2013年节能降耗合理化建议方案文档格式.doc
《2013年节能降耗合理化建议方案文档格式.doc》由会员分享,可在线阅读,更多相关《2013年节能降耗合理化建议方案文档格式.doc(21页珍藏版)》请在冰豆网上搜索。
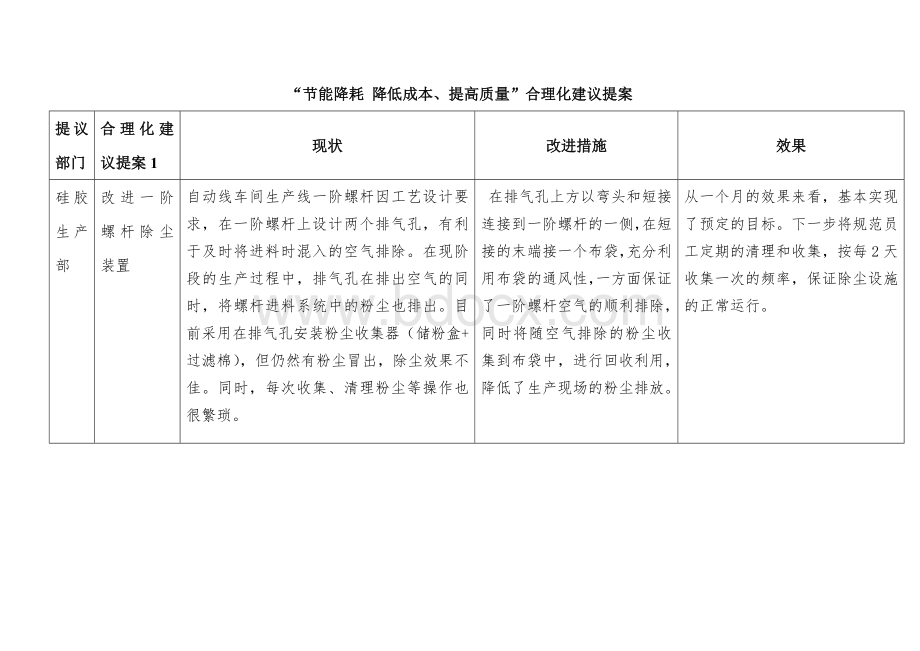
在排气孔上方以弯头和短接连接到一阶螺杆的一侧,在短接的末端接一个布袋,充分利用布袋的通风性,一方面保证了一阶螺杆空气的顺利排除,同时将随空气排除的粉尘收集到布袋中,进行回收利用,降低了生产现场的粉尘排放。
从一个月的效果来看,基本实现了预定的目标。
下一步将规范员工定期的清理和收集,按每2天收集一次的频率,保证除尘设施的正常运行。
合理化建议提案2
清理过滤器减少废胶
产品在分装过程中,主要是采取:
反应釜——连接软管——过滤器——分装机。
每缸生产结束后,对连接软管中的残留胶浆进行回收,而对过滤器的胶浆中的胶浆都作为废胶处理,因为一般在过滤网前端会有少量结晶物,为减少对产品质量的影响,都采取报废的方式处理,导致公司废胶量不断增加,造成不必要的浪费。
调查和分析,初步确定过滤器中的部分胶浆是可以回收利用的。
过滤器由2个半圆形喇叭口组成,中间夹一张过滤网,在清理过滤器的过程中,对过滤网前端的胶浆现场查看,发现有结晶物及少量杂质,如果回收利用可能会导致产品质量事故的发生,可作为废胶处理。
但在过滤器后端,因为过滤网的作用,能有效控制各类杂物。
要求现场清理人员将过滤器后端的胶浆进行收集,集中存放在一个桶内,每天及时送到制胶车间做返工处理。
此方案自10月28日开始,从过滤器后端收集的胶浆,经过初步统计,每个过滤器后端约可收集2kg胶浆,每天大约可收集30k左右。
合理化建议提案3
目的
有效控制白炭黑粉尘
制胶车间在生产过程中,需要将白炭黑从二楼投料口进料,通过管道进入一楼高速搅拌机,在加料过程中会在一楼、二楼产生大量的白炭黑粉尘,粉尘在车间排风扇的抽风状态下,大部分飞散到车间外部,对附近凉水塔、冷却水池中的水以及周边的环境造造成了不良的影响。
二楼目前有两个加料口,其中一个已有加料室,但因布袋除尘器的抽风能力限制,除尘效果不佳。
1、在二楼未安装加料室的加料口,增加密闭装置减少粉尘飞扬。
主要措施是在用白铁皮围住加料口的三面(一面留加料人员投料),形成一个半封闭的加料室。
2、在两个加料室的顶端,安装一个大功率排气扇,增加排气能力。
同时在加料室顶端以风管和三楼的2台布袋除尘器连接,将粉尘抽到布袋除尘器处理。
3、在一楼排风扇后端增加风管,将的粉尘排放到风管中,在风管末端采取喷淋装置,对除尘水进行收集和处理,达到除尘的效果。
此方案主要是充分利用了公司现有的设施,在不增加大的投入的前提下,实现生产现场粉尘得到有效控制的效果。
合理化建议提案4
冷却循环水系统改造
1、1#、4#线二阶机在抽真空过程中,经常发生真空管堵塞的现象,导致1#、4#停线。
2、二阶机在抽真空的过程中,将产品中的助剂大量抽到真空泵,影响生产线真空度,同时循环水发生变质,不能实现达标排放。
3、近期设备部对1#缓冲罐、外缓冲罐改造后,真空度能得到保证,但经常性出现缓冲罐堵、循环水浑浊需换水等现象。
