精馏工序开车Word文件下载.docx
《精馏工序开车Word文件下载.docx》由会员分享,可在线阅读,更多相关《精馏工序开车Word文件下载.docx(13页珍藏版)》请在冰豆网上搜索。
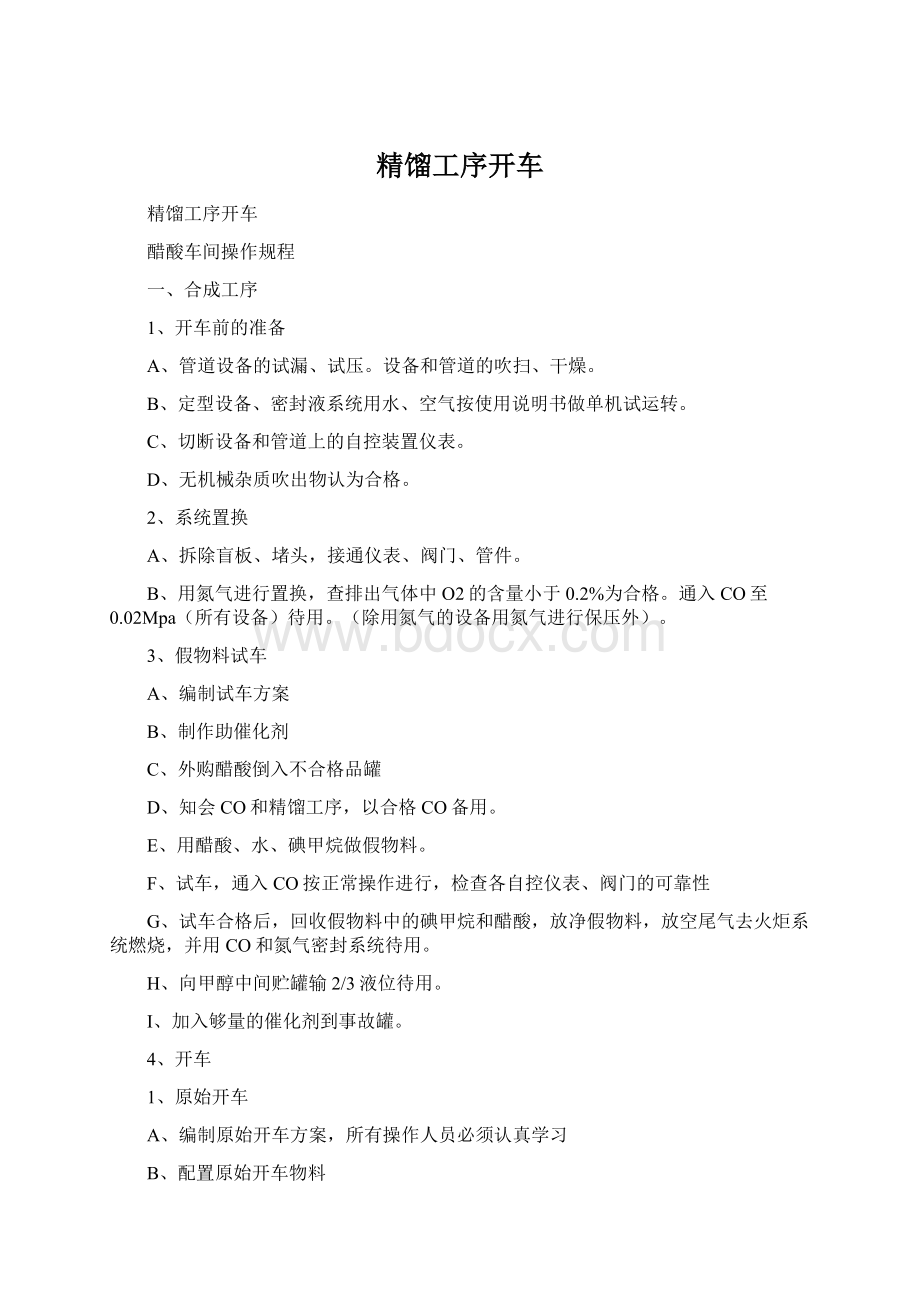
3、假物料试车
A、编制试车方案
B、制作助催化剂
C、外购醋酸倒入不合格品罐
D、知会CO和精馏工序,以合格CO备用。
E、用醋酸、水、碘甲烷做假物料。
F、试车,通入CO按正常操作进行,检查各自控仪表、阀门的可靠性
G、试车合格后,回收假物料中的碘甲烷和醋酸,放净假物料,放空尾气去火炬系统燃烧,并用CO和氮气密封系统待用。
H、向甲醇中间贮罐输2/3液位待用。
I、加入够量的催化剂到事故罐。
4、开车
1、原始开车
A、编制原始开车方案,所有操作人员必须认真学习
B、配置原始开车物料
C、检查事故罐所有进出口阀门是否按要求关闭或打开。
检查罐内是否充有CO气体,开动安全阀处于正常的工作状态。
D、将醋酸从中间罐区用不合格泵打入事故罐,其醋酸量是原始开车所需醋酸量,经计量后进入事故罐。
E、按原始开车物料配置所需的用水量的一半加入事故罐。
F、按原始开车物料配置所需的助催化剂量从催化剂工序的助催化剂贮槽计量进入书古罐。
G、用原始开车物料用水量所剩余的一半水加
H、
I、打开外循环换热器蒸汽切断阀,通入蒸汽加热循环液,使反应釜内溶液逐渐升温。
升温程序见复杂系统控制原理和操作手册。
4、正式投料,
1、正式投料前的升温过程中,随着反应釜内溶液温度升到100℃,打开反应釜液相出口管线上到外循环管线的阀门,同时关闭外循环主循环管线上反应釜到换热器之间的阀门,使反应釜出液除一部分经外循环泵、外循环换热器换热外,同时经转化釜小流量向蒸发器送料。
2、反映釜出口液体温度达到175℃时,加大通入CO量,使反应釜压力升高到3.0Mpa(绝),启动吸收甲醇富液泵,将吸收甲醇从吸收甲醇富液贮罐中泵出,以正常负荷的40%投料,惊调节阀、计量计算甲醇的量进行投料。
平稳后逐渐提升甲醇用量。
在提升过程,吸收甲醇富液量不够时,用新鲜甲醇与富液甲醇混合料。
3、启动中间罐区甲醇加料泵,将新鲜甲醇经流量计计量后与吸收甲醇富液混合进入反应釜。
4、随着反应釜反应的进行,反应后的液体流入转化釜内,转化釜液位逐渐上升到80%,手动打开连锁阀和调节阀,逐渐向蒸发器送料,并启动母液循环泵将事故罐中的液体逐渐加到反应釜中,维持反应釜液位。
CO与未反应的甲醇、醋酸甲脂在转化釜内进一步反应生成醋酸,放出热量,使转化釜内的温度逐渐上升到188.8℃
5、进入蒸发器的物料,在蒸发器上部分离,液体向下流入浸没式蒸发管内,集与下部空间,待下部液位达到20%时,关闭事故罐到母液循环泵进出口,打开蒸发器到母液循环泵之间的进口阀,将母液经母液循环泵送回反应釜,并维持蒸发器的液位平衡。
6、待转化釜反应液出口分析醋酸甲脂含量在0.6—0.8%之间时HI大于2.0%,醋酸含量小于产品醋酸需用的粗醋酸量时,启动蒸发器下部加热蒸汽阀门,,向加热段壳程通入蒸汽,但壳程内蒸汽夜里不得超过0.35Mpa,使其加热温度不得超过140℃
7、根据闪蒸气相流量来控制蒸发器通入蒸汽量,当流量达到正常时,停止蒸汽给入,当蒸气相流量小于正常流量时增加蒸汽给入量。
8、蒸发器下部的液位用母液循环泵的流量和由母液循环泵返回蒸发器的流量来控制。
若流量显示低于正常流量的30%时停止甲醇的加入量(吸收甲醇和新鲜甲醇),检查事故。
9、将事故罐剩余的物料逐渐压入蒸发器底部,打入反应釜中使用。
维持蒸发器下部液体液位在25%左右,70%的负荷开车正常后,逐渐加大投料量,调节各参数到规定的正常操作参数。
短期停车后的开车
短期、停车后,系统处于密封状态,反应液封欲反应釜和转化釜中,开车按以下步骤进行:
1、检查所有阀门的开、关是否符合开车要求
2、启动反应釜搅拌装置进行搅拌。
3、通入一定量的CO,使反应釜、转化釜的压力维持在正常的压力,即3.0Mpa(绝)和2.86Mpa(绝),同时启动高压吸收系统,操作步骤见吸收工序条款。
4、启动外循环泵进行反应液循环
5、启动外循环换热器蒸汽供应,对反应液进行加热使反应釜出口温度升到175℃。
6、反应釜出口温度升到175℃时,向反应釜投料,具体操作步骤见正式投料条款。
7、吸收甲醇贮罐液位处于高液位时,开车投料甲醇的加入可全用吸收甲醇代替新鲜甲醇(指合成工序投料)。
长期停车后的再开车,可按原始开车步骤进行。
物料的的准备可根据具体情况处理。
停车时贮存的物料必须做分析调整后方可使用。
停车
计划停车
1、接计划停车通知后,立即做好停车准备,同时联系其他工序也作好停车准备。
2、检查事故罐内有无溶液,液位多少、液相组成。
根据液相组成作好溶液处理,使其处于空罐状态。
接触仪表连锁。
3、停车时先停甲醇进料,即停止向中间罐区甲醇罐进料,停甲醇加料泵,逐渐减少吸收甲醇富液送料泵向反应釜送料流量。
进行减负荷操作;
停止蒸发器下部加热。
4、转化釜液体出口温度小于175℃、反应釜液体出口温度小于175℃时停止吸收甲醇送料泵,,停止反应釜吸收甲醇进料,减少CO进料量,减少高压吸收甲醇喷淋量,维持转化釜压力2.86Mpa(绝)
5、分析测定转化釜出口溶液中醋酸甲脂浓度小于1%时,继续降温。
6、反应釜出口温度、转化釜出口温度小于170℃时,停止向蒸发器进料,截断截止阀的同时停母液循环泵,使用外循环泵使反应液在反应釜、转化釜、外循环换热器、外循环泵之间形成循环。
降低外循环换热器的蒸汽压力,使反应液逐渐降温,并停止精馏工序的轻、重相的返回。
