金属的磷化镀锌Word下载.docx
《金属的磷化镀锌Word下载.docx》由会员分享,可在线阅读,更多相关《金属的磷化镀锌Word下载.docx(24页珍藏版)》请在冰豆网上搜索。
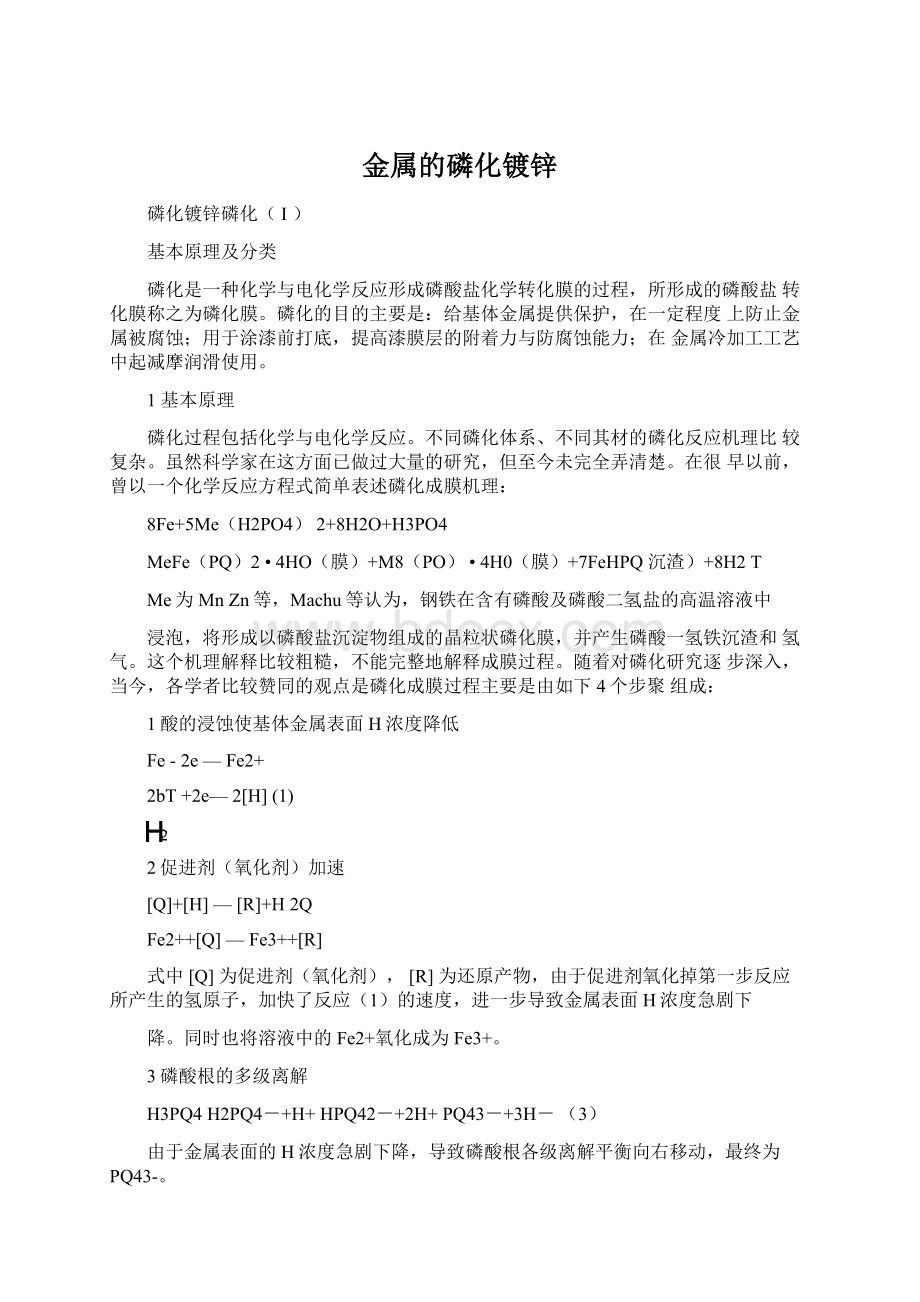
以上机理不仅可解释锌系、锰系、锌钙系磷化成膜过程,还可指导磷化配方与磷化工艺的设计。
从以上机理可以看出:
适当的氧化剂可提高反应
(2)的速
度;
较低的HF浓度可使磷酸根离解反应(3)的离解平衡更易向右移动离解出PO3-;
金属表面如存在活性点面结合时,可使沉淀反应(4)(5)不需太大的过饱和即可形成磷酸盐沉淀晶核;
磷化沉渣的产生取决于反应
(1)与反应
(2),溶液H浓度高,促进剂强均使沉渣增多。
相应,在实际磷化配方与工艺实施中表面为:
适当较强的促进剂(氧化剂);
较高的酸比(相对较低的游离酸,即H浓度);
使金属表面调整到具备活性点均能提高磷化反应速度,能在较低温度下快速成膜。
因此在低温快速磷化配方设计时一般遵循上述机理,选择强促进剂、高酸比、表面调整工序等。
关于磷化沉渣。
因为磷化沉渣主要是FePQ要相减少沉渣量就必须降低Fe3+的产生量,即通过两个方法:
降低磷化液的H浓度(低游离酸度)减少Fe2+氧化成为Fe3+。
锌材与铝材磷化机理基本与上相同。
锌材的磷化速度较快,磷化膜只有磷酸锌盐单一组成,并且沉渣很少。
铝材磷化一般要加入较多的氟化合物,使之形成AIF3、AlF63-,铝材磷化步聚与上述机理基本相同。
2磷化分类
磷化的分类方法很多,但一般是按磷化成膜体系、磷化膜厚度、磷化使用温度、促进剂类型进行分类。
2.1按磷化膜体系分类
按磷化成膜体系主要分为:
锌系、锌钙系、锌锰系、锰系、铁系、非晶相铁系六大类。
锌系磷化槽液主体成他是:
Zn2+、HHPO3、NO、HPQ、促进剂等。
形成的磷化膜主体组成(钢铁件):
Zn3(po4)2•4HO、ZrbFe(PQ)2•4H2Q磷化晶粒呈树枝状、针状、孔隙较多。
广泛应用于涂漆前打底、防腐蚀和冷加工减摩润滑。
锌钙系磷化槽液主体成分是:
Zn2+、C/、NO-、HPQ-、HPO以及其它添加物
等。
形成磷化膜的主体组成(钢铁件):
ZrbCa(P(4)2•4H2Q
Zn2Fe(PQ)2•4HOZra(PCh)2•4HQ磷化晶粒呈紧密颗粒状(有时有大的针状晶粒),孔隙较少。
应用于涂装前打底及防腐蚀。
2+2+--
锌锰系磷化槽液主体组成:
Zr、Mr、NO、HPQ、HPO以及其它一些添加物。
磷化膜主体组成:
Zr2Fe(PO4)2•4H2O、Zr3(PO4)2•4H2O、
(Mr‘FehFKPQ"
•4HO,磷化晶粒呈颗粒-针状-树枝状混合晶型,孔隙较少。
广泛用于漆前打底、防腐蚀及冷加工减摩润滑。
锰系磷化槽液主体组成:
