风洞试验模型部件轻量化快速制造应用力学论文物理论文Word文档格式.docx
《风洞试验模型部件轻量化快速制造应用力学论文物理论文Word文档格式.docx》由会员分享,可在线阅读,更多相关《风洞试验模型部件轻量化快速制造应用力学论文物理论文Word文档格式.docx(7页珍藏版)》请在冰豆网上搜索。
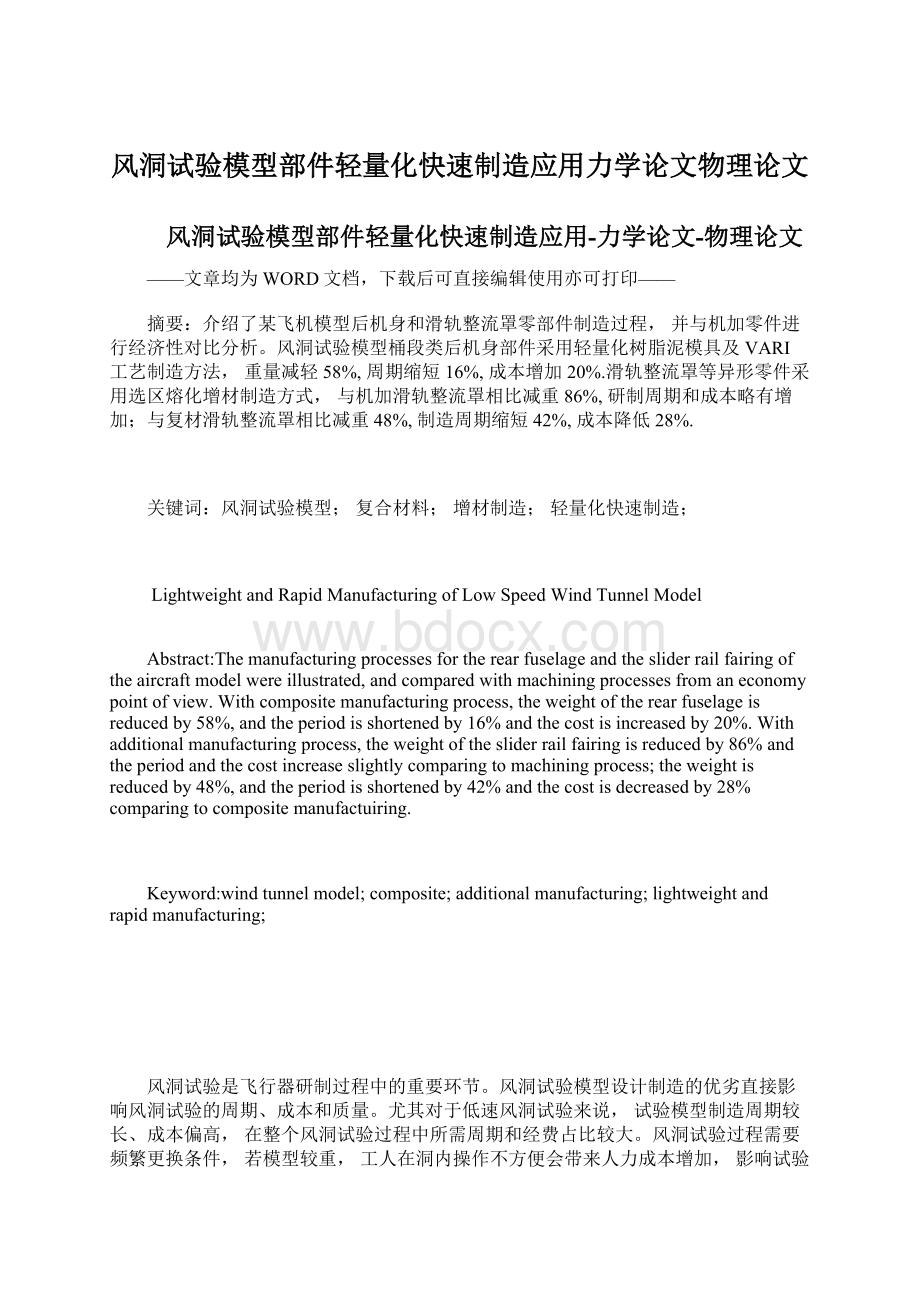
与复材滑轨整流罩相比减重48%,制造周期缩短42%,成本降低28%.
