影响水泥混凝土路面平整度的因素及其控制措施Word文档下载推荐.doc
《影响水泥混凝土路面平整度的因素及其控制措施Word文档下载推荐.doc》由会员分享,可在线阅读,更多相关《影响水泥混凝土路面平整度的因素及其控制措施Word文档下载推荐.doc(11页珍藏版)》请在冰豆网上搜索。
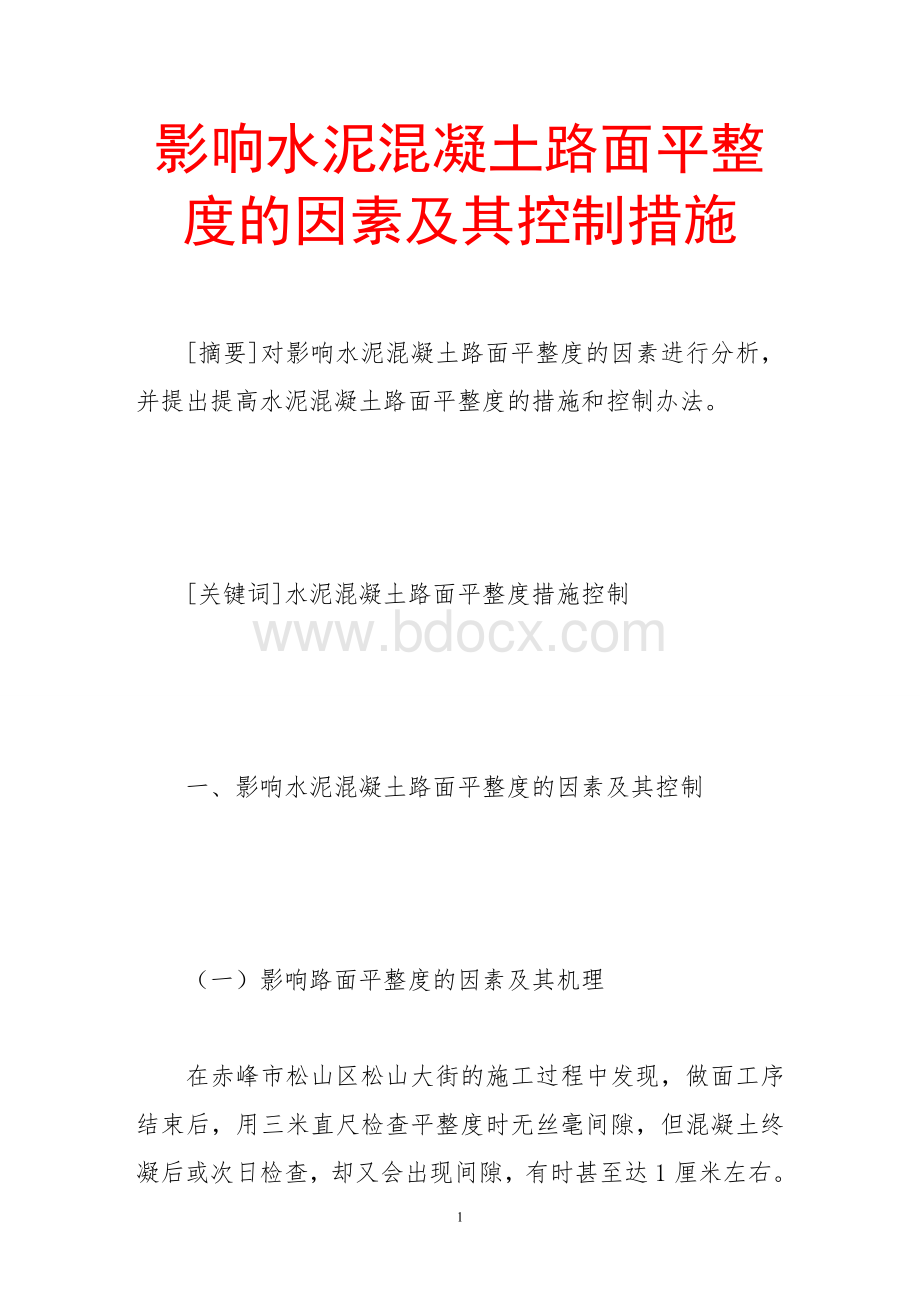
1.混凝土硬化过程中不均匀收缩的因素
(1)产生不均匀的机理
众所周知,新拌混凝土在一定温度条件下,毛细孔水、游离子水等不断蒸发,使毛细孔水在逐渐下降过程中,弯液面曲率逐渐增大;
在表面张力作用下,产生收缩力致使混凝土收缩。
上述收缩现象主要发生在浆体。
如果这种收缩是均匀进行的,对路面平整度不会产生什么影响或影响甚微。
若新拌混凝土水灰比值偏大、水泥浆体偏多,而水灰比或浆体在拌合料中分布不匀,或拌合料拌合不均,混凝土振捣密实度不均匀,收缩亦随之不均匀,将致使成型路面的不平整。
(2)不均匀收缩的因素
如上所述,产生混凝土硬化过程中不均匀收缩的因素主要是水灰比、浆体含量或密实度分布不均匀所致,可能是某一种因素所致,也可能是几种因素同时影响的结果。
一般有以下几种情况:
(3)水灰比控制不严
混凝土在拌制过程中,水灰比控制不严,拌合料时稠时稀,摊铺不均匀。
真空脱水时间不足,致使中部已达到塑性强度,边部却仍呈弹软状态,剩余水灰比分布不匀。
有的施工单位往往疏忽大意,相邻吸面未重叠放置吸垫,造成漏吸,则次处混凝土不仅仍处在初始水灰比状态,甚至还易在该处产生裂缝,也有的施工单位,为省事另拌砂浆或找补做面,不仅会造成表层水灰比不均匀,甚至会出现网裂或破皮。
(4)浆体含量不均匀
混凝土拌制时间不足所致、拌合料组成成分的不均匀或运料过程中产生离析现象,摊铺时又未重新翻拌,致使混合料中浆体不均匀分布,出现浆体或骨料集中现场。
振捣不足或振捣过度所致、浆体不上泛或浆体上泛过多、骨料下沉集中的分层离析,也会造成浆体含量的不均匀。
骨料集中处浆体含量少,收缩值小;
浆体集中处骨料较少,收缩值大。
(5)配料不准的影响
如果配料未采取准确秤量,致使骨灰比忽高忽低,或砂量时多时少,都会影响坍落度及和易性,水泥用量偏大或砂率偏低,都会造成真空脱水率的不均乃至最终水灰比和密实度的不均匀。
(二)前期工序所致影响
如前所述,路面平整度诸多因素的影响,而前期工序的影响,亦是重要因素之一。
例如:
1.模板的设置对平速度的影响,路面的标高和平速度都有赖于模板支设的稳固和模定的平整。
但实际施工中很难做到模顶标高和模板接头处的丝毫无差。
木模的变形,木模顶的磨损(磨损后沾染的砂浆很难清净),都会给平整度带来“先天不足”。
