小,并应避免过长的悬臂与狭槽。
(4)冲孔时,由于受到凸模强度的限制,孔的尺寸不宜过小,其数值与孔的形状、材料的机械性能、材料的厚度有关系。
(5)裁件的孔与孔之间、孔与边缘之间的距离a受模具强度和冲裁件质量的限制,其值不宜过小。
本设计中a的值均较小,以至使得模具的结构比较复杂,并在一定程度上影响到模具的使用寿命。
(6)冲裁件的精度和毛刺:
精度等级按查有关资料取IT8,毛刺高度为30~50
m。
由制件零件图资料可以知道:
制件冲裁工艺满足以上要求,采用精密冲裁时的模具结构复杂,而且模具寿命较低,故本设计中的冲裁采用普通冲裁。
弯曲结构的工艺性:
(1)弯曲件的圆角半径不宜小于最小弯曲半径,以免产生裂纹,但也不宜过大,因为过大时,会受到回弹的影响,弯曲角度与圆角半径的精度不宜保证。
弯曲半径是指冲件受压弯曲处的内半径。
最小弯曲半径是指能成功地进行弯曲的最小弯曲半径。
各种材料的最小弯曲半径都可以在相关资料上查得。
(2)弯曲件的弯边长度不宜过小,其值应为h>
R+2t,当h较小时,弯边在模具上支持的长度过小,不易得到形状标准的零件。
该设计零件h值都符合要求。
计算见后。
(3)对称弯曲件,左右弯曲半径应一致,一保证弯曲过程中受力平衡,防止滑动。
该设计零件的弯曲都是对称弯曲。
(4)弯曲件的精度:
弯曲件的精度与很多因素有关,如弯曲件材料的机械性能和材料的厚度、模具结构和模具精度、工序的多少和工序的先后顺序等等。
精度要求较高的弯曲件必须严格控制材料厚度公差。
在该设计中所选材料的厚度为标准厚度,故与料厚公差无关,所以选精度等级为精密级IT11。
制件弯曲工艺满足以上要求。
由于制件材料是不锈钢材料,具有良好的弯曲工艺性,在设计中应该考虑到其纤维方向,以利于模具的设计与制造,弯曲时折弯线的方向不能够与带料的纤维方向一致,应该垂直带料的纤维方向或者与其纤维方向成一定的角度,最好的角度为成45度。
按其先后顺序组合,可得如下三种方案:
1、先落料、再拉伸,切边和冲孔,采用单工序模具生产。
2、落料拉伸复合模具,和切边冲孔复合模具。
3、先落料冲孔,再拉伸,然后切边,
方案一模具结构,但是需要四到工序,生产成本高,生产效率低,只能满足小批量生产。
方案二模具结构也简单,适用于精度要求不是很高的产品。
方案三也需要三付模具,生产效率没有提高,操作方便。
但最终的产品精度难保证。
综上分析,冲裁件的尺寸精度要求不高,形状不大。
根据材料厚度(1.0mm),又通过以上3个方案的比较,采用方案2,可采用弹性卸料装置、倒装的落料拉伸复合模结构形式,和倒装的切边冲孔模。
三、确定模具结构:
根据确定的工艺方案,冲压件的形状特点,精度要求,生产批量,模具的制造和维修条件,操作的方便与安全性要求以及利用和实现机械化自动化的可能性等确定选用复合模。
切边冲孔模具总图如下图所示:
1、产品展开尺寸的计算:
公式是D=d4×
d4+4d2H-3.44rd2,然后开根号
经过实际计算D=99.8
取整数为100。
此尺寸目前是待定,在实际生产时需调节。
展开图为φ100的圆。
加上切边余量,此尺寸应放到105
2.板料确定
1)板料宽度:
B=(D1+2a1)-
=(105+2×
2.5)-
mm
=110-
查表得:
△=0.7
2)条料长度取1600mm
3)步距:
S=(D2+a)
=105+2
=107mm
4)钢板选择:
规格为1×
1600×
2600的钢板
5)材料利用率:
经排样计算为68.8%,计算过程略
5.冲压机计算
(一)初步确定压力机的型号:
1、落料拉伸模压力机的选择
落料:
F落=L+δb
=329.7×
1×
380
=125286N
=125.86KN
L—工件的周边长度
t—板料厚度
δb—材料的强度极限
δb查表=294~432,取380
卸料力:
F卸=K×
F落
=0.05×
125.86
=6.26KN
K值查表取0.05
拉伸力:
FL=πd1tσbκ1
式中,FL——拉伸力;
d1——拉伸件直径,根据料厚中线计算
t——材料厚度;
σb——材料抗拉强度。
κ1——系数
计算拉伸力:
FL=πd1tσbκ1(查表τ=350MPaK取1.3)
=3.14×
60×
350/1000KN
=65.94KN
2)总力:
F总=F拉伸+F落+F卸
=65.94+125.86+6.26
=198.06KN
3)初步确定压力机的型号:
F公称≥F总
因此选择压力机的型号为:
JC23—35
2、切边冲孔模压力机的选择
1)切边:
F切边=L+δb
=251.2×
=95456N
=95.456KN
95.456
=4.77KN
冲孔:
F孔1=Ltδb
=18.84×
=7159.2N
=7.2KN
L—孔的周边长度
t—板料厚度
δb—材料的强度极限
F总=F切边+F冲孔+F卸
=95.456+7.2+4.77
=107.426KN
JC23—35
3、型号为JC23—35压力机的基本参数如:
(表一)
公称压力/KN
350
垫板尺寸/mm
厚度60
滑块行程/KM
80
直径150
滑块行程次数/(次/min)
50
模柄孔尺寸/mm
直径50
深度70
最大封闭高度/mm
280
滑块底面积尺寸/mm
前后190
封闭高度调节量
60
左右210
滑块中心线至床身距离/mm
205
床身最大可倾角
20°
立柱距离/mm
300
工作台尺寸/mm
前后380
左右610
工作台孔尺寸
前后200
左右290
直径260
表一
(二).刃口尺寸计算:
1、落料拉伸模:
落料凹模:
D=(Dmax-x△)+
=(105-0.5×
0.62)+0.022=104.69+0.022mm
X查表:
尺寸精度为IT14级;
x=0.5
落料凸模:
d=(D-Zmin)-
=(104.69-0.246)-0.02=104.426-0.02mm
拉伸凸、凹模尺寸计算如下表:
拉伸
工作尺寸
计算公式
凹模尺寸注法
凹模
φ60+0.200
凹模计算:
Dd=(d+0.4△+z)+δd0
注:
δd=0.25△
φ60+0.050
凸模
凸模计算:
Dp=(d+0.4△)0-δp
δp=0.25△
φ580-0.05
2、切边冲孔模
切边凹模:
=(80-0.5×
0.62)+0.022=79.69+0.022mm
=(79.69-0.246)-0.02=79.426-0.02mm
冲孔凸模:
d=(dmin+x△)-
=(6+0.5×
0.43)ˉ0.011
=6.215ˉ0.011mm
冲孔凹模:
D=(4.215+Zmin)+
=(6.215+0.246)+
=6.461+
查表得Zmin=0.246
(三).弹性元件计算
弹性元件选用聚氨酯橡胶
1)自由高度:
H=h工件行程/Єi-Єy
=(18)/(35﹪~45﹪)-(10﹪~15﹪)
=60~90
取H=80
查表:
Єi=35﹪~45﹪;
Єy=10﹪~15﹪;
q=0.26
hm=产品拉身高度;
hm=18,
2)橡胶装模高度:
H装=H+H预
=80+18
=98mm
五.零部件设计
5.1冲裁模刃口尺寸计算
5.1.1尺寸计算原则
模具刃口尺寸精度是影响冲裁件尺寸精度的首要因素,模具的合理间隙值也要靠模具刃口尺寸及其公差来保证。
在决定模具刃口尺寸及其制造公差时,需考虑如下原则:
(1)落料制件尺寸由凹模尺寸决定,冲孔时孔的尺寸又凸模决定。
故设计落料模时,以凹模为基准,间隙取在凸模上;
设计冲孔模时,以凸模为基准,间隙取在凹模上。
(2)考虑到冲裁中凸、凹模的磨损,设计落料模时,凹模基本尺寸应取工件尺寸公差范围内的较小尺寸;
设计冲孔模时,凸模基本尺寸则应取工件的尺寸公差范围内的较大尺寸。
这样,凸、凹模虽磨损到一定程度,仍能冲出合格零件。
(3)由于凸、凹模均要冲裁件或废料发生摩擦,从而导致磨具磨损,凸模愈磨愈小,凹模愈磨愈大,结果使模具间隙愈用愈大,因此在设计新模具时,凸、凹模间隙应取最小合理间隙。
(4)确定凸、凹模制造公差时,应考虑到制件的精度要求。
如果对凸、凹模刃口精度要求过高(即制造公差过小)会使模具制造困难,增加成本,延长生产周期;
如果精度要求过低,(即制造公差过大),则生产出来的零件可能不合格,或使模具寿命低。
零件精度与模具精度的关系可查相关资料得到。
本设计中材料厚度为0.25mm,小与0.5mm,故取冲裁见精度为IT8,模具精度(标准公差等级)为IT6。
5.1.2尺寸的计算方法
由于模具加工和测量方法的不同,凹模和凸模刃口部分尺寸的计算公式与制造公差的标注也不同,基本上可以分为两类:
凸模和凹模分开加工与凸模和凹模配合加工。
由于本设计中的制件的材料属于薄料,为了保证凸、凹模间一定的间隙值必须采用配合加工。
