典型零件毕业设计综述Word格式文档下载.docx
《典型零件毕业设计综述Word格式文档下载.docx》由会员分享,可在线阅读,更多相关《典型零件毕业设计综述Word格式文档下载.docx(25页珍藏版)》请在冰豆网上搜索。
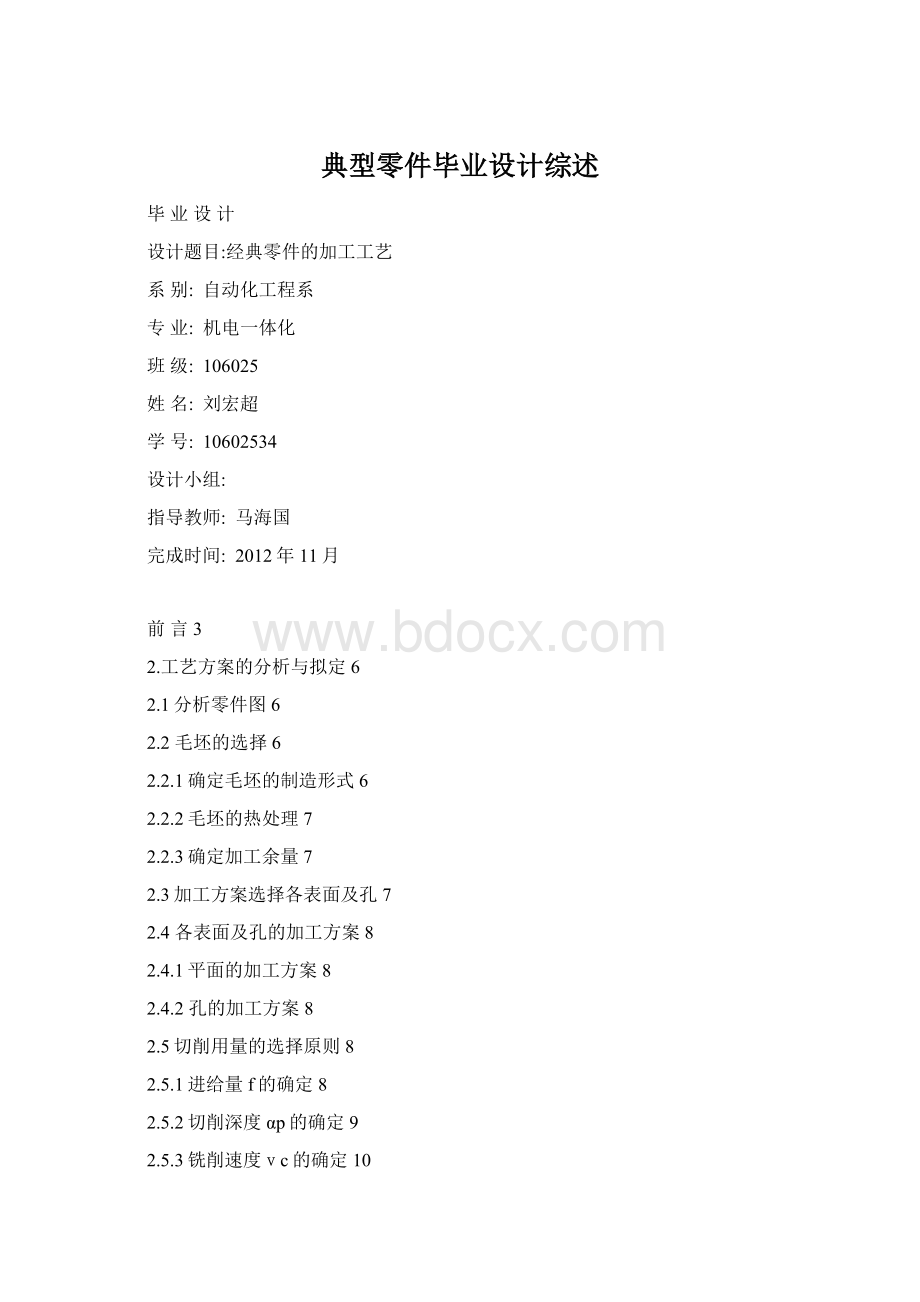
马海国
完成时间:
2012年11月
前言3
2.工艺方案的分析与拟定6
2.1分析零件图6
2.2毛坯的选择6
2.2.1确定毛坯的制造形式6
2.2.2毛坯的热处理7
2.2.3确定加工余量7
2.3加工方案选择各表面及孔7
2.4各表面及孔的加工方案8
2.4.1平面的加工方案8
2.4.2孔的加工方案8
2.5切削用量的选择原则8
2.5.1进给量f的确定8
2.5.2切削深度αp的确定9
2.5.3铣削速度vc的确定10
2.5.4主轴转速n的确定10
2.6拟订并确定加工工艺方案10
2.6.1拟订加工方案10
2.6.2比较并确定最终加工工艺方案12
2.7机床的选择12
2.7.1普通铣床的选择13
2.7.2加工中心的选择13
2.8工件的装夹与定位15
2.8.1工件的装夹方案15
2.8.2选择定位基准15
2.9夹具、刀具、量具的选择2.9.1夹具的选择17
2.9.2刀具的选择17
2.9.3量具的选择18
4.工序内容拟定18
4.1工序三的装夹方案18
4.2工步(3)的工艺分析19
4.2.2工步(5)的工艺分析20
结束语25
谢辞26
参考文献27
前言
数控机床(NumerialControlMachineTool)是用数字化信号对机床的运动及其加工过程进行控制的机床。
它是一种技术密集度及自动化程度很高的机电一体化加工设备,是数控技术与机床相结合的产物,它综合了应用计算机、自动控制、自动检测及精密机械等高新技术。
利用数控机床加工,其产品加工质量好,加工精度和效率均比普通机床高,尤其在轮廓不规则、复杂的曲线或曲面、多工艺复合化加工和高精度要求的产品加工时,其优点是传统机床所无法比拟的。
它的出现以及所带来的巨大效益引起世界各国科技界和工业界的重视。
随着数控机床已是衡量一个国家机械制造业技术改造的必由之路,是未来工厂自动化的基础。
需要大批量能熟练掌握数控机床编程、操作、维修的人员和工程技术人员。
但是我们装备制造业仍存在“六有六缺”的隐忧,即有规模、缺实力,有数量、缺巨人,有速度、缺效益,有体系、缺原创,有单机、缺成套,有出口、缺档次。
目前,振兴我国机械装备制造业的条件已具备,时机也很有利。
我们要以高度的使命感和责任感,采取有效的措施,克服发展中存在的问题,把我国从一个制造业大国建设成一个制造业强国,成为世界级制造业基地之一。
我的题目是配合件加工工艺及铣床夹具设计,包括铣端面、铣凸台、钻通孔等,对我们学过的知识进行一个概括总结。
这份毕业设计主要分为4个方面:
1.抄画零件图2.工艺方案的分析与拟订3.工艺设计4.夹具设计。
零件图通过在AUTOCAD上用平面的形式表现出来,更加清楚零件结构形状。
然后具体分析零件图由哪些形状组成,通过对零件的工艺分析,可以全面地了解零件,及时对零件结构和技术要求等做必要的修改,进而确定该零件是适合在哪台数控机床上加工,此零件我选择在加工中心上进行是因为加工中心具有自动换刀装置,在一次安装中,可以完成零件上平面的铣削,孔系的钻削、镗削、铣削等多工位的加工。
加工的部位可以在一个平面上,也可以在不同的平面上,因此既有平面又有孔系的零件是加工中心首选的加工对象,接着分析某台机床上应完成零件哪些工序加工等。
需要选择定位基准,零件的定位基准一方面要能保证零件经多次装夹后其加工表面之间相互位置的正确性,另一方面要满足加工中心工序集中的特点即一次安装尽可能完成零件上较多表面的加工。
定位基准最好是已加工面或孔。
再确定所有加工表面的加工方法、方案,选择刀具和切削用量。
然后拟订加工方案确定所有工步的加工顺序,进行工序划分;
先面后孔的加工顺序,因为平面尺寸较大,用平面定位比较稳定,而且孔的深度尺寸又是以平面为基准的,故先加工平面后加工孔。
最后再将需要的其他工序如普通加工工序插入,并衔接于数控加工工序序列之中,就得到了要求零件的数控加工工艺路线。
数控技术的广泛应用给传统的制造业的生产方式,产品结构带来了深刻的变化。
也给传统的机械,机电专业的人才带来新的机遇和挑战。
通过本次毕业设计让我们毕业生更好的熟悉数控机床,确定加工工艺,学会分析零件,工装设计。
为即将走上工作岗位打下良好的基础。
1零件简图
零件一
零件二
2.工艺方案的分析与拟定
2.1分析零件图
该工件材料为45#钢,其具有较高的强度、硬度,良好的耐磨性、塑性、韧性,切削性能较好。
材料选取锻成型毛坯零件1:
120mm*100mm*30mm,毛坯零件2:
120mm*100mm*30mm。
从工件整体上看,该工件结构较简单。
一个正方形板块高为20mm,板块两侧分别有深度为5mm的椭圆型凹槽,两侧钻有深15mm直径为Φ10mm的通孔,上下分别有一段圆环形凹槽,中心有Φ18通孔。
另外一个板块形板块高为20mm上还有一个复合型凹槽深5mm,大径为Φ28mm小径为Φ18的圆台形凹槽,凹槽和Φ18mm相切,深度为10mm,两侧有深为10mm的半圆形凹槽,其中有一个Φ10mm深为5mm的通孔,外边延伸一个宽为5mm的矩形凹槽,上边和下边都有一个相同的矩形凹槽。
整体零件精度要求不是太高,以上平面及Φ18mm的通孔作为定位基准。
2.2毛坯的选择
2.2.1确定毛坯的制造形式
数控铣床加工时,由于是自动化加工,除要求毛坯的余量要充分、均匀,毛坯除装夹要方便、可靠外,还应注意到数控铣床中最难保证的是加工面与非加工面之间的尺寸。
该零件为配合件,其形状较简单,但制造模具的材料,要求具有高硬度、高强度、高耐磨性、适当的韧性、高淬透性和热处理不变形(或少变形)及淬火时不易开裂等性能。
铸造适用于形状较复杂的零件,而锻造适用于强度较高、形状较简单的零件,最终根据该零件结构各特点的考虑,确定毛坯的制造形式为锻造。
据《机械加工技师综合手册》表2-10可查得合金工具钢,牌号为45。
主要特性为经调质处理后,具有良好的综合力学性能、低温冲击韧度及低的缺口敏感性。
淬透性良好,油淬时可得到较高的疲劳强度,水淬时复杂形状的零件易产生裂纹。
冷弯塑性中等,正火或调质后切削性能好。
一般在调质状态下使用,还可以进行碳氮共渗和高频表面淬火处理。
一经调质处理后用于制造中速、中等载荷的零件,如机床齿轮、轴、蜗杆等,调质并高频表面淬火后用于制造高硬度、耐磨的零件,如连杆、曲轴、套筒等。
根据《金属机械加工工艺人员手册》表3-13查得合金结构钢45,淬火温度850℃,冷却剂为油,回火温度520℃,冷却剂为水,油。
抗拉强度为980Mpa,钢材退火或高温回火供应状态下布氏硬度不大于207HBS。
从各方面考虑,所得毛坯的材料选用45的合金结构钢。
2.2.2毛坯的热处理
由于毛坯锻造出来存在内应力,为了消除内应力的对工件的的影响,毛坯锻造后应先缓冷,然后热处理淬火(850℃),中温回火(520℃),最后得到的组织为回火索氏体,应该零件表层要求有很高的耐磨性,所以调质后再进行表面淬火处理。
2.2.3确定加工余量
加工余量是指加工过程中所切去的金属层厚度。
加工余量分为加工总余量(毛坯余量)和工序余量。
加工总余量(毛坯余量)是毛坯尺寸与零件图样的设计尺寸之差;
工序余量是相邻两工序的工序尺寸之差。
加工余量的大小对于工件的加工质量和生产率均有较大的影响。
加工余量过大,会增加机械加工的劳动量和各种消耗,提高加工成本。
加工余量过小,则不能消耗前工序的各种缺陷、误差和本工序的装夹误差,造成废品。
所以要合理地确定加工余量。
总加工余量:
自由锻件3~5mm
工序余量:
粗铣1~1.5mm
高速精铣0.4~0.5mm
低速精铣0.1~0.15mm
粗铰0.15~0.35mm
精铰0.05~0.15mm–《数控加工工艺》P101
2.3加工方案选择各表面及孔
主要的因素:
1)要考虑加工表面的精度和表面质量要求,根据各加工表面的加工要求,选择加工方法及分几次加工。
2)根据生产类型选择,在大批量生产中可专用的高效率的设备。
在单件小批量生产中则常用通用设备和一般的加工方法。
如、柴油机连杆小头孔的加工,在小批量生产时,采用钻、扩、铰加工方法;
而在大批量生产时采用拉削加工。
3)要考虑被加工材料的性质,例如,淬火钢必须采用磨削或电加工;
而有色金属由于磨削时容易堵塞砂轮,一般都采用精细车削,高速精铣等。
4)虑工厂或车间的实际情况,同时也应考虑不断改进现有加工方法和设备,推广新技术,提高工艺水平。
5)还要考虑一些其它因素,如加工表面物理机械性能的特殊要求,工件形状和重量等。
2.4各表面及孔的加工方案
2.4.1平面的加工方案
查《机械加工技师综合手册》表5-3可以确定。
加工方案:
粗铣——精铣,经济加工精度等级为IT7~IT9,加工表面粗糙度为6.3~1.6um,一般不淬硬的平面,端铣表面粗糙度可较低。
2.4.2孔的加工方案
查《机械加工技师综合手册》表5-2可以确定。
钻——扩——粗铰——精铰,经济加工精度等级为IT7,加工表面粗糙度为1.6~0.8um,加工未淬火钢及铸铁的实心毛坯,也可以用于加工非铁金属,粗糙度稍高。
2.5切削用量的选择原则
数控编程时,编程人员必须确定每道工序的切削用量,并以指令的形式写入程序中。
切削用量包括主轴转速、背吃刀量及进给速度等,对于不同的加工方法,需选用不同的切削用量。
切削用量的选择原则是:
保证零件加工精度和表面粗糙度,充分发挥刀具切削性能,保证合理的刀具耐用度,并充分发挥机床的性能,最大限度提高生产率,降低成本。
2.5.1进给量f的确定
进给量是刀具在进给运动方向上相对于工件的位移量。
粗加工时,进给量的选择主要受切削力的限制。
根据加工材料、刀杆尺寸、工件直径及已确定的背吃刀量来选取较大的进给量。
在半精加工和精加工时,则按表面粗糙度要求,根据工件材料、刀尖圆弧半径、切削速度来选择合理的进给量。
当切削速度提高,刀尖圆弧半径增大,或刀具磨有修光刃时,可以选择较大的进给量以提高生产率。
粗铣时高速钢铣刀每齿进给量f=0.10~0.15mm/z
硬质合金钢铣刀每齿进给量f=0.10~0.25mm/z
精铣时高速钢铣刀每齿进给量f=0.02~0.05mm/z
硬质合金钢铣刀每齿进给量f=0.10~0.15mm/z
-《数控加工工艺》P165
钻中心孔时钻头每齿进给量f=0.05~0.1mm/r
钻孔时钻头每齿进给量f=0.1~0.2mm/r
扩孔时钻头每齿进给量f=0.2mm/r-《切削用量手册》表2.10
粗铰时铰刀每齿进给量f=0.4mm/r-《切削用量手册》表2.24
精铰时铰刀每齿进给量f=0.15mm/r-《切削用量手册》表2.25
2.5.2切削深度αp的确定
切削深度是指在垂直于进给方向上,待加工表面与已加工表面间的距离。
对于工艺系统刚性允许时,可以选取较大的切削深度,以减少走刀次数,提高生产效率。
对于零件的精度要求较高时,考虑适当留出半精加工和精加工的切削余量。
然而对于数控加工所留的精加工余量一般情况下比普通加工时所留余量小。
铣削时,精加工余量通常为0.2~0.8mm.和镗削加根据加工余量确定。
粗加工(Ra10~80µ
m)时,一次进给应尽可能切除全部余量。
在中等功率机床上,背吃刀量可达8~10mm。