MF、NO-、HPQ、HPO以及其它一些添加物。
在钢铁件上形成磷化膜主体组成:
(Mr,Fe)5^(PQ)4•4HQ磷化膜厚度大、孔隙少,磷化晶粒呈密集颗状。
广泛应用于防腐蚀及冷加工减摩润滑。
铁系磷化槽液主体组成:
Fe2+、HPQ、HPQ以及其它一些添加物。
磷化膜主体组成(钢铁工件):
Fe5H(PQ)4•4HO,磷化膜厚度大,磷化温度高,处理时间长,膜孔隙较多,磷化晶粒呈颗粒状。
应用于防腐蚀以及冷加工减摩润滑。
非晶相铁系磷化槽液主体成分:
N6(NH0、HPQ、HPQ、MoO(CIO3、NQ)以及其它一些添加物。
磷化膜主体组成(钢铁件):
Fe3(PO4)2•8H2O,Fe2O3,磷化膜薄,微观膜结构呈非晶相的平面分布状,仅应用于涂漆前打底。
2.2按磷化膜的厚度分类按磷化膜厚度(磷化膜重)分,可分为次轻量级、轻量级、次重量级、重量级
2
四种。
次轻量级膜重仅0.1〜1.0g/m,—般是非晶相铁系磷化膜,仅用于漆前打底,特别是变形大工件的涂漆前打底效果很好。
轻量级膜重1.1〜4.5g/m2,广
泛应用于漆前打底,在防腐蚀和冷加工行业应用较少。
次重量级磷化膜厚
4.6〜7.5g/m2,由于膜重较大,膜较厚(一般>3卩m),较少作为漆前打底(仅作为基本不变形的钢铁件漆前打底),可用于防腐蚀及冷加工减摩滑润。
重量级膜重大于7.5g/m2,不作为漆前打底用,广泛用于防腐蚀及冷加工。
2.3按磷化处理温度划分按处理温度可分为常温、低温、中温、高温四类。
常温磷化就是不加温磷化。
低温磷化一般处理温度30〜45C。
中温磷化一般60〜70C。
高温磷化一般大于80°
C。
温度划分法本身并不严格,有时还有亚中温、亚高温之法,随各人的意愿而定,但一般还是遵循上述划分法。
2.4按促进剂类型分类由于磷化促进剂主要只有那么几种,按促进剂的类型分有利于槽液的了解。
根据促进剂类型大体可决定磷化处理温度,如NQ-促进剂主要就是中温磷化。
促进剂主要分为:
硝酸盐型、亚硝酸盐型、氯酸盐型、有机氮化物型、钼酸盐型等主要类型。
每一个促进剂类型又可与其它促进剂配套使用,有不少的分支系列。
硝酸盐型包括:
NQ-型,NQ-/NC2一(自生型)。
氯酸盐型包括:
CIQ「,CIQ/N03「,CIQ-/NO2一。
亚硝酸盐包括:
硝基胍R-NOT/CIO3「。
钼酸盐型包括:
MoO4-,MoO4-/CIO3-,MoO4-/NO3-。
磷化分类方法还有很多,如按材质可分为钢铁件、铝件、锌件以及混合件磷化
磷化(II)——磷化前的预处理
一般情况下,磷化处理要求工件表面应是洁净的金属表面(二合一、三合一、四合一例外)。
工件在磷化前必须进行除油脂、锈蚀物、氧化皮以及表面调整等预处理。
特别是涂漆前打底用磷化还要求作表面调整,使金属表面具备一定的“活性”,才能获得均匀、细致、密实的磷化膜,达到提高漆膜附着力和耐腐蚀性的要求。
