数控加工工艺设计Word下载.docx
《数控加工工艺设计Word下载.docx》由会员分享,可在线阅读,更多相关《数控加工工艺设计Word下载.docx(16页珍藏版)》请在冰豆网上搜索。
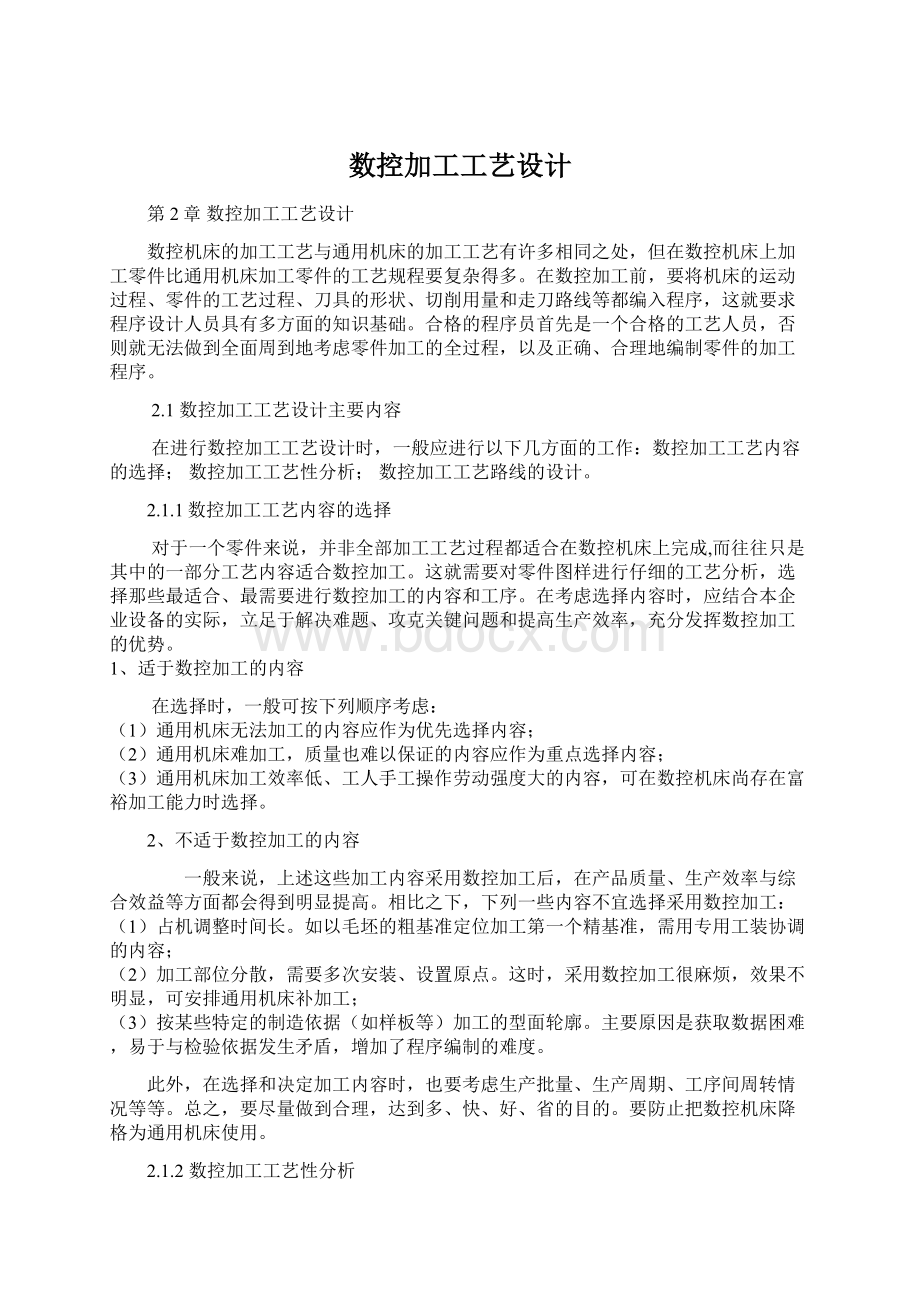
但由于零件设计人员在设计过程中考虑不周或被忽略,常常出现参数不全或不清楚,如圆弧与直线、圆弧与圆弧是相切还是相交或相离。
所以在审查与分析图纸时,一定要仔细核算,发现问题及时与设计人员联系。
3、定位基准可靠
在数控加工中,加工工序往往较集中,以同一基准定位十分重要。
因此往往需要设置一些辅助基准,或在毛坯上增加一些工艺凸台。
如图2.1a所示的零件,为增加定位的稳定性,可在底面增加一工艺凸台,如图2.1b所示。
在完成定位加工后再除去。
a)改进前的结构
b)改进后的结构
图2.1工艺凸台的应用
4、统一几何类型及尺寸
零件的外形、内腔最好采用统一的几何类型及尺寸,这样可以减少换刀次数,还可能应用控制程序或专用程序以缩短程序长度。
零件的形状尽可能对称,便于利用数控机床的镜向加工功能来编程,以节省编程时间。
2.1.3数控加工工艺路线的设计
图2.2工艺流程
数控加工工艺路线设计与通用机床加工工艺路线设计的主要区别,在于它往往不是指从毛坯到成品的整个工艺过程,而仅是几道数控加工工序工艺过程的具体描述。
因此在工艺路线设计中一定要注意到,由于数控加工工序一般都穿插于零件加工的整个工艺过程中,因而要与其它加工工艺衔接好。
常见工艺流程如图2.2所示。
数控加工工艺路线设计中应注意以下几个问题:
1、工序的划分
根据数控加工的特点,数控加工工序的划分一般可按下列方法进行:
(1)以一次安装、加工作为一道工序。
这种方法适合于加工内容较少的零件,加工完后就能达到待检状态。
(2)以同一把刀具加工的内容划分工序。
有些零件虽然能在一次安装中加工出很多待加工表面,但考虑到程序太长,会受到某些限制,如控制系统的限制(主要是内存容量),机床连续工作时间的限制(如一道工序在一个工作班内不能结束)等。
此外,程序太长会增加出错与检索的困难。
因此程序不能太长,一道工序的内容不能太多。
(3)以加工部位划分工序。
对于加工内容很多的工件,可按其结构特点将加工部位分成几个部分,如内腔、外形、曲面或平面,并将每一部分的加工作为一道工序。
(4)以粗、精加工划分工序。
对于经加工后易发生变形的工件,由于对粗加工后可能发生的变形需要进行校形,故一般来说,凡要进行粗、精加工的过程,都要将工序分开。
2、顺序的安排
顺序的安排应根据零件的结构和毛坯状况,以及定位、安装与夹紧的需要来考虑。
顺序安排一般应按以下原则进行:
(1)上道工序的加工不能影响下道工序的定位与夹紧,中间穿插有通用机床加工工序的也应综合考虑;
(2)先进行内腔加工,后进行外形加工;
(3)以相同定位、夹紧方式加工或用同一把刀具加工的工序,最好连续加工,以减少重复定位次数、换刀次数与挪动压板次数;
3、数控加工工艺与普通工序的衔接
