钻孔灌注桩首件认可总结Word文档格式.docx
《钻孔灌注桩首件认可总结Word文档格式.docx》由会员分享,可在线阅读,更多相关《钻孔灌注桩首件认可总结Word文档格式.docx(14页珍藏版)》请在冰豆网上搜索。
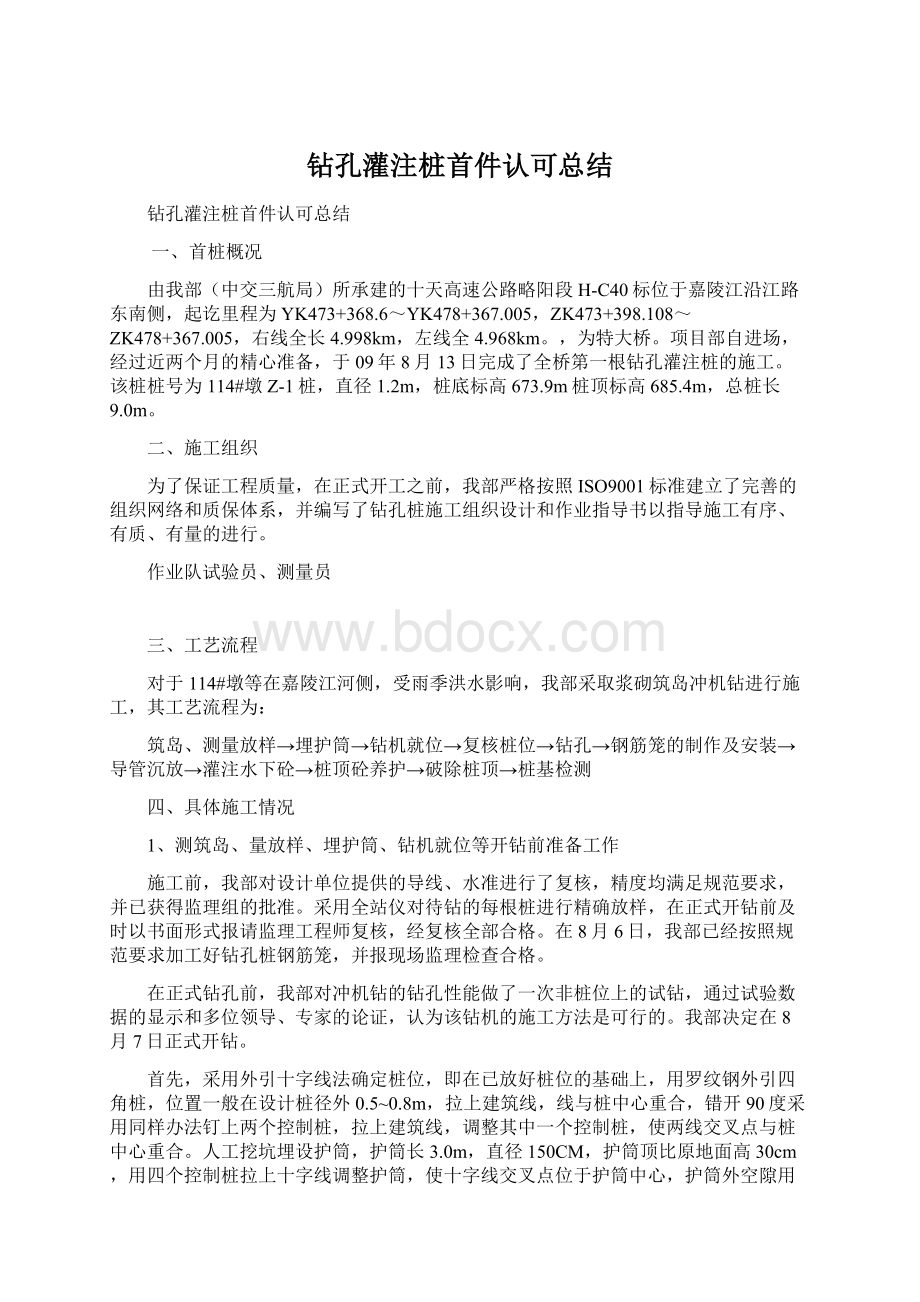
施工前,我部对设计单位提供的导线、水准进行了复核,精度均满足规范要求,并已获得监理组的批准。
采用全站仪对待钻的每根桩进行精确放样,在正式开钻前及时以书面形式报请监理工程师复核,经复核全部合格。
在8月6日,我部已经按照规范要求加工好钻孔桩钢筋笼,并报现场监理检查合格。
在正式钻孔前,我部对冲机钻的钻孔性能做了一次非桩位上的试钻,通过试验数据的显示和多位领导、专家的论证,认为该钻机的施工方法是可行的。
我部决定在8月7日正式开钻。
首先,采用外引十字线法确定桩位,即在已放好桩位的基础上,用罗纹钢外引四角桩,位置一般在设计桩径外0.5~0.8m,拉上建筑线,线与桩中心重合,错开90度采用同样办法钉上两个控制桩,拉上建筑线,调整其中一个控制桩,使两线交叉点与桩中心重合。
人工挖坑埋设护筒,护筒长3.0m,直径150CM,护筒顶比原地面高30cm,用四个控制桩拉上十字线调整护筒,使十字线交叉点位于护筒中心,护筒外空隙用土填实,使护筒牢固,再将十字线引到护筒上,用锯条在护筒上锯一小口,连上绑丝,这样即使四角桩因施工不慎位移,也不影响十字线中心,便于下笼与桩位中心对正。
然后,将冲机钻移动到桩位处,调整钻机钻杆垂直于地面,钻头中心对准桩中心。
护筒埋好钻机就位后后,测得其护筒顶标高为:
689.25m,根据桩底标高673.9m推算,应钻到护筒顶向下15.35m才能满足桩长要求。
最后,在114#墩—115号墩中间挖一泥浆循环池、沉淀池、挖排浆沟槽。
2、钻孔
8月7日8:
00分正式开钻。
钻进前,控制桩上拉上十字线,钻头中心尖对准十字交叉点,将钻头缓缓放入护筒内,开始钻进,随钻进用11KW泥浆泵将泥浆池中配制好的泥浆(主要采用膨润土、纯碱、纤维素和水按照0.15:
0.04:
0.002:
1比例调制而成,泥浆的比重控制在1.3左右)补充到孔中,浆面保持在距护筒顶面0.5m左右。
沟槽边派专人负责用铁锹向下游波动泥浆,以防泥浆在沟槽内沉淀。
泥浆流入泥浆池中后泥浆坑中,将泥浆采用静置沉淀法进行固液分离,分离出的净水重复利用或直接排入河中。
钻机取上的渣土用装载机随时清理出场地外。
大约在8月12日20:
30,经测试人员测深为:
16.60m,泥浆比重1.38,已超过了设计深度,至此钻孔结束。
3、清孔:
清孔之后泥浆比重为:
1.08、含砂率:
0.7%、粘度:
19Pa.s
4、钢筋笼安装:
清孔后钻机自行移走,钢筋笼分两节制作,骨架每节长度:
8m+2.375m,焊接采用采用双面焊,设计总长10.25m,实际量测长度过10.25(焊缝长度120mm)。
耳筋采用二级钢直径16布在加强筋四周,声测管3根用铁丝绑牢在加强筋上,现场质检人员检查,监理复查,其焊接长度和质量完全满足规范要求。
用小车托运到现场,16吨汽车起重机就位开始吊放钢筋笼。
吊筋:
采用四根二级钢直径16长5.005m(20cm焊接长),对称焊在笼顶控制笼顶标高684.245,至15:
00左右,钢筋笼安装结束。
我部迅速组织人员沉放导管导(导管水密及抗拉试验合格):
导管长1*4m+2.0*6m+1*0.5m。
5灌注前的准备工作
水下混凝土的搅拌采用2台JB1000型拌合机组成的拌和楼拌和,出料能力为20m3/h,混凝土的运输采用4辆10m3的搅拌车运输。
灌注混凝土,应连续进行,不得中断。
首批砼应满足初次导管埋深(≥1.0m)和填充导管底部间隙需要根据计算。
计算公式如下:
式中:
V——灌注首批混凝土所需数量(m3);
D——桩孔直径(m);
H1——桩孔底至导管底端间距,一般为0.4m;
H2——导管初次埋置深度(m);
d——导管内径(m);
h1——桩孔内混凝土达到埋置深度H2时,导管内混凝土柱平衡导管外(或泥浆)压力所需的高度(m),即H1=/;
、、,根据上式计算本工程1.5米桩首批砼不少于2.40方(导管直径250mm)。
灌注采用混凝土拌和站拌料,两辆搅拌运输车运送。
按设计要求为C25砼,其配比为:
1:
0.33:
1.98:
2.88:
0.008。
该混凝土和易性、粘聚性良好,塌落度为190mm,满足设计要求。
6、砼灌注
至18:
00左右准备工作结束,测量人员测得孔深为:
16.65m,深度超过设计要求,沉淀层厚度只有0.02m,泥浆比重仍为1.08,含砂率0.7%,粘度19Pa.s,已经符合灌注条件,经现场监理复核后,开始拌制混凝土。
18:
36分,开启阀门,导管悬高40cm,放下第一斗混凝土,测得导管埋深4.9m,满足规范要求的首次导管埋深大于1.0m的要求。
在其后的灌注中,除了后场搅拌车的机械故障外,浇筑基本正常,埋深控制在2~6m左右。
至19:
38,浇筑到标高683.6m,超灌0.7m,至此灌注结束,设计砼方量12.37m3,实灌方量15.5m3,扩孔系数为1.25,第一根钻孔桩顺利完成。
五、质量小组具体措施:
根据以往经验,结合本项目的特点,小组针对冲击钻对可能发生的问题进行了提前论证,并制定了预控措施,如下所示:
制图人:
刘红军
