汽车设计流程及相关设计软件Word格式.docx
《汽车设计流程及相关设计软件Word格式.docx》由会员分享,可在线阅读,更多相关《汽车设计流程及相关设计软件Word格式.docx(10页珍藏版)》请在冰豆网上搜索。
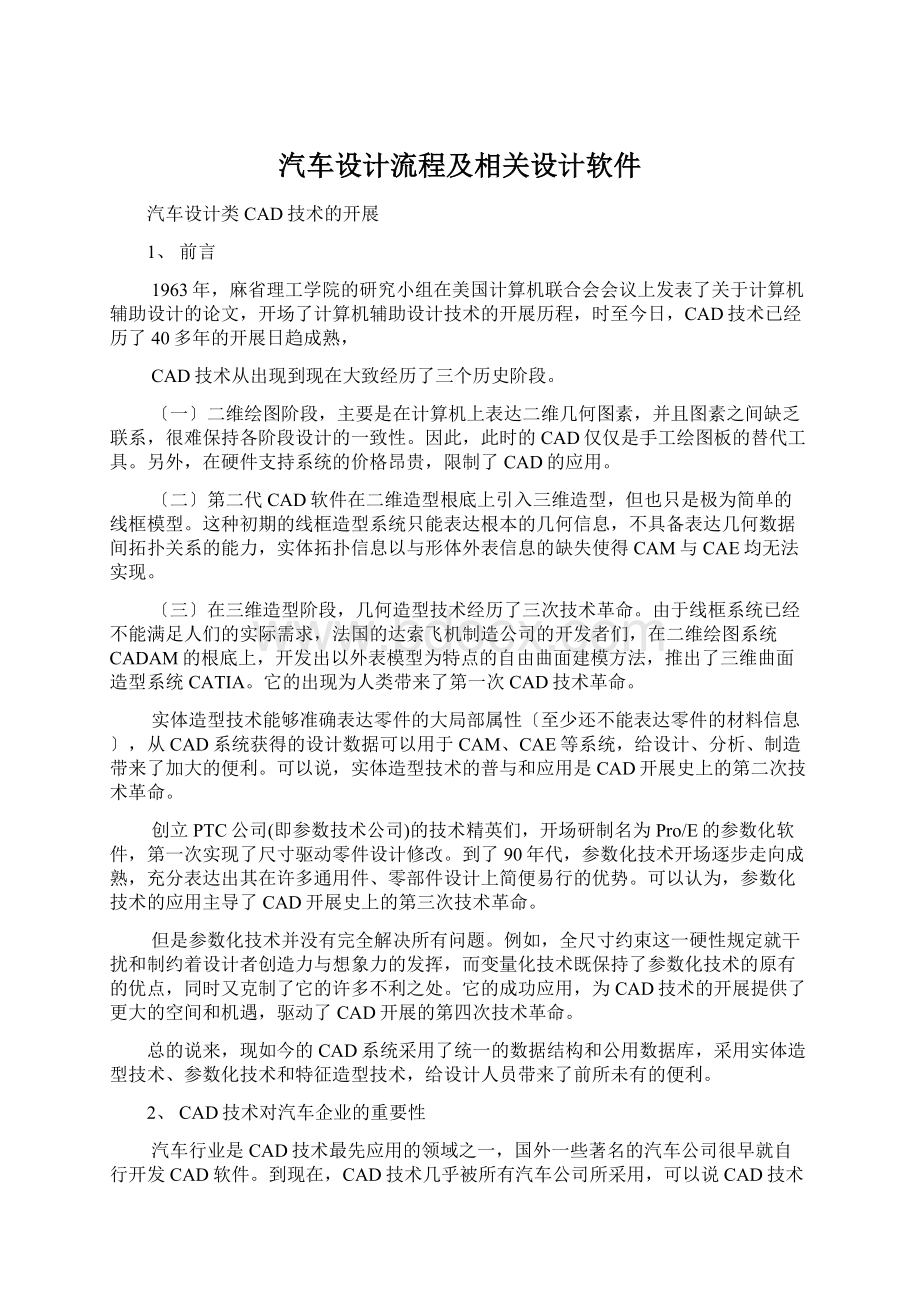
〔三〕在三维造型阶段,几何造型技术经历了三次技术革命。
由于线框系统已经不能满足人们的实际需求,法国的达索飞机制造公司的开发者们,在二维绘图系统CADAM的根底上,开发出以外表模型为特点的自由曲面建模方法,推出了三维曲面造型系统CATIA。
它的出现为人类带来了第一次CAD技术革命。
实体造型技术能够准确表达零件的大局部属性〔至少还不能表达零件的材料信息〕,从CAD系统获得的设计数据可以用于CAM、CAE等系统,给设计、分析、制造带来了加大的便利。
可以说,实体造型技术的普与和应用是CAD开展史上的第二次技术革命。
创立PTC公司(即参数技术公司)的技术精英们,开场研制名为Pro/E的参数化软件,第一次实现了尺寸驱动零件设计修改。
到了90年代,参数化技术开场逐步走向成熟,充分表达出其在许多通用件、零部件设计上简便易行的优势。
可以认为,参数化技术的应用主导了CAD开展史上的第三次技术革命。
但是参数化技术并没有完全解决所有问题。
例如,全尺寸约束这一硬性规定就干扰和制约着设计者创造力与想象力的发挥,而变量化技术既保持了参数化技术的原有的优点,同时又克制了它的许多不利之处。
它的成功应用,为CAD技术的开展提供了更大的空间和机遇,驱动了CAD开展的第四次技术革命。
总的说来,现如今的CAD系统采用了统一的数据结构和公用数据库,采用实体造型技术、参数化技术和特征造型技术,给设计人员带来了前所未有的便利。
2、CAD技术对汽车企业的重要性
汽车行业是CAD技术最先应用的领域之一,国外一些著名的汽车公司很早就自行开发CAD软件。
到现在,CAD技术几乎被所有汽车公司所采用,可以说CAD技术〔包括计算机辅助制造、计算机辅助工程分析〕的应用水平,已经成为评价一个国家汽车工业水平的重要指标。
在我国,汽车企业一直都作为国家和地方的利税大户,同时也是CAD技术应用的先锋。
CAD技术在企业中的成功应用,不仅带来了企业技术上的创新,同时带动了企业经营、管理旧模式的变革。
因此,它对我国传统产业的改造、新技术的兴起,以与汽车工业提高国际竞争力等方面,起到了巨大的推动作用。
传统的汽车车身设计方法的整个过程是基于手工设计完成的,其特点是整个过程是通过实物、模型、图纸、样板等来传递信息。
随着计算机技术的开展,计算机逐步代替人脑承当起复杂的计算和分析,同时引进CAD等现代设计方法,帮助工程师们抛掉传统的手工方式,既方便设计,又能改善设计质量,缩短设计周期。
