COG制备工艺气及气基竖炉直接还原炼铁实验台建设方案Word下载.docx
《COG制备工艺气及气基竖炉直接还原炼铁实验台建设方案Word下载.docx》由会员分享,可在线阅读,更多相关《COG制备工艺气及气基竖炉直接还原炼铁实验台建设方案Word下载.docx(14页珍藏版)》请在冰豆网上搜索。
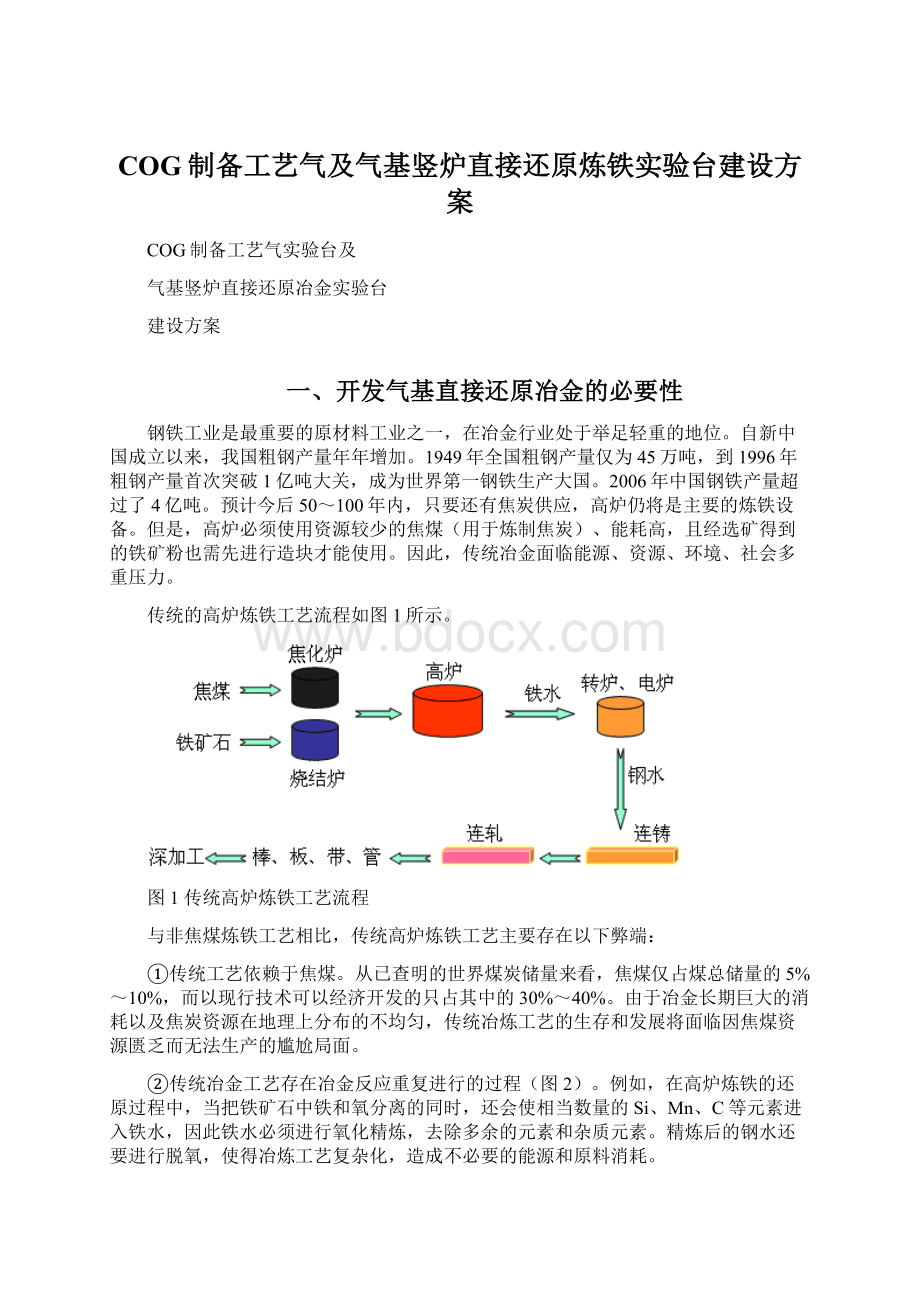
传统的高炉炼铁工艺流程如图1所示。
图1传统高炉炼铁工艺流程
与非焦煤炼铁工艺相比,传统高炉炼铁工艺主要存在以下弊端:
①传统工艺依赖于焦煤。
从已查明的世界煤炭储量来看,焦煤仅占煤总储量的5%~10%,而以现行技术可以经济开发的只占其中的30%~40%。
由于冶金长期巨大的消耗以及焦炭资源在地理上分布的不均匀,传统冶炼工艺的生存和发展将面临因焦煤资源匮乏而无法生产的尴尬局面。
②传统冶金工艺存在冶金反应重复进行的过程(图2)。
例如,在高炉炼铁的还原过程中,当把铁矿石中铁和氧分离的同时,还会使相当数量的Si、Mn、C等元素进入铁水,因此铁水必须进行氧化精炼,去除多余的元素和杂质元素。
精炼后的钢水还要进行脱氧,使得冶炼工艺复杂化,造成不必要的能源和原料消耗。
图2不同工艺钢铁生产过程中含氧量、含碳量的变化示意图
从图2可以看出,传统钢铁生产流程是先将铁矿石过度还原(渗碳)生成铁水,然后再将铁水中的碳通过氧化方法脱除精炼成钢,因此是二步法流程(高炉还原+转炉氧化)。
从氧化-还原基本冶金原理来分析,直接还原法具有直接将铁矿石炼成钢的一步法特征,故称“直接还原”。
③自然界中有用矿物并不都是单独存在的,常有多种金属元素共生的情况。
传统冶炼工艺对复杂的多金属矿处理显得无能为力,从而造成极大的资源浪费。
此外,冶炼厂含有铁、钒、钛、镍等重要资源的粉尘和渣滓,低品位铁矿石,选矿场的残渣等,传统工艺都无法处理。
根据资源特点来选择冶炼方法已势在必行。
④社会发展和科学技术进步对钢材质量要求越来越高。
电炉炼钢技术的迅速发展为优质钢生产提供了有效手段,然而日益增加的合金钢生产和应用,使得多次重复回收的废钢中杂质元素得以富集,严重影响了废钢的质量。
例如,美国在25年内,碳素钢废钢的Cu含量增加了20%,Ni含量增加了1.2倍,Sn含量增加了2倍。
由此可见,用洁净的海绵铁代替被污染的废钢,稀释和改善冶金钢水的化学成分,生产优质钢材已是大势所趋。
⑤传统冶金工厂生产规模大,工艺环节多,需要巨额投资。
建设一座年产200万吨钢的钢铁厂,需要165~250亿人民币的投资,而且必须有足够的原料供应。
而非焦煤冶金厂可小型化,投资相对少,建设周期短,可因地制宜地利用当地的复杂原料和多种能源来确定机动的产品方向,工艺灵活性大、适应性强。
⑥传统工艺中焦化、烧结、高炉等铁前系统产生的大量烟气、粉尘及水污染。
