763烧成系统调试报告解读Word文档下载推荐.docx
《763烧成系统调试报告解读Word文档下载推荐.docx》由会员分享,可在线阅读,更多相关《763烧成系统调试报告解读Word文档下载推荐.docx(31页珍藏版)》请在冰豆网上搜索。
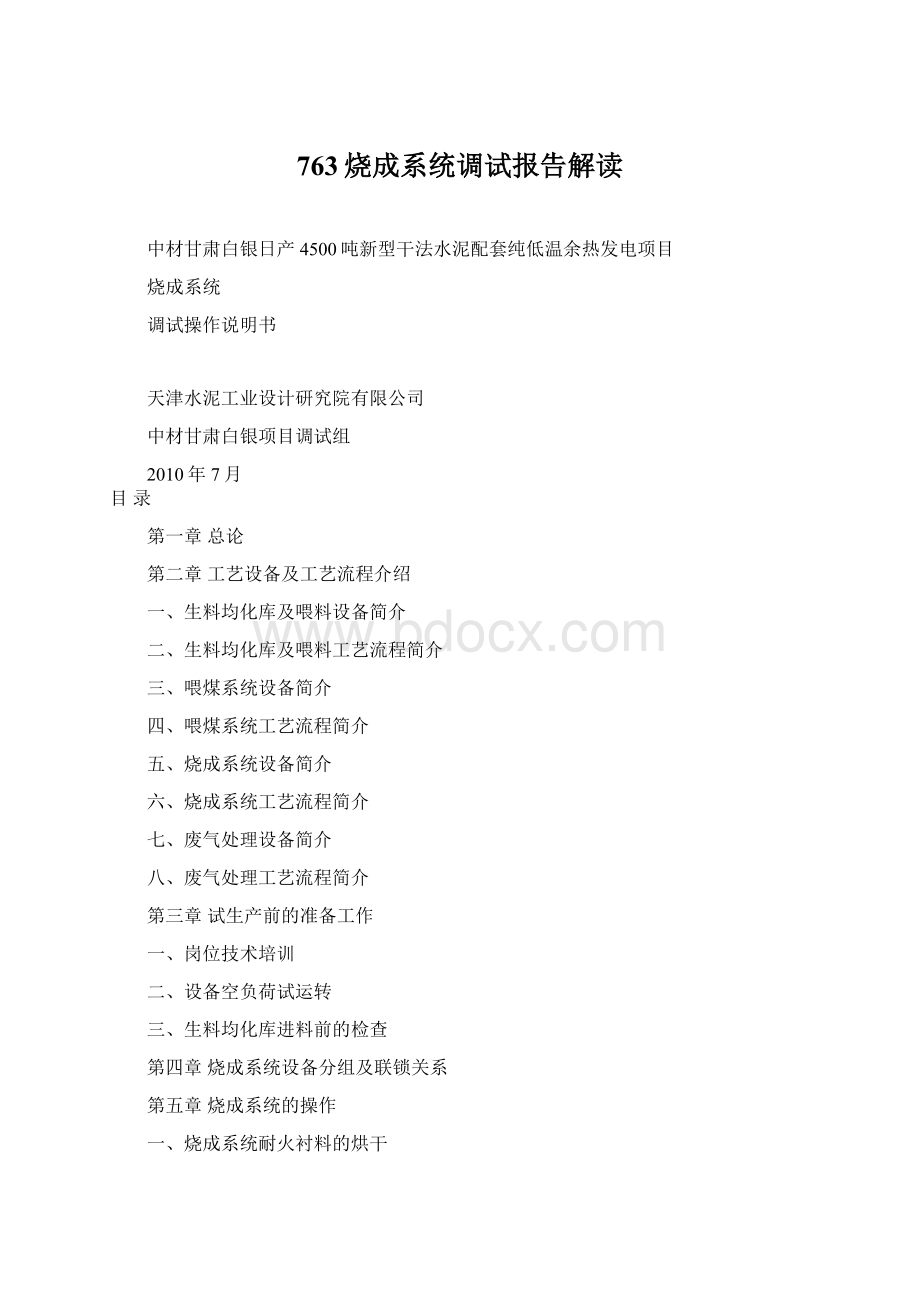
五、烧成系统设备简介
六、烧成系统工艺流程简介
七、废气处理设备简介
八、废气处理工艺流程简介
第三章试生产前的准备工作
一、岗位技术培训
二、设备空负荷试运转
三、生料均化库进料前的检查
第四章烧成系统设备分组及联锁关系
第五章烧成系统的操作
一、烧成系统耐火衬料的烘干
二、系统的投料试运行
三、系统的正常生产操作
四、常见故障及处理
五、烧成系统不正常现象的基本判断和解决办法
六、操作指导思想
第六章注意事项.
