压铸缺陷及解决的办法Word格式.docx
《压铸缺陷及解决的办法Word格式.docx》由会员分享,可在线阅读,更多相关《压铸缺陷及解决的办法Word格式.docx(13页珍藏版)》请在冰豆网上搜索。
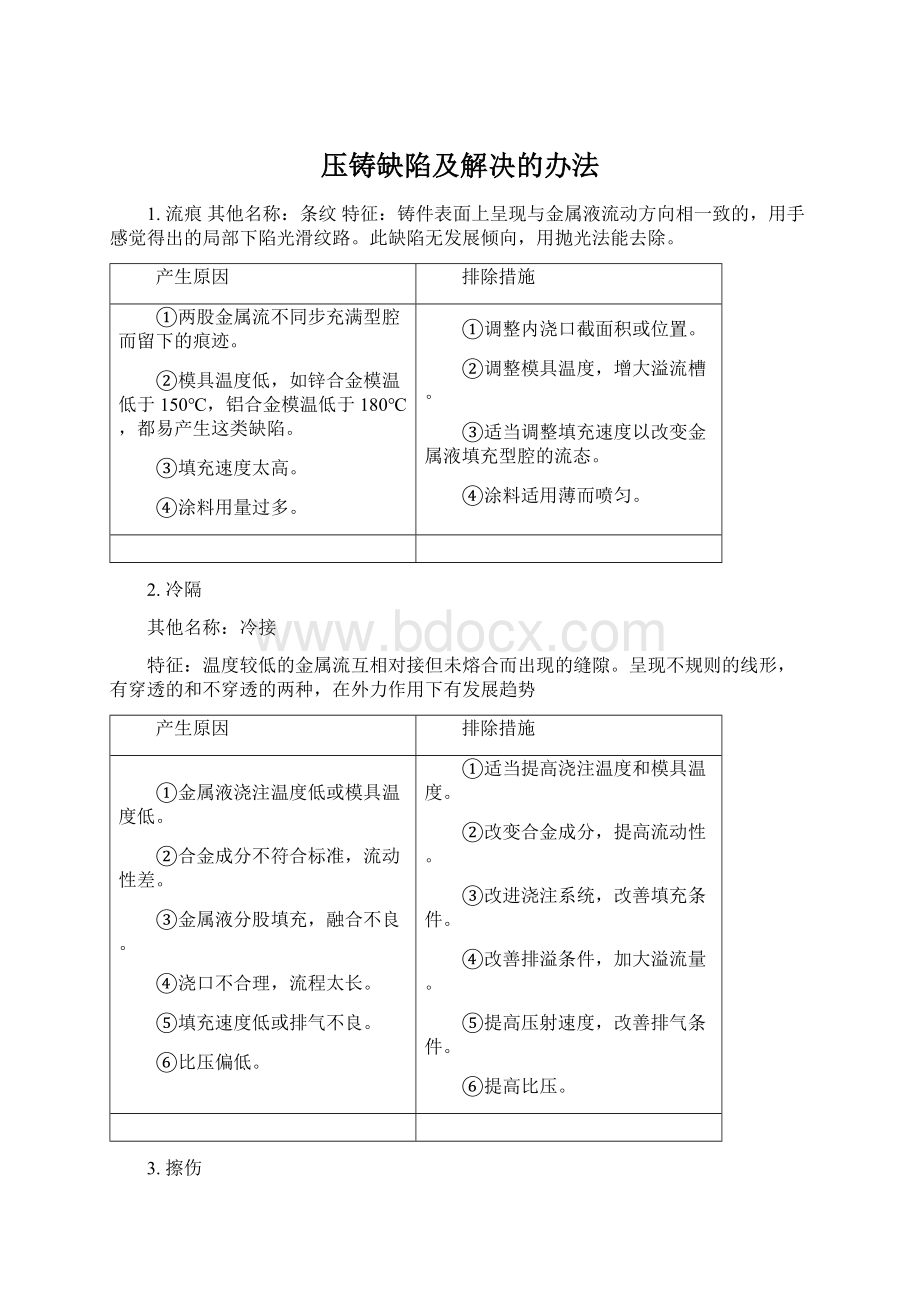
③金属液分股填充,融合不良。
④浇口不合理,流程太长。
⑤填充速度低或排气不良。
⑥比压偏低。
①适当提高浇注温度和模具温度。
②改变合金成分,提高流动性。
③改进浇注系统,改善填充条件。
④改善排溢条件,加大溢流量。
⑤提高压射速度,改善排气条件。
⑥提高比压。
3.擦伤
拉伤、拉痕、粘模伤痕
顺着脱模方向,由于金属粘附,模具制造斜度太小而造成铸件表面的拉伤痕迹,严重时称为拉伤面。
①型芯、型壁的铸造斜度大小或出现倒斜度。
②型芯、型壁有压伤痕。
③合金粘附模具。
④铸件顶出偏斜或型芯轴线偏斜。
⑤型壁表面粗糙。
①修正模具,保证制造斜度。
②打光压痕。
③合理设计浇注系统避免金属流对冲型芯型壁,适当降低填充速度。
④修正模具结构。
⑤打光表面。
⑥涂料常喷涂不到。
⑦铝合金中含铁量低于0.6%。
⑥涂料用量薄而均匀,不能漏喷涂料。
⑦适当增加含铁量至适当增加含铁量至0.6~0.8%。
4.凹陷
缩凹、缩陷、憋气、塌边
铸件平滑表面上出现凹瘪的部分,其表面呈自然冷却状态。
①铸件结构设计不合理,有局部厚实部位,产生热节。
②合金收缩率大。
③内浇口截面积太小。
④比压低。
⑤模具温度太高
①改善铸件结构,使壁厚稍为均匀,厚薄相差较大的连接处应逐步缓和过渡,消除热节。
②选择收缩率小的合金。
③正确设置浇注系统,适当加大内浇口的截面积。
④增大压射力。
⑤适当调整模具热平衡条件,采用温控装置以及冷却等。
5.气泡
鼓泡
铸件表皮下,聚集气体鼓胀所形成的泡。
①模具温度太高。
②填充速度太高,金属液流卷入气体过多。
③涂料发气量大,用量过多,浇注前未燃尽,使挥发气体被包在铸件表层。
④排气不畅。
⑤开模过早。
⑥合金熔炼温度过高。
①冷却模具至工作温度。
②降低压射速度,避免涡流包气。
③选用发气量小的涂料,用量薄而均匀,燃尽后合模。
④清理和增设溢流槽和排气道。
⑤调整留模时间。
⑥修整熔炼工艺。
6.气孔
空气孔
卷入压铸件内部的气体所形成的形状较为规则,表面较为光滑的空洞。
主要是包卷气体引起:
①浇口位置选择和导流形状不当,导致金属液进入型腔产生正面撞击和产生旋涡。
②浇道形状设计不良。
③压室充满度不够。
④内浇口速度太高,产生湍流。
⑤排气不畅。
⑥模具型腔位置太深。
⑦涂料过多,填充前未燃尽。
⑧炉料不干净,精炼不良。
⑨机械加工余量太大。
①选择有利型腔内气体排除的浇口位置和导流形状,避免金属液先封闭分型面上的排溢系统。
②直浇道的喷嘴截面积应尽可能比内浇口截面积大。
③提高压室充满度,尽可能选用较小的压室并采用定量浇注。
④在满足成型良好条件下,增大内浇口厚度以降低填充速度。
⑤在型腔最后填充部位处开设溢流槽和排气道,并应避免溢流槽和排气道被金属液封闭。