⑦焦化、烧结、高炉等铁前系统的流程长、工艺复杂,导致热效率低,能源浪费严重。
我国能源资源分布格局具有富煤、缺油、少气的特点。
单以丰富的煤炭资源而论,尽管目前已经探明的煤炭储量已超过10000亿吨,但能用于炼制焦炭的焦煤资源还是相对较少。
近年来,随着我国钢铁产量逐年攀升,每年焦煤开采量至少为47425万吨。
按煤炭详查资源总量估计,2070年以后我国的焦煤资源将面临枯竭,传统的焦煤冶金工艺将无法进行正常生产。
与此相反,大量的非焦煤资源在炼铁工艺中却无法得到充分利用,因此开发和采用非焦煤炼铁工艺已迫在眉睫。
非焦煤炼铁工艺是指不使用焦炭进行炼铁生产的各种工艺方法。
按工艺特征、产品类型及用途,可分为直接还原法和熔融还原法两大类别。
直接还原法(DirectReduction)是指“以气体燃料、液体燃料或非焦煤为能源和还原剂,在天然矿石(粉)或人造团快呈固态的软化温度以下进行还原获得金属的方法”。
熔融还原(SmeltingReduction)则“以非焦煤为能源和还原剂,在高温熔融状态下进行金属氧化物的还原,得到含碳的液态金属”。
与直接还原的不同之处是,熔融还原的发展目标只是探索和推广用煤炭代替焦炭的冶炼方法,其产品还是与传统冶炼工艺一样的液态产品,如铁水。
目前,全世界工业规模的直接还原法已有十几种,而大多数熔融还原工艺还处于研发阶段,已商业化的只有COREX。
直接还原法有气基(以CO+H2为还原剂)和煤基(以非焦煤为还原剂)两种。
气基直接还原法因具有容积利用率高、热效率高、生产率高等优点而成为非焦煤冶金工艺的主流技术。
在所有直接还原铁产量中,气基直接还原占到90%以上。
在所有气基DRI工艺中,以天然气为能源的竖炉法生产的直接还原铁占世界总产量的80%以上。
但由于受到天然气资源的限制,我国至今没有一个竖炉法直接还原铁生产工厂,导致每年大量进口昂贵的直接还原铁。
因此,开发替代天然气的气基竖炉直接还原冶金对于解决我国优质钢市场需求强劲、废钢严重短缺、直接还原铁自供严重不足等供需矛盾具有重要意义。
二、我国焦炉煤气利用现状
2.1焦妒煤气综合利用现状
按2001年产焦12406万t计算,全年焦炉煤气产量约为530亿m3。
其中与3000万t土焦相伴产生的约128亿m3煤气在炼焦过程中全部被烧掉,机焦炉产生的煤气则经过净化后,除部分用于焦炉自身加热外,剩余煤气均不同程度地得到了利用。
钢铁联合企业中的焦化厂,绝大部分焦炉均为复热式焦炉,一般采用高炉煤气加热,所产生的焦炉煤气经净化后供给炼铁、炼钢、轧钢等用户。
作为城市煤气气源厂的焦化厂,绝大部分焦炉也为复热式焦炉,可采用焦炉煤气加热,也可采用发生炉煤气加热,所产生的焦炉煤气经净化,达到城市煤气标准后供应城市居民用户或工业用户。
目前,以生产焦炭为主的独立焦化厂,如山西在土焦改机焦过程中新建的许多焦化厂,除少数焦化厂所产的煤气供应城市煤气或工业用途(如锻烧高铝钒土、金属镁等)外,大部分焦化厂的剩余煤气用于发电。
