《精益生产之JIT管理实战》讲义Word格式文档下载.doc
《《精益生产之JIT管理实战》讲义Word格式文档下载.doc》由会员分享,可在线阅读,更多相关《《精益生产之JIT管理实战》讲义Word格式文档下载.doc(29页珍藏版)》请在冰豆网上搜索。
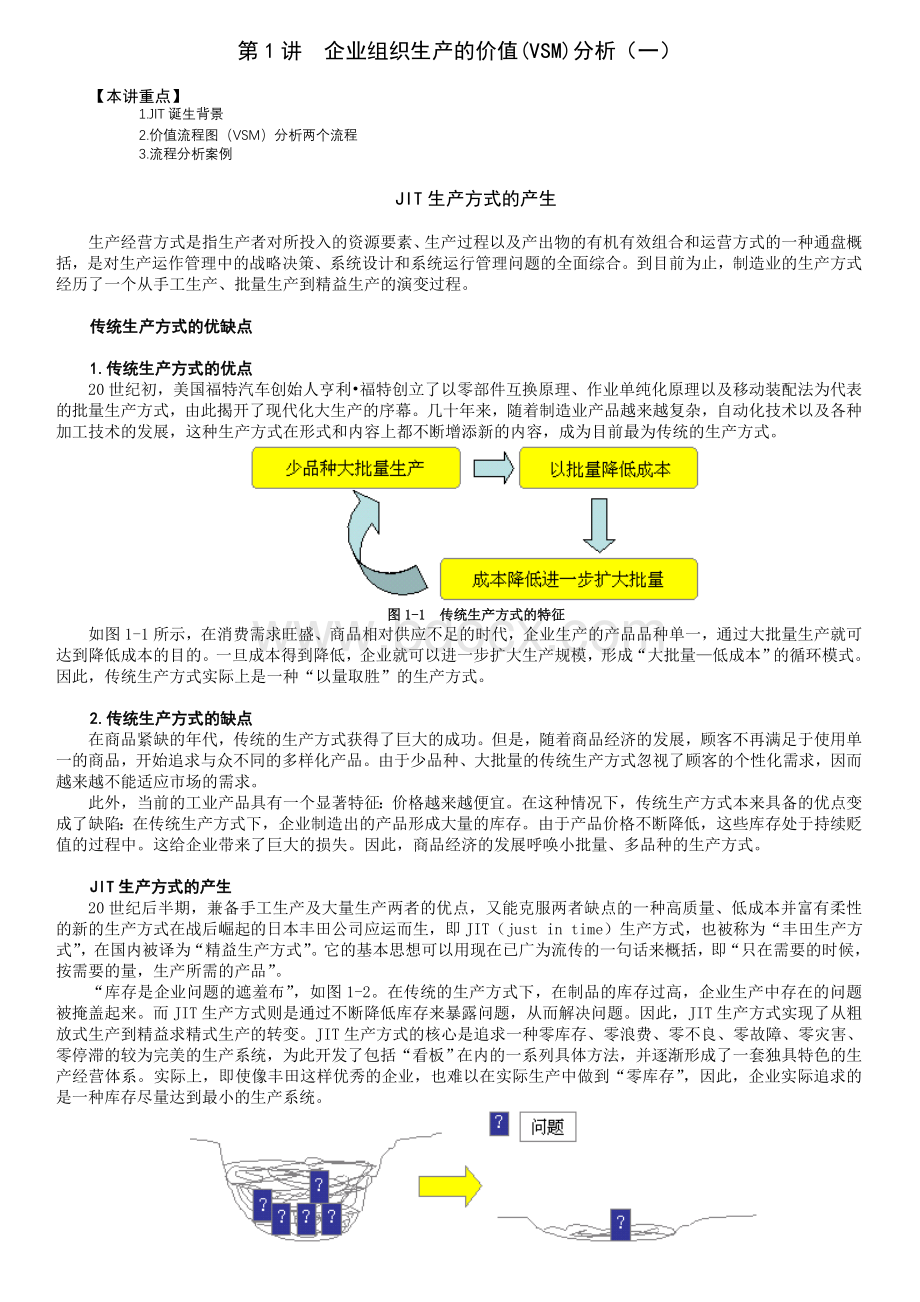
图1-1传统生产方式的特征
如图1-1所示,在消费需求旺盛、商品相对供应不足的时代,企业生产的产品品种单一,通过大批量生产就可达到降低成本的目的。
一旦成本得到降低,企业就可以进一步扩大生产规模,形成“大批量—低成本”的循环模式。
因此,传统生产方式实际上是一种“以量取胜”的生产方式。
2.传统生产方式的缺点
在商品紧缺的年代,传统的生产方式获得了巨大的成功。
但是,随着商品经济的发展,顾客不再满足于使用单一的商品,开始追求与众不同的多样化产品。
由于少品种、大批量的传统生产方式忽视了顾客的个性化需求,因而越来越不能适应市场的需求。
此外,当前的工业产品具有一个显著特征:
价格越来越便宜。
在这种情况下,传统生产方式本来具备的优点变成了缺陷:
在传统生产方式下,企业制造出的产品形成大量的库存。
由于产品价格不断降低,这些库存处于持续贬值的过程中。
这给企业带来了巨大的损失。
因此,商品经济的发展呼唤小批量、多品种的生产方式。
20世纪后半期,兼备手工生产及大量生产两者的优点,又能克服两者缺点的一种高质量、低成本并富有柔性的新的生产方式在战后崛起的日本丰田公司应运而生,即JIT(justintime)生产方式,也被称为“丰田生产方式”,在国内被译为“精益生产方式”。
它的基本思想可以用现在已广为流传的一句话来概括,即“只在需要的时候,按需要的量,生产所需的产品”。
“库存是企业问题的遮羞布”,如图1-2。
在传统的生产方式下,在制品的库存过高,企业生产中存在的问题被掩盖起来。
而JIT生产方式则是通过不断降低库存来暴露问题,从而解决问题。
因此,JIT生产方式实现了从粗放式生产到精益求精式生产的转变。
JIT生产方式的核心是追求一种零库存、零浪费、零不良、零故障、零灾害、零停滞的较为完美的生产系统,为此开发了包括“看板”在内的一系列具体方法,并逐渐形成了一套独具特色的生产经营体系。
实际上,即使像丰田这样优秀的企业,也难以在实际生产中做到“零库存”,因此,企业实际追求的是一种库存尽量达到最小的生产系统。
图1-2降低库存,发现问题
丰田公司在2004年的利润高达102亿美元,相当于通用、福特、克莱斯勒以及大众等四家企业利润总和的两倍。
