香水瓶模型数控加工工艺规程制订Word下载.docx
《香水瓶模型数控加工工艺规程制订Word下载.docx》由会员分享,可在线阅读,更多相关《香水瓶模型数控加工工艺规程制订Word下载.docx(22页珍藏版)》请在冰豆网上搜索。
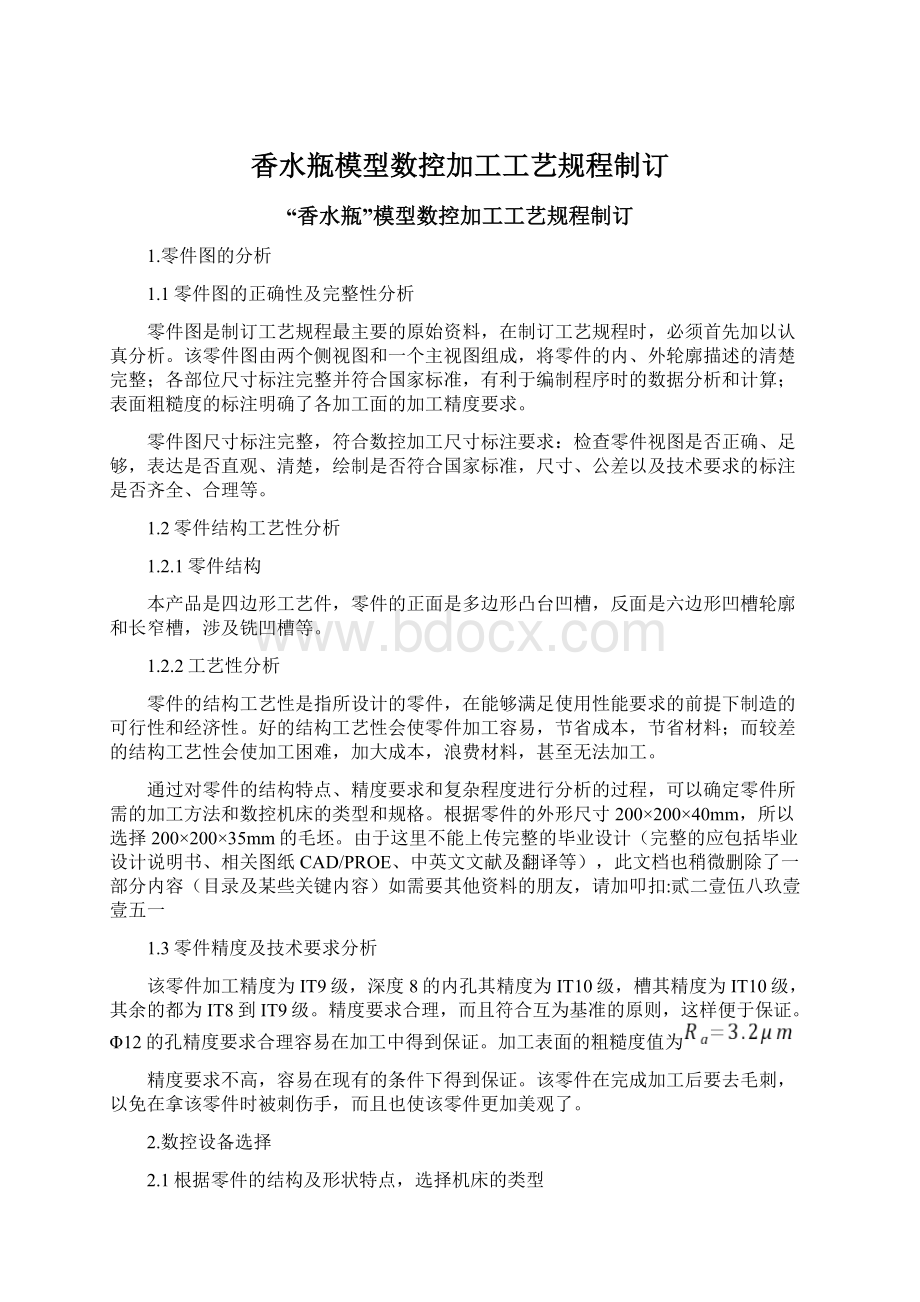
数控机床的最主要规格是几个数控轴的行程范围和主轴电机功率。
机床的三个基本直线坐标(X、Y、Z)行程反映该机床允许的加工空间,在车床中两个坐标(X、Z)反映允许回转体的大小。
一般情况下加工工件的轮廓尺寸应在机床的加工空间范围之内,因此,选用工作台面比典型工件稍大一些是出于安装夹具考虑的,所以工作台面的大小基本上确定了加工空间的大小。
个别情况下也允许工件尺寸大于坐标行程,这时必须要求零件上的加工区域处在行程范围之内,而且要考虑机床工作台的允许承载能力,以及工件是否与机床交换刀刀具的空间干涉、与机床防护罩等附件发生干涉等系列问题。
数控机床的主电机功率在同类规格机床上也可以有各种不同的配置,一般情况下反映了该机床的切削刚性和主轴高速性能。
我所选用的机床型号为VMC750E。
2.3根据零件的加工精度及表面质量要求,选择机床的精度等级
典型零件的关键部位加工精度要求决定了选择数控机床的精度等级。
数控机床根据用途又分为简易型、全功能型、超精密型等,其能达到的精度也是各不一样的。
简易型目前还用于一部分车床和铣床,其最小运动分辩率为0.01mm,运动精度和加工精度都在(0.03~0.05)mm以上。
超精密型用于特殊加工,其精度可达0.001mm以下。
由于我所要加工的零件在精度与表面质量上要求不是太高,所以加工精度保证在0.01mm就可以了。
关于设备选择应注意以下问题:
1)机床加工尺寸范围应与零件的外轮廓相适应。
2)机床的工作精度应与工序的精度要求相适应。
3)机床的生产效率应与零件的生产类型相适应。
4)机床的选择应考虑车间现有设备条件,尽量采用现有设备。
3.定位基准及装夹方式的确定
3.1选择定位基准
在制定工艺规程时,定位基准选择的正确与否,对能否保证零件的尺寸精度和相互位置精度要求,以及对零件各表面间的加工顺序安排都有很大影响,当用夹具安装工件时,定位基准的选择还会影响到夹具结构的复杂程度。
因此,定位基准的选择是一个很重要的工艺问题。
3.1.1定位精基准的选择原则
选择精基准时,主要考虑保证加工精度和工件安装方便可靠。
精基准的选择应遵循以下原则:
1.基准重合原则;
2.基准统一原则;
3.自为基准原则;
4.互为基准原则;
5.所选精基准应保证工件安装可靠,夹具设计简单、操作方便。
结合学校的现有设备、零件的加工要求及毛坯的质量,应以设计基准作为定位基准,这样设计基准与定位基准重合满足基准重合原则。
3.1.2粗基准的选择原则
选择粗基准时,主要要求保证各加工面有足够的余量,并注意应尽快获得精基准。
由于毛坯已经确定采用铝棒,而铝棒的毛坯多适应于加工尺寸较小、精度较高的零件。
铝棒的毛坯精度较高,外圆柱表面的毛坯余量均匀。
所以,可以直接采用毛坯的外圆柱表面作为粗加工定位基准。
以毛坯的外圆柱表面作为粗定位基准,加工出零件的精加工定为基准。
这样可以确保重要表面的精加工余量,采用外圆柱表面作为粗加工定位基准,达到了简单、方便、快捷的目的。