数控加工工序前后一般都穿插有其它普通加工工序,如衔接得不好就容易产生矛盾。
因此在熟悉整个加工工艺内容的同时,要清楚数控加工工序与普通加工工序各自的技术要求、加工目的、加工特点,如要不要留加工余量,留多少;
定位面与孔的精度要求及形位公差;
对校形工序的技术要求;
对毛坯的热处理状态等,这样才能使各工序达到相互满足加工需要,且质量目标及技术要求明确,交接验收有依据。
2.2数控加工工艺设计方法
在选择了数控加工工艺内容和确定了零件加工路线后,即可进行数控加工工序的设计。
数控加工工序设计的主要任务是进一步把本工序的加工内容、切削用量、工艺装备、定位夹紧方式及刀具运动轨迹确定下来,为编制加工程序作好准备。
2.2.1确定走刀路线和安排加工顺序
走刀路线就是刀具在整个加工工序中的运动轨迹,它不但包括了工步的内容,也反映出工步顺序。
走刀路线是编写程序的依据之一。
确定走刀路线时应注意以下几点:
1、寻求最短加工路线
如加工图2.3a所示零件上的孔系。
2.3b图的走刀路线为先加工完外圈孔后,再加工内圈孔。
若改用2.3c图的走刀路线,减少空刀时间,则可节省定位时间近一倍,提高了加工效率。
a)零件图样
b)路线1
c)路线2
图2.3最短走刀路线的设计
2、最终轮廓一次走刀完成
为保证工件轮廓表面加工后的粗糙度要求,最终轮廓应安排在最后一次走刀中连续加工出来。
如图2.4a为用行切方式加工内腔的走刀路线,这种走刀能切除内腔中的全部余量,不留死角,不伤轮廓。
但行切法将在两次走刀的起点和终点间留下残留高度,而达不到要求的表面粗糙度。
所以如采用2.4b图的走刀路线,先用行切法,最后沿周向环切一刀,光整轮廓表面,能获得较好的效果。
图2.4c也是一种较好的走刀路线方式。
a)路线1
b)路线3
c)路线3
图2.4铣削内腔的三种走刀路线
3、选择切入切出方向
考虑刀具的进、退刀(切入、切出)路线时,刀具的切出或切入点应在沿零件轮廓的切线上,以保证工件轮廓光滑;
应避免在工件轮廓面上垂直上、下刀而划伤工件表面;
尽量减少在轮廓加工切削过程中的暂停(切削力突然变化造成弹性变形),以免留下刀痕,如图2.5所示。
图2.5 刀具切入和切出时的外延
4、选择使工件在加工后变形小的路线
对横截面积小的细长零件或薄板零件应采用分几次走刀加工到最后尺寸或对称去除余量法安排走刀路线。
安排工步时,应先安排对工件刚性破坏较小的工步。
2.2.2确定定位和夹紧方案
在确定定位和夹紧方案时应注意以下几个问题:
(1)尽可能做到设计基准、工艺基准与编程计算基准的统一;
(2)尽量将工序集中,减少装夹次数,尽可能在一次装夹后能加工出全部待加工表面;
(3)避免采用占机人工调整时间长的装夹方案;
(4)夹紧力的作用点应落在工件刚性较好的部位。
如图2.6a薄壁套的轴向刚性比径向刚性好,用卡爪径向夹紧时工件变形大,若沿轴向施加夹紧力,变形会小得多。
在夹紧图2.6b所示的薄壁箱体时,夹紧力不应作用在箱体的顶面,而应作用在刚性较好的凸边上,或改为在顶面上三点夹紧,改变着力点位置,以减小夹紧变形,如图2.6c所示。
