压盖件的冲压工艺与落料冲孔复合模设计文档格式.docx
《压盖件的冲压工艺与落料冲孔复合模设计文档格式.docx》由会员分享,可在线阅读,更多相关《压盖件的冲压工艺与落料冲孔复合模设计文档格式.docx(8页珍藏版)》请在冰豆网上搜索。
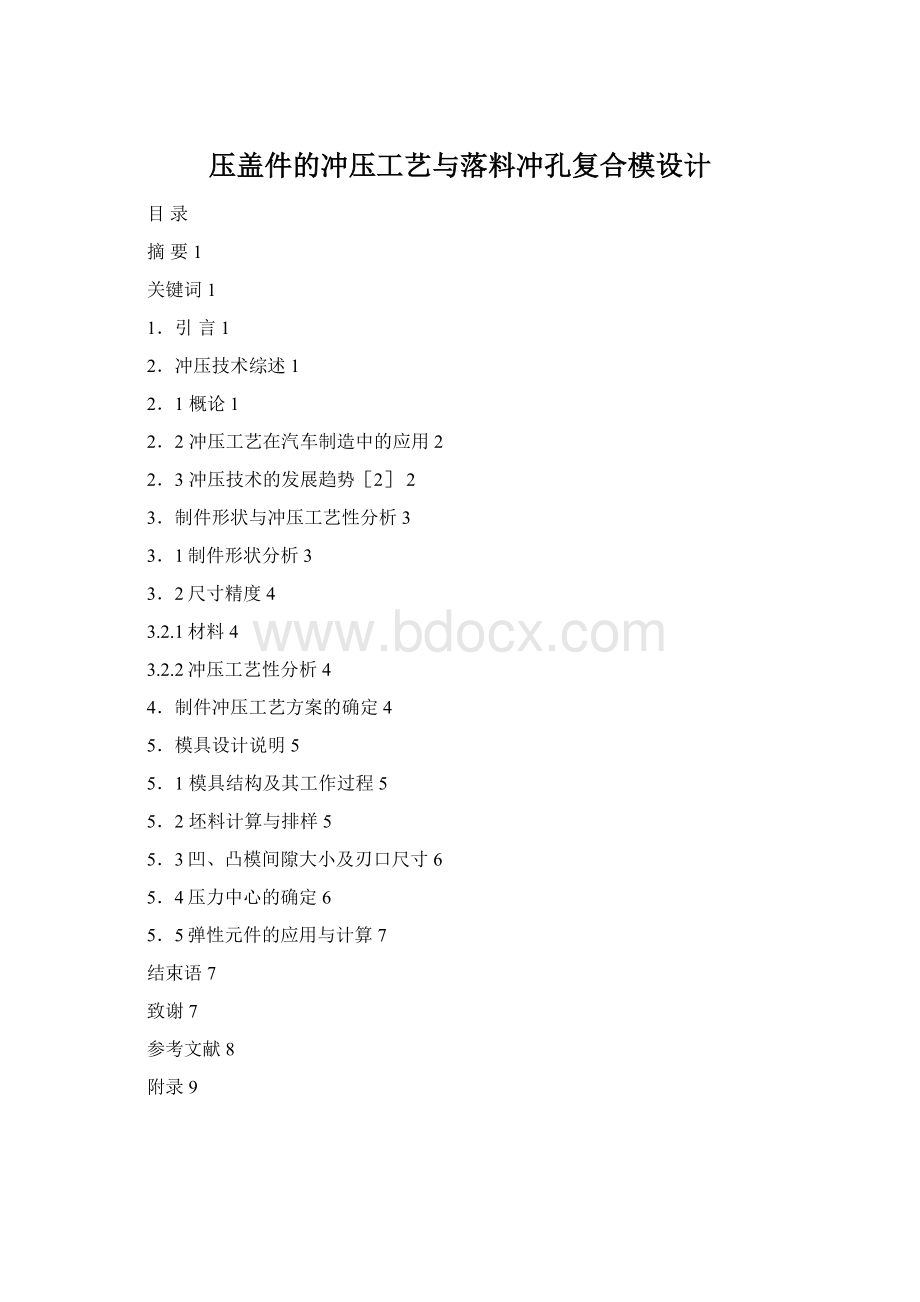
5.4压力中心的确定6
5.5弹性元件的应用与计算7
结束语7
致谢7
参考文献8
附录9
压盖件的冲压工艺与落料、冲孔复合模设计
***
指导教师:
【摘要】本文为毕业设计说明书。
内容主题是关于压盖件的冲压工艺分析与模具设计说明。
按毕业设计要求,根据产品图分析了零件的结构及冲压工艺性,对其冲压工艺方案进行了比较,提出了合理冲压工序排列方案。
文中就落料、冲孔复合模结构方案、相关工艺计算、模具工作零件尺寸计算与技术要求以及模具设计中的其他注意事项进行了必要说明。
【关键词】压盖件、冲压工艺、复合模设计
1.引言
本人毕业设计课题是一个汽车小型压盖件的冲压工艺分析与模具设计。
课题来源于吉利豪情汽车制造有限公司,结合企业生产实际进行分析与设计。
课题任务如任务书所示,要求分析零件的结构及冲压工艺性,对其冲压工艺方案进行比较,提出合理冲压工序排列方案,完成其落料、冲孔复合模的结构设计,绘制模具结构装配图及凸、凹模工作零件图。
同时,要求就相关工艺计算、模具工作零件尺寸计算与技术要求以及模具设计中的其他注意事项进行必要说明,写出设计说明书。
2.冲压技术综述
2.1概论
冲压工艺是塑性加工的基本方法之一。
它主要用于加工板料零件,所以有时也叫板料冲压。
冲压不仅可以加工金属板料,而且也可以加工非金属板料。
冲压加工时,板料借助于模具作用,于其内部产生使之变形的内力。
当内力的作用达到一定程度时,板料的某一部分便会产生与内力的作用性质相对应的塑性变形,从而获得一定的形状、尺寸和性能的零件。
2.2冲压工艺在汽车制造中的应用
冲压加工是完成金属塑性成形的一种重要手段,它是最基本、最传统、最重要的金属加工方法之一。
汽车制造中有60%-70%的金属零部件需经塑性加工成形,如车身上的各种覆盖件、车内支撑件、结构加强件,还有大量的汽车零部件,如发动机的排气弯管及消声器、空心凸轮轴、油底壳、发动机支架、框架结构件、横纵梁等等,都是经冲压而成形。
目前冲压技术正向精密、多功能、高效节能、安全清洁的生产方向发展。
冲压工件的制造工艺水平及质量,在较大程度上对汽车制造质量和成本有直接的影响。
