课程设计Word格式文档下载.docx
《课程设计Word格式文档下载.docx》由会员分享,可在线阅读,更多相关《课程设计Word格式文档下载.docx(8页珍藏版)》请在冰豆网上搜索。
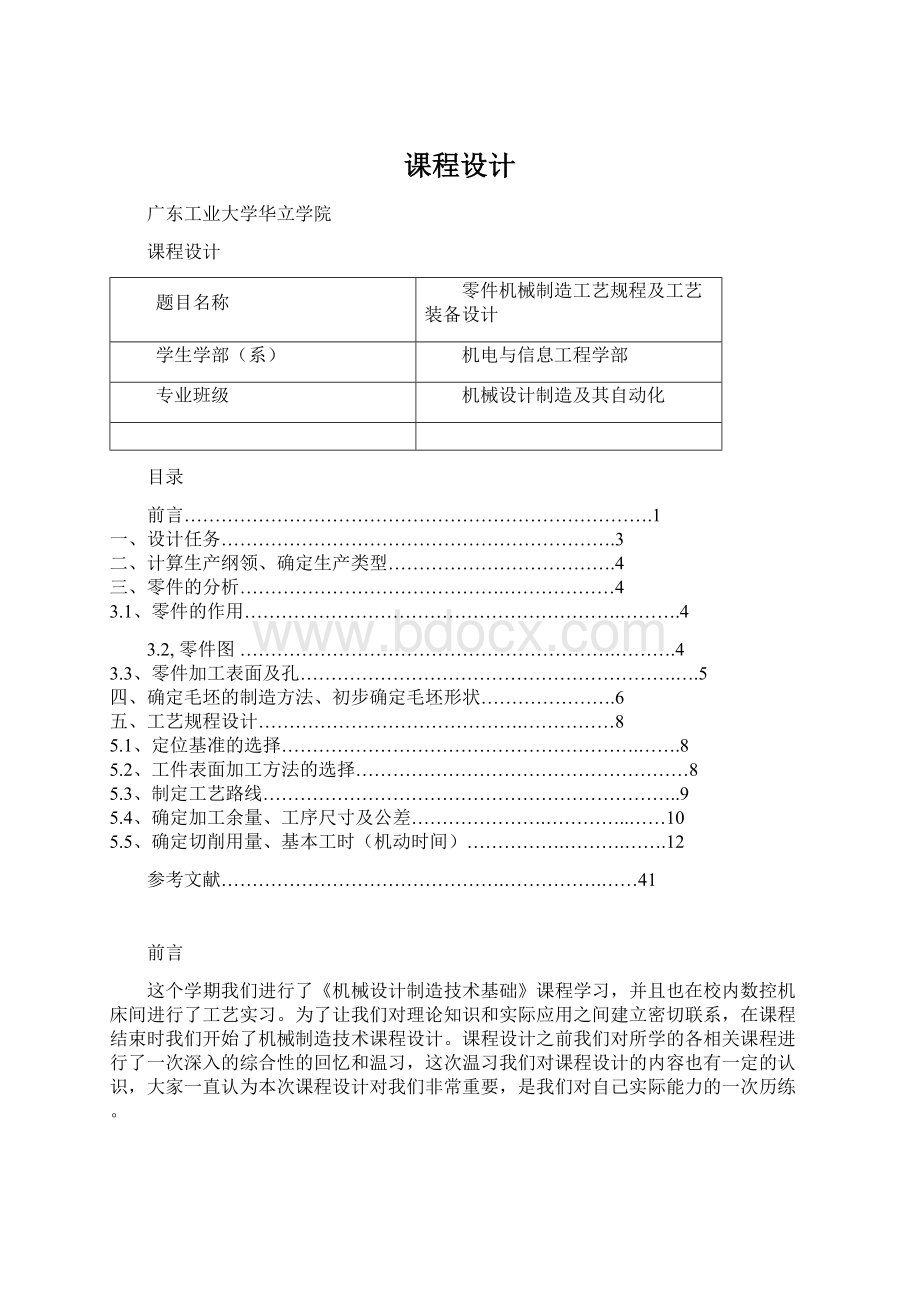
5.3、制定工艺路线…………………………………………………………..9
5.4、确定加工余量、工序尺寸及公差………………….…………..……10
5.5、确定切削用量、基本工时(机动时间)…………….……….…….12
参考文献……………………………………….…………….……41
前言
这个学期我们进行了《机械设计制造技术基础》课程学习,并且也在校内数控机床间进行了工艺实习。
为了让我们对理论知识和实际应用之间建立密切联系,在课程结束时我们开始了机械制造技术课程设计。
课程设计之前我们对所学的各相关课程进行了一次深入的综合性的回忆和温习,这次温习我们对课程设计的内容也有一定的认识,大家一直认为本次课程设计对我们非常重要,是我们对自己实际能力的一次历练。
通过这次课程设计对自己未来将从事的工作进行一次适应性训练,从中锻炼自己分析问题,解决问题的能力,同时,在课程设计过程中,我们认真查阅资料,切实锻炼了我们自我学习的能力。
本课程设计的是工业生产中经常用到的轴承座,虽然在设计中下了很大的功夫,取得了一定的收获,但是由于生产经验和专业知识有限,设计中一定存在较多的缺点和错误,恳请老师批评指正。
设计任务
1、零件模具图 1张
2、毛坯图 1张
3、机械加工工艺过程卡片 1份
4、机械加工工序卡片 1套
二、计算生产纲领、确定生产类型
零件的生产类型是指企业(或车间,工段,班组,工作地等)生产专业化程度的分类,它对工艺规程的制定具有决定性的影响。
生产类型一般可分为大量生产,成批生产和单件生产三种类型,不同的生产类型有着完全不同的工艺特性。
零件的生产类型是按零件的年生产纲领和产品特征来确定的。
生产纲领是指企业在计划期内应当生产的产品产量和进度计划。
年生产纲领是包括备品和废品在内的年产量。
零件的年生产纲领N可按下式计算:
N=QM(1+a%)(1+b%)
式中:
N—零件的生产类型(件/年);
Q—产品的年产量(台,量);
m—每台(辆)产品中该零件的数量(件/台,辆);
a%--备品率,一般取2%~4%;
b%--废品率,一般取0.3%~0.7%
根据上式计算求得零件的生产纲领,通过查表可得轴承座的生产类型为中批生产。
三;
零件的分析
3,1零件的作用
轴承座是轴承和箱体的集合体,以便于应用,这样的好处是可以有更好的配合,更方便的使用,减少了使用厂家的成本。
3,2零件图
3,3零件加工表面及孔
1,直径60和直径20两孔都具有较高的精度要求,表面粗糙度Ra的值是1.6um是加工的关键表面。
2,轴承座的下表面的粗糙度Ra为1.6um,底座固定孔的内孔表面粗糙度Ra为6.3,以及轴承座的下表面和轴承孔中心线有平行度要求,0.01um,也是粗糙度的加工表面。
