UG编程Word文档格式.docx
《UG编程Word文档格式.docx》由会员分享,可在线阅读,更多相关《UG编程Word文档格式.docx(16页珍藏版)》请在冰豆网上搜索。
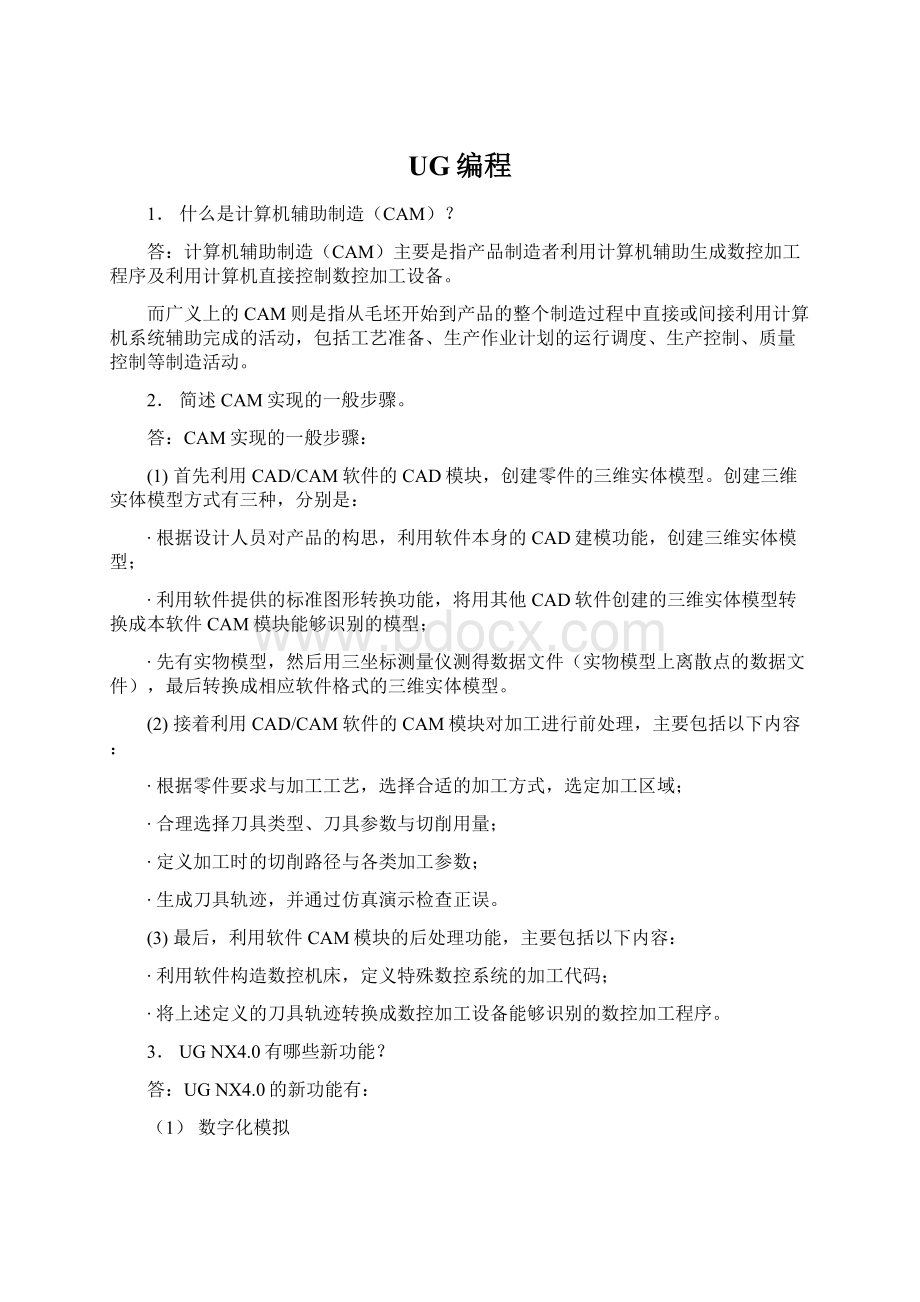
除了设计方面的知识,还可以用新的“制造向导编制器”来捕捉制造工艺方面的知识。
“制造向导编制器”是以NX3.0的核心技术“ProcessStudio”为基础,允许公司捕捉简单工作流程环境中的共用制造工艺。
然后系统自动完成“向导”建立过程或者为每一位用户提供一个自动程序。
该方法允许公司简化制造工艺,确保工艺能够被重复使用,而这正是缩短产品上市时间的关键。
NX4.0还延续了UGS的承诺,即在开发定制应用程序时让客户自由选择语言。
NX4.0支持Java编程语言,确保用户可以根据自身需要用最适当的工具来开发应用程序,并提供了一个共用框架,让用户能够访问NX的核心功能。
这一“开放式应用程序”方法还允许公司把NX应用程序和外部系统集成在一起,比如与专有系统相连接以便进行成本管理。
(3)可用性
以行业和体验为基础的一系列用户界面模板对NX4.0里面的改善NX4.0的盒外可用性。
用户可以选择自己的体验级别和行业,NX将会根据其选择显示一套最具生产性的功能。
公司可以根据自身需要创建自己的屏幕布置和图标,以便改善使用NX的生产力。
(4)系统工程
2-DLayout是一种新的概念设计方法,这是NX的竞争者所没有的。
有了2-DLayout,用户就可以快速创建设计方案,并且随着产品变革不断对设计方案进行充实丰富。
这一方法把早期概念规划引入到集成设计过程中,从而增加了创新速度。
此外,NX4.0也实现了UGS的诺言,它自带的数据迁移工具为希望过渡到NX的I-deas用户提供了及时有效的帮助。
4.比较说明数控车床和数控铣床对刀具要求的异同。
(1)数控车床对刀具的要求:
数控车床能兼作粗、精加工,对刀具要求也有所不同。
∙粗车刀具:
为使粗加工能以较大切削深度、较大进给速度地加工,要求刀具的强度高、耐用度好。
∙精车刀具:
精车时首先是保证加工精度,所以要求刀具的精度高、耐用度好。
∙为减少换刀时间和方便对刀,应可能多地采用机夹刀。
∙数控车床还要求刀片耐用度的一致性好,以便于使用刀具寿命管理功能。
在使用刀具寿命管理时,刀片耐用度的设定原则是以该批刀片中耐用度最低的刀片作为依据的。
在这种情况下,刀片耐用度的一致性甚至比其平均寿命更重要。