关键词:
风洞试验模型;
复合材料;
增材制造;
轻量化快速制造;
LightweightandRapidManufacturingofLowSpeedWindTunnelModel
Abstract:
Themanufacturingprocessesfortherearfuselageandthesliderrailfairingoftheaircraftmodelwereillustrated,andcomparedwithmachiningprocessesfromaneconomypointofview.Withcompositemanufacturingprocess,theweightoftherearfuselageisreducedby58%,andtheperiodisshortenedby16%andthecostisincreasedby20%.Withadditionalmanufacturingprocess,theweightofthesliderrailfairingisreducedby86%andtheperiodandthecostincreaseslightlycomparingtomachiningprocess;
theweightisreducedby48%,andtheperiodisshortenedby42%andthecostisdecreasedby28%comparingtocompositemanufactuiring.
Keyword:
windtunnelmodel;
composite;
additionalmanufacturing;
lightweightandrapidmanufacturing;
风洞试验是飞行器研制过程中的重要环节。
风洞试验模型设计制造的优劣直接影响风洞试验的周期、成本和质量。
尤其对于低速风洞试验来说,试验模型制造周期较长、成本偏高,在整个风洞试验过程中所需周期和经费占比较大。
风洞试验过程需要频繁更换条件,若模型较重,工人在洞内操作不方便会带来人力成本增加,影响试验周期;
模型过重会降低天平灵敏度和试验数据精准度[1].因此,实现低速风洞模型轻量化快速制造,是保证风洞试验短周期、低成本运行的重要手段。
目前,风洞试验模型制造领域轻量化快速制造技术主要包括复合材料制造技术和增材制造技术等。
1、风洞试验模型复合材料制造技术
1.1复合材料成型技术
碳纤维增强树脂基复合材料(以下简称复合材料)密度约为1.7g/cm3,抗拉强度3500MPa以上,其具有重量轻、比强度高等优点,被广泛用于航空航天领域飞行器结构件制造中。
在风洞试验模型,尤其是气弹、颤振模型制造过程中应用较多的复合材料制造方法,为真空辅助树脂注入成型工艺(VacuumAssistantResinInfusion,VARI)和预浸料-热压罐成型工艺。
VARI工艺在真空条件下完成,不需要施加额外压力,因此省却热压罐费用,由于不受热压罐尺寸限制,尤其适用于大尺寸复合材料零件成型,且成本较低[2].沈阳飞机设计研究所、中国空气动力研究与发展中心等单位采用此方法制造了大展弦比机翼低速、高速静气动弹性模型[3,4],大连理工大学采用该方法制造了一系列机翼、尾翼颤振模型,保证了几何与性能特征参数的精确性[5].VARI工艺在风洞试验模型领域的应用主要集中在气弹、颤振模型,通过剪裁设计实现刚度和强度模拟,而在常规测力试验模型中应用的报道较少。
相对于VARI工艺,预浸料-热压罐工艺对模具要求较高,成本随之增加,但制件性能大幅提升。
航空工业成都所和成飞采用预浸料-热压罐复合材料成型工艺成功制备了无超重全复材跨音速颤振模型,通过地面试验验证了该模型具有结构强度高、动力学特性精度高、分散性小、时效性好等诸多优点[6].
1.2复合材料成型轻量化树脂泥模具制造技术
复材成形模具通常采用框架式模具、整体模具、组合模具,常用材料包括铝、钢、殷钢、复材、等。
目前,VARI成型工艺常用整体金属模具,预浸料-热压罐工艺常用框架式金属或复材模具。
但金属模具制造周期较长,且重量较大,在车间现场操作须用吊车,极为不便。
另外,对于风洞试验模型桶段类零件来说,由于其曲率较大导致金属框架式模具制造难度增加。
因此,提出一种用于复材VARI成形的轻量化树脂泥模具。
其模具原材料包括树脂、铝粉等,密度为0.8g/cm3,原材料在混料桶搅拌后堆积成工装毛坯,在一定温度和时间内固化,最后采用数控加工成形。
为了保证模具气密性,在模具表面喷涂一层树脂,再次固化后进行精加工形成最终型面。
该模具具有重量轻、烧结时间短、制造成本低、可修复性强、可重复利用等特点。
2、风洞试验模型增材制造技术
区别于传统的切削减材制造技术,增材制造技术近年来发展方兴未艾。
在风洞模型制造领域应用较多的增材制造方式包括立体光固化技术(StereoLithographyApparatus,SLA)[7]、激光选区熔化成形技术(SelectiveLaserMelting,SLM)、激光直接成形技术(LaserSolidForming,LSF)和电弧熔丝成形技术(WireArcAdditiveManufacture,WAAM).