a)薄壁套
b)改进方法2
c)改进方法2
图2.6夹紧力作用点与夹紧变形的关系
2.2.3确定刀具与工件的相对位置
图2.7对刀点
对于数控机床来说,在加工开始时,确定刀具与工件的相对位置是很重要的,这一相对位置是通过确认对刀点来实现的。
对刀点是指通过对刀确定刀具与工件相对位置的基准点。
对刀点可以设置在被加工零件上,也可以设置在夹具上与零件定位基准有一定尺寸联系的某一位置,对刀点往往就选择在零件的加工原点。
对刀点的选择原则如下:
(1)所选的对刀点应使程序编制简单;
(2)对刀点应选择在容易找正、便于确定零件加工原点的位置;
(3)对刀点应选在加工时检验方便、可靠的位置;
(4)对刀点的选择应有利于提高加工精度。
例如,加工图2.7所示零件时,当按照图示路线来编制数控加工程序时,选择夹具定位元件圆柱销的中心线与定位平面A的交点作为加工的对刀点。
显然,这里的对刀点也恰好是加工原点。
在使用对刀点确定加工原点时,就需要进行“对刀”。
所谓对刀是指使“刀位点”与“对刀点”重合的操作。
每把刀具的半径与长度尺寸都是不同的,刀具装在机床上后,应在控制系统中设置刀具的基本位置。
“刀位点”是指刀具的定位基准点。
如图2.8所示,圆柱铣刀的刀位点是刀具中心线与刀具底面的交点;
球头铣刀的刀位点是球头的球心点或球头顶点;
车刀的刀位点是刀尖或刀尖圆弧中心;
钻头的刀位点是钻头顶点。
各类数控机床的对刀方法是不完全一样的,这一内容将结合各类机床分别讨论。
换刀点是为加工中心、数控车床等采用多刀进行加工的机床而设置的,因为这些机床在加工过程中要自动换刀。
对于手动换刀的数控铣床,也应确定相应的换刀位置。
为防止换刀时碰伤零件、刀具或夹具,换刀点常常设置在被加工零件的轮廓之外,并留有一定的安全量。
a)钻头的刀位点
b)车刀的刀位点
c)圆柱铣刀的刀位点
d)球头铣刀的刀位点
图2.8 刀位点
2.2.4确定切削用量
对于高效率的金属切削机床加工来说,被加工材料、切削刀具、切削用量是三大要素。
这些条件决定着加工时间、刀具寿命和加工质量。
经济的、有效的加工方式,要求必须合理地选择切削条件。
编程人员在确定每道工序的切削用量时,应根据刀具的耐用度和机床说明书中的规定去选择。
也可以结合实际经验用类比法确定切削用量。
在选择切削用量时要充分保证刀具能加工完一个零件,或保证刀具耐用度不低于一个工作班,最少不低于半个工作班的工作时间。
背吃刀量主要受机床刚度的限制,在机床刚度允许的情况下,尽可能使背吃刀量等于工序的加工余量,这样可以减少走刀次数,提高加工效率。
对于表面粗糙度和精度要求较高的零件,要留有足够的精加工余量,数控加工的精加工余量可比通用机床加工的余量小一些。
编程人员在确定切削用量时,要根据被加工工件材料、硬度、切削状态、背吃刀量、进给量,刀具耐用度,最后选择合适的切削速度。
表2.1为车削加工时的选择切削条件的参考数据。
表2.1车削加工的切削速度(m/min)