3,直径20孔的螺纹加工主要保证其定位尺寸的要求。
4,其余表面要求不高。
五工艺规程设计
5.1、定位基准的选择
正确地选择定位基准是设计工艺过程的一项重要内容。
也是保证零件加工精度的关键。
定位基准分为粗基准,精基准及辅助基准。
选择定位基准时,既要考虑零件的整个加工工艺过程,又要考虑零件的特征,设计基准和加工方法,根据粗,精基准的选择原则,合理选定零件加工过程中的定位基准。
通常在制定工艺规程时,总是先考虑选择怎样的精基准以确保达到精度要求并把各个表面加工出来,即先选择零件表面最终加工所用精基准和中间工序所用的精基准,然后在考虑选择合适的最初工序的粗基准把精基准面加工出来。
5.1.1选择粗基准
按照有关粗基准的选择原则,按照粗基准的选择原则:
选择要求加工余量小而均匀的重要表面的粗基准,以保证该表面有足够而均匀的加工余量。
直径100的外轮廓为基准,能方便加工出内轴孔,保证孔中心与轴承座下端面的平行度,直径100外轮廓面的面积较大,无浇口,冒口,飞边等缺陷,符合粗基准的要求。
加工工艺路线
根据零件的加工的几何形状,尺寸精度及位置精度,以及加工方法所能达到的经济精度,在生产纲领已确定的情况下,可以考虑采用万能机床配以专用工具,并尽量使工序集中来提高生产率。
查《机械制造工艺设计简明手册》得出零件的加工工艺路线如下:
工序1:
毛胚检验
工序2:
夹紧轴承座孔两侧毛胚,铣轴承座底面,采用X51立式铣床加专用夹具。
工序3:
以上下底面为基准,并夹紧,铣后端面,采用X5铣床加专用夹具。
工序4;
以底面为基准,夹紧前后断面,钻r43和r46的两个内孔,采用Z525钻床专用夹具。
工序5:
以底面为基准,夹紧前后断面,钻,铰r5孔,采用Z525钻床加专用夹具。
工序6;
以底面和后端面为基准,夹紧两侧面,钻r5螺纹固定孔,功螺纹,采用z525钻床加专用夹具。
工序7:
车圆角r5和r10,采用CA6140车床和专用夹具。
工序8;
去毛刺
工序9:
终检,入库。
5.4、确定加工余量、工序尺寸及公差
轴承座其材料为HT200。
由于产品的精度要求不高,生产纲领为中批生产,所以毛胚选用砂型铸造。
毛胚铸出后进行退火处理,以消除铸件在铸造过程中产生的内应力。
由文献一表2-2,该种铸件的尺寸公差等级为IT9级。
由文献一表2-2,可查出铸件主要尺寸的公差,现将主要毛胚尺寸及公差所示:
主要面尺寸
零件尺寸
总余量
公差IT
轴孔端面
R50
2
9
内孔
R30
4
底座
350*90
由此,可绘出其零件的毛胚图
粗铣底座底面
底面由粗铣和精铣两次加工完成,采用三面刃圆盘铣刀(高速钢),铣刀的规格为直径120*15,机床的型号·
·
X6132
刀具:
YG6硬质合金端铣刀。
由于铣刀在工作时,是断续切削,刀齿受到很大的机械冲击,在选择几何角度时,应保证刀齿具有足够的强度。
由金属切削原理与刀具可取y=5°
~λ=-10°