因此,磷化前处理是获得高质量磷化膜的基础。
1除油脂
除油脂的目的在于清除掉工件表面的油脂、油污。
包括机械法、化学法两类。
机械法主要是:
手工擦刷、喷砂抛丸、火焰灼烧等。
化学法主要:
溶剂清洗、酸性清洗剂清洗、强碱液清洗,低碱性清洗剂清洗。
以下介绍化学法除油脂工艺。
1.1溶剂清洗
溶剂法除油脂,一般是用非易燃的卤代烃蒸气法或乳化法。
最常见的是采用三氯乙烷、三氯乙烯、全氯乙烯蒸汽除油脂。
蒸汽脱脂速度快,效率高,脱脂干净彻底,对各类油及脂的去除效果都非常好。
在氯代烃中加入一定的乳化液,不管是浸泡还是喷淋效果都很好。
由于氯代卤都有一定的毒性,汽化温度也较高,再者由于新型水基低碱性清洗剂的出现,溶剂蒸汽和乳液除油脂方法现在已经很少使用了。
1.2酸性清洗剂清洗
酸性清洗剂除油脂是一种应用非常广泛的方法。
它利用表面活性剂的乳化、润湿、渗透原理,并借助于酸腐蚀金属产生氢气的机械剥离作用,达到除油脂的目的。
酸性清洗剂可在低温和中温下使用。
低温一般只能除掉液态油,中温就可除掉油和脂,一般只适合于浸泡处理方式。
酸性清洗剂主要由表面活性剂
(如0P类非离子型活性剂、阴离子磺酸钠型)、普通无机酸、缓蚀剂三大部分
组成。
由于它兼备有除锈与除油脂双重功能,人们习惯称之为“二合一”处理液。
常见的酸性清洗剂配方及工艺参数见下表。
工艺
低温型
中温型
磷酸酸基型
工业盐酸(31%
20%〜50%
工业硫酸(98%
0%〜15%
15%〜30%
工业磷酸(85%
10%〜40%
表面活性剂
(OP类,磺酸类)
0.4%〜1.0%
缓蚀剂
适量
使用温度
常量〜45C
50〜80r
常温〜80r
处理时间
适当
5〜10min
适当<
盐酸、硫酸酸基的清洗剂应用最为广泛,成本低,效率较高。
但酸洗残留的c「
、SQ2-对工件的后腐蚀危害很大。
而磷酸酸基没有腐蚀物残留的隐患,但磷酸成本较高,清洗效率低些。
对于锌件,铝件一般不采用酸性清洗剂清洗,特别锌件在酸中的腐蚀极快。
1.3强碱液清洗
强碱液除油脂是一种传统的有效方法。
它是利用强碱对植物油的皂化反应,形成溶于水的皂化物达到除油脂的目的。
纯粹的强碱液只能皂化除掉植物油脂而不能除掉矿物油脂。
因此人们通过在强碱液中加入表面活性剂,一般是磺酸类阴离子活性剂,利用表面活性剂的乳化作用达到除矿物油的目的。
强碱液除油脂的使用温度都较高,通常〉80C。
常用强碱液清洗配方与工艺如下:
氢氧化钠5%〜10%
硅酸钠2%〜8%
磷酸钠(或碳酸钠)1%〜10%
表面活性剂(磺酸类)2%〜5%
处理温度>80C
处理时间5〜20min
处理方式浸泡、喷淋均可
强碱液除油脂需要较高温度,能耗大,对设备腐蚀性也大,并且材料成本并不算低,因此这种方法的应用正逐步减少。
1.4低碱性清洗液清洗
低碱性清洗液是当前应用最为广泛的一类除油脂剂。
