汽车轮毂夹具说明书Word文件下载.docx
《汽车轮毂夹具说明书Word文件下载.docx》由会员分享,可在线阅读,更多相关《汽车轮毂夹具说明书Word文件下载.docx(11页珍藏版)》请在冰豆网上搜索。
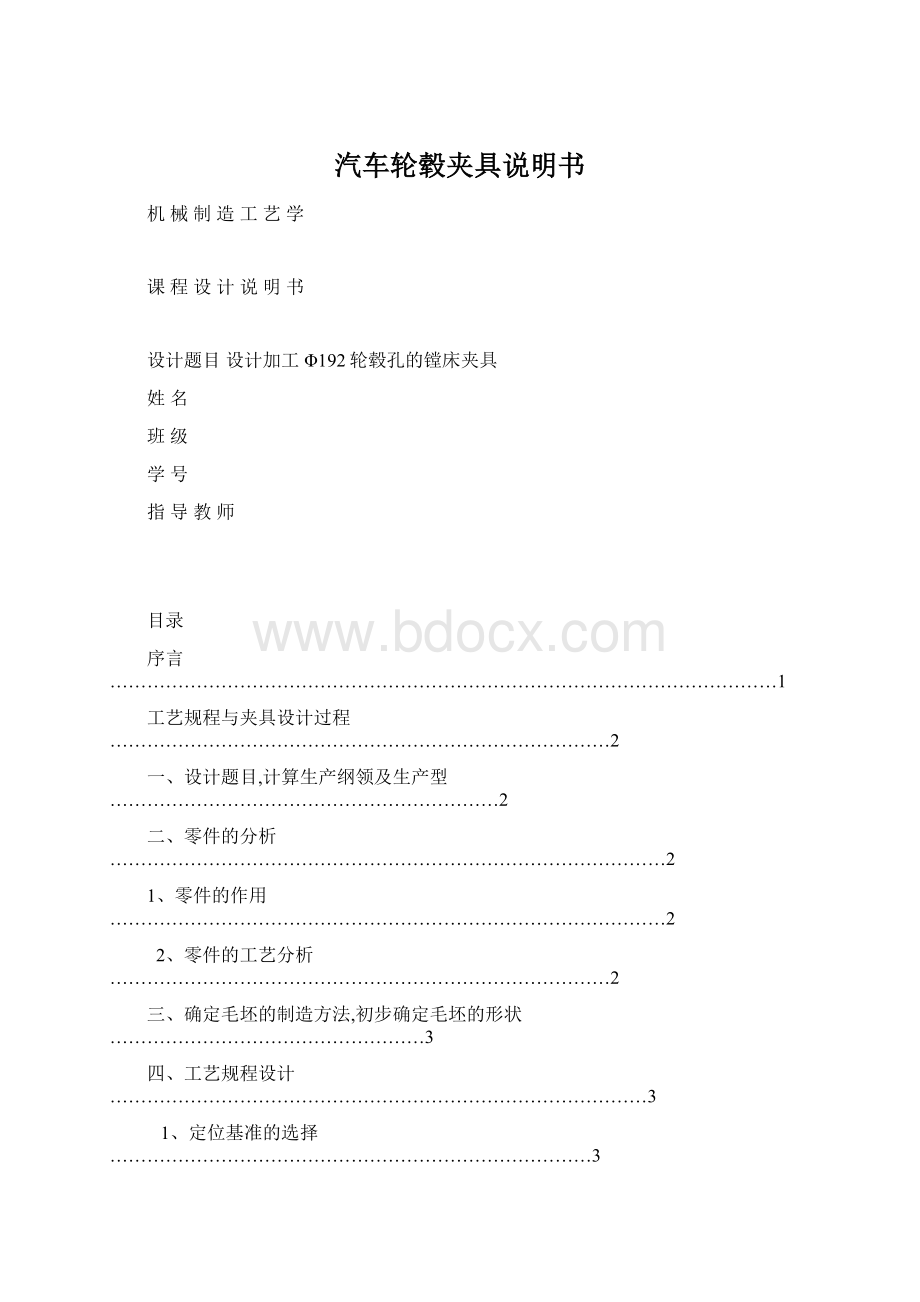
2、夹具设计的有关计算…………………………………………………………10
2.1、定位基准的选择……………………………………………………10
2.2、切削力及夹紧力计算………………………………………………10
2.3、定位误差分析…………………………………………………11
3、夹具结构设计及操作简要说明…………………………………………11
六、结束语…………………………………………………………………………………………14
七、致谢……………………………………………………………………………………………15
八、参考资料………………………………………………………………………………………16
工艺规程及机床夹具设计过程
一、设计题目:
轮毂零件的机械加工工艺规程及其镗孔专用机床夹具设计。
计算生产纲领,确定生产类型:
该零件是轮毂,按照指导老师的要求,设计此零件为中批量生产。
二、零件分析:
1、零件的作用:
轮毂是机器中的主要支撑及连接件,可以承受轮胎的重力和整个车身的重力。
轮毂的直径对行驶的影响和突出,因为车轮的直径是固定的,轮毂直径越大轮胎的胎壁就越扁平,在加速、刹车、转弯时轮胎的变形系数越小,行驶时就越稳定,万一爆胎时轮子的直径变化不是很大危害会有所降低。
2、零件的工艺分析
1、轮毂共有三组加工表面,它们之间有一定的位置要求
(1)车上端面B、下端面C、外圆表面D及外圆表面E
(2)镗
192mm内圆柱孔
(3)以
192mm内圆柱孔为中心在F端面上钻8个
12.5mm的孔并在C端面上钻8个对应的
12.5mm的孔。
2、位置要求:
(1)
12.5mm孔与其端面同轴度公差为
0.4mm
(2)M5螺纹孔与
192mm圆柱孔的中心线同轴度公差为
0.3mm
三、确定毛坯的制造方法,初步确定毛坯形状:
零件材料为45钢,考虑到零件需加工表面少,精度要求不高,有强肋,且工作条件差,既有交变载荷,又属于持续工作,故选用金属型锻件,以满足不加工表面的粗糙度要求及生产纲量要求。
零件形状简单,因此毛坯形状需与零件的形状尽量接近,又因内孔很小,不可锻出。
四、工艺规程的设计
1、定位基准的选择:
定位基准的选择是工艺规程设计中的重要工作之一,定位基准选择得正确与合理,可以使加工质量得到保证,生产率得以提高,否则,加工工艺过程中会问题百出,更有甚者,还会造成零件大批报废,使生产无法正常进行。
1、粗基准的选择:
该零件属于一般轴类零件,以外圆为粗基准就已经合理了(夹持长四点定位),为保证B面与孔轴线垂直,以便于保证以该两面为定位精基准时其它表面的尺寸精度加工要求,可以把B面与孔放在一个工序中加工,因而该工序总共要消除X,Y,Z,X,Y五个自由度(建立空间坐标系为:
以孔轴线方向为Z轴,垂直孔轴线,平行槽、花键、肋板对称线并且从槽180+0.012指向80+0.03的方向为X轴,同时垂直于X轴、Z轴的方向为Y轴,取坐标原点为孔轴线与A面的交点为原点),用三爪卡盘卡夹持外圆柱面。
消除X,Y,X,Y四个自由度,再用一个浮动支承顶住端面,消除Z自由度,达到定位要求。
⑵、精基准的选择:
主要考虑基准重合问题。
2、零件表面加工方法的选择:
本零件的加工面有端面、内孔、外圆表面、均布小孔等,材料为45钢,参考《机械制造工艺设计简明手册》(以下简称《工艺手册》)表1.4-7、表1.4-8及表1.4-17其加工方法选择如下:
⑴、端面B、C及外圆表面D、E:
根据GB1800-79规定毛坯的公差等级为IT13,表面粗糙度为Ra12.5um,要达到零件的技术要求,公差等级为IT9,表面粗糙度为Ra3.2um,需要经过车。
⑵、Φ192圆柱内孔:
公差等级为IT12,表面粗糙度为Ra6.3um,毛坯已经冲出孔,故采用镗
⑶、端面上的小孔:
零件技术要求表面粗糙度达到Ra12.5,钻即可满足要求
3、制定工艺路线:
制定工艺路线的出发点,应当是使零件的加工精度(尺寸精度、形状精度、位置精度)和表面质量等技术要求能得到合理的保证。
在生产纲领已经确定为中批量生产的条件下,可以考虑采用通用机床配以专用夹具并尽量使工序集中来提高生产率。
除此以外,还应当考虑经济效果,以便使生产成本尽量下降。
⑴、工艺路线方案一:
工序Ⅰ:
车上端面B
工序Ⅱ:
车下端面C
工序Ⅲ:
车外圆表面D
工序Ⅳ:
车外圆表面E
工序Ⅴ:
镗Φ192圆柱内孔,镗5×
45°
锥孔及镗Φ220的孔
工序Ⅵ:
钻上端面Φ12.5孔
工序Ⅶ:
钻下端面Φ12.5孔
工序Ⅷ:
去毛刺
工序Ⅸ:
终检
⑵、工艺路线方案二:
⑶、工艺方案的比较与分析:
上述两工艺方案的特点在于:
方案一工序Ⅰ、Ⅱ是以外圆表面为粗基准,用车床粗车B端面,然后再以B端面为基准钻孔。
方案二在该两工序中的定位加工方法也是相同的,只是在加工A端面时将铣床改用车床来加工,两个方案的定位方法都可以达到加工要求,但是从零件结构可知用铣床来加工在装夹时较困难,而用车床来加工在装夹时较方便。
另外,工艺路线一中是在完成前面4道工序后,才以外圆表面D、E及端面C及初外圆表面为定位基准来加工Φ192圆柱内孔,能较好的保证大孔的位置尺寸精度,而在工艺路线方案二中,先钻均布的16个小孔然后才镗Φ192圆柱内孔,这样就是重复采用粗基准定位,就不保证小孔与大孔的位置精度和对称中心,最终达不到零件技术要求,甚至会造成偏差过大而报废,这是重复利用粗基准而造成的后果。
通过以上的两工艺路线的优、缺点分析,最后确定工艺路线方案一为该零件的加工路线。
该工艺过程详见表2和表3,机械加工工艺过程卡片和机械加工工序卡片。
4、确定机械加工余量、工序尺寸及毛坯尺寸,设计、绘制毛坯图
⑴、确定毛坯余量(机械加工总余量),毛坯尺寸及其公差、设计、绘制毛坯图:
铸铁模铸造的机械加工余量按GB/T11351-89确定。
确定时根据零件重量来初步估算零件毛坯铸件的重量,加工表面的加工精度,形状复杂系数,由《工艺手册》表2.2-3,表2.2-4,表2.2-5查得,除孔以外各内外表面的加工总余量(毛坯余量),孔的加工总余量由表2.3-9查得,表2.3-9中的余量值为双边余量。