(2)数控铣床对刀具的要求:
∙铣刀刚性要好
一是为提高生产效率而采用大切削用量的需要;
二是为适应数控铣床加工过程中难以调整切削用量的特点。
当工件各处的加工余量相差悬殊时,通用铣床遇到这种情况很容易采取分层铣削方法加以解决,而数控铣削就必须按程序规定的走刀路线前进,遇到余量大时无法象通用铣床那样“随机应变”,除非在编程时能够预先考虑到,否则铣刀必须返回原点,用改变切削面高度或加大刀具半径补偿值的方法从头开始加工,多走几刀。
但这样势必造成余量少的地方经常走空刀,降低了生产效率,如刀具刚性较好就不必这么办。
∙铣刀的耐用度要高
尤其是当一把铣刀加工的内容很多时,如刀具不耐用而磨损较快,就会影响工件的表面质量与加工精度,而且会增加换刀引起的调刀与对刀次数,也会使工作表面留下因对刀误差而形成的接刀台阶,降低了工件的表面质量。
∙除上述两点之外,铣刀切削刃的几何角度参数的选择及排屑性能等也非常重要,切屑粘刀形成积屑瘤在数控铣削中是十分忌讳的。
总之,根据被加工工件材料的热处理状态、切削性能及加工余量,选择刚性好,耐用度高的铣刀,是充分发挥数控铣床的生产效率和获得满意的加工质量的前提。
5.说明数控加工工艺性分析的主要内容。
数控加工工艺性分析的主要内容:
(1)尺寸标注应符合数控加工的特点
在数控编程中,所有点、线、面的尺寸和位置都是以编程原点为基准的。
因此零件图样上最好直接给出坐标尺寸,或尽量以同一基准引注尺寸。
(2)几何要素的条件应完整、准确
在程序编制中,编程人员必须充分掌握构成零件轮廓的几何要素参数及各几何要素间的关系。
因为在自动编程时要对零件轮廓的所有几何元素进行定义,手工编程时要计算出每个节点的坐标,无论哪一点不明确或不确定,编程都无法进行。
但由于零件设计人员在设计过程中考虑不周或被忽略,常常出现参数不全或不清楚,如圆弧与直线、圆弧与圆弧是相切还是相交或相离。
所以在审查与分析图纸时,一定要仔细核算,发现问题及时与设计人员联系。
(3)定位基准可靠
在数控加工中,加工工序往往较集中,以同一基准定位十分重要。
因此往往需要设置一些辅助基准,或在毛坯上增加一些工艺凸台。
如图3-14(a)所示的零件,为增加定位的稳定性,可在底面增加一工艺凸台,如图3-14(b)所示。
在完成定位加工后再除去。
a)改进前的结构b)改进后的结构
图3-14工艺凸台的应用
(4)统一几何类型及尺寸
零件的外形、内腔最好采用统一的几何类型及尺寸,这样可以减少换刀次数,还可能应用控制程序或专用程序以缩短程序长度。
