压铸异常分析培训PPT格式课件下载.ppt
《压铸异常分析培训PPT格式课件下载.ppt》由会员分享,可在线阅读,更多相关《压铸异常分析培训PPT格式课件下载.ppt(27页珍藏版)》请在冰豆网上搜索。
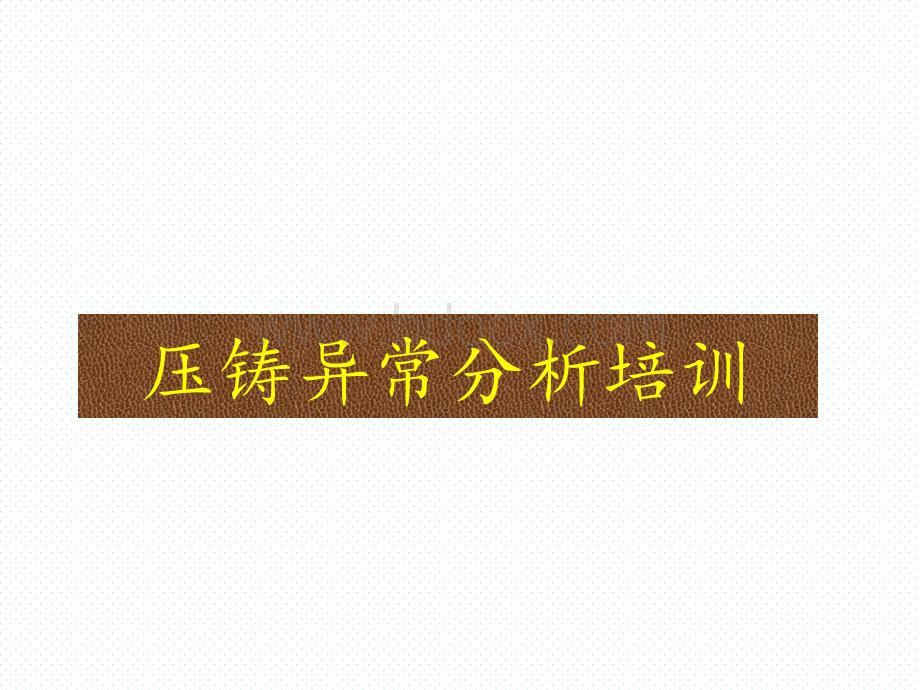
冷接(对接)B特征:
温度较低的金属流互相对接但未熔合而出现的缝隙,呈不规则的线形,有穿透的和不穿透的两种在外力的作用下有发展的趋势。
1、金属液浇注温度低或模具温度低。
2、合金成分不符合标准,流动性差。
3、金属液分股填充,溶合不良。
4、浇口不合理,流程太长。
5、填充速度低或排气不良。
6、比压偏低。
1、适当提高浇注温度和模具温度。
2、改变合金成分,提高流动性。
3、改进浇注系统,改善填充条件。
4、改善排溢条件,增大溢流量。
5、提高压射速度,改善中排气条件。
6、提高比压异常原因分析及改善方案异常原因分析及改善方案三、粘膜A其他名称:
拉力、拉痕、擦伤。
B特征:
顺着脱模方向,由于金属粘附,模具制造斜度太小而造成铸件表面的拉伤痕迹,严重时成为拉伤面。
1、型芯、型壁的铸造斜度太小或出现倒斜度。
型芯、型壁有压伤痕。
2、合金粘附模具。
3、铸件顶也偏斜,或型芯轴线偏斜。
4、型壁表面粗糙。
5、涂料常喷涂不到。
6、铝合金中含铁量低于0.6%。
1、修正模具,保证制造斜度。
2、打光压痕。
3、合理设计浇注系统,避免金属流对冲型芯、型壁,适当降低填充速度。
4、修正模具结构。
5、打光表面。
6、涂料用量薄而均匀,不能漏喷涂料。
7、适当增加含铁量至0.6-0.8%。
四、凹陷A其他名称:
缩凹、缩陷、憋气、缩影。
铸件平滑表面上出现的凹瘪的部分,其表面呈自然冷却状态。
1、铸件结构设计不合理,有局部厚实部们,产生热节。
2、合金收缩率大。
3、内浇口截面积太小。
4、比压低。
5、模具温度太高。
1、改善铸件结构,使壁厚稍为均匀,厚薄相差较大的连接处应逐步缓和过渡,消除热节。
2、选择收缩率小的合金。
3、正确设置浇注系统,适当加在内浇口的截面积。
4、增大压射力。
5、适当调整模具热平衡条件,采用温控装置以及冷却等。
异常原因分析及改善方案异常原因分析及改善方案五、气泡A其他名称:
鼓泡。
铸件表皮下,聚集气体鼓胀所形成的泡。
1、模具温度太高。
2、填充速度太高,金属流卷入气体过多。
3、涂料发气量大,用量过多,浇注前未燃尽,使挥发气体被包在铸件表层。
4、排气不顺。
5、开模过早。
6、合金熔炼温度过高。
1、冷却模具至工作温度。
2、降低压射速度,避免涡流包气。
3、选用发气量小的涂料,用量薄面均匀,燃尽后合模。
4、清理和增设溢流槽和排气道。
5、调整留模时间。
6、修整熔炼工艺。
异常原因分析及改善方案六、气孔A其他名称:
空气孔、气眼。
卷入压铸件内部内部的气体所形成的形状较为规则,表面较为光滑的孔洞。
C产生原因主要是包卷气体引起1、浇口位置先择各导流形状不当,导致金属液进入型腔产生正面撞击和产生旋涡。
2、浇道形状设计不良。
3、压室充满度不够。
4、内浇口速度太高,产生湍流。
5、排气不畅。
6、模具型腔位置太深。
7、涂料过多,填充前未燃尽。
8、炉料不干净,精炼不良。
9、机械加工余量太大。
1、选择有利于型腔内气体排除的浇口位置和导流形状,避免金属先封闭分型面上的排溢系统。
2、直浇道的喷嘴截面积应尽可能比内浇口截面积大。
3、提高压室充满度,尽可能选用较小的压室并采用定量浇注。
4、在满足成型良好的条件下,增大内浇口厚度以降低填充速度。
5、在型腔最后填充部位处开设溢流槽和排气道,并应避免溢流槽和排气道被金属液封闭。