附:
生料均化库及入窑喂料系统、烧成窑头及熟料输送、烧成窑中、烧成窑尾、原料粉磨/废气处理、煤粉制备系统工艺流程图
第一章总论
本套调试资料是天津水泥工业设计研究院有限公司为中材甘肃白银日产4500吨新型干法水泥配套纯低温余热发电项目调试工作编制的,仅适应于该工程。
本套资料包括:
《原料粉磨、废气处理系统调试操作说明书》、《煤粉制备系统调试操作说明书》、《烧成系统调试操作说明书》和《水泥粉磨系统调试操作说明书》。
本操作说明书仅供烧成系统操作时使用。
本操作说明书的内容,仅限于保证设备的正常运转及工艺操作的基本事项。
为了保证顺利生产,提高设备的运转率,操作人员在必须掌握操作说明书内容的基础上,应了解每台设备的性能及其正确使用,以便在实际操作中解决出现的各类问题。
编制本操作说明书的基本依据是各类设计文件,同时结合以往生产调试中的经验。
部分生产参数要在试生产时,根据本厂的实际情况确定。
厂方的有关人员对本操作说明书内容有疑问时,请与我院派驻现场调试人员进行协商解决。
为了更好地了解主要设备的原理、性能与操作方法,请参考有关的单机说明书。
由于水平有限,编写时间仓促,资料中不妥、错误之处在所难免,恳望批评指正。
熟料烧成系统采用了5000t/d新型干法预热器带窑外分解技术,其工艺流程较复杂,要求操作人员对主要设备、工艺流程了解清楚,并能根据流程原理,判断解决生产中的问题。
烧成系统主要介绍生料均化库底及喂料、喂煤、烧成、熟料冷却及输送、废气处理等部分。
详见763-13/14设备表
生料在均化库顶由斜槽输送布料入库,入库的生料在库内水平层状分布。
当库底卸料时,“漏斗”状料流垂直切割各料层,达到重力均化卸出生料。
均化库设七个卸料口,库底设有七大卸料区。
一个大卸料区围绕一个卸料口,又分成两个小区,卸料口出料时,这两个小区是轮换充气的。
此类均化库卸料要求是:
1、4两个相对卸料口同时卸料,卸料时间是可调的,一般初定为20分钟,对每个小区对应充气时间是10分钟。
这对卸料口卸料20分钟,换下一对(2、5)卸料口卸料20分钟,再换到第三对(3、6)卸料口卸料20分钟,直至第七对(7、3)卸料口卸料。
完成一个卸料周期为2小时20分钟。
库底卸料是由程序对各充气管路上的电动球阀控制,达到有序卸料。
库底罗茨风机(13/14.28)充气,卸出生料经手动螺旋闸门(13/14.15)、气动流量控制阀(13/14.16)和输送斜槽(13/14.18)后送入计量仓(13/14.19)。
正常生产时,由计量仓内物料重量控制库底气动流量控制阀(13/14.16)开度,维持计量仓料位,为仓下稳定出料提供先决条件。
计量仓有两套卸料装置,其中一套备用,出料装置上配有一台手动螺旋闸门(13/14.20)、气动流量控制阀(13/14.21)。
计量仓及其卸料装置由罗茨风机(13/14.29)充气卸料,生料由计量仓通过卸料装置卸出后由斜槽(13/14.26)送至斗式提升机(15c.01),在出料斜槽上设有生料计量秤(13/14.24)计量出仓生料量。
操作员给定生料喂料量,生料计量秤按给定值控制仓下电动流量阀的开度,使卸出量与给定值一致。
经计量仓卸出的生料,通过窑尾斗式提升机(15c.01)、空气输送斜槽(15c.02)、电动分料阀(15c.02-1)、回转锁风卸料器(15c.04)直接送入窑尾预热器。
在斜槽(13/14.26)前取样,对入窑生料进行检测,为烧成操作提供指导。
正常生产时,计量仓内物料是基本稳定的。
