轨道大巷掘进作业规程Word下载.docx
《轨道大巷掘进作业规程Word下载.docx》由会员分享,可在线阅读,更多相关《轨道大巷掘进作业规程Word下载.docx(42页珍藏版)》请在冰豆网上搜索。
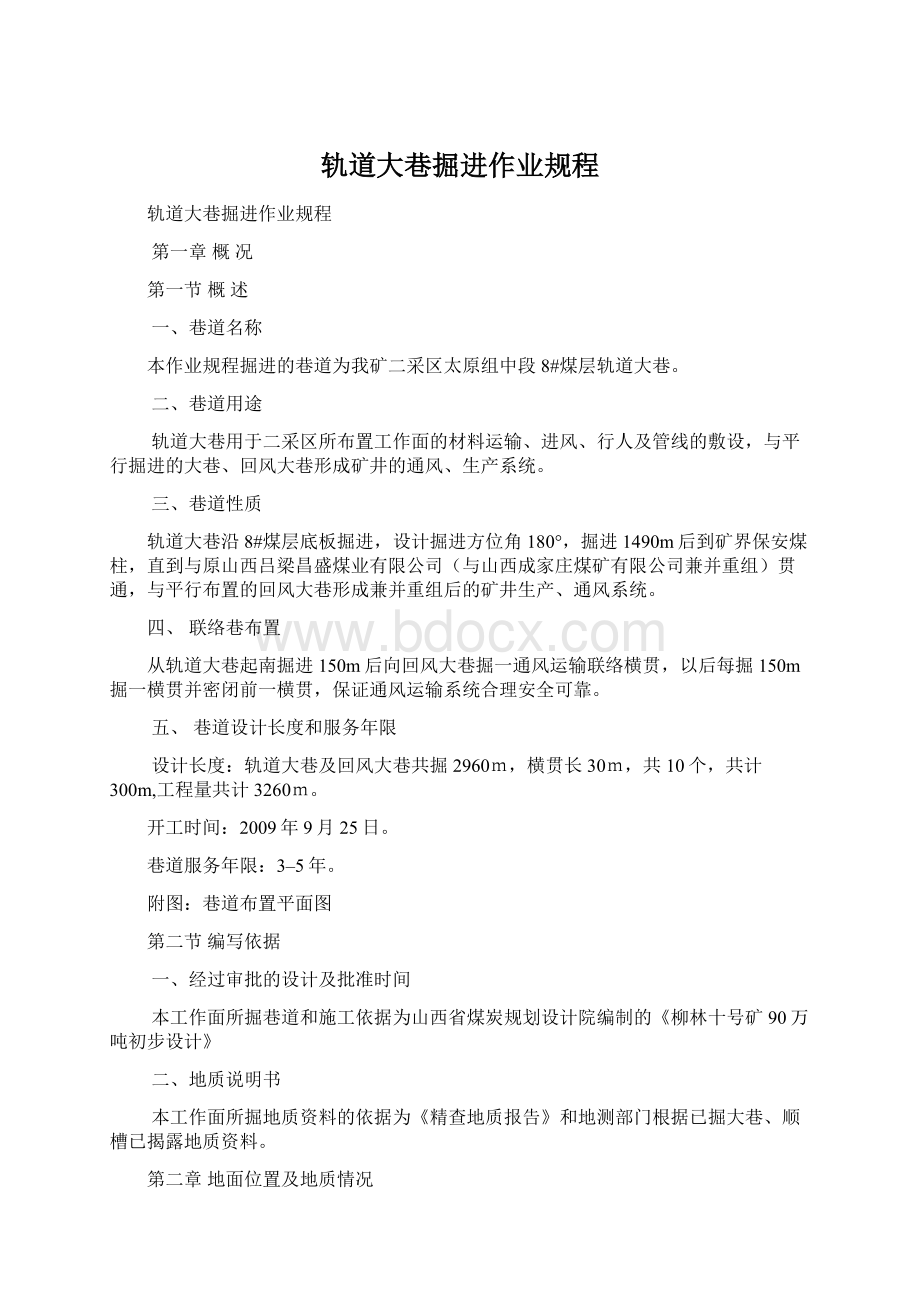
—6°
,属可采稳定性近水平厚煤层。
工作面煤层柱状图
第3节地质构造
顶底板情况见表2—2
煤
层
顶
底
板
类别
岩石名称
厚度/m
岩性特征
老顶
石灰岩
5–8
坚硬
直接顶
–4.0
直接底
泥岩、砂质泥岩
1–
较坚硬
本工作面顶板属I类II型,大致东西走向,倾向西南。
本掘进大巷位于我矿Ⅱ采区南翼,根据精查报告说明地质构造简单,属稳定的Ⅰ类Ⅰ型煤层,顶板属中等垮落Ⅰ类II型顶板;
根据开采实际情况揭露预计本掘进大巷工作面可能存在溶洞裂隙,无其它地质构造。
煤层特征见表2—3表2---3
指标
数值
备注
煤层厚度/m
2.6—2.2m
夹矸厚0.2—0.6
煤层倾角/(°
)
2—6°
/4°
倾向南东—北西
煤层硬度/f
3—4级
摩氏硬度
煤层构造
层理发育
构造简单,未发现断层
节理发育
局部地段发现裂隙
绝对瓦斯涌出量(m3/min)
0.46
属低瓦斯矿井
相对瓦斯涌出量(m3/T)
1.467
煤层爆炸指数
24%
煤层具有爆炸性,不易自燃
地温
17℃
地压
正常
无冲击地压
第四节水文地质情况
本区内主要含水层有奥陶系碳酸盐岩溶裂隙含水层,石碳系上统太原组灰岩岩溶裂隙含水层,上第三系、第四系孔隙含水层,现掘8#煤层的直接充水层为石灰岩岩溶裂隙含水层,其次在开采过程中产生的塌陷裂隙带,在其局部地段接近上第三系上新统底砾岩及风化裂隙水的充水补给,矿区内无常年性河流,只在雨季有短暂性流水补给。
根据三交详查区水文地质资料,奥灰水位标高最高为803m,水流方向为西南,本井田10#煤层底板标高最低为770m,仅在西部存在局部承压开采,现开采8#煤层赋存于10#煤层之上,不存在奥灰水水患。