缩短了加工时间,提高了生产效率。
3.2确定合理的装夹方式
3.2.1直接找正装夹
直接找正装夹是用百分表、划线盘或目测直接在机床上找正工件位置的装夹方法。
这种装夹方法容易有误差,不方便。
3.2.2划线找正装夹
划线找正装夹是先在毛坯上按照零件图划出中心线、对称线和各待加工表面的加工线,然后将工件装上机床,按照划好的线找正工件在机床上的装夹位置。
这种装夹方法生产率低,精度低,且对工人技术水平要求高,一般用于单件小批生产中加工复杂而笨重的零件,或毛坯尺寸公差大而无法直接用夹具装夹的场合。
3.2.3用夹具装夹
夹具是按照被加工工序要求专门设计的,夹具上的定位元件能使工件相对于机床与刀具迅速占有正确位置,不需找正就能保证工件的装夹定位精度。
这种装夹方法生产率高,定位精度高,但需要设计、制造专用夹具,广泛用于成批及大量生产。
由于毕业设计所加工的都是单件小批的工艺件,要求较高的精度,因此采用普通的平口虎钳夹具装夹。
4.选择刀具及对刀方式、对刀点
4.1正确选择粗、精加工刀具(附刀具卡)
由于毛坯采用45钢板,硬度、强度都不太大,所以粗、精加工的刀具都可以使用高速钢刀具。
数控加工刀具卡片
产品名称或代号
刀具卡片
零件名称
零件图号
DXXXFX
程序编号
%100
序号
刀具号
刀具名称
刀具规格
刀柄规格
刀片材料
备注
1
T01
面铣刀
Φ80
BT40
硬质合金
2
T02
立铣刀
Φ16
高速钢
3
T03
键槽铣刀
Φ8
4
T04
铰刀
Φ22
5
T05
钻头
Φ24.5
6
T06
Φ25
7
T07
Φ19.8
8
T08
Φ20
9
T09
Φ4
编制
刘馨阳
审核
张淑玲
日期
2011-9-30
共1页
第1页
4.2正确选择对刀方式
对刀的准确程度将直接影响加工精度,因此,对刀操作一定要仔细,对刀方法一定要同零件加工精度要求相适应。
本零件采用手动对刀。
对刀的操作步骤为:
1)将所用铣刀装到主轴上并使主轴中速旋转;
2)手动移动铣刀沿+X方向靠近被测边,直至铣刀周刃轻微接触到工件表面,即产生切屑;
3)保持X、Y坐标不变,将铣刀沿+Z向退离工件;
4)将机床坐标X置零,并X向工件另一侧移动,接触到工件表面产生切屑。
将数值记下,并沿X、+Z向移动刀具到数值的一半,并输到机床坐标系;
5)采用同样方法对Y轴,并将数值输到机床坐标系;
6)将Z周向下移动接触到工件表面产生切屑,将数值输入机床坐标系;
4.3选择合理的对刀点及换刀点
4.3.1合理确定对刀点
对刀点是工件在机床上定位(或找正)装夹后,用于确定工件坐标系在机床坐标系中位置的基准点。
对刀点选定后,便确定了机床坐标系和零件坐标系之间的相互位置关系。
加工中心对刀时一般以机床主轴轴线与端面的交点为刀位点,因此,无论采用哪种工具对刀,结果都是使机床主轴轴线与端面的交点与对刀点重合,利用机床的坐标显示确定对刀点在机床坐标系中的位置,从而确定工件坐标系在机床坐标系中的位置。
为提高零件的加工精度,减少对刀误差,对刀点应尽量选在零件的设计基准或工艺基准上。
本件为单件小批量生产,毛坯精度要求不高,所以采用手动手动手shou
手动对刀。
4.3.2合理确定换刀点
在加工中心等使用多种刀具加工的机床上,工件加工时需要经常更换刀具,在程序编制时,就要考虑设置换刀点。
