客车底盘总装焊装生产实用实用工艺流程Word格式文档下载.docx
《客车底盘总装焊装生产实用实用工艺流程Word格式文档下载.docx》由会员分享,可在线阅读,更多相关《客车底盘总装焊装生产实用实用工艺流程Word格式文档下载.docx(7页珍藏版)》请在冰豆网上搜索。
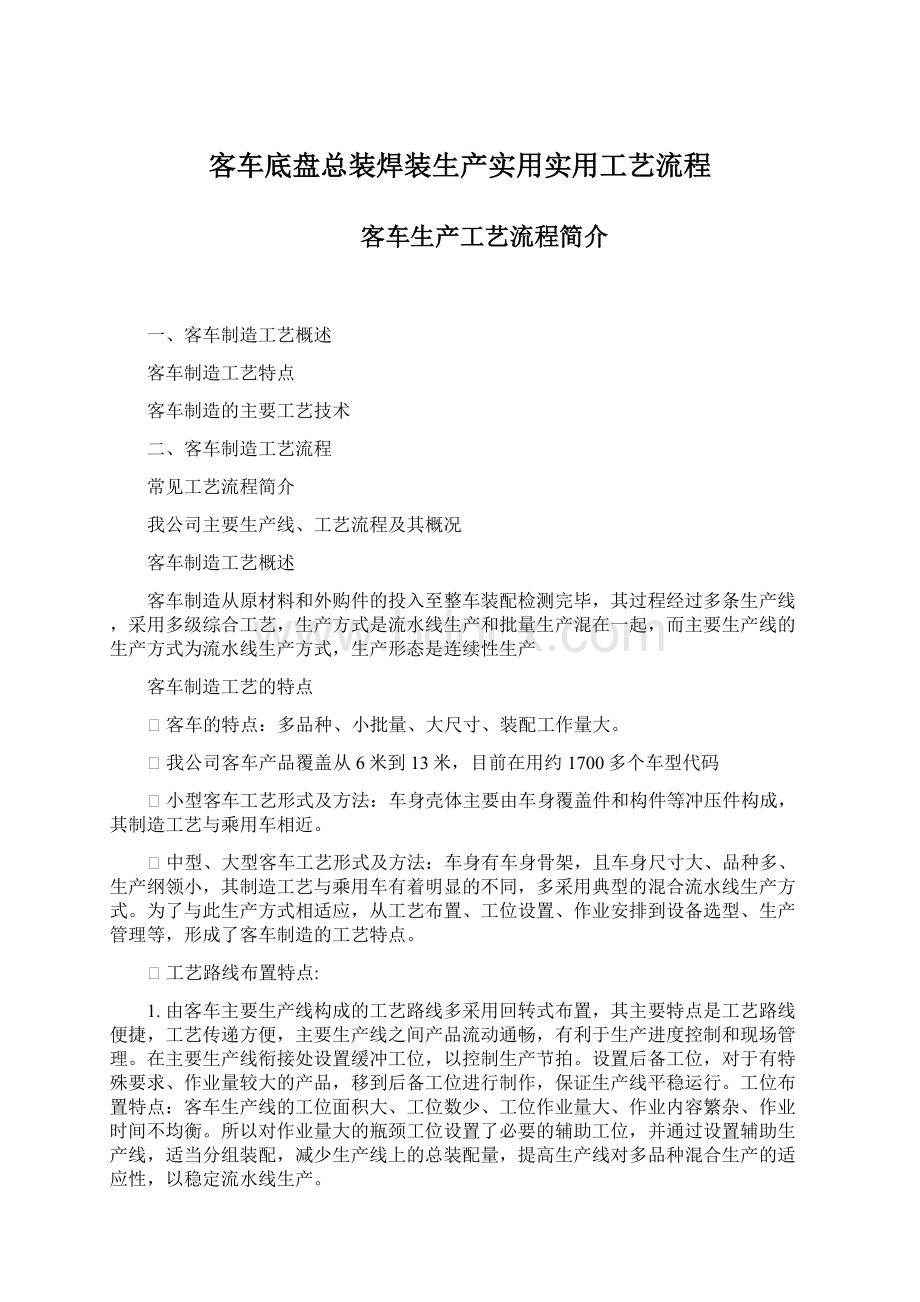
小型客车工艺形式及方法:
车身壳体主要由车身覆盖件和构件等冲压件构成,其制造工艺与乘用车相近。
中型、大型客车工艺形式及方法:
车身有车身骨架,且车身尺寸大、品种多、生产纲领小,其制造工艺与乘用车有着明显的不同,多采用典型的混合流水线生产方式。
为了与此生产方式相适应,从工艺布置、工位设置、作业安排到设备选型、生产管理等,形成了客车制造的工艺特点。
工艺路线布置特点:
1.由客车主要生产线构成的工艺路线多采用回转式布置,其主要特点是工艺路线便捷,工艺传递方便,主要生产线之间产品流动通畅,有利于生产进度控制和现场管理。
在主要生产线衔接处设置缓冲工位,以控制生产节拍。
设置后备工位,对于有特殊要求、作业量较大的产品,移到后备工位进行制作,保证生产线平稳运行。
工位布置特点:
客车生产线的工位面积大、工位数少、工位作业量大、作业内容繁杂、作业时间不均衡。
所以对作业量大的瓶颈工位设置了必要的辅助工位,并通过设置辅助生产线,适当分组装配,减少生产线上的总装配量,提高生产线对多品种混合生产的适应性,以稳定流水线生产。
2.一些生产规模较大的客车企业为了提高生产能力,适应客车品种多、批量小的生产特点,多采用设置两条并行的车身焊装线和两条并行的车身装配线与一条车身涂装线相衔接的方式,焊装线、装配线的工位采用串联式布置,整体浸渍磷化和浸漆、电泳底漆生产线工位采用串联式布置;
涂装线其他工位采用并列式布置。
由于主要生产线位于不同的厂房内,能更好地满足环境保护和安全性要求。
3.一些生产规模较大的客车企业为了提高生产能力,适应客车品种多、批量小的生产特点,多采用设置两条并行的车身焊装线和两条并行的车身装配线与一条车身涂装线相衔接的方式,焊装线、装配线的工位采用串联式布置,整体浸渍磷化和浸漆、电泳底漆生产线工位采用串联式布置;
客车工装、设备特点:
针对客车的生产特点,所采用的工装设备一般具有一定的通用性,以降低生产成本,缩短生产车型变化时生产线调整时间。
如焊接设备采用半自动CO2气体保护焊、适应几种车型生产的车身骨架组焊胎具、通用的气动和电动装配工具等。
客车因其车身尺寸大,形成了如侧围蒙皮张拉工艺、顶盖两侧蒙皮辊压成型工艺、车身骨架联装组焊等特点显著的工艺形式。
客车制造工艺水平相关因素:
与客车结构、生产规模、生产条件等因素密切相关。
由于客车结构的不同和工厂生产规模的差异,造成所选择的工艺方法和工装设备呈现多样性。