矿井井口标高都高于历年洪水位线以上15m,因而在掘进过程中无水患影响。
该掘进工作面四邻水文情况,掘进工作面北接集中轨道巷,东面为实体煤田,南部为兼并重组后轨道大巷,四邻均无采动情况,因而总体预计该掘进工作面水文地质条件简单,不存在水患威胁。
第三章巷道布置及支护说明
第一节巷道布置
该掘进大巷布置于石炭系上统太原组8#煤层,巷道沿煤层掘进,轨道巷开口位置在Ⅱ采区集中轨道巷南,开口真方位角为180°
00′00"
,巷道净断面规格为4.0×
3.0m,断面积为12m2,采用锚网喷支护。
该大巷与轨道大巷、回风大巷平行掘进,掘1500m(约)到矿界保安煤柱,直到与原山西吕梁昌盛煤业有限公司专用回风井贯通,形成资源整合后的通风、生产系统。
第二节矿压观察
我矿8#煤层顶板岩性为石灰岩,岩性坚硬,顶板稳定。
但在掘进过程中必须进
顶板压力观察,具体观察方法如下:
1、观察对象:
轨道大巷顶底板、煤邦。
二、观察内容:
巷道顶板离层量(下降);
底板相对移近量(底鼓);
两帮相对移近量(片帮);
锚杆、锚索的载荷及锚固力(拨拉);
扭矩等。
三、观测方法
1、测点布置:
正常情况下从轨道大巷开口后5米起每70±
5m,做一观察基点对巷道顶底板、两帮移近量观测。
用钢尺量,每周观察一次,观察基点尽量选在顶板完好无淋水地段。
2、用LC—280测力器检测顶、帮锚杆锚索锚固力,用力矩板手检查扭力是否达到要求。
每月进行三次拉拔测试,且每次抽查每组不少于3根,所测数据记录在册。
四、数据处理
由质量标准化办公室负责检测记录和数据分析处理。
第三节支护设计
一、巷道断面
运输大巷、回风大巷均采用“锚杆+钢带+金属菱形网+锚索”联合支护,断面为矩形,横贯采用“锚杆+梯子梁+金属菱形网”。
运输大巷净宽4m,高3m、回风大巷断面为:
5m,高3m,横贯断面为:
宽3m,高3m.
