复习内容Word文档下载推荐.docx
《复习内容Word文档下载推荐.docx》由会员分享,可在线阅读,更多相关《复习内容Word文档下载推荐.docx(8页珍藏版)》请在冰豆网上搜索。
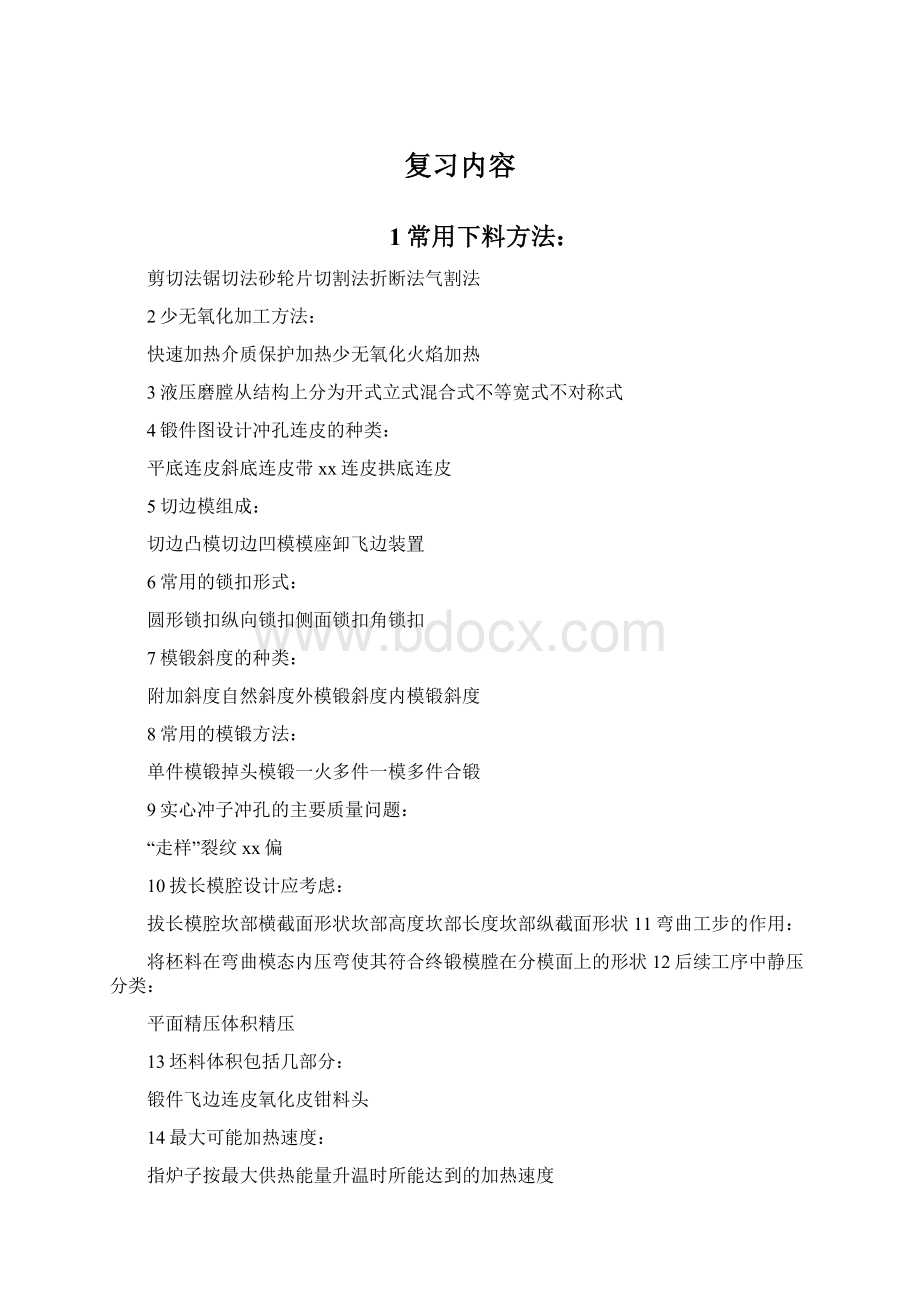
9实心冲子冲孔的主要质量问题:
“走样”裂纹xx偏
10拔长模腔设计应考虑:
拔长模腔坎部横截面形状坎部高度坎部长度坎部纵截面形状11弯曲工步的作用:
将柸料在弯曲模态内压弯使其符合终锻模膛在分模面上的形状12后续工序中静压分类:
平面精压体积精压
13坯料体积包括几部分:
锻件飞边连皮氧化皮钳料头
14最大可能加热速度:
指炉子按最大供热能量升温时所能达到的加热速度
15允许加热速度:
指加热过程中,在不破坏金属完成性的条件下所允许的加热速度16热锭:
由炼钢车间脱模后直接送到锻压车间,表面温度不低于600℃钢锭
1心轴拔长:
是一种减小空心坯料外径而增加其长度的锻造工序,用于锻制长筒类锻件2钢的锻造温度范围:
开始锻造温度和结束锻造温度之间的一段温度区间
3盐浴炉加热:
电流通过炉内电极产生的热量把导电介质熔融,通过高温介质的对流与传导将埋入介质中的金属坯料进行加热。
4一火多件:
用一根加热好的棒料连续锻几个锻件,每锻完一个锻件从棒料上分离下来再锻另一个
5局部镦粗第三规则:
在凸模镦粗,当D≤
1.5d
0,a≤2d
0时,当D≤
1.25d
0,a≤3d
0时,可正常镦粗不产生折迭
6体积精压:
将锻件放入尺寸精度高表面粗糙度小的模膛内进行锻压使其整个表面都受到压挤产生少量变形。
7自由锻锻件图,编制锻造工艺设计,工具指导,生产和验收锻件的主要依据:
也是联系其他后续加工工艺的重要技术资料,它是根据零件图考虑了加工余量,锻件公差,锻造余块检验试样及工艺卡头等绘制而成的
8大型锻件:
在大型锻压设备上锻造的体积尺寸与单件重量较大的重型锻件
9局部镦粗第二规则:
在凹模镦粗,当D≤
0,a≤d
0,a≤
1.5d
0时,可正常镦粗不产生折迭。
10模锻锻件图:
确定模锻生产过程,制定工艺规范,设计锻模,检验锻件及制造锻模的依据,是模锻最重要的基本技术条件之一。
11模锻斜度:
为是锻件成形后顺利地由模膛中取出,锻件侧表面上必须带有斜度
,12调头模锻:
毛坯下料长度可供锻两个锻件,坯料整体加热,在第一锻件锻完后调转1800,用钳子夹住锻件,余下的坯料锻另一个锻件。
13模锻工步:
模锻时坯料在锻模的一系列模膛中变形,坯料在每一模膛中的变形过程14锻模:
再热态或冷态下进行体积成型时所用模具总称
15钳口:
只在锻模的模锻模膛前面所做的空腔,它是由类钳口与钳口颈两部分组成16精密模锻:
是在一般模锻基础上逐步发展起来的一种少无切削加工新工艺
17平面精压:
在两精压平板之间,对锻件上一对或数对平行平面加压使变形部分尺寸精度提高,表面粗糙度降低的工序
18接触电加热:
是以低压大电流直接通入金属坯料,由金属坯料自身的电阻,在通过电流时产生的热量,使金属坯料加热。
19终锻模膛中钳口的通途检验角的用途
钳口用途①夹钳口在模锻时用来放置棒料及钳夹头②钳口颈用于加强夹钳材料为锻件之间的链接强度③齿轮类锻件在模锻时无夹钳料头,钳口是作为主件起模之用④在锻模制造时,钳口作为浇铸模膛检验件的浇口。
检验角用途①方便锻模安装调整时检验上、下模膛对准的情况②使锻模机械加工时有相互垂直的划线基准面
20作用:
合理分配坯料各部分的金属体积,以避免折迭的产生和有利于金属充满模膛,同时可以减少终锻模膛的磨损。
缺点:
增大模块尺寸,并列起偏心打击等。
应用:
对终锻时容易产生折迭和不易充满的锻件,常采用预锻工步。
21目的:
①去除氧化皮,提高锻件表面质量,改善锻件的后续切削加工条件②检查锻件表面质量③冷精和精密锻模也需要表面质量良好的坯料。
方法:
滚筒清理、喷砂清理、抛丸清理、酸洗清理。
22原则:
要求在锻造温度范围内金属具有良好的塑性和较低的变形抗力;
能锻出优质的锻件;
锻造温度范围应尽可能宽广些,以便减少加热火次,提高生产率。
以合金平衡相图为基础,再参考塑性图,抗力图和再结晶图,由塑性、质量和变形抗力三方面加以综合分析,从而定出始锻温度和终锻温度。
24应设计成斜底连皮
原因:
对于较大的孔,若仍用平底连皮,则锻件内孔处的多余金属不易向四周排除,而且由于金属的流动激烈容易在连皮四周处产生折迭,模膛内的冲头也会过早地磨损或压塌。
破坏形式有:
①在燕尾根部转角处产生裂纹②沿高度方向开始于模膛深处的纵向裂纹③模膛壁被打断④承击面被打塌
形成原因①主要是由于应力集中造成的,若设计不合理或制造不良,造成模块两侧于锤头或下砧接触面使燕尾悬空时。
更容易发生这种损坏。
从模具本身来看,若锻模材料不好成纤维安排不合适时也容易产生这种损坏②由于模膛侧壁受很大压力,相对于一定的模膛深度,当模锻高度较小时,应力值可能超过材料强度极限引起断裂。
当模膛内圆角半径较少和模膛有深而窄的凹槽或残留有加工刀刃时,有应力集中产生破坏③由模壁太薄引起。
模膛愈深,模壁亵渎和模膛底部圆角半径愈小和留有加工刀痕时愈易产生破坏④由承击面太小,多余能量较大或猛烈空打造成
25金属流动过程:
Ⅰ阶段由开始模压到金属与模具侧壁接触为止;
Ⅱ阶段金属充满模膛;
Ⅲ阶段金属充满模膛后,多余金属由桥口流出
