齿辊破碎机维护检修规程Word文件下载.docx
《齿辊破碎机维护检修规程Word文件下载.docx》由会员分享,可在线阅读,更多相关《齿辊破碎机维护检修规程Word文件下载.docx(12页珍藏版)》请在冰豆网上搜索。
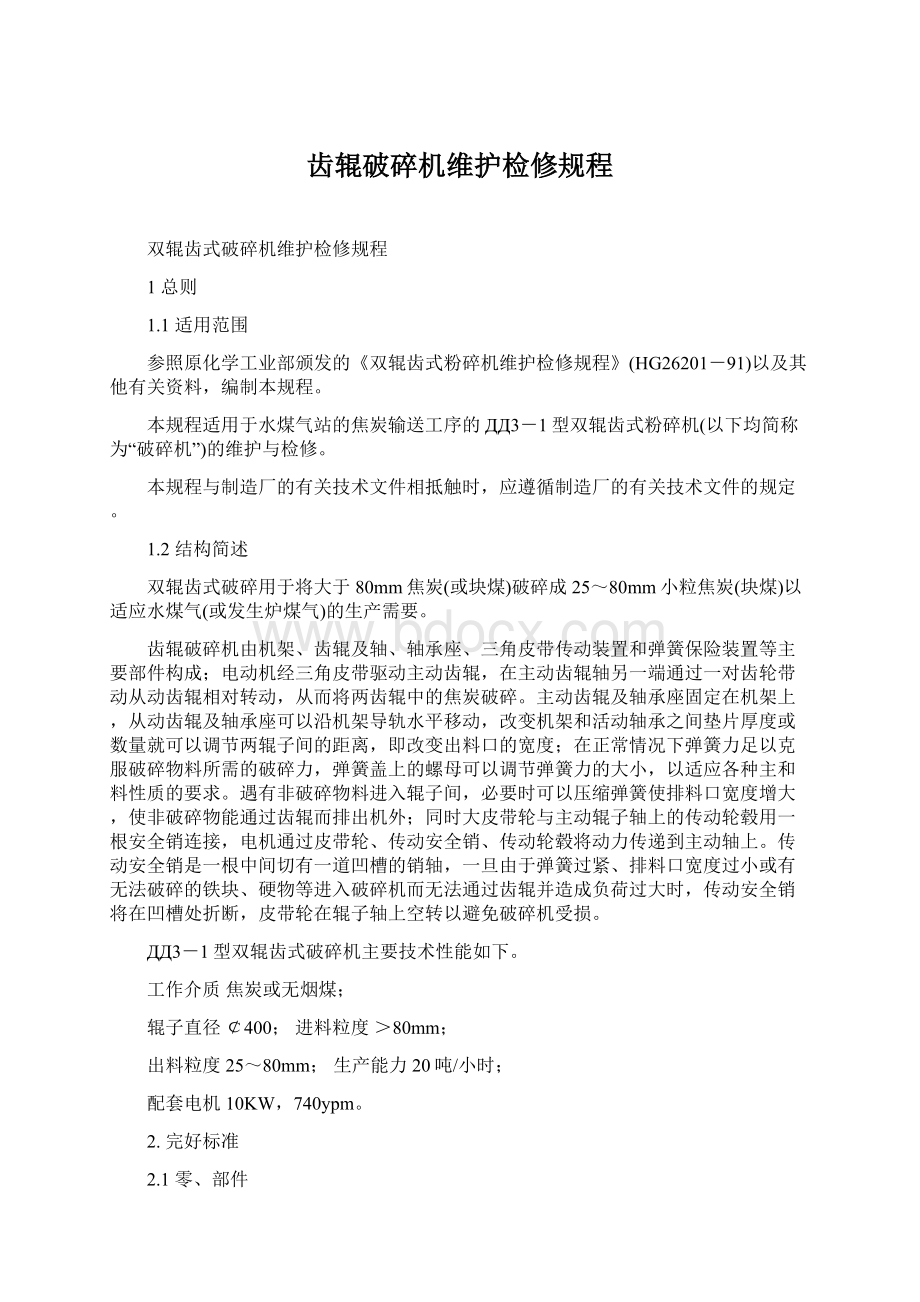
2.2运行性能
2.2.1设备运转平稳,无异常振动和杂音,电机温升和电流不超过允许值。
2.2.2设备达到铭牌出力或查定能力,满足生产需要。
2.2.3润滑良好,注油装置完整好用,油质符合规定要求。
2.2.4各轴承部位温度不超过65℃。
2.3技术资料
2.3.1设备档案齐全,各项数据填写及时、准确;
设备档案应包括如下内容:
2.3.1.1破碎机的出厂合格证、质量证明书,开箱检验记录。
2.3.1.2破碎机的安装、验收和性能试验记录齐全。
2.3.1.3破碎机的设备履历卡片及运行、检测、检修、验收、缺陷和事故记录,润滑油分析和更换记录等齐全、准确。
2.3.1.4破碎机的总装配图、主要零部件图及易损件图等齐全。
2.3.2破碎机的操作规程、安全规程和维护检修规程齐全。
2.4设备及环境
2.4.1设备整洁,表面无灰尘、油垢。
2.4.2设备及管道无跑、冒、滴、漏。
2.4.3设备周围环境整洁,无积水、杂物。
3.齿辊破碎机的维护
3.1维护
3.1.1齿辊破碎机及其附件应完整、可靠,材质符合设计要求,机体表面及其周围要保持清洁,无灰尘和油垢。
3.1.2操作人员应经过考核合格后持证上岗,要做到“四懂”“三会”(即懂结构、懂原理、懂性能、懂用途;
会使用、会维护保养、会排除故障)。
3.1.3破碎机在运行中,操作人员应按照岗位操作法的要求,定时、定点、定线地进行巡回检查,每小时至少一次。
检查内容为:
3.1.3.1破碎机运行是否平稳,有无杂音、异常振动,各轴承部位是否正常。
3.1.3.2检查电机、传动皮带及齿轮运转情况。
3.1.3.3检查各连接螺栓有无松动现象。
3.1.4严格执行《设备润滑管理制度》,定人、定点、定质、定量、定时添加或更换润滑脂。
一般情况下,轴承部位每月添加一次润滑脂,每年更换一次润滑油脂。
3.1.5破碎机长期运行后,因辊齿或辊面磨损使排料口宽度增加,因此应经常检查排出焦炭的粒度,必要时应调节活动辊子的位置,调节时要保持两个辊子互相平行,防止歪斜。
3.1.6破碎机开动前应检查双辊间有无铁块或杂物等卡住,应将所有杂物清理干净,保证破碎机在空载下开车;
启动后机器运行平稳、没有杂音时才允许进入焦炭。
给料量应均衡,避免过载。
若有大块焦炭卡住双辊要迅速停车,取出大块焦炭后并盘车正常方可重新加料。
如因负荷过大而使安全销折断,在更换安全销后必须将破碎机中所有物料全部清除干净,确认已排除故障后方可重新开车。