本零件轮毂材料为45钢,毛坯重量估算约为20kg,生产类型为中批量生产,采用金属型锻造毛坯。
①、B、C端面毛坯余量:
加工表面形状简单,由锻件重量为20kg,加工精度R12.5,保证长度尺寸为200mm,查《工艺手册》表2.2-4得单边加工余量为5.5mm,另查表1.4-24得长度尺寸公差范围为±
0.27,即长度方向毛坯尺寸为205.5±
0.27mm。
②、外圆表面D、E毛坯余量:
由毛坯重20kg,加工精度为3.2,加工表面形状简单,从孔的中心线到端面的长度尺寸为27mm,查《工艺手册》表2.2-4得单边余量为Z=5.5,另查表1.4-24得长度方向尺寸公差为±
0.195,即长度方向毛坯尺寸为32.5±
0.195mm。
③、孔Φ12.5mm均为实心,未铸造出来。
⑵、确定工序余量,工序尺寸及其公差:
确定工序(或工步)尺寸的一般方法是:
由加工表面的最后工序(或工步)往前推算,最后工序(或工步)的工序(或工步)尺寸只与工序(或工步)的加工余量有关。
前面已经根据有关资料查出零件各加工表面的加工总余量(即毛坯余量),将加工总余量分配给各工序(或工步)加工余量,然后由后往前计算工序(或工步)尺寸。
表1各加工表面的工艺路线、工序(或工步)、工序(或工步)
尺寸及其公差、表面粗糙度(未注单位:
mm)
加工表面
工序(或工步)名称
工序(或工步)余量
工序(或工步)基本尺寸
工序(或工步)经济精度
工序(或工步)尺寸及其偏差
表面粗糙度(um)
工序基本尺寸
公差等级
公差值
B面
半精车
Z=0.5mm
181
IT9
0.074
Ra3.2
粗车
Z=5
181.5
IT11
0.22
Ra6.3
毛坯
Z=5.5
186.5
IT13
0.54
Ra12.5
C面
Z=0.5
0.28
IT12
0.37
B端倒角
2×
0.21
C端倒角
0.39
外圆表面D
2Z=1
Φ221
0.084
2Z=10
Φ222
0.15
2Z=11
Φ232
外圆表面E
Φ310
Φ312
Φ322
镗Φ192圆柱孔
粗镗
2Z=6
Φ192
0.043
2Z=7
Φ186
0.18
镗Φ200圆柱孔
Φ200
IT8
0.023
5、确定切削用量及基本工时(机动时间)
在工艺文件中还要确定每一工步的切削用量。
(1)切削用量指:
背吃刀量asp(即切削深度ap)、进给量f及切削速度Vc。
(2)确定方法是:
确定切削深度——>
确定进给量——>
确定切削速度
(3)具体要求是:
①由工序或工步余量确定切削深度:
精、半精加工全部余量在一次走刀中去除;
在中等功率机床上一次走刀ap可达8~10mm。
②按本工序或工步加工表面粗糙度确定进给量:
对粗加工工序或工步按加工表面粗糙度初选进给量后还要校验机床进给机构强度
③可用查表法或计算法得出切削速度Vc查,用公式换算出查表或计算法所得的转速nc查,根据Vc查在选择机床实有的主轴转速表中选取接近的主轴转速n机作为实际的转速,再用换算出实际的切削速度Vc机填入工艺文件中。
对粗加工,选取实际切削速度Vc机、实际进给量f机和背吃刀量asp之后,还要校验机床功率是否足够等,才能作为最后的切削用量填入工艺文件中。
