CA6140主轴工艺与钻床磨床夹具的设计文档格式.docx
《CA6140主轴工艺与钻床磨床夹具的设计文档格式.docx》由会员分享,可在线阅读,更多相关《CA6140主轴工艺与钻床磨床夹具的设计文档格式.docx(55页珍藏版)》请在冰豆网上搜索。
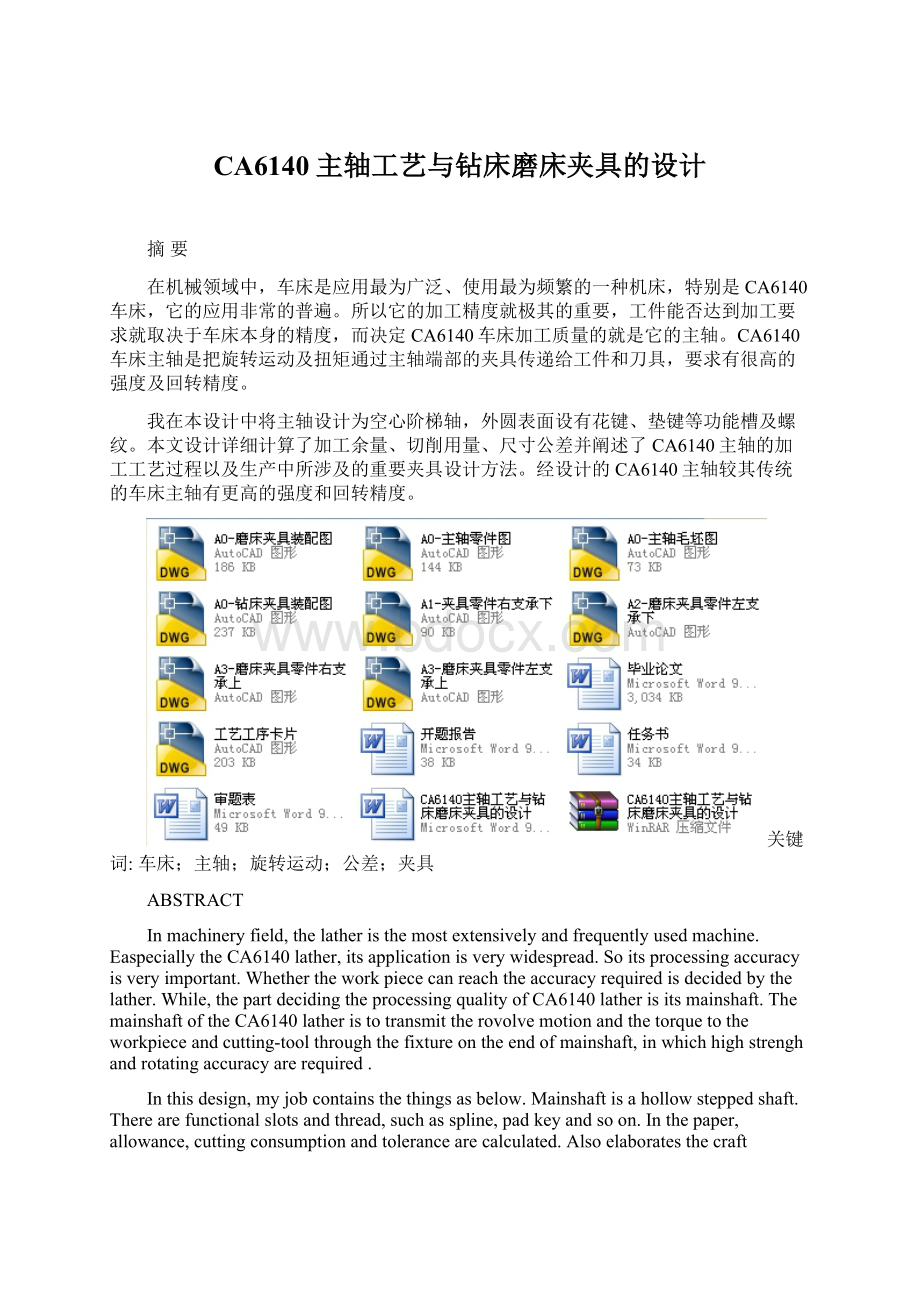
公差;
夹具
ABSTRACT
Inmachineryfield,thelatheristhemostextensivelyandfrequentlyusedmachine.EaspeciallytheCA6140lather,itsapplicationisverywidespread.Soitsprocessingaccuracyisveryimportant.Whethertheworkpiececanreachtheaccuracyrequiredisdecidedbythelather.While,thepartdecidingtheprocessingqualityofCA6140latherisitsmainshaft.ThemainshaftoftheCA6140latheristotransmittherovolvemotionandthetorquetotheworkpieceandcutting-toolthroughthefixtureontheendofmainshaft,inwhichhighstrenghandrotatingaccuracyarerequired.
Inthisdesign,myjobcontainsthethingsasbelow.Mainshaftisahollowsteppedshaft.Therearefunctionalslotsandthread,suchasspline,padkeyandsoon.Inthepaper,allowance,cuttingconsumptionandtolerancearecalculated.AlsoelaboratesthecraftprocessesofthemainshaftofCA6140lather,andthedesignofimportantfixture.Afterbeingdesigned,comparedwithtraditionallather,thestrengthandrotatingaccuracyareenhanced.
