材料成型工艺考试复习题目及答案Word格式文档下载.docx
《材料成型工艺考试复习题目及答案Word格式文档下载.docx》由会员分享,可在线阅读,更多相关《材料成型工艺考试复习题目及答案Word格式文档下载.docx(11页珍藏版)》请在冰豆网上搜索。
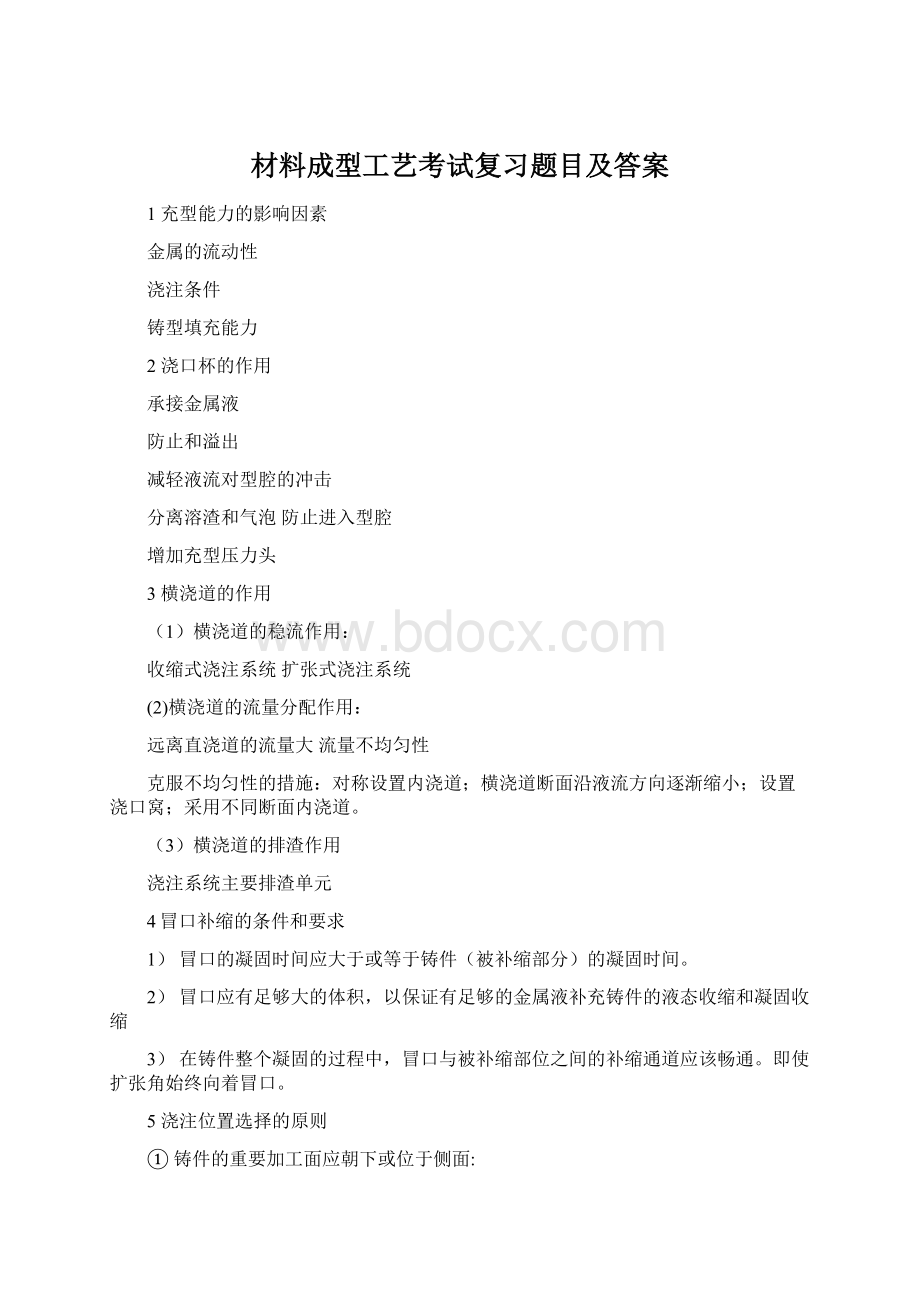
浇注系统主要排渣单元
4冒口补缩的条件和要求
1)冒口的凝固时间应大于或等于铸件(被补缩部分)的凝固时间。
2)冒口应有足够大的体积,以保证有足够的金属液补充铸件的液态收缩和凝固收缩
3)在铸件整个凝固的过程中,冒口与被补缩部位之间的补缩通道应该畅通。
即使扩张角始终向着冒口。
5浇注位置选择的原则
①铸件的重要加工面应朝下或位于侧面:
②铸件宽大平面应朝下:
③面积较大的薄壁部分应置于铸型下部或垂直:
④易形成缩孔的铸件,较厚部分置于上部或侧面:
⑤应尽量减少型蕊的数量:
⑥要便于安放型蕊、固定和排气:
6湿型砂的组成及性能要求
原砂(或旧砂)100粘土(膨润土)1-5%煤粉少于8%水分少于6%以及其它附加物
1)
紧实率和含水量
湿型砂不可太
干,因为干的型砂虽然流动性极好,但是型砂中膨润土未被充分润湿,性能较为干脆,起模困难,砂型易碎,表面的耐磨强度低,铸件容易生成砂孔和冲蚀缺陷。
型砂也不可太湿,否则型砂太粘,造型时型砂容易在砂斗中搭桥和降低造型流动性,还易使铸件产生针孔、气孔、呛火、水爆炸、夹砂、粘砂等缺陷。
一是紧实率,代表型砂的手感干湿程度;
另一是含水量,代表型砂的实际水分含量。
2_)
透气率
砂型的排气能力除了靠冒口和排气孔来提高以外,更要靠型砂的透气率。
因此砂型的透气率不可过低,以免浇注过程中发生呛火和铸件产生气孔缺陷。
3)
常温湿态强度
湿型砂必须具备一定强度以承受各种外力的作用。
4)湿压强度
一般而言,欧洲铸造行业对铸铁用高密度造型型砂的的湿压强度值要求较高。
5)
湿拉强度和湿劈强度
从材料力学角度来看,抗压强度只是在一定程度上代表型砂中膨润土膏的粘结力,同时又反映受压应力时砂粒之间的摩擦阻力,因而不能用湿压强度值直接说明型砂的粘结强度的好坏,而抗拉强度就无此缺点。
6)
湿剪强度
湿剪强度比湿压强度较能表明型砂的粘结力而且容易测定,将普通的标准试样放置在强度试验机的两块具有半面凸台的压头之间,沿中心轴方向施加剪切力,即可测定出剪切强度。
7)
型砂含泥量
型砂和旧砂的泥分是由两部分组成。
8)型砂粒度
型砂粒度直接影响透气性和铸件表面粗糙程度。
9)
有效膨润土量
一般湿型铸造生产中,都是根据型砂的湿态抗压强度高低补加膨润土量。
10
)型砂的有效煤粉量
生产铸铁件的湿型砂大多加入煤粉附加物,每次混砂时需补加少量煤粉。
11)型砂韧性
型砂不可太脆,应当具有一定的韧性。
12)
起模性
型砂的起模性是一个极其复杂的综合特性
13)抗夹砂性(热湿拉强度)
用湿型砂浇注较厚大的平板类铸件时,最容易产生夹砂类缺陷(包括起皮、沟痕、结疤、鼠尾)
14)型砂的颗粒在外力作用下可以紧密靠近的性能称为可紧实性。
具有良好可紧实性的型砂能够保证砂型表面密实。
7各种铸造缺陷产生的原因
1)砂眼:
型砂强度不够或局部没有冲紧型腔,浇口内散砂未吹干净合箱时砂型局部挤坏掉砂浇注系统不合理冲坏砂型
2)冷隔:
浇注温度过低浇注速度太慢浇口位置不当或浇口太小
3)粘砂:
未刷涂料或涂料太薄浇注温度过高型砂耐火隆不够
4)夹砂:
型砂强度太低浇注温度过高内浇口过于集中使局部型砂烘烤历害
5)裂纹:
铸件设计不合理壁厚差别太大砂型退让性差阻碍铸件收缩浇注系统不当使铸件各部分冷却收缩不均匀造成过大的内应力
7浇注系统的分类
根据各单元断面积比例收缩式扩张式半扩张式
根据金属液导入型腔位置顶注式底注式中注式阶梯式
、
8压铸和低压铸造的区别
低压铸造组织致密,力学性能较好,但生产率较低。
而压力铸造生产率高,适宜于薄壁铸件,但铸件中缩松,不致密,不使用于气密性要求高的铸件。
低压是反重力铸造的一种方法,成型过程平稳,铸件中的气孔比较少.而压力铸造是一种高速成型过程,流速比较快,用于薄壁件较多
9铸造加热的目的
最主要的就是为了避免和防止不加热没法使用的现象!