它的碱性低,一般pH值为
9〜12。
对设备腐蚀较小,对工件表面状态破坏小,可在低温和中温下使用,除
油脂效率较高。
特别在喷淋方式使用时,除油脂效果特别好。
低碱性清洗剂主要由无机低碱性助剂、表面活性剂、消泡剂等组成。
无机型助剂主要是硅酸钠、三聚磷酸钠、磷酸钠、碳酸钠等。
其作用是提供一定的碱度,有分散悬浮作用。
可防止脱下来的油脂重新吸附在工件表面。
表面活性剂主要采用非离子型与阴离子型,一般是聚氯乙烯0P类和磺酸盐型,它在除油脂过程中起主要的作用。
在有特殊要求时还需要加入一些其它添加物,如喷淋时需要加入消泡剂,有时还加入表面调整剂,起到脱脂、表调双重功能。
低碱性清洗剂已有很多商业化产品,如PA30-IM、PA30-SM、FC-C4328、Pyroclean442等。
一般常用的低碱性清洗液配方和工艺如下:
浸泡型喷淋型
三聚磷酸钠4〜10g/l4〜10g/l
硅酸钠0〜10g/l0〜10g/l
碳酸钠4〜10g/l4〜10g/l
消泡剂00.5〜3.0g/l
表面调整剂0〜3g/l0〜3g/l
游离碱度5〜20点5〜15点
处理温度常温〜80C40〜70C
处理时间5〜20min1.5〜3.0min
浸泡型清洗剂主要应注意的是表面活性剂的浊点问题,当处理温度高于浊点时,表面活性剂析出上浮,使之失去脱脂能力,一般加入阴离子型活性剂即可解决。
喷淋型清洗剂应加入足够的消泡剂,在喷淋时不产生泡沫尤为重要。
铝件、锌件清洗时,必须考虑到它们在碱性条件下的腐蚀问题,一般宜用接近中性的清洗剂。
2酸洗
酸洗除锈、除氧化皮的方法是工业领域应用最为广泛的方法。
利用酸对氧化物溶解以及腐蚀产生氢气的机械剥离作用达到除锈和除氧化皮的目的。
酸洗中使用最为常见的是盐酸、硫酸、磷酸。
硝酸由于在酸洗时产生有毒的二氧化氮气体,一般很少应用。
盐酸酸洗适合在低温下使用,不宜超过45C,使用浓度
10%〜45%,还应加入适量的酸雾抑制剂为宜。
硫酸在低温下的酸洗速度很慢,宜在中温使用,温度50〜80C,使用浓度10%〜25%磷酸酸洗的优点是不会产生腐蚀性残留物(盐酸、硫酸酸洗后或多或少会有少会有Cl-、SO42-残留),比
较安全,但磷酸的缺点是成本较高,酸洗速度较慢,一般使用浓度10%〜40%,处理温度可常温到80C。
在酸洗工艺中,采用混合酸也是非常有效的方法,如盐酸-硫酸混合酸,磷酸-柠檬酸混合酸。
在酸洗除锈除氧化皮槽液中,必须加入适量的缓蚀剂。
缓蚀剂的种类很多,选用也比较容易,它的作用是抑制金属腐蚀和防止“氢脆”。
但酸洗“氢脆”敏感的工件时,缓蚀剂的选择应特别小心,因为某些缓蚀剂抑制二个氢原子变为氢分子的反应,即:
2[H]TH2T,使金属表面氢原子的浓度提高,增强了“氢脆”倾向。
因此必须查阅有关腐蚀数据手册,或做“氢脆”试验,避免选用危险的缓蚀剂。
>
3表面调整