在原材料的价格和使用量基本相同的情况下,丰田公司通过开展JIT生产,使生产的信息流和实物流的运转时间远远低于竞争对手。
目前,丰田、理光、福特汽车、美国通用汽车等优秀企业利用这种方法来分析自己的生产组织运作过程,从而应对多品种小批量、产品换代快等环境要求。
产品的生产周期
推行JIT生产并不是要彻底否定现状,也不是完全照搬其他企业的经验与方法,而应该首先分析企业自身是如何组织生产的,从而把企业在组织生产过程中存在的问题暴露出来,然后运用JIT的一系列方法进行变革与改善。
要分析企业自身组织生产的特点则必须首先了解产品的生产周期。
在现代生产中,产品的生产周期(LeadTime)是被企业管理者反复强调的一个概念,简称L/T。
如图1-3所示,产品的生产周期是由信息处理周期和实物流动周期组成的。
信息流、实物流和资金流将企业、客户以及供应商这三者有机地连接在了一起。
图1-3产品生产周期的构成
1.信息处理周期
不同的产品具备不同的生产特点。
例如,汽车生产厂家一般按照订单进行生产,而电器生产企业则按照市场预测来组织生产。
无论是按照订单,还是按照市场预测来组织生产,首先要进行的是接受订单、形成销售决议,然后制定出生产计划并下发到各个制造车间,再根据生产计划向供应商发出采购订单。
信息的流转形成了一条从客户到供应商的信息流,完成一次信息流所需的时间构成信息处理周期。
2.物品流动周期
供应商在获得采购订单后,在采购周期内向企业供应原材料;
企业经过加工周期、组装周期和送货周期,将成品送到客户手中。
可见,物品流转的方向是从供应商到客户,与信息流转的方向是相反的。
物品的流转形成实物流,物品完成流转所需的时间构成物品流动周期。
无论是JIT生产管理还是供应链管理,核心问题之一都是如何压缩产品的生产周期,亦即如何压缩信息处理周期和物品流动周期。
信息处理周期和物品流动周期的缩短会促使资金流转的速度加快,资金流转所创造的利润也就会大幅增加。
价值流程图(VSM)分析
缩短产品的生产周期是迅速适应市场需求的关键,而价值流程图(VSM)分析方法正是了解产品生产周期的有效工具。
VSM(ValueStreamMapping,价值流程图)分析方法诞生于20世纪90年代中期的美国,是一种能系统改善信息(情报)流程、实物流程的方法。
VSM分析的两个流程
价值流程图(VSM)分析的是两个流程:
第一个是信息(情报)流程,即从市场部接到客户订单或市场部预测客户的需求开始,到使之变成采购计划和生产计划的过程;
第二个是实物流程,即从供应商供应原材料入库开始,随后出库制造、成品入库、产品出库,直至产品送达客户手中的过程。
此外,实物流程中还包括产品的检验、停放等环节。