5.1其它常见质量问题及预控处理措施
5.1.1地质勘探资料和设计文件存在的问题与处理措施
地质补充勘探资料主要存在地质柱状图各不同地层层厚与实际不符,而设计是以地质补勘资料为依据的。
处理措施:
在钻进过程中每进尺2米捞取渣样并做好记录同时与补勘地质图做比较,如差别较大(持力层层厚相差2米以上),及时上报监理、业主、设计方再做现场确定。
5.1.2钻孔深度的误差
钻孔的终孔标准应以桩端进入持力层深度为准,不宜以固定孔深的方式终孔。
因此,钻孔到达桩端持力层后应及时取样鉴定,确定钻孔是否进入桩端持力层。
终孔标准不仅参照设计桩底标高、设计桩长,还要以设计终孔原则结合现场实际来定。
5.1.3钻孔垂直度不符合规范要求
造成钻孔垂直度不符合规范要求的主要原因如下:
(1)、场地平整度和密实度差,钻机安装不平整或钻进过程发生不均匀沉降,导致钻孔偏斜。
(2)、钻进遇软硬土层交界面或倾斜岩面时,高速冲击钻进使钻锥受力不均,造成钻锥偏离方向。
控制钻孔垂直度的主要技术措施为:
(1)、压实、平整施工场地。
(2)、在软硬土层交界面或倾斜岩面处钻进,应小冲程钻进。
发现钻孔偏斜,应及时回填片石,冲平后再低速冲击钻进。
5.1.3桩端持力层判别错误
持力层判别是钻孔桩成败的关键,现场施工必须给予足够的重视。
对于非岩石类持力层,判断比较容易,可根据地质资料的深度,结合现场取样进行综合判定。
处理措施:
对于桩端持力层为微风化岩或中风化岩的桩,判定岩层界面难度较大,可采用以地质资料的深度为主要参考,结合钻锥的受力、进尺情况和孔口捞样进行综合判定。
5.1.4孔底沉渣过厚或开灌前孔内泥浆含砂量过大
孔底沉渣过厚除清孔泥浆质量差,清孔无法达到设计要求外,还有测量方法不当造成误判。
要准确测量孔底沉渣厚度,首先应准确测量桩的终孔深度。
在含砂、砂砾的地层钻孔,当采用正循环清孔时,前阶段应采用高粘度浓浆清孔,并加大泥浆泵的流量,使砂石粒能顺利地浮出孔口。
孔底沉渣厚度符合设计要求后,应把孔内泥浆密度降至1.1~1.2g/cm3。
清孔整个过程应专人负责孔口捞渣和测量孔底沉渣厚度,及时对孔内泥浆含砂率和孔底沉渣厚度的变化进行分析,若出现清孔前期孔口泥浆含砂量过低,捞不到粗砂粒,或后期把孔内泥浆密度降低后,孔底沉渣厚度增大较多。
则说明前期清孔时泥浆的粘度和稠度偏小,砂粒悬浮在孔内泥浆里,没有真正达到清孔的目的,施工时应特别注意这种情况。
5.1.5初灌时埋管深度达不到规范值
我国《公路桥涵施工技术规范》JGJ041-2000规定,灌注导管底端至孔底的距离一般为400mm,初灌时导管埋深应≥1000mm。
在计算砼的初灌量时,有时只计算了1.4m桩长所需的砼量,漏算导管内积存的砼量,初灌量不足造成埋管深度达不到规范值。