因此,国外著名汽车公司都不惜花巨资实施CAD技术,一方面加快新车型上市的速度满足复杂多变的市场需求,另一方面节省开发本钱,向消费者提供物美价廉、物超所值的产品,从而提高自身市场竞争力。
CAD技术对于中国汽车企业的重要性是不言而喻的。
尽管在2002年,中国汽车行业发生“井喷〞,一时间汽车成为和手机、房子一样炙手可热的商品,中国汽车业就此迎来了开展的大好时机。
同时,国外汽车企业看到了中国广阔的汽车市场,纷纷在华投资建厂,而国内的汽车公司趁机和国外公司合资,以为可以借助外国公司先进的技术来提高自身的研发能力,可实际上事与愿违。
外国公司并不愿意把先进的技术介绍给中国的公司,中国公司始终充当着OEM的角色,仅仅是外国公司在中国的制造基地,汽车研发水平仍难有所提高。
在2006年,国家将按照对WTO的承诺取消汽车进口配额。
步入21世纪的中国汽车工业将受到来自跨国汽车公司的巨大生存压力,以与数字化和产品、技术不断创新的严峻挑战。
因此,全面应用CAD技术是中国汽车工业开展过程中的必由之路,应纳入到各个汽车企业的开展战略中。
3、CAD技术在汽车工程领域的应用状况
美国福特汽车公司在上世纪80年代初就开场CAD系统的规划与实施,到了1985年有一半以上的产品设计工作在图形终端上实现,至90年代初其产品开发全面采用CAD。
早期的CAD系统已自行开发的PDGS和CAD为主,后来逐步过渡到以I-DEAS为其核心主流软件。
在CAD技术开展初期,美国通用公司就自主研发以设计车身为目标的DAC—1系统,来分析和综合车身的三维曲线设计。
到上世纪90年代初,美国通用汽车公司选中UG作为全公司的CAD/CAE/CAM/CIM主导系统。
经过不断的开展,公司已100%采用CAD来进展设计制造,并取消了中间过程,使计算机与制造终端直接相连,最终实现了系统网络化。
我国从上世纪70年代开场研究和推广CAD,使得CAD技术在国内得到了广泛的应用,并从中取得了不错的经济回报。
到目前为止,国内大型制造型企业如汽车企业已普遍实施了CAD系统,取代手工作业,一些大型汽车企业的CAD应用水平也接近国际先进水平。
但由于我国CAD软件自主研发术水平与兴旺国家之间存在巨大的差距,国内一些研究机构和公司推出的CAD系列软件得不到更广泛的应用,市场占有率低,尤其在CAD系统集成方面还是刚刚起步。
随着我国市场化程度的加深,市场竞争的加剧,迫使汽车企业必须改变传统的设计、制造、管理、销售模式,来提升企业竞争力和市场应变能力。
可以说,实施CAD系统是最有效的方式之一。
3.1汽车模具CAD技术
模具是能生产出具有一定形状和尺寸要求的零件的一种生产工具,也就是通常人们所说的模子。
模具生产具有高效、节材、本钱低、保证质量等一系列优点。
我国在对汽车新车型的开发上远远落后兴旺国家,其中一个重要原因就是覆盖件模具的设计效率低。