⑥深腔处开设排气塞,采用镶拼形式增加排气。
⑦涂料用量薄而均匀,燃尽后填充,采用发气量小的涂料。
⑧炉料必须处理干净、干燥,严格遵守熔炼工艺。
⑨减少机械加工余量。
⑩调整压射速度和快压射速度的转换点。
降低浇注温度,增加比压。
7.缩孔
缩空、缩眼
压铸件在冷凝过程中,由于内部补偿不足所造成的形状不规则,表面较粗糙的孔洞。
①合金浇注温度过高。
②铸件结构壁厚不均匀,产生热节。
③比压太低。
①遵守合金熔炼规范,避免合金液过热太长,降低浇注温度。
②改进铸件结构,消除金属积聚部位,壁厚均匀,缓慢过渡。
③适当提高比压。
④溢流槽容量不够,溢口太薄。
⑤压室充满度太小,余料太薄,最终补缩起不到作用。
⑥内浇口较小。
⑦模具的局部温度偏高。
④加大溢流槽容量,增厚溢流口。
⑤提高压室充满度,采用定量浇注。
⑥适当改善浇注系统,以利压力很好地传递。
⑦冷却模具局部温度偏高处。
8.花纹
铸件表面上呈现的光滑条纹,肉眼可见,但用手感觉不出,颜色不同于基体金属的纹路,用0#砂布稍擦几下即可去除。
①填充速度太快。
②涂料用量太多。
③模具温度偏低。
①尽可能降低压射速度。
②涂料用量薄而均匀。
③提高模具温度。
9.裂纹
铸件上合金基体被破坏或断开形成细丝状的缝隙,有穿透的和不穿透的两种,有发展趋势。
裂纹可以分为冷裂纹和热裂纹两种,他们的主要区别是冷裂纹铸件开裂处金属未被氧化,热裂纹铸件开裂处金属被氧化。
①铸件结构不合理,收缩收到阻碍,铸造圆角太小。
②抽芯及顶出装置在工作中发生偏斜,受力不均匀。
③模具温度低。
④开模及抽芯时间太迟。
⑤选用合金不当或有害杂质过高,使合金塑性下降。
①改进铸件结构,减少壁厚差,增大铸造圆角。
②修正模具结构。
③提高模具工作温度。
④缩短开模及抽芯时间。
⑤严格控制有害杂质,调整合金成分。
10.欠铸
浇不足、轮廓不清、边角残缺
金属液未充满型腔,铸件上出现填充不完整的部位。
(1)合金液流动不良引起:
①合金液含气量高,氧化严重,以致流动性下降。
②合金浇注温度及模具温度过低。
③内浇口速度过低。
④蓄能器内氮气压力不足。
⑤压室充满度小。
⑥铸件壁太薄或厚薄悬殊等设计不当。
(2)浇注系统不良引起:
①浇口位置,导流方式,内浇口股数选择不当。
②内浇口截面积太小。
(3)排气条件不良引起:
①排气不畅。
②涂料过多,未被烘干燃尽。
③模具温度过高,型腔内气体压力较高,不易排出。
(1)改善合金的流动性:
①采用正确的熔炼工艺,排除气体及非金属夹杂物。
②适当提高合金浇注温度和模具温度。
③提高压射速度。
④补充氮气,提高有效压力。
⑤采用定量浇注。
⑥改进铸件结构,适当调整壁厚。
(2)改进浇注系统:
①正确选择浇口位置和导流方式,对不良形状铸件及大铸件采用多股内浇口为有利。
②增大内浇口截面积或提高压射速度。
(3)改善排气条件:
①增设溢流槽和排气道,深凹型腔处可开设通气塞。
②涂料使用薄而均匀,吹干燃尽后合模。
③降低模具温度至工作温度。
11.印痕
推杆印痕、镶块或活动块拼接印痕。
