天大大港石化认识实习报告 申海蛟301007Word格式文档下载.docx
《天大大港石化认识实习报告 申海蛟301007Word格式文档下载.docx》由会员分享,可在线阅读,更多相关《天大大港石化认识实习报告 申海蛟301007Word格式文档下载.docx(16页珍藏版)》请在冰豆网上搜索。
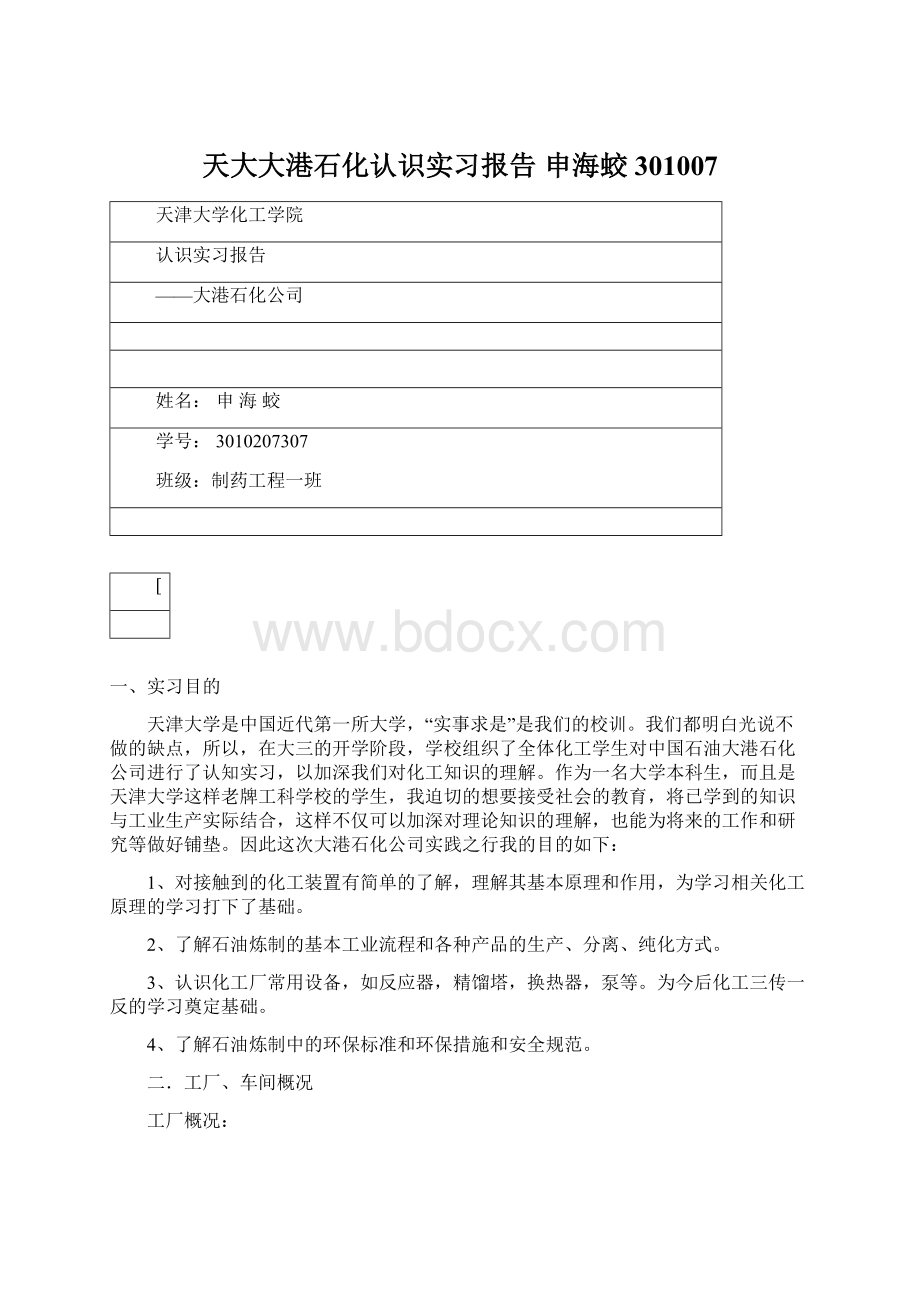
二.工厂、车间概况
工厂概况:
大港石化公司始建于1965年,地处天津东南,渤海之滨,海陆空交通便捷,基础设施完善。
经过近40年的发展,现加工能力500万吨/年,2008年加工原油425万吨,轻油收率76%,综合商品率91.1%,柴汽比3,利润总额3.9亿元。
大港石化公司共分为四个生产车间:
一联合、二联合、三联合、四联合。
主要的生产装置包括500万吨/年常减压装置、100万吨/年延迟焦化装置、160万吨/年催化裂化装置、30万吨/年催化重整装置、50万吨/年柴油加氢改质装置等等,以及一些其他辅助生产装置,如水处理装置、动力锅炉装置等。
该公司属燃料——化工型的生产企业,原料主要是大港高凝原油,同时参炼部分进口原油。
主要产品包括90#汽油、93#汽油、97#汽油、0#柴油、-10#柴油、液化气、丙烯、石脑油及MTBE等。
车间概况:
第一联合车间
(1)500万吨/年常减压装置
装置主要加工为大港高凝原油和进口原油。
主要由电脱盐系统、初馏和常压系统及减压分馏系统组成。
(2)100万吨/年延迟焦化装置
延迟焦化装置由中油股份华东设计院设计,2003年底开始建设,2004年11月建成投产。
装置以减压渣油为主要原料,年处能力为100万吨(80~110万吨/年)。
第二联合车间(未参观)
第三联合车间
(1)160万吨/年催化裂化装置
催化装置于1998年、2000年、2002年、2004年、2006年进行了五次较大规模的技术改造,目前装置设计规模160万吨/年,主要包括反再(包括烟气能量回收系统和三旋)、分馏、吸收稳定、双脱(包括干气、液化气脱硫和汽油、液化气脱硫醇)、轴流风机(包括两台备用风机和由电机、变速箱、轴流风机及烟机组成的三机组)和以背压式蒸汽透平驱动的气压机等六部分。
(2)30万吨/年液化气分离装置
气分装置由北京寰球化学工程公司设计,投产于2003年7月,原设计能力为20万吨/年,2004年经过改扩建后,现加工能力达30万吨/年。
装置主要由脱丙烷、脱乙烷及丙烯精馏三部分组成
(3)5万吨/年MTBE装置
MTBE(甲基叔丁基醚)装置是由中国石化洛阳石油化工工程公司设计的搬迁改造工程。
原装置为林源炼油厂气体分馏装置技术改造配套工程(MTBE装置),装置公称设计能力为3×
104t/a甲基叔丁基醚产品。
搬迁后装置公称设计能力扩能改造为5×
第四联合车间
(1)30万吨/年催化重整装置
装置设计规模:
