机械制造工艺副变速拨叉说明书Word文档格式.doc
《机械制造工艺副变速拨叉说明书Word文档格式.doc》由会员分享,可在线阅读,更多相关《机械制造工艺副变速拨叉说明书Word文档格式.doc(17页珍藏版)》请在冰豆网上搜索。
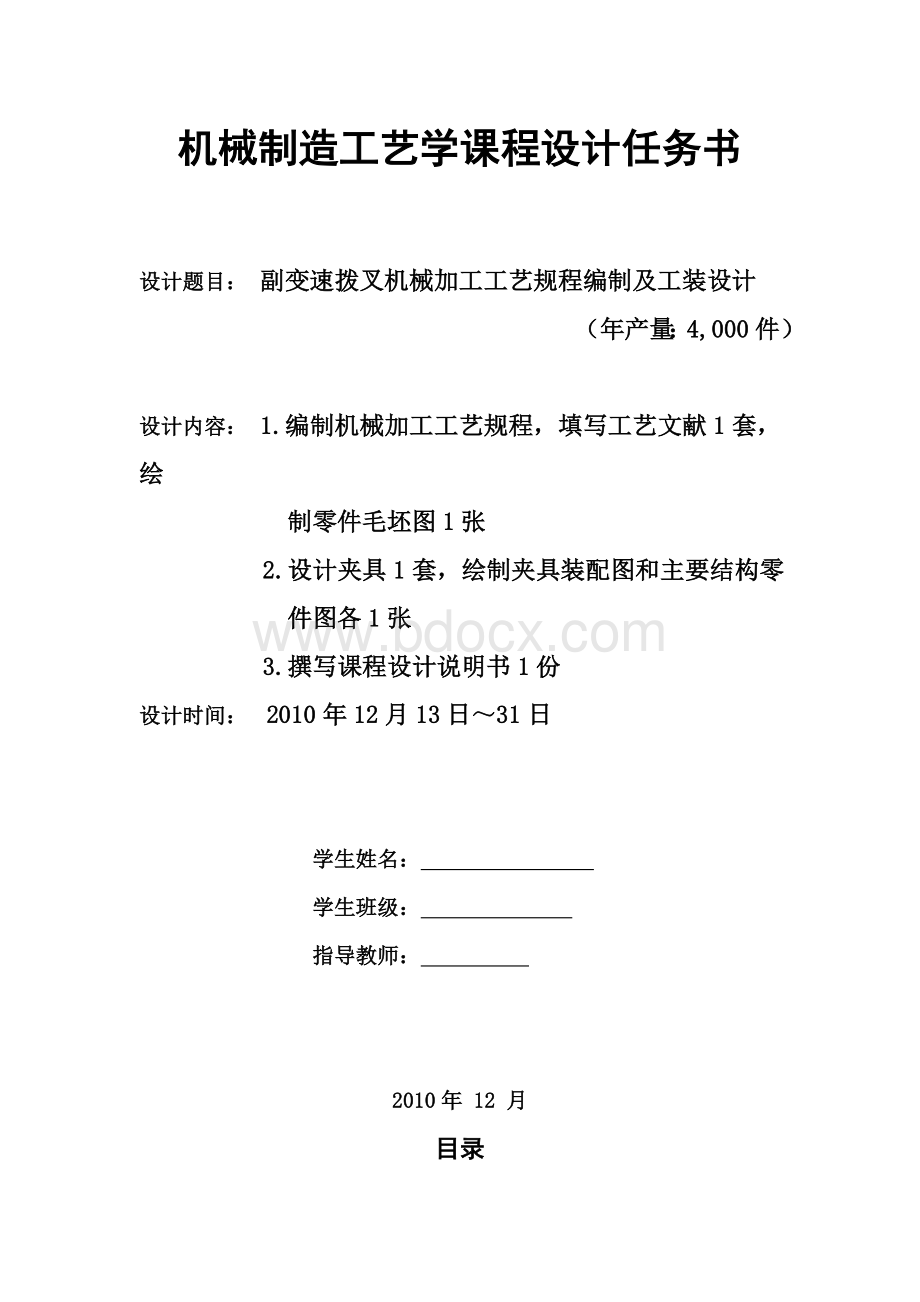
Y5零件分析
(一)零件的作用
副变速拨叉应用在副变速箱的换档机构中,拨叉头孔套早变速叉轴上。
拨叉脚则夹在双联变换齿轮的槽中。
当需要变速时,操纵变速杆,变换操纵机构就通过拨叉头部的操纵槽带动拨叉与变速叉轴一起在变速箱中滑移,拨插脚拨动双联变换齿轮在花键上滑动一改变档位,从而改变速度。
该拨叉变速时要承受弯曲应力和冲击载荷的作用,因此该零件具有足够的强度和刚度以及韧性,以适应拨叉的工作条件。
该拨叉形状特殊,结构简单。
为实现变速的功能,其叉轴孔与变速叉轴有配合要求,因此加工精度要求较高。
叉脚两端面在工作中需要承受冲击载荷,为增强起耐磨性,该表面要求高频淬火处理,硬度为48—58HRC。
拨叉头两端面和叉脚两端面在轴方向上均高于相邻表面,这样既减少了加工表面又提高了变速时叉脚端面的接触刚度。
该零件除了主加工表面外,其余的表面加工精度均较低,不需要高精度的机床加工,通过铣削、钻床的粗加工就可以达到加工要求。
(二)零件的工艺分析
1.确定毛坯
零件材料为KTH-10,考虑到零件在加工工程中所受冲击力不大,并且为中批量生产,因此,选择金属模砂型铸造毛坯。
铸件要求不能有砂眼、疏孔等缺陷,以保证零件的强度、硬度和刚度,使其在外力作用下不至于发生意外事故。
2.主要尺寸精度和形位公差
(1)Φ24的圆柱
(2)Φ14的孔的尺寸精度为H9(+0.0430),内表面粗糙度为3.2,其中心轴线的基准线偏差为Φ0.025
(3)两叉头同侧的表面粗糙度为6.3
(4)零件图中14H13(+0.270)凹槽表面粗糙度为12.5
(5)叉脚端面40H(-0.12-0.24)表面粗糙度为12.5。
二,零件的工艺分析及生产类型的确定
一,确定毛坯
1,确定毛坯种类:
零件材料为KTH350-10,考虑到零件在加工过程中所受冲击力不大并且为中批量生产,所以,选择金属模机械砂型铸造毛坯。
查表,选用铸件尺寸公差等级为CT10。
保证的尺寸公差在1-3mm。
副变速拨叉毛坯图见附件一,零件图见附件二。
三,工艺规程设计
(一)选择定位基准:
1:
粗基准选择:
以零件的左端面为主要粗基准,以零件的左端面外圆为辅助粗基准。
2:
精基准选择:
根据精基准的选择原则“基准统一原则”以及考虑到工件的装夹与加工方便,选用加工后的左端面为主要精基准,以零件的左端面外圆为辅助精基准。