表面调整的目的,是促使磷化形成晶粒细致密实的磷化膜,以及提高磷化速度。
表面调整剂主要有两类,一种是酸性表调剂,如草酸。
另一种是胶体钛。
两者的应用都非常普及,前者还兼备有除轻锈(工件运行过程中形成的“水锈”及“风锈”)的作用。
在磷化前处理工艺中,是否选用表面调整工序和选用那一种表调剂都是由工艺与磷化膜的要求来决定的。
一般原则是:
涂漆前打底磷化、快速低温磷化需要表调。
如果工件在进入磷化槽时,已经二次生锈,最好采用酸性表调,但酸性表调只适合于》50C的中温磷化。
一般中温锌钙系磷化不表调也行。
磷化前预处理工艺是:
除油脂——水洗——酸洗——水洗——中和——表调——磷化
除油除锈“二合一”——水洗——中和——表调——磷化除油脂——水洗——表调——磷化
中和一般就是0.2%〜1.0%纯碱水溶液。
在有些工艺中对重油脂工件,还增加预除油脂工序。
磷化(川)一一磷化工艺
(1)
1防锈磷化工艺
磷化工艺的早期应用是防锈,钢铁件经磷化处理形成一层磷化膜,起到防锈作
用。
经过磷化防锈处理的工件防锈期可达几个月甚至几年(对涂油工件而言),广泛用于工序间、运输、包装贮存及使用过程中的防锈,防锈磷化主要有铁系磷化、锌系磷化、锰系磷化三大品种。
铁系磷化的主体槽液成分是磷酸亚铁溶液,不含氧化类促进剂,并且有高游离酸度。
这种铁系磷化处理温度高于95C,处理时间长达30min以上,磷化膜重大于10g/m2,并且有除锈和磷化双重功能。
这种高温铁系磷化由于磷化速度太慢,现在应用很少。
锰系磷化用作防锈磷化具有最佳性能,磷化膜微观结构呈颗粒密堆集状,是应用最为广泛的防锈磷化。
加与不加促进剂均可,如果加入硝酸盐或硝基胍促进
剂可加快磷化成膜速度。
通常处理温度80〜100C,处理时间10〜20min,膜重
在7.5克/m以上。
锌系磷化也是广泛应用的一种防锈磷化,通常采用硝酸盐作为促进剂,处理温度80〜90C,处理时间10〜15min,磷化膜重大于7.5g/m2,磷化膜微观结构一般是针片紧密堆集型。
防锈磷化一般工艺流程:
除油除锈一一水清洗一一表面调整活化一一磷化一一水清洗一一铬酸盐处理一—烘干一一涂油脂或染色处理
通过强碱强酸处理过的工件会导致磷化膜粗化现象,采用表面调整活化可细化晶粒。
锌系磷化可采用草酸、胶体钛表调。
锰系磷化可采用不溶性磷酸锰悬浮液活化。
铁系磷化一般不需要调整活化处理。
磷化后的工件经铬酸盐封闭可大幅度提高防锈性,如再经过涂油或染色处理可将防锈性提高几位甚至几十倍,见表1。
表1磷化膜与涂油复合对耐蚀性的影响
材料
出现锈蚀时间(h)(盐雾ASTMB117-
64)
裸钢
0.5
钢+涂油
15.0「
钢+16g/m锌磷化
4.0
钢+锌磷化+涂油
550.0
摘自FreemanDB.PhosphatingandMetalPretreatmentWoodhead-Faukner,1986.