3.1.7运行中应经常检查各润滑点的润滑情况和轴承温度,一般情况下不允许超过65℃。
加油点零件应完整无缺,防止环境粉尘污染润滑脂。
3.1.8做好设备的清扫、清洁工作,保持设备和环境整洁。
上述各项检查内容中出现故障时,操作人员应及时处理,排除故障并如实填写原始记录;
若故障无法排除时,应根据故障情况采取适当措施如停车、启动备用设备等等,并及时报告有关部门。
3.2常见故障及处理方法
齿辊破碎机的常见故障及处理方法如下表。
故障现象
故障原因
处理方法
轴承发热超过允许温度
1.滑动轴瓦压得过紧,间隙不够或瓦面刮得不好
2.润滑油(脂)脏,润滑不良
3.密封环磨损
4.负荷过大
1.调节轴瓦间隙,轴瓦合金刮好
2.更换润滑油(脂)
3.调整密封环间隙
4.适当减少加料,均匀加料
双辊卡死
铁块或硬杂物卡住
立即停车将铁块或硬杂物取出
出料颗粒大
1.双辊磨损,间隙增大
2.滑动轴承弹簧力不够
1.调节间隙或更换辊子的齿板
2.调紧弹簧
大皮带轮不转或转数不够
1.由于有铁块、硬物或者弹簧过紧等原因造成负荷过大导致大皮带轮的安全销折断
2.皮带过松打滑
1.检查故障原因并排除,更换安全销
2.停车皮带上打蜡,调整皮带长度
齿板松动
固定齿板有螺栓松弛
拧紧螺栓
机器振动
各部紧固螺栓松弛,特别是机架地脚螺栓螺母松弛
系统地拧紧全部连接螺栓,注意检查并拧紧地脚螺栓螺母
4.齿辊破碎机的检修
4.1检修周期及内容
4.1.1破碎机的检修分为小修、中修和大修,检修周期如下:
4.1.1.1破碎机小修的检修周期为12个月。
4.1.1.2破碎机中修的检修周期为36个月。
4.1.1.3破碎机大修的检修周期72个月时。
4.1.2检修内容如下:
4.1.2.1小修
1.检查清理破碎机内堵塞物料;
2.检查齿辊牙齿的磨损与损坏情况;
3.检查各轴承的润滑和磨损情况,添加或更换润滑脂;
4.检查传动齿轮的啮合和磨损情况;
5.更换安全销。
4.1.2.2中修
1.包括小修内容;
2.修理更换传动齿轮;
3.检查或更换轴承;
4.检查调整或更换传动皮带。
4.1.2.3大修
1.包括中修内容;
2.破碎机解体清洗、检查修理或更换零部件;
3.修理或更换齿辊的齿板、齿辊轴。
4.2检修方法及质量要求
4.2.1检修前的准备工作和检修中的注意事项
4.2.1.1确定检修内容,制订检修方案,编制检修计划和检修进度。
4.2.1.2检修前向检修人员进行任务、技术、安全交底,检修人员应熟悉检修规程和质量标准,对于破碎机存在的重大缺陷,应提出相应的技术措施。
4.2.1.3落实检修所需的材料与备件,校验检修中所使用的量具、仪器,准备好检修所需的工具,尤其是专用工具。