汽车冲压件都应具有良好的工艺品性和经济性,衡量其水平的重要标志有冲压件的工序数、车身总成的分块数量和尺寸大小、冲压件的结构等因素。
减少冲压过程的工序数,意味着减少冲压件数、节省工装数量、简化冲压过程的传送装置,缩减操作人员和冲压占地面积,是节约投资额和能耗的极好措施,所以冲压制造商都能把冲压工序数设计作为降低汽车制造成本的重要途径,甚至不惜改进产品设计来满足制造工艺方面的要求。
同时,还应采用尽量大尺寸的合理的车身总成分块,如整块式车身左右侧板及车顶盖板,既可使汽车外形美观,使之空气阻力减少,又可减少冲压件数量及焊点,能有效地降低成本。
而且现代汽车制造大量使用卷料、薄壳式整体车身结构的高强度钢板与镀锌钢板,都要求应用冲压新工艺。
2.3冲压技术的发展趋势[2]
(1)进入90年代以来,高新技术全面促进了传统成形技术的改造及先进成形技术的形成和发展。
21世纪的冲压技术将以更快的速度持续发展。
发展的方向将更加突出“精、省、净”的需求。
(2)冲压成形技术将更加科学化、数字化、可控化。
科学化主要体现在对成形过程、产品质量、成本、效益的预测和可控程度。
成形过程的数值模拟技术将在实用化方面取得很大发展,并与数字化制造系统很好地集成。
人工智能技术、智能化控制将从简单形状零件成形发展到覆盖件等复杂形状零件成形,从而真正进入实用阶段。
(3)注重产品制造全过程,最大程度地实现多目标全局综合优化。
优化将从传统的单一成形环节向产品制造全过程及全生命期的系统整体发展。
(4)对产品可制造性和成形工艺的快速分析与评估能力将有大的发展。
以便从产品初步设计甚至从构思时起,就能针对零件的可成形性及所需性能的保证度,作出快速分析评估。
(5)冲压技术将具有更大的灵活性或柔性,以适应未来小指量多品种混流生产模式及市场多样化、个性化需求的发展趋势,加强企业对市场变化的快速响应能力。
(6)重视复合化成形技术的发展。
以复合工艺为基础的先进成形技术不仅正在从制造毛坯向直接制造零件方向发展,也正在从制造单个零件向直接制造结构整体的方向发展。
加入wto以后,中国的汽车工业等支柱产业必将有大的发展。
我国的冲压行业既充满发展的机遇,又面临进一步以高新技术改造传统技术的严峻挑战。
国民经济和国防建设事业将向冲压成形技术的发展提出更多更新更高的要求。
我国的板料加工领域必须加强国内外力量的联合,加强技术的综合与集成,加快传统技术从经验向科学化转化的进程。
加速人才培养,提升技术创新能力,提高冲压技术队伍的整体素质和生产企业的竞争力.