2.一般我们要求模顶标高与设计标高相同,只是在真空脱水前要始终保证混凝土面高于模顶5毫米左右(真空脱水后混凝土收缩值,一般为路面厚度的2%),以作脱水收缩预留值。
但振动梁及提浆棒(滚筒)均须紧贴在模板上拖滚,路拱横坡也使浆体向低侧流动,此值便难以保持,致使真空脱水收缩后混凝土面低于模顶,失去顶平标准而影响平整度。
二、提高路面平整度的措施及其质量控制
针对上述因素,不断改进施工工艺,严格施工质量控制,是提高路面平整度的主要关键。
为便于阐述,现按与平整度有关的工艺流程顺序,分述如下:
(一)混凝土制备
1.按真空脱水混凝土要求进行配合比设计和试配
一般300号混凝土最好采用425号普通水泥,因为火山灰水泥含很细的附加填充料,具有很强的吸水能力,影响脱水效果。
矿渣水泥脱水效果介于二者之间。
初始水灰比可控制在0.5-0.55之间,坍落度采用了3-5厘米(过小利于振捣密实和脱水效果,但外加减水剂时可用1-3厘米)。
水泥用量偏高或砂率偏低,都对真空脱水不利,因此水泥用量一般采用每立方米330-350公斤,砂石比控制在0.52左右。
若为加快施工速度,尽快脱模,使混凝土更好地收缩密实,宜用较高砂量,骨料系用连续级配或最大粒径3厘米;
若为提高强度,节省水泥,宜用较少砂量,骨料采用间断级配或最大料径限4厘米。
2.坚持称量配料,经常检查砂石含水量及袋装水泥亏重情况,以保配料准确。
3.须有专人检查拌料时间和测试坍落度,以保拌料均匀和水灰比准确。
(二)基层
干燥天气应提前洒水湿润,防止基层吸收混凝土水分,影响含水量分布不均。
(三)支模
①尽量采用钢模。
钢模刚度较好,易于支设稳固,模顶平整光洁,使用周期长。
若用木模,内壁和模顶应用铁皮包裹。
②为保证真空脱水后混凝土面不低于模顶,可用模顶临时敷设角钢的方法,以保证真空脱水前混凝土高出模顶之预留缩值。
角钢平整光洁,振动梁及提浆棒(滚筒)在其上拖滚更为方便,真空脱水结束后即可拆除。
(四)摊铺
对拌合不均或运料发生离析的混合料,摊铺前须重新翻拌均匀,否则不得进行下道工序施工,摊铺时混凝土不得抛掷,尤其是近模处要反扣铁锹铺放。
摊铺高度要考虑振捣下沉值并尽量铺平。
(五)振捣
1.应用平板振捣器纵横全面振捣,相邻行列重叠20厘米左右,防止漏震。
2.既要防止漏振或振捣不足,也要防止振捣过度,以混合料停止下沉、表面泛浆不再冒泡为度,一面产生分层离析。
3.应用振捣棒(插入式振捣器)仔细认真振捣,能减少接缝处的微鼓峰脊现象。
(六)振拖
①震动梁速度不宜过快,每分钟约1米左右即可。
边振拖边找补,甚至表面平实为止。
②经常检查震动梁有无下挠变形,及时修正更换。
(七)提浆刮平
1.先清净模顶砂浆,以保证提浆棒紧贴模顶拖滚。