7、反应釜出口温度小于100℃、压力降为常压,转化釜出口温度小于90℃时停止外循环泵,停CO进气,停高压吸收系统,关闭方空尾气,补充CO维持反应釜、转化釜压力2.5Mpa(绝)。
蒸发器温度小于90℃时,将下部液体放入事故罐,用0.3Mpa(绝)CO保护封存。
8、如果反应系统主要设备需要进行检修或长期停车时,营将反应釜、转化釜内的液体全部放入事故罐并用CO密封保存。
反应釜、转化釜、蒸发器液体放净后,用稀醋酸冲洗,冲洗液排入集液槽贮存。
紧急停车
由于本工艺催化剂的特殊性,应尽量避免紧急停车。
紧急停车时,首先要根据事故发生部位及情况(查看连锁逻辑图)用CO进行保压处理(反应釜、转化釜发生事故时除外)
1、突然停电、停水、停蒸汽时,应立即关闭甲醇进料阀,吸收甲醇近料阀、反应液出口阀、高压吸收塔尾气调节阀,用CO保她,事故处理完毕后根据停车时间长短做相应的处理,再根据系统状态进行开车。
2、突然停CO时,立即关闭新鲜甲醇进料、吸收甲醇进料,同时关闭转化釜尾气进高压吸收塔进口阀、液体出口阀、重相和轻相返回反应釜阀,进行密封保压。
当压力降下时从CO中见罐运气维持。
停母液循环泵、停蒸发器加热蒸汽。
故障排除后再开车。
3、其他机械设备故障,视故障处于系统的部位做相应的处理。
‘
10.4催化剂的工序
10.4.1开车前的准备工作
10.4.1.1装置安装完成后的检查
(1)检查装置流程是否按设计流程安装合格
(2)检查设备、管道是否按设计要求进行,单机试运行(运转设备)合格,非标设备、管道吹扫,清洗是否合格。
(3)检查仪器、仪表安装是否合格,
(4)标准催化剂制备釜(R401)的液位容积。
10.4.1.2假物料水试车
水试车的目的,主要是对催化剂制备系统进行考察和测试,走通流程,为操作人员提供和积累一定操作经验。
(1)系统全部仪表,阀门按流程检查复位,待用。
(2)分别向制备釜冷凝器(E401)、碘甲烷冷却器(E402)通冷却水和冷冻水。
(3)建立搅拌器密封液系统。
(4)外界来的除氧水经FIQSA—402计量后加入催化剂制备釜(R401)中,至釜容积的80%,压力保持常压。
启动搅拌器进行搅拌,开蒸汽加热,连续运行4个小时。
(5)检查测试运行状况,合格后停止假物料试车。
(6)排净假物料水试车后停留在各设备、管道中的水,并用压缩空气吹干。
(7)用氮气置换系统合格后,密封系统充液待用。
10.4.2
10.4.2.1原始开车
(1)确定整个系统准备完成,已用氮气密封待用。
(2)液体投料,按物料平衡图(HAC0502-2-05)中401和402合计的总物料量,分别将各股物料量,由LISA-401液位,对应的液体体积设置,逐一投入催化剂制备釜内,最后投除氧水时,余留除氧水量的1/3,待固体加料完成后,在冲洗漏斗后全部投完。
(3)三碘化铑固体粉末的加料。