预处理部分设计规模为34.35×
104t/a;
重整部分设计规模为30×
104t/a.装置组成:
由预处理部分、重整部分及余热锅炉等几部分组成。
本装置以直馏石脑油和焦化加氢石脑油为原料,主要产品为RON95的高辛烷值汽油组分,副产品为氢气及少量燃料气。
(2)5万吨/年重整汽油分离苯装置
苯抽提装置由中国石油集团华东设计院设计,年处理能力5万吨(预分馏部分为20.958×
104t/a;
抽提部分为5.99×
104t/a)。
该装置于2005年7月破土动工兴建,于2006年10月开工投产。
苯抽提装置采用金伟晖公司开发的SUPER-SAE-Ⅱ专利技术。
(3)50万吨/年柴油加氢改质装置
柴油加氢装置由中石化北京设计院设计,1999年12月竣工投产,原设计加工量为40万吨/年,装置于2003年扩能改造,改造完成后,处理量提至50万吨/年。
装置原料为催化柴油和焦化柴油,装置投产后使我公司的柴油主要调和组分在胶质含量、沉渣量、颜色及安定性等方面有了很大的改观。
(4)10000Nm3/h催化干气制氢装置
10000Nm3/h变压吸附制氢装置是化工部西南化工研究院负责工艺设计,1998年开始建设。
1999年11月开车投入运行。
装置分为原料和预处理部分、变压吸附部分、氢气部分、解吸气部分;
是将我公司催化裂化装置的副产品催化干气里的氢气提纯至99.99%以上,供加氢精制装置做氢气源;
剩余杂质由解吸气压缩机加压后送公司燃料管网。
(5)16万吨/年汽油加氢装置
16万吨/年焦化汽油加氢装置是由原有的8万吨/年润滑油加氢装置改造而成的。
2004年,该装置由华东设计勘察院进行改造设计,取消了原装置的分馏系统,对反应系统进行了适当改造,于2004年12月1日正式投产。
装置以延迟焦化装置生产的焦化汽为油原料,产品为加氢脱硫、脱氮后的精制油,作为重整装置的预加氢进料,副产品为含氢、硫化氢为主的干气。
三.炼油生产工艺
常减压装置
1.装置简介
该装置由中石化北京设计院设计,于1996年11月投产运行,原装置整体设计能力为150×
104t/a,2004年由中油华东设计院设计,装置进行改造,常减压装置设计处理能力达到500×
104t/a(常压塔、常压炉最大处理能力为450×
104t/a),减压装置处理能力为325×
104t/a。
常减压装置主要由电脱盐系统、初馏和常压系统及减压分馏系统组成。
原油蒸馏采用三级蒸馏:
初馏、常压蒸馏和减压蒸馏。
2.原料与产品
装置主要加工为大港高凝原油和进口原油。
原料及产品如下图所示:
3.工艺流程图
常减压蒸馏是原油加工的第一道工序。
本装置是根据原油中各组份的沸点(挥发度)不同用加热的方法从原油中分离出各种石油馏份。
其中常压蒸馏馏出低沸点的汽油、柴油等组份,而沸点较高的蜡油、渣油等组份留在未被分出的液相中。
将常压渣油经过加热后,送入减压蒸馏系统,使常压渣油在避免裂解的较低温度下进行分馏,分离出馏份油等二次加工原料,剩下减压渣油作为延迟焦化装置原料。