4、1#、4#生产线所有装置基本相同,但在生产同一产品时,2条生产线二阶螺杆筒腔温度存在较大的差异,1#线二阶螺杆筒腔温度远远高于4#线,4#线在与1#线真空度相同的情况下没有因助剂抽出堵塞缓冲罐的现象发生。
5、1#线、4#线一阶机、二阶机温差大,主要是因为冷却系统不同而形成。
目前1#、2#、3#一阶机共用1台冷却塔,4#线一阶机单独使用1台冷却塔。
1#、4#线二阶机采用冰机冷却水进行降温,但1#线配置的是20匹冰机,同时还串联1#、2#、3#线的静态机冷却;
4#线配置的是40匹冰机,仅连接4#线的静态机冷却。
由此可以看出,生产系统冷却循环水系统配置不合理。
6、生产系统3个冷却塔按“两开一备”的运行模式设计,从目前运行的情况来看,仅4#冷却塔是正常运行的,1#、2#、3#共用的冷却塔因长周期运行,冷却塔内的塑料蜂窝板严重变形,影响冷却效果,经现场测试,在11月22日的生产过程中,1#、2#、3#共用的冷却塔仅供1#运行时的温度比4#线冷却塔温度高5-6度(1#线为27-28°
C,4#为21-22°
C),在1#、2#线同时使用冷却塔时比4#线冷却塔温度高8-10°
C左右,夏季的温差可能更大。
备用的冷却塔因冷却效果不好一直未投用,主要原因是冷却塔内塑料蜂窝板填充不足,导致向上抽风时没有和塑料蜂窝板流下的水进行完全的热交换,而是从冷却塔周围未填充蜂窝板的空间直接抽走,影响冷却效果。
1、改造一阶冷却循环水系统,1#、2#共用1台冷却塔,3#、4#共用1台冷却塔,形成“两开一备”的生产管理模式。
2、改造二阶冰机冷却系统,1#、2#共用1台冰机,3#、4#共用1台冰机。
目前1#冰机功率为20匹,能否修复已损坏的40匹冰机系统,确保制冷量能满足生产要求。
形成和3#、4#共用的40匹冰机系统均衡。
3、对冷却塔进行修复,一台更换塑料蜂窝板,另一台填充部分缺失的塑料蜂窝板,保证冷却塔能正常运行。
4、对1#、2#、3#、4#线一阶机筒体冷却水管,1#、4#二阶机筒体的冷却水管进行检查、清洗,确保冷却管道畅通。
5、目前中控室计算机不能显示部分双螺杆区段的温度,要全面检查4条生产线的热电偶,确保中控室集散系统能对双螺杆各区的温度进行有效监控。
6、以上方案实施后,还可采用降低1#二阶机直流电机转速,降低筒腔温度,即有目前的300转/分钟调整为270转/分钟左右。
1.解决1#、4#线二阶机在抽真空过程中,真空管堵塞。
2.改造一阶冷却循环水系统达到均衡
合理化建议提案5
优势
硅胶技术部
107吨桶胶的回收
公司目前对生产使用的2万107胶采取吨桶,生产使用后拉到刮胶处由专人刮胶,刮出的胶由厂家进行回收
1、制作专用沥胶架。
用角铁制作2个铁架,用于107吨桶沥胶,铁架表面倾斜约15-20度。
吨桶107胶空桶沥胶24小时后,放置在沥胶铁架上12小时,通过重力作用,吨桶内的残余胶浆经放胶口流入小桶中集中回收。
2、少量残余的胶浆由当班人员用专用刮刀将余胶刮出来,流入小桶中。
三、3、小桶中回收的胶浆直接投入生产系统中,不再外送加工。
4、沥胶工作纳入放胶人员日常工作职责中,不再需要增加人工刮胶费用。
按每月收集2吨107胶计算,和铁桶刮胶对比,减少费用为:
2吨胶减少人工费用:
2000元
减少加工费用:
2*1700=3400元
减少胶的损失:
2吨*(1-70%)*17000元/吨=10200元
每月预计可降低成本约:
2000+3400+10200=15600元