Keywords:
Lather;
Mainshaft;
RotatingMovement;
Tolerance;
Fixture
第1章绪论
1.1概述
精密机床的关键部件是进给系统和主轴系统,不同类型的机床主轴,对所选用轴承的精度要求既有相同点,也有不同之处。
数控机床和轴承磨床可以归于精密机床一类。
现代精密机床和传统机床的结构,从原理上来说,没有太大的变化,主要还是区别于导轨加工技术的改进和主轴系统精度的提高。
1.2车床的发展史
车床的发展大致可区分成四个阶段,雏型期,基本架构期、独立动力期与数值控制期,底下将针对其发展的过程加以介绍。
车床的诞生不是发明出来的,而是逐渐演进而成,早在四千年前就记载有人利用简单的拉弓原理完成钻孔的工作,这是有记录最早的工具机,即使到目前仍可发现以人力做为驱动力的手工钻床,之后车床衍生而出,并被用于木材的车削与钻孔,英文中车床的名称Lathe(Lath是木板的意思)就是由此而来,经过数百年的演进,车床的进展很慢,木质的床身,速度慢且扭力低,除了用在木工外,并不适合做金属切削,直到工业革命前。
这段期间可称为车床的雏型期。
18世纪开始的工业革命,象征着以工匠主导的农业社会结束,取而代之的是强调大量生产的工业社会,由于各种金属制品被大量使用,为了满足金属另件的加工,车床成了关键性设备,18世纪初车床的床身已是金属制,结构强度变大更适合做金属切削,但因结构简单,只能做车削与螺旋方面的加工,到了19世纪才有完全以铁制零件组合完成的车床,再加上诸如螺杆等传动机构的导入,一部具有基本功能的车床总算开发出来。
但因动力只能靠人力、兽力或水力带动,仍无法满足需求,只能算是刚完成基本架构的建构。
瓦特发明了蒸气机,使得车床可藉由蒸气产生动力用来驱动车床运转,此时车床的动力是集中一处,再藉由皮带与齿轮的传递分散到工厂各处的车床,20世纪初拥有独立动力源的动力车床(EngineLathe)终于被开发,也将车床带到新的领域。
此期间拜福特公司大量生产汽车所赐,许多汽车零件必须以车床加工,为了确保零件供应充足,供货商必须大量采购车床才能应付所需,即使到今天车床的发展仍受到汽车产业的荣枯所左右。
1.3本课题研究的内容和设计思想
保证主轴支承轴颈的尺寸、形状、位置精度和表面粗糙度,主轴前端内、外锥面的形状精度、表面粗糙度以及它们对支承轴颈的位置精度。
主轴支承轴颈的尺寸精度、形状精度以及表面粗糙度要求,可以采用精密磨削方法保证。
磨削前应提高精基准的精度。
保证主轴前端内、外锥面的形状精度、表面粗糙度同样应采用精密磨削的方法。
为了保证外锥面相对支承轴颈的位置精度,以及支承轴颈之间的位置精度,通常采用组合磨削法,在一次装夹中加工这些表面。
主轴加工中,为了保证各主要表面的相互位置精度,选择定位基准时,应遵循基准重合、基准统一和互为基准等重要原则,并能在一次装夹中尽可能加工出较多的表面。
由于主轴外圆表面的设计基准是主轴轴心线,根据基准重合的原则考虑应选择主轴两端的顶尖孔作为精基准面。
用顶尖孔定位,还能在一次装夹中将许多外圆表面及其端面加工出来,有利于保证加工面间的位置精度。
所以主轴在粗车之前应先加工顶尖孔。
为了保证支承轴颈与主轴内锥面的同轴度要求,宜按互为基准的原则选择基准面。
如车小端1∶20锥孔和大端莫氏6号内锥孔时,以与前支承轴颈相邻而它们又是用同一基准加工出来的外圆柱面为定位基准面(因支承轴颈系外锥面不便装夹);
在精车各外圆(包括两个支承轴颈)时,以前、后锥孔内所配锥堵的顶尖孔为定位基面;
在粗磨莫氏6号内锥孔时,又以两圆柱面为定位基准面;
粗、精磨两个支承轴颈的1∶12锥面时,再次用锥堵顶尖孔定位;
最后精磨莫氏6号锥孔时,直接以精磨后的前支承轴颈和另一圆柱面定位。
定位基准每转换一次,都使主轴的加工精度提高一步。
对车床主轴的精确要求,就显示出其加工过程中夹具的重要性。
夹具的主要功能是装夹工件,使工件在夹具中定位和夹紧。
在机械加工中,使用机床夹具的目的主要有以下六个方面:
1.保证加工精度;
2.提高劳动生产率;
3.改善工人劳动条件;
4.降低生产成本;
5.确保工艺纪律;
6.夸大机床工艺范围。
设计夹具时,应满足下列四项要求:
1.保证工件的加工精度要求;