企业在进行价值流程图(VSM)分析时,首先要挑选出典型的产品作为深入调查分析的对象,从而绘制出信息(情报)流程和实物流程的现状图,然后将现状图与信息(情报)和实物流程的理想状况图相比较,发现当前组织生产过程中存在的问题点,进而针对问题点提出改进措施。
【案例】
2002年11月某企业在推进JIT改善活动时,总经理发出指示,要求在全公司内开展全员参与的改善活动,以对市场变化做出快速反应,由于企业生产的产品种类非常多,并且大多数产品的主流生产过程大同小异,为此,企业在改善过程中选择了一个典型产品进行分析。
如下图所示:
销售金额大、生产数量多、生产周期长的一种零件被选择出来进行分析。
这样,分析调查就有针对性,便于经常性调查,验证起来也比较容易。
对这种零件进行详细的调查后发现,这种零件的基本资料为:
P/O每月4次,订单量每月约14000Pcs,每月进行3次生产,日产量约3600Pcs,每周送货两次。
相关人员据此画出了企业的信息(情报)流程和实物流程的现状图,如第9页图所示。
从现状图中粗虚线以上部分可以看到:
客户向香港的分公司发出订单,香港分公司再以E-mail或传真的形式传到深圳的这家工厂。
工厂接到订单后花了两天时间制定生产计划,又花了两天分别向两家供应商发送原材料采购订单。
整个信息流L/T是8天时间,海外材料到货L/T则是60天。
现状图中粗虚线以下部分为实物流:
提前3~5天把原料领好后,在工厂的二栋二楼中开始组织生产。
生产完成后由品质管理科开始检验,停留1天后更换场地进行包装,在包装区域内停留十几个小时。
包装完成后,品质管理科每隔6小时抽检一次,然后进行组装。
组装完成后再由品质管理科进行确定,确定后的成品在库房中放置14天后开始出货。
整个实物流L/T折算下来需要23~28天的时间。
工厂设想的信息(情报)流和实物流的理想状况如第下图所示。
从理想状况图中可以看到:
接到紧急订单后,只需要花费2天时间就可形成生产计划;
在最紧急的状态下,只需要花费6天的时间即可完成实物流。
因此,从领料开始算起,这家工厂设计的理想的信息流L/T为2天,理想的实物流L/T为6.05天。
通过信息(情报)流程和实物流程的现状图与理想状况图的比较,这家工厂组织人员开展了热烈的讨论,通过讨论发现很多问题点:
第一、信息流通过香港分公司周转后周期长、成本高;
第二、原材料订购时间需要60天,延缓了周转速度;
第三、在产品生产过程中,生产L/T时间长,中间的在库量太大,重复的搬送和停顿非常多;
第四、成品的在库量太大,时间长达14.6天。
暴露出问题点后,工厂制定出了相应的改善目标,开始着手解决问题。
通过从接订单、调度、生产到制品出货位置的流程改善,缩短全体L/T。