(二)制定工艺路线
考虑到零件的几何形状,尺寸精度以及位置精度等技术要求,以及加工时的经济性,尽量使工序能够集中起来。
零件的加工方法及工艺路线如下:
方案一:
工序一:
先铸件回火
工序二:
以Φ24外端面为粗定位基准,粗铣拨叉左右两端面;
用成型刀铣左右两端面
工序三:
以Φ24外端面为基准,铣叉脚右端面;
倒角
工序四:
以Φ24外端面为基准,钻,扩,铰孔Φ14mm孔
工序五:
以叉脚右端面为精基准,铣叉脚左端面,倒角;
铣14H13()槽
工序六:
以叉脚右端面为精基准,钻Φ8.7孔
工序七:
去毛刺
工序八:
终检
方案二
工序1:
粗铣,精铣右端面,以左端面为粗基准,采用立式铣床加专用夹具。
工序2:
钻,扩,铰,及精铰孔,以右端面以及外圆为基准,采用立式钻床以及专用夹具。
工序3:
粗铣,精铣左端面,以及粗铣,精铣两叉头左侧及右侧,以右端面为定位基准,采用立式铣床及专用夹具。
工序4:
粗铣,精铣两叉头内侧,以孔中心为定位基准,采用卧式铣床及专用夹具。
工序5:
粗铣,精铣槽,以孔表面为定位基面,采用卧式铣床及专用夹具。
工序6:
钻,扩,铰及精铰孔,以孔表面为定位基面,采用立式钻床及专用夹具。
工序7:
去毛刺。
工序8:
终检。
通过比较,方案一的加工精度和加工顺序都没有方案二好,因此,将加工工艺路线确定为:
(三)加工余量,工序尺寸及公差的确定
1,各个工序加工余量,精度等级
工序
加工表面
加工内容
加工余量(mm)
精度等级(CT)
工序尺寸(mm)
表面粗糙度
工序余量(mm)
1
右端面
粗铣
2
12
74.4
1.2
精铣
10
73.2
25
两叉头右侧
3
12.2
1.6
10.6
孔
钻,扩
12,1.8
11
13.8
0.2
粗铰及精铰
0.14
0.06
7
14
3.2
左端面
71.2
70
两叉头左侧
7.6
8
6
6.3
4
两叉头内侧
36
9
40
12.5
5
槽
13.6
0.7
0.5
8.7
确定切屑用量及时间定额
一、铣端面以及两叉头左侧
1、加工条件:
被加工材料KTH350-10其最小抗拉强度为330MPa,最低延伸率为10的黑心可锻铸铁。
零件大小为x=70mm,y=85mm。
2、加工要求:
粗铣右端面,加工余量为2mm。
3、刀具选择:
选择硬质合金端铣刀YG8,根据,,选取铣刀直径D=40mm,d=16mm,齿数12。
在0.15~0.3mm/z之间。
4、切屑深度:
因为加工余量较小,一次走刀即可完成。
即被吃刀量为2mm。
5、选用铣床:
查《机械制造工艺设计简明手册》表4.2-35,选用X51立式铣床,同时查得主轴转速:
100电动机功率:
4.5kw。