换刀点的位置应根据换刀时刀具不碰到工件、夹具和机床的原则而定。
所以机床出场前换刀点已确定,为一个固定点。
5.制定数控加工方案
5.1合理划分数控加工工序
工序主要是指一个或一组工人在一个工作地点或一台机床上,对同一个或几个零件进行加工所连续完成的那部分工艺过程,划分是否为同一个工序的主要依据是:
工作地点(或机床)是否变动和加工是否连续。
本零件的加工工序如下:
1)粗、精铣正面
2)粗、精铣反面
5.2确定工序的合理性
数控加工工序的划分一般可分为:
1)以一次安装所进行的加工作为一道工序
2)以一个完整数控程序连续加工的内容为一道工序
3)以工序上的结构内容组合用一把刀具加工为一道工序
4)以粗精加工为一道工序
工艺路线方案:
1)铣上平面
2)钻中心孔φ24.5
3)铰孔φ25±
0.02
4)钻四周4-φ19.8孔
5)铰孔4-φ20孔
6)粗铣四片槽宽为10为深度5的凹槽
7)精铣四片槽宽为10为深度5的凹槽
8)粗铣槽宽为5为深度3的六边形凹槽
9)精铣槽宽为5为深度3的六边形凹槽
10)铣下平面
11)粗铣中心φ160内圆轮廓
12)精铣中心φ160内圆轮廓
13)粗铣不规则的多段线内槽轮廓
14)精铣不规则的多段线内槽轮廓
15)粗铣中间椭圆内槽轮廓
16)精铣中间椭圆内槽轮廓
把粗、精加工步骤一次就加工完,所以可以避免装夹的误差经以上分析我所选的是方案。
5.3确定各工序工步的次序并绘制走刀路线图(附走刀路线图)
走刀路线见走刀路线图。
6.合理确定切削用量
切削用量的大小对切削力、切削功率、刀具磨损、加工质量、生产率和加工成本等均有显著的影响。
在切削加工中,采用不同的切削用量会得到不同的切削效果,为此必须合理选择切削用量。
所谓合理选择切削用量,是指在保证工件加工质量和刀具耐用度的前提下,充分发挥机床、刀具的切削性能,使生产率最高,生产成本最低。
对于不同的加工方法,需要选用不同的切削用量。
切削用量的选择原则是:
保证零件加工精度和表面粗糙度,充分发挥刀具切削性能,保证合理的刀具耐用度;
并充分发挥机床的性能,最大限度提高生产率,降低成本。
6.1确定合理的数控加工余量
加工余量是指加工过程中,所切去的金属层厚度。
分工序加工余量(相邻两工序的工序尺寸之差)和加工总余量(毛坯尺寸与零件图设计尺寸之差),加工总余量等于各工序加工余量之和。
影响加工余量的因素:
①上工序表面粗糙度和缺陷层
②上工序的尺寸公差
③上工序的形位误差
④本工序的装夹误差
确定加工余量的方法:
①经验估算法凭借工艺人员的实践经验估计加工余量,所估余量一般偏大,仅用于单件小批生产。
②查表修正法先从加工余量手册中查得所需数据,然后再结合工厂得实际情况进行适当修正。
此方法目前应用最广。
③分析计算法根据加工余量的计算公式和一定的试验资料,对影响加工余量的各项因素进行综合分析和计算来确定加工余量的一种方法。
适用于贵重材料和军工生产。
余量的方法
确定加工余量时应该注意的几个问题:
①采用最小加工余量原则在保证加工精度和加工质量的前提下,余量越小越好,以缩短加工时间、减少材料消耗、降低加工费用。
②余量要充分防止因余量不足而造成废品。
③余量中应包含热处理引起的变形
④大零件取大余量零件愈大,切削力、内应力引起的变形愈大。
因此工序加工余量应取大一些,以便通过本道工序消除变形量。