为了保护人身安全模具安全;
保护模具寿命;
防止、减少铸造缺陷;
便于喷涂涂料;
减小包紧力;
提高金属液充型能力;
10锻模飞边槽的作用
1.造成足够大的横向阴力迫使金属充满模膛
2.容纳坯料上的多余金属。
起补偿与调节的作用
3.对于锤类设备上锻模缓冲模具撞击提高锻模寿命
11闭式模锻的特点
1锻件不产生飞边模锻斜度很小甚至为零材料利用率高
2变型金属处于更加强大的三向压应力状态可提高材料的塑性和机械性能
3可分凹模闭式精锻常常可减少甚到取消制坯工步省去切边和辅助工序平均提高生产率25-50%
主要问题:
对于一些大中型锻件模具寿命低
12模膛的分类
制坯模膛
模锻模膛预锻模膛
终锻模膛
13挤压变形金属的流动情况
正挤压:
金属的流动方向跟挤压杆的运动方向相同的挤压生产方法
特征:
变形金属与挤压筒壁间有较大的滑动摩擦引起挤压力增大金属变形流动不均匀
导致组织性能不均匀,限制了挤压速度提高加速工模具的磨损
反挤压:
金属的流动方向跟挤压杆的相对运动方向相反的挤压生产方法。
变形金属与挤压筒间无相对摩擦,挤压力小,金属变形流动均匀,挤压速度快。
但制品表面较正挤压差,外接圆尺寸较小,设备造价较高,辅助时间较长。
14拉深的系数及缺陷
拉深系数:
每次拉深后圆筒形件的直径d与拉深前毛坯直径D之比
拉深比=1*
拉深系数反应圆筒形件拉深的变形程度。
拉深系数越小拉深变形程度越大
缺陷:
起皱和拉裂还有凸耳和残余应力
15冲裁时板料分离过程
随着凸模继续压入材料己经出现的上下裂纹逐渐向金属内层扩展延伸当裂纹相遇重合时材料即被剪断完成分离过程
:
侧向压力一定小于垂直压力而在压力小的地方裂纹更易产生和扩展,因此冲裁时初使裂纹从模具刃口侧面产生之后迅速扩展完成分离。
16铸造纤维组织的性能及设计
17冲裁模的尺寸要求
冲裁模合理尺寸是由凸模凹模刃口尺寸及其公差决定的。
实际冲裁中;
’
1.落料冲孔件的切断面都带有斜度,即在同一切断面有大端小端尺寸
2.落料件的大端尺寸与凹模尺寸接近冲孔件小端尺寸与凹模尺寸接近。
在测量和使用冲裁件时落料件是以大端为基准冲孔件以小端为基准
3.冲裁生产过程中凸凹模磨损的结果是使间隙增大
重要概念
1盒法造型:
是用液态热固性树脂粘结剂和催化剂制成的芯砂,吹射入被加热到一定温度的芯盒内(芯盒温度为180—250)贴近芯盒表面的砂芯受热,其粘结剂在很短时间即可缩聚而硬化。
2自硬冷芯盒法造型:
将原砂,液态树脂及液态催化剂混合均匀后填充到芯盒(或砂箱)中,稍紧实即于室温下在芯盒内(或砂箱)内硬化成形,称为自硬冷芯盒法制芯
3熔模铸造:
(又称精密铸造或失蜡铸造)用易熔材料制成模型,然后在模型上涂挂耐火材料,硬化之后再将模型熔化,排出型外,从而获得无分型面的铸型
4消失模铸造:
(又称气化模铸造或实型铸造)它是采用泡沫塑料模样代替普通模样紧实造型,造好造型后不取出模样,直接浇入金属液,在高温金属液的作用下,模样受热气化,燃烧而消失,金属液取代原来泡沫塑料模样占据空间位置,冷却凝固后即获得所需的铸件。
5计算毛坯:
长轴类锻件终锻前,最好将原毛坯沿轴向预制成各截面面积等于带飞边锻件的相应截面积的中间毛坯,以保证终锻时锻件各处充填饱满且飞边均匀从而节约金属