合理化建议提案6
增加直分压胶机1台
1、现在中性透明胶、中性瓷白硬包、灰色硬包等产品的生产过程:
反应釜→桶→分装
2、1缸料可压出3.5桶胶,需要消耗4个塑料袋,成本约4*8=32元。
3、1桶中性透明软包胶在压出到分装,经现场抽检,约产生2.5公斤左右的废胶,造成的浪费约为:
4*2.5*10元/公斤=100元
采用直分压胶后,生产过程为:
反应釜→分装,可减少废胶的产生和塑料袋的消耗。
1台压胶机按每天直分5缸产量计算,可节约:
5*100=500元,可节约塑料袋:
5*3.5=17个。
按8元/个计算,可节约:
17*8=136元,每月可节约:
(500+136)*26=16536元。
2、采用直分压胶机,1缸胶的生产时间由75-80分钟减少至60分钟,
提高了工作效率;
同时,减少了频繁换桶,降低了劳动强度。
3、现有的中性瓷白硬包、灰色硬包等产品的生产,在增加压胶机以后均可采用直分方式进行分装,进一步减少废胶的产生和物料的消耗。
4、增加直分压胶机后,可减少现有生产线的3台小型压胶机(2台硬包、1台软包)。
“节能降耗降低成本、提高质量”合理化建议提案
合理化建议提案7
改进白油管线
公司白油管线是由油库经过管道输送至制胶车间门口的储罐中,然后由储罐经过铁桶分别运到制胶车间和自动线车间。
特别是自动线车间在生产负荷较大的情况下,每天需要人工将20多桶白油从储罐用手推车运到车间内,通过管道泵打入生产系统。
改进白油管线是在公司原闲置的白油管线的基础上,做部分的管道改造,使白油通过管道泵直接由储罐进入生产线系统。
可有效避免雨水天气时运输白油时可能进水的现象,同时减少了白油运输环节,降低了员工的劳动强度。
自动线包装机配备自动喷码机。
目前自动线包装机采用人工装罐,是将喷码后摆放混乱的管子再整理后放入包装机管箱,因此经过两道工序:
先集中喷码,再在包装机处整理。
自动线包装机需要专人放管,影响单位包装效率。
自动线包装机操作人员可直接将原包装整齐摆放的管子一次性加入管箱内,不需要专人整理摆放管子,可减免先喷码后整理摆放的两道工序。
也可减少现有喷码处人员数和工作量,进一步降低成本,比如:
每台喷码机的价格约在10000元左右,四条自动线配备四台喷码机大约在40000元左右,但属于一次性投入;
其节约的喷码处人力成本,以每人月工资3000元计算,年工资超过35000元,但属于持续投入。
改善处理返工胶工具
目前返工胶处理时采用人工挤压的方式,耗时耗人,效率低下,且胶管内残留胶较多。
采用气动胶枪
采用气动胶枪,可迅速将胶管内待处理胶液挤出,快速高效,可降低操作时间和提高效率。
比如:
返工100支胶,采用现有手工挤压方式,一人切二人挤压,大概需要20分钟;
若采用气动胶枪打胶,二人可在10分钟之内完成,而且劳动强度也低。
增添直封压料机带2台包装机
制胶车间因压料机缺少,导致成品胶先压入到200L铁桶内,再后续分装,导致工作时间变长(每釜料压入铁桶约耗时15分钟)和浪费(每个铁桶分装后约有超过2kg物料无法压干净)。
除可增加直封压料机数量外,可否采取每台压料机带两台包装机的形式,降低每釜料包装时间,从而提高直封效率。
现有直封工艺每釜料大约需耗时40-50分钟,采用单出口单包装机,若采用双出口双包装机可将每釜料包装时间缩短至20-30分钟。
硅胶技