附图:
巷道断面支护图
(二)支护方式
采用“锚杆+钢带+金属菱形网+锚索”联合支护,支护材料为螺纹钢树脂锚杆、220-3-5000-5-1000W型钢带、金属菱形网、高强度低松驰预应力钢绞线锚索、一次性圆钢锚杆或可回收铁质锚杆等材料,并喷浆加固支护,喷浆厚度为100㎜.
二、支护设计
(一)设计方法
根据目前的情况,结合已施工巷道的经验数据,采用工程类比法进行该面锚杆支护设计。
(二)类比工程的选择和比较
82201工作面回风顺槽、轨道巷均采用锚杆、锚索支护,现正在已掘进完成。
目前工作面整体状况良好,能够满足安全及生产需要。
82201工作面与轨道大巷工作面位于同一区、同一煤层,顶板岩性比较接近,且位于82201工作面以西,所以选择82201工作面作为皮带运输大巷掘进工作面支护设计的类比对象是合适的,其工作面回风顺槽、皮带顺槽的支护参数对轨道大巷的锚杆支护设计有重要的参考价值。
(三)锚杆支护长度计算
L=KH+L1+L2=2×
0.7+0.3+0.05=1.75m
式中L--锚杆总长度m
H--直接顶不稳定岩层厚度(取0.7m)
K--安全系数一般取2
L1--锚杆锚入稳定岩层的深度一般取0.2-0.3m
L2--锚杆外露长度一般取0.05m
为安全起见锚杆长度取2.0m。
2、锚杆的间排距确定
对于无预应力的锚杆,要求每根锚杆承担岩石的重量,要
小于或者等于锚固力或杆体拉断力的较小值。
即KHDR≤Q,锚杆支护面积应为D≤Q÷
(HDR)
式中D—锚杆支护有效面积
Q—Ф18mm的钢锚杆锚固力或杆体拉断力的最小值为50KN,约5.1吨
K—安全系数取2
H—不稳定岩层厚度(取0.7m)
R—岩层平均容重取2.6T/m3
经计算D≤Q÷
(HDR)≤5.1÷
(0.7×
2×
2.6)≤1.4m2
根据巷道断面规格,锚杆排距定为1.2m,锚杆间距则为1.0m,支护面积小于1.4m2。
根据以上计算确定选用2.0m长的钢锚杆,快速树脂锚固剂端头锚固力最小值为50KN/根的螺纹钢金属锚杆,完全可以控制顶板。
风动锚杆机进行支护。
1、本工作面煤层顶板为石灰岩及砂质泥岩。
2、根据顶锚杆通过吊悬作用组合梁,达到支护效果的条件,应满足:
L≥L1+L2+L3
式中:
L—锚杆总长m
L1—锚杆外露长(钢带厚度3mm+托板厚度25mm+螺母厚度24mm+间隙富裕5mm,顶锚杆外露40mm,总外露长度取100mm)
L2—有效长度(顶锚杆取免压拱高)
L3—锚入岩层内深度(顶锚杆取300mm)
普氏免压拱高
b=[B/2+Htan(45°
-W帮/2)]/f顶
f顶—顶板岩石普氏系数P取=2
B--宽度
W帮—两帮围岩的内摩擦角取63.43°
b=[4000/2+3000×
tan(45°
-63.43/2)]/2=1979mm
依据上述公式计算得出:
顶锚杆长L顶≥2500mm(0.1+0.3+1.979≈2.5)
固L取:
2.5m
3、按锚杆所能悬吊的重量确定排、间距:
a=(Q/KRL2)1/2
a—锚杆排间距
Q—锚杆锚固力70KN
K—安全系数2.5
R—岩体容重2.8×
103kg/m3
L2—普氏免压拱高度
L2—B/2F2
B巷道掘井宽度4m
F2—顶板岩石普氏坚固系数Fr=2
L2=4/(2×
2)=1.0m
a=[70×
1000/(2.5×
2.8×
1000×
1.2×
9.8)]1/2=0.922
故取a=0.8m和1m间排距的2倍小于锚杆长度。
(四)支护材料的选择
1、轨道大巷支护设计为:
锚杆+钢带+金属菱形网+锚索联合支护,两邦采用可回收钢杆质锚支护,并进行喷浆加固支护,支护厚度0.1m.