2耐磨减摩润滑磷化工艺
对于发动机活塞环、齿轮、制冷压缩机一类工件,它不仅承受一次载荷,而且还有运动摩擦,要求工件能减摩、耐摩。
锰系磷化膜具有较高的硬度和热稳定性,能耐磨损,磷化膜具有较好的减摩润滑作用。
因此,广泛应用于活塞环,轴承支座,压缩机等零部件。
这类耐磨减摩磷化处理温度70〜100C,处理时
间10〜20min,磷化膜重大于7.5g/m2。
在冷加工行业如:
接管、拉丝、挤压、深拉延等工序,要求磷化膜提供减摩润滑性能,一般采用锌系磷化,一是锌系磷化膜皂化后形成润滑性很好的硬脂酸锌层,二是锌系磷化操作温度比较低,可在40、60或90T条件下进行磷化处
理,磷化时间4〜10min,有时甚至几十秒钟即可,磷化膜重量要求》3g/m便
可。
工艺流程是:
耐磨减摩磷化减摩润滑磷化(冷加工)
除油除锈除油除锈
水清洗水清洗
锰系磷化锌系磷化
干燥皂化(硬脂酸钠)涂润滑油脂干燥
3漆前磷化工艺
涂装底漆前的磷化处理,将提高漆膜与基体金属的附着力,提高整个涂层系统的耐腐蚀能力;
提供工序间保护以免形成二次生锈。
因此漆前磷化的首要问题是磷化膜必须与底漆有优良的配套性,而磷化膜本身的防锈性是次要的,磷化膜细致密实、膜薄。
当磷化膜粗厚时,会对漆膜的综合性能产生负效应。
磷化体系与工艺的选定主要由:
工件材质、油锈程度、几何形状;
磷化与涂漆的时间间隔;
底漆品种和施工方式以及相关场地设备条件决定。
一般来说,低碳钢较高碳钢容易进行磷化处理,磷化成膜性能好些。
对于有锈(氧化皮)工件必须经过酸洗工序,而酸洗后的工件将给磷化带来很多麻烦,如工序间生锈泛黄,残留酸液的清除,磷化膜出现粗化等。
酸洗后的工件在进行锌系、锌锰系磷化前一般要进行表面调整处理。
在间歇式的生产场合,由于受条件限制,磷化工件必须存放一段时间后才能涂漆,因此要求磷化膜本身具有较好的防锈性。
如果存放期在10天以上,一般应采用中温磷化,如中温锌系、中温锌锰系、中温锌钙系等,磷化膜的厚度最好应在2.0
9
〜4.5g/m之间。
磷化后的工件应立即烘干,不宜自然凉干,以免在夹缝、焊接处形成锈蚀。
如果存放期只有3〜5天,可用低温锌系、轻铁系磷化,烘干效果会好于自然凉干。
3.1单室喷淋磷化工艺
整个前处理工艺只有一个喷室,在喷室的下面有多个贮液槽体,不同的处理液
喷淋工件后流回各自的槽体中。
例如首先喷淋脱脂液,待脱脂液流回脱脂槽后,关闭阀门;
然后喷淋水洗,水洗完成后关闭水洗阀门;
下一步再喷淋磷化液,这种单室处理方法可实行如下几种工艺流程:
脱脂——磷化“二合一”(轻铁系)——水清洗——(铬封闭)——出件
脱脂——水清洗——磷化——水清洗——(铬封闭)——出件
脱脂一一水清洗一一表面调整一一磷化一一水清洗一一(铬封闭)一一出件
这种磷化工艺一般不提倡安排酸洗工序,以免造成设备腐蚀或产生工序间锈蚀。
单室工艺设备少占用场地小,简便易行,但浪费较大,仅适合于批量少的间歇式生产场合。