零件的形状尽可能对称,便于利用数控机床的镜向加工功能来编程,以节省编程时间。
6.简述对零件进行数控加工工艺设计的主要任务。
对零件进行数控加工工艺设计时,一般应进行以下几方面的工作:
•数控加工工艺内容的选择
•数控加工工艺性分析
•数控加工工艺路线的设计
7.工件如图3-26所示,试编制加工程序。
已知:
材料是铝,毛坯尺寸Φ80×
30mm;
刀具采用键槽铣刀,直径8mm。
图3-26练习4零件图
零件轮廓加工程序
O0004
G54
G90G17G40G49G80
G00Z50.
G00X-40.Y-40.
M03S800
G00Z5.
G01Z-5.F80
G01G41X-35.Y0D01
G02I15.
G01Y32.
G01X0.
G02Y-32.R32.
G03X-20.Y37.736R37.736
G01Z5.
G00G40X-25.
G00G41X-21.Y0D01
G01Z-5.
G03X-11.R5.
G03I-9.
G03X-21.R5.
G00G40Y-40.
G00Z100.
G00X0.Y0.
M05
M30
8.工件如图3-27所示,试编制加工程序。
(凹模,深5mm)
材料是钢,毛坯尺寸Φ80×
图3-27练习5零件图
O0005
G00X15.Y25.
G00G41X14.894Y17.825D01
G01Z-5.F30
G03X19.894Y22.825R-5.
G01X10.106
G03X5.776Y15.325R5.
G01X10.670Y6.849
G03X19.330R5.
G01X24.224Y15.325
G03X14.894Y17.825R-5.
G00G40Y10.
G00X-16.Y25.
G00G41X-15.106Y17.825D01
G01Z-5.
G03X-10.106Y22.825R-5.
G01X-19.894
G03X-24.224Y15.325R5.
G01X-19.330Y6.849
G03X-10.670R-5.
G01X-5.776Y15.325
G03X-15.106Y17.825R-5.
G00X10.
G00G41X11.156Y-10.D01
G03X16.156Y-5.R-5.
G01X-16.156
G03X-20.407Y-12.632R5.
G03X20.407R24.
G03X11.156Y-10.R-5.
G00G40Y-20.
G00X0Y0
1.概念题:
(1)创建加工坐标系的方法有哪些?