五、夹具设计
为了提高劳动生产率,保证加工质量,降低劳动成本,需要设计专用夹具。
按指导老师的布置,设计第Ⅴ道工序——镗Φ192圆柱内孔,镗5×
锥孔及镗Φ220的孔。
本夹具将用于CA6140,刀具为YG6硬质合金镗刀,对工件内孔进行加工。
1、问题的提出:
本夹具主要用于第Ⅴ道工序镗Φ192圆柱内孔,镗5×
锥孔及镗Φ220的孔,由于该孔精度要求高,所以,在本道工序加工时,应该考虑其精度要求,同时也要考虑如何提高劳动生产率。
2、夹具设计的有关计算:
⑴、定位基准的选择:
由零件图可知,Φ192圆柱内孔中心线有平行度要求,与B端面有垂直度要求。
为了使定位误差为零,应该选择以端面为定位基准的夹具。
但这种定心夹具在结构上将过于复杂,因此这里只选用以外圆表面主要定位基面。
⑵、切削力及夹紧力计算:
刀具:
YG6硬质合金端铣刀
(见《切削手册》表3.28)
其中:
CF=54.5,ap=4.5,XF=0.9,fZ=0.18,YF=0.74,ae=28,UF=1.0,d0=100,qF=1.0,n=255,WF=0,Z=10
∴F=54.5×
4.50.9×
0.180.74×
28×
10/(100×
2550)≈166.1(N)
水平分力:
FH=1.1F实≈182.7(N)
垂直分力:
FV=0.3F实≈49.8(N)
在计算切削力时,必须安全系数考虑在内。
安全系数:
K=K1K2K3K4。
K1=1.5K2=1.1K3=1.1K4=1.1
∴F/=KFH=(1.5×
1.1×
1.1)×
182.7=364.8(N)
实际加紧力为F加=KFH/(U1*U2)=364.8/0.5=729.6(N)
其中U1和U2为夹具定位面及加紧面上的磨擦系数,U1=U2=0.025
螺母选用M16X1.5细牙三角螺纹,产生的加紧力为
W=2M/D2tg(a+6055)+0.66(D3-d3)/(D2-d2)
M=19000N.MD2=14.8mma=2029,D=23mmd=16mm
解得:
W=1O405(N)
此时螺母的加紧力W已大于所需的729.6的加紧力F加,故本夹具可安全工作。
心轴取材料为Q235
查表得Q235的许用弯曲应力为:
158Mpa
弯曲应力=M/Wz=32FL/3.14d3=99.4X32X0.028/[3.14X(0.022)2]
=2.67<
<
许用弯曲应力158Mpa
(3)定位误差分析
由于槽的轴向尺寸的设计基准与定位基准重合,故轴向尺寸无基准不重合度误差。
径向尺寸无极限偏差、形状和位置公差,故径向尺寸无基准不重合度误差。
即不必考虑定位误差,只需保证夹具的花键心轴的制造精度和安装精度。
且工件是以内孔在心轴上定位,A端面靠在定位块上,该定位心轴的尺寸及公差一现规定为与零件内孔有公差相同,就是Ф220.28mm。
因为夹紧与原定位达到了重合,能较好地保证了车端面D所得到的尺寸和孔中心线的尺寸和公差要求。
3、夹具结构设计及操作简要说明:
如前所述,在设计夹具时,应该注意提高劳动率。
为此,在螺母夹紧时采用开口垫圈,以便装卸,夹具体底面上的一对定位键可使整个夹具在机床工作台上有正确的安装位置,以利于铣削加工。