⑴顶板采用锚网配合梯子梁支护。
锚杆规格为Φ20×
L=2000mm,间、排距为1000×
1200mm,每根锚杆采用两节
MSCK2340型树脂锚固剂,菱形金属网规格为1200×
4000mm,采用12号铁丝编制。
⑵巷邦采用3根塑料胀套圆钢锚杆加挂金属网配合支护。
锚杆长度为2000mm.两煤帮支护间、排距1000mm×
1200mm,呈矩形排列,距顶往下300mm处打一根锚杆,仰角15°
,其余按间距1000mm各打一根,最后一根锚杆向下25°
,中间一根均垂直打入到巷帮。
巷帮所挂金属菱形网规格为1200×
3000mm。
⑶顶部布置双排锚索加强支护,锚索规格为6000—Φ15.24—7股,有效长度为5.8m—5.85m,每根锚索采用4支MSCK2340型树脂锚固剂锚固,每两根锚杆打一锚索,配套厚14mm,200mm×
200mm,中孔Φ16型钢板。
2、横贯为:
锚杆+梯子梁+金属菱形网+托板联合支护
⑴顶板采用锚网配合梯子梁联合支护。
⑵锚杆规格为Φ20×
L=1800mm,间、排距为1000×
1200mm,每根锚杆采用两节MSCK型树脂锚固剂。
⑶巷帮采用6根Φ20×
L=1800型一次性圆钢锚杆加挂金属网配合梯子梁支护。
每根锚杆采用一节MSCK2340型树脂锚固剂。
两煤帮支护间距1000mm,排距为1200mm,呈矩形排列;
距顶往下300mm处打一根锚杆且仰角15°
,其余从上往下按间距1000mm各打一根,其最后一根锚杆向下25°
。
支护材料见表3—2
表3—2
材料名称
规格
材质
用途
帮锚杆
Ф20×
2000
螺纹钢
支护巷帮
顶锚杆
护顶
锚索
6000-Ф15.24-7股
钢绞线
树脂锚固剂
Ф23
MSCK2340
锚固剂
托盘
Ф130100、中孔Ф2216
圆钢
护帮、顶
钢带
220-3-5000-5-1000W
170-3-3000-4-650W
钢板
梯子梁
3m
10号钢筋
护顶、帮
金属网
1200×
3000菱形网
12#铁丝
(五)质量标准与检验
1、各级领导必须坚持“安全第一,质量为本”的原则,狠抓基础工作,严格质量检验制度,消灭不合格品,实现质量标准化。
2、工程质量检查及评级严格按有关标准执行。
3、技术科对队组进行定期抽查,每月三次,队组质量验收员必须班班验收工程质量并进行登记和办理交接班手续。
4、必须坚持对安全质量不合格的工程“返工处理”的原则。
质量标准与检验见表3—3表3—3
项目
设计长度
允许偏差
巷道宽/㎜
4000
-30-100
巷道高/㎜
3000
合格
优良
锚杆扭力矩/Nm
顶≥100
符合设计要求
帮≥40
锚杆间排距/㎜
顶1000×
800
±
100
帮1000×
锚杆锚固力/KN
顶≥70
符合设计
帮≥30
锚杆角度/(°
见支护断面图
5
锚杆外露长度/㎜
40
≤40
锚索间排距/㎜
2400×
50
锚索外露长度/㎜
350
≤350
锚索初锚力/KN
≥200
备注:
锚杆、锚索的扭力矩、锚固力每50m检查一组,每根锚杆、锚索支护质量必须符合达到设计标准,总合格率达到90%以上为合格,合格率低于90%以下必须全部重新加固。
第四节支护工艺
掘进综掘机、落煤、出煤,掘进循环进尺0.6m,永久支护每掘进一循环支护一次;