4.2.1.4破碎机交付施工单位进行检修前,设备所在单位必须按照原化学工业部颁发的《化学工业企业安全管理制度》和《化学工业部安全生产禁令》的有关规定切断电源,并挂上“有人工作,禁止合闸”警戒牌;
不具备施工条件时不得强行检修。
4.2.1.5在检修中零部件的拆装应按规定顺序进行,尽量使用专用工具;
一些可以不拆的组合件尽量不拆;
在拆卸过程中不准随意破坏零件,万不得已时必须经过有关技术人员的批准。
4.2.1.6检修过程中,零部件在拆卸后和装配前都必须按要求对检修部位及关键部位进行测量,要记录下检修部位和关键部位的原始数据,如破碎机轴瓦间隙等,并与图纸进行核对,作为以后装配时的参考;
要如实填写检修记录。
经过检修的零部件尺寸及各部位的配合尺寸,必须恢复到有关图纸和技术文件所规定或允许的范围内。
4.2.1.7拆卸时,各零件的相对位置和方向要做好标记,要放置有序以免回装中出现漏装、错位、倒向等错误。
即使具有互换性的零件在组装时也不得随意调换位置,以免使原先磨合的配件又重新开始磨合,甚至产生其它问题;
拆卸下来的零件要清洗干净,摆放整齐;
精密加工的零件或部位要用干净布包扎好,不得直接接触地面。
4.2.2机身及机架
4.2.2.1机身两侧护板应平整,平面翘曲度不得大于1.5mm,否则应予以修正。
厚度磨损达到原设计的2/5时应予以更换。
4.2.2.2机架的水平及垂直平面调整应以轴承为基准面,在轴承部位测量机架的纵向和横向水平度误差均应不大于0.20mm/m。
4.2.2.3在安装和校准机架后,拧紧地脚螺栓,在机架与基础之间的间隙中进行再灌浆。
水泥浆应具有良好的流动性,以便使水泥浆达到各个角落形成一个完整而又坚固的灌浆层。
灌浆层凝固并将破碎机的地脚螺帽再次拧紧后才可以继续安装破碎机的其它部件。
4.2.3齿辊
破碎机的齿辊由齿辊轴、轴毂和高锰钢齿板等零件组成。
4.2.3.1齿辊轴及轴瓦
1.轴与轴颈应无损坏、裂纹等缺陷,对于轻微的划痕和碰伤可用油石或细砂布来打磨,如发现裂纹即更换新轴。
2.轴的弯曲度不得大于0.25mm,否则必须调直或更换新轴;
轴颈的锥度和椭圆度不得大于0.02mm。
3.轴颈部分表面粗糙度为1.60,轴瓦与轴颈接触弧面应为100°
~120°
,接触面上的接触点数在每平方厘米内至少有3个接触印迹;
轴瓦与轴颈之间的顶间隙为轴颈直径的0.10~0.15%,每侧的侧间隙应为顶间隙的50~70%。
轴瓦的顶部间隙超过轴颈的0.25%时,或者轴瓦合金磨损达到原厚度的1/2时,轴瓦应予以报废。
4.主轴中心线与轴颈中心线不重合偏差不大于0.2mm/m;
轴在拆卸后要保护轴颈表面,以免受到损伤或脏污。
5.主轴中心线与键槽中心线不重合偏差不大于0.2mm/m;
键与键槽应紧密结合,不得加垫片;