影响因素①模膛(模锻件)的具体尺寸和形状②飞边槽桥口部分的尺寸和飞边槽的位置③终锻前坯料的具体形状和尺寸④坯料本身性质的不均与情况⑤设备工作速度
26作用①增加金属流出模膛的阻力,迫使金属充满模膛②容纳多余金属③缓冲,减弱上下模的打击,防止迷局的压塌和开裂(图)
27变形特点及缺陷:
内侧金属受压,可能产生折迭,外侧金属受拉,易引起裂纹,断面积减少,长度略有增加。
注意问题:
确定坯料尺寸时应考虑到变形区断面减少,一般坯料断面应比锻件断面稍大,10%~15%
28锻模中心:
锻模xx中心与键槽中心线交点。
模膛中心:
承受锻件反作用力的合力作用点。
模块中心:
模块对角线的交点。
影响:
当锻模中心与模膛中心不重合时,锻造会产生偏心矩,使上下模产生错形,造成锻件分模面上的错差,增加废品率,同时还会增加设备磨损,降低锻模寿命。
29方法:
①使用润滑剂和预热工具②采用凹形毛坯③采用软金属垫④采用铆镦,叠镦和套环内镦粗⑤采用反复镦粗拔长
30内容:
①根据零件图绘制锻件图②确定坯料重量和尺寸③确定变形工艺和锻比④选择锻压设备⑤确定锻造温度范围。
加热和冷却规范⑥确定热处理规范⑦填写工艺卡片等31考虑问题:
①模膛的布排②错移力的平衡以及导向问题③锻模的强度④模块尺寸和标准32模锻工艺过程即由坯料经过一系列加工工序制成模锻件的整个生产过程。
组成工序:
①备料工序②加热工序③锻造工序④锻后工序⑤检验工序
33P151-156
34包括内容:
①选择分模面的位置和形状②确定机械加工余量、余块和锻件公差③确定锻模斜度④确定圆角半径⑤确定冲孔连皮形状和尺寸⑥制定锻件技术条件⑦绘制锻件图35注意问题:
①弯曲模膛的形状是根据模锻模膛在分模面上的外形来设计的②弯曲模膛的急突弯曲处,应做成润徐的最大圆角③下模应有两个支点,以支承压弯前坯料。
此两点的高度应使坯料水平④当用原坯料在模膛压弯时,在模膛末端应做出挡料太,以供定位;
如坯料先经过滚压制坯,可利用钳口颈定位⑤分模面应做成上、下模突出分模面部分高度大致相等⑥为更好定位和防止压弯时坯料走偏,模膛突出部分在宽度方向应做成弧形凹坑⑦为防碰撞,模膛下模空间应留有间隙。
36锤上模锻锻件图上圆角半径的种类,各自的作用,圆角半径设计过大或过小对锻件质量和锻模寿命有那些影响
种类:
外圆角半径;
内圆角半径
作用:
避免锻模在热处理时和模锻过程中因应力集中导致模具开裂,并保证充满成形;
使金属易于流动充填模膛,防止产生折迭和模膛过早被压塌。
过小,金属充满模膛的相应处则相分困难,易引起锻模崩裂。
过大,机加工余量受到影响;
过小,模锻时金属流动形成的纤维会被割断,力学性能下降;
过大,金属过早流失,易充不满。
37试分析锤上模锻与热模锻压力机上模锻的工艺特点有哪些?