凸模和凹模配合加工的方法是先做好其中的一件(凸模或凹模)作为基准件,然后以次为基准来加工另一件,使它们之间保持一定的间隙。
对于落料先做凹模,并以它作为基准配做凸模;
对于冲孔,先做凸模,并以它作为基准配做凹模。
因此只需在基准件上标注尺寸和制造公差,另一件只标注基本尺寸并注明配做所留间隙值,这样凸模极限下偏差和凹模极限上偏差不在受间隙限制。
这种方法不仅容易保证凸、凹模间隙很小,而且还可放大基准件的制造公差,使制造容易。
目前一般工厂都采用此种方法。
使用此种方法时,只需计算出基准件的刃口尺寸,配制件上只需标注基本尺寸,不标注偏差,同时要在图样技术要求上注明:
配制件刃口尺寸按基准件实际尺寸配制,保证双面间隙值为
5.1.3凸、凹模刃口尺寸的计算
在冲孔时,应以凸模为基准件,凸模磨损后尺寸变小,可按下式计算:
在落料时,应以凹模为基准件,凹模磨损后尺寸变大,按下式计算:
式中
—基准件尺寸(mm);
—相应的工件极限尺寸(mm);
—系数,查资料取值;
在本设计中取0.75或1。
—工件公差(mm);
—基准件极限偏差(mm)。
在本设计中取
凹模刃口尺寸按凸模刃口实际尺寸配制,保证双面间隙值为
=0.021~0.027mm。
由于本设计中有10多个冲裁工序,详细计算过程记录比较繁琐,故只记录计算结果。
各个冲裁凸模刃口尺寸详细见零件图。
5.2弯曲模工作部分尺寸的计算
弯曲模工作部分的尺寸主要是指凸模、凹模的圆角半径和凹模的深度。
对U形件的弯曲模则还有凸、凹模之间的单边间隙模具横向尺寸等。
5.2.1凸、凹模的圆角半径
(1)凸模圆角半径r当r/t较小时,凸模圆角半径即等于弯曲件的内弯半径r,但不应小于弯曲件材料许可的最小圆角半径
弯曲半径是指冲件材料受压弯曲处的内半径。
最小弯曲半径指能成功的进行弯曲的最小弯曲半径。
不同的材料,最小弯曲半径也不相同。
均可在相关资料上查得。
1Cr18Ni9的最小弯曲半径根据硬化程度不同最小弯曲半径也不相同。
本设计选取该材料的最小弯曲半径为0.5t,即0.5×
0.25=0.125mm。
(2)凹模圆角半径r实际生产中,凹模圆角半径通常根据材料的厚度t选取,当t<
2mm时,r=(3~6)t;
当t=2~4mm时,r=(2~3)t;
当t>
4mm时,r=2t。
凹模圆角半径不能选取过小,以免材料表面擦伤,甚至出现压痕。
熬磨两边的圆角半径应一致,否则在弯曲时毛坯会发生偏移。
在设计中选用最小弯曲半径为4t=4×
0.25=1mm。
V形件弯曲凹模的底部可开退刀槽或取圆角半径
—凹模底部圆角半径(mm);
—凸模圆角半径(mm);
t—弯曲件材料厚度(mm)。
5.2.2凹模深度
弯曲凹模深度要适当,若过小,则工件两端的自由部分太多,弯曲件回弹大,不平直,影响零件质量;
若过大,则多消耗模具钢材,需较大的压力机行程。
弯曲V形件时,凹模深度及底部最小厚度的取值可查资料得到,但是由于本设计中的制件的尺寸较小,故深度可取制件的实际尺寸,厚度取凹模的高度。
弯曲U形件时,若弯边高度不大或要求两边平直,则凹模深度应大于工件的高度。
5.2.3凸、凹模间隙
弯曲V形件时,凸、凹模间隙是靠调整压力机的闭合高度来控制的,不需要在设计、制造模具时确定。
对于U形件的弯曲,则必须选择适当的间隙。
间隙的大小对工件质量和弯曲力有很大的影响。
间隙愈小,则弯曲力愈大;
间隙过小,会使工件边部壁厚减薄,降低凹模寿命。
间隙过大,则回弹大,降低工件的精度。
凸、凹模单边间隙c一般可按下式计算:
式中c—弯曲模凸、凹模单边间隙(mm);
t—工件材料厚度(基本尺寸)(mm);
△—工件材料厚度的正偏差(mm);
x—间隙系数。
当工件精度要求较高时,其间隙应适当缩小,取c=t。
某些情况,甚至选取略小于材料厚度的负间隙。
本设计选取的间隙就是c=t。
5.2.4凸、凹模工作部分尺寸的计算公式
设计中,对弯曲件的标注形式的不同,则计算公式也有所不同。
在本设计中用外形尺寸标注弯曲件,此时应以凹模为基准先确定凹模尺寸,工件为单向偏差,其计算公式如下:
凹模尺寸为
凸模尺寸为
—凹模尺寸(mm);
—凸模尺寸(mm);
L—弯曲件基本尺寸(mm);
△—弯曲件尺寸公差(mm);
c—凸、凹模之间的单边间隙(mm);
—凸、凹模制造公差,采用IT8标准公差等级。
油箱底壳不良品主要是破裂、皱纹、精度和外观不佳:
(1)破裂。
为防止油箱底壳破裂,一般采用模具具体部位的修理,毛坯的再改善,