6、深腔处开设排气塞,采用镶拼形式增加排气。
7、涂料用量薄而均匀,燃尽后填充,采用发气量小的涂料。
8、炉料必须处理干净、干燥,严格遵守熔炼工艺。
9、调整压射速度,慢压射速度和快压射速度的转换点。
10、降低浇注温度,增加比压。
内部内部缺陷缺陷异常原因分析及改善方案七、缩孔A其他名称:
缩眼、缩空。
压铸件在冷凝过程中,由于内部补偿不足所造成的形状不规则,表面表面较粗糙的孔洞。
C产生原因1、合金浇注温度过高。
2、铸件结构壁厚不均匀,产生热节。
3、比压太低。
4、溢流槽容量不够,溢口太薄。
5、压室充满度太小,余料(料饼)太薄,最终补缩起不到作用。
6、内浇口较小。
7、模具的局部温度偏高。
D排除措施1、遵守合金熔炼规范,合金液过热时间太长,降低浇注温度。
2、改进铸件结构,消除金属积聚部位,均匀壁厚,缓慢过渡。
3、适当提高比压。
4、加大溢流槽容量,增厚溢流口。
5、提高压室充满度,采用定量浇注。
6、适当改善浇注系统,以利压力很好传递。
异常原因分析及改善方案八、花纹A特征:
铸件表面上呈现的光滑条纹,肉眼可见,但用手感觉不出的,颜色不同于基体金属的纹络,有0#砂布、百洁布等稍擦几下即可去除。
B产生原因1、填充速度太快。
2、涂料用量太多。
3、模具温度偏低。
C排除措施1、尽可能降低压射速度。
2、涂料用量薄而均匀。
3、提高模具温度。
异常原因分析及改善方案九、裂纹A特征:
铸件上合金基体被破坏或断开形成细丝状的缝隙,有穿透的和不穿透的两种,有发展的趋势。
B裂纹可分为冷裂纹和热裂纹两种,它们的主要区别是:
冷裂纹铸件开裂处金属未被氧化,热裂纹铸件开裂处金属被氧化。
C产生原因1、铸件结构不合理,收缩受到阻碍,铸件圆角太小。
2、抽芯及顶出装置在工作中发生偏斜,受力不均匀。
3、模具温度低。
4、开模及抽芯时间太迟。
5、选用合金不当或有害杂质过高,使合金塑性下降。
锌合金:
铅、锡、隔、铁偏高;
铝合金:
锌、铜、铁偏高;
铜合金:
锌、硅偏高;
镁合金:
铝、硅、铁偏高。
D排除措施1、改进铸件结构,减少壁厚差,增大铸造圆角。
2、修正模具结构。
3、提高模具工作温度。
4、缩短开模及抽芯时间。
5、严格控制有害杂质,调整合金成份,遵守合金熔炼规范或重新选择合金牌号。
异常原因分析及改善方案一、欠铸A其他名称:
浇不足、轮廓不清、边角残缺。
金属液未充满型腔,铸件上出现填充不完整的部位。
C产生原因1、合金流动不良引起:
(1)、金属液含气量高,氧化严重,以致流动性下降。
(2)、合金浇注温度用模具温度过低。
(3)、内浇口速度过低。
(4)、蓄能器内氮气压力不足。
(5)、压室充满度低。
(6)、铸件壁太薄或厚薄悬殊等设计不当。
2、浇注系统不良引起:
(1)、浇口位置、导流方式、内浇品股数选择不当。
(2)、内浇口截面积太小。
3、排气条件不良引起:
(1)、排气不畅。
(2)、涂料过多,未被烘干燃尽。
(3)、模具温度过高,型腔内气体压力较高,不易排出。
D排除措施1、改善合金的流动性:
(1)、采用正确的熔炼工艺,排除气体及非金属夹杂物。
(2)、适当提高合金浇注温度和模具温度。
(3)、提高压射速度。
(4)、补充氮气,提高有效压力。
(5)、采用定量浇注。
(6)、秘方进铸件结构,适当调整壁厚。
2、改进浇注系统:
(1)、正确选择浇口位置和导流方式,对非良形状铸件及大铸件采用多股内浇口为有利。
(2)、增大内浇口截面积或提高压射速度。
3、改善排气条件:
(1)、增设溢流槽和排气道,深凹型腔处可开设通气塞。
(2)、涂料使用薄而均匀,欠干燃尽后合模。
(3)、降低模具温度至工作温度。