铸件表面由于模具型腔磕碰及推杆、镶块、活动块等零件拼接所留下的凸出和凹下的痕迹。
①推杆调整不齐或端部磨损。
②模具型腔、滑块拼接部分和其活动部分配合欠佳。
③推杆面积太小。
①调整推杆至正确位置。
②紧固镶块或其他活动部分,消除不应有的凹凸部分。
③加大推杆面积或增加个数。
12.网状毛刺
网状痕迹、网状花纹、龟裂毛刺
由于模具型腔表面产生热疲劳而形成的铸件表面上的网状凸起痕迹和金属刺。
①模具型腔表面龟裂造成的痕迹,内浇口区域附件的热传导最集中,摩擦阻力最大,经受熔融金属的冲蚀最强,冷热交变最剧,最易产生热裂,形成龟裂。
②模具材料不当,或热处理工艺不正确。
③模具冷热温度变化大。
④合金液浇注温度过高,模具预热不够。
⑤模具型腔表面粗糙度Ra太大。
⑥金属流速高及正面冲刷型壁。
①正确选用模具材料及合理的热处理工艺。
②模具在压铸前必须预热到工作温度范围。
③尽可能降低合金浇注温度。
④降低合金液浇注温度,模具预热到合适温度。
⑤提高模具型腔表面质量,降低Ra数值,镶块定期退火,消除应力。
⑥正确设计浇注系统,在满足成型良好的条件下,尽可能用较小的压射速度。
13.有色斑点
油斑、黑色斑点
铸件表面上呈现的不同于基体金属的斑点,一般由涂料碳化物形成。
①涂料不纯或用量过多。
②涂料中含石墨过多。
①涂料使用应薄而均匀,不能堆积,要用压缩空气吹散。
②减少涂料中的石墨含量或选用无石墨水基涂料。
14.麻面
充型过程中由于模具温度或合金温度太低,在近似于欠压条件下铸件表面形成的细小麻点状分布区域。
①填充时,金属分散成密集液滴,高速撞击型壁。
②内浇口厚度偏小。
①正确设计浇注系统,避免金属液产生喷溅,改善排气条件,避免液流卷入过多气体,降低内浇口速度并提高模具温度。
②适当调整内浇口厚度。
15.飞边
披缝
铸件边缘上出现的金属薄片。
①压射前机器的锁模力调整不佳。
②模具及滑块损坏,闭锁元件失效。
③模具镶块及滑块磨损。
④模具强度不够造成变形。
⑤分型面上杂物未清理干净。
⑥投影面积计算不正确,超过锁模力。
⑦压射速度过高,形成压力冲击峰过高。
①检查合模力或增压情况,调整压射增压机构,使压射增压峰值降低。
②检查模具滑块损坏程度并修整之,确保封锁元件起到作用。
③检查磨损情况并修复。
④正确计算模具强度。
⑤清除分型面上杂物。
⑥正确计算,调整好合模力。
⑦适当调整压射速度。
16.分层
隔皮
铸件上局部存在有明显的金属层次。
①模具刚性不够,在金属液填充过程中,模板产生抖动。
②压射冲头与压室配合不好,在压射中前进速度不平稳。
③浇注系统设计不当。
①加强模具刚度,紧固模具部件。
②调整压射冲头与压射,保证配合良好。
③合理设计内浇口。
17.疏松
铸件表面上呈现松散不紧实的宏观组织。
①模具温度过低。
②合金浇注温度过低。
③比压低。
④涂料过多。
①提高模具的温度之工作温度。
②适当提高合金浇注温度。
③提高比压。
④涂料薄而均匀。
18.错边(错扣)
错缝
铸件的一部分与另一部分在分型面上错开,发生相对位移(对螺纹称错扣)。
①