双管板换热器的设计与制造Word文档下载推荐.docx
《双管板换热器的设计与制造Word文档下载推荐.docx》由会员分享,可在线阅读,更多相关《双管板换热器的设计与制造Word文档下载推荐.docx(5页珍藏版)》请在冰豆网上搜索。
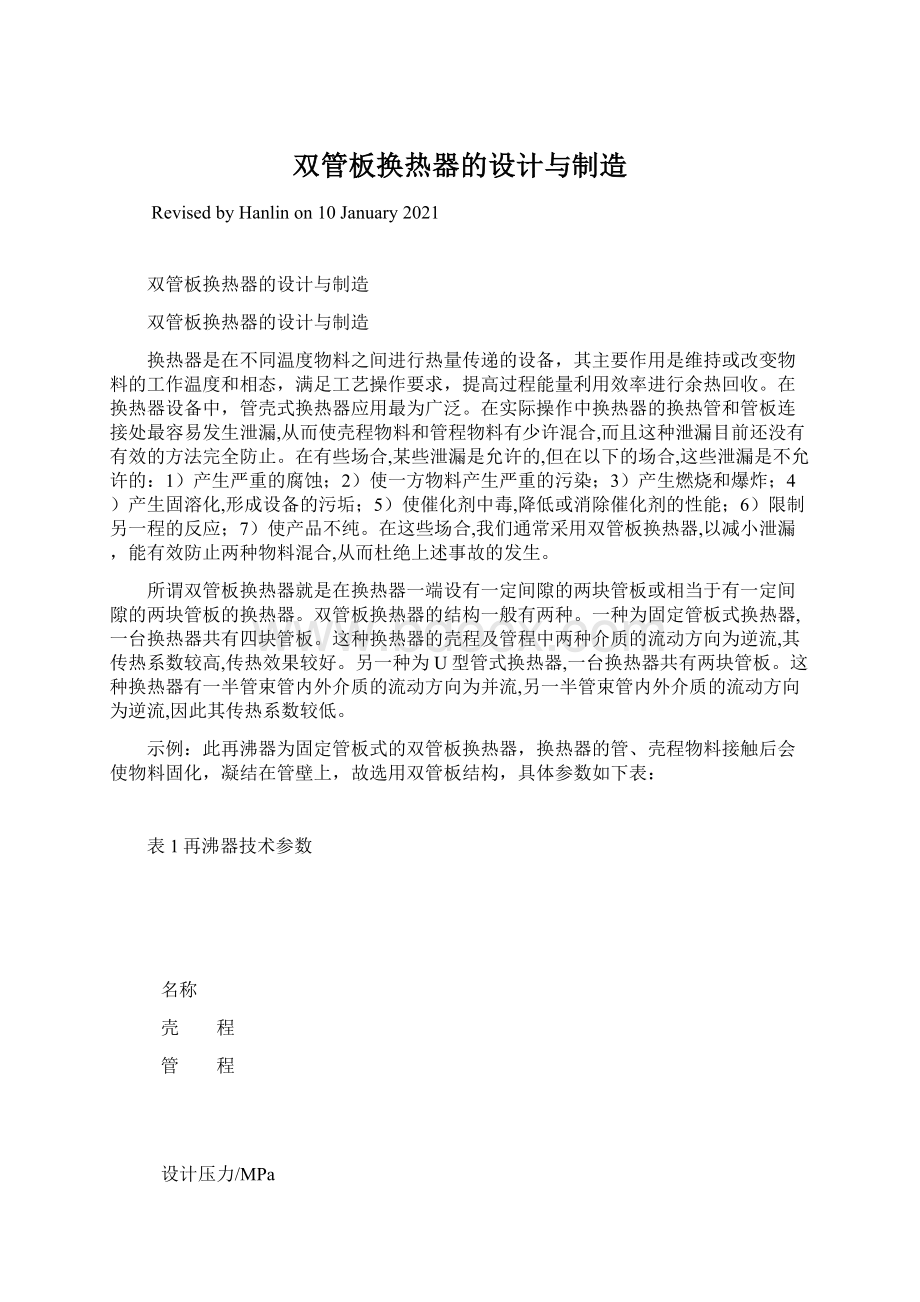
6)限制另一程的反应;
7)使产品不纯。
在这些场合,我们通常采用双管板换热器,以减小泄漏,能有效防止两种物料混合,从而杜绝上述事故的发生。
所谓双管板换热器就是在换热器一端设有一定间隙的两块管板或相当于有一定间隙的两块管板的换热器。
双管板换热器的结构一般有两种。
一种为固定管板式换热器,一台换热器共有四块管板。
这种换热器的壳程及管程中两种介质的流动方向为逆流,其传热系数较高,传热效果较好。
另一种为U型管式换热器,一台换热器共有两块管板。
这种换热器有一半管束管内外介质的流动方向为并流,另一半管束管内外介质的流动方向为逆流,因此其传热系数较低。
示例:
此再沸器为固定管板式的双管板换热器,换热器的管、壳程物料接触后会使物料固化,凝结在管壁上,故选用双管板结构,具体参数如下表:
表1再沸器技术参数
名称
壳 程
管 程
设计压力/MPa
2.7
-0.1
最高工作压力/MPa
4.0/-0.1
0.35/-0.1
设计温度/℃
265
230
进口工作温度/℃
236
190
出口工作温度/℃
198
物料
水蒸汽
溶剂+顺酐
管子与管板连接形式
强度胀
强度焊+贴胀
程数
1
腐蚀裕度/mm
0
焊接接头系数
0.85
由于此再沸器的管、壳程的操作参数比较高,前期设计制造的再沸器使用后一个月左右就泄漏,无法使用,严重影响生产。
为此从设计、试验、制造多方面进行了改进。
设计
鉴于该再沸器的高参数,及双管板换热器结构的特殊性,在设计时,换热管与管板的连接则是换热器安全运行的关键。
在换热器的内管板处,两侧均与换热管连接,必须采用强度账接的形式,而此处又是密封壳程和固定换热管的部位,该处强度账接的质量将直接影响整个设备的使用,尤其是在较高的操作条件下。
胀接是靠管子的塑性变形和管板的弹性变形来达到密封和紧固的一种机械连接方法。
对于换热管的账接通常有两种,液压胀和机械胀。
液压胀管时,胀接区的管子是在高液压内压的作用下产生弹性变形,然后产生塑性变形而被挤压到管板孔壁上。
随着压力的增加,在管子与管板之间的接触压力作用下,管板首先产生弹性变形,然后产生塑性变形。
压力撤消后,如果管板的自由弹性恢复量比管子的大,就会在管子与管板之间产生残余接触压力,实现胀接连接。
这种账接方式适合于操作压力不高的情况,当操作压力大时,账接的强度不足,并且在账接的过程中所用的账接的附件的损坏率也比较高。