⑤总加工余量(毛坯余量)和工序余量要分别确定总加工余量的大小与所选择的毛坯制造精度有关。
粗加工工序的加工余量不能用查表法确定,应等于总加工余量减去其他各工序的余量之和。
我加工的工艺件为单件生产,所以采用经验估算法,根据公式:
Z=a-b,Z=da-db估算出本工艺件的工序余量为:
工序一:
估算表面余量为3,单边余量为5,双边余量为10
工序二:
估算表面余量为3,单边余量为5,双边余量10
总余量为两工序余量之和:
36
6.2确定背吃刀量
背吃刀量应根据加工余量确定。
粗加工时应尽量用一次走刀切除全部加工余量,当加工余量过大、机床功率不足、工艺系统刚度不够、断续切削及切削时冲击振动较大时,可分几次走刀。
多次走刀时,应将第一次的背吃刀量取大些,一般为总加工余量的2/3~3/4。
在中等切削功率的机床上,粗加工背吃刀量可达8~10mm,精加工背吃刀量可取为0.1~0.5mm。
6.3确定进给速度
6.3.1确定进给量
进给量是数控铣床切削用量中的重要参数,主要根据零件的加工精度和表面粗糙度要求以及刀具、工件的材料性质选取。
最大进给量受机床刚度和进给系统的性能限制。
1)当工件的质量要求能够得到保证时,为提高生产效率,可选择较高的进给量。
一般在100~200mm/min范围内选取。
2)当加工精度、表面粗糙度要求高时,进给量应选小些,一般在20~50mm/min范围内选取。
生产实际中多采用查表法、经验法确定合理的进给量。
粗加工时,根据工件材料、铣刀直径及已确定的背吃刀量来选择进给量;
在半精加工和精加工时,则按加工表面粗糙度要求,根据工件材料,切削速度来选择进给量。
6.3.2进给速度的确定
进给速度是数控机床切削用量中的重要参数,主要根据零件的加工精度和表面粗糙度要求以及刀具、工件的材料性质选取。
最大进给速度受机床刚度和进给系统的性能限制。
确定进给速度的原则:
1)当工件的质量要求能够得到保证时,为提高生产效率,可选择较高的进给速度。
2)在切断、加工深孔或用高速钢刀具加工时,宜选择较低的进给速度,一般在20~50mm/min范围内选取。
3)当加工精度,表面粗糙度要求高时,进给速度应选小些,一般在20~50mm/min范围内选取。
4)刀具空行程时,特别是远距离“回零”时,可以设定该机床数控系统设定的最高进给速度。
6.4确定主轴转速
6.4.1确定切削速度
确定的最终目的是确定铣床主轴转速。
生产中经常根据实践经验和有关手册资料选取切削速度,然后算出主轴转速。
在生产中选择切削速度的一般原则是:
(1)粗铣时,背吃刀量和进给量较大,故选择较低的切削速度;
精铣时,背吃刀量和进给量均较小,故选择较高的切削速度。
(2)工件材料强度、硬度高时,应选较低的切削速度。
(3)刀具材料的切削性能愈好,切削速度也选得愈高。
6.4.2确定主轴转速
主轴转速的计算公式为:
n=1000Vc/πD
式中切削速度的单位为m/min,由刀具的耐用度决定;
n——主轴转速,单位为r/min;
D——铣刀直径,单位为mm。
计算出主轴转速n后,在CAD/CAM编程软件主轴转速设置栏中输入接近的转速。
主轴转速应根据允许的切削速度和工件(或刀具)直径来选择。
其计算公式为:
n=1000v/πD式中v----切削速度,单位为m/min,由刀具的耐用度决定;
n---主轴转速,单位为r/min;
