第章疲劳强度概述Word格式文档下载.docx
《第章疲劳强度概述Word格式文档下载.docx》由会员分享,可在线阅读,更多相关《第章疲劳强度概述Word格式文档下载.docx(21页珍藏版)》请在冰豆网上搜索。
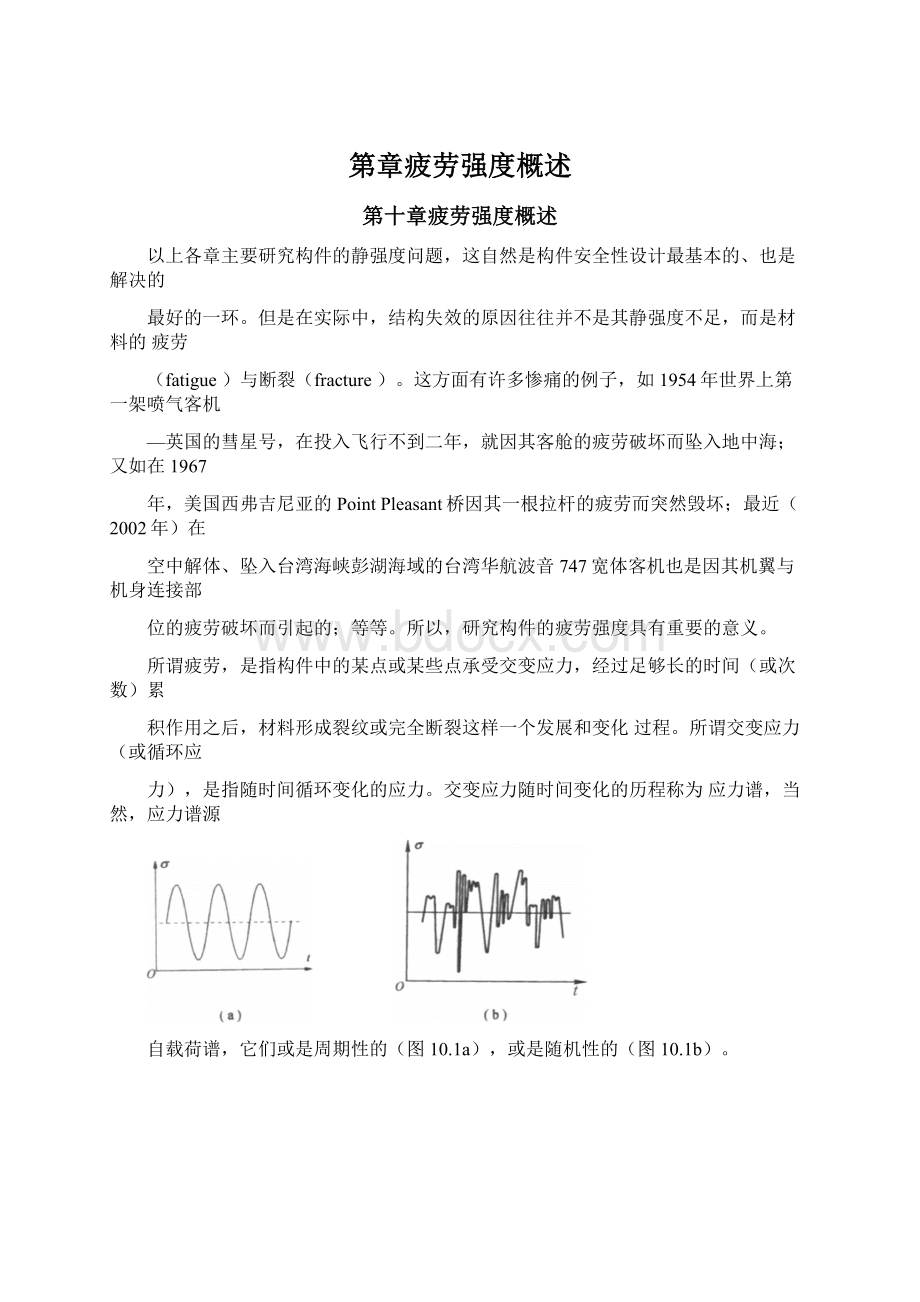
图10.1
理论与实验研究均表明,构件在交变应力下的疲劳破坏,
与静应力下的失效有本质区别,疲劳破坏具有以下特点:
•破坏时应力低于材料的强度极限,甚至低于材料的屈服应力;
•破坏是一个积累损伤的过程,即需经历多次应力循环后才能出现;
•即使是塑性材料,破坏时一般也无明显的塑性变形,即表现为脆性断裂;
•在破坏的断口上,通常呈现两个区域,一个是光滑区域,另一个是粗粒状区域。
例如,
车轴疲劳破坏的断口如图10.2所示。
以上现象可以通过疲劳破坏的形成过程加以说明。
原来,当交变应力的大小超过一定限
度并经历了足够多次的交替重复后,在构件内部应力最大或材质薄弱处,将产生细微裂纹(即
所谓疲劳源),这种裂纹随应力循环次数增加而不断扩展,并逐渐形成宏观裂纹。
在扩展过程中,由于应力循环变化,裂纹两表面的材料时而互相挤压,时而分离,或时而正向错动,从而形成断口的光滑区。
另一方面,由于裂纹不断扩展,当达到其临界长度时,构件将发生突然断裂,断口的粗粒状区就是突然断裂造成的。
因此,疲劳破坏的过程又可理解为疲劳裂纹萌生、逐渐扩展和最后断裂的过程。
本章主要研究构件在交变应力作用下的疲劳强度,以及构件的疲劳寿命估算。
10.1交变应力循环特征
在一个应力循环中,应力的极大值与极小值,分别称为最大应力和最小应力。
最大应力
Gax与最小应力Gin的代数平均值,称为平均应力,并用6表示,即
(10-1)
最大应力与最小应力的代数差之半,称为应力幅,并用;
二表示,即
(10-2)
交变应力的变化特点,可用比值r表示,并称为应力比或循环特征,即
(10-3)
试验表明,r对材料的疲劳强度有直接影响。
在交变应力中,如果最大应力与最小应力
的等值反向,即匚max--;
「min,其应力比「=-1(图10.3b),则称为对称交变应力。
在交变应力中,如果最小应力Cmin为零,其应力比r=0(图10.3C),则称为脉动交变应力。
除对称循环
外,所有应力比r=_1的交变应力,均属于非对称交变应力。
所以,脉动交变应力也是一种非对称交变应力。
以上关于交变应力的概念,都是采用正应力匚表示。
当构件承受交变切应力时,上述概
念仍然适用,只需将正应力;
「改为切应力.即可。
10.2S-N曲线和材料的疲劳极限