键槽磨损后,可根据磨损情况适当加大,但最大只能按标准尺寸增大一级,在结构和受力允许时,可在原键槽的90°
或120°
方向另开键槽。
6.轴瓦应与轴颈配合修刮,要求轴瓦与轴在整个长度上应有75~80%的弧面接触,接触角为100~120°
;
轴瓦背面应与外壳瓦窝弧面严密贴合,每平方厘米内至少有一个接触印迹。
轴瓦巴氏合金与瓦壳结合应牢固,巴氏合金瓦面不应有裂纹、砂眼、和剥落现象。
可以用煤油浸泡轴瓦约30分钟,取出轴瓦擦干,再将巴氏合金与瓦壳结合处均匀涂上一层白粉,经过30分钟以后如发现有油迹渗出则说明轴瓦的将巴氏合金与瓦壳结合不严密应重新浇铸。
轴瓦巴氏合金与轴承座的脱壳面积如超过半个轴瓦面积的20%或轴瓦合金表面有磨损、擦伤、剥落和熔化等缺陷,缺陷面积超过其接触面积的25%时,应重新浇铸巴氏合金。
低于上述数据时,可用气焊修补,修补用巴氏合金的化学成份应与原有的一致。
7.轴承座不得有毛剌、裂纹、断裂等缺陷;
轴承座与轴瓦配合的孔表面粗糙度为1.60,配合公差为J7。
8.轴承座安装后水平度误差应不超过15mm/m。
4.2.3.2轴毂
1.安装后水平误差不大于0.05mm,轴毂的直线度偏差不大于0.07mm
2.轴毂上安装齿板的四个平面应平整,相对两个平面应互相平行;
其横断面应呈正方形。
4.2.3.3齿板
1.齿板与轴毂结合的平面应平整,齿板与轴毂能紧密贴合,用红油检查每平方厘米内接触点不少于3点。
2.齿板安装后齿辊齿顶与外壳间隙为1~5mm,齿辊两端与端盖间隙为0.5~1.5mm,两个辊轴之间的距离应符合技术要求,间隙超过标准时应进行调整或修理。
3.安装齿板时,辊齿的齿尖应对准另一齿轴的齿槽。
4.齿辊安装后固定齿辊的轴线与可动齿辊的轴线应互相平行,不得歪斜,两齿辊的轴线不平行度偏差应不超过0.20/1000;
可动齿辊轴两边的弹簧受力应均匀。
4.2.3.4辊轴调节装置及弹簧
1.可动齿辊轴承座应在导轨上能自由滑动,不得有卡涩现象;
齿辊面磨损后,排料口宽度增加,需要对活动辊进行调节,调节时将活动轴承座与机架间的垫片数量或厚度减少,使双辊间距符合出料粒度要求。
调节时要保持两个辊子互相平行,防止歪斜。
2.可动齿辊两端调节弹簧安装前,检验其自由高度是否等高,两根弹簧高度允差为±
0.5mm,两端面必须平行并与中心线垂直,端面应光洁平整;
如发现弹簧有裂纹等缺陷必须更换,不得继续使用。
3.弹簧在最大设计负荷下工作24小时不得发生残余变形,否则应更换;
在机组运转过程中如发现残余变形时应立即更换;
弹簧力的大小对于出料粒度有影响,因此弹簧的松紧调节要适宜,不要过紧或过松,并用双螺帽锁紧。
4.2.4传动齿轮
用涂色、压铅等方法检查传动齿轮的啮合面磨损情况,当啮合间隙和磨损量超过规定要求时,应进行调整、修理或更换。