在中国,产生大量剩余焦炉煤气的主要有两类焦化厂:
一是以生产焦炭为主的独立焦化厂,其生产的焦炉煤气既不能供应城市用户,又没有合适的工业用户;
二是目前供应城市煤气用户的焦化厂,如北京焦化厂、天津煤气厂、上海焦化厂等,在采用天然气取代焦炉煤气供应城市煤气用户后,焦炉煤气没有合适的用户。
这些过剩的煤气迫切希望找到经济、合理、高效的综合利用途径。
2.2焦妒煤气综合利用发展思路
焦炉煤气含有H2(55~60%),CH4(23~27%),CO(5~8%),CO2(1.5~3.0%),N2(3~7%),O2(<
0.5%),CmHn(2~4%),密度为0.45~0.50Kg/Nm3,低位发热量17900KJ/Nm3。
焦炉煤气的主要成分是H2、CH4和CO,因此,它不仅是优质的气体燃料,还是理想的化工合成原料。
基于此,焦炉煤气的综合开发利用也应从燃料和化工原料两条思路上考虑。
(1)开发利用煤气的联合工业用户
焦炉煤气作为洁净的气体燃料,若用于生产水泥、建材、耐火材料,可大大提高产品的质量和品位。
如山西菜焦化厂利用自产的焦炉煤气焙烧高铝钒土,利用焙烧高铝钒土的余热生产蒸汽供全厂蒸汽用户,不仅提高了产品质量,扩大了市场,还实现了能源的综合利用,降低了生产成本。
(2)开发以焦炉煤气为原料的化工合成项目
焦炉煤气是制造合成氨的理想原料。
氢气是合成氨的直接原料气,焦炉煤气中含有55%一60%的氢气,其它成分如甲烷、一氧化碳等,可经转化、变换、脱碳等工序制得纯氢气,然后氢气与氮气合成氨。
近年来,随着变压吸附制氢技术的推广应用,使焦炉煤气制合成氨的投资和电耗进一步降低。
山西焦化集团从20世纪70年代建厂时就配套建成了焦炉煤气合成氨装置,并生产尿素。
焦炉煤气同样是合成甲醇、二甲醚的理想原料,其本身含有生产甲醇和二甲醚的原料气H2和CO。
焦炉煤气经过部分氧化蒸汽转化后,气体中H2/CO=3.0,接近合成甲醇和二甲醚的最佳值(H2/CO=2.05~2.15)。
而以煤和重油为原料生产甲醇和二甲醚时,由于氢碳比偏低,变换、脱碳装置流程长/投资大。
甲醇不仅是一种重要的基础有机化工原料,而且可加入汽油掺烧或代替汽油作为动力燃料。
目前山西省开发的以甲醇为燃料的清洁燃料汽车已成功投入使用。
山西省正在筹建以焦炉煤气为原料的甲醇生产基地。
二甲醚具有优良的混溶性,易溶于汽油和水,可替代柴油用作清洁汽车燃料,也可替代液化气用作民用燃料,其发展前景被普遍看好。
(3)焦炉煤气用于制氢
焦炉煤气是制氢的理想原料,其所含的55%一60%的氢气可通过变压吸附法生产纯度为99.9%或更高的氢气。
氢气是化学工业合成的重要原料气之一,还是化学工业中常用的还原剂和氢化剂。
在电子工业中,氢是制取半导体材料——硅的重要原料。
气象上用于探空气球。
氢已成为运载火箭航天器的重要燃料之一。