国内传统的模具设计方法已不能适应汽车工业的开展需要,而引进国外的覆盖件模具产品花费过高,而且会严重阻碍汽车产品的更新换代。
要解决上述问题,就必须研究开发我国自己的模具CAD技术,同时在国外先进的通用造型软件根底上进展二次开发无疑是一种必要而又有效的手段。
模具结构设计一般可分为二维设计和三维设计两种,两种方法各有其优、缺点。
计算机二维设计优点是设计速度快、占用计算机内存小、对计算机硬件配置要求不高,使用本钱低廉;
缺点是设计错误不易被发现,不能直接用于分析和加工。
而三维设计可实现参数化、基于特征、全相关等,使得产品在设计阶段易于修改,同时也使得并行工程成为可能。
另外,三维设计形象、直观,设计结构是否合理使人一目了然,但三维设计会导致计算机运算速度低、软件占用硬盘和内存的空间大、设计速度慢等。
国外汽车覆盖件模具CAD技术的开展已进入实质性的应用阶段,不仅全面提高了模具设计的质量,而且大大缩短了模具的生产周期。
近些年来,我国在汽车覆盖件模具CAD技术的应用方面也取得了显著的进步,但目前依然存在着一些问题,如设计效率低、标准化程度低、专用性差、开发手段落后、用户界面不能满足要求等,针对此,模具CAD技术主要向参数化、智能化、集成化、专业化等方面开展。
3.2汽车车身CAD技术
车身是汽车的一个非常重要的总成,占汽车车身质量和造价的40%—60%,其设计的好坏直接影响着汽车的使用性能。
车身又决定了汽车外形的美观程度,而汽车外形是消费者在购车时首先考虑的因素,对影响消费者的决策起着关键性的作用。
同时车身还必须有足够的强度和静刚度、良好的动力学性能指标,到达保证成员平安和汽车寿命,抗振抗噪,节约能源等目标。
车身CAD技术以三维造型为根底。
在传统的设计中,由于缺乏有效的辅助工具,开发人员常常以二维为根底进展构思,然后扩X到三维。
CAD技术在车身开发中的应用,使原来的旧模式有了彻底的改观。
设计人员通过与CAD系统的交互,将自己脑中的概念模式转化为清晰的视觉模式——几何实体,易于优化和改良,提高了工作效率和设计质量。
车身CAD技术面向制造和装配。
能熟练使用CAD进展产品设计的开发人员,主要集中于产品的数学建模,缺乏对制造技术的了解,而未考虑设计产生的数据对后续加工的影响。
为了准确加工产品,CAD系统提供的数据应该面向制造,保证其完整性和一致性,直接作为数控机床的输入数据。
在60年代初期,国外一些汽车制造公司就开场了模具CAD的研究。
例如DIEP公司研制成功的模具CAD系统,使整个生产准备周期由18周缩短为6周。
目前我国已有许多企业采用模具CAD技术,取得了丰富的经历和技巧,使模具精度和生产率大为提高,但是由于多方面的原因,尽管有些企业已经实现了无图纸设计,其模具CAD工作大多局限于计算机画图〔puterAidedDraft〕和二维设计,只有个别企业的汽车模具设计和制造能力接近国际先进水平。
此外,国内也出现了一些拥有自主的软件,如航空航天大学华正模具研究所开发的CAD系统CAXA等,解决了生产中的一些问题,但还没有得到很好的推广和使用。
车身CAD技术基于PDM。
在车身部件的开发中,可能会有多个车型设计要交替进展,产生多种数据版本,因此引入产品数据管理技术,建立统一的CAD工程数据库,消除车身开发中各局部内部信息和数据间的矛盾和数据冗余,从而保证开发过程顺利进展。
基于PDM的车身CAD集成系统结构由用户层、应用层、系统层、PDM系统集成层、异构环境处理层组成。
其中用户层由处在集成环境中各人员组成包括设计人员、工艺人员、制造人员等。
应用层由CAX系统和用户界面组成。
PDM系统集成层是整个系统的核心,由具有数据管理、数据操作的应用性软件组成。
异构环境层提供了集成所需的网络平台、操作系统平台、网络间数据传输与操作等功能。
3.3汽车底盘CAD技术
汽车总布置是汽车设计中重要的一环,对汽车产品质量起决定性的作用。
总体布置采用模块化设计,模块之间互相联系,彼此间可以交换数据。
在进展布置设计时,都是在三维空间内进展,因此必须确定零部件位置,这对建立整车坐标系与总称的坐标系很有必要。
在已建立的坐标系中建立数学模型,用坐标点的方法完成总称装配。
待设计完成后,要进展干预检查,一般分为位置干预检查和运动干预检查。
汽车动力性、操纵稳定性、制动性都是性能分析的重要工作。
另外,汽车总布置CAD系统是以数据库、图形库为根底的,设计过程中产生的一系列数据对于今后的工作会有很大的帮助,节省工作量。
总成图形库存储的是与整车总布置密切相关的零部件,其数据包含了对总成的特征结构和尺寸的描述。
总布置数据库主要包含设计中一些中间参数和数学模型运行结果,具有动态性。
3.4CAD技术在汽车轻量化中的应用
汽车减小自重,不仅可以改善汽车的各项性能,还能降低油耗节省资源。
有两种途径可实现汽车轻量化,一种是采用复合材料,另一种是减小汽车结构尺寸。
但不是为了保证汽车具有较高的平安性,采用缩小尺寸的方式必有一个界度。
尽管现如今复合材料已经广泛用于汽车上,但是从整体上来说,还没有完全到达节省资源的目的。
一方面继续研究性能更为优越的轻量化材料,另一方面可以从设计方面入手。
目前CAD系统只能表示实体的几何和拓扑信息,而不能表示材料信息。
一个现代化的CAD系统应该能建立实体内部的材料信息,即在一个实体内有着不同的材料结构。
而许多结构部件要求材料性能在零件内部随位置变化而连续变化,这要做既能满足零件的性能要求,又能节省大量材料。
比方气缸,其内部承受高温,因此可采用耐高温材料——陶瓷,外部要求具有良好的延展性,可采用金属,因此可以实现陶瓷材料和金属基体间