永久支护顶板每循环(0.6m)支护一次;
两帮支护滞后工作面不大于10m;
顶锚索加强支护滞后工作面不大于30m,顶板破碎或地质变化带顶帮支护全部每循环永久支护一次紧跟工作面。
严禁空顶作业。
1、安装顶板锚杆
⑴施工顶板锚杆眼,采用MYT—120C2、Φ20mm钻头、B—IP系列可接长钻杆风动锚杆钻机,按梯子梁眼位由巷道中间向两帮施工锚杆眼,锚杆眼深度为1.70~1.75m。
打眼时要将锚杆机放平、垫稳、垂直于顶底板打眼。
⑵送树脂锚固剂,向锚杆眼内装入两个MSCK2340型树脂锚固剂,装好后用锚杆缓慢地推入孔底。
⑶搅拌树脂锚固剂:
用连接套将钻机与锚杆销螺母连接起来,然后升起钻机。
推进锚杆送到孔底后,停止升钻机,搅拌20—30S后停机,然后撤钻,防止未凝固自然下垂。
⑷安装锚杆:
15分钟后挂网、上钢带、安装托盘紧固锚杆,并用力矩扳手检查紧固力不小于100Nm.
⑸在顶板与钢带之间铺设单层金属菱形网,规格:
L×
B=5000×
900mm,金属网长边垂直巷道掘进方向铺设,长边对接,短边搭接150mm,用双股14#铁丝呈“三花”型连接,连接扣间距100mm;
也可以用成形铁丝直接穿接,要求金属网平整、拉紧、贴顶、不留网包。
2、安装帮锚杆:
⑴砍壁修整巷道两邦,为防止巷道片邦先砍两邦上部成型后打眼安装上部两排锚杆,安装好后再支设下部。
⑵两帮联接金属网,联接方式同顶锚杆。
⑶按设计部位施工打帮锚杆眼:
采用风动锚杆,1.8m长钻杆φ42mm钻尖打1.7m深钻孔,抖动钻杆排净煤粉。
⑷安装帮锚杆:
使用可回收倒楔式塑料胀套锚杆,先将塑料胀壳楔拧在锚杆上轻轻插入孔内用6分圆钢管套在锚杆上轻击将塑料胀壳加紧塞入孔底,然后挂好网,木托板及铁托盘拧满扣,使其撑开塑料壳与钻孔壁楔紧。
安装锚杆:
15分钟后安装木托板紧固锚杆,并用力矩扳手检查紧固力不小于40kN(可回收锚杆为30kN),锚杆外露长度≤400mm。
3、锚索安装
⑴锚索为加强支护,但机掘巷道滞后于工作面不能大于30m。
⑵安装锚索
A、锚索孔施工:
拉线定位(按钢带眼距控制)后,采用MYT—120C2、28mm钻头、B—IP系列可接长钻杆打眼,眼深为5.8-5.85m。
B、送树脂锚固剂:
向孔中装入4个MSCK型树脂锚固剂,用规格为6000-Φ15.4-7股钢绞线慢慢将树脂锚固剂推进。
C、搅拌树脂锚固剂:
用连接套将锚杆钻机与钢绞线连接起来,然后升起钻机推进,直至推入孔底,停止升钻机,搅拌30—40S后停机,加设小木楔,撤钻。
D、安装:
两人合作将钢带按锚索孔穿过固定好,然后上锚索锁具。
E、张拉钢绞线:
24小时后拉千斤顶张拉钢绞线,初锚力达到200KN。
安装完毕进入下一循环。
F、顶锚索钢带按规定间排距安装且相互搭接,连成一片。
4、支护形式
(1)工作面支护方式
①顶板完整,直接采用“锚杆+金属网+钢带+锚索”联合支护,永久支护每割一循环(0.6m)紧跟工作面掘进,顶锚杆距工作面的最大距离为0.8m,最小距离为0.2m,锚网永久支护代替了落后的吊环式临时支护。
②顶板压力过大或局部破碎时,顶锚杆排距缩小为800mm,小循环作业支护,缩小空顶距离。
临时支护与永久支护关系平面图
5、锚杆支护技术要求:
(1)使用标准支护材料,钢带规格为4m长的W型钢带,顶锚杆为Φ20mm,L=2000mm高强度螺纹钢锚杆,帮锚杆为Φ20mm,L=2000mm可回收倒楔式铁质锚杆,锚索规格为6000—Φ15.24—7股高强度低松驰预应力钢绞线。
(2)风动锚杆钻机或煤电钻打眼时,必须垂直顶底板打眼,非工作人员不得靠近。
(3)顶部金属网规格为4000mm×
900mm,帮部金属网规格为3000mm×
1200mm,网与网重叠搭接不小于150mm,用双股14#铁丝呈“三花”型连接,连接扣间距不大于100mm。
(4)顶帮锚杆托盘必须紧贴岩面,锚杆扭力矩达到设计要求。
(5)顶锚杆每根使用MSCK型树脂锚固剂2卷,锚索每根使用MSCK型树脂锚固剂4卷。
(6)锚杆、锚索搅拌时间为20—45s,搅到眼底后,必须保持推力2min后才能松锚杆钻机。
(7)锚杆、锚索必须做拉力试验,巷道必须做点定期量取顶板下沉高度。
(8)锚杆眼位必须量取定点,工作面应配备长短两种钻杆(直径相同)采用短打长套,以保证锚杆设施角度和深度。
(9)过断层或顶板破碎带时,锚杆支护改为钢棚支护,工字钢棚缩小棚距,棚距为0.6-0.8m。
(10)发现不合格或失修的锚杆,必须及时补修。
第四章施工工艺
第一节施工方式
1、轨道大巷采用综掘机掘进,与回风大巷之间的横贯采用炮掘方式掘进。
2、首先完善通风系统、进排水管路和出煤、运料系统。
3、然后调整刮板输送机、皮带输送机。
4、根据技术科给定的开口位置及中线施工。
第二节掘进作业
一、机掘施工方式
1、综掘工艺流程
综掘机截割工艺流程图与截割程序图。
操作顺序:
安全检查—校正激光指向仪标定中腰线—启动油泵电机—启动第二运输机—启动第一运输机—启动星轮—启动截割头—截煤—装运煤—临时支护—永久支护—清理—接刮板
(一)、综掘机结构
①、截割部电机150kw,截割头最大直径755mm,长685mm,循环进度0.6m
②、铲板部铲板宽度2.8m
③、第一输送机
④、本体部
⑤、行走部
⑥、后支承
⑦、水系统
⑧、润滑系统
⑨、电控部输入电压1140v/660v
⑩、液压系统液压油箱容积500L,泵站由75kw电机驱动。
本机共有11个油缸。
整机尺寸:
长9340mm,宽2900mm,高1650mm
作业范围:
截割高度4800mm,宽度5400㎜
2、施工顺序:
安全检查→延伸皮带→综掘机切割出煤→敲帮问顶→临时支护→打锚杆眼安装锚杆进行永久支护→收尾(整理工程质量标准化)。
⑴安全检查
①严格执行交接班制度,及时处理上一班遗留的隐患。
②对工作面所有设备进行检查,确保能正常运转。
③检查工作面瓦斯,将探头挂在规定位置。
④对上一班的工程质量进行检查。
⑵延伸皮带
①每个生产班在割煤前必须延伸皮带,延伸皮带机尾掘进机联接钢丝绳的方式进行,各联接部位必须牢固,钢丝绳绳头用不少于3个绳卡固定。
②掘进机司机、皮带延伸作业人员必须与皮带机头张紧绞车工用电话密切联系,互相配合好。
延伸前必须先开动皮带机头张紧绞车,将储带仓里的皮带松开。
③掘进机司机必须密切观察掘进机运行及皮带机尾的移动情况,发现问题立即停止作业及时处理。
④钢丝绳摆幅范围及皮带机尾前移方向严禁有人。
⑤皮带机尾延伸前必须备好足够的皮带管、架。