可达到零排放的无污染高效氢燃料电池动力汽车已投入试验运行,世界各大汽车公司已陆续推出该类型汽车样车。
氢能的应用范围今后必将不断扩大。
(4)焦炉煤气甲烷化供城市煤气用户
对目前供应城市煤气用户的独立焦化厂,在天然气进入城市后,也可对焦炉煤气进行甲烷化,将其热值提高后掺入天然气管网供应城市煤气用户。
(5)焦炉煤气发电
焦炉煤气哲时没有合适用途时,也可用来发电。
焦炉煤气用于电厂锅炉时,其热效率可达90%,利用锅炉生产蒸汽发电,发电后的蒸汽还可供焦化厂生产用。
焦炉煤气也可直接用于燃气透平机发电。
中国利用航空发动机自动研制的焦炉煤气透平发电机已在陕西焦化厂及究州矿务局焦化厂得到成功应用。
(6)焦炉煤气用于直接还原铁
钢铁联合企业中,焦化厂生产的含有大量H2和CO的焦炉煤气本身就是还原性气体,将焦炉煤气送入热裂解炉中,其中CH4经加氧催化裂解,即可得到含H274%、CO25%的还原性气体,可直接送入气基竖炉生产直接还原铁。
由此而促成的高炉一直接还原铁一焦炉的联合流程是高炉流程工艺技术的自身完善,是钢铁生产向短流程过渡的重要发展方向。
墨西哥HYLSA公司详细比较分析了利用焦炉煤气发电和利用焦炉煤气生产直接还原铁的经济性。
见图3。
图3焦炉煤气用于发电和用于冶炼直接还原铁的经济性比较
因此,从经济性角度看,焦炉煤气用于生产直接还原铁明显好于发电。
焦炉煤气热值按16746KJ/Nm3计算,不计电耗、水耗等,吨DRI能耗9.97GJ/t。
三、焦炉煤气用于气基竖炉直接还原炼铁原理
参照墨西哥HYLSA公司HYL-ZR工艺,焦炉煤气用于气基竖炉直接还原炼铁的结构图如图4所示。
其中合成气既可由焦炉煤气制备,也可通过天然气蒸汽转化、煤制气等方法制备。
图4焦炉煤气用于气基竖炉直接还原炼铁的结构图
由图4可知,气基竖炉直接还原炼铁工艺主要由以下部件或子系统组成:
⑴竖炉、⑵工艺气制备子系统、⑶工艺气增湿器、⑷工艺气加热器、⑸氧气供给子系统(合成气中含有甲烷时才需要)、⑹炉顶气换热器、⑺炉顶气激冷/洗涤系统、⑻H2O脱除器、⑼CO2脱除器、⑽工艺气循环压缩机、⑾直接还原铁冷却子系统、⑿辅助公用设施等。
核心设备是竖炉。
在竖炉的还原带,铁矿石首先通过热的还原气的热量传递预热到还原过程所需的温度水平。
预热阶段过后,还原气H2和CO与氧化铁还原反应,矿石中的氧被去除。
还原反应的机理包括还原剂气体在反应界面的吸附催化、固相层内离子和电子的扩散、新相核的形成及长大等。
还原过程的机理可描述为:
其中氢还原反应过程为:
CO还原反应过程为:
冷却过程的渗碳反应为:
四、气基竖炉直接还原炼铁实验台建设方案
由图4可知,气基竖炉直接还原炼铁过程是一个非常复杂的系统,其中多项核心、关键技术掌握在国外大公司手里。
直接还原冶金技术的进步经历了一个漫长、耗资巨大的发展过程。
开始提出的直接还