3.制件形状与冲压工艺性分析
3.1制件形状分析
制件形状与尺寸如图2-1所示,为油泵连接板。
外形不对称,由4段直线和5段圆弧平滑连接而成。
中心为梨形孔翻边,翻边高度7.5mm。
翻边孔两边分别有一大一小的4孔。
孔径分别为φ8.4和φ4.6.
图2-1制件图
3.2尺寸精度
制件图中,大孔孔心距78mm±
0.20mm,冲裁度断面的表面粗糙度为6.3Ra/μm,其余尺寸未注公差,属自由尺寸,一般冲压均能满足其尺寸精度要求。
3.2.1材料
普通碳素结构钢Q235,冷轧板(未退火),厚度为1.5mm,屈服点235Mpa,抗拉强度410-490Mpa(GB701-1997)。
冲压性能良好。
3.2.2冲压工艺性分析
该件形状与结构简单,适宜冲裁,零件外形转角处都有圆角过渡,避免了清角,减小了冲裁难度。
孔边距远大于凸凹模允许的最小间距,符合冲压工艺性要求。
4.制件冲压工艺方案的确定
该零件冲压的基本工序包括落料、冲制大小4孔、中心梨形预制孔和翻边,其翻边高度7.5mm。
设想有以下几种工艺方案:
方案一:
先落料,分别冲孔、翻边,采用单工序模生产。
方案二:
落料-冲制4孔—冲制梨形预制孔和翻边;
方案三:
落料-冲制二孔φ8.4,再采用级进模冲制二小孔、梨形预制孔并翻边。
方案还可以安排数种。
这里本人先就上述三种方案进行讨论和比较。
方案一,采用单工序模生产,显然模具结构简单、但至少要采用5套模具才能完工,工艺过程复杂,模具成本增加,且生产率较低,难以满足该零件的年产量要求。
方案二中冲孔精度容易保证,且生产率高。
但是还需要4副模具,模具成本还是高,工艺过程仍然复杂。
方案三只需要两副模具,生产率也高,零件的冲压精度亦能得到保证。
通过对上述三种方案的分析比较,该件的冲压生产选用方案三。
根据指导教师的分工意见,学生本人的模具设计任务是完成落料—冲制二孔φ10的复合模设计。
中间工序图见图4-1。
图4-1中间工序图
5.模具设计说明
5.1模具结构及其工作过程
该落料-冲孔(φ8.4)复合模采用的是正装模结构形式。
正装模具的结构特点是凹模安装在下模座上。
无论是工件的落料还是冲孔,工件或废料都能非常方便地落入冲床工作台内的卸料孔中。
因此在设计正装模具时,就不必考虑工件或废料的流向。
使得所设计出的模具结构简单且实用。
在设计冲模时,应遵循的设计原则是:
应优先选用正装模具结构。
只有在正装模具结构下能满足工件技术要求时,才可以考虑采用其它形式的模具结构。
模具整体主要由以下零件组成——上底板、上垫板、凸模固定板、导套、导柱、凸模、固定销、凹模、下垫板、内六角螺钉、下底板、凹凸模、卸料板、橡胶等,
详见模具装配图(另附)。
5.2坯料计算与排样
工件的边长50mm,工件厚度1.5mm,查表得到,工件间a1=1.8,沿边a=2.0由于工件类似圆形,所以采用直对排样,如图5-1。
条料宽度为98.8mm
A=5906.533m2(工件面积)B=98.8mmS=99.8mm
图5-1排样图
5.3凹、凸模间隙大小及刃口尺寸
由图可知,该零件属于无特殊要求的一般零件,2xΦ8.4由冲两孔获得,查表得2Cmin=0.132mm