k=60°
a=10°
加工要求粗铣轴承座的下地面。
确定加工余量
由毛胚图可知:
总加工余量为2mm,文献二表8-30可知精加工余量1mm,根据实际情况,调整为0.2mm,故其粗加工余量为(2-0.2)=1.8mm。
确定每齿进给量
由《切削加工简明实用手册》表8-95,取每齿粗铣的进给量为0.2mm/z,取精加工每齿进给量为1.5mm/z,粗铣走刀一次ap=1.8mm,精铣走到一次ap=0.2MM.
计算切削用量
由表8-56,取粗铣,精铣的主轴转速分别为150r/min和300r/min,由前面选择的刀具直径120mm,故相应的切削速度分别为:
V粗=dn/1000=(120*150π)/1000=56.52m/min
V精=πdn/1000=(120*300π)/1000m/min=113m/min
校核机床功率(只需校核粗加工即可)
由文献二表2.4-96得切削功率为P=92.4*10^-5
取Z=16n=150/60=2.5r/s,
故P=92.4*10^5*120*10^0.06*1.8*16*2.5*1=0.35kw
其所消耗量功率远小于机床功率,故可用。
轴轴面的加工
轴断面的加工由铣削来完成,此时,刀具:
YG6硬质合金端铣刀,刀具不变,机床不变。
工序单边总余量由毛胚图与零件图可知为2mm,由于本工序为粗加工,尺寸精度和表面质量可不考虑,从而可采用不对称端铣,以提高进给量和加工效率。
由表8-95可得:
ap=2mmf=2mm/r由文献二表8-56可得n=600r/min则就可确定相应的切削速度:
故
V=πdn/1000=(120*600π)/1000=226.08m/min
直径100顶面的加工
顶面的加工由铣削来完成,工序余量为2mm由文献二表8-95可得ap=3mm,且上表面精度要求不高,故上表面可一次性加工完成。
由于上表面较小,可采用端铣刀加工,但是增加了换到时间,降低了效率。
故刀具仍可用刀具直径为120的YG6硬质合金面铣刀。
可取f=1.5mm/r由文献二表8-56可得n=600r/min则就可确定相应的切削的速度:
V=(πdn)/1000=(120*600π)/1000=117.75m/min
直径60内孔
由零件图及毛胚图可知,加工总余量为4mm,由于精度要求,须粗镗和半精镗各一次。
由文献二表8-86,粗加工时,取进给量F=0.5mm/r,ap=3mm精加工时,ap=1mm,F=0.2mm/r.由表8-87查得粗镗直径60内孔的切削速度V粗=1.2m/min,V精=1.6m/min由此算出转速为n粗=(1000v)/πd=(1000*1.6)/π*60=82.9m/min
直径70内孔
由文献二表8-86,粗加工时,取进给量F=0.5mm/r,ap=3mm精加工时,ap=1mm,F=0.2mm/r.由表8-87查得粗镗直径70内孔的切削速度V粗=1.2m/min,V精=1.6m/min由此算出转速为n粗=(1000v)/πd=(1000*1.6)/π*70=76.2m/min