4.主要单元操作
该装置主要涉及的单元操作就是蒸馏,原油蒸馏采用三级蒸馏:
采用初馏塔方案,以增加装置的灵活性,减少常压炉、常压塔的负荷。
增设初馏塔侧线抽出,并将其侧线油打入常压塔一中回流线,进一步分馏。
不但降低了加热炉的热负荷,节省了能耗,而且也降低了常压塔下部的汽液负荷,提高了常压塔的处理量。
常压塔内件采用大通量、高效率、高弹性的华东化工学院的专利产品导向浮阀塔盘,部分塔段采用规整填料。
常一、常二汽提塔为导向浮阀塔盘,常三汽提塔采用乱堆填料。
减压蒸馏采用深拔技术,减压塔选用全填料内件,采用先进的液体分布器(根据各段不同汽液负荷条件,选用不同性能的填料)。
生产方式按照干式操作考虑,可以转成微湿式操作。
减压进料口设置360°
环型分配器,使上升气体均匀分布,减少雾沫夹带。
减压塔顶系统采用三级抽空系统。
增压器和一级抽空器采用传统的蒸汽抽空方式,二级采用机械抽空系统和蒸汽抽空系统相互备用,节约能量和投资。
5.主要操作条件
原油换热要达到250℃以上才可以进入装置进行反映,而常压蒸馏换热系统和减压蒸馏换热系统统一考虑,采用窄点技术,优化设计,充分利用装置余热,使原油换热终温达到300℃以上。
加热炉采用热管式空气预热器,降低能耗,节约费用。
延迟焦化装置
装置以减压渣油为主要原料,年处能力为100万吨(80~110万吨/年),主要产品为汽油、柴油、液化气、蜡油、石油焦,副产品为干气。
装置主体包括焦化、分馏、吸收稳定三部分,辅助系统包括焦炭塔水力除焦和天车装置。
工艺上采用一炉两塔、单井架水力除焦、无堵焦阀密闭放空的先进工艺,生焦周期为24小时。
原料与产品如下图所示:
3.工艺流程图
焦化是焦炭化的简称,是重质油(如重油、减压渣油、裂化渣油甚至土沥青等)在高温条件下进行裂解和缩合反应,生成油气(含不凝气、汽油、轻柴油、轻蜡油、重蜡油)和石油焦的过程。
图1反应系统的工艺流程图
图2分馏系统的工艺流程图
图3吸收系统的工艺流程图
4.主要单元操作
装置单元操作主要包括焦化、分馏、吸收稳定三部分,辅助系统包括焦炭塔水力除焦和天车装置。
延迟焦化的反应机理与热裂化基本相似,只是延迟焦化工艺是将重质油进行高温热裂解。
渣油在通过加热炉时,采用高流速和较高的加热强度,使油品在短时间内获得焦化反应所需的热量,并迅速离开加热炉管进入焦炭塔内进行裂解、缩合反应。
反应生成的高温油气经分馏塔切割后得到富气、粗汽油、柴油、蜡油;
反应生成焦炭采用水力除焦的方法除焦。
富气和粗汽油经吸收、解吸后分离出干气、液化气和稳定汽油。
在加热炉管中控制原料油基本上不发生裂化反应,而延缓至专设的焦炭塔中进行裂化反应。
在焦化反应中,重质芳香烃是生焦的必要条件,一般认为缩合反应是重质芳香烃与烯烃同时作用的过程。
5.设备的主要操作条件