6、确定切屑速度和工作台每分钟进给量。
查《切削用量简明手册》表3.27中公式计算查表
74.8m/min
7、工时定额的确定
完成零件加工的一个工序的时间定额公式:
其中-单件时间定额;
-基本时间;
-辅助时间;
-布置工作时间;
-休息及生理需要时间;
-准备与终结时间;
N-一批零件的数量。
基本时间:
计算可得.
辅助时间:
=0.2=0.08min.
布置工作时间:
=0.05×
0.48=0.024min.
休息及生理需要时间=0.03×
0.480.02min
准备与终结时间在中批量生产中可以忽视。
工时定额T=0.53min
二、加工孔
被加工材料KTH350-10其最小抗拉强度为330MPa,最低延伸率为10的黑心可锻铸铁,孔直径为14mm。
钻孔至12mm,扩孔至13.8mm,精铰至14mm。
2、选择刀具:
钻孔时,高速钢,钻头直径12mm,扩孔时,高速钢,钻头直径13.8mm,铰孔时,YG8,钻头直径为14mm。
进给量,切削速度查《切削用量简明手册》表2.30算得。
3、选用钻床:
查《机械制造工艺设计简明手册》表4.2-14,选用立式钻床Z525。
主轴最大行程175mm,主轴转速97r/min,主轴最大转矩245.25N,功率2.8kw。
4、时间定额的确定
钻孔的基本时间:
;
计算可得:
=0.2=0.76min.
=0.05*3.8=0.19min.
休息及生理需要时间=0.03*3.80.11min
工时定额4.86min
扩孔的基本时间:
=0.2=1.02min.
=0.05*5.1=0.26min.
休息及生理需要时间=0.03*5.10.15min
工时定额6.53min
铰孔的基本时间:
:
=0.2=0.98min.
=0.05*4.9=0.25min.
休息及生理需要时间=0.03*4.90.15min
工时定额6.28min
加工孔所用的额定工时为:
T=17.6min
三、加工孔
被加工材料KTH350-10其最小抗拉强度为330MPa,最低延伸率为10的黑心可锻铸铁,孔直径为8.7mm。
钻孔至7mm,扩孔至8mm,精铰至8.7mm。
钻孔时,高速钢,钻头直径7mm,扩孔时,高速钢,钻头直径8mm,铰孔时,YG8,钻头直径为8.7mm。
进给量,切削速度查《切削用量简明手册》表2.30算得扩孔时,高速钢,钻头直径8mm,
=0.2=0.46min.
=0.05*2.3=0.12min.
休息及生理需要时间=0.03*2.3=0.07min
工时定额2.95min
=0.2=0.64min.
3.2=0.16min.
3.2=0.96min
工时定额4.1min
=0.2=0.92mi