ⅰ选择【操作导航器】工具条中的【几何视图】图标
,点击屏幕右侧【操作导航器】图标
,打开【操作导航器-几何体】对话框如图4-6所示,双击坐标系
,打开坐标原点【MILL_ORIENT】对话框。
ⅱ在【加工创建】工具条中选择【创建几何体】图标
,打开【创建几何体】对话框,
在【子类型】中选择坐标系MCS图标
,单击
按钮,打开坐标系【MCS】对话框,和坐标原点【MILL_ORIENT】对话框的作用一致。
(2)简述工件几何与毛坯几何的作用与区别。
工件几何:
是指包含零件信息和毛坯信息的过程零件。
工件如果需要模拟加工就必须指定工件几何。
毛坯几何:
是定义要加工成零件的原材料。
(3)简述各种进给速度的名称及其对应的运动阶段。
▽快速(Rapid)
该选项用于设置快进速度。
即刀具从初始点(FromPoint)到下一个前进点(GotoPoint)的移动速度。
▽逼近(Approach)
该选项用于设置逼近速度。
即刀具从起刀点(StartPoint)到进刀点(EngagePoint)的进给速度。
▽进刀(Engage)
该选项用于设置进刀速度,即刀具切入零件时的进给速度。
它是刀具从进刀点(EngagePoint)到初始切削位置(InitialCuttingPosition)的移动速度。
▽第一刀切削(FirstCut)
切入材料后的第一刀的进给速度。
▽步进(Stepover)
步距进给速度:
相邻两刀之间的跨过速度。
▽切削(Cut)
切削进给速度:
正常切削状态的进给速度。
▽横越(Traversal)
横越速度:
刀具从一个切削区转移到另一个切削区的非切削移动速度。
▽退刀(Retract)
退刀速度:
离开切削区返回Retract点的速度。
▽返回(Return)
返回速度:
退刀运动完成后返回Return点的速度。
▽分离(Departure)
离开速度:
即刀具从加工部位退出时的移动速度。
1概念题:
⑴平面铣适用于什么形状的零件?
平面铣(PlanarMilling)主要用于平面轮廓、平面区域或平面孤岛的粗、精加工,尤其适用于需大量切除毛坯余量的场合。
⑵简述平面铣加工几何类型。
平面铣所涉及的加工几何包括下列5种:
零件几何体,毛坯几何体,检查几何体,修剪几何,底平面。
⑶在自动进刀和退刀中,倾斜类型有哪几种?
各适于什么情况下使用?
在自动进刀和退刀中,倾斜类型有下列几种:
▽如果指定了预钻进刀点,可以沿毛坯上的预钻孔垂直进刀到切削层的深度,而忽略斜式进刀参数。
▽斜线(OnLine)
:
斜直线进刀,斜直线沿刀具轴的投影与切削刀轨重合。
必须在单向切削(Zig)和往复式切削(Zig_Zag)方法中使用斜线(OnLine)。
▽刀轨形状的斜线(OnShape)
斜式进刀,进刀轨迹沿刀具轴投影到层的刀轨平面内,刚好与刀轨重合。
应当在仿形外轮廓(FollowPeriphery)、仿形零件(FollowPart)切削方法中使用刀轨形状的斜线(OnShape)。
▽螺旋(Helical)
进刀轨迹是螺旋线。
应当在仿形外轮廓(FollowPeriphery)、仿形零件(FollowPart)切削方法中使用螺旋(Helical)。
1.概念题
固定轴曲面轮廓铣的常用驱动方式有哪些?
指出其异同点。
实施固定轴曲面轮廓铣的一般步骤?