疲劳试验与S-N曲线
图10.5
材料的疲劳性能由试验测定,最常用的试验是旋转弯曲疲劳试验(图10.5)。
首先准备一组材料和尺寸均相同的光滑试样(直径为6~10mm)。
试验时,将试样的两端
安装在疲劳试验机的支承筒上,并由电机带动而旋转,在试样的中部通过轴承悬挂砝码,使试样的中部处于纯弯曲状态。
于是,试样每旋转一圈,其中部一点处的材料即经历一次对称
循环的交变应力。
由计数器记下试样断裂时所旋转的总圈数或所经历的应力循环数N,即试
样的疲劳寿命,试验一直进行到试样断裂为止。
同时,根据试样的尺寸和砝码的重量,按弯曲正应力公式二M.W,计算试样横截面上的最大正应力。
对同组试样挂上不同重量的砝码进行疲劳试验,将得到一组关于最大正应力和相应寿命N的数据。
图10.6
以最大应力二为纵坐标,疲劳寿命的对数值lgN为横坐标,根据上述数据绘出最大应力
(Stress)和疲劳寿命间的关系曲线,即SN曲线。
例如,钢的SN曲线如图10.6a所示;
几
种铸钢与铸铁的S-N曲线如图10.6b所示。
可以看出,应力愈大,疲劳寿命愈短。
对于寿命N小于104(或105)的疲劳问题,一般称
为低周疲劳,反之称为高周疲劳。
二、疲劳极限
试验表明,一般钢和铸铁等的S-N曲线均存在水平渐近线。
该渐近线的纵坐标所对应的
应力,称为材料的持久极限,用;
二或,r表示,下标r代表应力比。
然而,有色金属及其合金的S-N曲线一般不存在水平渐近线(图10.7)。
对于这类材料,通常根据构件的使用要求,以某一指定寿命N°
(例如107~108)所对应的应力作为极限应力,
并称为材料的疲劳极限,或条件疲劳极限。
图10.7
为简单起见,以下将持久极限与疲劳极限(或条件疲劳极限)统称为疲劳极限。
同样,也
可通过试验测量材料在拉-压或扭转等交变应力下的疲劳极限。
试验发现,钢材的疲劳极限与其静强度极限二b之间存在下述关系:
弯
cr丄吒(0.4~0.5)crb
拉压狂(0.33~0.59^3(10-4)
扭
0;
拓(0.23~0.29)%
可见,在交变应力作用下,材料的疲劳强度显著降低。
10.3影响构件疲劳极限的主要因素
以上所述材料的疲劳极限,是利用表面磨光、横截面尺寸无突然变化以及直径为6~10mm
的小尺寸试样测得的。
试验表明,构件的疲劳极限与材料的疲劳极限不同,它不仅与材料的性能有关,而且与构件的外形、横截面尺寸、表面状况及使用环境等因素有关。
、构件外形的影响
图10.8
图10.9
试验表明,应力集中促使疲劳裂纹的形成,因此,应力集中对疲劳强度有显著影响。
