套筒加工工艺及夹具设计Word格式文档下载.docx
《套筒加工工艺及夹具设计Word格式文档下载.docx》由会员分享,可在线阅读,更多相关《套筒加工工艺及夹具设计Word格式文档下载.docx(15页珍藏版)》请在冰豆网上搜索。
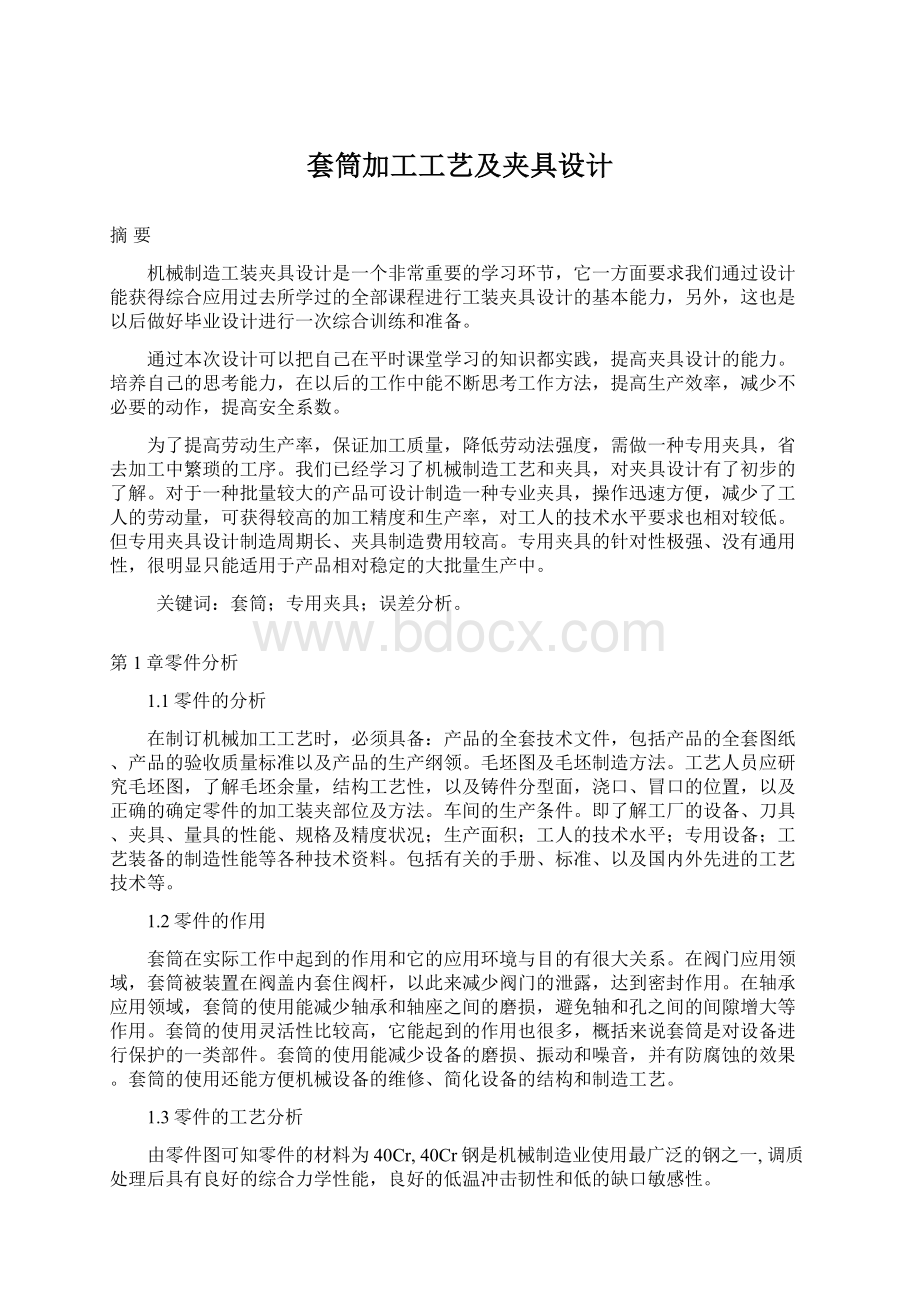
毛坯图及毛坯制造方法。
工艺人员应研究毛坯图,了解毛坯余量,结构工艺性,以及铸件分型面,浇口、冒口的位置,以及正确的确定零件的加工装夹部位及方法。
车间的生产条件。
即了解工厂的设备、刀具、夹具、量具的性能、规格及精度状况;
生产面积;
工人的技术水平;
专用设备;
工艺装备的制造性能等各种技术资料。
包括有关的手册、标准、以及国内外先进的工艺技术等。
1.2零件的作用
套筒在实际工作中起到的作用和它的应用环境与目的有很大关系。
在阀门应用领域,套筒被装置在阀盖内套住阀杆,以此来减少阀门的泄露,达到密封作用。
在轴承应用领域,套筒的使用能减少轴承和轴座之间的磨损,避免轴和孔之间的间隙增大等作用。
套筒的使用灵活性比较高,它能起到的作用也很多,概括来说套筒是对设备进行保护的一类部件。
套筒的使用能减少设备的磨损、振动和噪音,并有防腐蚀的效果。
套筒的使用还能方便机械设备的维修、简化设备的结构和制造工艺。
1.3零件的工艺分析
由零件图可知零件的材料为40Cr,40Cr钢是机械制造业使用最广泛的钢之一,调质处理后具有良好的综合力学性能,良好的低温冲击韧性和低的缺口敏感性。
由零件图可知Φ45中心线是主要的设计基准和加工基准,该零件的主要加工表面为Φ45外圆表面、Φ25的内圆表面、表面45的两个端面。
由以上分析可知,以上位置精度要求由参考文献中有关面和孔加工精度及机床所能达到的位置精度可知,上述技术要求是可以达到的。
第2章工艺分析
2.1确定毛坯的制造形式
选择毛坯应该考虑生产规模的大小,它在很大程度上决定采用某种毛坯制造方法的经济性。
如生产规模较大,便可采用高精度和高生产率的毛坯制造方法,这样,虽然一次投资较高,但均分到每个毛坯上的成本就较少。
而且,由于精度较高的毛坯制造方法的生产率一般也较高,既节约原材料又可明显减少机械加工劳动量,再者,毛坯精度高还可简化工艺和工艺装备,降低产品的总成本。
选择毛坯应该考虑工件结构形状和尺寸大小。
例如,形状复杂和薄壁的毛坯,一般不能采用金属型铸造;
尺寸较大的毛坯,往往不能采用模锻、压铸和精铸。
再如,某些外形较特殊的小零件,由于机械加工很困难,则往往采用较精密的毛坯制造方法,如压铸、熔模铸造等,以最大限度地减少机械加工量。