⑥皮带机尾到位后,掘进机后退5m,将掘进机切断电源、闭锁开关,拆开钢丝绳。
⑦然后将皮带机尾用地锚或其它方式固定牢固,安装好皮带管、架后将皮带涨紧。
⑶截割方法
根据工作面煤层中部含有夹矸的实际情况,截割时先从中底部煤层(左方)切割掏窝槽,然后从左向右自下而上截割。
开掘窝槽时,先转动截割头依靠掘进机行走履带,伸缩油缸和升降油缸完成掏槽工作,每次截深为600mm,当窝槽的开掘工作完成以后,关闭行走马达,让装载部与刮板输送机工作,使铲板紧贴底板,并落下后部稳定器将掘进机略微抬高,使机器在切割过程中有良好的稳定性。
驱使转动的切割头,根据巷道断面的宽度水平摆动开掘横槽,切割头移动到位后,使其开高一个距离,每次跨距不大于600mm,接着驱使切割头水平摆动。
重复以上动作,直至完成整个断面的切割工作。
每完成一个大循环(2.4m)后,驱动机头上下移动,切割使煤壁平直。
⑷敲帮问顶
掘进完一个大循环后,停机闭锁,把截割头放在底板上,然后由带班长用长柄工具进行敲帮问顶,发现顶帮有离层现象应及时有效的进行处理,并把工作面的浮矸、活矸、伞檐处理掉,确保作业场所的安全,方可组织其它工序,敲帮问顶人员必须站在顶板支护完好区域内进行。
⑸永久支护工艺见第三章第四节支护工艺。
⑹收尾
①清理工作面浮煤、巷道卫生。
②将工作面管线、工具、设备悬挂摆放整齐。
③进行工程质理管理工作,巷道断面、支护质量符合设计要求。
3、掘进机使用安全注意事项;
⑴司机必须经过培训持证上岗,无关人员不得擅自开机。
⑵截割头必须在旋转情况下才能向煤壁钻进。
⑶当截头已钻进煤岩壁里时,不允许启动截割电机,须先退出后,方可启动。
⑷需振动时必须等振动正常后,才能进行切割。
遇到坚硬岩石时应当减小切割深度,不允许长时间空开振动。
切割时必须将铲板放下后支撑打起,以增加其稳定性。
⑸掘进面为半煤半岩时,应先破煤再破岩,破岩时必须将五联阀组的进给速度变换手柄推入,方可缓慢地切割岩石。
⑹大块掉落煤岩,需用破碎后再装载,不能用刮板机强拉。
⑺工作时若有不正常的声响,应立即停机检查,查明原因排除故障后才允许开机。
⑻当发现液压系统压力值严重波动,溢流阀经常开启,系统有噪音和严重发热时,应立即停机检查。
⑼油箱油温超过70℃时,须降温后再开机工作。
⑽载割头在工作时,若遇闷车现象,应立即停机,以防切割电机的损坏。
⑾载割前必须提前3分钟发出警报,载割过程中,掘进机左右两侧及迎头严禁有人。
⑿掘进机使用维护按《EBJ—120TP型悬臂式掘进机使用维护说明书》执行。
⒀掘进机必须装有前照明灯和尾灯。
⒁掘进机更换大部件时,所使用导链的负载能力必须大于部件重量,导链要挂在牢固可靠的支护上。
⒂综掘机司机必须根据巷道中线进行截割,严禁超控超割破坏顶底板及两邦煤壁,最后支护必须由人工砍壁成型。
二、炮掘施工方式
1、横巷施工时采用钻眼爆破法施工。
炮掘时采用先拉槽后刷帮压顶的方法。
2、钻眼放炮工艺流程
钻眼前的准备→检查瓦斯→钻眼→装药联线→检查瓦斯→撤人放警戒→爆破→检查瓦斯及爆破效果→洒水降尘、维护顶板→临时支护→出煤→永久支护。
3、爆破说明书
采用ZM-150D型煤电钻,1200mm钻杆,Φ45mm的钻头打眼,使用MFB-100型发爆器,2级煤矿许用乳化销安炸药,煤矿许用瞬发或毫秒电雷管正向