减轻锻模模膛磨损。
按照上述要求计算的坯料,称为计算毛坯。
6应力中性层:
在毛坯截面上的应力由外层的拉应力过渡到内层的压应力时中间有一层金属切向应力为零或不连续称为应力中性层。
7应变中性层:
板料弯曲时外层纤维受拉内层纤维受压在拉深与压缩之间必然有一层金属长度不变。
这层金属称为应变中性层。
8冲孔连皮:
模锻不能直接锻出透孔,因此在设计热锻件图时必须在孔内保留一层连皮,然后在切边压力机上冲除掉。
重要原理
1最小允许壁厚的作用及影响因素
在一定铸造条件下,铸造合金液能充满铸型的最小厚度称为该铸造合金的最小厚度。
为了避免铸件的浇不足和冷隔等缺陷,铸件的设计壁厚不应小于最小壁厚。
最小壁厚主要由合金种类和铸件尺寸大小决定。
由于厚壁铸件易产生缩孔,缩松,晶粒粗大,偏析等缺陷,铸件的力学性能下降。
设计厚大铸件时,要避免以增加壁厚的方式提高强度。
砂型铸造各种铸造合金铸件的临界壁厚可按其最小壁厚的3倍考虑。
2预锻模膛和终锻模膛的作用
预锻的主要目的是在终锻前进一步分配金属。
分配金属是为了:
确保金属无缺陷流动,易于充填模膛:
减少材料流向飞边槽的损失:
减少终锻模膛磨损:
取得所希望的金属流线和便于控制锻件的力学性能。
但采用预锻模膛也会带来不利影响,容易造成偏心打击,影响锤杆的寿命,容易使上下模错移,增大模块尺寸,降低生产率。
终锻模膛用于锻件最终成形。
它由按热锻件图加工制造的模膛和模膛周围的飞边槽所组成。
为了便于操作,一般没有钳口。
3冲裁凸凹模与拉深凸凹模的区别
冲裁模的凸凹模间隙对冲裁件断面有很大的影响
合理间隙——能够使断面质量、尺寸精度、模具寿命和
冲裁力等方面得到最佳效果的间隙。
合理间隙的确
定是冲裁工艺及模具设计的关键问题。
合理间隙值的确定方法有理论确定法和经验确定法。
当冲裁件断面质量和尺寸精度要求较高时,则采用
推荐的较小间隙值。
当冲裁件质量要求不高时则以降低冲裁力、提高模
具寿命为主要考虑因素,采用较大的间隙值。
落料冲孔件的切断面都带有斜度,即在同一切断面有大端小端尺寸
落料件的大端尺寸与凹模尺寸接近冲孔件小端尺寸与凹模尺寸接近。
冲裁生产过程中凸凹模磨损的结果是使间隙增大。
拉深凸凹模圆角半径及间隙对圆筒件拉深的影响
合理选择圆角半径及半径是避免导致产品质量缺陷和拉深工艺失败的关键环节
4硅溶胶型壳出现壳鼓和裂纹的原因
干燥不良的型壳质量不好,因为这类型壳的硅溶胶还未转变成凝胶,或者刚胶凝尚含有较多溶剂,马上涂挂下一层必然会发生冻胶回溶现象或者吸收下层溶胶引起型壳溶胀,剥落,掉砂,甚至使制壳工艺无法进行下去。
干燥过程中,随着溶剂的蒸发,型壳将发生收缩,若各部分干燥不均匀,收缩不一致,就会形成内应力而导致开裂。
5横锻斜度和圆角半径的作用?
为什么不锻出通孔?
模锻斜度的作用是使锻件能顺利从模膛中取出。
圆角半径:
外圆角作用是避免锻模在热处理和模锻过程中因应力集中而导致模具开裂,并保证金属能充满此处。
内圆角作用是使金属易于流动充填深腔,防止锻件在筋部产生折叠,也防止模膛中较窄的凸出部分压塌。
分模面的确定原则:
(1)模锻件的最大截面处,且最好为平直面;
(2)使上、下两模沿分模面的模膛轮廓一致;
(3)使模腔深度最浅;
(4)