原料油(减压渣油或其他重质油如脱油沥青、澄清油甚至污油)经加热到495~505℃进入焦炭塔,待陆续装满(留一定的空间)后,改进入另一焦炭塔。
热原料油在焦炭塔内进行焦化反应,生成的轻质产物从顶部出来进入分馏塔,分馏出石油气、汽油、柴油和重馏分油。
催化裂化装置
1.装置简介
催化装置是由中石化北京设计院设计,1996年12月建成投产。
装置原设计规模120万吨/年。
催化装置于1998年、2000年、2002年、2004年、2006年进行了五次较大规模的技术改造,目前装置设计规模160万吨/年,主要原料为减压蜡油、减压渣油和常压渣油,主要产品有汽油、柴油、液化气等。
装置组成主要包括反再(包括烟气能量回收系统和三旋)、分馏、吸收稳定、双脱(包括干气、液化气脱硫和汽油、液化气脱硫醇)、轴流风机(包括两台备用风机和由电机、变速箱、轴流风机及烟机组成的三机组)和以背压式蒸汽透平驱动的气压机等六部分。
2.原料与产品
催化重整装置主要是生产高辛烷值的汽油,重整原料主要是直馏汽油,而辛烷值比较高的组分主要是芳烃、环己烷、异构烷烃、直链烷烃,而催化重整的目标也就是增大这些成分在原料油中的成分,生产高标高的汽油、柴油等等。
催化裂化是炼油工业中重要的二次加工过程,是重油轻质化的重要手段。
它是使原料油在适宜的温度、压力和催化剂存在的条件下,进行分解、异构化、氢转移、芳构化、缩合等一系列化学反应,原料油转化成气体、汽油、柴油等主要产品及油浆、焦炭的生产过程。
催化裂化的生产过程包括以下几个部分:
反应再生部分:
其主要任务是完成原料油的转化。
原料油通过反应器与催化剂接触并反应,不断输出反应产物,催化剂则在反应器和再生器之间不断循环,在再生器中通入空气烧去催化剂上的积炭,恢复催化剂的活性,使催化剂能够循环使用。
烧焦放出的热量又以催化剂为载体,不断带回反应器,供给反应所需的热量,过剩热量由专门的取热设施取出加以利用。
分馏部分:
主要任务是根据反应油气中各组份沸点的不同,将它们分离成富气、粗汽油、轻柴油、回炼油、油浆,并保证汽油干点、轻柴油凝固点和闪点合格。
吸收稳定部分:
利用各组份之间在液体中溶解度不同把富气和粗汽油分离成干气、液化气、稳定汽油。
5.主要操作条件
反应再生的部分的条件要求较为严格,第一段再生是在较低的再生温度(640℃~710℃)下将催化剂上的部分炭和全部氢烧掉,这样降低了第二再生器的水蒸汽分压,虽然第二再生器温度(680℃~730℃)比一再高,但由于没有水蒸汽存在,因而使催化剂免于水热失活。
两段再生能很好的保持催化剂的活性和选择性,提高了催化剂的利用效率。
设备的自动化控制
这是在控制室屏幕的图片:
催化重整装置
装置组成:
原料和产品如下图所示
(1)重整原料的预加氢精制反应原理
预加氢部分是原料预处理部分的核心,其作用是脱除对重整催化剂活性有害的物质,其中包括砷、铅、铜、硫、氮、氧、双键烯烃等。