4.2.5皮带轮
4.2.5.1技术要求
1.保证皮带轮与轴的同心度,当皮带轮的直径为D时,一般要求其外圆的径向圆跳动应小于(0.00025~0.0005)D;
端面摆动量小于(0.005~0.001)D。
2.两皮带轮中间平面的轴向偏移量应小于1/100A(A为皮带轮的实际中心距)。
3.两皮带轮轴线的平行度误差应小于1/100A。
4.皮带轮工作表面的表面粗糙度要适当,一般为1.60或0.80。
5.皮带在小皮带轮上的包角应大于120°
。
6.皮带的张紧力应适当。
4.2.5.2安装前的准备工作
1.按图纸要求检验零件的尺寸、几何形状及表面粗糙度是否达到要求。
2.将皮带轮及轴清理干净,并按要求准备好连接键;
当配合面为圆锥面时,需用涂色法检查其配合情况,接触面积应大于75%,并且分布均匀。
3.选择装配方法,并准备适当的压入工具。
4.2.5.3安装及质量检查
1.破碎机皮带轮和轴的装配:
皮带轮和轴采用过渡配合(H7/k6);
一般可采用锤击法进行装配。
即采用手锤或大锤敲打安装,但不得用锤直接敲打轮毂,应在轮毂上垫上木块或铜棒。
为了便于安装,装配前应在配合面上涂以润滑油。
皮带轮安装在轴上后,应对其径向圆跳动和端面摆动量进行检查。
一般采用划针检查,在要求较高时则用千分表检查。
一般造成皮带轮径向圆跳动和端面摆动的原因如表1。
表1.
原因
消除方法
轴弯曲
轴校直
轴与孔配合间隙过大
在轴与孔间垫薄铜片或用喷涂方法增大轴径或减小孔径
皮带轮孔本身缺陷(皮带轮孔与其外圆不对中;
皮带轮孔中心线与端面不垂直)
修配或更换皮带轮
2.皮带轮的配对安装皮带轮安装后应对其相互位置的正确性进行检查。
皮带轮相互位置的正确性主要是由皮带轮轴向偏移量和皮带轮中心线平行度来衡量。
皮带轮轴向偏移量的测定有直尺测定法(中心距不大的场合下使用)和拉线法两种。
具体方法如图1所示。
皮带轮中心线平行度的检查方法如图2所示。
测量L1和L2,设测量点相距L,则每米长度上的平行度误差δ为:
δ=(L1-L2)×
1000/Lmm
3.皮带的安装安装三角皮带时,应先将皮带轮的中心距调小,再将皮带放入轮槽,并调整好中心距。
三角皮带的型号应与轮槽吻合,皮带在轮槽中的位置应恰当,如图3所示。
适当的预紧力是保证三角皮带正常工作的重要因素。
预紧力不足皮带将在皮带轮上打滑,使皮带轮发热,胶带磨损;
预紧力过大,则使胶带的寿命降低,轴和轴承间的比压增大,磨损加快。
在皮带传动中,皮带预紧力是通过在两皮带轮的切边中点处,垂直带边加一载荷P,使其产生规定的挠度来控制,如图4所示。
三角皮带传动中,规定在载荷P的时作用下每100mm长的切边中点产生1.6mm挠度时的预紧力为恰当值,P值如表2。
表2.