选择毛坯应考虑零件的机械性能的要求。
相同的材料采用不同的毛坯制造方法,其机械性能往往不同。
例如,金属型浇铸的毛坯,其强度高于用砂型浇铸的毛坯,离心浇铸和压力浇铸的毛坯,其强度又高于金属型浇铸的毛坯。
强度要求高的零件多采用锻件,有时也可采用球墨铸铁件。
零件材料为40Cr,该零件为套类零件,套类零件的结构特点是,具有同轴度要求较高的内、外旋转表面,壁薄而易变形,端面和轴线要求垂直,零件长度一般大于直径。
套类零件起支承或导向作用,在工作中承受径向力或轴向力和摩擦力。
套筒类零件毛坯材料的选择主要取决于零件的功能要求、结构特点及使用时的工作条件。
套筒类零件一般用钢、铸铁、青铜或黄铜和粉末冶金等材料制成。
有些特殊要求的套类零件可采用双层金属结构或选用优质合金钢,双层金属结构是应用离心铸造法在钢或铸铁轴套的内壁上浇注一层巴氏合金等轴承合金材料,采用这种制造方法虽增加了—些工时,但能节省有色金属,而且又提高了轴承的使用寿命。
套类零件的毛坯制造方式的选择与毛坯结构尺寸、材料、和生产批量的大小等因素有关。
孔径较大(一般直径大于20mm)时,常采用型材(如无缝钢管)、带孔的锻件或铸件;
孔径较小(一般小于20mm)时,一般多选择热轧或冷拉棒料,也可采用实心铸件;
大批大量生产时,可采用冷挤压、粉末冶金等先进工艺,不仅节约原材料,而且生产率及毛坯质量精度均可提高。
套筒类零件的功能要求和结构特点决定了套筒类零件的热处理方法有渗碳淬火、表面淬火、调质、高温时效及渗氮。
根据以上,选择‘棒料’,因为它易采购,成本低,准备周期短。
2.2定位基准的选择
定位基准的选择是工艺规程设计中的重要工作之一,基面的选择正确与合理,可以使加工质量得到保证,生产率得到提高。
否则,加工工艺过程会问题百出,更有甚者,还会造成零件大批报废,使生产无法进行。
2.2.1粗基面的选择
如果必须首先保证工件上加工表面与不加工表面的位置要求,则应以不加工表面作为粗基准,如在工件上有很多不加工表面。
则应有与其中的加工表面的位置精度要求较高的表面作粗基准。
如果必须首先保证工件某重要表面的余量均匀,应选择该表面作粗基准。
选作粗基准的表面应平整,没有浇口或飞边等缺陷,以便定位可靠。
粗基准只能用一次,以免产生较大的的位置误差。
对一般的轴类零件来说,以外圆作为基准是合理的,按照有关零件的粗基准的选择原则:
当零件有不加工表面时,应选择这些不加工的表面作为粗基准,当零件有很多个不加工表面的时候,则应当选择与加工表面要求相对位置精度较高大的不加工表面作为粗基准,从零件的分析得知,以毛坯的外圆作为粗基准。