在对称交变应力作用下,应力集中对疲劳极限的影响,用有效应力集中因数或疲劳缺口因数k;
4或k)表示,它代表光滑试样的疲劳极限与同样尺寸但存在应力集中的试样的疲劳极限的比值。
R/d
图10.10
图10.8、图10.9和图10.10分别给出了阶梯形圆截面钢轴在对称循环弯曲、拉-压和对称
循环扭转时的有效应力集中因数。
应该指出,上述曲线都是在D.d=2且d=30~50mm的条件下测得的。
如果Dd<
2,则
有效应力集中因数为
K;
「=1(K;
:
0-1)(10-5)
K=1(K0-1)(10-6)
V¥
式中,K;
q和K0为Dd=2的有效应力集中因数值;
•为修正系数,其值与Dd有关,可由
图10.11查得。
至于其它情况下的有效应力集中因数,可查阅有关手册。
由式(10-9)与(10-10)可知:
如果q;
-=0和q=0,则K;
-=1和K=1,说明材料对应力集中不敏感;
如果q.;
=1和尸1,贝UK..:
;
=Kt;
「和K沪心.,材料对应力集中十分敏感。
对于钢材,敏感系数之值可采用下述经验公式确定:
(10-11)
式中:
R为缺口(如沟槽及圆孔)的曲率半径;
A为材料常数,其值与材料的强度极限二b以
及屈服应力与强度极限的比值(屈强比h^/Cb有关(图10.12)。
mb。
当需求q;
_时,可分别
(10-11)即可确定
图10.12有两个横坐标,一为强度极限二,另一为屈强比
根据强度极限与屈强比由该图求出两个,A值,然后将二者的平均值代入式q;
_。
当需求q时,则只需根据屈强比求出.A值并代入上式即可。
对于铝合金,估算敏感系数的经验公式则为
(10-12)
1
q一10.9/R
应该指出,目前对敏感系数的研究还不充分。
因此,确定有效应力集中因数最可靠的方法是直接进行实验或查阅有关实验数据。
但在资料缺乏时,通过敏感系数来确定有效应力集中因数,仍不失为一个相当有效的办法。
图10.13
由图10.8~16-10可以看出:
圆角半径R愈小,有效应力集中因数K.0和K0愈大;
材料
的静强度极限6愈高,应力集中对疲劳极限的影响愈显著。
所以,对于交变应力下工作的零构件,尤其是用高强度材料制成的零构件,设计时应尽
量减小应力集中。
例如:
增大圆角半径;
减小相邻杆段横截面的粗细差别;
采用凹槽结构
10.13a);
设置卸荷槽(图10.13b);
将必要的孔或沟槽配置在构件的低应力区;
这些措施均能显著提高构件的疲劳强度。
图10.14
二、构件截面尺寸的影响
图10.15
弯曲和扭转疲劳试验均表明,疲劳极限随构件横截面尺寸的增大而降低。