与此相似的另一种方法,采用外围小容量罐体盛处理液,通过泵与管道抽液后与热水混合后喷淋在工件上达到脱脂、磷化效果,喷淋后药液不回收,这种方法更简单,但浪费更大。
3.2多室“标准”工位磷化工艺:
1预脱脂50〜70C1〜2min
2脱脂50〜70E2〜4min
3水清洗1〜2道常温0.5〜1.0min
4表面调整常温0.5〜1.0min
5磷化35〜60C2〜6min
6水清洗<2道常温0.5〜1.0min
7去离子水洗常温0.5〜1.0min
8铬酸盐处理40〜70E0.5〜1.0min
9烘干低于180C
处理方式可采用全喷淋、全浸泡、喷淋-浸泡结合三种方式。
对家用电器行业一般采用全喷淋方式,它效率高,整个前处理只需要十几分钟即可完成,节省场地设备。
汽车行业流行采用喷淋-浸泡相结合的方式。
表面调整工序并非必须,表调剂加到脱脂槽内也可达到相同效果。
磷化后的去离子水洗必不可少。
磷化后的铬酸盐处理,可提高整个涂层系统的耐腐蚀性能
(见表2),但由于铬的环境污染问题,因此应慎使用。
表2铬酸盐处理对漆膜耐蚀性能影响
划痕3mnT散时间(h)
(盐雾ASTMB117-6)
去离子水洗
铬酸盐处理
轻铁系
48
96
锌系
2.0
144
240
锌钙系
1.2
216
288
192
312
25
264
360
*数据来源与表1相同
3.3混合件磷化处理工艺(锈蚀工件)
1脱脂40〜70C3〜8min
2水清洗常温0.5〜1.0min
3酸洗40〜70r3〜8min
4水清洗常温0.5min
5中和常温0.5〜1.0min
6表面调整常温0.5min
7磷化35〜60C3〜10min
8水清洗常温0.5〜1.0min
9脱离子水洗常温0.5〜1.0min
10铬酸盐水洗40〜70E0.5〜1.0min
(11)烘干<
180C
除非有足够的理由,酸洗工序一般不采用喷淋处理方式,喷淋会带来设备腐蚀以及工件工序间生锈等一系列问题。
其他各工序均可采用全喷淋或喷-浸相结合
的施工方式。
对于混合件(无锈工件、有锈、氧化皮工件同时混合处理),采用脱脂除锈
“二合一”代替分步脱脂除锈的方法已经应用有几十年的历史,同样可获满意效果。
对于酸洗和脱脂除锈“二合一”一般采用非挥发性的无机酸较适宜。
磷化(W)――磷化工艺
(2)
在磷化工序中,由于各个磷化液生产厂家和就应用厂家基于不同的性能要求,涉及不同配方的磷化液在磷化工艺中应用。
但规模商品化应用的也仅只有几大主要类型,如轻铁系、锌系、锰系、锌钙系,所采用的的促进剂基本都是钼酸盐、硝酸盐、亚硝酸盐、氯酸盐、有机硝硝基化合物等。
磷化处理温度通常为常温型5〜30r,低温型35〜45C,中温型50〜70°
在磷化配方中,大家也许还经常可见到“三合一”、“四合一”,即除油除锈磷化钝化综合处理剂,由于这类几合一处理剂,在国内外都不提倡采用,这量不作叙述。
1配方组成及性能
1.1常温低温型磷化
常温磷化是不加温磷化,温度范围是5〜30C。
低温磷化通常指磷化温度为35〜45