皮带
型号
P,Kgf
O
0.50~0.80
C
2.40~3.20
A
0.85~1.20
D
4.90~6.70
B
1.40~1.70
E
7.20~10.0
4.2.5.4三角皮带传动件的使用与维护
1.皮带运行中应随时调整,以保持适当的预紧力,不能过紧或过松。
新装的皮带不宜过紧,一般应运转数天并有松弛现象以后,再进行调整。
2.应防止皮带接触酸、碱、柴油、机油、汽油等物,避免阳光直接曝晒。
3.不同厂出品或新旧程度不同的三角皮带不能同组使用,不同规格型号的皮带也不能互相替代。
4.三角皮带不宜在高于60℃的环境下运转。
5.皮带轮轮孔有裂纹,轮槽缺口或槽面严重磨损时应予以更换;
三角皮带出现磨损严重,皮带与槽底接触,皮带老化,有裂纹或塑性扭曲等情况时均应更换;
同一皮带轮上的三角皮带应同时更换。
6.为防止皮带打滑,使用皮带腊或皮带油时应涂于皮带的工作面上,但一般不采用;
如发生打滑可增加皮带张紧力。
7.保持皮带和皮带轮的干净整洁,防止灰尘侵入。
8.为确保安全运行必须加防护罩。
5试车与验收
5.1试车前的准备工作
5.1.1确认检修项目已全部完成,检修质量符合检修规程的质量标准。
5.1.2确认设备内没有残存异和的,安全装置和附件齐全,动作灵敏。
5.1.3确认和中润滑部位按润滑要求注满润滑脂。
5.1.4具体落实试车安全注意事项,并有专人负责。
5.1.5环境整洁无杂物,所有安全设施均符合要求。
5.2无负荷试车
确认试车前的准备工作已经完成,手动盘车两三周,注意机内有无异常声响或阻塞现象,确认转动无阻方可开车;
先瞬时开车启动后立即停车,检查各部情况及转动方向,再进行第二次启动,运行30分钟,如运转正常则继续运行二小时。
无负荷试车应达到下列要求:
5.2.1按程序启动和停车,各有关连锁系统均符合设计要求。
5.2.2运行中破碎机各部位声响正常,无异常磨擦、碰撞现象;
所有紧固件应牢固无松动现象。
5.2.3各轴承运行、润滑正常,轴承温升在规定范围之内。
5.2.4大皮带轮(飞轮)运转平稳。
5.2.5所有调整机构应灵活并达到规定的调整范围。
5.2.6所有摩擦部位不得有擦伤、烧伤、掉屑和研磨等现象。
5.3负荷试车
5.3.1破碎机经无负荷试车合格后,应停车全面检查机组的各个部位及联接件,若无松动和异常磨损时,可以进行负荷试车。
5.3.2试车中注意检查轴承温度,一般不超过65℃(温升不超过40℃)。
5.3.3破碎机进出料应保持均匀,投料数量和出料粒度应严格执行操作规程。
5.3.4负荷试车连续运转时间一般不少于两个工作班时间。
5.3.5负荷试车结束后,应检查传动皮带等有无松动和异常磨损。
5.3.4验收破碎机达到下列各项要求时可以办理验收交接手续,交付生产。
5.3.4.1检修质量符合本规程要求,检修记录齐全、准确。
5.3.4.2各项试车运行正常,符合要求。
5.3.4.3安全联锁装置完整、准确、灵敏。
5.3.4.4零部件完整,机组整洁。
6维护检修安全注意事项
6.1维护安全注意事项
6.1.1严格按操作规程启动、运行与停机。
6.1.2设备运行时禁止擦拭运转部位。
6.1.3传动皮带等部位应有良好的防护装置,不得随意拆除安全防护装置。
6.1.4电机外壳应有良好的接地,不准用水冲洗电机及设备。
6.1.5启动破碎机前必须先盘车,不准带负荷启动。
6.2检修安全注意事项
6.2.1检修前必须按规定办理检修任务书。
6.2.2检修前必须切断电源并在电源处挂“有人工作,禁止合闸”的标志牌。
6.2.3检修工具及拆卸、清洗、更换的零部件要在规定的地方整齐摆放,实行科学检修、文明施工。
6.2.4需在生产现场进行动火作业时,必须办理动火证,经许可后方可动火。
6.3试车安全注意事项
6.3.1试车工作应由专人负责,统一指挥;
试车应由专人操作,操作者应持有本岗位的“安全作业证”。
6.3.2设立明显的试车标志,禁止无关人员进入试车现场。
6.3.3按运转设备起动前的安全要求,做好试车前的各种安全检查并符合要求,如接地线完好牢固、地脚螺栓紧固、安全防护装置齐全、安全销应装正确等。
6.3.4试车中注意破碎机的运转是否正常,如发现异常应立即停车检查、处理,消除故障后重新试车。