2Cmax=0.240mm
则2Cmax-2Cmin=0.108mm
由公差表查得Φ8.4为IT6~IT7级,取x=0.5
冲孔凸模
dp=(dmin+x△)0δp=(8.4+0.5)0-0.008mm=8.9-0.0200mm
冲孔凹模
dd=(dp+2Cmin)δp0=(8.9+0.132)00.012mm=9.03200.020mm
校核:
︱δp+δp︱≦2Cmax-2Cmin
︱0.020+0.020︱≦0.108mm
0.040mm≦0.108mm(满足间隙公差)
落料凹模:
以制件外形尺寸为基本尺寸;
凸模与落料凹模配作,取间隙0.15mm。
5.4压力中心的确定
定义:
模具压力中心是指冲压时诸冲压力合力的作用点位置。
为了确保压力机和模具正常工作,应使冲模的压力中心与压力机滑块的中心相重合。
本冲模压力中心,可用解析计算法求出
以0为坐标原点,X0=L1X0/L1=49Y0=L1Y0/L1=47.4
∴压力中心:
(49;
47.4)
5.5弹性元件的应用与计算
FQ橡皮圈=Fq
=(17.5)2∏·
0.26=250(KN)
式中F-橡皮圈受力面积,mm
q-单位压力值,mpa,查表如下
表5-1
压缩量%
10
15
20
25
30
35
q值(mpa)
0.26
0.50
0.74
1.06
1.52
2.10
由上得:
FQ橡皮圈﹥FQ。
结束语
这次毕业设计,历时两个月。
在此期间,针对设计内容进行了大量的工作,顺利完成了毕业设计中所提出的各项任务,基本达到了毕业设计的目的。
通过此毕业设计,掌握了模具设计的方法和步骤,并结合具体的零件进行了具体的设计工作,包括凸、凹模间隙大小的确定,压力中心的确定,冲裁工艺性的分析,冲裁力的计算等。
从绘制复合模图纸,到完成CAD造型设计,完成落料冲孔模方案设计和相关设计计算,掌握了完整的工程设计过程,工程设计应用能力得到了锻炼和提高。
但由于缺乏实际工作经验,在这些设计过程中也遇到了很多困难,但在指导老师周述积教授的指导下,问题都迎刃而解。
在设计期间,学习并运用CAD对落料冲孔模进行设计,提高了我对CAD的运用能力和计算机的应用能力,为以后工作奠定了初步基础。
总之,通过本次毕业设计,加强了我对各项知识的学习深度,更培养了分析问题和解决问题的能力,教会我怎样才能按步骤有条不紊地进行工作。
这些为我走上工作岗位奠定了基础。
致谢
感谢我的导师周教授,他们严谨细致、一丝不苟的作风一直是我工作、学习中的榜样;
他们循循善诱的教导和不拘一格的思路给予我无尽的启迪。
感谢我的室友们,从遥远的家来到这个陌生的城市里,是你们和我共同维系着彼此之间兄弟般的感情,维系着寝室那份家的融洽。
三年了,仿佛就在昨天。
三年里,我们没有红过脸,没有吵过嘴,没有发生上大学前所担心的任何不开心的事情。
只是今后大家就难得再聚在一起吃每年元旦那顿饭了吧,没关系,各奔前程,大家珍重。
我们在一起的日子,我会记得。
在毕业设计即将完成之际,我的心情无法平静,从开始进入课题到论文的顺利完成,有多少可敬的师长、同学、朋友给了我