客车制造主要工艺技术
基本工艺:
冲压、焊接、喷涂和装配工艺是客车制造的四种基本工艺。
这四种基本工艺在客车车身制造中的具体应用,形成了车身骨架制造、车身蒙皮制造、车身构件冲压成型、车身焊装、金属构件磷化和车身喷涂、底盘和车身装配,以及整车性能调试检测等客车制造工艺。
主要设备:
在客车车身生产中所使用的主要设备有下料设备、冲压设备、焊接设备、磷化设备、喷涂设备以及转运设备等;
主要工艺装备:
工艺装备主要有冲压模具、骨架焊装胎具、前后风窗框组焊胎具、各种工作台以及检验样板等。
冲压:
小型客车车身的构件、覆盖件等零部件大部分是冲压件,大客车车身的板弯件、部分车身外蒙皮、司机门门体、乘客门门体、保险杠等零部件也是冲压件。
因此冲压工艺是车身零部件的主要生产工艺。
车身冲压零件的尺寸精度和表面质量是保证车身质量的基础,只有稳定的冲压件质量才能保证生产出合格的车身总成。
板材、模具和冲压设备是冲压生产的三大要素。
焊装:
客车车身骨架采用CO2气体保护焊,在焊接胎具上组焊而成。
其制造过程包括矩形管下料、矩形管弯曲成型、车身骨架五大片(前围、后围、左侧围、右侧围和顶盖骨架)的组焊和车身骨架联装组焊等。
骨架构件在五大片焊接胎具上定位、夹紧并组焊,形成五大片车身骨架。
五大片焊接胎具一般由底架、胎具本体和定位夹紧装置等部件组成,可以保证骨架组焊精度要求。
车身骨架的五大片与车身底架或车架在骨架联装组焊胎具上完成整车车身骨架的组焊。
利用组装胎组焊整车车身骨架,组焊精底高,质量好。
因此骨架联装组焊胎具是车身骨架制造工艺中的关键设备。
车身焊装工艺:
是在车身焊装线上进行的多种作业方法的总称。
对于小型车车身,冲压成型的构件和覆盖件通过焊装而形成车身总成(又称之白皮车身),焊装是车身成型的关键。
车身焊装工艺将车身零部件焊装为合件,再将若干合件和零部件焊装为分总成,最后将分总成、合件、零件装焊成白车身。
在车身焊装过程中,通常使用专用的装焊胎具将其零件进行定位、夹紧,装焊胎具和焊接设备是焊装的主要工装设备。
对于大型客车,在车身焊装线上的各工位依次完成车身骨架联装组焊、侧围蒙皮张拉、前后围蒙皮组焊、各种门体以及前后保险杠的安装等作业。
车身焊装质量不但影响车的外观质量,也影响车身装配件的装配质量。
磷化处理工艺:
能有效提高车身金属构件的耐腐蚀能力和车身的使用寿命,金属表面的磷化处理方法一般采用喷射法和浸渍法。
喷射法是指磷化液借助喷嘴以一定的压力喷向构件表面来实现磷化处理的方法,适用于大型的连续生产的构件。
对于复杂的金属构件,采用浸渍法更好,其生成的磷化膜致密平滑。
客车车身采用的磷化处理方法有金属构件的浸渍法磷化、车身总成(白皮车身)整体浸渍法和车身总成喷射法磷化三种。
磷化处理工艺包括金属表面在涂装前的除油、除锈和磷化处理,也称为涂装前金属表面处理。