2.2.2精基面的选择
用公用基准作为精基准,以消除不重合误差,即“基准重合”原则。
尽可能使各个工序的定位都采用同一基准,即“基准统一”。
当精加工或光整加工工序要求余量小而无效均匀时,应选择加工表面本身作为精基准,即“自为基准”原则。
为了获得均匀的加工余量或较高的位置精度,遵循“互为基准”原则。
精基准的选择,尤其是主要定位面,应有足够大的面积和精度,以保证定为基准可靠。
同时还应使夹紧机构简单,操作方便。
即“便于装夹”原则。
精基准的选择主要考虑基准重合的问题。
选择加工表面的设计基准为定位基准,称为基准重合的原则。
采用基准重合原则可以避免由定位基准与设计基准不重合引起的基准不重合误差,零件的尺寸精度和位置精度能可靠的得以保证。
为使基准统一,应该选择Φ25的孔作为精基准。
2.2.3拟定工艺路线
拟定工艺路线的出发点:
应当是使零件的几何形状、尺寸精度及位置精度等技术要求能得到合理的保证。
在生产纲领和生产类型已确定为大批量生产的条件下,可以采用万能机床配以专用工夹具,并尽量使工序集中来提高生产率。
除此之外,还考虑经济效果,以使降低成本。
工艺路线:
毛坯-车端面-钻中心空-车外圆-铰孔-钻Φ6的孔-去毛刺-检验
方案一:
20粗车:
粗车端面,粗车外圆Φ45,保留余量0.5mm。
30半精车:
半精车外圆Φ45,保留余量0.2mm。
40精车:
精车外圆,保证粗糙度。
50切断:
划线切断保证长度60mm
60钻:
调头装夹钻Φ23的通孔。
70粗车:
粗车Φ23的内孔,保留加工余量0.2mm。
80精车:
精车Φ23的内孔,保留加工余量0.1mm。
90钻:
专用夹具钻Φ6的孔
100热处理:
热处理保证硬度。
110磨:
磨内圆保证粗糙度。
120去毛刺
130检验
方案二:
10车端面:
车一端面保留长度65
20钻中心孔:
钻中心孔用双顶尖固定
30车外圆:
车外圆Φ45
40钻通孔:
钻Φ23的通孔
50车外圆:
掉头车端面车外圆Φ45
60扩孔:
扩孔至Φ24.9
70铰孔:
铰孔至尺寸要求
80倒角:
倒角45度
90钻孔:
100去毛刺
110检验
2.3工艺方案的比较分析
上面两个工艺方案的比较,可以看出方案一的加工为在零件所需要的长度基础上进行加长处理,然后再用双顶尖的装夹方式固定,这样在先加工出中心孔的情况下可以一刀将整个零件的外圆的尺寸要求车到位,这样在由于零件较长的情况下不能直接钻完整个工件的孔和在两端车螺纹以及扩孔,可以分两次调头装夹在机床上面,可以方便的加工。