D----工件直径或刀具直径,单位为mm。
计算的主轴转速n最后要根据机床说明书选取机床有的或较接近的转速。
7.确定切削速度、主轴转数及进给量的具体数值
主体加工条件:
工件材料:
45钢板。
机床:
VMC750E立式加工中心(HNC-21m)。
工件毛坯尺寸200×
35。
1.铣平面
⑴机床:
VMC750E
⑵铣上平面
①刀具:
Φ80mm盘铣刀
②切削速度Vc
参考《数控加工工艺及设备》表5-3可知:
Vc=90m/min
③确定主轴转速ns
ns=
=
=561.2r/min(取整数ns=600r/min)
④进给量F=fzzn
参考《数控加工工艺及设备》表5-2,取进给量fz=0.15mm/z
则进给量F=fzzn=0.15×
3×
561.2=75.54mm/min(取整数F=80mm/min)
2.铣六边形外轮廓
⑵粗铣六边形外轮廓
Φ16mmHSS立铣刀
Vc=18m/min
=578.8r/min(取整数ns=600r/min)
578=112.7mm/min(取整数F=110mm/min)
⑶精铣六边形外轮廓
Vc=40m/min
=778.8r/min(取整数ns=850r/min)
参考《数控加工工艺及设备》表5-2,取进给量fz=0.04mm/z
则进给量F=fzzn=0.04×
778.8=83.5mm/min(取整数F=80mm/min)
3.⑵铣上平面
4.铣轮廓
⑵
Φ5mmHSS键槽铣刀
=575.9r/min(取整数ns=600r/min)
④进给量F=fzzn
参考《数控加工工艺及设备》表5-2,取进给量fz=0.1mm/z
则进给量F=fzzn=0.1×
2×
575.9=78.9mm/min(取整数F=80mm/min)
⑶精形人型内轮廓
Φ10mmHSS键槽铣刀
Vc=38m/min
=794.8r/min(取整数ns=800r/min)
参考《数控加工工艺及设备》表5-2,取进给量fz=0.02mm/z
则进给量F=fzzn=0.02×
794.8=57.64mm/min(取整数F=60mm/min)
5.铣φ12内轮廓
⑵粗铣φ12内轮廓
575.9=78.2mm/min(取整数F=80mm/min)
⑶精铣φ12内轮廓
Φ10mmHSS直柄键槽铣刀
Vc=36m/min
=788.8r/min(取整数ns=800r/min)
参考《数控加工工艺及设备》表5-2,取进给量fz=0.01mm/z
则进给量F=fzzn=0.01×
788.8=58.6mm/min(取整数F=60mm/min)
7.铣削加工下平面
VMC750E
⑵铣削加工下平面,保证总体尺寸高度34mm。
578=67.5mm/min(取整数F=70mm/min)
8.铣Φ160内圆轮廓
⑵粗铣Φ160内圆轮廓
Φ16mmHSS键槽铣刀
=679.8r/min(取整数ns=650r/min)
579.8=77.6mm/min(取整数F=80mm/min)
⑶精铣Φ160内圆轮廓
=796.8r/min(取整数ns=800r/min)
参考《数控加工工艺及设备》表5-2,取进给量fz=0.03mm/z
则进给量F=fzzn=0.03×
796.8=69.4mm/min(取整数F=70mm/min)
8.编制数控加工程序(附程序单)并进行校验