金属表面磷化处理后应立即涂装防锈底漆。
涂装工艺:
是对客车零、部件和车身表面处理的工艺。
客车对装饰性、耐候性、耐腐蚀性要求很高,车身涂层具有保护功能和装饰功能。
装配工艺:
就是把零部件按照整车工艺流程的需要进行装配,是保证整车品质的最终关口。
总装配工艺(包括整车的检测调试)是客车生产中的最后一道工序,汽车检测线是企业对出厂客车的装配质量、技术性能和安全性能进行检测的质量保证措施和主要手段。
客车制造工艺流程
客车制造的主要生产线采用流水线作业方式。
各客车制造厂因其生产规模、生产条件和生产车型的不同,所采取的工艺流程亦有所不同,常见的工艺流程可归纳为三类。
1、脱壳式
2、扣合式
我公司生产线、工艺流程概况
一、部件准备车间,主要完成车身及底盘零部件自制件的加工。
按工作内容主要可分为:
剪折工位、钳工工位、焊接工位、等离子工位、备料工位、浸漆工位。
矩形管下料,重点控制的是下料尺寸、角度。
其下料的准确程度关系到小总成乃至车身总成的尺寸准确程度。
下料设备一般采用带式锯床、盘式锯床、弓式锯床、冲床等。
零部件公司:
自制车架,后期计划。
二、底盘装配车间,主要工作是将各个零部件进行组装,最终装配成能够独立行走的三类底盘,目前单班产约10台客车底盘,共分13个装配工位,底盘装配通过地板链进行输送。
1、翻转工位:
拥有底盘翻转设备,可以实现底盘的翻转。
2、支架工位:
主要装配转向系统及打车辆的唯一身份识别号码——VIN码。
3、吊装工位:
主要工作内容是将分装好的发动机带变速箱总成通过行车吊装到车架上。
4、底盘调试:
底盘调试即对下线的底盘的各个系统进行调整,加油,加防冻液,启动发动机。
最终要求是底盘能达到独立行走状态。
三、焊装车间主要工作内容是进行车身骨架、封板的焊装以及车身与底盘的扣合,目前单班最高产能为73台(18+18+20+15+2)。
共分大巴、公交、中巴、三条焊装线,每条生产线18个装配工位。
以及大型车事业部和豪华车事业部。
1、顶盖低位作业工位:
中顶蒙皮、侧顶蒙皮采用低位作业的方法,不仅降低了员工劳动强度,大大提高了操作的安全性,而且也便于控制顶蒙皮的焊接、制作质量,缩短了顶蒙皮焊接、空调进/回风口以及天窗口的制作工时。
2、总拼工位:
采用我司独立研发的总拼工装,通过限位块的快速翻转能实现多种大巴、中巴车型的车身总拼工作,满足了柔性化生产的需要。
每台车身的总拼,都严格按工艺要求操作,对于车身的关键尺寸,除了工装上加以保证外,现场员工每台车都要进行测量、记录,保证车身的总体尺寸在可控的范围内。
3、侧蒙皮安装工位:
采用液压拉伸机张拉蒙皮。
与传统的手工张拉机相比,不仅省时、省力,而且也解决了手工张拉在拉紧蒙皮的同时极易造成骨架变形的问题,蒙皮张拉后的平整度有了较大提高。
另外,液压拉伸机还能根据车型的不同,自动调整夹具的高度、长度、宽度方向的位置,满足了多品种、柔性化生产的要求。