金属杂质通过吸附作用沉积在催化剂表面,而无机杂质则转化为易于脱除的无机物如H2S、NH3、H2O等,使重整原料油中S<0.5μg/g(w),N<0.5μg/g(w),As<1ng/g(w),Cu及Pb均<10ng/g(w),并通过加氢反应使双键烯烃饱合为烷烃。
(2)重整反应部分工艺原理
催化重整是以C6~C11石脑油馏分为原料,在一定的操作条件和催化剂作用下,烃类分子发生重新排列,使环烷烃和烷烃转化为芳烃,同时产生氢气的过程。
重整反应深度(指生成油的辛烷值或芳含)与原料油性质,催化剂性能(金属功能Mt和酸性功能Ac)以及操作反应苛刻度有关。
图一:
30万吨/年重整装置工艺原则流程图(预处理部分)
图二:
30万吨/年重整装置工艺原则流程图(重整反应、再接触部分)
采用国内成熟可靠的半再生重整工艺技术。
主要的单元操作包括两部分:
预加氢和重整部分。
预加氢部分采用循环氢流程,加氢反应后缺损的氢气经由再接触提纯后的重整氢补充。
该系统压力通过控制预加氢产物分离罐的压力来控制。
重整反应部分选用抚顺研究院的CB-11、CB-8催化剂,采用二段装填和二段混氢工艺技术。
重整产氢经增压和再接触提纯后送出装置,供柴油加氢和汽油加氢使用。
5.主要操作条件
该装置原料为石脑油或低质量汽油,其中含有烷烃、环烷烃和芳烃。
含较多环烷烃的原料是良好的重整原料。
催化重整用于生产高辛烷值汽油时,进料为宽馏分,沸点范围一般为80~180℃;
用于生产芳烃时,进料为窄馏分,沸点范围一般为60~165℃。
重整原料中的烯烃、水及砷、铅、铜、硫、氮等杂质会使催化剂中毒而丧失活性,需要在进入重整反应器之前除去。
对该过程的影响因素除了原料性质和催化剂类型以外,还有温度、压力、空速和氢油比。
温度高、压力低、空速小和低氢油比对生成芳烃有利,但为了抑制生焦反应,需要使这些参数保持在一定的范围内。
此外,为了取得最好的催化活性和催化剂选择性,有时在操作中还注入适当的氯化物以维持催化剂的氯含量稳定。
【柴油加氢改质装置】
装置原料为催化柴油和焦化柴油,产品如下图所示:
加氢精制是馏分油在氢压下进行催化改质的统称。
是指在催化剂和氢气存在下,石油馏分中硫、氮、氧的非烃组分和有机金属化合物分子发生脱除硫、氮、氧和金属的氢解反应,烯烃和芳烃分子发生加氢反应使其饱和。
通过加氢精制可以改善油品的气味、颜色和安定性,提高油品的质量,满足环保对油品的使用要求。
柴油加氢精制的主要化学反应为加氢脱硫、脱氮、脱氧,烯烃、芳烃加氢饱和等反应。
四.实习收获感受
9月6日,化工学院制药工程和高分子专业的四个班级一起来到了大港石化公司进行实习。
作为一个制药工程专业的学生,我十分期待着这次实习。
一方面,是想通过认识实习完成对化学工程从理性认识到感性认识的转化,让自己更快更好的理解课本上的知识在实际中的应用,明确化学与化工的区别;