异常原因分析及改善方案温度温度Si含量含量Al-Si相图拓展拓展异常原因分析及改善方案十一、印痕A其他名称:
推杆印痕、镶块或活动块拼接印痕。
铸件表面由于模具型腔磕碰及推杆、镶件、活动块等零件拼接所留下的凸出和凹下的痕迹。
C产生原因1、推杆调整不齐或端部磨损。
2、模具型腔、滑块拼接部分和其活动部分配合欠佳。
3、推杆面积压小。
D排除措施1、调整推杆至正确位置。
2、紧固镶块或其他活动部分,消除不应有的凹凸部分。
3、加大推杆面积或增加个数。
异常原因分析及改善方案十二、网状毛刺A其他名称:
网状痕迹、网状花纺、龟裂毛刺。
由于模具型腔表面产生热疲劳而形成的铸件表面上的网状凸起痕迹和金属刺。
C产生原因1、模具型腔表面龟裂造成的痕迹,内浇口区域附近的热传导最集中,摩擦阻力最大,经受熔融金属的冲蚀最强,冷热交变最剧,最易产生热裂,形成龟裂。
2、模具材料不当或热处理工艺不正确。
3、模具冷热温差变化大。
4、合金液浇注温度过高,模具预热不够。
5、模具型腔表面粗糙度Ra太大。
6、金属流速过高及正面冲刷型壁。
D排除措施1、正确选用模具材料及合理的热处理工艺。
2、模具在压铸前必须预热到工作温度范围。
3、尽可能降低合金浇注温度。
4、提高模具型腔表面质量,降低Ra数值。
5、镶块定期退火,消除应力。
6、正确设计浇注系统,在满足成型良好的条件下,尽可能用较小的压射速度。
异常原因分析及改善方案十三、有色斑点A其他名称:
油斑、黑色斑点。
铸件表面上呈现的不同于基体金属的斑点,一般由涂料碳化物形成。
C产生原因1、涂料不纯或用是过多。
2、涂料中含石墨过多。
D排除措施1、涂料使用应薄而均匀,不能堆积,要用压缩空气吹散。
2、减少涂料中的石墨含量或选用无石墨水基涂料十四、麻面A特征:
充型过程中由于模具温度或合金液温度太低,在近似于欠压条件下铸件表面形成的细小麻点状分布区域。
B产生原因1、填充时金属分散成密集液滴,高速撞击型壁。
2、内浇口厚度偏小。
C排除措施1、正确设计浇注系统,避免金属液产生喷溅,改善排气条件,避免液流卷入过多气体,降低内浇品速度并提高模温度。
2、适当调整内浇口厚度。
异常原因分析及改善方案十五、飞边A其他名称:
披缝。
铸件边缘上出现的金属薄片。
C产生原因1、压射前机器的锁模力调整不佳。
2、模具及滑块损坏,闭锁元件失效。
3、模具镶块用滑块磨损。
4、模具强度不够造成变形。
5、分型面上杂物未清理干净。
6、投影面积计算不正确,超过锁模力。
7、压射速度过高,形成压力冲击峰过高。
D排除措施1、检查合模力或增压情况,调整压射增压机构,使压射增压峰值降低。
2、检查模具滑块损坏程度并修整,确保闭锁无件起到作用。
3、检查磨损情况并修复。
4、正确计算模具强度。
5、清除分型面上的杂物。
6、正确计算调整锁模力。
7、适当调整压射速度。
异常原因分析及改善方案十六、分层、夹层A其他名称:
隔皮。
B铸件上局部存在明显的金属层次。
C产生原因1、模具刚性不够,在金属液填充过程中,模板产生抖动。
2、压室冲头与压室配合不好,在压射中前进速度不平稳。
3、浇注系统设计不当。
D排除措施1、加强模具刚度,紧固模具部件。
2、调整压射冲头与压室,保证配合良好。
3、合理设计内浇口。
十七、疏松A特征:
铸件表层上呈现松散不紧实的宏观组织。
B产生原因1、模具温度过低。
2、合金浇注温度过低。
3、比压小。
4、涂料过多。
C排除措施1、提高模具温度至工作温度。
2、适当提高合金浇注温度。
3、提高比压。
4、涂料薄而均匀。
异常原因分析及改善方案十八、错边(错扣)A其他名称:
错缝、段差。
铸件的一部分与另一部分在分型面上错开,发生相对位移(对螺纹称错扣)。
C