采用SLA加工方法,美国空军实验室飞行部制造了X-45A风洞试验模型[8],波音公司制造了推力模型换向装置[9],西安交通大学制造了测力模型、孔道一体化测压模型和气动弹性模型[10],并提出树脂-金属复合镀层方法,以弥补SLA材料强度不足等问题[11].中国航空工业空气动力研究院应用SLM技术加工了某挂弹模型折叠舵翼和进气道部件[12].波音公司航空/噪声/推进实验室采用LSF技术直接打印模型部件样件,了四个机加零件制造和手工装配过程[9].WAAM技术具有成形尺寸大、设备简单、制造成本低、材料利用率和沉积效率高等优势,已成为可实现高质量金属零件经济快速成形的方法之一。
英国CranfieldUniversity采用WAAM技术为英国飞机研究协会公司(ARA)试制了风洞试验模型不锈钢机翼[13].上述文献提到了增材制造技术在模型领域复杂零件快速制造方面的应用,并没有重点介绍增材技术所带来的轻量化制造优势。
3、风洞试验模型部件轻量化快速制造应用
3.1复合材料桶段类部件制造
风洞试验模型桶段类部件(如后机身)通常采用金属制造,主要有两种加工方式:
一是将部件按照工艺成本及可加工性分成若干零件,零件机加后再用螺栓连接成形;
二是整体机加外形,再进行内部结构减重加工。
第一种方法制造过程繁琐,手工装配工作量大,装配精度难以保证;
第二种方法制造成本偏高,原材料浪费严重且减重效果不明显。
桶段类部件采用复合材料可实现轻量化制造,但复合材料成形需要模具,金属模具的加工又增加了部件制造周期及成本,因此提出基于轻量化树脂泥模具采用VARI工艺成型复合材料部件的制造方法。
以后机身部件为例,其设计结构如图1所示。
由预埋铝合金连接件、碳纤维复合材料蒙皮及加强筋、预埋铝合金平垂尾安装骨架等组成。
预埋铝合金连接件、预埋平垂尾骨架与复材蒙皮通过胶沾连接。
蒙皮采用碳纤维加PMI泡沫夹芯结构,厚度为5mm,沿机身横、纵向设计碳纤维加强筋以提高结构刚强度。
碳纤维采用上海某公司生产的T700斜纹织物及双轴向织物,PMI泡沫为某复合材料公司的H52-P/3型泡沫,树脂采用上海某公司的5028低温环氧树脂。
在两个半侧树脂泥模具表面涂抹脱模剂,依次铺放T700斜纹织物、双轴向织物、PMI泡沫及双轴向织物,形成碳纤维泡沫夹芯结构。
此结构布置好后进行真空树脂导入,置入烘箱于50℃固化8小时。
待产品固化后在内表面铺设碳纤维加强筋并放置金属件,合模后进行整体二次真空树脂导入,再次置入烘箱加热固化8小时,待产品固化后脱模,制造过程如图2所示。
经三坐标检测,该后机身部件制造精度为0.5mm.
后机身轻量化树脂泥模具(图3)由沈阳万龙伟业机械制造有限公司制造,左右两侧模具总重量396kg,与金属模具相比,重量减轻75%,生产周期缩短20%.该模具由树脂基体材料表面覆盖超硬树脂层制成,精铣后可满足复材模具气密性和表面粗糙度要求。
3.2异形零件增材制造
风洞试验模型飞机滑轨整流罩通常采用传统机加铣削成形,无法进行内部减重,材料利用率低且加工周期较长。
随着复合材料的发展,飞机滑轨整流罩也逐渐采用复合材料加铝合金骨架制造,但复材模具的制造导致加工周期同样较长且成本偏高。
对于此类零件,采用面向激光选区熔化增材制造的中空结构,内部辅以点阵网状结构(图4(a)),可降低部件重量,显着缩短加工周期。
未精抛的飞机模型中空滑轨整流罩零件如图4(b)所示,在西安铂力特增材技术股份有限公司生产的BLT-S300设备上采用AlSi10Mg进行打印,成形时间60小时,成形完成后按顺序进行热处理、线切割、去支撑、打磨、喷砂、精抛等工序,成形零件重量为180g.
4、轻量化快速制造技术经济性分析
表1所示为后机身和滑轨整流罩采用不同制造方法时重量、制造周期和成本对比。
对于后机身部件,采用树脂泥模具和复合材料制造重量减轻58%,制造周期缩短16%,成本增加20%.采用增材制造方式制造滑轨整流罩,重量与铝合金滑轨整流罩相比减轻86%,与复材滑轨整流罩相比减轻48%;
制造周期与机加铝合金滑轨整流罩相比略有增加,与复材滑轨整流罩相比减少42%;
成本与机加铝合金滑轨整流罩相比增加38%,与复材滑轨整流罩相比降低28%.由此可见,采用复合材料和增材制造方式,可显着降低风洞试验模型重量;
对于大尺寸桶段类部件,采用复合材料制造可缩短制造周期,但成本略有增