另一方面,有时导管低至孔底的距离偏大,而导管安装人员没有及时把实际距离通知砼灌注班,形成初灌量不足导致埋管深度达不到规范值。
初灌砼量V应根据设计桩径、导管管径、导管安装长度、孔内泥浆密度进行计算,且V≥V0+V1。
V0为1.4m桩长的砼量,V0=1.2×
1.4πD2/4(单位:
m3);
1.2-桩的理论充盈系数;
D-设计桩径(m)。
V1为初灌时导管内积存的砼量,V1=(hπd2/4)(ρ+0.55πd)/2.4(单位:
h-导管安装长度(m);
d-导管直径(m);
ρ-孔内泥浆密度(t/m3);
0.55-导管内壁的摩阻力系数;
2.4-砼的密度(t/m3)。
5.1.6灌注砼时堵管
灌注砼时发生堵管主要是灌注导管破漏、灌注导管底距孔底深度太小、完成二次清孔后灌注砼的准备时间太长、砼配制质量差、灌注过程灌注导管埋深过大等原因引起。
灌注导管在安装前应有专人负责检查,可采用肉眼观察和敲打听声相结合的方法进行检查,检查项目主要有灌注导管是否存在小孔洞和裂缝、灌注导管的接头是否密封、灌注导管的厚度是否合格。
必要时采用试拼装压水的方法检查导管是否破漏。
灌注导管底部至孔底的距离应为300~400mm,在灌浆设备的初灌量足够的条件下,应尽可能取大值。
隔水栓应认真细致制作,其直径和园度应符合使用要求,其长度应≤200mm。
完成第二次清孔后,应立即开始灌注砼,若因故推迟灌注砼,应重新进行清孔。
否则,可能造成孔内泥浆悬浮的砂粒下沉而使孔底沉渣过厚。
5.1.7灌注砼过程钢筋笼上浮
引起灌注砼过程钢筋笼上浮的原因主要有如下三方面:
(1)、砼初凝和终凝时间太短,使孔内砼过早结块,当砼面上升至钢筋笼底时,砼结块托起钢筋笼。
(2)、清孔时孔内泥浆悬浮的砂粒太多,砼灌注过程中砂粒回沉在砼面上,形成较密实的砂层,并随孔内砼逐渐升高,当砂层上升至钢筋笼底部时便托起钢筋笼。
(3)、砼灌注至钢筋笼底部时,灌注速度太快,造成钢筋笼上浮。
若发生钢筋笼上浮,应立即查明原因,采取相应措施,防止事故重复出现。
5.1.8桩身砼强度低或砼离析
发生桩身砼强度低或砼离析的主要原因是施工现场砼配合比控制不严、搅拌时间不够和水泥质量差。
严格把好进库水泥的质量关,控制好施工现场砼配合比,掌握好搅拌时间和砼的和易性,是防止桩身砼离析和强度偏低的有效措施。
5.1.9桩身砼夹渣或断桩
引起桩身砼夹泥或断桩的原因主要有如下四方面:
(1)、初灌砼量不够,造成初灌后埋管深度太小或导管根本就没有入砼内。
(2)、砼灌注过程拔管长度控制不准,导管拔出砼面。
(3)、砼初凝和终凝时间太短,或灌注时间太长,使砼上部结块,造成桩身砼夹渣。