4、车身扣合工位:
严格控制车身相对底盘的位置,进行多点、多维度的测量并记录,保证车身与底盘的相对位置偏差控制在5mm范围内。
非电泳工艺流程:
1顶盖低位作业—2总拼工位—3校正工位—4二层骨架工位—5侧蒙皮工位—6顶盖补焊工位—7乘客区封板工位—8驾驶区封板工位—9侧仓门安装工位—10车身扣合—11仓骨架—12仓封板—13底盘件安装—14乘客门、保险杠工位—15打磨—16修整—17交检
电泳后工艺流程:
1顶盖低位作业—2总拼工位—3校正工位—4二层骨架工位—5侧蒙皮工位—6顶盖补焊工位—7乘客区封板工位—8驾驶区封板工位—9行李仓骨架、踏步骨架工位—10行李仓封板、踏步封板工位—11侧仓门安装工位、乘客门、保险杠工位—12打磨、修整—车身电泳(后台阶隔音棉、仓门气弹簧、打胶<
后台阶、发泡挡板、轮罩>
、工艺撑杆拆除)—13扣车身、底盘防护工位—14行李仓骨架补焊工位—15仓封板补焊工位—16底盘件、前后保—17下线修整—18交检
刮涂腻子、大顶打胶
特殊防腐
油漆修整
底盘漆
下线修整
电泳车间简介
电泳生产线占地面积10000多平方米,生产节拍7~8分钟,年产达25000台车身和车架。
电泳线主要工艺:
脱脂—脱脂后水洗—表调—磷化—磷化后水洗—电泳—电泳后水洗—烘干—强冷。
电泳主要特点:
一、设备先进,工艺完善。
设有14个电泳主槽(容积300余立方米),关键部件采用进口设备;
采取16道电泳工序,立邦电泳漆可保证涂膜的耐盐雾性能达1000小时以上,极大提升了整车防腐蚀能力。
二、全线自动化,效率高。
输送系统通过程序控制,自动完成规定的工艺动作。
电泳设备设有自动运行按键,实现一键操作。
三、烘干产生烟雾少,有利员工的身心健康。
四、节能、环保。
电泳漆以水为剂,避免了环境污染,生产过程也更安全;
通过污水膜处理技术,使电泳产生的污水再利用率达到65%以上。
五、共线电泳,通过调整升压曲线和车架搭摞等措施,实现车身、车架共线生产,从而电泳槽液更新周期加快,有利槽液稳定,实现电泳生产规模效益
总装车间主要从事整车的内外饰、空调、灯具、和仪表等的安装和调试,车间占地面积12288平方米,(三期厂房248米*144米),拥有三条流水生产线,采用间歇移动式地面单板链传输、混流式生产,能灵活应对大巴、中巴以及公交等多种车型的生产需要。
每条生产线按照总装工艺流程分设17个工位。
1、空调:
我公司与苏州同创、扬州杰信、日本电装等国内外知名汽车空调制造商合作开发出不同型号适应不同客户要求的客车专用空调系统,采用环保安全型R134a制冷剂、氮气保压真空加注工艺,顶置式散热器布置,同时在车厢内壁夹层填充环保隔热材料,保证车内温度冬暖夏凉、降低燃料消耗。
2、电器:
电器工位负责安装阅读灯、扬声器、内顶灯等电器设备