可在仓满后,关闭进料阀门,仓底依照正常喂料,通过一时段仓重差,来标定生料计量秤,而不影响正常生产。
在预热器顶层,斜槽(15c.02)上设电动分料阀(15c.02-1),可调整入两列预热器的生料量,使出两列C1筒的废气温度尽量一致。
生料均化库及入窑喂料系统工艺流程图见附图。
详见763-19设备表
窑头、窑尾煤粉仓布置在煤粉制备车间内,煤粉仓设有荷重传感器,仓下设计量及输送设备。
两个煤粉仓卸煤粉分别进入两台PFISTER转子喂料秤,该喂料系统按给定值输出煤粉,并分别输送至窑头、窑尾燃烧器,输送空气由罗茨风机提供。
输送至窑尾煤粉,通过双通道煤粉燃烧器入分解炉燃烧。
输送至窑头煤粉,直接进入窑头燃烧器入窑燃烧。
当煤粉仓不进煤粉时,可通过一段时间仓重差值,标定仓下喂煤称,而不影响正常生产。
喂煤系统工艺流程图见附图。
详见763-15a,b,c,12/16,22设备表
烧成系统由Φ4.8×
72m回转窑,五级双系列低压损旋风预热器和TTF型分解炉组成,系统能力5000t/d。
本次设计采用小窑门罩,分解炉用三次风从篦冷机头部抽取,在分解炉内,物料有强烈的旋转和喷腾运动,停留时间长。
分解炉和窑头均采用多通道燃烧器,以保证煤的正常稳定煅烧。
预热器系统采用天津水泥工业设计研究院有限公司针对劣质煤开发的第三代低压损预分解系统。
分解炉采用性能优良的三喷腾型TTF分解炉,该分解炉结构简单、阻力系数低、有三喷腾和碰顶效应、湍流回流作用强、物料分散及换热效果好、温度场及浓度场均匀、固气停留时间比大等特点。
TTF型分解炉具有如下特点:
a.分解炉直接安装在窑尾烟室上面,窑气直接进入分解炉,保证了窑系统的稳定操作。
b.气体、物料和燃料在炉内混合均匀,形成一稳定的燃烧区,避免了炉内局部过热,所以分解炉很少结皮;
由于炉子底部与窑尾烟室直接相连,开口大,不易发生堵塞,同时从根本上避免了离线式分解炉塌料对生产造成的不利影响。
c.分解炉有后燃烧区,在主燃烧区没有完全燃烧的燃料,在后燃烧区可达到完全燃烧。
避免了由于燃料的后燃烧而引起的预热器堵塞。
d.通过三次风的分级设置,分解炉的下柱段有较大的脱硝空间,使排出的NOx低,对环境污染少。
e.分解炉的流体阻力较小,减小了系统的动力消耗。
f.单通道对称四点喷入煤,优化分解炉温度场。
生料在C2-C1的风管处进入预热器。
生料自上而下与热气体悬浮换热升温,入分解炉分解碳酸盐后,经C5收集后,从窑尾烟室喂入回转窑。
入窑物料表观分解率为90~95%,物料温度约860℃;
入窑物料经回转窑高温煅烧,发生固、液相反应,形成高温熟料。
高温熟料出窑入篦冷机快速冷却。
回转窑内煤粉燃烧后,产生的高温废气经烟室从分解炉底部入炉。
在分解炉内,煤粉、三次风、预热后的生料及回转窑的高温废气,通过旋流和喷腾,实现气料充分混合,完成燃烧、分解。
分解炉排出的气料,在C5内气料分离,物料入窑,废气经各级旋风筒,自下而上与生料悬浮换热降温,最后从C1排出,窑尾高温风机将废气送入废气处理系统,或入生料磨/煤磨供烘干用。
熟料在篦冷机的推动下与鼓入的冷空气进行热交换,排出的高温热空气一部分在小窑门罩处作为二次风入窑供煤粉燃烧,另一部分作为三次风经三次风管送入分解炉。
冷却机废气一部分进入余热锅炉用于纯低温发电,另一部分经电收尘器净化处理后排入大气,烟气的正常排放浓度≤50mg/m3(标)。
充分冷却后的熟料经篦冷机末端破碎机破碎,由槽式输送机送到熟料库储存。