答案:
(1)曲线/点驱动方法:
曲线/点驱动方法通过指定点或选择曲线来定义驱动几何。
指定点时,驱动路径是指定点之间指定顺序的直线段。
选择曲线时,驱动点指定曲线生成。
曲线可以是封闭或开放、连续或非连续,也可以是平面曲线或空间曲线。
边界驱动方法:
边界驱动方法通过指定边界和环来定义切削区域。
边界并不依赖零件表面的形状和尺寸,而环则必须位于零件几何表面的外部边缘内。
区域铣削驱动方法:
区域铣削驱动方法通过指定切削区域、添加陡峭容纳环和修剪几何约束来定义固定轴曲面轮廓铣操作。
与边界驱动不同的是,区域铣削驱动方法不需要指定驱动几何,利用零件几何自动计算出不冲突的环
曲面区域驱动方法:
曲面区域驱动方法,是在驱动曲面上创建网格状的驱动点阵列,产生的驱动点,这些驱动点首先生成在驱动面上,然后沿投影矢量方向投影到零件表面上而生成刀轨。
曲面区域驱动方法常用于可变轴铣削加工形状复杂的零件表面,也可用于固定轴铣削加工复杂零件表面。
(2)
创建固定轴铣,首先要定义被加工的几何体,然后指定合适的驱动方法、投射失量与刀轴,再设置必要的加工参数,最后生成刀具路径,并可对刀具路径进行模拟加工。
1)定义需要加工的几何体
对所有驱动方法,都可以定义零件几何与检查几何,对区域铣驱动方法与清根驱动方法,还可以定义切削区域与修剪几何,所有几何体都可以通过片体、实体、小面体、表面区域或表面来定义。
2)指定合适的驱动方法
根据加工表面的形状与复杂性,以及刀轴与投射失量的要求来确定适当的驱动方法,一旦选定了驱动方法,也就决定了可选择的驱动几何类型,以及可用的投射失量、刀轴与切削方法。
3)设置合理的投射失量
可用投射失量的类型取决于所指定的驱动方法。
4)设置必要的加工参数
加工参数包括切削参数、非切削运动参数、进给量、避让几何、机床控制等参数。
5)生成刀具路径并进行模拟加工
进行模拟加工,是为了验证刀具路径是否符合要求,若不符合要求,则可修改以上任一一项设置,直到满意为止。
9.概念题
(1)孔加工循环的类型有哪几类?
叙述一下各种类型的动作过程。
①标准钻…
该循环过程是,刀具首先以快进速度移动到点位上方,然后以循环进给速度钻削到要求的孔深,最后以快速退回安全点。
接着刀具快速移动到新的点位上,进入一个新的循环。
该循环是钻孔最常用的循环,但不适用于加工深孔及有一定深度的韧性材料的孔,在FANUC系统中对应的G代码是G81。
②标准钻,深度…
该循环与“标准钻…”循环不同在于,钻削时刀具采用间隙进给,即刀具钻削到指定的深度增量后退出孔外排屑,接着再向下钻削指定深度增量,再退刀排屑,…,如此反复,直至孔底。
其它循环动作与“标准钻…”循环相同。
该循环用于深孔钻削,这就是数控编程中排屑钻,在FANUC系统中对应的G代码是G83。
③标准钻,断屑…
该循环与“标准钻,深度…”循环不同在于,刀具钻削到指定的深度增量后,并不是退出孔外排屑,而是退一较小距离,起到断屑作用。
其它动作与“标准钻,深度…”循环相同。
该循环用于韧性材料的钻孔加工,这就是数控编程中断屑钻,在FANUC系统中对应的G代码是G73。
④标准钻,埋头…
该循环基本动作与“标准钻…”循环相同,唯一不同在于钻削深度由埋头孔径控制,即在循环参数设定时与“标准钻…”循环不同,其第一个设定参数是“Csink直径”。
该循环用于埋头孔加工,在FANUC系统中对应的G代码仍是G81,只是孔深由UG软件从埋头孔径自动换算,比较操作方便。
⑤标准攻丝…
该循环与“标准钻…”循环不同在于,在孔底主轴停,退刀时主轴反转,以切削速度退回。
该循环用于螺纹孔加工。
在FANUC系统中对应的G代码是G84。
⑥标准镗…