(工艺特点意义对应!
)锤:
多次成形、加工余量,公差100%、斜度正常、上模充填效果好、氧化皮清除容易、制坯拔长,滚压都适合、整体式、高度方向尺寸不精确、一台设备加工成形、开式,闭式都可以,无超载、
热模锻压力机:
一次成型、50~70%、斜度可减1-2级、上下模充填效果一般,多模膛、清除困难、制坯、馕块式、锻件精度高、一台设备制坯,终锻压力机成形、超载易闷车压力机便于实现生产的连续化,机械化、
38锤上模锻时制坯模膛的布排应考虑哪些问题
①制坯模膛尽可能按工艺顺序排列,操作时一般只允许改变一次方向,以缩短操作时间②模膛的排列应多加热炉,切边压力机的位置相适应③氧化皮最多模膛是锻模中头道制坯模膛④弯曲模膛的位置应使锻件能以最简便的方式移动或翻转送入终锻模膛内。
⑤拔长模膛位置如在锻模右边,应采用直式;
如在左边,应采用斜式⑥切刀位置,前切刀一般位于锻模的右前角,后切刀一般在左后角。
39为什么对大型锻件切边凹模通常采用分块式
因为分块式由两块以上的模块组成,制造比较容易,热处理时不易淬裂,变形小,便于修磨,调整和更换。
40模锻时模具的形状对金属变形和流动有哪些影响。
①控制锻件的最终形状和尺寸②控制金属的流动方向③控制塑性变形区④提高金属的塑性⑤控制坯料失稳提高成形极限
41试分析模锻时叉形锻件内端角产生充不满的原因
因为沿横向流动的金属先水平外流,与模膛接触后部分金属转向内角处流动。
由变形流动决定内端角处不易充满,还由于此处被排出的金属除沿横向流入模膛外,有很大一部分沿轴向流入飞边槽,造成内端角处金属充不满。
42锤上模锻,对于工字型断面锻件折迭产生的原因,防止折迭产生的措施
①靠近接触面附近的金属要有流动②该部分金属必须沿水平方向外流③由中间部分排出的金属量较大
措施:
①使中间部分金属在终锻时的变形小一些,即由中间部分排出的金属少一些②创造条件使终锻时由中间部分排出的金属量尽可能向上和向下流动,继续填充模膛43热模锻压力机上模锻时,在设计预锻模膛时,除应考虑锤上预锻模膛设计原则外,还应具体考虑哪些问题?
①预锻模膛的高度尺寸比终锻工步图相应大2~5mm,而宽度尺寸适当减少,并使预锻件横截面积大于终锻件②若终锻面的横截面呈圆形,则相应的预锻件横截面应为椭圆形③应严格控制预锻件各部分的体积,使终锻时多余的金属能合理地流动,避免由于金属回流而形成折迭等缺陷④当终锻金属不能以镦粗而重要以压入方式充填模膛时,预锻与终锻应有显著差别,以限制金属径向流动
44编制自由锻工艺过程中,确定变形工艺时,确定工序尺寸时应注意哪些问题
①工序尺寸必须符合工艺特点②必须保持各部分有足够的体积③多火次锻件时必须注意中间各火次加热的可能性④有些长轴类锻件轴向尺寸要求精确,且沿轴向又不能镦粗,必须预计到轴向在修整时会略有伸长
45拔长高合金工具钢时,当送进量较大并且在坯料同一部位反复锤击时,为什么常易在对角线方向上产生裂纹
坯料被压缩时,沿横截面上金属流动的情况如图,A区的金属带着靠它的a区金属向轴心方向移动,B区的金属带着靠近它的b区金属向增宽方向流动,因此,a、b两区的金属向着两个相反的方向流动,当坯料翻转900再