钻直径20孔
该孔可选由高速钢钻头钻出底孔后,再由扩孔钻钻出。
由文献二表8-81得扩孔时的余量为3mm,根据实际情况可取为2mm,故钻孔的余量为Z钻=20-2=18mm
钻孔工序尺寸及公差,由文献二表8-69,钻孔的进给量f=0.2mm/r,由文献二表8-71求得钻孔时的切削速度v=0.35m/s=21m/min由8-79知扩孔的进给量为0.8mm/s。
由此算出转速为:
n=(1000v)/Πd=668.8r/min
按钻床的实际转速取n=600r/min,则实际切削速度为:
v=πdn/1000=(π*11.6)/1000=21.85m/min
因为加工灰铸铁是KM=Kf,由文献三表8-78,可查Kf=1,故F=1884.1N
M=225.63*11.6*0.2*1*10^-3=6.6N.M
他们均小于机床所能提供的进给率和扭转力矩,故机床刚度足够。
小结
大学三年转眼就过去了通过毕业设计,使我综合的运用了几年所学的专业知识。
在毕业设计中,发现自己在理论与实践中有很多的不足,自己知识中存在着很多漏洞,看到了自己的实践经验还是比较缺乏,理论到实践的能力还急需提高。
这次毕业设计,让我真切的体会到理论与实际相结合的意义,为我今后的机械制造技术设计思路奠定了基础。
这次课程设计虽然不是属于实践的操作,但是从这次课程设计中能让我学习到一些课本中不能引起我们注意的细节东西。
这次的课程设计主要是机械加工工艺规程设计,从中认真复习了有关书本知识,学会了如何分析零件的工艺性,学会了查各类工艺手册。
选择加工余量,确定毛胚的形状,大小等,绘制出了毛胚图。
又根据毛胚图和零件图构想出了工艺方案。
其中运用了基准选择,时间定额计算等方面的知识。
还结合了我们生产实习中所看到的实际情况来选择设备,填写了工艺文件。
我非常感谢我的指导老师万老师。
自从做毕业设计以来,我时刻体会着万老师严肃的科学态度,严谨的治学精神,精益求精的工作作风,我在不明白一些设计的问题和有关画图方面的问题时,每次去老师那里,老师都会在百忙之中给我们足够的时间去问问题,有时候还会和我们一起讨论设计的方案。
即使是周末只要我们有问题也愿意舍弃她自己宝贵的休息时间来给我们解答问题,而且每次都是那么的耐心,认真,和蔼,这让我很感动。
整个过程万老师都倾注了大量的心血。
正是在万老师科学,严谨的指导下,我的课程设计才能顺利完成,这篇论文才得以顺利完成,再次向我的知道老师,万老师表示深深的敬意和感谢!
在完成毕业设计的过程中,我发现了我自己很多不足和需要改进的地方。
这些我会在今后踏出校园,步入社会的工作和生活中不断努力学习和充实自己。
参考文献
一:
公差配合与测量技术·
机械工业出版社
二:
切削加工简明实用手册·
化学工业出版社
三:
机床制造工艺与夹具·
四:
金属切削原理与刀具·
五:
机械加工工艺手册·
北京出版社
六:
机械制造工艺学·
七:
切削用量简明手册·