被切削材料名称
轻切削
切深0.5~10.mm
进给量
0.05~0.3mm/r
一般切削
切深1~4mm
进给量
0.2~0.5mm/r
重切削
切深5~12mm
0.4~0.8mm/r
优质碳素结构钢
10#
100~250
150~250
80~220
45#
60~230
70~220
80~180
合金钢
σb≤750MPa
100~220
100~230
σb>
750MPa
80~200
2.3填写数控加工技术文件
填写数控加工专用技术文件是数控加工工艺设计的内容之一。
这些技术文件既是数控加工的依据、产品验收的依据,也是操作者遵守、执行的规程。
技术文件是对数控加工的具体说明,目的是让操作者更明确加工程序的内容、装夹方式、各个加工部位所选用的刀具及其它技术问题。
数控加工技术文件主要有:
数控编程任务书、工件安装和原点设定卡片、数控加工工序卡片、数控加工走刀路线图、数控刀具卡片等。
以下提供了常用文件格式,文件格式可根据企业实际情况自行设计。
2.3.1数控编程任务书
它阐明了工艺人员对数控加工工序的技术要求和工序说明,以及数控加工前应保证的加工余量。
它是编程人员和工艺人员协调工作和编制数控程序的重要依据之一,详见表2.2。
表2.2 数控编程任务书
工艺处
数控编程任务书
产品零件图号
任务书编号
零件名称
使用数控设备
共页第页
主要工序说明及技术要求:
编程收到日期
月日
经手人
编制
审核
编程
批准
2.3.2数控加工工件安装和原点设定卡片(简称装夹图和零件设定卡)
它应表示出数控加工原点定位方法和夹紧方法,并应注明加工原点设置位置和坐标方向,使用的夹具名称和编号等,详见表2.3。
表2.3工件安装和原点设定卡片
零件图号
J30102-4
数控加工工件安装和原点设定卡片
工序号
零件名称
行星架
装夹次数
3
梯形槽螺栓
2
压板
1
镗铣夹具板
GS53-61
编制(日期) 审核(日期)
批准(日期)
第 页
共 页
序号
夹具名称
夹具图号
2.3.3数控加工工序卡片
数控加工工序卡与普通加工工序卡有许多相似之处,所不同的是:
工序简图中应注明编程原点与对刀点,要进行简要编程说明(如:
所用机床型号、程序编号、刀具半径补偿、镜向对称加工方式等)及切削参数(即程序编入的主轴转速、进给速度、最大背吃刀量或宽度等)的选择,详见表2.4。
表2.4数控加工工序卡片
单位
数控加工工序卡片
产品名称或代号
零件图号
工序简图
车间
使用设备
工艺序号
程序编号
夹具名称
夹具编号
工步号
工步作业内容
加工面
刀
具
号
刀补量
主轴转速
进给速度
背
吃
刀
量
备注
年月日
共页
第页
2.3.4数控加工走刀路线图
在数控加工中,常常要注意并防止刀具在运动过程中与夹具或工件发生意外碰撞,为此必须设法告诉操作者关于编程中的刀具运动路线(如:
从哪里下刀、在哪里抬刀、哪里是斜下刀等)。
为简化走刀路线图,一般可采用统一约定的符号来表示。
不同的机床可以采用不同的图例与格式,表2.5为一种常用格式。