工艺方案二是直接加工出工件的整个长度,这样就减少了钻中心孔的工序,且方案一需要在最后切断保留的长度,相对而言节省了时间,但通过仔细分析零件图可以发现,两次装夹车外圆的同轴度有误差,故只能在之前对工件进行加长用以在机床上装夹。
故通过分析选择工艺方案一为最佳的方案。
1.确定工艺过程方案
10毛坯:
选择120的棒料
20粗车:
2.4选择刀具具、量具
2.4.1刀具的选择
20车:
车两端面保证长度100mm,倒角45度,宜选用机床CA6140车床。
40钻:
钻中心孔,用双顶尖固定,宜选用机床CA6140车床。
50粗车:
车外圆Φ45×
60mm,宜选用机床CA6140车床。
钻Φ23的孔,宜选用机床CA6140车床。
70切断:
划线切断,宜选用机床CA6140车床。
80车:
粗车端面保证长度60mm,宜选用机床CA6140车床。
90铰孔:
铰孔至尺寸要求,宜选用机床CA6140车床。
110倒角:
倒角45度,宜选用机床CA6140车床。
120钻孔:
专用夹具钻Φ6的孔,宜选用机床Z525立式钻床。
2.4.2选择量具
本零件属于成批生产,一般情况下尽量采用通用量具。
根据零件的表面的精度要求,尺寸和形状特点,参考相关资料,选择如下:
1)选择加工面的量具
用分度值为0.05mm的游标长尺测量,以及读数值为0.01mm测量范围75mm~100mm的外径千分尺。
2)选择加工孔量具
因为孔的加工精度介于IT7~IT9之间,可选用读数值0.01mm测量范围50mm~125mm和0mm~25mm的内径千分尺即可。
2.5机械加工余量、工序尺寸的及毛坯尺寸的确定
套筒的材料为40Cr,硬度为220~240HBS,生产类型为大批量生产,且外形较为简单,可采用棒料进行生产。
根据上诉原始资料及加工工艺,分别确定各加工表面的机械加工余量、工序尺寸及毛坯尺寸如下:
120X50的棒料。
2.5.1外圆表面加工余量
通过图纸分析可以了解,该零件技术要求中要求在外圆有Ra1.6的表面粗糙度要求,仅粗加工是不能保证表面粗糙度的,必须精加工,查《机械设计工艺设计简明手册》可知Φ18-Φ50,经热处理和未经经热处理零件的粗、车长度小于等于200)加工余量。
粗车加工余量2mm
精车加工1mm
2.5.2长度方向的加工余量
长度方向的余量查《切削加工简明实用手册》表8-16,直径上的余量,该零件长度为60且该零件用中心孔定位安装
加工余量1.6-1.7mm取1.5mm。
2.5.3内孔的加工余量
由于孔的尺寸较大,查《机械设计工艺设计简明手册》可知毛坯上必须预留孔