关闭加料漏斗下部的加料阀,打开引风机(C401),将称量好的RhI3(按铑计4.22kg),加入漏斗内,关闭漏斗盖,关闭漏斗上的抽气阀门,再打开催化剂制备釜上的抽气阀门使催化剂制备釜成微负压;
启动催化剂制备釜搅拌器进行搅拌,打开加料漏斗下部加料,将固体粉末三碘化铑假如催化剂制备釜。
关闭抽气阀并停引风机(C401),用剩余除氧水冲洗加料漏斗,待全部加完后,关闭加料漏斗下部的加料阀门。
(4)用一氧化碳置换催化剂制备釜(R401)、制备釜冷凝器(E401)及其相连的管道,阀门数次后,催化剂制备系统用一氧化碳充压到0.8Mpa(绝),启动PICSA-402压力调节系统和FIC-401流量调节系统,维持催化剂制备系统压力0.8Mpa(绝)。
(5)开蒸汽加热系统,对催化剂制备釜加热升温,控制反应温度为140℃。
(6)约10个小时后,取样分析溶液中铑的浓度,当铑离子浓度达到2400ppm时,停止加热催化剂制备釜,冷却降温。
(7)待催化剂制备釜内溶液温度降至常温后,停止搅拌,用一氧化碳将制好的催化剂溶液压入催化剂储罐(V405)储备待用或直接送至合成工序事故罐(V102)或补加至蒸发器(V103)。
10.4.2.2正常开车
(1)液体投料
根据精馏工序脱轻塔(T201)塔底采出液各组分浓度,按物衡图液体总投物料(图中401加402)量计算,设定LISA-401在一定值基础上,打开进料阀,通知精馏工序将脱轻塔塔底采出液切换至催化剂制备釜(R401)并同时通知合成工序注意操作控制,当催化剂制备釜液体达到规定值后,通知精馏工序将脱轻塔塔底采出液切换至合成工序,并通知合成工序注意操作控制。
关闭进料阀。
(2)三碘化铑固体粉末的投料
同原始开车
(3)加入除氧水
根据脱轻塔塔釜采出液的水含量,按物料平衡图的总投物料水含量计算出需添加的水量,全部用于冲洗加料漏斗。
(4)其他步骤同原始开车。
10.4.2.3正常停车
(1)分析催化剂溶液中的铑离子浓度达到2400ppm时停加热蒸汽。
(2)开冷却水冷却催化剂制备釜,待降到常温后停止搅拌。
(3)将催化剂溶液用一氧化碳压入催化剂储罐(v405)或送至合成工序事故罐(V102)或补加至蒸发器(V103)。
(4)关闭系统维持系统微正压(防止空气进入系统),待用。
10.4.2.4长期停车
除按正常停车外,再排空夹套内的水及机械密封仓内的密封液,并用氮气置换催化剂制备系统并保压。
10.4.3催化剂溶液再生
(1)检查确定催化剂制备釜是否空罐待用。
(2)将催化剂制备釜液位计LISA-401液位值设定为80%。
(3)将需再生的母液(其他金属腐蚀离子>5000ppm)从蒸发器下部利用位差送入催化剂制备釜(R401)内,当LISA-401达到80%液位时,关闭进料阀.
(4)用一氧化碳置换充压维持在0.3Mpa(绝).
(5)启动搅拌系统进行搅拌.
(6)开蒸汽加热,控制催化剂制备釜