2.保证工人的操作方面安全;
3.达到加工的生产率要求;
4.满足夹具一定的使用寿命和经济性要求。
第2章零件的分析
2.1零件的作用
CA6140车床主轴是把旋转运动及扭矩通过主轴端部的夹具传递给工件和刀具,要求有很高的强度及回转精度,其结构为空心阶梯轴,外圆表面有花键、电键等功能槽及螺纹。
2.1.1支承轴颈
主轴两主支承轴颈A、B和1:
12锥度与双列向心短圆锥磙子轴承配合,并支承在主轴箱孔上是主轴部件的装配基准。
其圆度和同轴度将引起主轴回转误差,影响被加工工件的精度,必须严格控制。
主支承轴颈圆跳动公差为0.005mm,1:
12锥面接触率70%,表面粗糙度Ra为0.4µ
m。
主轴中间辅助支承为单列滚子轴承,用以提高主轴刚性和回转精度。
其径向圆跳动公差为0.01mm;
表面粗糙度Ra为0.4µ
尺寸公差等级为IT6。
2.1.2头部锥孔
主轴头部莫氏6号锥孔是用来安装夹具的定位面的。
可安装顶尖,也可安装刀具。
其对支承轴颈A、B的圆跳动,近轴端公差为0.005mm,离轴端300公差为0.01mm。
锥面的接触率≥70%表面粗糙度为0.4µ
m,硬度要求HRC52。
主轴锥孔的轴线与支承轴颈线不重合,将使被加工工件产生相对位置误差。
2.1.3头部短锥
主轴头部短锥C和大台阶面D是安装卡盘的定位面。
其圆跳动为0.008µ
m,表面粗糙度Ra为0.8µ
头部短锥C对支承轴颈的圆跳动将卡盘产生同轴度误差。
大台阶端面D对支承轴颈轴线跳动将卡盘产生垂直度误差。
2.1.4装配轴颈
主轴上共安装三个齿轮,其中一个空套,一个单键连接,另一个是花键连接。
装配轴颈对支承轴颈径向圆跳动公差为0.015mm~0.9mm。
表面粗糙度Ra为0.4~0.6µ
m,尺寸公差等级为IT5。
装配轴颈对支承轴颈的同轴度误差,会引起主轴传动齿轮啮合不良,当主轴转速很高时,还会影响齿轮的传动平稳性,产生噪生。
加工工件时,会在工件表面产生重复出现的震纹,精加工是尤为明显。
2.1.5轴向锁紧
主轴外圆上有三段螺纹,用于轴承等铃部件的轴向锁紧。
当主轴螺纹的轴线与支承轴颈歪斜时,会引起主轴上琐紧螺母端面倾斜,造成主轴内圈轴线的同向倾斜,引起主轴的径向跳动。
因此,控制螺纹轴线与支承轴颈轴线的同轴度≤0.025mm。
从上面分析看出:
CA6140车床主轴加工面较多,包括内外圆、内外锥、单键和花键、螺纹等,而且尺寸精度、性为精度以及表面粗糙度要求均较高,部分表面还需要表面淬火,但主要加工表面是以上五种,其中两主支承轴颈本身的尺寸精度、形状精度,两支承之间的同轴度和主支承轴颈与其它表面相互位置精度以及表面粗糙度,则是主轴加工的关键。
2.2零件的工艺分析
在拟定CA6140车床主轴工艺工艺过程时,应考虑一些问题。
2.2.1加工阶段的划分
加工过程大致划分为四个阶段:
顶尖孔之前是预加工阶段;
打顶尖孔之后至调质前的工序为粗加工阶段调质处理后至表面淬火前的工序为半精加工阶段;
表面淬火后工序为精加工阶段。
要求较高的支承轴颈和莫氏6号锥孔的精加工,则应在最后进行。
整个主轴加工的工艺过程,是以主要表面(特别是支承轴颈)的加工为主线,穿插其它表面的加工工序组成的。
这样安排的优点是:
粗加工时切除大量金属是产生的变形,可以在半精加工和精加工中去掉。
而主要表面放在最后,可不受其它表面加工的影响,并方便安排热处理工序,有利于机床的选择。
2.1.3工序顺序安排
工序顺序的安排主要根据基面先行、先粗后精、先主后次的原则,并注意下列几点:
主轴毛坯锻造后,一般安排正火处理。
其目的是,消除锻造残余应力,改善金属组织,降低硬度,改善切削加工性能。
棒料毛坯可不进行该道热处理工序。
粗加工后,安排调质处理。
其目的是获得均匀细致的索氏体组织,提高零件的综合力学性能,以便在表面淬火时得到均匀致密的硬度层,并使硬化层的硬度由表面向中心逐渐降低。
同时索氏体的金属结构经加工后,表面粗糙度较细。
最后,还须对有相对运动的轴颈表面和经常与夹具接触的锥面进行淬火或氮处理,以提高其耐磨性。
一般高频淬火安排在粗磨之前;
氮化安排在粗磨之后,精磨之前。
(一)外圆表面的加工顺序
先加工大直径外圆,以免一开始就降低工件刚度。
(二)深孔加工
应安排在调质以后进行,