立式注塑机机械结构设计设计Word文件下载.docx
《立式注塑机机械结构设计设计Word文件下载.docx》由会员分享,可在线阅读,更多相关《立式注塑机机械结构设计设计Word文件下载.docx(32页珍藏版)》请在冰豆网上搜索。
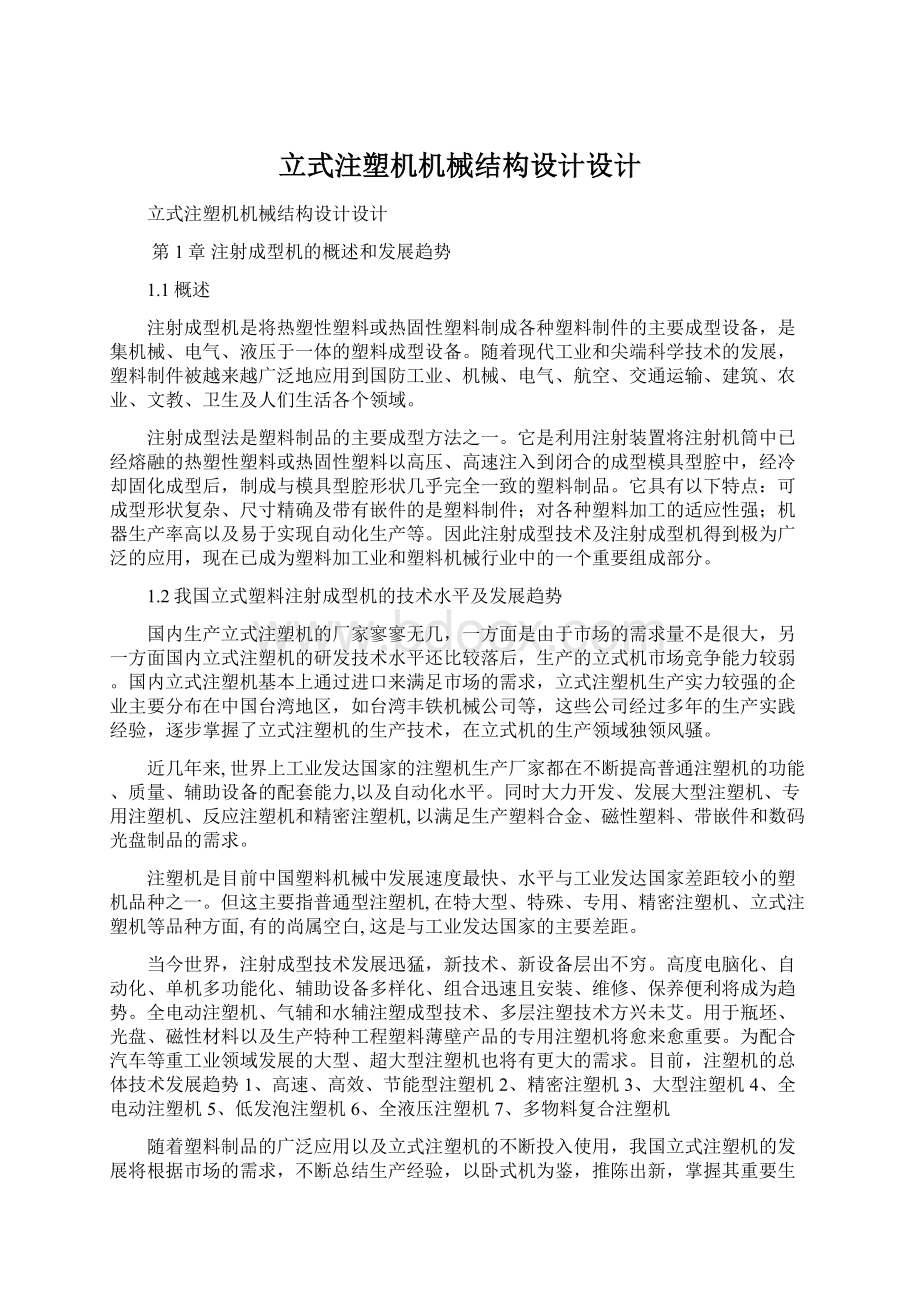
但这主要指普通型注塑机,在特大型、特殊、专用、精密注塑机、立式注塑机等品种方面,有的尚属空白,这是与工业发达国家的主要差距。
当今世界,注射成型技术发展迅猛,新技术、新设备层出不穷。
高度电脑化、自动化、单机多功能化、辅助设备多样化、组合迅速且安装、维修、保养便利将成为趋势。
全电动注塑机、气辅和水辅注塑成型技术、多层注塑技术方兴未艾。
用于瓶坯、光盘、磁性材料以及生产特种工程塑料薄壁产品的专用注塑机将愈来愈重要。
为配合汽车等重工业领域发展的大型、超大型注塑机也将有更大的需求。
目前,注塑机的总体技术发展趋势1、高速、高效、节能型注塑机2、精密注塑机3、大型注塑机4、全电动注塑机5、低发泡注塑机6、全液压注塑机7、多物料复合注塑机
随着塑料制品的广泛应用以及立式注塑机的不断投入使用,我国立式注塑机的发展将根据市场的需求,不断总结生产经验,以卧式机为鉴,推陈出新,掌握其重要生产技术,不断提高国内企业的自主研发能力,不断缩小与发达国家的差距,促进我国立式注塑机的蓬勃发展。
1.3课题研究意义
国内外权威人士认为,21世纪在材料领域将是塑料的天下。
由于塑料的可再生特点,塑料制品对于其它材料的可替代性,决定了塑料工业将持续发展,在农用灌溉、产品包装、建筑材料、汽车构件、信息产业、生命科学都有广泛应用,这是我国塑机产业能够持续繁荣发展的市场前景。
与西方发达国家年人均塑料消费品100多公斤相比,我国年人均塑料消费品不足13公斤。
因此,我国的塑料机械工业将有极大的发展潜力,尤其是立式注塑机,其在我国的市场占有率较低,因此研究设计立式注塑机可在一定程度上填补国内注塑机行业的空白,而且立式注塑机具有占地面积较小,容易安放嵌件,装卸模具较方便等优点,适应于复杂、精巧产品的自动成型及嵌件成型、模内组合成型,被广泛应用于国防、机电、汽车、交通运输、建材、包装、农业及人们日常生活等各个领域。
因此研究立式注塑机对塑料工业的发展及塑料制品的生产具有重要的现实意义。
第2章总体设计方案
2.1合模装置的初步设计
注塑机的合模装置按工作原理分主要有液压式和肘杆式两种。
液压式合模装置的优点如下:
在油缸已定的情况下,合模力仅与工作油的压力有关,因此要改变合模力可直接通过调节工作油的压力来实现,调整方便,读数易于显示;
若油缸已定,移模速度仅取决于油泵的流量,在移模的过程中,油泵的流量不变,其移模速度不变;
动模板在油缸行程范围内的任意点,可以停止并施压,故对不同厚度的模具适应性好,合模时,模具和模板因仅受活塞杆推力的作用故受力比较均匀。
而肘杆式合模装置相对于液压式而言,尺寸较大,在工作过程中容易受力不均,从而影响立式注塑机的稳定性及工作性能。
故设计时采用液压式合模装置。
2.2锁模方式的初步设计
一般立式注塑机的锁模方式有:
上模固定,下模上升闭模;
下模固定,上模下降闭模。
前者由于要克服模具的重力,对注塑机的合模系统有特殊要求;
后者可利用模具的重力进行合模,在相同的条件下可增加合模力。
故设计时采用后者,即下模固定,上模下降闭模。
2.3注射装置的初步设计
注塑机塑化注射装置基本上有双阶柱塞式、螺杆柱塞式和往复螺杆式。
前两种共同存在着以下缺点:
料筒内滞料现象严重;
料筒清理不方便;
结构上不够紧凑等。
而往复螺杆式同柱塞式相比具有如下优点:
塑化能力大;
塑化速率快、均化好;
注射压力损失小;
结构紧凑、熔料停滞分解现象少、清理料筒方便等。
故设计时采用往复螺杆式注射装置。
2.4驱动装置的初步设计
注塑机常用的驱动方式有油马达和电动机。
目前除大型注塑机考虑使用电动机驱动外,其余绝大多数均使用油马达直接驱动螺杆。
采用油马达驱动主要有以下优点:
可在比较大的范围内实现螺杆的无级调速;
一般属于恒力矩传动;
传动特性软、启动惯性小、不会超负荷工作;
对螺杆能起安全保护作用;
液压马达体积比同规格的电动机小得多,传动装置易于实现体积小、重量轻、结构简单的要求等。
故设计时采用液压马达驱动装置。
2.5液压油缸的布置形式
为了降低立式注塑机的重心,提高注塑机的稳定性,注射油缸、移模油缸及合模油缸均采用双缸对称布置。
2.6模板的平面布置形式
注塑机模板的平面布置形式有二柱式、四柱式、C式卧放、D式立放。
二柱式在受偏载或者模板面积较大时,容易引起模具开缝溢料,主要用在小型机器上。
四柱式因承载大,定位导向性能好,较为普遍采用。
至于采用C式卧放还是D式立放,主要从便于模具的安装和操作来考虑。
设计时采用四柱式布置。
第3章注射系统的设计
注射系统在工作过程中具有塑化、注射和保压的功能,其必须满足以下要求:
(1)在预定的时间内能将固态的塑料熔融塑化为黏流态的物料,并且能按预定的熔料量、温度为注射成型提供均匀的熔料;
(2)根据工艺要求能将塑化好的熔料以适合的压力和速度注射入模具的型腔中;
(3)当完全充模后,能在预定的时间内持续对模腔中的熔料保持一定的压力,保证制品的补缩和彻底排掉气体。
注射系统的主要组成部分包括塑化注射装置、驱动装置和计量装置等。
塑化注射装置由螺杆、机筒及加热冷却元件组成,在螺杆头部还可设置防止熔体倒流的止逆环或各种剪切混炼元件。
螺杆驱动装置主要由减速器机构、主轴套和旋转驱动电动机或液压马达组成。
计量装置是由支架和行程挡块组成的装置,它与螺杆预塑后退动作相联系,起塑化和计量作用。
3.1螺杆的设计
注射螺杆是注射系统中最关键的零部件。
注射螺杆具有塑化物料和将物料注进模具型腔的功能。
塑化时,机筒的加热和螺杆的转动使塑料在往前输送的过程中实现塑料的熔融,将固态塑料变为黏流态的熔体;
注射时,螺杆往前移动将机筒前端的熔体注射进模腔中。
螺杆的结构和工作特性对注射成型机的生产效率和注塑制品的质量都有很大的影响。
螺杆的主要技术参数有螺杆直径、螺杆的长径比、螺杆的行程、螺杆的转速、螺杆的扭矩、螺杆的驱动功率、螺杆的塑化能力等。
3.1.1螺杆的直径
螺杆直径。
3.1.2螺杆的长径比
长径比大的螺杆,可以得到低温均质的熔体和稳定的挤出以及高的塑化能力,这在挤出机的螺杆设计中已经了解到。
但是注射螺杆仅作预塑用,塑化时出料的稳定性对制品质量的影响甚小,并且塑料塑化时所经过的时温历程要比挤出螺杆要长。
所以,注射螺杆的长径比,没有必要取得像挤出螺杆那样长。
一般在18~22之间,长的也很少超过24就能满足要求。
从设计制造和使用的角度来看,也是希望用效果相近而长度较短的螺杆。
这样对螺杆机筒的制造、缩短机身长度、减轻机器的重量以及对机筒的清理方面都会带来好处。
设计时取螺杆的长径比为20。
3.1.3螺杆的长度L
一般根据螺杆的长径比来确定螺杆的长度。
螺杆的长径比为20,则螺杆的长度mm。
3.1.4螺杆的螺纹螺距S及螺纹角θ
为了方便螺杆的加工,一般取螺纹螺距mm,螺纹升角θ=17º
40´
。
3.1.5螺杆螺棱法向宽度e
一般e=(0.08~0.12),这里取。
3.1.6螺杆的转速n
螺杆的塑化能力与螺杆的转速成正比。
在一般情况下螺杆的塑化能力随着螺杆转速的增加而增加。
但在较高的转速条件下,其塑化能力的增加也非正比增加,有时却相反。
这是由于螺杆加料处的摩擦条件在改变,甚至发生料加不进的现象。
对于结晶型熔解热大的塑料,高速时如对机筒温度不作相应调整,则会因料不能得到充分地预热而使塑化能力得不到提高。