该循环与“标准钻…”循环不同在于,退刀时是以切削进给速度退回。
该循环用于孔的粗镗加工,常用双刃镗刀加工。
在FANUC系统中对应的G代码是G85。
⑦标准镗,拖…
该循环与“标准镗…”循环相比,区别在于,在孔底主轴停止,刀具以快速进给速度退回。
其它循环动作与“标准镗…”循环相同。
该循环也用于孔的粗镗加工。
在FANUC系统中对应的G代码是G86。
⑧标准镗,不拖…
该循环与“标准镗…”循环相比,区别在于,在孔底主轴准停后刀具有一横向让刀动作,退刀时主轴不转,返回安全点后刀具横向退回让刀值,主轴再次起动。
其它循环动作与“标准镗,…”循环相同。
由于有让刀动作,退刀时不会损伤已加工面,因此该循环用于孔的精镗加工,而且必须采用单刃镗刀加工。
在FANUC系统中对应的G代码是G76。
⑨标准镗,返回…
该循环与“标准镗…”循环相比,区别在于,刀具到达指定点位后,主轴准停、横向让刀,刀具快速进给到孔底,横向退回让刀值,主轴起动,向上切削加工指定Z轴坐标,主轴再次准停,让刀返回安全平面,刀具退回让刀值。
该循环在数控系统中称为“背镗”,也用于孔的精镗加工,但只能用于通孔的镗削加工,而且必须激活安全平面。
在FANUC系统中对应的G代码是G87。
10标准镗,手动…
该循环与“标准镗…”循环相比,区别在于,刀具加工到孔底,主轴停转,由操作者手动退刀。
在FANUC系统中对应的G代码是G88。
(2)简述孔位加工的一般步骤。
孔位加工的一般步骤:
步骤一:
初始化加工环境
步骤二:
创建操作
步骤三:
定义几何体
步骤四:
设定循环参数
步骤五:
设定机床参数
步骤六:
定义刀具
步骤七:
生成刀轨
步骤八:
后处理
也可以按下列步骤:
1.概念题
(1)可变轴曲面轮廓铣的常用驱动方式有哪些?
实现高速加工的工艺策略?
(2)可变轴曲面轮廓铣加工常用的刀轴控制方法有哪些?
(1)可变轴曲面轮廓铣的驱动方法有7种:
∙曲线/点驱动方法
∙边界驱动方法
∙螺旋驱动方法
∙曲面区域驱动方法
∙刀轨驱动方法
∙径向切削驱动方法
∙用户函数驱动方法
基于高速加工对硬件、软件的要求,工艺员在制订工艺策略时要注意如下几点。
1)轻而恒定的切削负荷
使用较小的步距和窄的切削深度,比如平面铣和型腔铣可以使用浅的切削深度和较大的步距,也可以使用深的切削深度和小的步距;
曲面轮廓铣使用多次切削。
使用Z-Level铣可以使负荷比较恒定。
2)圆滑的拐角
通过“拐角和进给率控制”对话框对刀轨的拐角处进行圆倒角,可以由对话框中的“圆角”选项指定圆角半径。
3)圆滑过渡所有进刀、退刀、步距和非切削运动
使用“自动进刀和退刀”参数来指定圆弧、螺旋或斜式的进退刀运动;
通过将“拐角和进给率控制”对话框的“圆角”选项指定为全部刀路来圆滑拐角和步距。
4)使用Z-Level加工
型腔铣的Z-Level铣方法利用陡峭面和非陡峭面的分开加工来保证恒定的残余材料高度。
通过型腔铣的Z-Level-Profile铣的切削参数中的“层到层”参数指定为“直接对部件”、“倾斜于工件”、“对部件的交叉倾斜”,可以保证在层间没有提刀动作,因此特别适合高速加工。
可以用Z-Level-Profile铣作精加工。
垂直于驱动曲面
该选项只可用于曲面区域驱动方法的可变轴轮廓铣加工操作。
在每个驱动点都垂直于驱动曲面定义的矢量作为驱动点投影到零件表面的投影矢量。
如果零件表面可以作为驱动曲面,通常直接指定零件表面为驱动曲面,不需要另外指定零件表面。
直纹线
直纹面驱动是利用直纹面类型的驱动曲面的直纹线来定义刀轴方向的。
该方法主要用来进行侧刃加工,即使用刀具的侧面来加工零件型面。
1.概念题
UG/p