另一方面,通过认识实习,熟悉今后在课堂上将要讲到的反应器、换热器、精馏塔、泵等化工常用设备,并对三传一反有进一步的了解,以促进今后化工单元操作课程的学习。
这次认识实习虽然时间很短,但是收获颇丰,概括起来有以下几点:
安全是化工产业第一个需要思考的因素。
化工是一个高危险系数的行业,所以在对安全的控制是十分的严格的,在化工生产的每一个步骤,都要严格按规程办事,任何时刻都要战战兢兢,临渊履薄,万不可贪图省事而酿成惨剧。
而且事实证明,我国的化工企业正在从传统的高污染,劳动密集型行业过渡到绿色化,科技密集型的新型行业,作为化工人,我们欣喜的看到,传统化工与新型科技的结合,新型的绿色化工正以蓬勃之势兴起!
作为未来的化学工程师,我们更该踏踏实实学习,学好专业知识,为祖国的化工业贡献一分自己的微薄的力量。
认识实习让我认识到让设备运转起来是一个很大的工程,在这其中充分体现的学科交叉。
从化工学科的单元设计,到机械学科的设备制造,到自动化学科的自动化控制,再到计算机等学科的支持,科技在实际生产中结合的非常紧密。
我们不可能样样精通,但至少尽量涉猎面广一些,并培养自己的团队意识和协作能力,这样才能更好的适应现代化工业的需要,把科学实实在在转化为第一生产力。
我们学生应该更加注重理论联系实际。
只是学了两年基础知识的我们来到这个工厂发现自己根本就还什么都不懂,这让我下决心在今后的学习中更加奋发,不但在理论上更在实践上多下功夫。
而且师傅告诉我们,我们在化工基础课上学了很多东西,到工作岗位上却发现都用不上。
这更加要求我们更加注重实践,注重理论联系实际,给自己创造机会加强对化学工业这个行业而不止是学科的认识,为我们能够更好的去融入未来的化工生产中去。
环境保护问题仍是一个很重要的问题。
随着近年来国家标准的提高,厂区建设日益趋向环保化、节能化,可是仍存在一些问题。
在整个化工厂内,可以说是到处都弥漫着刺激性难闻的气体,对工人师傅们的身体很不好,这样大大的降低了人们对化工行业的兴趣,大部分的人员就是因为身体问题不得不早早的离开化工行业,所以我认为在可持续性发展的今天,环保问题也是一个不亚于经济增长的问题,我们必须用可持续发展的眼光去看待这个问题,才能在获得一个长久的利益。
我们也要将课堂上学到的知识应用到实践生产当中去,在与工人师傅的交流中,我发现化工行业的反应条件仍然很苛刻,而且好多设备也都是国外进口的,这就需要我们通过自己的努力,去研究更温和的反应过程,去打造更专业的反应仪器。
例如柴油的加氢反应,条件远超过我的想象,石油化工是一个十分依赖催化剂的行业,如果能有更好的催化剂,一定能创造更多的经济效益。
当然我不是催化专业的,只是个例子而已。
最后,作为一名刚刚进入大三的学生,专业知识方面才只是刚刚起步,特别我是制药专业,并不是纯化工专业,对化工知识的了解可以说是完全不深刻。
这次大港参观实习,让我收获颇丰,也同时希望中国的化工在新世纪发展得更好,也希望我们日后能在化工行业里尽自己的一份力!