此外,螺杆转速又关系到螺杆对塑料的剪切速率和熔料的轴向温差,故对热敏性塑料(PVC等)螺杆转速要低,而对热稳定性好、粘度低的塑料(PS、PE等)需要较高的转速。
因此,对螺杆转速的确定,主要根据塑化能力、剪切均化等方面的要求来确定。
查阅《塑料材料学》,各种常用塑料注塑时所需螺杆的转速如表3-1:
表3-1各种常用塑料注塑所需螺杆的转速
材料
LDPE
HDPE
PP
HPVC
PS
ABS(通用型)
PMMA
PC
MPPO
转速
<
80
30~60
≤80
28
70
20~30
40~70
73
设计时取螺杆的最高转速n=80r/min。
3.1.7螺杆的结构及各段的长度、螺槽的深度
注塑机在使用过程中,由于经常需要更换塑料品种,所以拆换螺杆也比较频繁。
停机调换螺杆不仅强度大,同时又会影响机器的生产效率。
因此,设计一种适应性比较强的通用性螺杆,通过调整工艺条件(温度、螺杆转速、背压等)来满足不同塑料制品的加工要求。
这样可免于经常更换螺杆,同时也可降低机器的成本。
故设计时采用通用型螺杆,既可加工非结晶型塑料,又可加工结晶型塑料。
参考《塑料机械设计》表2-3-2,通用型螺杆各段的长度分别为:
加料段:
50~60%L
压缩段:
20~30%L
均化段:
20~30%L
,
对于通用型螺杆均化段槽深取加料段的槽深压缩段如图3-1所示:
图3-1螺杆各段的尺寸
3.1.8螺杆的行程s
螺杆的行程一般取为3.5(螺杆的直径)左右为宜。
故设计时取
3.1.9螺杆与机筒的间隙δ
螺杆与机筒的间隙值是设计时的重要数据,间隙大了,将会使塑化能力下降和注塑时熔料的回泄量增加。
反之,间隙小了又会增加制造方面的困难和螺杆的功率消耗。
根据实际使用情况,根据JB/T7267—94表4,当螺杆的直径为15~30mm时,螺杆与机筒的最大径向间隙δ≤0.12mm。
3.1.10螺杆的驱动功率及扭矩
参考《塑料机械设计》,按照经验公式计算。
螺杆的驱动功率计算公式如下:
式中:
—螺杆的驱动功率(kw);
—由螺杆结构参数及传动方式有关的系数,取C=0.00016;
—螺杆的直径(cm);
n—螺杆的转速(r/min)。
其中
故
螺杆扭矩的计算公式如下:
—螺杆扭矩();
D—螺杆的直径(cm);
—比例系数,对于热塑性塑料;
—由树脂性能而定的指数,。
螺杆的扭矩:
螺杆的扭矩需留20%~30%的余量,以作备用,故
3.1.11螺杆的材料
螺杆的材料一般为氮化钢(38