表2.5数控加工走刀路线图
数控加工走刀路线图
NC01
工步号
程序号
O100
机床型号
XK5032
程序段号
N10~N170
加工内容
铣轮廓周边
共1页
第页
编程
校对
审批
符号
含义
抬刀
下刀
编程原点
起刀点
走刀方向
走刀线相交
爬斜坡
铰孔
行切
2.3.5数控刀具卡片
数控加工时,对刀具的要求十分严格,一般要在机外对刀仪上预先调整刀具直径和长度。
刀具卡反映刀具编号、刀具结构、尾柄规格、组合件名称代号、刀片型号和材料等。
它是组装刀具和调整刀具的依据,详见表2.6。
表2.6数控刀具卡片
数 控 刀 具 卡 片
使用设备
刀具名称
镗刀
TC-30
刀具编号
T13006
换刀方式
自动
程序编号
具
组
成
编号
规格
数量
备注
T013960
拉钉
390、140-5050027
刀柄
391、01-5050100
接杆
Φ50×
100
4
391、68-03650085
镗刀杆
5
R416.3-12205325
镗刀组件
Φ41-Φ53
6
TCMM110208-52
刀片
7
GC435
编制
审校
批准
共页
第页
不同的机床或不同的加工目的可能会需要不同形式的数控加工专用技术文件。
在工作中,可根据具体情况设计文件格式。
本章提示:
机械加工工艺基础知识,是编制实用、理想数控加工程序的重要基础。
本章主要讨论了数控加工的主要内容,数控加工工艺与常规机械加工工艺的衔接。
更多的机械加工艺问题,请查阅:
www.china-和
思考题与练习题
一、选择题
1.在程序编制时,总是把工件看作()。
A:
静止的B:
运动的
2.车刀的刀位点是指()。
主切削刃上的选定点B:
刀尖
3.精加工时,切削速度选择的主要依据是()。
刀具耐用度B:
加工表面质量
4.在安排工步时,应安排()工步。
简单的B:
对工件刚性破坏较小的
5.在确定定位方案时,应尽量将()。
工序分散B:
工序集中
二、判断题
1.()立铣刀的刀位点是刀具中心线与刀具底面的交点。
2.()球头铣刀的刀位点是刀具中心线与球头球面交点。
3.()由于数控机床的先进性,因此任何零件均适合在数控机床上加工。
4.()换刀点应设置在被加工零件的轮廓之外,并要求有一定的余量。
5.()为保证工件轮廓表面粗糙度,最终轮廓应在一次走刀中连续加工出来。
三、简答题
1.何谓对刀点?
2.何谓刀位点?
3.何谓换刀点?
4.数控工艺与传统工艺相比有哪些特点?
5.数控编程开始前,进行工艺分析的目的是什么?
6.如何从经济观点出发来分析何种零件在数控机床上加工合适?
7.确定对刀点时应考虑哪些因素?
8.指出立铣刀、球头铣刀和钻头的刀位点。
9.指出下列夹紧方案中(图2.9¬
图2.12)不合理之处,并提出改进方案。
图2.9习题图1
图2.10习题图2
图2.11习题图3
图2.12习题图4
10.确定走刀路线时应考虑哪些问题?
11.简要说明切削用量三要素选择的原则。
12.在数控机床上加工时定位基准和夹紧方案的选择应考虑哪些问题?