2.拖滚时若发现显露石子,可使提浆棒一头不动,另一头提起轻击数次,使其浆复平平实。
有些施工单位很善于使用提浆棒。
他们来回拖滚十几次,致使表面非常平实,用三米直尺检查不出间隙,直空脱水后仍保持无凹凸痕迹,给做面创造了良好条件,对确保路面平整度具有决定性作用。
(八)真空脱水
1.购置滤布应先了解滤布缩水率大小,适当加大所需尺寸。
2.脱水开始应采用400毫米汞柱真空度,3~5分钟内逐步上升到600毫米汞柱,以防开始便采用高真空度使表层过早致密,堵塞下层出水通道,影响脱水效果。
结束前亦应逐渐减弱真空度并先掀开吸垫四角,以利残留水排出。
3.每次吸垫位置应与前次重叠20厘米。
以防漏吸。
笔者意见,还应适当重叠些,以免交接范围内发生弹软现象,造成含水量分布不均匀。
4.要保持足够脱水时间。
一般规定脱水时间在混凝土厚度的1-1.5倍范围,基本已能满足。
由于脱水时间与脱水深度呈抛物线关系,随深度的增加,真空传播速度逐步衰减,最后继续增加时间并不会增加脱水量。
因此,时间过长并无利。
[
5. 1、基坑开挖
(1)、土方开挖时,准确计算土方工程量,做好土方调配。
计算挖方量与回填土方量,确保回填土方存量,本工程回填土方量较大,用于回填的土方应集中堆至甲方(或经双方协商指定的临时堆土处)指定弃土处以备回填。
(2)、根据本工程地质勘查报告,为平衡土方量,地表杂填土运至场外城郊弃土处,其余用于回填的土方应集中存于场地东北角。
(3)、本工程场地土质较好,地下水位较深,挖土放坡系数按1:
0.33进行。
(4)、根据桩位图及基础平面图,考虑打桩机械施工时的最小工作面宽度,基坑底部尺寸为从最外排桩边到槽边不小于1.5m。
(5)、在土方开挖过程中项目技术员、工长应经常检查基槽开挖尺寸、标高,保证基坑大小、标高正确。
严防基槽不够宽或基坑超挖。
6.
(1)、组织项目施工人员认真阅读施工图纸,掌握工程内容,熟悉挖土尺寸、标高、轴线位置,使每个在施人员都掌握图纸内容
7.
(2)做到层层交底制度,工程师向施工工长交底、施工工长向施工班组长交底、施工班组长向施工人员交底,层层落实质量责任制,保证土方施工顺利进行。
(3)工地技术人员应旁站检查基坑标高,挖土深度不得超过基底设计标高,挖至基底设计标高基础不能及时灰土施工时。
(4)在挖土过程中应对轴线控制桩、引桩、现场水准点加以保护,并经常测量和检查是否位移,对破坏的轴线引桩要及时修复。
(5)人工破桩头,清理桩头时应使用专用工具,避免破坏桩身,保证桩顶面平整,标高一致符合设计要求。
(6)施工中如发现有文物或古墓应妥善保护,并及时报请有关部门处理。
8.
(1)
土方开挖施工采用水平分段,垂直分层的方法施工。
每段大约10m到15m之间,每层约1.2m深。
11