截面尺寸对疲劳极限的影响,用尺寸因数匸或■:
.表示。
它代表光滑大尺寸试样的疲劳极
限与光滑小尺寸试样疲劳极限之比值。
图10.14给出了圆截面钢轴对称循环弯曲与扭转时的
尺寸因数。
可以看出:
试样的直径d愈大,疲劳极限降低愈多;
材料的静强度愈高,截面尺寸的大小对构件疲劳极限的影响愈显著。
弯曲和扭转疲劳极限随截面尺寸增大而降低的原因,可利用图10.15加以说明。
图中所
示为承受弯曲作用的两根直径不同的试样,在最大弯曲正应力相同的条件下,大试样的高应力区比小试样的高应力区厚,因而处于高应力状态的晶粒多。
所以,在大试样中,疲劳裂纹更易于形成并扩展,疲劳极限因而降低。
另一方面,高强度钢的晶粒较小,在尺寸相同的情况下,晶粒愈小,则高应力区所包含的晶粒愈多,愈易产生疲劳裂纹。
轴向加载时,光滑试样横截面上的应力均匀分布,截面尺寸的影响不大,可取尺寸因数
。
三、表面加工质量的影响
最大应力一般发生在构件表层,同时,构件表层又常常存在各种缺陷(刀痕与擦伤等),
因此,构件表面的加工质量和表面状况,对构件的疲劳强度也有显著影响。
表面加工质量对构件疲劳极限的影响,可用表面质量因数一:
表示。
它代表用某种方法加
工的构件的疲劳极限与光滑试样(经磨削加工)的疲劳极限之比值,表面质量因数1与加工方
法的关系如图10.16所示。
图10.16
表面加工质量愈低,疲劳极限降低愈多;
材料的静强度愈高,加工质量对构件疲劳极限的影响愈显著。
所以,对于在交变应力下工作的重要构件,特别是在存在应力集中的部位,应当力求采用高质量的表面加工,而且,愈是采用高强度材料,愈应讲究加工方法。
还应指出,由于疲劳裂纹大多起源于构件表面,因此,提高构件表层材料的强度、改善表层的应力状况,例如渗碳、渗氮、高频淬火、表层滚压和喷丸等,都是提高构件疲劳强度
的重要措施。
四、环境和温度的影响
海水、水蒸气、酸、碱溶液等腐蚀介质环境对构件的疲劳强度也有显著的影响,这种疲劳称为腐蚀疲劳,其过程是力学作用与化学作用的耦合,破坏机理十分复杂。
因此,加强构件的表面(如电镀)、使用耐腐蚀材料(如高鉻钢)等,都是提高构件疲劳强度的措施。
温度的降低,金属材料会表现出低温脆性,一旦出现裂纹,更易发生断裂;
高温将降低材料的强度,可能引起蠕变,对疲劳强度也是不利的。
另外,温度的升高还会使为改善材料的疲劳性能而引入的残余压应力而消失。
10.4构件的疲劳强度计算
一、对称交变应力下构件的强度条件
由以上分析可知,当考虑应力集中、截面尺寸、表面加工质量等因素的影响以及必要的
安全因数后,拉压杆或梁在对称交变应力下的许用应力为