熟料烧成系统工艺流程图见附图。
七、废气处理系统设备简介
详见《原料粉磨及废气处理系统调试说明书》
八、废气处理系统工艺流程简介
由窑尾一级旋风筒出来的高温废气经高温风机(15c.08)进入增湿塔(12/16.17),出增湿塔气体进入生料粉磨系统作为烘干热源。
依据生料磨的出口气体温度及生料成品的水分,调节增湿塔出口温度及生料磨车间各热风管道上的电动百叶阀的开度。
通过增湿塔增湿降温的废气与生料粉磨系统排出的废气混合后进入窑尾袋收尘器。
净化后的废气经风机排入大气。
窑尾袋收尘器和增湿塔收集下来的窑灰经输送设备输送至生料入库提升机(13/14.01)进入生料均化库,当生料磨停止运行时,则直接至入窑提升机(15c.01)进入窑系统。
增湿塔底部的螺旋输送机可正反向运行。
当增湿塔排灰水份高,有团块时,打开用于外排的电动锁风阀,螺旋输送机反转,湿灰外排。
废气处理系统工艺流程图见附图。
第三章试生产前的准备工作
烧成系统采用旋风预热窑外分解工艺生产,系统流程复杂,对操作维修人员的素质及设备质量要求较高,厂方应做好包括人员、物资、技术、安全等方面试生产前的准备工作。
本系统采用中央控制室集中控制,操作员不仅仅要在计算机屏幕上控制各设备,调整各运行参数;
还应知道当前的屏幕状态与现场实际是如何对应,知道利用屏幕所给的一切信息判断各设备运行状态,有异常时操作快而准确。
因此操作员应熟读本操作说明书、有关主机设备说明书,了解设计意图,掌握操作要领。
本系统各岗位工或巡检工应对工艺流程清楚,已接受过现场安全教育,有一定的设备维护经验。
系统内各岗位工段应有明确的岗位责任制度,安全制度,正确的操作制度。
机电设备安装后的空载试运转包括单机试车和联动试车。
单机试车是对机电设备制造,安装质量的初次检验,要求按照有关标准进行和验收。
进行中应记录空载电流、温升、振动等情况。
以备带负荷试车对比用。
单机试车由厂方、监理方,设备安装等方面组织进行。
联动试车是检验系统内各设备的开停是否按设计联锁开停;
有故障时,能否自动保护设备;
有紧急情况时,能否按安全要求紧急停车。
联动试车,由厂方统一组织,安装、监理、设计等配合进行。
联动试车需要现场与中控,现场与现场多方面联系,动用较多人员,岗位工、巡检工、操作员等应参加。
1.试车前的准备
1.1设备各润滑点按规定加油。
油量、牌号正确,油路畅通,油压、油温正常。
1.2确认需水冷的设备水路畅通,流量和水质符号要求,管路无渗漏。
1.3设备内部清扫检查、应无杂物。
然后做好各检查孔的密封。
1.4各管道阀门(电动、手动)现场用红油漆注明开关位置、方向等,并检查开关时的灵活性。
1.5现场的仪表检查。
做到仪表指示正确,与中控显示一致。
1.6设备紧固检查。
如地脚螺栓,有传动连杆等易松部位都要进行严格的检查。
1.7热风管道法兰连接的密封性,膨胀节保护螺栓拆除。
1.8耐火材料的砌筑情况,预热器中各测量孔通畅,留孔大小合适。
1.9各级预热器灰斗负压测管、吹堵管畅通,各闸阀开关位置关系正确。
1.10预热器上清堵工具,安全防护用品要备齐。
2.试车后的确认事项
2.1设备转向、转速正确,空载电流、振动、轴承温升、噪音等符合有关规定,并做好记录。
2.2润滑系统、水冷系统工作正常,各点压力、温度、流量正常。
2.3机旁和中控的关系,控制符合设计要求。
2.4各阀门开度指示,应做到现场指示、中控指示、机械装置自身位置三者一致,且运转灵活。
2.5各工艺测点、设备监控点的温度、