因此本台双管板换热器采用机械账。
机械胀接是一种传统的胀接技术,又称为滚轧法,实施机械滚胀时,由胀珠胀撑滚压管内壁,管壁径向扩大,首先胀满间隙,之后进行紧胀,胀珠轧碾管内壁,管壁被胀珠和孔壁挤压,挤压区中的局部管壁发生塑变;
进行径向扩大的同时,金属轴向流动。
孔壁在胀率小时,处于弹性状态;
胀率增大,孔端抗挤压强度小,先塑性变形,成喇叭口;
当管外壁被胀珠挤压,其接触压力使得管壁中间接触区的局部层面开始塑性变形,产生径向扩大和轴向流动。
层面之下的孔壁仍处于弹性状态。
施胀中,该层面上的变形随同胀珠的螺旋运动进行变形过程,但每次重复,层面加深,层层深入。
管壁和孔壁的受轧碾层面,晶粒破碎,晶格畸变,而硬度增加。
撤去胀管器后,管端和板孔进行回弹,由于管桥厚度远大于管壁而弹性变形量大,则管孔弹压管端。
此时,实现了以胀接的严密性、抗拉脱性的牢固性为目的的胀接要求,完成胀接。
现在生产的机械胀管机运用起来方便,并且效率也高。
在GB151-1999《管壳式换热器》中,胀管槽的宽度规定为3mm,但也指出,根据不同的胀接方法可以适当修改。
按通常方式图样中的内侧管板管孔的胀管槽宽度是3mm,深度是0.5mm,胀管槽距管板端面8mm,胀管槽的尺寸链为8mm-3mm-6mm-3mm如图3所示。
为解决本双管板换热器的操作压力比较大的难题,我们增加了一个胀管槽,增大拉脱力的承载能力,将胀管槽的尺寸链改为8mm-3mm-6mm-3mm-6mm-3mm。
在对该换热器的管板强度计算时,将固定双管板换热器分解成两个固定管板换热器,运用SW6固定管板换热器模块分别进行计算。
2.1首先不考虑壳程外管板的加强作用(即去掉壳程外管板),看成一个固定管板换热器,根据设计条件计算壳程管板的厚度。
2.2将管程管箱设为一个管箱、聚液壳设为壳程(这里聚液壳作为壳程,设计温度取环境温度、设计压力按常压,取作0.001MPa因为取0无法计算),不考虑另一侧管箱和双管板的加强作用,将剩下的部分设为另一个管箱(设计压力和温度按原壳程取)。
根据管程和壳程的不同温度及压力,分别计算壳程管板和壳程外管板的厚度。
2.3(最后,壳程管板和壳程外管板分别取计算中的较大值,这样保证固定管板的安全可靠。
同时,为了改善内管板强度胀的受力,在壳程又设置了两个波形膨胀节。
这样在结构的关键点处进行优化,达到了提高设备使用能力的要求。
试验
为了保证胀接质量,我公司在胀管前做胀接评定试验。
3.1试验准备:
首先制作模拟换热器,其管板厚度按产品实际管板厚度确定,管板间距、管孔排列形式按设计图纸要求。
管壳程管板间距、管孔尺寸、换热管尺寸、管间距均与产品相符。
模拟换热器壳程筒体厚度应能承受产品双管板换热器的壳程试验压力。
3.2试验过程:
①测量内管板1管孔尺寸D和胀前换热管3外径d0、内径di和壁厚t,见表2;
②根据要求,强度胀接率p应控制在10%~20%,由胀接率公式p=[(d-di)-(D-d0)]/t×
100%推算出胀后换热管内径d的范围,胀接时,先将外管板4胀焊合格,再根据d值对内管板进行强度胀接,记录下胀管仪的扭矩M。
3.3试验结果:
对模拟换热器进行壳程水压试验,试验压力5.85MPa,经检查,换热管与管板连接处无任何泄漏现象,说明此胀接工艺能够满足该双管板换热器的强度胀接要求。
制造
控制4块管板的同心度、平行度、扭曲度及其与壳体轴线的垂直度,可保障设备的制造质量,也可保障换热管与管板的连接性能。
而确保内侧管板与换热管液压胀接的拉脱力和密封性及其检验,是保证再沸器制造质量的关键。
4.1管板及折流板为增加两块管板管板管孔及折流板管孔的对中性,在满足制造能力的前提下,把折流板、两组管板按工作位置顺序定位焊焊好,再进行划线钻孔。
采用数控钻床加工管孔,以保证管孔直径、垂直度及管孔间距。
钻孔时,切削和退刀速度应尽量慢,以保证管孔的表面粗糙度为Ra3.2~Ra6.4,钻孔时还应留有0.1mm的铰孔余量。
钻孔后对管板孔进行铰孔,以消除管孔上的纵向划痕,保证管孔的表面粗糙度为Ra1.6~Ra3.2。
每块折流板正、反面的管孔均要仔细倒角,清除毛刺,防止穿管时损伤管子的外表面。
把双管板和折流板按钻孔的方向顺序叠置,用换热管逐孔预穿。
4.2管束与壳体组装在壳体内组装拉杆、折流板,并进行穿管。
先组对第1组双管板,调整第1组双管板与壳体的垂直度和同心度。
在壳体内把拉杆装于内侧管板上,按钻孔的顺序组对折流板。
每装一块折流板,就从外侧管板密封面方向穿入梅花形的数组换热管。
其目的是自然调整折流板与管板的同心度。
待用螺母紧固折流板之后,可从折流板朝外侧管板方向穿入全部换热管。
最后组装另一组双管板,测量外侧管板和内侧管板的同心度、平行度和扭曲度及双管板之间距。
穿入全部换热管后,以外侧管板面为基准,调整换热管伸出管板面的长度为2~3mm。
双管板与换热管连接的顺序为,先胀接内侧管板与换热管,后焊接外侧管板与换热管。
4.3外侧管板与换热管焊接按焊接工艺要求,采用氩弧焊,先焊接第1层,进行压力为0.05MPa的气密性试验。
然后采用氩弧焊再焊接第2层,进行100%PT检查。
4.4压力试验首先按图样压力进行壳程的水压试验,从隔离腔的空间检查管子与内侧管板的连接质量。
壳程水压试验合格后,组焊隔离腔使之成为密闭的腔体,按图样压力进行水压及气密性试验。
最后对管程进行气压试验。
使用
经过从设计、试验、制造等一系列的严格运行下,最终圆满的完成了该再沸器的设计和制造,完成了最终的试验和检验,并在设备使用中收到良好的社会效益和经济效益。