这家企业完成了以下目标:
情报处理L/T从原来的8天缩减为4天,材料接收L/T从60天缩减为30天,生产L/T由23.28天缩减为11.8天,在制品库存量从15184个/月缩减为7592个/月。
第2讲企业组织生产的价值(VSM)分析
(二)
1.企业管理的问题点
2.精益生产的目标取向
企业管理的问题点
VSM分析的对象:
浪费
VSM分析的主旨是立即暴露存在的浪费问题,并彻底排除浪费。
只有识别了问题,才能改善,很多不熟悉精益生产的人之所以会遇到一大堆难题,是因为他们没有找到问题点。
因此,要改善企业组织生产过程中的浪费问题,首先要认识浪费。
1.什么是浪费
在JIT生产方式中,浪费的含义与通常所说的浪费有所区别。
对于JIT来讲,凡是超出增加产品价值所绝对必需的最少量的物料、设备、人力、场地和时间的部分都是浪费。
因此,浪费不仅仅是指不增加价值的活动,还包括所用资源超过“绝对最少”界限的活动。
其中,随着企业管理水平的逐步提高,“绝对最小”的界限是不断下降的。
2.价值流程图分析关注的八大浪费
价值流程图分析关注的八大浪费包括:
不良/修理的浪费、过分加工的浪费、动作的浪费、搬运的浪费、库存的浪费、制造过多/过早的浪费、等待的浪费以及管理的浪费。
这些浪费都是与JIT生产方式相违背的。
八大浪费并不是在有VSM之后提出的,以丰田为代表的企业早在20世纪60年代就提出了这一概念。
其中,管理的浪费直到上个世纪90年代才真正得到人们的重视。
精益生产管理的着眼点与目标取向
精益生产管理的着眼点
精益生产管理的着眼点之一是创造价值,把不产生价值、却占用企业资源的业务(情报)流程环节、实物流程环节全部删除。
通过解决重复、停顿现象去发现问题,使得管理流程的价值最大化。
因此,推行JIT要以价值为关注焦点开展革新活动。
精益生产管理的另一个着眼点是缩短时间。
缩短时间就是从市场需求开始,一直到生产计划制定、采购计划制定、生产的组织、仓储以及生产制造和成品出货的全部过程L/T的缩短,从而降低成本,提高反应速度。
因此,应在不增加资源投入的情况下,以缩短信息/作业时间为改善的着眼点,寻找快速完成业务和生产的办法,始终把缩短L/T作为改善变革的驱动力。
精益生产管理的目标取向
精益生产管理的目标取向即不断设置更高的目标以求达成。
如图1-4所示,分别以精益生产关注的生产组织过程时间及价值损耗为横坐标和纵坐标,可见,旧的流程的价值损耗比较高、生产组织过程的时间比较长,而新流程的生产组织时间与价值损耗都有很大的缩减。
精益生产管理要解决的问题就是如何创造价值并缩短时间。
因此,在改善活动中应以此来指导企业的日常经营,把时间短、损耗