结果,本夹具总体的感觉还比较紧凑。
结束语
机械的加工工艺及夹具设计是在完成了大学的全部课程之后,进行的一次理论联系实际的综合运用,使我对专业知识、技能有了进一步的提高,为以后从事专业技术的工作打下基础。
机械加工工艺是实现产品设计,保证产品质量、节约能源、降低成本的重要手段,是企业进行生产准备,计划调度、加工操作、生产安全、技术检测和健全劳动组织的重要依据,也是企业上品种、上质量、上水平,加速产品更新,提高经济效益的技术保证。
然而夹具又是制造系统的重要组成部分,不论是传统制造,还是现代制造系统,夹具都是十分重要的。
因此,好的夹具设计可以提高产品劳动生产率,保证和提高加工精度,降低生产成本等,还可以扩大机床的使用范围,从而使产品在保证精度的前提下提高效率、降低成本。
当今激烈的市场竞争和企业信息化的要求,企业对夹具的设计及制造提出了更高的要求。
在设计中,需要对零件加工工艺方案和夹具进行设计,在确定加工工艺方案时,可能会出现工艺路线的不合理,甚至出现不能保证加工所要求达到的精度。
在进行夹具设计时,可能因定位基准选择不合理,出现过定位或欠定位造成加工的零件的精度得不到保证。
在选择夹紧机构时由于机构的大小,尺寸等不合理,而达不到夹紧的目的,也可能因夹紧力作用点或作用面的位置不合理而使工件产生翻转。
所以在设计过程中应制订多套方案,以供比较选择最优,同时还要多请教指导老师和同学,并多查阅相关的书籍来尽可能好的完成设计。
在机械制造中,为完成需要的加工工序、装配工序及检验工序等,使用着大量的夹具。
利用夹具,可以提高劳动生产率,提高加工精度,减少废品,可以扩大机床的工艺范围,改善操作的劳动条件。
因此,夹具是机械制造中的一项重要的工艺装备。
夹具设计的基础理论一个好的机床夹具,首先要保证能加工出合格的产品。
为此,所设计的夹具首先应满足以下两项要求:
第一,在未受外力作用时,加工件对刀具和机床应保持正确的位置,即加工件应有正确的定位。
第二,在加工过程中,作用于加工件上的各种外力,不应当破坏加工件原有的正确定位,即对加工件应有正确的夹紧。
主要参考资料
[1]
孙丽媛,机械制造工艺及专用夹具设计指导,北京:
冶金工业出版社,2002。
[2]东北重型机械学院等,机床夹具设计手册,上海:
上海科学技术出版社,1979。
[3]
刘守勇等,机械制造工艺与机床夹具.
北京:
机械工业出版社,1994.7
[4]
王启平,机床夹具设计[M].哈尔滨:
哈尔滨工业大学出版社,1988.
[5]
林文焕.陈本通,机床夹具设计[M].北京:
国防工业出版社,1987.
[6]
徐发仁,机床夹具设计[M].重庆:
重庆大学出版社,1996.7
[7]
王昆等,机械设计课程设计[M].武汉:
高等教育出版社,1995
[8]
邱宣怀,机械设计[M].第四版.北京:
高等教育出版社,1997
[9]
柯明扬,机械制造工艺学[M].
北京航天航空大学出版社,1995
[10]孟少龙,机械加工工艺手册第1卷,北京:
机械工业出版社,1991。
[11]《金属机械加工工艺人员手册》修订组,金属机械加工工艺人员手册,上海: